使用LED环氧树脂的常见问题及解决方案
LED封装过程中的出现的问题以及解决方法
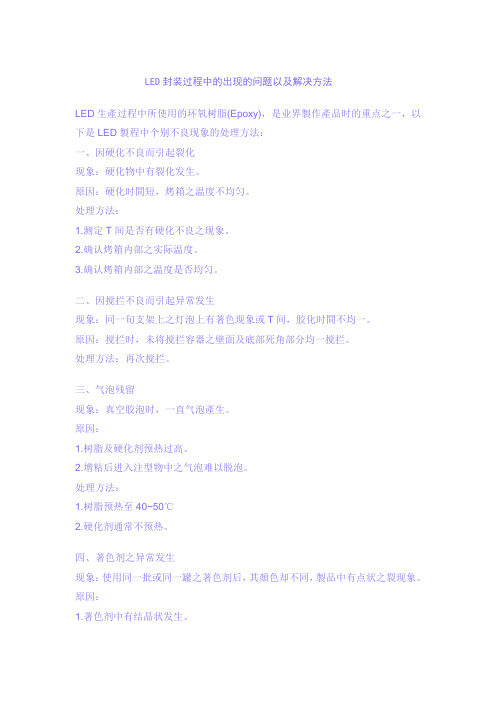
LED封装过程中的出现的问题以及解决方法LED生產过程中所使用的环氧树脂(Epoxy),是业界製作產品时的重点之一,以下是LED製程中个别不良现象的处理方法:一、因硬化不良而引起裂化现象:硬化物中有裂化发生。
原因:硬化时間短,烤箱之温度不均匀。
处理方法:1.测定T间是否有硬化不良之现象。
2.确认烤箱内部之实际温度。
3.确认烤箱内部之温度是否均匀。
二、因搅拦不良而引起异常发生现象:同一旬支架上之灯泡上有著色现象或T间,胶化时間不均一。
原因:搅拦时,未将搅拦容器之壁面及底部死角部分均一搅拦。
处理方法:再次搅拦。
三、气泡残留现象:真空胶泡时,一直气泡產生。
原因:1.树脂及硬化剂预热过高。
2.增粘后进入注型物中之气泡难以脱泡。
处理方法:1.树脂预热至40~50℃2.硬化剂通常不预热。
四、著色剂之异常发生现象:使用同一批或同一罐之著色剂后,其顏色却不同,製品中有点状之裂现象。
原因:1.著色剂中有结晶状发生。
2.浓度不均,结晶沉降反致。
处理方法:易结晶,使用前100~120 ℃加热溶解后再使用。
五、光扩散剂之异常发生现象:DP-500不易分散,扩散剂在灯泡内沉降,以致有影子出现。
原因:添加沉降防止剂变性不同分散不易。
处理方法:加强搅拦。
六、硬化剂之吸湿之异常发生现象:1.有浮游或沉降之不溶解物。
2.不透明成乳白色。
原因:1.因水酸化后成白色结晶。
2.使用后长期放置。
3.瓶盖未架锁紧。
处理方法:1.使用前确认有无水酸化现象。
2.防湿措施。
七、Display case 中有气泡残留现象:长时間脱泡后製品中仍有气泡残留。
原因:1.增粘效果现象发生,不易脱泡。
2. Display case之封胶用粘著胶带有问题。
处理方法:1.确认预热温度搅拦时間,真空脱泡之时間,真空度。
2.真空度不可过高。
3.树脂过当预热。
4.灌胶前case预热。
八、在长烤硬化时有变色(著色)现象现象:短烤离模后,长烤硬化时有变色(著色)现象。
原因:1.烤箱局部部分温度过高。
LED封装制程不良处理方法
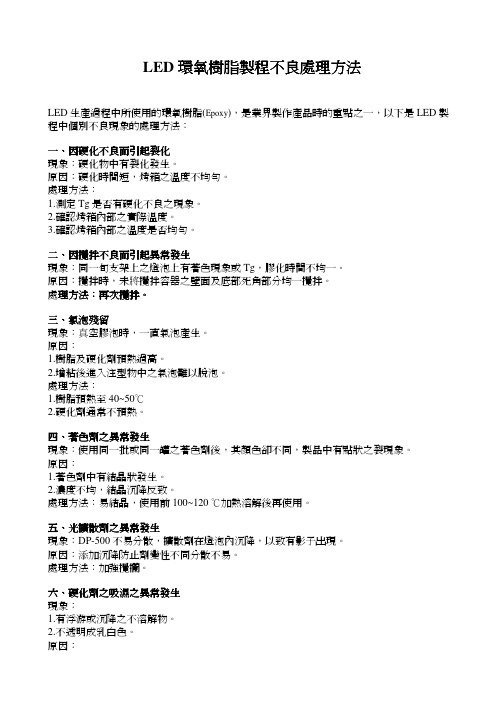
五、光擴散劑之異常發生 現象:DP-500 不易分散,擴散劑在燈泡內沉降,以致有影子出現。 原因:添加沉降防止劑變性不同分散不易。 處理方法:加強攪攔。
六、硬化劑之吸濕之異常發生 現象: 1.有浮游或沉降之不溶解物。 2.不透明成乳白色。 原因:
1.因水酸化後成白色結晶。 2.使用後長期放置。 3.瓶蓋未架鎖緊。 處理方法: 1.使用前確認有無水酸化現象。 2.防濕措施。
七、Display case 中有氣泡殘留 現象:長時間脫泡後製品中仍有氣泡殘留。 原因: 1.增粘效果現象發生,不易脫泡。 2. Display case 之封膠用粘著膠帶有問題。 處理方法: 1.確認預熱溫度攪攔時間,真空脫泡之時間,真空度。 2.真空度不可過高。 3.樹脂過當預熱。 4.灌膠前 case 預熱。
十、硬化劑變色 現象:硬化劑變茶色。 原因: 1.經預熱。 2.硬化劑長期放置或放置於高溫之所。 處理方法: 1.硬化劑不可預熱。 2.暗所存放(促進劑之因)不宜長期存放。
十一、光擴散劑之固形化 現象:無流動性,成固形狀。 原因:因添加無機物後,樹脂成固體狀(特別是冬天)。 處理方法:加熱融化。
十二、支架爬膠 現象:支架爬膠或是過錫爐時不能著錫。 原因:支架表面凹凸不平產生毛細現象。
處理方法: 1.確認支架表面有無凹凸。 2.變更低蒸氣壓之希釋劑。
十三、燈泡中從支架上有氣泡 現象:燈泡中之支架上的蓋子還有金線部分有氣泡連續地發生及殘留。 原因:因預熱溫度高(350~400 ℃通常 200-250 ℃)使鍍銀起化學變化。 處理方法:Wire bonding 時降低預熱溫度。
关于环氧树脂自流平地面施工易出现问题及防治措施
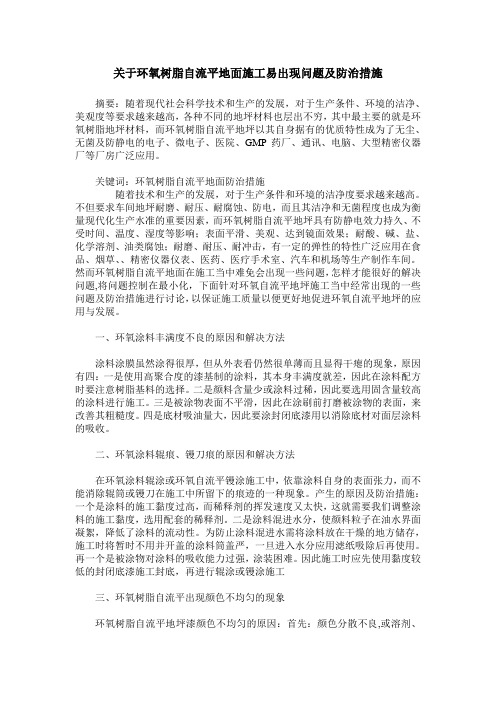
关于环氧树脂自流平地面施工易出现问题及防治措施摘要:随着现代社会科学技术和生产的发展,对于生产条件、环境的洁净、美观度等要求越来越高,各种不同的地坪材料也层出不穷,其中最主要的就是环氧树脂地坪材料,而环氧树脂自流平地坪以其自身据有的优质特性成为了无尘、无菌及防静电的电子、微电子、医院、GMP药厂、通讯、电脑、大型精密仪器厂等厂房广泛应用。
关键词:环氧树脂自流平地面防治措施随着技术和生产的发展,对于生产条件和环境的洁净度要求越来越高。
不但要求车间地坪耐磨、耐压、耐腐蚀、防电,而且其洁净和无菌程度也成为衡量现代化生产水准的重要因素,而环氧树脂自流平地坪具有防静电效力持久、不受时间、温度、湿度等影响;表面平滑、美观、达到镜面效果;耐酸、碱、盐、化学溶剂、油类腐蚀;耐磨、耐压、耐冲击,有一定的弹性的特性广泛应用在食品、烟草、、精密仪器仪表、医药、医疗手术室、汽车和机场等生产制作车间。
然而环氧树脂自流平地面在施工当中难免会出现一些问题,怎样才能很好的解决问题,将问题控制在最小化,下面针对环氧自流平地坪施工当中经常出现的一些问题及防治措施进行讨论,以保证施工质量以便更好地促进环氧自流平地坪的应用与发展。
一、环氧涂料丰满度不良的原因和解决方法涂料涂膜虽然涂得很厚,但从外表看仍然很单薄而且显得干瘪的现象,原因有四:一是使用高聚合度的漆基制的涂料,其本身丰满度就差,因此在涂料配方时要注意树脂基料的选择。
二是颜料含量少或涂料过稀,因此要选用固含量较高的涂料进行施工。
三是被涂物表面不平滑,因此在涂刷前打磨被涂物的表面,来改善其粗糙度。
四是底材吸油量大,因此要涂封闭底漆用以消除底材对面层涂料的吸收。
二、环氧涂料辊痕、镘刀痕的原因和解决方法在环氧涂料辊涂或环氧自流平镘涂施工中,依靠涂料自身的表面张力,而不能消除辊筒或镘刀在施工中所留下的痕迹的一种现象。
产生的原因及防治措施:一个是涂料的施工黏度过高,而稀释剂的挥发速度又太快,这就需要我们调整涂料的施工黏度,选用配套的稀释剂。
LED用环氧树脂异常发生原因说明篇
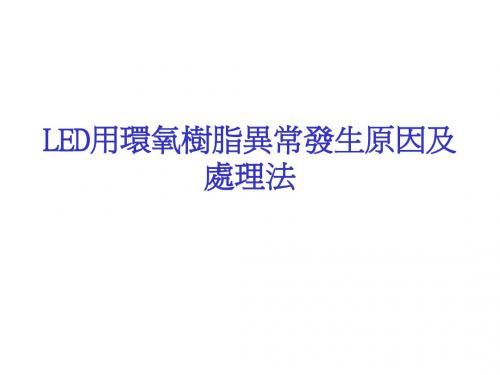
(3) 樹脂及硬化劑之配合比率 及其特性
•1) 硬化劑之使用量視所需之特性而論. •2) 一般硬化劑配合比率少時, 硬化物之 • 硬度為硬且黃變. •3) 硬化劑配合比率多時, 硬化物變脆且 • 著色少.
樹脂及硬化劑之配量
1) 樹脂、硬化劑的配量必須正確操作。
2) 配合比例是依據樹脂、硬化劑的成分所計算出來的,若無依照所指定配 比去配量、混合,將無法達到所定的特性。 3) 添加染料、擴散劑時,必須注意硬化劑的混合比。必須調整硬化劑的混 合比。
110 100
80 %R
60
40 4000 3800 3600 3400 3200 3000 2800 2600 2400 2200 2000 1900 1800 1700 1600 1500 1400 1300 1200 1100 1000 900 800 700 600 500
Wavenumber[cm-1] Ë~ ¼ « ¦W ÀÑ ¤ ¸ ¿ º ¦^ ¼ n â Æ ú wé É ´ ©¤ ® SYSTEM A/B (50 : 50 ) 4 cm-1 16 Cosine 99/04/01 14:34
例: 擴散劑 DP-500 配量: 樹脂 擴散劑樹脂含量 總樹脂含量 硬化劑所需量 分散劑 50% 樹脂 50% 比對樹脂混合量 4 ~ 6 %
100g 3g (擴散劑6g ×50%) 103g 103g
配膠實例解說
50 : 50 t¦ñ¨ ©½ ¤Ò w ¤© ~ [ C â L â z ú µÆ¨¥ÆÃ¦ µ¦³§ CTE (×10 ) Tg ( J ) ¢ lôÊ §¤§ FT - IR
Wavenumber[cm-1] Ë~ ¼ « ¦W ÀÑ ¤ ¸ ¿ º ¦^ ¼ n â Æ ú wé É ´ ©¤ ® SYSTEM A/B (40 : 60 ) 4 cm-1 16 Cosine 99/04/01 14:18 Anhydride peaks are confirmed.
环氧树脂裂纹解决方案(3篇)

第1篇一、引言环氧树脂作为一种高性能的有机高分子材料,广泛应用于航空航天、电子电器、汽车、船舶、建筑等领域。
然而,在实际应用过程中,环氧树脂制品往往会出现裂纹问题,严重影响其性能和寿命。
本文将针对环氧树脂裂纹产生的原因进行分析,并提出相应的解决方案,以期为环氧树脂制品的制造和应用提供参考。
二、环氧树脂裂纹产生的原因1. 材料因素(1)环氧树脂本身特性:环氧树脂具有优异的力学性能、耐化学腐蚀性能和绝缘性能,但在低温、高应力、高湿度等环境下,其性能会受到影响,易产生裂纹。
(2)固化剂和填料:固化剂的选择不当、填料颗粒大小分布不均等都会影响环氧树脂的力学性能,进而导致裂纹的产生。
2. 制造工艺因素(1)配料比例:配料比例不当会导致环氧树脂固化不完全,产生应力集中,从而产生裂纹。
(2)固化条件:固化温度、固化时间、固化压力等固化条件对环氧树脂的固化程度和力学性能有很大影响,不当的固化条件会导致裂纹的产生。
(3)成型工艺:模具设计不合理、成型压力不足、冷却速度过快等都会导致应力集中,产生裂纹。
3. 应用环境因素(1)温度:环氧树脂在不同温度下的性能差异较大,温度变化会引起材料收缩和膨胀,从而产生裂纹。
(2)湿度:环氧树脂在潮湿环境下易吸水,导致材料膨胀和收缩,产生裂纹。
(3)载荷:长期承受载荷会导致环氧树脂产生疲劳裂纹。
三、环氧树脂裂纹解决方案1. 材料选择与改性(1)选择合适的环氧树脂品种:针对不同应用环境,选择具有优异性能的环氧树脂品种。
(2)优化固化剂和填料:选用合适的固化剂和填料,提高环氧树脂的力学性能和耐环境性能。
(3)添加增韧剂:通过添加增韧剂,提高环氧树脂的断裂伸长率和冲击韧性,降低裂纹敏感性。
2. 制造工艺优化(1)配料比例:严格控制配料比例,确保环氧树脂固化完全。
(2)固化条件:优化固化温度、固化时间和固化压力等固化条件,提高环氧树脂的力学性能。
(3)成型工艺:优化模具设计,确保成型压力均匀,降低成型过程中的应力集中。
环氧树脂开裂原因
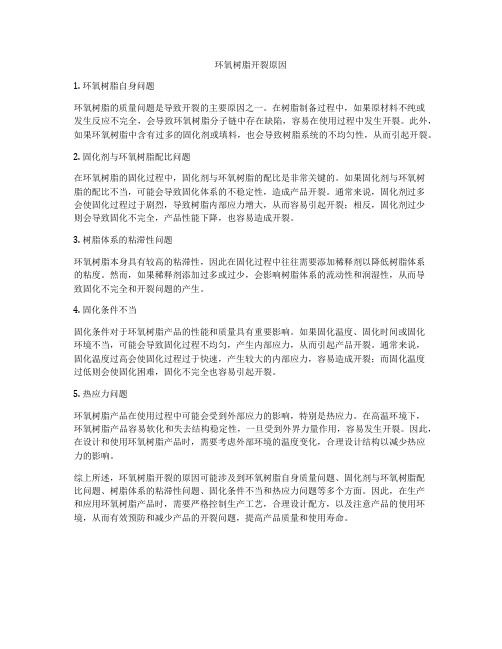
环氧树脂开裂原因1. 环氧树脂自身问题环氧树脂的质量问题是导致开裂的主要原因之一。
在树脂制备过程中,如果原材料不纯或发生反应不完全,会导致环氧树脂分子链中存在缺陷,容易在使用过程中发生开裂。
此外,如果环氧树脂中含有过多的固化剂或填料,也会导致树脂系统的不均匀性,从而引起开裂。
2. 固化剂与环氧树脂配比问题在环氧树脂的固化过程中,固化剂与环氧树脂的配比是非常关键的。
如果固化剂与环氧树脂的配比不当,可能会导致固化体系的不稳定性,造成产品开裂。
通常来说,固化剂过多会使固化过程过于剧烈,导致树脂内部应力增大,从而容易引起开裂;相反,固化剂过少则会导致固化不完全,产品性能下降,也容易造成开裂。
3. 树脂体系的粘滞性问题环氧树脂本身具有较高的粘滞性,因此在固化过程中往往需要添加稀释剂以降低树脂体系的粘度。
然而,如果稀释剂添加过多或过少,会影响树脂体系的流动性和润湿性,从而导致固化不完全和开裂问题的产生。
4. 固化条件不当固化条件对于环氧树脂产品的性能和质量具有重要影响。
如果固化温度、固化时间或固化环境不当,可能会导致固化过程不均匀,产生内部应力,从而引起产品开裂。
通常来说,固化温度过高会使固化过程过于快速,产生较大的内部应力,容易造成开裂;而固化温度过低则会使固化困难,固化不完全也容易引起开裂。
5. 热应力问题环氧树脂产品在使用过程中可能会受到外部应力的影响,特别是热应力。
在高温环境下,环氧树脂产品容易软化和失去结构稳定性,一旦受到外界力量作用,容易发生开裂。
因此,在设计和使用环氧树脂产品时,需要考虑外部环境的温度变化,合理设计结构以减少热应力的影响。
综上所述,环氧树脂开裂的原因可能涉及到环氧树脂自身质量问题、固化剂与环氧树脂配比问题、树脂体系的粘滞性问题、固化条件不当和热应力问题等多个方面。
因此,在生产和应用环氧树脂产品时,需要严格控制生产工艺,合理设计配方,以及注意产品的使用环境,从而有效预防和减少产品的开裂问题,提高产品质量和使用寿命。
环氧树脂绝缘件可能产生的缺陷及原因

环氧浇注料易生何质量问题?环氧树脂浇注件容易出现的问题有表观问题和内在问题。
中国环氧树脂行业协会专家说,表观问题主要表现为气泡、开裂、缺陷、变形等,内在问题主要表现为制件机械强度不足、电性能达不到要求、局部放电高或击穿、制件热变形温度偏低等。
当前业界要对此全面重视,以适应我国在全球领先的环氧树脂制备及应用发展势头。
这位专家指出,环氧树脂浇注件的内在质量同表观质量是相关的,有气泡、开裂、缺陷等现象的制件,其机械强度、电性能往往是不合格的,分析出现这些现象的原因需从原料、配方、制件的设计及浇注工艺过程等各方面去考虑。
原料、配方的选择,决定着制件的极限质量指标。
如普通苯酐-BPA型环氧树脂等的浇注件,其Tg的极限值为125℃左右,如果需要进一步提高Tg就必须选择其他的固化剂或其他环氧树脂。
但即使有很好的原料、合理的配方,如果浇注工艺选择不合理、操作技术差,制件也不可能达到原设计所要求的性能。
对于一些在浇注制造中容易出现的问题及其原因,专家分析认为有以下几个方面:一是气泡浇注件产生气泡是常见的现象,在一定的质量范围内对气泡的控制是个相对的概念,即只有气泡的大小和多少之分,绝对没有气泡是不可髓的,质量控制的目标是要求气泡少和小,产生气泡的原因很多,主要原因包括真空效率低、真空度或真空抽度速率达不到要求,树脂、固化剂含挥发份过多、填料吸水过多且未进行预处理,浇注时固化反应过快形成爆聚,混合料黏度过大;二是缺陷,缺陷可以说是大的气泡,即气泡达到一定程度称为缺陷,产生缺陷的原因包括浇注料黏度过大以致于未能充满模具,模具密封不严产生部分料渗漏,初始固化温度过高、混合料凝胶过快;三是开裂环氧浇注件的开裂一直是环氧树脂浇注技术研究的一个重要课题,特别是因内应力产生的微裂缝是影响浇注件质量的主要因素,浇注件产生裂缝的主要原因包括浇注材料选用及配方设计不合理(材料太脆、浇注件冷热变化时开裂,浇注固化时材料收缩率太大,浇注件固化过程中产生大量微裂缝等),浇注件本身设计或模具、嵌件设计不合理浇注件内部形成应力集中点,脱模操作不慎、局部用力过大(由于脱模时材料未完全固化且脱模温度较高,此时固化物的机械强度很低在外力下很容易产生裂缝),凝胶固化温度过高、制件固化后冷却速度过快等。
LED软灯条封装树脂胶水种类及常见问题解决
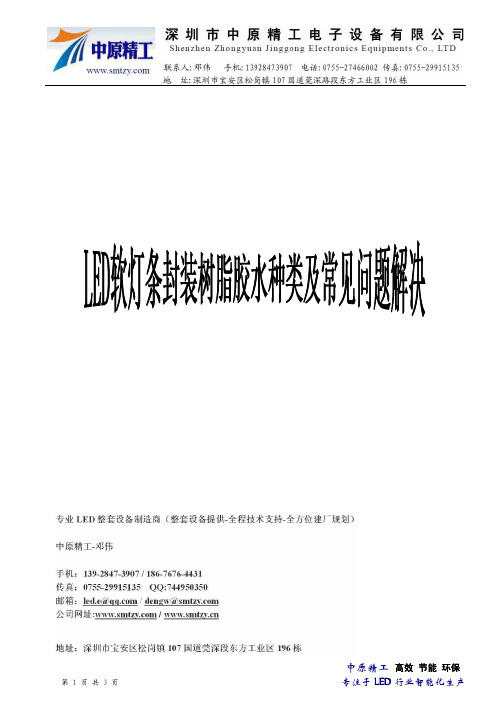
LED软灯条封装树脂胶水种类及常见问题解决一、LED软灯条封装树脂胶水种类树脂种类环氧树脂聚氨酯改性环氧树脂聚氨酯树脂透光率85―92 88-92 91-95 适宜用途户内户内户外/户内抗黄变性能户外2个月后发黄户外三个月后发黄户外至少三年不发黄柔韧性能一般良好优异使用温度范围-5℃至55℃-5℃至65℃-35℃至95℃使用中可能存在的隐患◆低温下变硬变脆,软带光条会发生断裂现象。
◆温度高于60℃的环境中韧性变差,容易发生断裂现象。
◆光条灯珠长期亮灯500到700小时后,灯珠部分树脂变成黄褐色,灯珠不能透光,需要更换。
◆低温下变硬变脆,软带光条会发生断裂现象。
◆温度高于70℃的环境中韧性变差,容易发生断裂现象。
◆光条灯珠长期亮灯1500到3000小时后,灯珠部分树脂变成黄褐色,灯珠不能透光,需要更换。
◆在-35℃至110℃的环境中,光条不会发生断裂现象。
◆在集装箱运输过程中,光条不会因为集装箱的高温环境而断裂。
◆光条灯珠长期亮灯50000小时,树脂也不会发生颜色变化。
保二、LED软带光条封装常见问题序号软灯条封装常见问题解决方法1 LED软灯条胶体内有气泡◆.需要对胶水抽真空处理。
◆.真空度不够。
◆.胶水的使用超过了操作时间2 LED软灯条不干或者有些地方偏硬或者偏软◆.混合搅拌不均匀。
◆.混合比例不正确3 LED软灯条表面水波纹◆.混合比例不精确。
◆.混合搅拌不充分。
◆.胶水的使用超过了操作时间4 LED软灯条表面出现水雾◆.空气中湿气过高◆.使用后的胶水未密封完全而受潮,或接触到水◆.滴胶工具中含有清冼时的残留溶剂或胶水接触到溶剂。
5 LED软灯条胶水表面粘手◆.混合比例或搅拌过程出错。
◆.B胶受潮6 LED软灯条胶水与线路板附着力差,容易脱离◆.由于线路板表面有绝缘漆,想要达到理想状态较难◆.胶水比例不正确及未搅拌均匀◆.胶水本身配方问题7. LED软灯条对折及低温下柔韧性差,容易断,户外黄变◆环氧树脂材料本身限制,建议使用聚氨酯树脂(PU胶),聚氨酯树脂可以在-35℃至95℃环境中使用,户外至少三年不发黄8. LED软灯条表面滴的不饱满,胶水容易溢到旁边◆胶水太稀,询问供应商胶水是否合适◆混合比例不准确◆操作方法不正确(参考附件图片)。
- 1、下载文档前请自行甄别文档内容的完整性,平台不提供额外的编辑、内容补充、找答案等附加服务。
- 2、"仅部分预览"的文档,不可在线预览部分如存在完整性等问题,可反馈申请退款(可完整预览的文档不适用该条件!)。
- 3、如文档侵犯您的权益,请联系客服反馈,我们会尽快为您处理(人工客服工作时间:9:00-18:30)。
使用LED环氧树脂的常见问题及解决方案
在使用led 封装环氧树脂AB 胶过程中发现的一些常见问题,并给出了相应解决方案,以供大家参考。
也请各位在使用中提出发现的另类问题,我们大家来共同寻求解决方案。
一、LED 黄变。
原因:1、烘烤温度过高或时间过长;2、配胶比例不对,A 胶多容易黄。
解决:1、AB 胶在120-140 度/30 分钟内固化脱模,150 度以上长时间烘烤易黄变。
2、AB 胶在120-130 度/30-40 分钟固化脱模,超过150 度或长时间烘烤会黄变。
3、做大型灯头时,要降低固化温度。
二、LED 气泡问题。
原因:1.碗内气泡:支架蘸胶不良。
2.支架气泡:固化温度太高,环氧固化过于激烈。
3.裂胶、爆顶:固化时间短,环氧树脂固化不完全或不均匀。
AB 胶超出可使用时间。
4.灯头表面气泡:环氧胶存在脱泡困难或用户使用真空度不够,配胶时间过长。
解决:根据使用情况,改善工艺或与环氧供应商联系。
三、LED 支架爬胶。
原因:1、支架表面凹凸不平產生毛細現象。
2、AB 胶中含有易挥发材料。
解决:请与供应商联系。
四、LED 封装短烤离模后长烤变色。
原因:1、烘箱内堆放太密集,通风不良。
2、烘箱局部温度过高。
3、烘箱中存在其他色污染物质。
解决:改善通风。
去除色污,确认烘箱内实际温度。
五、同一排支架上的灯,部分有着色现象或胶化时间不一,品质不均。
原因:搅拌不充分。
解决:充分搅拌均匀,尤其是容器的边角处要注意。
六、不易脱模。