齿轮精度检测项目
齿轮检验的3个公差组

齿轮检验的3个公差组一般厂家检验ff、Fβ、Fr、Wk、ΔW,欧洲厂家主要要求检测Fi″、fi″、Fr、Wk。
还有一个隐含要求,就是装配后噪音要小。
1、齿轮的检测有三方面要求:传递运动的精确性、平稳性、载荷分布的均匀性。
2、这三个公差组各有数个检测项目,按国标要求每个公差组只检一项或两项(当然不是随意选)一般情况下设计者会给出每个公差组的精度等级和需检测的项目。
3、但有时图纸上会给出数个项目或只给精度等级和标准,这种情况下个人认为最好和设计沟通一下,看对方有什么要求,否则你费了半天劲可能人家一句话你就得从头再来。
若设计没什么要求那你可以按标准要求每个公差组检一项或两项就可以了,记住是按照标准要求,不是自己随意挑的。
4、个人感觉一般情况下是这样的,每一公差组检FP或公法线变动和FR,第二公差组检Fα和FPT,第三公差组检Fβ。
纯属个人感觉没有依据。
5、除了这三方面的要求外,还有齿厚要求,当然这个是好检的,可测公法线或跨棒距。
渴望与大家一同进步,有愿意讨论的可加我QQ951666310,注明机械,或发邮件wzfsxx@一典型零件检测view09f4486fb84ae45c3b358ce1.html1.5齿轮的检测1.5.1 齿轮线性尺寸的测量1.5.1.1分析工作任务书1.阅读齿轮零件图,了解减速器直齿圆柱齿轮的结构;只供学习与交流2. 熟练掌握齿轮的基础知识;3.掌握齿轮检测原理;4. 掌握常用的齿轮检测工具;5.选择齿轮的检测方案,确定测量工具;6.进行检测;7.记录数据并进行数据处理;一典型零件检测1.5齿轮的检测1.5.1 齿轮线性尺寸的测量1.5.1.1分析工作任务书1.阅读齿轮零件图,了解减速器直齿圆柱齿轮的结构;2. 熟练掌握齿轮的基础知识;3.掌握齿轮检测原理;4. 掌握常用的齿轮检测工具;5.选择齿轮的检测方案,确定测量工具;6.进行检测;7.记录数据并进行数据处理;只供学习与交流8.上交检测报告,进行评价。
齿轮精度等级标准8-7-7
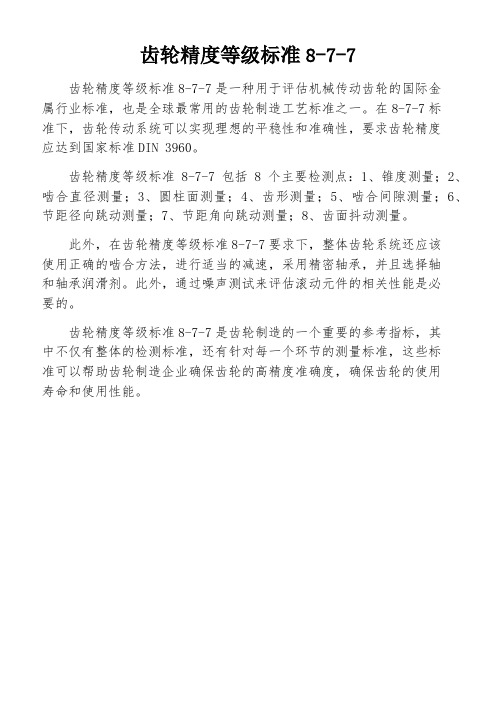
齿轮精度等级标准8-7-7
齿轮精度等级标准8-7-7是一种用于评估机械传动齿轮的国际金
属行业标准,也是全球最常用的齿轮制造工艺标准之一。
在8-7-7标
准下,齿轮传动系统可以实现理想的平稳性和准确性,要求齿轮精度
应达到国家标准DIN 3960。
齿轮精度等级标准8-7-7包括8个主要检测点:1、锥度测量;2、啮合直径测量;3、圆柱面测量;4、齿形测量;5、啮合间隙测量;6、节距径向跳动测量;7、节距角向跳动测量;8、齿面抖动测量。
此外,在齿轮精度等级标准8-7-7要求下,整体齿轮系统还应该
使用正确的啮合方法,进行适当的减速,采用精密轴承,并且选择轴
和轴承润滑剂。
此外,通过噪声测试来评估滚动元件的相关性能是必
要的。
齿轮精度等级标准8-7-7是齿轮制造的一个重要的参考指标,其
中不仅有整体的检测标准,还有针对每一个环节的测量标准,这些标
准可以帮助齿轮制造企业确保齿轮的高精度准确度,确保齿轮的使用
寿命和使用性能。
齿轮间接触精度检测方法

齿轮间接触精度检测方法
齿轮是一种常见的机械元件,广泛应用于各种机械传动系统中。
齿轮的间接触精度是指齿轮与齿轮之间的接触面的精度,它直接影响到齿轮传动的性能和使用寿命。
因此,对齿轮间接触精度进行准确检测是非常重要的。
常用的齿轮间接触精度检测方法主要有以下几种:
1. 接触模型法:这种方法基于齿轮的理论接触模型,通过测量齿轮的几何参数,如齿高、齿距等,计算出齿轮的理论接触区域。
然后,利用接触模型与实际测量的齿轮接触区域进行比较,从而得出齿轮间接触精度的评估结果。
2. 光学检测法:这种方法利用光学原理,通过测量齿轮表面的形貌特征来评估齿轮的间接触精度。
常用的光学检测方法包括摄像测量法、激光扫描法等。
这些方法可以对齿轮表面进行非接触式的测量,具有高精度和高效率的优点。
3. 声学检测法:这种方法利用声学原理,通过测量齿轮传动过程中产生的声音信号来评估齿轮的间接触精度。
根据声音信号的频谱特征,可以判断齿轮的接触状况以及存在的问题,如齿面磨损、齿距误差等。
4. 振动检测法:这种方法利用振动传感器对齿轮传动系统的振动信号进行监测和分析,以评估齿轮的间接触精度。
通过分析振动信号
的频谱特征和振动模态,可以判断齿轮的接触状况以及存在的问题,如齿面磨损、齿距误差等。
以上是常用的齿轮间接触精度检测方法,每种方法都有其优缺点和适用范围。
在实际应用中,可以根据具体情况选择合适的方法进行检测。
总结起来,齿轮间接触精度的检测是保证齿轮传动系统正常运行的重要环节。
通过合理选择和应用检测方法,可以及时发现齿轮的问题,并采取相应的措施进行修复和调整,从而保证齿轮传动系统的性能和寿命。
齿轮检测报告
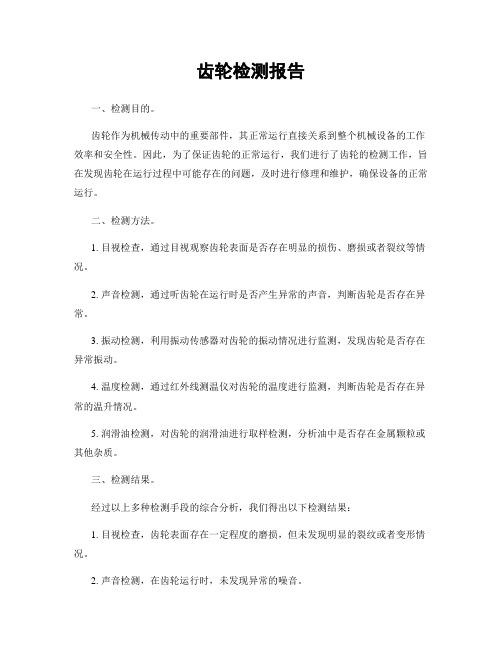
齿轮检测报告一、检测目的。
齿轮作为机械传动中的重要部件,其正常运行直接关系到整个机械设备的工作效率和安全性。
因此,为了保证齿轮的正常运行,我们进行了齿轮的检测工作,旨在发现齿轮在运行过程中可能存在的问题,及时进行修理和维护,确保设备的正常运行。
二、检测方法。
1. 目视检查,通过目视观察齿轮表面是否存在明显的损伤、磨损或者裂纹等情况。
2. 声音检测,通过听齿轮在运行时是否产生异常的声音,判断齿轮是否存在异常。
3. 振动检测,利用振动传感器对齿轮的振动情况进行监测,发现齿轮是否存在异常振动。
4. 温度检测,通过红外线测温仪对齿轮的温度进行监测,判断齿轮是否存在异常的温升情况。
5. 润滑油检测,对齿轮的润滑油进行取样检测,分析油中是否存在金属颗粒或其他杂质。
三、检测结果。
经过以上多种检测手段的综合分析,我们得出以下检测结果:1. 目视检查,齿轮表面存在一定程度的磨损,但未发现明显的裂纹或者变形情况。
2. 声音检测,在齿轮运行时,未发现异常的噪音。
3. 振动检测,齿轮的振动情况正常,不存在异常振动。
4. 温度检测,齿轮的温度在正常范围内,未发现异常的温升情况。
5. 润滑油检测,齿轮的润滑油中未检测到金属颗粒或其他异常杂质。
综上所述,齿轮经过本次检测,未发现严重的异常情况,但存在一定程度的磨损,建议在日常维护中加强对齿轮的润滑和保养工作,延长其使用寿命。
四、检测建议。
1. 加强润滑,定期对齿轮进行润滑保养,确保齿轮在运行时的正常润滑状态。
2. 定期检测,建议定期对齿轮进行检测,及时发现问题并进行修理,避免因齿轮故障导致设备损坏。
3. 注意负荷,在使用过程中,避免超负荷运行,以免对齿轮造成过大的压力和磨损。
4. 注意清洁,定期对齿轮进行清洁工作,避免灰尘和杂质进入齿轮内部,影响正常运行。
五、总结。
通过本次齿轮检测,我们对齿轮的运行状态有了全面的了解,并提出了相应的建议。
齿轮作为机械传动中的核心部件,其正常运行对设备的安全和效率有着重要的影响。
齿轮精度与检测技术手册

齿轮精度与检测技术手册
齿轮精度与检测技术手册
一、齿轮精度的定义
齿轮精度是指齿轮副在正常工作条件下能够符合预定的性能指标。
这
些性能指标包括噪声、振动、传动误差等等。
二、齿轮精度的影响因素
1.加工设备的精度
2.切削工具的质量
3.刀具的刃磨装置和磨削工艺
4.加工工艺参数的控制
三、齿轮精度的分类
1.精密齿轮:一般要求传动误差小于等于1′~2′,噪声级数不高于6级。
2.高精密齿轮:一般要求传动误差小于等于0.5′,噪声级数不高于5级。
3.超精密齿轮:一般要求传动误差小于等于0.3′,噪声级数不高于4级。
四、齿轮的检测方法
1.齿啮度测量法
2.重块法
3.网格法
4.光学测量法
5.声学测量法
五、齿轮的检测标准
1. JB/T5000-2007《齿轮检测规范》
2. GB/T10095-2008《齿轮用数字显示传动误差仪》
3. GB/T10096-2008《齿轮用数字显示噪声仪》
六、齿轮的质量控制
1.加工工艺的控制
2.检测方式的规范
3.配套检测设备的完善
4.数据分析和处理的及时性
以上是齿轮精度与检测技术手册的内容,希望对你有所帮助。
齿轮各类精度的考核项目

齿轮各类精度的考核项目
齿轮的精度是指齿轮加工及其配合精度。
在齿轮加工中,有以下几个主要的考核项目:
1. 齿轮的齿数:齿数是齿轮的重要参数之一,也是确定齿轮使用性能的重要指标。
2. 齿轮的模数:模数是齿轮齿数与齿距之比,也是齿轮加工时的重要参数。
3. 齿轮的齿面粗糙度:齿轮齿面粗糙度是用来描述齿轮齿面质量的指标,通常使用 Ra 值来表示。
4. 齿轮的齿向跳动:齿向跳动是指齿轮齿距与齿轮理论数值之间的差异,它会影响齿轮的传动精度和噪声。
5. 齿轮的轴向跳动:轴向跳动是指齿轮轴向之间的差异,主要影响齿轮的装配精度和工作稳定性。
6. 齿轮的中心距:中心距是指两个齿轮的轴线之间的距离,它是齿轮传动的基础参数之一。
7. 齿轮的啮合间隙:啮合间隙是指两个齿轮齿面之间的间隔,它会影响齿轮的相对位置和传动精度。
8. 齿轮的公差:公差是指允许的误差范围,齿轮加工中需要控制的公差包括齿距公差、齿形公差、齿厚公差等。
以上是齿轮加工中常见的一些精度考核项目,通过对这些项目的控制和检测,可以确保齿轮的加工精度和使用性能。
齿轮齿面接触精度的检测要求
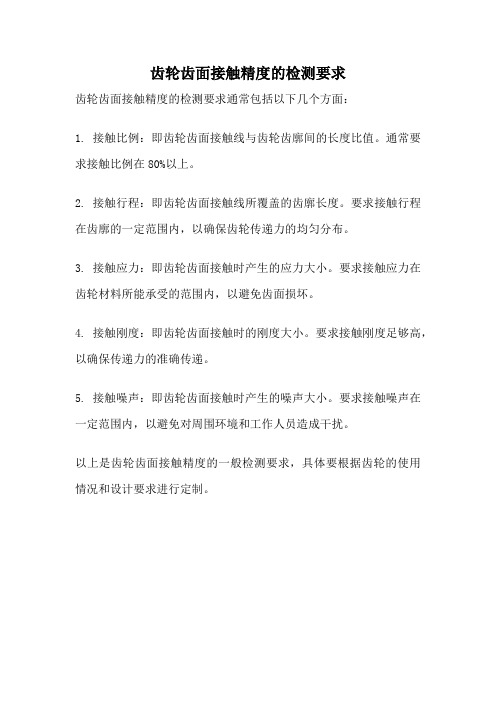
齿轮齿面接触精度的检测要求
齿轮齿面接触精度的检测要求通常包括以下几个方面:
1. 接触比例:即齿轮齿面接触线与齿轮齿廓间的长度比值。
通常要求接触比例在80%以上。
2. 接触行程:即齿轮齿面接触线所覆盖的齿廓长度。
要求接触行程在齿廓的一定范围内,以确保齿轮传递力的均匀分布。
3. 接触应力:即齿轮齿面接触时产生的应力大小。
要求接触应力在齿轮材料所能承受的范围内,以避免齿面损坏。
4. 接触刚度:即齿轮齿面接触时的刚度大小。
要求接触刚度足够高,以确保传递力的准确传递。
5. 接触噪声:即齿轮齿面接触时产生的噪声大小。
要求接触噪声在一定范围内,以避免对周围环境和工作人员造成干扰。
以上是齿轮齿面接触精度的一般检测要求,具体要根据齿轮的使用情况和设计要求进行定制。
[生活]齿轮传动精度的评定指标
![[生活]齿轮传动精度的评定指标](https://img.taocdn.com/s3/m/9ec040b50129bd64783e0912a216147917117e78.png)
齿轮传动精度的评定指标根据齿轮精度要求,把齿轮的误差分成影响传递准确性误差、影响运动平稳性误差、影响载荷分布均匀性误差和影响侧隙的误差。
并相应提出精度评定指标。
1、传递准确性的评定指标(1)、切向综合偏差ΔF i′ΔF i′是指被测齿轮与理想精确的测量齿轮单面啮合时,在被测齿轮一转内,实际转角与公称转角之差的总幅度值。
它以分度圆弧长计值。
它是是几何偏心、运动偏心加工误差的综合反映,也就是对齿轮径向误差和切向误差的综合反映,因而是评定齿轮传递运动准确性的最佳综合评定指标。
ΔF i′是在单面啮合综合检查仪(简称单啮仪)上进行测量的,单啮仪结构复杂,价格昂贵,在生产车间很少使用。
(2)、齿距累积总偏差ΔF p及齿距累积偏差ΔF pk(书185页图10-11、10-12)ΔF p是指在分度圆上,任意两个同侧齿面间的实际弧长与公称弧长之差的最大绝对值。
ΔF pk是指在分度圆上,任意K个齿距间的实际弧长与公称弧长之差的最大绝对值,K为从2到Z/8的整数(Z为被评定齿轮的齿数)。
规定ΔF pk是为了把齿距累积总偏差限制在局部圆周上。
齿距累积总偏差ΔF p反映了一转内任意个齿距的最大变化,它直接反映齿轮的转角误差,是几何偏心和运动偏心的综合作用结果,也就是对齿轮径向误差和切向误差的综合反映。
因而可以较为全面地反映齿轮的传递运动准确性,是一项综合性的评定项目。
但因为只在分度圆上测量,故不如切向综合误差反映的全面。
(3)、齿圈径向跳动△Fr△Fr是指齿轮一转范围内,测头在齿槽内与齿高中部双面接触,测头相对于齿轮轴线的最大变动量。
△Fr主要反映由于齿坯偏心引起的齿轮径向长周期误差。
可用齿圈径向跳动检查仪测量,测头可以用球形或锥形。
(4)、径向综合偏差△F i〞△F i〞是指与理想精确的测量齿轮双面啮合时,在被测齿轮一转内,双啮中心距的最大变动量。
当被测齿轮的齿廓存在径向误差及一些短周期误差(如齿形误差、基节偏差等)时,若它与测量齿轮保持双面啮合转动,其中心距就会在转动过程中不断改变,因此径向综合偏差△F i〞主要反映由几何偏心引起的径向误差及一些短周期误差。
- 1、下载文档前请自行甄别文档内容的完整性,平台不提供额外的编辑、内容补充、找答案等附加服务。
- 2、"仅部分预览"的文档,不可在线预览部分如存在完整性等问题,可反馈申请退款(可完整预览的文档不适用该条件!)。
- 3、如文档侵犯您的权益,请联系客服反馈,我们会尽快为您处理(人工客服工作时间:9:00-18:30)。
产生齿轮加工误差的主要因素:
1 几何偏心(e 几)
由齿轮齿圈基准轴线与齿轮工作时旋转轴线不重合造成。
几何偏心是径向误差的主要来源。
2 运动偏心(e 运)
由机床分度蜗轮加工误差即安装偏心引起的,是切向误差的主要来源。
3 机床传动链周期误差
4 滚刀制造误差与安装误差
单个齿轮评定指标:
一 影响运动准确性的项目('i F ∆ p F ∆ pk F ∆ r F ∆ ''i F ∆ w F ∆): 1 切向综合误差('i F ∆)
被测齿轮与理想精确的测量齿轮单面啮合检验时,被测齿轮转一转,实际转角与公差转角之差的总幅度值。
(转角误差) 单啮仪
2 齿距累积误差(p F ∆)和k 个 齿距累积误差(pk F ∆)
p F ∆分度圆上,任意两个同侧齿面间的实际弧长与公称弧长的最大差
值。
pk F ∆任意k 个齿距间······(2~z/2)
齿距仪、万能测齿仪、光学分度头 3 齿圈径向跳动(r F ∆) 齿轮一转范围内,侧头在齿槽内
相对于齿轮轴线最大变动量。
主要 由几何偏心引起。
4 径向综合误差('
i F ∆‘)
被测齿轮与理想精确齿轮双面啮合时,被测轮转一转,双啮中心距最大变动量。
双面啮合综合检测仪 5 公法线长度变动(w F ∆)
齿轮一周范围内,实际公法线长度最大值与最小值之差。
由运动偏心引起。
代表的公法线卡规或公法线千分尺
二 影响传动平稳性的误差项目('i f ∆ ''
i f ∆ f f ∆ pb f ∆ pt f ∆ f f β∆)
1 一齿切向综合误差('
i f ∆)
被测齿轮与理想精确的测量齿轮单面啮合时,在被测齿轮一齿距角内,实际转角与公称转角之差的最大幅度值。
单啮仪
2 一齿径向综合误差(''
i f ∆)
被测齿轮与理想精确的测量齿轮单面啮合时,在被测齿轮一齿距角内,双啮中心距的最大波动。
双啮仪
3 齿形误差(f f ∆)
齿轮端截面上,齿形工作部分内,包容实际齿形的两条设计齿形间的法向距离。
渐开线检测仪 4 基节偏差(pb f ∆) 实际基节与公称基节之差。
基节仪,万能测齿仪 5 齿距偏差(pt f ∆)
在分度圆上,实际齿距与公称齿距之差。
6 螺旋线波度误差(f f β∆)
宽斜齿轮齿高中部实际齿线波纹的最大幅度。
沿齿面发现方向记值。
用于评定轴向重合度βε>1.25的6级及高于6级精度的斜齿轮及人字齿轮的传动平稳性。
三 影响载荷分布均匀性的误差项目(F β∆ b F ∆ px F ∆) 1 齿向误差(F β∆)
分度圆柱面上,齿宽工作部分范围内,包容实际齿线的两条设计齿线之间的端面距离。
主要由齿坯断面跳动和刀架导轨倾斜引起。
斜齿轮,还受差动传动链调整误差影响。
齿向测量仪和导程仪 2 接触线误差(b F ∆)
基圆柱的切平面内,平行于公称接触线,并包容实际接触线的两条最近的直线间的法向距离。
包括方向误差和形状误差。
滚齿中,斜齿轮的接触线形状误差主要来源于滚刀误差和进给链误差。
能反映齿向和齿形误差。
渐开线或螺旋线检测仪 3 轴向齿距偏差(px F ∆)
在齿轮基准轴线平行而大约通过齿高中部的一条直线上,任意两个同侧齿面间实际距离与公称距离之差。
沿齿面法线方向计值。
在滚齿中,由滚齿机差动连的调整误差、刀架导轨的倾斜、齿坯端面跳动等引起。
光学机械仪器
四 影响侧隙的单个齿轮因素及检验项目 1 齿厚偏差(s E ∆)
分度圆柱面上,齿厚的实际值与公称值之差。
2 公法线平均长度偏差(m W E ∆)
齿轮一周范围内,公法线实际长度的平均值W 与其公称值W 之差。