高拉速连铸
连铸技术的发展状况及高效连铸

机作业率大大提高(≥80%)。
1.2高效连铸的主要作用
1.2.1
连铸坯产量大幅度提高
004
从1989年到2001年我国连铸坯产量由1
投资3~4亿元。
万t增加到12 000万t以上,连铸比由16.3%提高 到87.5%。如果只靠投资新建铸机,而没有连铸机 的高效化,新建和原有铸机都是那样的低生产率,要 想达到这样的总产量是不可想象的,无论资金投入、 场地占用等许多方面都是难以承受的。高教连铸技 术为钢铁行业的调整结构降低成本作出了贡献。 1.2.2 实现炼钢车间的炉机匹配 我国的转炉车间炉容从几吨到200 t都有小方坯 生产。由于小方坯铸机生产能力低,3台转炉配4、5 台甚至6台连铸机,匹配关系复杂混乱,工艺制度不 能保证。这反过来又影响了铸机生产和铸坯质量。 经过连铸机的高效化改造,设备可靠性增加,浇 铸速度提高,连铸机的台时产量大幅提高。实现了各 种模式的炉机匹配生产。如原3炉4、5机全连铸炼 钢车间只需要3台铸机.1炉对1机生产。原来炉容 较小的3炉2机加模铸的车间可实现3炉对2机的 全连铸生产。 炉机匹配后的最大好处全车间生产顺行,工艺制 度得以执行。钢水的温度、氧化性、到位时间都可保 证。这又促进了铸机生产的稳定、高速、优质。 1.2.3经济效益 实现高教连铸使各项技术指标提高,消耗下降, 铸坯质量改善,可使企业降低成本节省投资,获得很 大的经济效益。 连铸直接效盎首钢三炼钢厂统计,由于提高合 格坯收得率、节省备件费用、减少耐材消耗等可降低 连铸坯成本约7元/t。广钢转炉厂节省中间包材料 及提高铸坯收得率可降低连铸坯成本10元/t。 综合经济效益包括降低冶炼消耗、降低连铸成 本、提高综合成材率等,见表4。
450
mm,带厚度2.3~3.2
mm,拉速达35~70 m/rain,该生产线计划于2001年
连铸结晶器保护渣
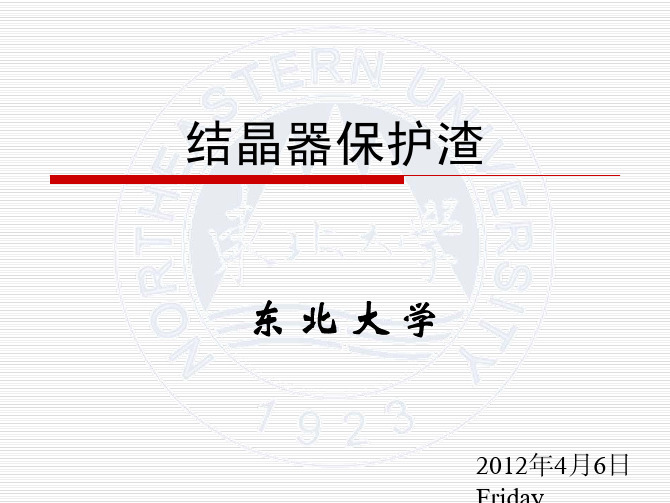
连铸技术
炭质材料对熔化速度的影响规律是:炭量越多, 炭的粒度越小和比表面积越大,则降低熔化速 度的作用越强烈。常用的炭质材料降低熔化速 度的顺序是:碳黑>高炭石墨> 土状石墨。。
27
3.3 保护渣粘性特征
连铸技术
保护渣粘度是控制结晶器与铸坯之传热和润滑的 重要参数。粘度过大,熔化的保护渣不易渗入 结晶器和铸坯之间的缝隙内,铸坯的润滑条件 恶化,导致坯壳不易从结晶器内拉出,甚至造 成粘性漏钢事故。粘度过低,熔化的保护渣大 量流入结晶器和铸坯之间,铸坯润滑和传热不 均,导致表面裂纹产生,产生废品。
19
连铸技术
20
硅氧离子团结构图
连铸技术
21
氧化物对保护渣熔体网络的作用
连铸技术
22
3 连铸保护渣的物理和化学性质
连铸技术
连铸过程对保护渣的物理及化学性质有一定的要 求。保护渣的熔化温度、粘度及表面张力的大 小取决于渣的化学成分。保护渣的研制和使用 过程要对其密度、熔化温度、粘度、表面张力 和溶解吸收非金属夹杂物能力等基本性质进行 测定。除了上述几个基本性质之外,保护渣的 熔融速度、熔融模型以及导热性也是衡量保护 渣性能的主要指标。
用于连铸保护渣的原材料种类繁多,分为天然矿 物(如石灰石、萤石、硅灰石、石英砂等)和 人造矿物(工业废渣、水泥熟料、玻璃粉、人 造硅灰石等)。
6Leabharlann 连铸技术保护渣组成、性能与原料选择之间的关系
7
连铸技术
保护渣的物性指标主要包括成分、熔点、熔速、 粘度等,这些指标主要取决于 CaO、SiO2、 Al2O3的百分含量、组成助熔剂和熔速调节剂 的成分及加入量。不同的钢种、断面或拉速对 保护渣的特性要求差别比较大,相应地,保护 渣的化学成分变化也很大。
高效连铸知识问答
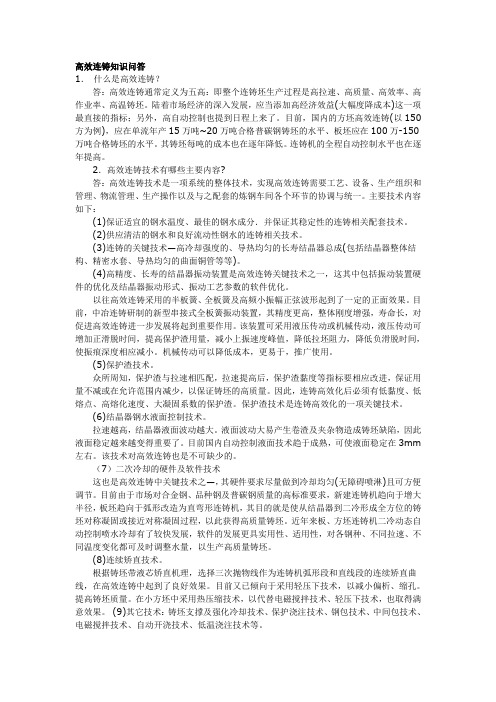
高效连铸知识问答1.什么是高效连铸?答:高效连铸通常定义为五高:即整个连铸坯生产过程是高拉速、高质量、高效率、高作业率、高温铸坯。
陆着市场经济的深入发展,应当添加高经济效益(大幅度降成本)这一项最直接的指标;另外,高自动控制也提到日程上来了。
目前,国内的方坯高效连铸(以150方为例),应在单流年产15万吨~20万吨合格普碳钢铸坯的水平、板坯应在100万-150万吨合格铸坯的水平。
其铸坯每吨的成本也在逐年降低。
连铸机的全程自动控制水平也在逐年提高。
2.高效连铸技术有哪些主要内容?答:高效连铸技术是一项系统的整体技术,实现高效连铸需要工艺、设备、生产组织和管理、物流管理、生产操作以及与之配套的炼钢车间各个环节的协调与统一。
主要技术内容如下:(1)保证适宜的钢水温度、最佳的钢水成分.并保证其稳定性的连铸相关配套技术。
(2)供应清洁的钢水和良好流动性钢水的连铸相关技术。
(3)连铸的关键技术—高冷却强度的、导热均匀的长寿结晶器总成(包括结晶器整体结构、精密水套、导热均匀的曲面铜管等等)。
(4)高精度、长寿的结晶器振动装置是高效连铸关键技术之一,这其中包括振动装置硬件的优化及结晶器振动形式、振动工艺参数的软件优化。
以往高效连铸采用的半板簧、全板簧及高频小振幅正弦波形起到了一定的正面效果。
目前,中冶连铸研制的新型串接式全板簧振动装置,其精度更高,整体刚度增强,寿命长,对促进高效连铸进一步发展将起到重要作用。
该装置可采用液压传动或机械传动,液压传动可增加正滑脱时间,提高保护渣用量,减小上振速度峰值,降低拉坯阻力,降低负滑脱时间,使振痕深度相应减小。
机械传动可以降低成本,更易于,推广使用。
(5)保护渣技术。
众所周知,保护渣与拉速相匹配,拉速提高后,保护渣黏度等指标要相应改进,保证用量不减或在允许范围内减少,以保证铸坯的高质量。
因此,连铸高效化后必须有低黏度、低熔点、高熔化速度、大凝固系数的保护渣。
保护渣技术是连铸高效化的一项关键技术。
提高拉速对铸坯质量的影响及相应措施

提高拉速对铸坯质量的影响及相应措施在连铸生产的诸多技术参数中,拉速(以下用来表示)是至关重要的一种。
对铸机产量和铸坯质量都有极为重要的影响。
纵观连铸的发展史,提高是一个重要的方面。
连铸的技术进步主要也是围绕着的提高来实现的。
提高可以增加铸机产量,减少铸机台数或铸坯流数,还可以提高铸坯表面温度有利于热送。
近年来薄板坯连铸的问世,要求将提高到更高的水平。
决定了连铸机的生产效率。
近年来,我国推广使用高拉速、高连浇率、高作业率和高铸坯质量的高效率连铸机。
然而高拉速和高铸坯质量往往是相互矛盾的,我们的任务是要根据钢种和产品质量要求,通过采用相关技术,使连铸机的拉速和铸坯质量协调发展。
1 近年来提高连铸拉速的相关技术高效连铸的核心技术是高拉速。
近年来,国内外在提高连铸拉速方面的研究工作取得了显著成绩,许多与提高的配套技术已投入生产应用。
例如:1)采用二冷动态配水技术。
连铸坯作业中过高,容易造成铸坯凝固时间不充分。
二冷动态配水最主要的功能是对铸坯进行热跟踪,根据跟踪结果对二冷水进行调节。
在连铸过程中,带液芯的铸坯在二冷区约有80%的热量传出,来完成液芯凝固及坯壳冷却过程。
如果使用的二冷技术不得当,使得矫直时铸坯表面温度低于900度,正好位于脆性区,那么铸坯在矫直力作用下形成表面裂纹。
还可能由于二次冷却不均匀,使得铸坯表面温度呈现周期性回升,而引起坯壳膨胀,产生中间裂纹和皮下裂纹。
针对这些不足,动态二冷配水技术保证了铸坯表面温度的平稳,有利于铸坯质量的稳定和提高;保证了生产的顺行,避免了生产事故,减小了现场操作人员的操作强度;缩短了热换中包的时间,适应了提高的要求。
2)采用漏钢预报技术。
连铸坯作业中过高,冷却时间不充分,容易造成黏附性漏钢。
漏钢对连铸生产危害巨大,轻者引起双浇、堵塞喷嘴、减少金属收得率;重者严重损害设备,引起缺流、烧坏二冷装置、中断连铸、钢水回炉等;还可能对操作者自身造成伤害,影响生产的正常进行,造成停产。
炼钢连铸工艺流程的介绍
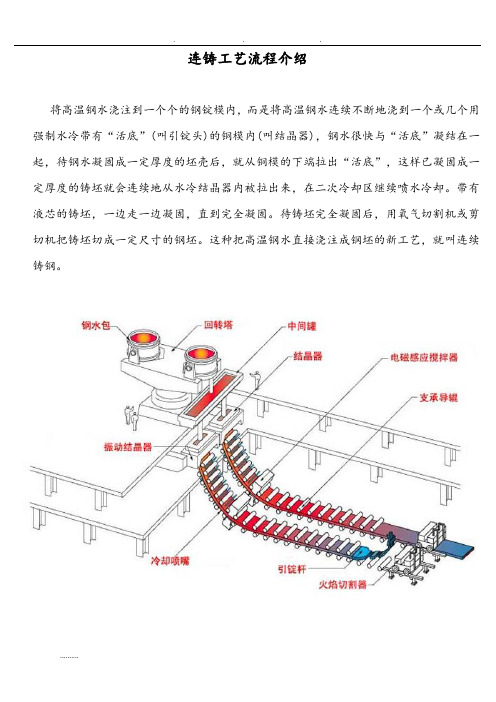
连铸工艺流程介绍将高温钢水浇注到一个个的钢锭模内,而是将高温钢水连续不断地浇到一个或几个用强制水冷带有“活底”(叫引锭头)的铜模内(叫结晶器),钢水很快与“活底”凝结在一起,待钢水凝固成一定厚度的坯壳后,就从铜模的下端拉出“活底”,这样已凝固成一定厚度的铸坯就会连续地从水冷结晶器内被拉出来,在二次冷却区继续喷水冷却。
带有液芯的铸坯,一边走一边凝固,直到完全凝固。
待铸坯完全凝固后,用氧气切割机或剪切机把铸坯切成一定尺寸的钢坯。
这种把高温钢水直接浇注成钢坯的新工艺,就叫连续铸钢。
【导读】:转炉生产出来的钢水经过精炼炉精炼以后,需要将钢水铸造成不同类型、不同规格的钢坯。
连铸工段就是将精炼后的钢水连续铸造成钢坯的生产工序,主要设备包括回转台、中间包,结晶器、拉矫机等。
本专题将详细介绍转炉(以及电炉)炼钢生产的工艺流程,主要工艺设备的工作原理以及控制要求等信息。
由于时间的仓促和编辑水平有限,专题中难免出现遗漏或错误的地方,欢迎大家补充指正。
连铸的目的: 将钢水铸造成钢坯。
将装有精炼好钢水的钢包运至回转台,回转台转动到浇注位置后,将钢水注入中间包,中间包再由水口将钢水分配到各个结晶器中去。
结晶器是连铸机的核心设备之一,它使铸件成形并迅速凝固结晶。
拉矫机与结晶振动装置共同作用,将结晶器内的铸件拉出,经冷却、电磁搅拌后,切割成一定长度的板坯。
连铸钢水的准备一、连铸钢水的温度要求:钢水温度过高的危害:①出结晶器坯壳薄,容易漏钢;②耐火材料侵蚀加快,易导致铸流失控,降低浇铸安全性;③增加非金属夹杂,影响板坯内在质量;④铸坯柱状晶发达;⑤中心偏析加重,易产生中心线裂纹。
钢水温度过低的危害:①容易发生水口堵塞,浇铸中断;②连铸表面容易产生结疱、夹渣、裂纹等缺陷;③非金属夹杂不易上浮,影响铸坯内在质量。
二、钢水在钢包中的温度控制:根据冶炼钢种严格控制出钢温度,使其在较窄的范围内变化;其次,要最大限度地减少从出钢、钢包中、钢包运送途中及进入中间包的整个过程中的温降。
连铸机拉速的提升和作业率的提高毕业论文
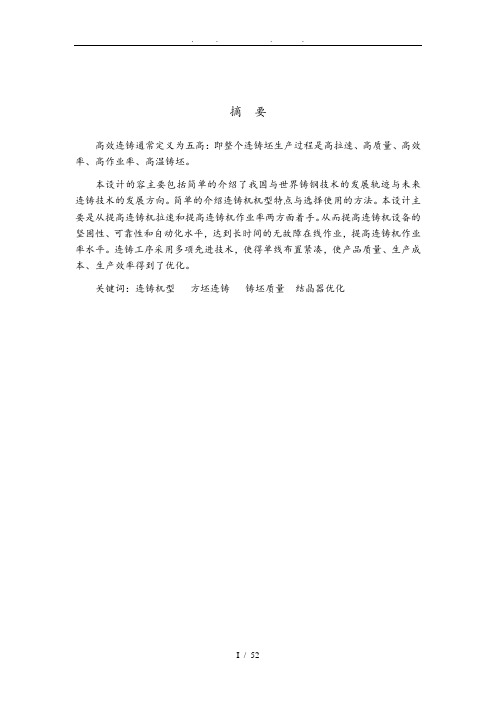
摘要高效连铸通常定义为五高:即整个连铸坯生产过程是高拉速、高质量、高效率、高作业率、高温铸坯。
本设计的容主要包括简单的介绍了我国与世界铸钢技术的发展轨迹与未来连铸技术的发展方向。
简单的介绍连铸机机型特点与选择使用的方法。
本设计主要是从提高连铸机拉速和提高连铸机作业率两方面着手。
从而提高连铸机设备的坚固性、可靠性和自动化水平,达到长时间的无故障在线作业,提高连铸机作业率水平。
连铸工序采用多项先进技术,使得单线布置紧凑,使产品质量、生产成本、生产效率得到了优化。
关键词:连铸机型方坯连铸铸坯质量结晶器优化AbstractEfficient continuous casting is usually defined as five high : that the entire billet production process is high speed 、high quality 、 high efficiency、high operating rates. High temperature slab.The design covers the brief introduction to China and the world steel technology development path and future direction of continuous casting technology. Brief characteristics of continuous casting machine models and select the method used. This design is mainly to increase speed and improve the continuous casting machine continuous casting machine of two aspectsContinuous casting machine equipment to enhance the robustness, reliability and automation level, to achieve long trouble-free online operations and increase the rate of horizontal continuous casting machine operation. Continuous casting process uses a combination of advanced technology, making single compact layout, product quality, production costs, production efficiency has been optimized.Key words: continuous casting billet Slab qualityMold Optimization目录摘要IABSTRACT II第一章绪论11.1连续铸钢技术简介11.2世界连铸技术的发展11.3连续铸钢的优越性71.3.1传统连铸进入工业成熟期的技术发展71.3.2连续铸钢技术的最新发展与未来81.4我国铸钢技术的开发与应用12第二章连铸机的机型和特征142.1连铸机的机型和特点142.2连铸机的结构特征162.3连铸机机型的选择17第三章总体设计183.1总体方案的确立183.2弧形连铸机总体设计计算与确定183.2.1铸坯断面193.2.2冶金长度(液心长度)203.2.3拉坯速度233.2.4连铸机生产能力的计算263.2.5连铸机生产能力的计算273.2.6校核铸坯是否完全凝固283.2.7带液一点矫直的可能性293.2.8连铸机流数的计算30第四章振动装置设计与计算314.1结晶器的振动参数314.2振动机构的驱动功率(P)334.2.1振动总负荷334.2.2动负荷334.2.3驱动功率P的计算34第五章 PROENGINEER软件简介34PROE的简介:34第六章结论41参考文献43附录45致48第一章绪论1.1 连续铸钢技术简介连续铸钢是一项把钢水直接浇铸成形的节能新工艺,它具有节省工序、缩短流程,提高金属收得率,降低能量消耗,生产过程机械化和自动化程度高,钢种扩大,产品质量高等许多传统模铸技术不可比拟的优点。
连铸介绍

为什么高效连铸特别强调保证浇注钢水温度2010-03-19 22:02适宜的钢水温度(不同的钢种有不同的温度要求)可使高效连铸生产获得高质量的铸坯;而钢水过热度提高,钢坯坯壳减薄,钢水易于二次氧化,夹杂物增多,耐材严重冲蚀,易出现较肚、漏钢、柱状晶发达、中心偏析严重、缩孔严重等一系列问题。
高效连铸的生产实践和理论都得出了相同结论,即低温浇铸是提高拉速及改善铸坯质量的重要手段之一。
当然,温度低要有界限,温度过低会出现钢水流动性差、水口冻结、夹杂物难以上浮等问题。
所以高效连铸特别强调要保证浇注钢水温度;即钢水浇注温度均匀稳定地保证在规定的范围内。
高效连铸机的钢包支撑装置的特点高效连铸机的钢包支撑无论是回转台还是三包位行走小车,都应该做到换包快捷,易于上水口,易于阻挡下渣,最好能配有耐用的动态称重装置,以适合多炉连浇、保护浇铸等高效连铸的基本要求。
高效连铸机对中间包的要求(1)中间包容量大,钢水液面深度要保证足够的夹杂物上浮时间。
目前,年产60万吨的4机4流高效方坯连铸机中间包容量可达25吨,液面溢流标高900mm。
(2)中间包要有最佳温度场及热流分布(通过内腔形状,坝、挡墙等方法获取),以达到各水口之间的温度尽可能的均匀,即外侧水口与内侧水口温度差在±3℃为好。
(3)高效连铸由于连浇炉数高,要求中间包外壳体及底部不变形;炉衬经久耐用,最好是整体喷涂。
耐材不易腐蚀脱落污染钢水,尤其水口要经久耐用,最好配置水口快速更换装置。
高效连铸机对中间包车的要求高效连铸机作业率高,因此要求中间包车的事故率要低。
中间包车的升降系统要可靠耐用,升降平稳,以适应保护浇铸的要求。
称重装置尤其应可靠,使用寿命长,保证监控中间包液面高度,使中间包液面稳定,波动小,满足高效连铸的需要。
中间包车的横向移动要平稳精确,保证水口与结晶器的准确对位。
目前小方坯上多采用高低腿门式中间包车,这种中间包车易于操作,采用液压驱动,更快捷、平稳。
高拉速连铸保护渣的理化性能研究

tmprtr fh u u o l b rpr d cdadte hn ae n a— e eaueo e t mo l f xs ud e o el r ue n i rtadAk b dl h p ye h me g o pi a h i r , . h h c dc mi oet s e srt nrt ce:d T ep ̄i ln e cl rpre fh u u nb — o ee n a ' < aa h ap i o t mol f xc emg dl a
维普资讯
20 0 2年 6月 第 】卷 第 3 8 期
炼
钢
J n 2 0 u 0 2
Vo 8 No 3・ 3 I1 . 5
Se tdma ig kn
高 拉 速连 铸 保 护 渣 的理 化 性能 研 究
章 耿
刘 承 军
( 钢集 团公 司 ) 宝
实验 采 用 C t 一S( —NaO 一 R —Ab a) i
—
原高度 14时的半球温度来表示 ,升温速度 1 / O ℃ ・ n 。熔化 速 度 定 义 为 l30℃ 恒 温 条 件 下 mi 0
渣 柱完全熔 化 所需 的时 间 本实 验采 用旋 转粘度 HN 定 连铸保 护渣 的粘 - 度 和凝 固温 度 , 程 在 M< i 过  ̄2高温炉 内进行 。凝 S
Re e r h OlPh sc nd Ch m ialPr p r iso o l sa c i y iala e c o e te f M u d Fl x f rHi h S e d Ca tn u o g p e sig
Z a gG n hn eg ( ag n op ) B o agC r
消耗量减 少 , 造成 结 晶器 壁与 凝 固坯 壳之 间的润
- 1、下载文档前请自行甄别文档内容的完整性,平台不提供额外的编辑、内容补充、找答案等附加服务。
- 2、"仅部分预览"的文档,不可在线预览部分如存在完整性等问题,可反馈申请退款(可完整预览的文档不适用该条件!)。
- 3、如文档侵犯您的权益,请联系客服反馈,我们会尽快为您处理(人工客服工作时间:9:00-18:30)。
连铸技术发展
7、90年代-传统连铸的完善和近终形连铸技术的兴起
传统连铸向降低生产成本、强化高级产品生产、注重环境的方 向发展; 近终形连铸取得成功: - CSP、ISP等薄板坯连铸技术被愈来愈多的工厂采用,品种 也逐步扩大; - QSP、CONROLL等中厚度板坯连铸连轧技术开发成功。
全球最高水平的板坯连铸
大包下渣检测系统 长水口自动安置 热中间包循环使用 滑板+步进液压缸控制 80t密封中间包
上装引锭杆 辊缝测量
连浇自动操作(浇铸平台、搅拌站)
垂直段3m
非正弦波振动 快速更换结晶器窄边改变浇铸铸坯厚度
钢包吹氩远程自动控制
10点弯曲
气水喷雾二冷,喷嘴堵塞监测
分节辊轻压下(17m)
冶金长度49m
5点矫直
B:铸坯厚度; t0:已确定适宜的温度; θp:实际出现温度。
高拉速导致拉漏增加的原因
粘结性拉漏
结晶器内表面温度提高; 保护渣耗量减少。
结晶器出口坯壳减薄 d=K(L/V)1/2+B 坯壳与结晶器内壁间摩擦力增大
保护渣消耗量是高速连铸 工艺的一项重要操作指标
保护渣的消耗量对铸坯的润 滑非常重要,消耗量不当,可 能引起铸坯纵裂纹、粘结漏 钢、振痕过深、横角裂、角部 纵裂及铸坯凹坑。 高拉速下保护渣消耗量减 小,液渣膜变薄,初生坯壳受 到的摩擦力增大。 高拉速下初生坯壳厚度减 薄,在过多摩擦力下易破裂, 产生漏钢。
高拉速连铸技术 与粘结漏钢
连铸技术发展
1、早期的连铸技术开发(1886~1937)
浇铸有色金属; 金属液面波动大; 拉漏频繁,采取的对策:提高结晶器冷却强度 “ 拉-停-拉”方法以 增加坯壳厚度。
连铸技术发展
2、早期连铸技术的突破
1937年,S. Junghans开发成功振动结晶器技术; 1938年I. Rossi购买了Junghans连铸技术的专利和设备制造权; 振动结晶器连铸技术随后在有色金属工业应用; 40年代末欧、美、苏等钢厂开始进行钢水连铸试验。
非稳态浇铸
结晶区液面波动 开浇 更换中间包 连续粘结
操作原因
不合适保护渣 不合适地结晶器锥度
粘结对结晶器铜板温度的影响
浸入式水口尺寸、夹角、埋入深度
浸入式水口流出的钢水如向上分流过强,会造成表面波动过大引 起的卷渣等。 浸入式水口流出的钢水如向上分流过小,表面供热不足,会造成 保护渣熔化不良、保护渣流入不均匀,容易产生纵裂纹缺陷。
国内开始重视高速连铸
近年来日本钢铁企业高拉速连铸取得了显著进展; JFE仓敷钢铁厂3#板坯铸机(220mm厚)拉速达到3m/min,并且 在2.4 m/min拉速下浇铸汽车板钢,2.0m/min拉速下浇铸中碳亚 包晶钢; 神户制钢加古川钢铁厂可以在2m/min拉速下浇铸汽车板钢。 日本高拉速连铸取得的进步对中国钢铁界震动很大。徐匡迪、 瑞钰等院士提议的新一代钢铁流程中对高拉速连铸给予了很重 的地位。
高拉速连铸用保护渣:
适量LiO2、BaO; 粘度、凝固温度、结晶温度; 保护渣耗量≥0.4kg/mm2。
高效强冷结晶器:
铜板厚度、固定螺栓布置、水槽结构; 冷却水压力、流速; 结晶器工作曲面。
非正弦波振动结晶器:
振动波形(正弦波、三角波、锯齿波等); 频率、振幅、负滑脱时间、负滑脱量等。
高拉速连铸关键技术
炉外精炼的周期短于转炉炼钢 和连铸的周期; 适应多炉连浇的要求; 使转炉、连铸机都获得高的生 产效率。
板材流程采用LF精炼 LF时间长于转炉炼钢和连 铸; 炉外精炼无法成为炼钢- 铸工序间的缓冲; 影响整条生产线的效率。
温度变化导致拉速的变化
1.02 × 252 dV = (t 0 − θp ) B
切割控制
在线去毛刺控制 铸坯搬送控制 铸坯喷印号读取 铸坯喷印号判定 高温铸坯表面缺陷检测设备
中间包内衬自动喷涂
中间包自动预热控制
中间包
高拉速连铸技术
日本80年代中后期、欧洲90年代中后期开始进行高拉速连铸试验研 究: 板坯拉速达到了2.5~3m/min,工作拉速在2.2m/min以上; 小方坯拉速达到了4~5m/min。 高速连铸主要困难: 拉漏增加; 铸坯表面和内部缺陷增多。 当时没有解决高拉速连铸优质汽车板钢铸坯结晶器卷渣和中碳亚包 晶钢铸坯表面纵裂纹问题,上述钢种拉速仍大都在1.2-1.3 m/min 以下。
防止拉漏的措施
防止粘结性拉漏
增大冷却水流速,降低铜板内壁温度; 增大保护渣耗量-低粘度保护渣; 高频率、小振幅振动。
减少摩擦力
采用低粘度、低凝固温度、低结晶温度保护渣 高频率、小振幅振动。
增加结晶器出口坯壳厚度
增加结晶器长度; 提高冷却水流速; 改善结晶器-坯壳接触,减少气隙。
高拉速连铸关键技术
结晶器钢水电磁制动技术:
FC结晶器(上下平面制动); EMLA和EMLS电磁技术。
拉漏预报和防止技术:
单排热电偶和多排热电偶; 误报率显著降低。
浸入式水口结构改进和结晶器液面波动控制:
水口夹角、浸入深度、浇铸速率等; F数控制。
二冷动态控制技术
保护渣的作用
防止钢液氧化; 钢液表面保温; 吸收夹杂物; 润滑; 均匀传热。
连铸技术发展
3、50年代-连续铸钢进入工业化
1954年Halliday开发了“ 负滑脱”振动技术; 结晶器润滑和浸入式水口等技术连铸钢水取得成功。 加拿大Atlas Steel厂54年建成610mm宽板坯铸机; 1959、1960年苏联建成宽板坯铸机; 采用连铸的多是电炉钢厂,钢种多为特殊钢; 技术水平较低:产量低、作业率低,不能实现连浇。
不同类钢适用的保护渣凝固温度示意图
保护渣重要的物性参数:结晶温度
结晶析出会降低保护渣的润滑效果,拉漏可能 性增加; 结晶温度高可以减弱液体保护渣的发达程度, 减缓传热; 固体保护渣层中结晶相析出,渣膜中易产生微 裂纹和晶界均会增大传热热阻; 降低玻璃相辐射传热的效果。
保护渣重要的物性参数: 熔化温度和熔化速度
保护渣熔化温度和熔化速度对保护渣液渣层高度及 坯壳与结晶器壁之间的流入有重要影响。 影响保护渣熔化速率的因素: 自由碳含量; 碳颗粒的粒度; 保护渣熔化温度; 保护渣原料粒度; 拉速。
粘度
CaO SiO2 CaO/SiO2 Al2O3 Na2O F Fe2O3
凝固温度
熔化温度
粘度
MnO MgO B 2 O3 BaO Li2O TiO2 K2 O
4K 2 L ( ) V= 2 D
拉速的确定原则
3、根据经验公式冶金长度,来计算连铸机的工作拉速 L’为铸坯的断面周长,A为铸坯的断面面积,f:为和 钢种、铸坯形状、结晶器参数及冷却制度有关的常数。
L V=f A
'
拉速的确定原则
工序间生产节奏合理匹配
t炉外精炼 < t转炉炼钢 ≤t连铸 t转炉炼钢 ≤t连铸 < tLF精炼
数学模型得到的F数
数学模型得到的F数
谢
谢!
钢包运输自动控制
日本钢管福山厂6#板坯铸机
最大拉速3m/min
全球最高水平的板坯连铸
生产管理计算机 过程控制 信息处理 连铸过程计算机 操作支援
大包回转台钢包安置 大包管、线路连接 大包包盖安置 大包搅拌气体流量控制 大包浇铸位置移动 中间包预热控制、移动、升降
大包自动浇铸(中间包重量控制)
电气系统
凝固温度
熔化温度
采用添加Na2O、Li2O来降低保护渣粘度
电磁制动技术
电磁制动技术
NKK开发的交流运动磁场结晶器钢水稳定装置示意图
FC结晶器
川崎制铁开发的FC结晶器示意图
结晶器漏钢的成因
漏钢的类型:
粘结
保护渣不合适
漏钢的原因:
润滑不够; 结晶器锥度不合适; 拉速波动太大; 结晶器液面波动太大; 结晶器一冷太弱; 钢水脱氧不够; 大型夹杂物。
拉速的确定原则
1、根据结晶器出口坯壳厚度,来计算拉速。 根据结晶器的有效长度及其凝固常数、最薄的凝固坯 壳厚度来计算拉速(m/min),见下式。δ最小为1015mm,小方坯取下限,板坯取上限。
K结 2 V = L( ) δ最小
拉速的确定原则
2、根据冶金长度,来计算连铸机的最大拉速。 首先确定连铸机的平均凝固系数K(方坯可取30,板 坯可取27,单位mm/min1/2)及冶金长度L(m),铸坯 的厚度D(mm),见下式。
浸入式水口流出的钢流对钢水表面波动带来的 影响可用钢水表面波动指数-F指数加以描述。
F =
ρ Q LV e (1 − sin θ )
4
1 • D
水模型得到的F数与表面缺陷的关系
NKK研究结果 川崎制铁研究结果
为连铸工艺参数优化提供了坚实的基础,但是由于撞击点速度、角度和 撞击点距弯月面的距离难以测定等原因,结果难以在其他企业推广。
连铸技术发展
6、80年代-连铸技术成熟阶段
生产高质量钢铸坯技术和体制已经确立; 板坯连铸开始采用HCR、HDR工艺; 高速连铸、中间包加热、液压振动、电磁制动 、拉漏预报、二 冷动态控制、轻压下等大批新工艺技术得到广泛应用; 年产300万吨以上的大型连铸板坯铸机建立; 发达国家连铸比超过或接近90%; 以高拉速、高作业率、高质量、高度自动化、 高稳定性生产为 标志,常规连铸达到了其成熟阶段。
仪表系统
符号表示:
自动控制
大包浇铸终了判定 长水口连接、脱开 测温、取样 长水口气体流量控制 二次冷却控制 凝固终点控制 机内保温装置监测
压缩铸造控制 导辊开口度、对弧测定 铸坯表面温度测定 喷嘴堵塞检测 异钢种连浇分离铁板插入
自动开浇、停浇控制 拉速控制 保护渣加入 钢水液面控制 结晶器综合诊断 保护渣流入情况监测 在线调宽控制 浸入式水口更换 浸入式水口Ar流量控制 结晶器锥度、振动监测