综述报告——刻蚀简介
刻蚀简介
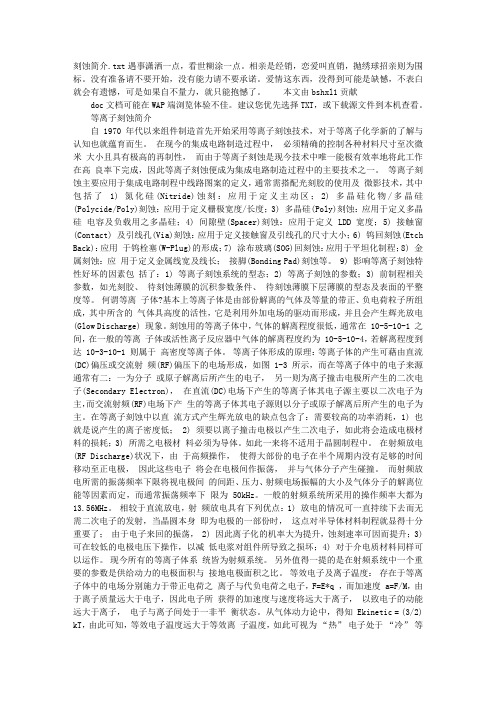
刻蚀简介.txt遇事潇洒一点,看世糊涂一点。
相亲是经销,恋爱叫直销,抛绣球招亲则为围标。
没有准备请不要开始,没有能力请不要承诺。
爱情这东西,没得到可能是缺憾,不表白就会有遗憾,可是如果自不量力,就只能抱憾了。
本文由bshxl1贡献doc文档可能在WAP端浏览体验不佳。
建议您优先选择TXT,或下载源文件到本机查看。
等离子刻蚀简介自 1970 年代以来组件制造首先开始采用等离子刻蚀技术,对于等离子化学新的了解与认知也就蕴育而生。
在现今的集成电路制造过程中,必须精确的控制各种材料尺寸至次微米大小且具有极高的再制性,而由于等离子刻蚀是现今技术中唯一能极有效率地将此工作在高良率下完成,因此等离子刻蚀便成为集成电路制造过程中的主要技术之一。
等离子刻蚀主要应用于集成电路制程中线路图案的定义,通常需搭配光刻胶的使用及微影技术,其中包括了1) 氮化硅(Nitride)蚀刻:应用于定义主动区;2) 多晶硅化物/多晶硅(Polycide/Poly)刻蚀:应用于定义栅极宽度/长度;3) 多晶硅(Poly)刻蚀:应用于定义多晶硅电容及负载用之多晶硅;4) 间隙壁(Spacer)刻蚀:应用于定义 LDD 宽度;5) 接触窗(Contact) 及引线孔(Via)刻蚀:应用于定义接触窗及引线孔的尺寸大小;6) 钨回刻蚀(Etch Back):应用于钨栓塞(W-Plug)的形成;7) 涂布玻璃(SOG)回刻蚀:应用于平坦化制程;8) 金属刻蚀:应用于定义金属线宽及线长;接脚(Bonding Pad)刻蚀等。
9) 影响等离子刻蚀特性好坏的因素包括了:1) 等离子刻蚀系统的型态;2) 等离子刻蚀的参数;3) 前制程相关参数,如光刻胶、待刻蚀薄膜的沉积参数条件、待刻蚀薄膜下层薄膜的型态及表面的平整度等。
何谓等离子体?基本上等离子体是由部份解离的气体及等量的带正、负电荷粒子所组成,其中所含的气体具高度的活性,它是利用外加电场的驱动而形成,并且会产生辉光放电(Glow Discharge) 现象。
刻蚀过程研究报告
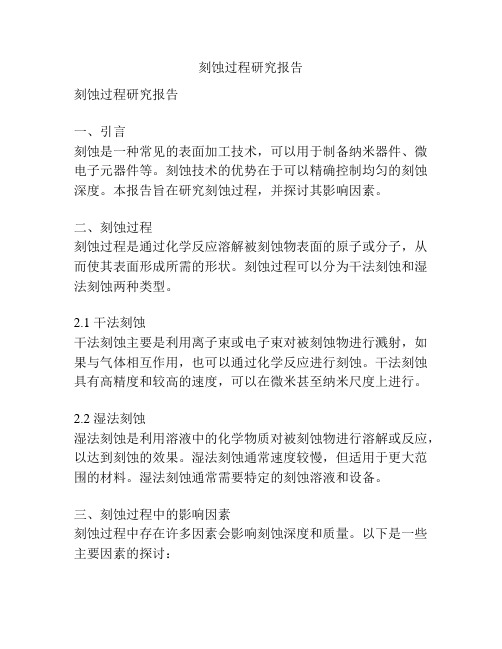
刻蚀过程研究报告刻蚀过程研究报告一、引言刻蚀是一种常见的表面加工技术,可以用于制备纳米器件、微电子元器件等。
刻蚀技术的优势在于可以精确控制均匀的刻蚀深度。
本报告旨在研究刻蚀过程,并探讨其影响因素。
二、刻蚀过程刻蚀过程是通过化学反应溶解被刻蚀物表面的原子或分子,从而使其表面形成所需的形状。
刻蚀过程可以分为干法刻蚀和湿法刻蚀两种类型。
2.1 干法刻蚀干法刻蚀主要是利用离子束或电子束对被刻蚀物进行溅射,如果与气体相互作用,也可以通过化学反应进行刻蚀。
干法刻蚀具有高精度和较高的速度,可以在微米甚至纳米尺度上进行。
2.2 湿法刻蚀湿法刻蚀是利用溶液中的化学物质对被刻蚀物进行溶解或反应,以达到刻蚀的效果。
湿法刻蚀通常速度较慢,但适用于更大范围的材料。
湿法刻蚀通常需要特定的刻蚀溶液和设备。
三、刻蚀过程中的影响因素刻蚀过程中存在许多因素会影响刻蚀深度和质量。
以下是一些主要因素的探讨:3.1 温度温度对刻蚀过程有显著影响。
当温度升高时,刻蚀速度会加快。
这是由于温度升高会加快化学反应速率,并减小化学物质的粘度,促进刻蚀剂在被刻蚀物上扩散。
3.2 浓度刻蚀溶液的浓度也是影响刻蚀过程的重要因素。
较高的浓度通常会导致较高的刻蚀速度。
然而,过高的浓度可能会导致不均匀的刻蚀或侵蚀。
3.3 溶液pH值溶液的pH值对刻蚀过程也有重要影响。
不同的材料在不同的pH范围内会有较好的刻蚀效果。
因此,控制刻蚀溶液的pH值对于获得所需的刻蚀效果至关重要。
3.4 刻蚀时间刻蚀时间是影响刻蚀深度的重要因素之一。
刻蚀时间较短可能导致刻蚀不充分,刻蚀时间较长可能导致刻蚀过渡到被刻蚀物内部,影响刻蚀质量和准确度。
四、结论刻蚀是一种重要的表面加工技术,可以精确控制被刻蚀物的形状和尺寸。
温度、浓度、溶液pH值和刻蚀时间是影响刻蚀过程的主要因素。
为了获得理想的刻蚀效果,需要合理调控改变这些因素。
刻蚀过程还有待于进一步研究和优化。
多晶刻蚀研究报告

多晶刻蚀研究报告一、背景介绍多晶刻蚀是一种常见的表面加工技术,用于改善材料的表面质量和性能。
它通过将材料暴露在化学溶液中,利用溶液中的反应物质与材料表面发生反应,以达到去除表面杂质、平整表面、改变表面形貌等目的。
二、刻蚀过程的原理多晶刻蚀是基于物理化学反应的刻蚀技术。
在刻蚀过程中,溶液中的刻蚀剂与材料表面发生反应,生成可溶性物质和产物。
这些可溶性物质会随着溶液的对流、扩散等运动形式从表面溶解,进而实现刻蚀的目的。
三、多晶刻蚀的适用材料多晶刻蚀适用于多种材料,包括但不限于: - 金属材料:铝、铜、钛、不锈钢等; - 半导体材料:硅、镓化合物等; - 光学材料:玻璃、石英等。
四、多晶刻蚀的刻蚀模式多晶刻蚀的刻蚀模式主要有两种:均匀刻蚀和选择性刻蚀。
1. 均匀刻蚀均匀刻蚀是指在刻蚀过程中,材料的所有部分被均匀地去除,从而获得平整的表面。
这种刻蚀模式适用于需要获得平整表面的应用场景,如光学镜面加工。
2. 选择性刻蚀选择性刻蚀是指在刻蚀过程中,某些材料的特定部分被选择性地去除,而其他部分相对保留。
这种刻蚀模式广泛应用于微电子器件的加工中,如制作晶体管、电容器等。
五、多晶刻蚀的影响因素多晶刻蚀的效果受多个因素影响,主要包括刻蚀剂、温度、溶液浓度、刻蚀时间等。
1. 刻蚀剂刻蚀剂是刻蚀过程中的关键因素之一。
常用的刻蚀剂包括酸性刻蚀剂、碱性刻蚀剂和混合刻蚀剂。
不同刻蚀剂对材料的刻蚀速率和表面形貌有着显著的影响。
2. 温度温度对刻蚀速率和刻蚀选择性有着明显的影响。
一般来说,温度升高会加快刻蚀速率,但过高的温度可能导致刻蚀剂的不稳定和材料的溶解过程。
3. 溶液浓度溶液浓度是影响刻蚀速率的重要因素。
溶液浓度越高,刻蚀速率越快。
但过高的溶液浓度可能导致刻蚀剂浓度过高,从而影响刻蚀的选择性。
4. 刻蚀时间刻蚀时间是控制刻蚀深度的因素。
刻蚀时间越长,刻蚀深度越大。
六、多晶刻蚀的应用领域多晶刻蚀技术广泛应用于以下领域:1. 微电子器件的制造多晶刻蚀在集成电路制造中起着重要的作用。
综述报告——刻蚀简介

微加工技术——刻蚀简介自从半导体诞生以来,很大程度上改变了人类的生产和生活。
半导体除了在计算机领域应用之外,还广泛地应用于通信、网络、自动遥控及国防科技领域。
本文主要介绍半导体制造工艺中的刻蚀工艺。
随着半导体制造大规模集成电路技术的发展,图形加工线条越来越细,硅片尺寸越来越大,对刻蚀工艺的要求也越来高。
因此,学习了解刻蚀工艺十分必要。
本文将主要从刻蚀简介、刻蚀参数及现象、干法刻蚀和湿法刻蚀四个方面进行论述。
1、刻蚀简介1.1 刻蚀定义及目的刻蚀就是用化学的、物理的或同时使用化学和物理的方法,有选择地把没有被抗蚀剂掩蔽的那一部分薄膜层除去,从而在薄膜上得到和抗蚀剂膜上完全一致的图形。
刻蚀的基本目的,是在涂光刻胶(或有掩膜)的硅片上正确的复制出掩膜图形[1]。
刻蚀,通常是在光刻工艺之后进行。
通过刻蚀,在光刻工艺之后,将想要的图形留在硅片上。
从这一角度而言,刻蚀可以被称之为最终的和最主要的图形转移工艺步骤。
在通常的刻蚀过程中,有图形的光刻胶层〔或掩膜层)将不受到腐蚀源显著的侵蚀或刻蚀,可作为掩蔽膜,保护硅片上的部分特殊区域,而未被光刻胶保护的区域,则被选择性的刻蚀掉。
其工艺流程示意图如下。
1.2 刻蚀的分类从工艺上分类的话,在半导体制造中有两种基本的刻蚀工艺:干法刻蚀和湿法腐蚀。
干法刻蚀,是利用气态中产生的等离子体,通过经光刻而开出的掩蔽层窗口,与暴露于等离子体中的硅片行物理和化学反应,刻蚀掉硅片上暴露的表面材料的一种工艺技术法[1]。
该工艺技术的突出优点在于,是各向异性刻蚀(侧向腐蚀速度远远小于纵向腐蚀速度,侧向几乎不被腐蚀),因此可以获得极其精确的特征图形。
超大规模集成电路的发展,要求微细化加工工艺能够严格的控制加工尺寸,要求在硅片上完成极其精确的图形转移。
任何偏离工艺要求的图形或尺寸,都可能直接影响产品性能或品质,给生产带来无法弥补的损害。
由于干法刻蚀技术在图形转移上的突出表现,己成为亚微米尺寸下器件刻蚀的最主要工艺方法。
半导体工艺原理----刻蚀工艺(2013513)(贵州大学)综述
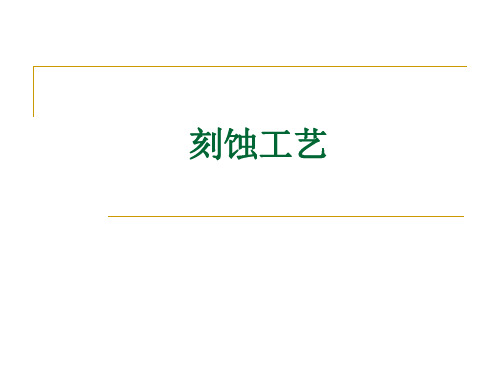
栅掩膜对准 Gate Mask Alignment
栅掩膜曝光 Gate Mask Exposure
Development/Hard Bake/Inspection
Etch Polysilicon刻蚀多晶硅
Etch Polysilicon 继续
Strip Photoresist 剥去光刻胶
材料 SiO2 腐蚀剂 HF(水中含49%),纯HF NHF4:HF(6:1),缓冲HF或BOE 注释 对硅有选择性,对硅腐蚀速率很慢,腐蚀速率依 赖于膜的密度,掺杂等因素 是纯HF腐蚀速率的1/20,腐蚀速率依赖于膜的密 度,掺杂等因素,不像纯HF那样使胶剥离 腐蚀速率主要依赖于薄膜密度,膜中O,H的含量
在10以上,Si3N4/Si的选择性在3-5, SiO2/ Si3N4的选 择性在2-4 。
(3)多晶硅化物(Polysilicon)的刻蚀
大多数金属对SiO2的附着力很差,并且可以使用扩散也能完
成自对准工艺,采用多晶硅来取代金属。但多晶硅的电阻还 是太大,所以在多晶硅的上方再加一层金属硅化物(Metal Silicide),以多金硅和硅化金属所组合而成的导电层,便
刻蚀选择比
刻蚀选择比是指同种腐蚀液对不同材料刻蚀速率的比 值。
举例
BOE对高饱和正硅酸乙酯磷硅酸玻璃的刻蚀速率是 6000 Å/min, 硅的刻蚀速率是 30 Å/min。
刻蚀均匀性
圆片上和圆片间的重复性 标准偏差不均匀性
最大最小均匀性
刻蚀剖面
刻蚀剖面
刻蚀技术分类:
温法腐蚀:进行腐蚀的化学物质是溶液; 干法腐蚀(一般称为刻蚀):进行刻蚀的化学物质是气体。
CF4/O2 HBr,Cl2,Cl2/HBr/O2 单晶硅 SiO2 与多晶硅的刻蚀剂相同 SF6,NF3,CF4/O2,CF4
刻蚀介绍.

聚合物(Polymer)的形成
聚合物是在刻蚀过程中由光刻胶中的碳并与刻蚀 气体和刻蚀生成物结合在一起而形成的;能否形 成侧壁聚合物取决于所使用的刻蚀气体类型。 聚合物的缺点:聚合物在刻蚀结束后难以去除;
在反应室的任何地方都有聚合物,影响纵向的刻
蚀速率,增加反应室的清洗工作。
8. 等离子体诱导损伤 等离子体诱导损伤有两种情况:
干法刻蚀的优点(与湿法腐蚀比)
1. 刻蚀剖面各向异性,非常好的侧壁剖面控制 2. 好的CD控制 3. 最小的光刻胶脱落或粘附问题 4. 好的片内、片间、批次间的刻蚀均匀性 5. 化学品使用费用低
干法刻蚀的缺点(与湿法腐蚀比)
1. 对下层材料的刻蚀选择比较差 2. 等离子体诱导损伤 3. 设备昂贵
光伏发电技术基础
山东理工职业学院
第六章
刻蚀
6.1 引 言
刻蚀的概念: 用化学或物理的方法有选择地去除硅片表面层材料的 工艺过程称为刻蚀。 刻蚀示意图:
Photoresist mask
Film to be etched
Photoresist mask
Protected film
(a) Photoresist-patterned substrate
(a)
4. 选择比 选择比:指在同一刻蚀条件下,刻蚀一种材料对另 一种材料的刻蚀速率之比。 高选择比: 意味着只刻除想要刻去的膜层材料,而 对其下层材料和光刻胶不刻蚀。 SiO2对光刻胶的选择比=(ΔTsio2/t1)/(ΔT胶/t1)b)t1时刻
5. 均匀性 刻蚀均匀性是指刻蚀速率在整个硅片或整批硅片上 的一致性情况。非均匀性刻蚀会产生额外的过刻蚀。 ARDE效应-微负载效应:Aspect Ratio Dependence Etching
刻蚀工艺介绍

刻蚀工艺介绍一、概述刻蚀工艺是一种常用的微纳加工技术,用于在半导体材料表面上制造微米级或纳米级的结构。
该工艺通过使用化学或物理方法,将材料表面的一部分物质移除,从而实现对材料形貌、形状和尺寸的精确控制。
刻蚀工艺在半导体、光学、生物医学、纳米科技等领域具有广泛的应用。
二、刻蚀分类根据刻蚀介质的不同,刻蚀工艺可分为湿法刻蚀和干法刻蚀两种。
湿法刻蚀是指将样品浸泡在特定溶液中,通过溶液中的化学反应来刻蚀样品表面;干法刻蚀则是在真空或气氛下,通过离子轰击或物理气相反应来刻蚀样品表面。
根据刻蚀模式的不同,刻蚀工艺又可分为均匀刻蚀和选择性刻蚀两种。
均匀刻蚀是指样品表面的物质均匀地被移除,形成平整的表面;选择性刻蚀则是指只有特定的材料被刻蚀,而其他材料不受影响。
三、湿法刻蚀湿法刻蚀是一种利用化学反应来刻蚀样品表面的方法。
常用的刻蚀液包括酸性、碱性和氧化性溶液。
酸性溶液可以刻蚀碱金属、半导体和金属材料,常见的有HF、HCl、H2SO4等;碱性溶液则可以刻蚀硅、氮化硅等材料,常见的有KOH、NaOH等;氧化性溶液则可以刻蚀金属和半导体,常见的有HNO3、H2O2等。
湿法刻蚀的优点是刻蚀速度快,刻蚀深度可控制,适用于大面积的刻蚀加工。
然而,湿法刻蚀的缺点是刻蚀剂对环境有一定的污染,并且刻蚀后需要进行清洗和处理。
四、干法刻蚀干法刻蚀是一种在真空或气氛中进行的刻蚀工艺,常用的刻蚀方式包括物理刻蚀和化学气相刻蚀。
物理刻蚀是利用离子轰击的方式来刻蚀样品表面,常用的设备有离子束刻蚀机和反应离子刻蚀机。
离子束刻蚀机通过加速和聚焦离子束,使其撞击样品表面,将表面物质溢出,从而实现刻蚀效果;反应离子刻蚀机则是将离子束与气体反应,生成化学反应产物,再通过气体流动将产物带走。
化学气相刻蚀是通过将刻蚀气体引入到反应室中,使其与样品表面发生化学反应,从而刻蚀样品表面。
干法刻蚀的优点是刻蚀速度快,刻蚀深度可控制,适用于高精度的刻蚀加工。
然而,干法刻蚀的缺点是设备复杂、昂贵,需要对真空系统进行维护和操作。
刻蚀设备与工艺介绍

刻蚀设备与工艺介绍刻蚀是一种重要的微纳加工技术,用于从薄膜或器件上去除材料以形成所需的图案和结构。
刻蚀可以用于制造各种微纳器件,如集成电路、光子学器件、传感器和微机电系统(MEMS)等。
在刻蚀过程中,通过控制刻蚀设备和工艺参数,可以实现所需的刻蚀深度、尺寸和形状。
刻蚀设备通常包括刻蚀机、刻蚀槽和辅助设备。
刻蚀机是刻蚀的核心设备,主要包括物理刻蚀机和化学刻蚀机。
物理刻蚀机主要通过物理方法,如离子轰击、物理挥发和物理溅射等,去除材料。
常见的物理刻蚀机有反应离子刻蚀(RIE)机、平行板刻蚀机和电子束刻蚀机等。
化学刻蚀机通过化学反应去除材料,常见的化学刻蚀机有浸没式刻蚀机和喷雾式刻蚀机等。
辅助设备包括真空系统、气体供给系统、温控系统和控制系统等,用于提供所需的刻蚀环境和参数控制。
刻蚀工艺是刻蚀的关键,它决定了刻蚀速率、选择比和表面质量等。
常见的刻蚀工艺包括湿刻蚀、干刻蚀和等离子体刻蚀等。
湿刻蚀是一种在液体介质下进行的刻蚀工艺,常用的刻蚀液有酸、碱和溶剂等。
湿刻蚀可以实现高选择性和较大的刻蚀深度,但其刻蚀速率较慢且难以控制。
干刻蚀是一种在气体介质中进行的刻蚀工艺,常用的气体有氧气、氮气和氟化物等。
干刻蚀速率较快且易于控制,但选择比较低且表面质量较差。
等离子体刻蚀是一种在等离子体条件下进行的刻蚀工艺,通过将气体电离产生等离子体,利用等离子体的化学反应和物理效应实现刻蚀。
等离子体刻蚀具有高选择性、较大的刻蚀速率和良好的表面质量,广泛应用于集成电路和光子学器件等领域。
刻蚀工艺的参数对刻蚀结果有重要影响,包括刻蚀气体、功率、压力、温度和刻蚀时间等。
不同的刻蚀工艺需要不同的参数组合,需要通过实验和优化来确定最佳参数。
刻蚀设备和工艺在微纳加工中起着至关重要的作用,它们决定了刻蚀的效率和质量。
随着微纳加工技术的不断发展,刻蚀设备和工艺将进一步提高,以适应更多元化的应用需求。
- 1、下载文档前请自行甄别文档内容的完整性,平台不提供额外的编辑、内容补充、找答案等附加服务。
- 2、"仅部分预览"的文档,不可在线预览部分如存在完整性等问题,可反馈申请退款(可完整预览的文档不适用该条件!)。
- 3、如文档侵犯您的权益,请联系客服反馈,我们会尽快为您处理(人工客服工作时间:9:00-18:30)。
微加工技术——刻蚀简介自从半导体诞生以来,很大程度上改变了人类的生产和生活。
半导体除了在计算机领域应用之外,还广泛地应用于通信、网络、自动遥控及国防科技领域。
本文主要介绍半导体制造工艺中的刻蚀工艺。
随着半导体制造大规模集成电路技术的发展,图形加工线条越来越细,硅片尺寸越来越大,对刻蚀工艺的要求也越来高。
因此,学习了解刻蚀工艺十分必要。
本文将主要从刻蚀简介、刻蚀参数及现象、干法刻蚀和湿法刻蚀四个方面进行论述。
1、刻蚀简介1.1 刻蚀定义及目的刻蚀就是用化学的、物理的或同时使用化学和物理的方法,有选择地把没有被抗蚀剂掩蔽的那一部分薄膜层除去,从而在薄膜上得到和抗蚀剂膜上完全一致的图形。
刻蚀的基本目的,是在涂光刻胶(或有掩膜)的硅片上正确的复制出掩膜图形[1]。
刻蚀,通常是在光刻工艺之后进行。
通过刻蚀,在光刻工艺之后,将想要的图形留在硅片上。
从这一角度而言,刻蚀可以被称之为最终的和最主要的图形转移工艺步骤。
在通常的刻蚀过程中,有图形的光刻胶层〔或掩膜层)将不受到腐蚀源显著的侵蚀或刻蚀,可作为掩蔽膜,保护硅片上的部分特殊区域,而未被光刻胶保护的区域,则被选择性的刻蚀掉。
其工艺流程示意图如下。
1.2 刻蚀的分类从工艺上分类的话,在半导体制造中有两种基本的刻蚀工艺:干法刻蚀和湿法腐蚀。
干法刻蚀,是利用气态中产生的等离子体,通过经光刻而开出的掩蔽层窗口,与暴露于等离子体中的硅片行物理和化学反应,刻蚀掉硅片上暴露的表面材料的一种工艺技术法[1]。
该工艺技术的突出优点在于,是各向异性刻蚀(侧向腐蚀速度远远小于纵向腐蚀速度,侧向几乎不被腐蚀),因此可以获得极其精确的特征图形。
超大规模集成电路的发展,要求微细化加工工艺能够严格的控制加工尺寸,要求在硅片上完成极其精确的图形转移。
任何偏离工艺要求的图形或尺寸,都可能直接影响产品性能或品质,给生产带来无法弥补的损害。
由于干法刻蚀技术在图形转移上的突出表现,己成为亚微米尺寸下器件刻蚀的最主要工艺方法。
在特征图形的制作上,已基本取代了湿法腐蚀技术。
对于湿法腐蚀,就是用液体化学试剂(如酸、碱和溶剂等)以化学的方式去除硅片表面的材料。
当然,在通过湿法腐蚀获得特征图形时,也要通过经光刻开出的掩膜层窗口,腐蚀掉露出的表面材料。
但从控制图形形状和尺寸的准确性角度而言,由于湿法刻蚀是各向同性刻蚀(侧向与纵向腐蚀速度相同),在形成特征图形方面,湿法腐蚀一般只被用于尺寸较大的情况(大于3微米)。
由于这一特点,湿法腐蚀远远没有干法刻蚀的应用广泛。
但由于它的高选择比和批量制作模式,湿法腐蚀仍被广泛应用在腐蚀层间膜、去除干法刻蚀残留物和颗粒等工艺步骤中。
干法刻蚀和湿法刻蚀的区别可以见如下示意图。
(a)湿法刻蚀的各向同性刻蚀剖面(b)干法刻蚀的各向异性刻蚀剖面从刻蚀材料上来分类的话,刻蚀主要可分为金属刻蚀、介质刻蚀、硅(多晶硅)刻蚀。
2、刻蚀参数及现象在刻蚀过程中,刻蚀速率、均匀性、选择比是刻蚀最主要的刻蚀参数。
以下我们将分别进行介绍。
2.1 刻蚀速率刻蚀速率是指刻蚀过程中去除表面材料的速度,通常用A/min表示。
通常对于量产,为提高产能,希望有较高的刻蚀速率。
在采用单片工艺的干法刻蚀设备中,这一参数是非常重要的。
刻蚀速率的计算公式如下[1]ER (etch rate)=△T/tER:刻蚀速率;△T:刻蚀量;t:刻蚀时间;刻蚀量单位为(A或µm),刻蚀时间单位为分钟(min)。
刻蚀速率由工艺和设备变量决定。
如,被刻蚀材料类型、刻蚀机的结构配置、使用的气体和工艺参数设置。
刻蚀速率通常正比于刻蚀剂的浓度。
硅片表面几何形状等因素不同,可造成不同的硅片之间不同的刻蚀速率。
如,被刻蚀的面积较大,则会消耗较多的刻蚀剂,也就是说大部分气相刻蚀基在等离子反应过程中被消耗了,刻蚀剂浓度下降,刻蚀速率就随之减慢。
反之,需刻蚀的面积较小,刻蚀速率就相对快些。
这种现象,被称为负载效应。
对于负载效应带来的刻蚀速率的变化,在有效的终点检测中起着重要的作用。
2.2 均匀性刻蚀速率的均一性,直接影响刻蚀整体的均匀性,是保证硅片刻蚀图形一致性的基础参数。
其计算公式如下[1]Ux=士Eave/2 (Emax-Em i n)*100%E:面内各点刻蚀速率的平均值;Emax:面内刻蚀速率最大值;Emin:面内刻蚀速率最小值;µx:被刻蚀材料x的速率均一性,Ux的单位为(士%)等离子密度的分布、刻蚀腔体的构造均会影响刻蚀速率的均一性。
一般而言,刻蚀速率的均一性受刻蚀腔体的限制,不同的刻蚀设备之间,在某一刻蚀速率的均一性上会有差别,体现出不同设备的性质。
2.3 选择比选择比,指在同一种刻蚀条件下,被刻蚀材料的刻蚀速率与另一种材料的刻蚀速率的比值。
如,对光刻胶的选择比计算公式,如下所示[1]:Sr=E f/ErSr:对光刻胶的选择比,E f::被刻蚀材料刻蚀速率,Er:光刻胶刻蚀速率选择比低可以低到1:1,意味着被刻材料和另一种材料被去除的一样快。
而选择比高可以高到100:1甚至100以上,意味着被刻蚀材料相对与另一种材料易被去除,而在去除过程中,不影响对另一种材料的刻蚀,将过刻蚀影响降致最低。
至于刻蚀条件中,应使用多高的选择比,则应根据被刻蚀膜膜质的情况、图形的结构和对所要刻蚀图形的形状、尺寸的要求,来选择适当的选择比。
选择比高,有利于刻蚀高宽比较高的图形。
但,对于多层膜结构的图形,在进行层间刻蚀时,则不适合使用选择比高的刻蚀条件。
基于以上基本参数,我们可以根据工艺的需要,在调整实际刻蚀工艺参数时,对这些基础刻蚀参数进行选择和组合,以获得满足需要的刻蚀图形。
另外,从刻蚀管理的角度而言,除如上三种基本刻蚀参数外,刻蚀的整体均匀性、腔体之间的工艺差、刻蚀中的颗粒污染、残留物、等离子损伤等,均属于刻蚀参数范畴。
它们将在刻蚀的整个工艺评价中,被逐一确认。
只有既达到刻蚀参数的要求,又能刻蚀出符合规格的图形,这样的刻蚀条件,才能被应用在实际的量产中。
3、干法刻蚀3.1 干法刻蚀原理干法刻蚀,是利用气态中产生的等离子体,通过经光刻而开出的掩蔽层窗口,与暴露于等离子体中的硅片行物理和化学反应,刻蚀掉硅片上暴露的表面材料的一种工艺技术法。
所谓的等离子体,是宇宙中常见的物质,其中包含了中性的粒子、离子和电子,它们混合在一起,表现为电中性。
在干法刻蚀中,气体中的分子和原子,通过外部能量的激发,形成震荡,使质量较轻的电子脱离原子的轨道与相邻的分子或原子碰撞,释放出其他电子,在这样的反复过程中,最终形成气体离子与自由活性激团。
而干法刻蚀,则利用了气体等离子体中的自由活性激团与离子,与被刻蚀表面进行反应,以此形成最终的特征图形[2]。
3.2 干法刻蚀过程干法刻蚀的过程如下图所示。
干法刻蚀时,在样品表面同时发生物理作用和化学作用。
反应腔体内气体等离子体中的离子,在反应腔体的扁压作用下,对被刻蚀的表面进行轰击,形成损伤层,从而加速了等离子中的自由活性激团在其表面的化学反应,经反应后产生的反应生成物,一部分被分子泵从腔体排气口排出,一部分则在刻蚀的侧壁上形成淀积层。
干法刻蚀就是在自由活性激团与表面反应和反应生成物不断淀积的过程中完成的。
离子轰击体现了干法刻蚀的各向异性,而由于侧壁的淀积,则很好的抑制了自由活性激团反应时,同性作用对侧壁的刻蚀[3]。
正因为干法刻蚀这一物理反应和化学反应相结合的独特方式,在各向异性和各向同性的相互作用下,可以精确的控制图形的尺寸和形状,体现出湿法刻蚀无法比拟的优越性,成为亚微米图形刻蚀的主要工艺技术之一。
刻蚀时,刻蚀气体主要分为惰性系、腐蚀系、氧化系以及C,F系等几类。
刻蚀反应,包括了物理反应和化学反应。
根据等离子体中自由活性激团与主要表面材料的刻蚀反应,其基本化学反应式可归纳为如下几种。
SiO2: 3SiO2+4CF3*→3SiF4 ↑+2 CO↑+2C O2 ↑Si: Si+4F*→S iF4↑Si+4C1*→SiC l4↑W: W+6F*→WF6↑A1: A1+3C1*→A1C13↑当然,在实际的刻蚀过程中,根据加工工序的要求,以及被刻蚀图形的膜层结构,还包括了上述以外的其他材料。
如金属刻蚀中的Ti, TiN;金属配线层之间的有机或无机silica;钝化刻蚀中的SiON3;以及其他介质膜刻蚀中的SiN等。
3.3 干法刻蚀应用分类干法刻蚀,主要应用在图形形成工艺中。
随着在生产制造上的广泛应用,针对图形加工,干法刻蚀可细致的被分为:有图形刻蚀和无图形刻蚀两大类。
大部分干法刻蚀工艺,涉及有图形刻蚀。
而对于部分无图形刻蚀,仍然可以通过干法刻蚀来完成。
如LDD侧壁、孔塞、光刻胶的剥离。
虽然无图形刻蚀是湿法腐蚀的项目之一,但根据生产工艺的需要,在部分关键的无图形刻蚀中,均采用了干法刻蚀技术,如LDD的侧壁刻。
LDD侧壁的形状和尺寸的好坏,会直接影响器件的特性,用干法刻蚀进行刻蚀的控制是最好的选择。
加上湿法腐蚀对于氧化膜的腐蚀作用和各向同性特征,是无法形成LDD侧壁的特殊形貌的。
另外对光刻胶的剥离则是另一个干法刻蚀的例子。
根据各加工工序、被刻蚀材料膜质的不同,干法刻蚀工艺又可以被细分成如下几项:a.硅基板刻蚀(silicon etch)b.氮化膜刻蚀(SiN etch)。
c.金属多晶硅刻蚀(W-silicide etch)d.多晶硅刻蚀(poly-silicon etch)。
e.金属刻蚀(metal etch)f.金属钝化刻蚀(SioN3 etch )g.去胶刻蚀(Ash etch)综上所述,干法刻蚀根据被刻蚀的材料类型,可系统的分成三种。
即金属刻蚀、介质刻蚀和硅刻蚀。
介质刻蚀是用于介质材料的刻蚀,如二氧化硅、氮化硅等。
上述涉及介质的刻蚀,均属于介质刻蚀。
硅刻蚀(包括多晶硅),应用于需要去除硅的场合,如刻蚀多晶硅晶体管栅和硅槽电容等。
金属刻蚀,则主要在金属层上去掉铝合金复合层,制作出互连线。
3.4 干法刻蚀设备讨论干法刻蚀设备,先要介绍一下等离子刻蚀反应器。
等离子刻蚀反应器有以下几种类型:圆桶式等离子体反应器、平板(平面)反应器、顺流刻蚀系统、三极平面反应器、离子铣、反应离子刻蚀(RIE )、高密度等离子体刻蚀机[5]。
从干法刻蚀等离子形成的方式而言,干法刻蚀方式主要包括有电极放电和无电极放电两大类。
有电极放电主要有:RIE即Reactive Ion Etch(高周波、低周波、2周波、相位制御)。
无电极放电主要为:诱导放电、U波、ECR-Electron Cycbrton Resonance[6]。
所谓低周波,是指采用400kHz低周波的放电模式。
上下部电极共用一个RF 电源,离子追随底周波电界Vpp运动,可获得较大的离子能量,适用于氧化膜刻蚀。
所谓2周波,则指在上部电极加载27MHz的周波,产生中密度的等离子体,在下部电极加载800kHz的周波,制御离子能量。