钛管焊接工艺
工业钛管焊接施工工艺_secret
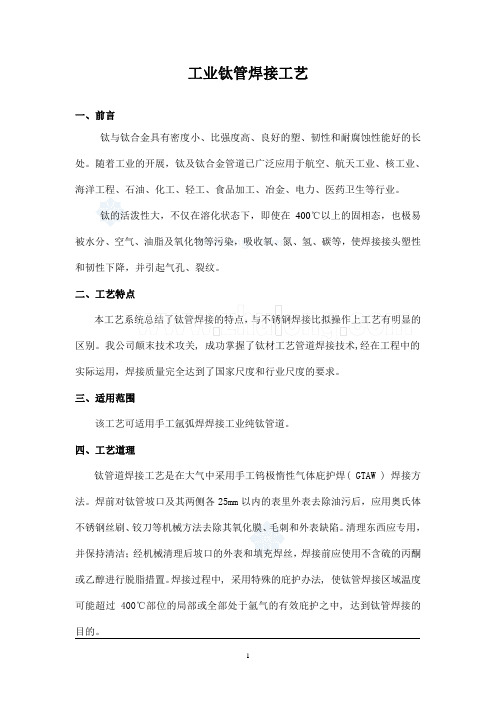
工业钛管焊接工艺一、前言钛与钛合金具有密度小、比强度高、良好的塑、韧性和耐腐蚀性能好的长处。
随着工业的开展,钛及钛合金管道已广泛应用于航空、航天工业、核工业、海洋工程、石油、化工、轻工、食品加工、冶金、电力、医药卫生等行业。
钛的活泼性大,不仅在溶化状态下,即使在400℃以上的固相态,也极易被水分、空气、油脂及氧化物等污染,吸收氧、氮、氢、碳等,使焊接接头塑性和韧性下降,并引起气孔、裂纹。
二、工艺特点本工艺系统总结了钛管焊接的特点,与不锈钢焊接比拟操作上工艺有明显的区别。
我公司颠末技术攻关, 成功掌握了钛材工艺管道焊接技术,经在工程中的实际运用,焊接质量完全达到了国家尺度和行业尺度的要求。
三、适用范围该工艺可适用手工氩弧焊焊接工业纯钛管道。
四、工艺道理钛管道焊接工艺是在大气中采用手工钨极惰性气体庇护焊( GTAW ) 焊接方法。
焊前对钛管坡口及其两侧各25mm以内的表里外表去除油污后,应用奥氏体不锈钢丝刷、铰刀等机械方法去除其氧化膜、毛刺和外表缺陷。
清理东西应专用,并保持清洁;经机械清理后坡口的外表和填充焊丝,焊接前应使用不含硫的丙酮或乙醇进行脱脂措置。
焊接过程中, 采用特殊的庇护办法, 使钛管焊接区域温度可能超过400℃部位的局部或全部处于氩气的有效庇护之中, 达到钛管焊接的目的。
五、工艺流程及操作要点5.1 工艺流程施工筹办→材料验收→划线查验→下料及坡口加工→坡口周边措置→焊件组对→焊接→焊缝外不雅查抄→焊缝P T 、RT探伤→预制管段水压试验→排水、枯燥→管口封闭运输→现场组装。
5.2 操作要点施工筹办A.焊接工艺评定及焊工测验施工前,应按照设计文件及现场设备、工业管道焊接工程施工及验收尺度GB50236的要求进行焊接工艺评定试验,按照评定合格的工艺,编制焊接工艺指导书,指导焊工培训、测验,取得测验合格证的焊工, 方可参加焊接施工。
B.场地筹办预制场合内应安排在室内,保持环境枯燥、清洁、无尘埃、无黑色金属的打磨、切割和焊接施工,而且具有焊接材料的贮存、清洗设施和良好的施焊条件;现场焊接时,应有防风和防雨雪的办法,并应保持相对湿度在 90%以下。
工业钛管焊接工法

工业钛管焊接工法工业钛管焊接工法引言:在工业领域中,钛管的使用越来越普遍。
钛具有优异的耐腐蚀性、高强度、低密度等特点,使其广泛应用于航空航天、化工、医疗等领域。
然而,由于其特殊性质,钛的焊接工艺相对较为复杂。
本文将介绍工业钛管焊接的一些常用工法,并探讨其特点和注意事项。
一、焊接工法及特点:1. 氩弧焊接法:氩弧焊接法是目前工业钛管焊接最常用的方法之一。
其特点是焊接过程稳定,气氛保护良好,焊接口质量较高。
在氩气保护下,采用直流或交流电弧进行焊接,通过熔化焊条和基材表面形成液态金属池,然后使其冷却凝固,形成焊接接头。
氩弧焊接法的优点是焊接接头质量高,焊缝表面光滑,适用于薄壁钛管的焊接。
2. 等离子焊接法:等离子焊接法是一种高功率能量集中区的焊接方法,适用于较厚且壁厚不均匀的钛管。
等离子焊接利用高能电弧产生的等离子体来提供熔化焊条和基材所需的热量,通过高功率电弧激发成气体离子,再让离子与零件表面的金属原子相撞击,使其发生热交换并熔化。
这种焊接方法可以在大功率下实现高速焊接,适用于大规模焊接作业。
3. 焊锡焊接法:焊锡焊接法适用于工业钛管与其他材料的连接。
该方法主要是先在钛管和另一种金属表面涂敷焊锡,然后通过加热使焊锡熔化并与两种金属融合。
焊锡焊接法具有焊接速度快、连接强度高、气氛保护良好等优点。
然而,由于钛的反应性较强,焊锡焊接时需要注意选择化学性能符合要求的焊锡。
二、焊接注意事项:1. 气氛保护:钛具有强烈的化学性质,在高温条件下非常容易氧化。
因此,在焊接过程中必须采取有效的气氛保护措施,以保持焊接区域的稳定与纯净。
常用的气氛保护方法包括氩气保护和真空保护。
选择气氛保护方法时需要考虑工艺要求和成本效益。
2. 清洁作业环境:焊接区域应保持干净、整洁,避免灰尘、油污等杂质的污染。
因为这些杂质会在焊接过程中生成气体,影响焊缝质量和气氛保护效果。
3. 控制焊接温度:对于工业钛管来说,焊接温度是十分关键的因素。
钛管胀接加焊接工艺

钛管胀接密封焊工艺考虑连接的强度,密封性,减缓缝隙腐蚀,便于制造加工等要求,换热管与管板的连接一般采用胀接加密封焊的连接结构。
由于钛及其合金屈强比大(在退火状态下σ0.2/σb=0.7~o.9),延伸率相对较低,选用的管壁又较薄,胀按时管端轻易发生裂纹。
为降低管端的减薄量和防止产生裂纹,同普通钢管胀接相比,应选用较小的间隙,较低的胀管率,严格控制管子伸出管板表面的长度。
在φ38×1.2钛管胀接中,控制胀管间隙在0.3~0.4毫米,胀管率(管子内径的胀大值对管孔直径的相对百分率)控制不超过0.5%,管子伸出管板表面不大于1.5毫米,经外观查看及试压证实,胀接质量合格。
密封焊时应严格清洗管板及管端的待焊部位,控制管端伸出管板高度(φ38×1.2钛管伸出高度0.5~1.5毫米),采用不填加焊丝的自动或半自动氩弧自熔焊,这样得出的焊缝丰满,高度整齐,成形光滑美观,呈银白色或淡稻黄色的金属光泽。
工业纯钛的使用状态为退火状态,用于工业纯钛设备的焊丝,一般要选用比母材纯度高一个级别的工业纯钛焊丝,TA2多用于换热管。
一、焊接技术要求钛焊缝表面不得有气孔、咬边、裂纹等表面缺陷,钛焊缝(包括热影响区)表面以银白色、金黄色、局部少量蓝色为合格。
二、钛材焊接所面临的影响2.1 气体及杂质污染的问题工业纯钛具有良好的耐蚀性、塑性、韧性、焊接性和较高的比强度,其熔点高达1672℃,在常温下,由于钛表面致密氧化膜的作用,使其性能很稳定。
但在高温下具有很强的化学活泼性,随着温度的升高,其化学活泼性会迅速增强。
在焊接过程中,液态熔滴和熔池金属具有强烈吸收氢、氧、氮的作用,而且在固态下,这些气体已与其发生作用。
随着温度的升高,钛吸收氢、氧、氮的能力也随之明显上升,大约在250℃左右开始吸收氢(生成的TiH2强度很低,对钛的机械性能产生严重影响),从400℃开始吸收氧(提高钛及钛合金的硬度和强度,使塑性却显著降低),从600℃开始吸收氮(形成脆硬的氮化钛(riN)而且氮与钛形成间隙固溶体时所引起的晶格歪挪程度,比氧引起的后果更为严重),这些气体被吸收后,将会直接引起焊接接头脆化,是影响焊接质量的极为重要的因素。
钛管焊接方法

钛管焊接方法一、钛管焊接的那些事儿钛管焊接可真是个有趣又有点小复杂的事儿呢。
咱先来说说钛这个材料哈,钛的化学性质比较活泼,在高温下特别容易和空气中的氧、氮、氢等元素发生反应,这就给焊接带来了不少挑战。
钛管焊接的方法有不少种。
比如说手工钨极氩弧焊,这可是个挺常用的方法。
在进行手工钨极氩弧焊的时候,要特别注意保护气体的流量和纯度。
氩气作为保护气体,就像是钛管焊接时的小卫士,得让它好好地把焊接区域给保护起来,防止钛管被那些坏家伙——氧啊氮啊之类的元素入侵。
而且焊接的时候,焊工师傅的手法得特别稳,就像拿着绣花针一样,稍微抖一下,可能焊接的质量就会受到影响。
还有等离子弧焊也能用于钛管焊接呢。
这种焊接方法的能量比较集中,焊接速度相对来说可以快一些。
不过这就对设备的要求比较高啦,设备要是不给力,那可不行。
而且在操作的时候,对焊接参数的控制要特别精准,像电流、电压、焊接速度这些参数,就像是一个个小机关,哪一个没调好,都可能影响到最后的焊接效果。
激光焊接也开始逐渐应用于钛管焊接了。
激光焊接的优点就是焊缝窄、热影响区小。
但是呢,激光焊接设备的成本可不低,而且对操作人员的技术要求也很高。
操作人员得像个技术高超的魔法师一样,熟练地操控着激光设备,才能让钛管焊接得又好又漂亮。
在钛管焊接之前,还有一些准备工作可不能马虎。
首先得把钛管的接口处理干净,不能有油污、铁锈之类的杂质。
这就好比我们要在一块干净的画布上画画一样,如果画布脏兮兮的,那画出来的画肯定不好看。
而且钛管的对接要非常精准,要是对接歪了,那焊接出来的钛管肯定也是歪歪扭扭的,不符合要求。
钛管焊接完成之后呢,还得进行一些检验工作。
像外观检验啊,看看焊缝是不是均匀、美观,有没有气孔、裂纹之类的缺陷。
如果有,那就得重新焊接啦。
还有无损检测,这就像是给焊接好的钛管做个体检,看看内部有没有什么隐藏的问题。
反正就是说呢,钛管焊接虽然有不少挑战,但是只要我们掌握了正确的方法,精心准备,认真操作,再加上严格的检验,就能够把钛管焊接得很好,让钛管在各种工程和设备中发挥它应有的作用啦。
工业钛管焊接施工工法(2)
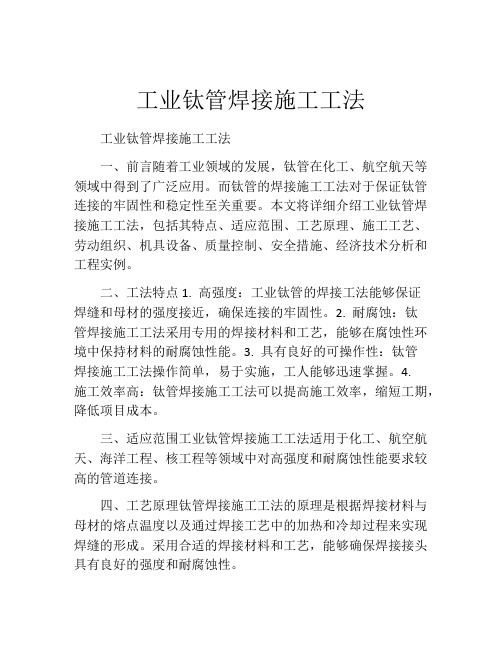
工业钛管焊接施工工法工业钛管焊接施工工法一、前言随着工业领域的发展,钛管在化工、航空航天等领域中得到了广泛应用。
而钛管的焊接施工工法对于保证钛管连接的牢固性和稳定性至关重要。
本文将详细介绍工业钛管焊接施工工法,包括其特点、适应范围、工艺原理、施工工艺、劳动组织、机具设备、质量控制、安全措施、经济技术分析和工程实例。
二、工法特点1. 高强度:工业钛管的焊接工法能够保证焊缝和母材的强度接近,确保连接的牢固性。
2. 耐腐蚀:钛管焊接施工工法采用专用的焊接材料和工艺,能够在腐蚀性环境中保持材料的耐腐蚀性能。
3. 具有良好的可操作性:钛管焊接施工工法操作简单,易于实施,工人能够迅速掌握。
4.施工效率高:钛管焊接施工工法可以提高施工效率,缩短工期,降低项目成本。
三、适应范围工业钛管焊接施工工法适用于化工、航空航天、海洋工程、核工程等领域中对高强度和耐腐蚀性能要求较高的管道连接。
四、工艺原理钛管焊接施工工法的原理是根据焊接材料与母材的熔点温度以及通过焊接工艺中的加热和冷却过程来实现焊缝的形成。
采用合适的焊接材料和工艺,能够确保焊接接头具有良好的强度和耐腐蚀性。
五、施工工艺1. 准备工作:包括材料准备、焊接设备检查、施工区域准备等。
2. 管道预热:根据钛管的规格和焊接材料的要求,进行适当的预热。
3. 焊接参数设定:根据钛管的材质和规格,设置合适的焊接参数。
4. 焊接操作:根据焊接程序进行焊接操作,保证焊接接头的质量。
5. 焊后处理:包括焊缝清理、焊后加热处理等。
6. 检验验收:对焊接接头进行非破坏性检验和力学性能测试,确保施工质量。
六、劳动组织钛管焊接施工工法需要合理组织施工人员,根据施工计划和要求分工合作,以确保施工进度和质量。
七、机具设备钛管焊接施工工法需要的机具设备包括焊接设备(例如氩弧焊机、等离子焊机)、焊接材料(例如钛焊丝)、焊接工具(例如焊接钳、切割机)等。
八、质量控制钛管焊接施工工法的质量控制包括对焊接设备的检查和保养、焊接材料的质量检验、焊接工艺的参数控制、焊接接头的检验和验收等。
钛管焊接方法和技巧

钛管焊接方法和技巧
钛管焊接是一项复杂的工艺,需要特定的方法和技巧来确保焊接质量。
以下是钛管焊接的一些常见方法和技巧:
1. 选择合适的焊接方法,常见的钛管焊接方法包括TIG(氩弧焊)、MIG(气体保护焊)和电弧焊。
TIG焊接通常被认为是最适合焊接钛管的方法,因为它可以提供高质量的焊缝并且对操作者的技能要求较高。
2. 准备工作,在进行钛管焊接之前,需要对管道进行充分的清洁和准备工作。
这包括去除表面的氧化物和油脂,以确保焊接区域的干净和无污染。
3. 控制焊接参数,钛对氧氮等气体的敏感性很高,因此在焊接过程中需要严格控制焊接参数,如电流、电压、气体流量等,以确保焊接区域的惰性气氛和温度。
4. 使用合适的填充材料,选择合适的填充材料对于钛管焊接至关重要。
通常使用纯钛或钛合金作为填充材料,以确保焊缝与基材具有相似的性能。
5. 控制焊接速度,在进行钛管焊接时,需要控制焊接速度,以确保焊接区域的热输入均匀,避免产生裂纹或变形。
6. 质量检测,完成焊接后,需要进行质量检测,包括对焊缝进行X射线或超声波检测,以确保焊接质量符合标准要求。
总的来说,钛管焊接需要严格控制焊接参数,选择合适的焊接方法和填充材料,并进行质量检测,以确保焊接质量和安全性。
同时,操作人员需要具备专业的焊接技能和经验,以确保钛管焊接的顺利进行。
钛合金管道焊接工艺流程
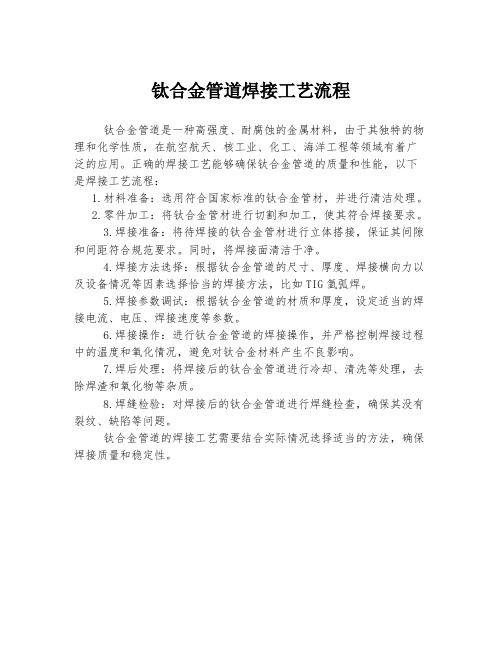
钛合金管道焊接工艺流程
钛合金管道是一种高强度、耐腐蚀的金属材料,由于其独特的物理和化学性质,在航空航天、核工业、化工、海洋工程等领域有着广泛的应用。
正确的焊接工艺能够确保钛合金管道的质量和性能,以下是焊接工艺流程:
1.材料准备:选用符合国家标准的钛合金管材,并进行清洁处理。
2.零件加工:将钛合金管材进行切割和加工,使其符合焊接要求。
3.焊接准备:将待焊接的钛合金管材进行立体搭接,保证其间隙和间距符合规范要求。
同时,将焊接面清洁干净。
4.焊接方法选择:根据钛合金管道的尺寸、厚度、焊接横向力以及设备情况等因素选择恰当的焊接方法,比如TIG氩弧焊。
5.焊接参数调试:根据钛合金管道的材质和厚度,设定适当的焊接电流、电压、焊接速度等参数。
6.焊接操作:进行钛合金管道的焊接操作,并严格控制焊接过程中的温度和氧化情况,避免对钛合金材料产生不良影响。
7.焊后处理:将焊接后的钛合金管道进行冷却、清洗等处理,去除焊渣和氧化物等杂质。
8.焊缝检验:对焊接后的钛合金管道进行焊缝检查,确保其没有裂纹、缺陷等问题。
钛合金管道的焊接工艺需要结合实际情况选择适当的方法,确保焊接质量和稳定性。
钛管道焊接工艺指导书
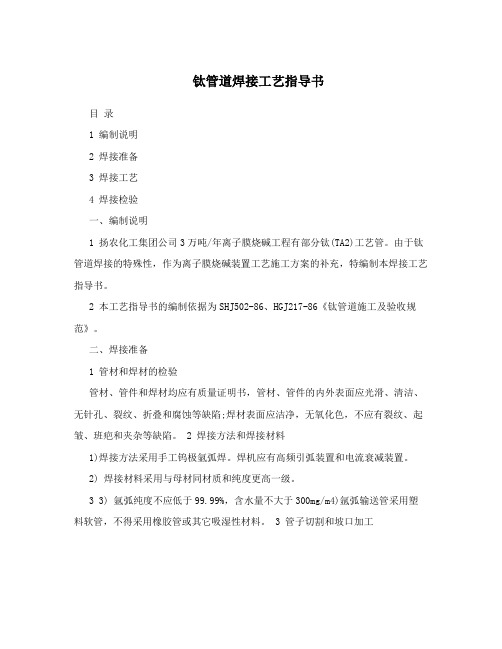
钛管道焊接工艺指导书目录1 编制说明2 焊接准备3 焊接工艺4 焊接检验一、编制说明1 扬农化工集团公司3万吨/年离子膜烧碱工程有部分钛(TA2)工艺管。
由于钛管道焊接的特殊性,作为离子膜烧碱装置工艺施工方案的补充,特编制本焊接工艺指导书。
2 本工艺指导书的编制依据为SHJ502-86、HGJ217-86《钛管道施工及验收规范》。
二、焊接准备1 管材和焊材的检验管材、管件和焊材均应有质量证明书,管材、管件的内外表面应光滑、清洁、无针孔、裂纹、折叠和腐蚀等缺陷;焊材表面应洁净,无氧化色,不应有裂纹、起皱、班疤和夹杂等缺陷。
2 焊接方法和焊接材料1)焊接方法采用手工钨极氩弧焊。
焊机应有高频引弧装置和电流衰减装置。
2) 焊接材料采用与母材同材质和纯度更高一级。
3 3) 氩弧纯度不应低于99.99%,含水量不大于300mg/m4)氩弧输送管采用塑料软管,不得采用橡胶管或其它吸湿性材料。
3 管子切割和坡口加工1) 管子切割采用机械切割或采用机械切割时其表面不得有氧化层等离子弧割。
采用等离子弧切割时要用机械方法(砂轮)除去油污染层,管子加工应采用清洁的专用工具。
2) 坡口形式为?型。
3) 管子切口及坡口表面应平整,不得有裂纹、重皮,并清除毛刺、凸凹、缩口、熔渣及氧化物等。
切口平面最大倾斜度偏差不得超过2.5mm。
4 坡口及焊丝的清理1) 坡口及其两侧各25mm以内外表面清除油污后,用细锉或奥氏体不锈钢丝刷等方法清除其氧化膜、毛刺等缺陷。
清洁采用清洁的专用工具。
2) 经机械清理后的表面,焊前使用不含硫的丙酮或乙醇进行脱脂处理。
脱脂严禁使用氧化物容剂,并避免将棉质纤维附于坡口表面。
3) 焊丝的清理方法与母材焊口相同。
5 焊口组对1) 焊口组对间隙0~1mm。
2) 管子组对应做到内壁平齐,对口挡边量不得超过0.2mm。
3) 定位焊采用与正式焊接相同的焊接材料和焊接工艺,其焊缝长度一般为10mm左右,高度不超过1.3mm。
- 1、下载文档前请自行甄别文档内容的完整性,平台不提供额外的编辑、内容补充、找答案等附加服务。
- 2、"仅部分预览"的文档,不可在线预览部分如存在完整性等问题,可反馈申请退款(可完整预览的文档不适用该条件!)。
- 3、如文档侵犯您的权益,请联系客服反馈,我们会尽快为您处理(人工客服工作时间:9:00-18:30)。
钛管焊接工艺1前言PTA装置是扬子乙烯二期工程的重点项目。
该装置生产能力为年产45万吨精对苯二甲酸,它是同期同西德吉玛公司引进的54万吨/年聚脂装置的配套装置,也是国内最大的聚脂原料生产装置。
由于生产条件苛刻,工艺复杂,整个装置设备、管道多(147593米,其中不锈钢管道占全部的1/4),使用材料特殊(如钛材)。
因此给施工带来较大难度,尤为突出的是钛管的焊接施工。
该装置的钛管管径φ21~508mm,壁厚l.5~l4mm,近900m,约500道焊缝,其中可通过预制完成的约400道,需现场焊接的约100道。
焊接质量要按鲁奇公司的标准检查、验收。
技术难度大,特别是钛管的全位置焊接,国内施工经验不多。
为确保焊接质量和施工工期,我公司进行了一系列的焊接工艺试验,制定了合理的施工方案,特别对钛管的全位置焊接进行了技术攻关,并获得成功。
2技术条件2.1钛管的设计技术条件与标准2.1.1设计技术条件2.1.1.1管材及配件材质:DIN178503.7025,3.7035,3.7055.其化学成分如下表:2.1.1.2管材规格:φ508×4.5,φ408×14,φ26.9×l.5,φ21.3×2.6。
2.1.1.3钛管工作条件;温度224℃,压力2.5MPa,介质醋酸,溴化物。
2.1.1.4管道质量要求:焊接接头系数1,焊缝射线检验100%,水压试验压力3.75MPa,气密性试验压力0.625MPa2.1.2技术标准2.1.2.1管道工程钛材焊接规范LON1015E2.1.2.2钛管施工技术条件伍德公司标准2.1.2.3钛管施工及验收规范SHJ502-862.2 焊接特点钛管焊接是利用惰性气体对焊接区进行有效保护的TiG焊接工艺。
由于钛材具有特殊的物理化学特性,因而其焊接工艺与其它金属存在较大差异。
焊接时必须保证:(1)焊接区金属在250℃以上不受活性气体N,0、H及有害杂质元素C,Fe,Mn等的污染。
(2)不能形成粗晶组织。
(3)不能产生较大的焊接残余应力和残余变形。
所以,焊接过程须按合理的工艺,严格按工序质量管理标准,实行全过程的质量控制。
使人、机、料、法各因素均处于良好的受控状态,从而在合理的工期内,保证钛管的焊接质量。
3材料、设备及工具要求3.1钛管及配件;应具有制造厂的出厂合格证和质量证明书。
经复验其规格、化学成分、力学性能及供货状态均应符合DIN17850标准的要求。
3.2焊接材料3.2.1焊丝:焊丝牌号为ERTi-2。
选择焊丝应符合:(1)焊丝的化学成分和力学性能应与母材相当;(2)若焊件要求有较高的塑性时,应采用纯度比母材高的焊丝。
焊丝在使用前要进行材质复验,检查出厂合格证和质量证明书;焊丝表面应清洁,无氧化色、无裂纹、起皮、斑疤和夹渣等缺陷。
焊丝的化学成分应符合AWS A5.16一70的有关规定。
3.2.2氩气:工业一级纯氩,纯度不得低于99.98%,含水量小于50Mg/L氩气在使用前先检查瓶体上的出厂合格证,以验证氢气的纯度指标,然后检查瓶阀有无漏气或失灵现象。
3.2.3钨极:选用φ2.0~φ3.0 mm铈钨极,其化学成分应符合如下要求:3.3焊接设备3.3.1焊机:采用直流TiG焊机。
焊机应保证优良的工作特性和调节特性,同时配备有完好的电流表和电压表。
3.3.2焊炬:采用QS一75°/500型水冷式TiG焊焊炬。
焊炬应具有结构简单,轻巧耐用,枪体严密,绝缘良好,气流稳定,夹钨捧牢固,适合于各种位置焊接的特点。
3.3.3氩气输送管;采用半硬质塑料管,不宜用橡胶软管和其它吸湿材料。
使用时应专用,不得与输送其它气体的管相互串用。
氩气管不宜过长,以免压力降过大引起气流不稳,一般不超过30m。
3.3.4焊接夹具:用奥氏体不锈钢或铜制管卡兰、锁紧螺栓等组对钛管及配件。
应确保对钛管及配件有一定的夹紧力,以保证轴线一致,间隙均匀合适。
3.3.5辅助设备及工具:氩气保护罩,磨光机,专用锉刀,不锈钢丝刷等。
4焊接工艺4.1管道预制阶段4.1.1管道切割与坡口加工;管材切割与坡口加工应在专门的作业场所内采用机械加工方法进行。
加工时要用非污染介质洁净水进行冷却,以防氧化。
加工工具应专用,并保持清洁,以防铁质污染。
加工好的管口应保证表面平整,无裂纹、重皮等缺陷。
切口平面最大倾斜度偏差不超过管径的1%。
4.1.2表面清理:用奥氏体不锈钢制的钢丝刷清除钛管所有焊接表面及坡口附近100mm内的锈皮、油漆、脏物、灰尘和能与钛材起反应的杂物。
用砂轮修整加工面,清除飞边、毛刺、凸凹等缺陷。
4.1.3组对:将钛管、配件对准、夹好,轴线不得偏移,间隙均匀一致,并应防止钛管在装配中被损伤和污染。
避免强制组对。
定位焊采用和正式焊接相同的焊接工艺。
4.1.4脱脂处理:用赛璐珞海棉沾无硫乙醇或无硫丙酮对所有焊接表面和坡口附近50mm内全部做脱脂处理,处理后的表面应无任何残留物。
4.1.5焊接:应在有关标准规定的条件下进行。
4.1.5.1焊接工艺评定在钛管正式施焊前,用φ252×14 TA2管进行焊接性试验,在此基础上进行φ36×4,φ252×14垂直固定及水平固定位置的四项焊接工艺评定。
焊接工艺评定宜在焊接试验室进行。
试验前拟定了与工程施工实际相同的焊接方案,评定原则、要求、方法均按ASME IX执行。
评定合格的工艺参数如下: a、坡口条件b电源种类和特性:直流正接c焊接规范4.1.5.2焊工资格根据焊接工艺评定所提供的工艺参数,在专家的指导下组织焊工进行学习,并请有经验的焊工师傅作示范,对将参与焊接的焊工进行操作技能培训和考试。
结果参加培训的五名焊工全部通过DIN8560规定的考试,并参加钛管的焊接工作。
4.1.5.3焊材焊丝为德方提供的ERTi-2,规格经工艺评定后确定为φ2.0、φ3.0。
焊丝在使用前应按坡口的清理方法进行表面清理及脱脂处理,施焊时焊丝的端部应除去10~20mm长。
4.1.5.4焊接环境钛管施工需在预制厂房内进行,在现场焊接固定口时,应根据需要搭设防雨、防风棚,保证焊接环境符合工艺要求。
若出现下列条件之一时,不准进行焊接。
4.1.5.5层间清理与保护对多层焊道,在下一层施焊前,首先检查表面氧化程度,如有异常情况,应立即进行表面处理或返修处理,处理时必须用专用的奥氏体不锈钢制钢丝刷和砂轮。
4.1.5.6焊缝表面酸洗钝化处理钛材焊接后,经表面色泽检查合格后须对焊缝和热影响区进行酸洗钝化处理。
酸洗后必须立即用水彻底冲洗.以除去残留在焊件上的酸液。
整个酸洗过程的温度应控制在40℃以下。
酸洗钝化液按下列比例配方;4.1.6焊接检验所有焊缝均应进行外观检查,X射线照相检查,着色检验和压力试验等项检验,均应合格。
4.2管道安装阶段经检验合格的预制管道接单线图及安装质量要求进行管道安装。
安装时不能将铁质工具和支架与钛管直接接触,不能用强制方法固定钛管。
安装时的现场固定焊口,焊接工艺同预制管道时的工艺.焊工应是全位置焊接培训考试合格的焊工。
4.3钛管焊接工艺流程简图如下所示:5焊接质量控制5.1组对质量控制:组对时须将方向长度偏差、间距偏差、角度偏差、法兰相邻螺栓距离偏差、法兰面与管中心垂直偏差等,均应控制在规定的范围内。
5.2施焊质量控制:焊接重点控制焊工、焊材、焊接工艺和无损检测几个主要环节。
主要采取如下措施;5.2.1加强氩气对焊接区的保护钛在250℃以上吸氢,400℃以上吸氧,600℃以上吸氮,这些元素的渗入将大大降低钛的力学性能。
因此氩气对热态焊缝的保护是焊接接头质量优劣的关键因素。
钛材管道的焊接保护都是通过管内通氩,管外用专门的保护罩来进行的。
保护罩的形式一般有整罩结构、半罩结构和弯头罩结构。
a、整罩结构为避免铁离子污染,所有保护用的结构材料采用铜材制作。
整罩结构形式如图:结构由氩气导管、缓冲器、保护罩、密封口等组成。
氩气导管采用φ6mm铜管,进人混合室有一横管上钻有一排φ1~1.5mm 小孔,孔方向前上壁,主要使氩气人口减少冲力,分布均匀,再通过二层20~40目的铜丝网进入保护区罩。
保护罩的直径宜比钛管直径大40mm左右,长度一般在80~120mm,密封口长20mm左右,宜与钛管外径保持均匀的1~2mm的间隙。
这样一方面避免氩气流失太多,另一方面又可保证保护区内微正压,可防止外部空气混入。
喷嘴焊丝插入口在25~40mm左右。
如太小则影响视线看不清焊缝,难以保证质量,太大则氩气流失严重,影响效益。
b、半罩结构半罩结构的原理基本同全罩结构,在口径较大Dg150以上采用此种结构。
半罩的长度一般在230~250mm,宽90~100mm,高40mm,密封口长40mm。
对半罩以外部分,为减少氩气流失,增加保护效果,并且为固定半罩,适合全位置焊接需要,须制作一条弧形的,宽度30~50mm,中间带凹形的保护带,该带两端连接在保护罩上,一端固定,一端采用活扣连接。
在实际施焊中可达到理想的保护效果,也解决了全位置焊接中一些技术难题。
c、弯头罩结构为达到氩气保护弯头焊缝的目的,必须增加一个弯头形状的附加罩。
在固定焊时,弯头附加罩不动,直管保护罩与弯头附加罩活动配合,可绕弯头附加罩旋转,达到氩气保护的目的。
d、管内充氩保护,均采用分段充氩的方法。
在焊口的两侧200~300mm 的地方,作好密封装置,封好充氩。
密封装置采用胶皮和不锈钢夹板封口。
出气口采用φ4mm孔径,进气口采用φ8mm孔径,这样可保证将管内空气驱赶干净,达到氩气保护的目的,另一方面保证管内做正压,防止外部空气进入,有利于焊缝成形。
但也不能使正压力过大,压力过大将使溶池金属喷出或产生背面内凹缺陷。
进气侧应密封严密,防止进氩气时从缝隙处带人空气而导致氩气保护被破坏。
对全位置焊接的焊口,充氩比较困难,因为焊口两端距离都较长,还有弯头件等。
充氮仍采用分段充氮方法,在该道焊缝组对前,就将密封垫片(由不锈钢夹板与胶皮组成,充氩管为软胶管,并联一根有一定强度的不锈钢丝)放置在管道内距焊口200~300mm处。
待焊缝组对焊接完成后,将密封垫片取出即可。
5.2.2加强焊工培训,提高全位置焊口质量对于钛管的全位置焊口的焊接,是现场施工的一个重要突破口。
由于操作受阻(要带动保护罩一起转动,还不能使用内填丝法)和视线不好,无法准确掌握熔池的形成、结晶情况,容易产生内凹及熔合不良的缺陷,因此焊工必须掌握要领,熟练操作,做到节奏均匀,快速填丝,控制熔池温度,才能保证焊接质量。
上岗焊工必须培训考试合格,在此基础上选出素质好、体力充沛的焊工进行全位置管道焊缝的焊接。
5.2.3严格执行焊接工艺,提高焊缝一次合格率由于钛材焊接的特殊要求和工艺特点,焊口多次受热会较大地降低材料的韧性,因此在焊接过程中要精心组织管理,严格执行工艺制度、最大可能地提高焊工的一次焊接合格率。