连铸连轧知识点
连铸连扎一-绪论

连铸连轧-绪论 连铸连轧 绪论
第一章
Logo
Contents
1 2 3 4
连铸连轧简介
连铸连轧的优点
连铸技术存在的问题
连铸连轧存在与发展的意义
Company Logo
Logo
1.1 定义及分类
连铸连轧
定义:由连铸机生产出来 定义:
的高温无缺陷坯, 的高温无缺陷坯,无需清理 和再加热(但需经过短时均 和再加热( 热和保温处理) 热和保温处理)而直接轧制 成材,这样把“ 成材,这样把“铸”和“轧 ”直接连成一条生产线的工 艺流程。 艺流程。
连铸: 连铸:95 t 钢坯 模铸: 模铸:86 t 钢坯
Company Logo
Logo
3 连铸技术存在的问题
缺陷
要保证连铸坯直接轧制和热装, 要保证连铸坯直接轧制和热装,无缺 陷铸坯比率越高越好。 陷铸坯比率越高越好。 为保证铸坯有足够的轧制温度, 为保证铸坯有足够的轧制温度,一般 要保证温度在1000~1100℃以上, 要保证温度在 ~ ℃以上, 且断面温度要均匀。 且断面温度要均匀。
美国 中国 日本
英国
世界钢产量与连铸比的关系
我国钢产量与连铸比的关系
Company Logo
Logo
2 连铸连轧的优点
1、简化生产工艺流程。仅连铸工 、简化生产工艺流程。 序就取代了模铸工艺中的整模、 序就取代了模铸工艺中的整模、 铸锭、脱模、均热、开坯等工序。 铸锭、脱模、均热、开坯等工序。
英国
1979 新日铁大分厂建成世界第一个 最新型的钢铁联合企业, 最新型的钢铁联合企业,采用 大型转炉配连铸机, 大型转炉配连铸机,实现全连 铸。
1964 谢尔顿钢铁厂实现全连铸生产。 谢尔顿钢铁厂实现全连铸生产。
连铸连轧——精选推荐

连铸连轧第⼀章模铸与连铸的⽐较模铸:钢⽔→整模→浇铸→脱模→均热→初轧→成品轧制连铸:钢⽔→连铸→成品轧制液态铸轧:钢⽔→铸轧成品模铸铸锭的凝固将炼成的钢⽔浇注到铸铁或砂型制成的钢锭模内,凝固后形成的锭⼦称为钢锭。
钢锭经轧制或锻压成为钢材后⽅能使⽤,所以钢锭是半成品。
根据浇注⽅法的分为上注钢锭和下注钢锭。
下注锭的表⾯质量优于上注锭。
根据脱氧程度的不同⼜有沸腾钢钢锭、半镇静钢钢锭和镇静钢钢锭三种。
沸腾钢是脱氧不完全的钢,镇静钢是脱氧完全的钢,半镇静钢的脱氧程度介于前两者之间,接近于镇静钢。
钢锭的应⽤现状模铸锭与连铸坯相⽐,所占⽐例逐年减少,最终将减少到约占10%,其中合⾦钢和不锈钢将减少到20%,⼯具钢和特殊钢将减少到40%。
这是由于连铸坯可以多炉连浇、收得率⾼、不需初轧或开坯、能耗低,质量甚⾄优于模铸锭。
但模铸镇静钢不可能完全被淘汰,因为锻造⽤钢、⼀些⼩批量⽣产的⾼级合⾦钢及VAR(真空电弧重熔)和ESR(电渣精炼)⽤的坯料仍需⽤模铸镇静钢来⽣产。
钢锭的质量钢锭的质量有表⾯质量和内部质量之分。
表⾯质量:结疤、裂纹、表⽪的纯净度和致密度。
内部质量:钢锭内部的纯净度、致密度、低倍⾮⾦属夹杂物数量和宏观偏析的程度。
沸腾钢的表⾯质量好,但由于锭⼼偏析⼤,内部质量不如镇静钢。
连铸:使⾦属液由中间包经浸⼊式⽔⼝不断地通过⽔冷结晶器,凝成硬壳后从结晶器下⽅出⼝连续拉出,经喷⽔冷却,全部凝固后切成坯料的⼀种铸造⼯艺。
连铸的设备以弧形连铸机为例,主要有钢包⽀承装置、盛钢桶(钢包)、中间罐、结晶器(⼀次冷却装置)、结晶器振动装置、铸坯导向和⼆次冷却装置、引锭杆、拉坯矫直装置(拉矫机)、切割设备和铸坯运出装置(见辊道和横向移送设备)等连铸的优点变间断⽣产为连续⽣产,产量↑(连铸⽐,连浇炉数)冷却强度⼤,铸造组织⽐较细密,偏析⼩切头切尾率少,成才过程烧损和切损少,成材率提⾼8~12%⼯艺过程缩短,⽣产周期短,能耗、运输成本降低,能耗降低30~60%(视是否热装、热送、直接轧制⽽定)环保条件好,⽆整、脱模时的污染便于⾃动化,提⾼技术⽔平连铸的好处在于节能和提⾼⾦属收得率。
高级连铸连轧工应知应会

编订:__________________审核:__________________单位:__________________高级连铸连轧工应知应会Deploy The Objectives, Requirements And Methods To Make The Personnel In The Organization Operate According To The Established Standards And Reach The Expected Level.Word格式 / 完整 / 可编辑文件编号:KG-AO-8993-37 高级连铸连轧工应知应会使用备注:本文档可用在日常工作场景,通过对目的、要求、方式、方法、进度等进行具体的部署,从而使得组织内人员按照既定标准、规范的要求进行操作,使日常工作或活动达到预期的水平。
下载后就可自由编辑。
应知:1、连铸连轧工生产线设备的结构、性能、原理及调整试车方法;2、设备一、二级保养规范和设备验收方法;3、连铸连轧生产线所用工装的种类、制作标准和设计基本原理;4、原材料标准及主要试验方法;5、常用燃料的种类及燃烧的基本原理、对燃烧的控制方法及节能的途径;6、电线电缆的基本理论知识;7、有关的主导产品基本理论知识;8、控制制品性能、外观和尺寸的工艺方法;9、铜、铝及其合金精炼的基本原理;10、金属学、熔炼及压力加工原理;11、新产品工艺规程编制的基本方法;12、连铸连轧生产线的工艺参数、设备状况、工装质量对产品质量的影响;13、国内、外新技术、新工艺、新材料、新设备的发展应用情况;14、计算机在生产中应用知识。
应会:1、操作连铸连轧生产线所有设备、并生产出合格产品;2、参加设备的技术改造和修理;3、根据制品情况改进工艺和工装;4、编制不同质量要求产品的工艺规程;5、推广、应用新技术、新工艺、新材料、新设备;6、判断和解决质量及关键技术问题;7、指导和组织连铸连轧全面质量管理工作。
连铸连轧技术
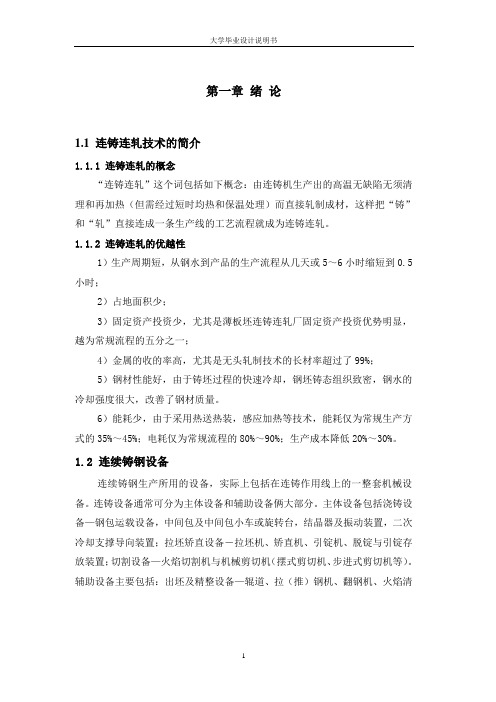
第一章绪论1.1 连铸连轧技术的简介1.1.1 连铸连轧的概念“连铸连轧”这个词包括如下概念:由连铸机生产出的高温无缺陷无须清理和再加热(但需经过短时均热和保温处理)而直接轧制成材,这样把“铸”和“轧”直接连成一条生产线的工艺流程就成为连铸连轧。
1.1.2 连铸连轧的优越性1)生产周期短,从钢水到产品的生产流程从几天或5~6小时缩短到0.5小时;2)占地面积少;3)固定资产投资少,尤其是薄板坯连铸连轧厂固定资产投资优势明显,越为常规流程的五分之一;4)金属的收的率高,尤其是无头轧制技术的长材率超过了99%;5)钢材性能好,由于铸坯过程的快速冷却,钢坯铸态组织致密,钢水的冷却强度很大,改善了钢材质量。
6)能耗少,由于采用热送热装,感应加热等技术,能耗仅为常规生产方式的35%~45%;电耗仅为常规流程的80%~90%;生产成本降低20%~30%。
1.2 连续铸钢设备连续铸钢生产所用的设备,实际上包括在连铸作用线上的一整套机械设备。
连铸设备通常可分为主体设备和辅助设备俩大部分。
主体设备包括浇铸设备—钢包运载设备,中间包及中间包小车或旋转台,结晶器及振动装置,二次冷却支撑导向装置;拉坯矫直设备-拉坯机、矫直机、引锭机、脱锭与引锭存放装置;切割设备—火焰切割机与机械剪切机(摆式剪切机、步进式剪切机等)。
辅助设备主要包括:出坯及精整设备—辊道、拉(推)钢机、翻钢机、火焰清理机等;工艺设备—中间包烘烤装置、吹氖装置、脱气装置、保护渣供给与结晶润滑装置等;自动控制与测量仪表—结晶器液面测量与显示系统、过程控制计算机、测温、测重、测长、测速、测压等仪表系统。
在连续铸钢的生产线上,出拉坯矫直机脱锭后的连铸坯需按用户或下部工序的要求,将铸坯切成定尺或倍尺。
因此在所有的连铸设备中,切割设备是非常重要的一种设备。
由于连铸坯必须在连续的运动过程中实现切割,因而连铸工艺对切割设备提出了特殊的要求,既不管采用什么型式的切割设备都必须与连铸坯实行严格的同步运动。
连铸连轧知识点
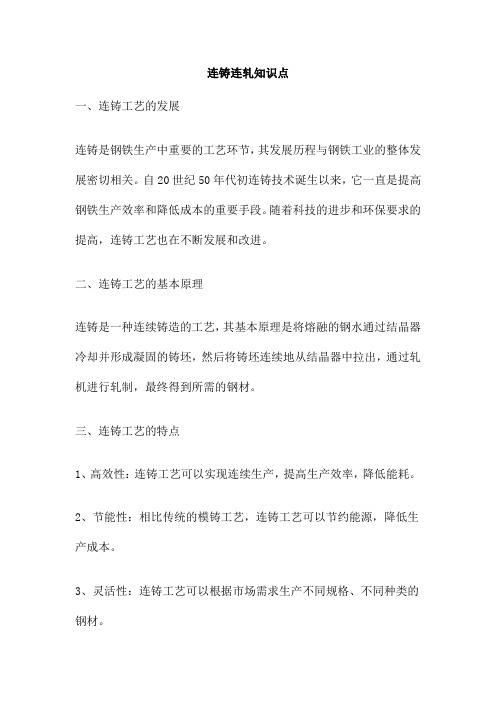
连铸连轧知识点一、连铸工艺的发展连铸是钢铁生产中重要的工艺环节,其发展历程与钢铁工业的整体发展密切相关。
自20世纪50年代初连铸技术诞生以来,它一直是提高钢铁生产效率和降低成本的重要手段。
随着科技的进步和环保要求的提高,连铸工艺也在不断发展和改进。
二、连铸工艺的基本原理连铸是一种连续铸造的工艺,其基本原理是将熔融的钢水通过结晶器冷却并形成凝固的铸坯,然后将铸坯连续地从结晶器中拉出,通过轧机进行轧制,最终得到所需的钢材。
三、连铸工艺的特点1、高效性:连铸工艺可以实现连续生产,提高生产效率,降低能耗。
2、节能性:相比传统的模铸工艺,连铸工艺可以节约能源,降低生产成本。
3、灵活性:连铸工艺可以根据市场需求生产不同规格、不同种类的钢材。
4、环保性:连铸工艺可以减少废弃物的产生,降低环境污染。
四、连铸工艺的应用范围连铸工艺广泛应用于各种钢铁产品的生产,包括板材、带材、型材、管材等。
随着技术的发展,连铸工艺也逐渐应用于有色金属、稀有金属等领域。
五、连铸工艺的未来发展方向随着科技的不断发展,连铸工艺的未来发展方向主要集中在以下几个方面:1、智能化:利用先进的自动化技术和智能化设备,提高生产过程的自动化水平和生产效率。
2、绿色化:进一步降低能耗和废弃物排放,实现生产过程的环保和可持续发展。
3、高效化:研发更高效的连铸技术,提高生产速度和产品质量。
薄板坯连铸连轧轧制区组织模拟薄板坯连铸连轧是一种高效、节能的钢材生产工艺,具有较高的生产效率和产品质量。
在轧制过程中,钢材的组织形态和性能特点对产品的质量和使用性能具有重要影响。
因此,薄板坯连铸连轧轧制区组织模拟成为了一个备受的研究领域。
通过组织模拟,可以深入了解轧制过程中材料的组织变化和性能特点,为工艺优化和产品性能提升提供理论支持和实践指导。
薄板坯连铸连轧轧制区背景及基础概念薄板坯连铸连轧是指将液态钢水倒入薄板坯连铸机中进行连续铸造,然后将连铸坯送入轧机进行连续轧制。
薄板坯连铸连轧复习资料

4)工序见时间(时钟推进)——温度协调优化基础上的最佳物流流量;
5)工序装置“在线”/“离线”的协同化和利用率;
6)工序间生产体(如:钢液、铸坯、轧件等)的收得率最大化。
即:物流通过时间的“最小化”(min/t);系统能耗的“最小化”(kJ/t);最大的工艺设备“在线率”(%);投资额、投资效率的优化(元/t)。
9、薄板坯连铸连轧的质量优势:薄板坯连铸连轧技术除了其短流程、近终形、节约能源、低成本的优势以外,另一个重要的优点就是质量好。薄板坯的原始铸态组织晶粒就比传统板坯更细、更均匀。原始组织精细为最终组织的细化创造了条件。同时,由于冷却强度大,板坯的微观偏析也可以得到较大的改善,分布也更均匀。因此,产品的性能均匀、稳定。
3、第一代、第二代薄板坯连铸连轧的特点:
第一代:工艺流程紧凑、简化,投资成本低,能源消耗低,产品质量高。它首次将连铸、温度均匀化和热轧三个工艺阶段连接在一起,可有效地生产高质量的热轧带钢。
第二代:1)各种薄板坯连铸连轧工艺的结晶器断面尺寸都有了相应变化,根据液芯压下量的大小在浇铸前和浇铸中灵活设定铸坯厚度来适应终轧带卷厚度的要求。2)实现了半无头轧制和铁素体轧制,并且终轧产品厚度可做到超薄带尺寸(≤0.8mm)3)温度均匀段——加热炉的长度加大。
10、液芯压下的优点:
1)改善表面质量:结晶器厚度增大、弯月面稳定性好、润滑更好;
2)改善内部质量:中心偏析和疏松减小、柱状晶破碎、晶粒细化;
3)生产灵活性:铸机可按最合理的方式进行生产。
11、薄板坯连铸连轧压下规程:1)第一架轧机由于来料厚度过大(传统热连轧一般40mm一下,而薄板坯连铸为50mm),为了有利于稳定咬入,通常压下率较小,在40%以下;
连铸连轧技术

连铸连轧技术
目录
1、连铸连轧技术的概念和优点 、
2、连铸连轧的关键技术 、
2.3
铸轧工艺
最早的铸轧技术是液芯铸轧技术, 最早的铸轧技术是液芯铸轧技术,出结晶器下口 60mm的铸坯带液芯时经软压变至 的铸坯带液芯时经软压变至45~50mm,形成固 的铸坯带液芯时经软压变至 , 相后再轧至15mm厚。液芯铸轧可以看成是降低能耗、 相后再轧至 厚 液芯铸轧可以看成是降低能耗、 提高产品质量的一种生产薄板带的技术发展方向。 提高产品质量的一种生产薄板带的技术发展方向。 新开发出的铸压轧技术,则将“ 新开发出的铸压轧技术,则将“铸、压、轧”融 为一体,出结晶器下口的坯壳仅为10~15mm的铸坯 的铸坯, 为一体,出结晶器下口的坯壳仅为10~15mm的铸坯, 此时在1300°C左右受辊压,是芯部焊合,随后由四 左右受辊压, 此时在 ° 左右受辊压 是芯部焊合, 辊轧机将铸坯轧成15~24mm的热轧板卷。 的热轧板卷。 辊轧机将铸坯轧成 的热轧板卷
2.2
薄壁浸入式水口
在连铸技术中,为提高铸坯质量 在连铸技术中 为提高铸坯质量, 为提高铸坯质量 在中间包与结晶器之间设有浸入式 水口,其主要作用是 水口 其主要作用是:(1)防止钢水二 防止钢水二 其主要作用是 次氧化氮化和钢水的飞溅;(2)调节 次氧化氮化和钢水的飞溅 调节 钢水流动状态和注入速度;(3)防止 钢水流动状态和注入速度 防止 保护渣非金属夹杂物卷入钢水中, 保护渣非金属夹杂物卷入钢水中 对促进钢水中夹杂物的上浮起重要 作用;(4)对边铸拉坯成材率和铸坯 作用 对边铸拉坯成材率和铸坯 质量有决定性影响。 质量有决定性影响。
第九部分连续铸扎
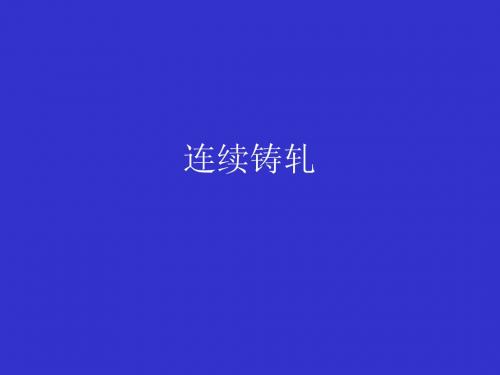
变形镁合金带坯铸轧技术的可行性分析
• 镁带坯连续铸轧技术作为冶金及材料研究领域 内的一项前沿技术。在这种工艺中, 液态金属 在辊式结晶器之间, 即两个轧辊的辊缝间一边 凝固一边被轧制, 轧辊主要是起冷凝熔体的作 用, 但又起轻量的轧压作用。它的组织具有快 速凝固与定向结晶的特点,晶体生长的方向性很 强. 连续铸轧是一个很复杂的过程,金属一方面 连续散热与凝固,另一方面还受到轧制, 而不是 铸造过程与热轧过程的简单混合,它们互相影响 着.在连续铸轧过程中金属凝固涉及到的学科有 材料学、热力学、动力学、振动理论、流体理 论、晶体生长理论等问题.
• 目前只能通过热模拟的方法研究所浇合 金的高温变形行为, 充分认识实验合金在 凝固冷却过程中凝固坯壳的高温力学性 能的变化规律, 以便在生产过程中合理地 控制浇注温度、铸轧速度、冷却强度及 辊缝预留量, 进而达到控制凝固终点的位 置, 实现铸轧过程中轧制变形的合理控制, 才能从根本上减少铸轧过程中出现裂纹。
• 另外,在铸轧过程中,液体金属在结晶凝固的 同时发生塑性变形, 即在薄带内部还是液芯时 就开始轧制变形. 此时如果凝固终点控制不当, 也就是压下量分配不合理, 就有可能使薄带因 严重不均匀变形产生内部裂纹和表面裂纹, 影 响产品质量. 大量铸轧试验证实,固液两相区的 变形对产品质量有关键性的作用;薄带变形过 程中形成的内裂纹主要源于两相区.但是由于铸 轧过程中变形区温度很高, 且液固两相区位于 凝固壳的内部, 很难在线测出液固两相区的实 际变形情况.
• CSIRO的双辊式铸轧机(twin roll caster)采 用专利技术可生产铸造状态的镁合金薄板带, 自2000年以来,该研究组织就致力于开发即能 连续生产(大批量)又能中、小批量生产镁薄 板的工艺,同时该工艺不但能生产优质的常规 镁合金薄板,还应能够生产新型镁合金薄板。 目前已商业化批量铸轧出了常规镁合金 (AZ31、AZ61、AM60、AZ91)与一批新镁 合金带卷,厚度为2.3-5mm,并用CSIRO开发 的特殊工艺顺利的轧成0.5-0.6mm的薄板带。
- 1、下载文档前请自行甄别文档内容的完整性,平台不提供额外的编辑、内容补充、找答案等附加服务。
- 2、"仅部分预览"的文档,不可在线预览部分如存在完整性等问题,可反馈申请退款(可完整预览的文档不适用该条件!)。
- 3、如文档侵犯您的权益,请联系客服反馈,我们会尽快为您处理(人工客服工作时间:9:00-18:30)。
连铸连轧部分知识点1、连铸生产工艺对连铸设备的要求:1)必须适合高温钢水由液态变成液固态,又变成固态的全过程;2)必须具有高度的抗高温,抗疲劳强度的性能和足够的强度;3)必须具有较高的制造和安装精度,易于维修和快速更换,充分冷却和良好的润滑等。
2、连铸流运行轨迹将连铸机分为哪几种?简述每种机型的特点?1)立式连铸机、立弯式连铸机、弧形连铸机、椭圆形连铸机和水平连铸机。
2)A、立式连铸机:此铸机坯壳冷却均匀,且不受弯曲矫直作用,故不宜产生内部和表面裂纹,有利于夹杂物上浮,但其设备高度大,操作不方便,投资费用高,设备维护及事故处理难,铸坯断面和定长及拉速受限,并且铸坯因钢水静压力大,板坯股肚变形较突出。
B、立弯式连铸机:铸机的中间包,结晶器,导辊,引锭杆沿垂线分布。
拉矫机切割机沿水平布置,浇注和冷却凝固在垂直方向上完成,完全凝固后被顶弯90°,进入弯曲段,在水平方向出坯,它的铸机高度比立式下降,运输方便,可适合较长定尺的要求,但由于增加了一次弯曲和矫直,一造成裂纹。
C、弧形连铸机:分为单点矫直弧形连铸机,多点矫直弧形连铸机,直结晶器弧形连铸机。
a)单点矫直弧形连铸机:优点:高度比立式、立弯式低,故设备重量轻,投资费用低,安装和维修方便,钢水对铸坯的静压力小,可减少因股肚造成的内列和偏析,有利于提高拉速改善铸坯质量。
缺点:钢水凝固过程中,非金属夹杂物有向弧内聚焦的倾向,一造成铸坯内部杂物分布不均匀。
b)多点矫直弧形连铸机:优点:固液界面变形率降低铸坯带液芯矫直时,不产生内部裂纹,有利于提高拉速。
c)直结晶器弧形连铸机优点:具有立式的优点,有利于大型夹杂物的上浮及钢中夹杂物的平均分布,比立弯式高度更高,建设费用低。
缺点:铸坯外弧侧坯壳受拉伸,两相区易造成裂纹缺陷,设备结构复杂,检修,维修难度大。
D、椭圆形连铸机:其优点是高度较弧形大大减小,钢水静压力低,铸坯股肚量小,内部裂纹中心偏析得到改善,投资节约20%----30%(比弧形)。
但结晶器内钢水中的夹杂物几乎无上浮机会,故对钢水要求严格。
E、水平连铸机:其优点是设备高度最低,钢水物二次氧化,铸坯质量得到改善,不受弯曲及矫直作用,有利于防止裂纹,设备维护简单,事故处理方便,但中间包和结晶器连接处的分离较贵,结晶器和铸坯间润滑困难,拉坯时结晶器不振动,适合小坯量,多种浇注,200mm以下方坯,圆坯,特殊钢。
3、连铸连轧的定义:由连铸机生产出来的高温无缺陷坯,不需要清理和再加热(但需经过短时均热和保温处理)而直接轧制成材,这样把“铸”“轧”直接连成一条生产线的工艺流程就称为连铸连轧。
4、连铸和连轧紧凑联结的方法:连铸坯热装、直接轧制。
连铸坯热装工艺是指连铸机生产的钢坯不经过冷却,在热状态下卷入加热炉加热,然后进行轧制的方法。
连铸坯直接轧制工艺是指铸机出来的高温铸坯不再经过加热或只对边棱进行轻度的补充加热就直接送往轧机轧制成材。
5、连铸连轧的优点:1)简化生产工艺流程,生产周期短;2)占地面积少;3)固定资产投资少;4)金属的收得率高;5)钢材性能好;6)能耗少;7)工厂定员大幅降低;8)劳动条件好,易于实现自动化。
6、提高拉坯速度的限制因素:1)拉坯力的限制;2)铸坯断面影响;3)铸坯厚度影响;4)结晶器导热能力的限制;5)速度对铸质的影响;6)钢水过热度的影响;7)钢种的影响。
7、二冷区包括:足辊段、支撑导向段和扇形段。
二冷区冷却方式:1)干式冷却;2)水喷雾冷却;3)水—气喷雾冷却(效果最好)。
8、倒锥度:为了减少气隙,加速钢水的传热和坯壳生长,通常结晶器的下口断面比上口断面小。
倒锥度过小会导致坯壳过早脱离铜壁产生气隙,降低冷却效果,或使结晶器的坯壳厚度不够产生拉漏事故;倒锥度过大容易导致坯壳与结晶器铜壁之间的挤压力过大从而加速铜壁的磨损。
9、结晶器满足要求:1)结构简单重量轻;2)良好的导热性和水冷条件;3)应做上下往复运动并加润滑剂;4)结晶器有足够的刚度,以免影响铸坯质量。
10、结晶器震动方式:同步式、负滑脱式、正弦振动式11、结晶器调宽方法:1)停机变宽;2)平移变宽;3)转动加平移变宽(最具代表性)。
12、立式轧边机中立辊的基本形状:1)平辊;2)锥形辊;3)带平或凸槽的底表面的孔型辊;4)带斜槽底表面的孔型辊。
13、轧制调宽中特殊的辊型法:1)扇贝形轧辊增宽;2)具有交错辊环的轧辊增宽;3)具有中部凸出块的轧辊增宽;4)具有可变环型凸出块的轧辊增宽锥形辊增宽;5)大凸度辊增宽;6)锥形辊增宽。
14、短锤头调宽压力机分为:1)起—停式调宽压力机;2)连续式调宽压力机;3)摇动式调宽压力机。
特点:1)起停式条款压力机:工件在工作中保持静止,定位精确,夹持辊可以防止板坯和弯曲;2)连续式条款压力机:对工件的压缩与工作的前进是同步的,作业周期短,效率高,工作连部表面质量高;3)摇动式条款压力机:以上两个优点结合。
15、长锤头压力机对板坯减宽时通常需要一个行程。
16、轧件调宽过程中易出现的失稳情况:板坯的倾翻、板坯的翘曲。
板坯的倾翻预防办1)用孔型辊或带底腔的锥度辊来防止脱分;2)采用倾斜立辊防止板坯升高。
板坯翘曲预防办法:1)中心支撑,两端支撑,三点支撑;2)采取防止下弯的措施;3)把两个立辊斜置。
17、减少调宽切量的方法:1)利用凸形板坯法;2)润滑轧制法;3)后推板坯轧制法;4)凸形断面轧制法;5)利用可变孔形尺寸轧制法;6)板坯端部预成型法。
18、轧制过程瞬时速度变化的影响因素:1)轧制规格对速度的影响;2)换辊对速度的影响;连铸过程瞬时速度变化的影响因素:1)中间包液面高度变化对拉速的影响;2)水口通流截面变化对拉速的影响;3)钢温变化对拉速的影响;4)过渡过程对坯料的处理。
19、热带轧制中采用的保温罩系统:绝热保温罩,反射保温罩,逆辐射保温罩(保温效率最高)。
20、连铸坯在线保温技术:1)为了保证铸坯达到剪切机前,液芯完全凝固,应该知道该冶金长度,为了保证拉速,适应轧制需要,增加结晶器的长度;2)软二冷,进入矫直机的温度应保证在1000℃以上;3)铸坯被切断后,利用高速辊道运输,或采用保温辊道运输,降低温度损失;4)铸坯边角散热快,采取(补)加热措施。
21、连铸坯热送热装特点:1)节能效果显著;2)提高了炉子的加热能力;3)提高了成材率;4)缩短了生产周期;5)降低炉子的热效率。
22、连铸坯的质量概念包括:1)铸坯洁净度;2)铸坯表面质量;3)铸坯内部质量;4)铸坯断面形状。
连续铸坯表面质量决定于钢水在结晶器的凝固过程;铸坯内部质量主要决定于钢水在二冷区的凝固过程。
23、连铸夹杂物形成显著特征:1)连续递加速度快,夹杂物长大机会少,尺寸小,不易上浮;2)连铸多了中间包,钢液与大气、熔渣接触时间长,易被污染;3)模铸钢锭夹杂多集中在头尾部,通过切头尾可减轻夹杂物危害,而连铸仅靠切头尾难以解决问题。
24、星状裂纹形成原因:主要是因结晶器的铜渗入钢液所致,铸坯在少许应力作用下晶间即会发生断裂。
预防措施:采用镀Cr、Ni结晶器。
(较薄时采用镀Cr较厚时采用镀Ni)25、表面纵向裂纹发生在板坯那个部位?形成原因?答:主要发生在板坯宽面中央位置及内部。
原因:初生坯壳厚度不均匀,在薄的地方应力集中,当应力超过坯壳抗拉强度时产生纵向裂纹。
26、表面横向裂纹发生的原因:ALN沿晶界析出所致。
27、液面结壳:液面结壳就好像浮在结晶器保护渣层下边,钢水表面之上,当它与坯壳的凝固层接触时,就融在坯壳表皮层上冰一起被拉入结晶器之中。
凹坑:铸坯表面粗糙形成了铸坯表面出现皱纹,严重的呈现出山谷状的凹陷。
重皮:对于横向凹陷,由于沿拉坯方向收到结晶器摩擦力的作用,很容易产生横裂纹。
如果这时有钢水渗漏出来,遇到结晶器壁若能重新凝固,就形成所谓的重皮。
28、内裂纹形成的三阶段:1)拉伸力作用到凝固界面;2)造成柱状晶间开裂;3)偏析元素富集的钢液填充到开裂的空隙小。
29、鼓肚变形:是连铸工艺过程的一种特有现象,它是由于铸坯已经凝固的坯壳受到了内部钢水的静压力作用,使两个支撑辊之间的坯壳宽面向外凸起。
铸坯鼓肚量大小的影响因素:1)铸坯横断面的尺寸与形状;2)钢水静压力;3)支持辊的间距;4)凝固的坯壳的厚度;5)钢的高温弹性模数;6)坯壳的温度;7)拉速。
减小鼓肚的措施:1)降低连铸机的高度;2)二冷区采用小辊距、密排列、铸机由上到下辊距应由密到疏;3)支持辊要严密对中;4)加大二冷区冷却强度;5)防止支持辊的冷却变形,板坯的支持辊最好选用多节辊。
30、连铸保护渣三层结构:由下到上→熔渣层;过渡层(烧结层);粉渣层。
31、薄板坯连铸机浸入式水口要求:1)与结晶器铜板间需有一定的间隔,以保证不凝钢;2)水口直径大小能提供足够的钢水流量;3)水口应有足够的壁厚,以使其有较长的使用寿命;4)浸入式水口的内部与外部形状,尤其是开口的布置和配置,决定了结晶器内钢水的流向和钢液的形状,以及注入结晶器后引起的功能配置。
32、对薄板坯结晶器要求:1)结晶器应具有良好的导热性和钢性;2)重量要轻,以减少振动时的惯性力;3)内表面耐磨性和耐腐蚀性要好且不应该出现结晶器的铜渗入到钢液之中的问题;4)结晶器结构要简单,以利于制造和维护34、薄板坯连铸保护渣的名称及特点:名称:1)是否发热:分为发热渣和绝热保护渣;2)外形:粉渣,实心颗粒和空心颗粒渣;3)从基料来看:混合型,预溶型和烧结型渣;4)是否含氟:有氟渣和无氟渣。
特点:1)绝热保温;2)隔绝空气,防止钢水二次氧化;3)净化钢渣界面,吸附钢液中夹杂物;4)润滑凝坯壳并改善传热;5)充填坯壳与结晶器之间气隙,改善结晶器传热条件。
35、电磁搅拌技术的作用:1)明显的提高铸坯质量;2)改善了晶体结构;3)提高了一冷端的冷却效率;4)中心碳偏析也显著减少。
36、液芯压下技术的定义:是在铸坯出结晶器下口后,对其坯壳施加压力加工,此时液芯仍保留在其中。
就是在液芯末端以前对铸坯施以压缩加工。
注意事项:液芯压下厚度必须小于产生裂纹的最大压下值,压下后的叠加应变低于产生裂纹的临界应变,最好在上部扇形段完成压下,且不要集中在很短的区域。
37、薄板坯连铸连轧生产中常用三种加热炉,那种占地面积大、最简单、技术最新?1)隧道式辊底加热炉(CSP、FTSR):加热段、均热段、缓冲段、出料端。
优缺点:使用最多,可靠性强,工艺顺畅,使用灵活,占地面积过大,生产线过长,维护费用高(耐热辊的定期更换)。
2)感应加热(ISP):是在加热炉中采用排列在辊道上的一组感应线圈实行加热技术。
优缺点:较长的缓冲时间,可灵活调整加热温度和深度,占地小,新技术不成熟,维护困难,投资相对大。
3)步进梁式加热炉(CONROLL):优缺点:最简单,技术成熟,投资少,使用维修费用低,易掌握,对铸坯单位重量有限制(单重增大、炉子过宽导致投资增多)。