曲轴滚压校直原理
压力矫直机——精选推荐

压力矫直机1、压力矫直机的工作原理压力矫直机与辊式矫直机同属于利用反复弯曲并逐渐减小压弯挠度方法达到矫直目的的设备。
它是最简单的矫直设备。
压力矫直机的工作原理是将带有原始弯曲的工件支承在工作台的两个活动支点之间用压头对准最弯部位进行反向压弯的。
当压弯量与工件弹复量相等时,压头撤回后工件的弯曲部位变直。
如此进行,工件各弯曲部位必将全部变直从而达到矫直的目的。
当然凭经验设定的压弯量很难准确的与工件的弹复量相等,所以在头一次反向压弯后要检测弹复量与压弯量的差值即残留挠度值,用此值修正第二次压弯量,用新压弯量进行再次反向压弯,再检测,直到矫直为止。
通常靠人的感观和经验确定压弯量时,常需3次以上的修正工作。
现代使用微机来设定压弯量则只需1至2次修正工作.而且速度快,质量稳定。
2、压力矫直机的分类早期的压力矫直机都是通用型的压力机。
随着矫直技术的发展.考虑到矫直工艺的特殊性:如行程小.不需退料,能翻钢或能换向,支点位置可调等特点而设计出专用矫直压力机。
最常见的仍为曲轴式压力矫直机。
在其连杆与滑块之间用螺纹连接.改变螺纹长度可以得到不同的开距,但行程固定不变。
其进一步的发展就是曲柄偏心式压力矫直机。
通过调节曲柄轴外的偏心套的相位角使可改变偏心距而得到不同的行程,以满足了不同断面尺寸工件的矫互直需要,提高了矫直工作效率。
上述两种矫直压力机要具备很大矫直力时常需要庞大的结构尺寸。
为了满足大型钢材的矫直需要,又不致使结构尺寸过大,而产生了大压力小行程的肘杆式矫直压力机。
在大型锻件及钢坯的矫直中翻钢是一道麻烦的工序,为解决不翻钢问题而创造了卧式换向压弯式矫直机。
操作者根据工件原始弯曲方向决定矫直所需的反弯方向与位置。
先开动辊道移送工件定好位置;然后开动齿轮齿条升降机构使小滑块升到工件的凸弯处,使大滑块变成两个支点;第三步开动蜗轮螺母把大滑块推到工件处并将其压靠;第四步开动曲轴连杆机构使小滑块对工件进行压弯以达到矫直目的。
曲轴滚压校直原理

1曲轴滚压校直原理曲轴滚压校直是根据曲轴的滚压变形规律,针对被校直曲轴的具体变形情况,在计算机专家系统指导下对该曲轴的轴颈圆角的某些部位施加适当的压力进行滚压,使其产生与原变形方向相反的变形,以达到校直的目的[1]。
实践证明,滚压校直后的工件基本上克服了变形回复的缺点,而且使被滚压的轴颈圆角部分得到了表面强化处理,提高了工件的疲劳强度和承载能力。
多缸发动机曲轴的轴颈和曲拐较多,弯曲刚度较低,而且在圆周方向上各向异性,加上材料的不均匀性,以及冷热加工中变形和残余应力等综合因素的影响,使得曲轴的弯曲变形十分复杂,其轴线是一条任意的空间曲线。
因而在应用滚压校直这一新技术时,建立科学的校直专家系统来指导滚压加工是问题的关键所在。
专家系统根据被测曲轴的具体情况,通过分析,解决如下问题:在曲轴的哪些轴颈、轴颈的哪个部位施加滚压力;施加滚压力的角度范围,以及在各角度下该施加多大的滚压力;施加滚压力的滚压圈数。
滚压校直后需要对曲轴再进行测量,如果仍然超差,则进行新一轮的滚压校直,直到合格为止。
22)滚压力和滚压圈数的影响。
在确定了需要滚压的轴颈及其角度范围后,还要确定在各滚压区域该施加多大的滚压力。
各主轴颈的径向跳动量与滚压力的大小有关,但两者之间并不成线性关系,而且存在较大的不确定性。
分析产生这一现象的原因,除了材料本身在塑性范围内的受力与变形不成线性比例外,还与工件的残余应力、缺陷、材质不均以及工件的结构尺寸偏差等因素有关。
因此,难以用简单的数学公式对滚压力与曲轴的弯曲变形之间的关系进行精确的表达。
另外,是用较大的滚压力、较少的滚压圈数,还是反之,二者之间为辨证关系。
从提高工效的角度考虑,前者为好;从减少回复变形量出发,后者为佳。
专家系统需要选择一个最优方案。
(3)曲轴结构尺寸的影响。
在其它条件固定的前提下,曲轴结构尺寸对曲轴滚压所产生的弯曲变形的总体影响趋势为:轴颈之间开档宽度越小,圆角尺寸越大,则弯曲变形就越大,并且轴颈开档尺寸对变形的影响大于轴颈圆角半径的影响。
曲轴圆角滚压工艺

,,,,,,,,,,,,,,,,,,,,,, ! 上接第 . / 页"
滚压被加工曲轴的连杆颈的 圆 角 # 调 整 油 缸 供 油 管 路 压 力可调节曲轴圆角滚压压力 " 从 而 可 控 制 曲 轴 圆 角 滚 压 变形量 # 主 轴 颈 的 圆 角 由 固 定 在 支 承 架 上 的 滚 压 头 滚 压 " 并作稳定支撑作用 " 防止 曲 轴 弯 曲 变 形 " 标 准 曲 轴 还起到滚压校正作用 # 通过多次试验 " 我们总结出 以 下 曲 轴 圆 角 滚 压 经 验 数据 * & "’ 滚压次数 ! 滚压次 数 较 少 时 " 达 不 到 应 有 的 塑 性变 形 % 次 数 过 多 时 " 容 易 破 坏 塑 性 变 形 带 # 在 生 产 中 " 以滚压 -%" , 圈为佳 # & #’ 滚压速度 (! 滚 压 速 度 过 快 " 容 易 引 起 较 大 的
!!!
0 " $ # 23 4 & ’ 5 ( 6
锻 !! 压
!!!!! !
曲轴圆角滚压工艺
扬动股份有限公司 ! ! 江苏 !! " ! 刘秋鹏 ! " " # #
!! 曲轴圆角滚压对曲轴提高疲劳强度有显著作用 " 曲轴 圆角滚压强化工艺已成为提高产品竞争力的重要手段# 常见的曲轴圆角滚压主要有以下三种类型 $ % "& 切线滚压 ! 切线滚压 就 是 在 精 磨 主 轴 颈 和 连 杆 颈时 用 砂 轮 磨 出 与 滚 轮 半 径 大 小 相 同 的 圆 角 % 偏差 见图 " & # 该方法易在轴颈 表 面 ! , **& 进行滚压 % J #, 和侧表面挤出一线凸台 " 需 在 后 续 工 序 中 进 行 磨 削 # 另 外 " 在轴颈感应淬火后进行 滚 压 " 容 易 引 起 很 大 的 弯 曲 变形 " 需进行滚压校直处理 # % #& 半精加工后滚压 ! 半 精 加 工 后 滚 压 就 是 在 曲 轴 精磨成形之前进行滚压强 化 " 这 样 可 避 免 滚 压 起 台 " 但 在后续工序中需将塑性变形 带 磨 去 一 部 分 " 这 就 大 大 削 弱了滚压强化效果 " 故目前很少采用 # % && 圆角沉割滚压 ! 即在 过 渡 圆 角 处 沉 割 出 与 滚 轮 半径大小相 同 的 圆 角 % 偏 差 #, ! , **& 进 行 滚 压 " 见 图" \# 圆角沉割滚压 消 除 了 以 上 两 种 滚 压 方 法 的 缺 陷 " 还可以使应力分散 # 目前国外 发 动 机 曲 轴 几 乎 全 部 采 用 圆角沉割滚压方法 # 能及正常使用 # 半精加工后滚 压 的 精 加 工 会 减 少 滚 压 层 的深度 " 严重影响曲轴的使 用 寿 命 " 导 致 柴 油 机 的 大 修 时间缩短 # 圆角沉割滚压虽然 避 免 了 上 述 两 种 滚 压 方 式 的缺陷 " 但对前道工序要求 较 高 " 必 须 有 专 用 的 精 密 机 床保证才能达到 " 资金投入 较 大 # 为 了 克 服 切 线 滚 压 及 半精加工后滚 压 存 在 的 缺 陷 " 同 时 又 不 增 加 资 金 投 入 " 我公司曲轴的圆角滚压采用 上 ’ 下 滚 压 头 夹 紧 后 进 行 圆 角滚压的方法 % " 曲 轴 滚 压 圆 角 为. 如图 # 所 示& + **" 将两只! " , ** 的 钢 球 嵌 进 纯 铜 衬 内 " 固 定 在 上 滚 压 头 上进行圆角滚压 " 下滚压头 为 嵌 进 两 只 ! " ’ ** 的 滚 柱 " 作为固定支承 #
曲轴校直工艺分析

1 概 述
机 的曲轴 示意 图 。
曲 轴 是 内 燃 机 的 重 要 零 件 , 担 着 内燃 机 功 率 承
输 出的作用 。在工作 中 , 曲轴 承受 缸 内气体作 用力 、
往 复 作 用 力 转 惯 性 力 和 摩 擦 力 的 周 期 性 反 复 冲 旋 击 , 高 燃 烧 压 力 为 5 a 1MP , 曲 轴 的 各 个 最 MP  ̄ 3 a 在
b s s f r t e p o u to fn d lr c s r n c a k h f wih s r i h e i g t c n l g a i o h r d c i n o o u a a tio r n s a t t t a g t n n e h o o y,r s a c n e t e e r h a d ts s h v e n t k n f r t e b t i d fs r i h e i g t c n l g - Be c t ag t n n n l r s r i h e a e b e a e o h o h k n s o ta g t n n e h o o y n h s r i h e i g a d Ro l t ag t e
维普资讯
20 0 2年 第 2期
内
燃
机
工
程
此 工艺流程 采 用铸造 球 铁 毛坯 , 用 数控 车床 使
旋 风 内铣 进 行 粗 加 工 , 有 一 道 精 校 直 工 序 , 只 工 艺 过 程 采 用 压 力 校 直 工 艺 , 淬 火 工 序 , 个 工 艺 无 整 路线较 短 。 22 . 曲轴 滚 压 校 直 工 艺
曲轴圆角滚压强化方式的基本原理

曲轴圆角滚压强化方式的基本原理
曲轴的圆角部位具有特殊性,所以很容易产生疲劳破坏,所以除了对圆角进行淬火外,我们还要采取另外一种强化方式-圆角滚压。
曲轴在发动机工作的过程中,会受到弯曲、扭转、拉压等交变应力的作用。
曲轴的圆角过渡处在曲轴中是相当薄弱的部位,尤其是连杆轴颈和主轴颈的过渡处,在生产过程中经过磨削加工后留下的刀痕处是最脆弱的地方,因此,我们要通过圆角滚压来增强圆角的强度。
图4.3.1-1曲轴圆角区域的显微硬度
曲轴的圆角滚压强化方法就是指在滚轮的压力作用下,在曲轴的连杆轴颈和主轴颈的过渡圆角处,形成一条滚压塑形变形带来达到强化圆角的效果的一种强化方式。
圆角滚压强化方法是提高曲轴的疲劳强度最行之有效的手段之一,它是实现曲轴生产过程中“以铁代钢”的关键工艺环节。
据统计资料显示,球墨铸铁曲轴材料的曲轴经过圆角滚压处理后,它的寿命可以提高百分之八十到百分之二百,钢制材料的曲轴经过圆角滚压处理后,它的寿命可以提高百分之七十到百分之一百五十。
由于圆角滚压强化工艺对生产技术要求较高,因此国内能实现曲轴圆角滚压工艺的厂家不多,而且采用的相关生产设备基本上都是从国外引进的,针对这一现象,我们进行了多项试验,以期设计出适合朝柴曲轴生产的方法。
轴类自动校直机工作原理

轴类自动校直机是对汽车及其他机械行业广泛应用的各种轴类零件在热处理过程中产生变形,而进行校直的设备。
校直机通过对变形点的压力校直,效果理想,效率高,工作稳定。
轴类自动校直机工作原理
辊子的位置与被校直制品运动方向成某种角度,两个或三个大的是主动压力辊,由电动机带动作同方向旋转,另一边的若干个小辊是从动的压力辊,它们是靠着旋转着的圆棒或管材摩擦力使之旋转的。
为了达到辊子对制品所要求的压缩,这些小辊可以同时或分别向前或向后调整位置,一般辊子的数目越多,校直后制品精度越高。
制品被辊子咬入之后,不断地作直线或旋转运动,因而使制品承受各方面的压缩、弯曲、压扁等变形,最后达到校直的目的。
轴类自动校直机的特点
操作简单易学、测量精度高、可适应多种工件等特点。
在自动校直过程中,操作者只需要操作工件的装卸以及“自动启动”按钮,工件的弯曲度测量、校直点定位、加压校直以及弯曲度检查等动作全部由校直机自动完成,这在很大程度上保证了测量结果的准确性、提高了生产效率,同时减轻了操作者的劳动强度。
该产品具有设定最大校直量限制的功能,有效的保护工件不会被压断或压裂,从而保证工作安全具有工件的弯曲量数字显示及柱形图直观显示功能,全中文的人机对话界面美观、清新、方便人员操作学习自动校直工作循环完成后,自动判别工件是否满足公差要求,给出声光指示可存储200种以上工件校直参数的超大型数据库系统,满足用户生产需求。
曲轴滚压变形分析与滚压校直工艺研究
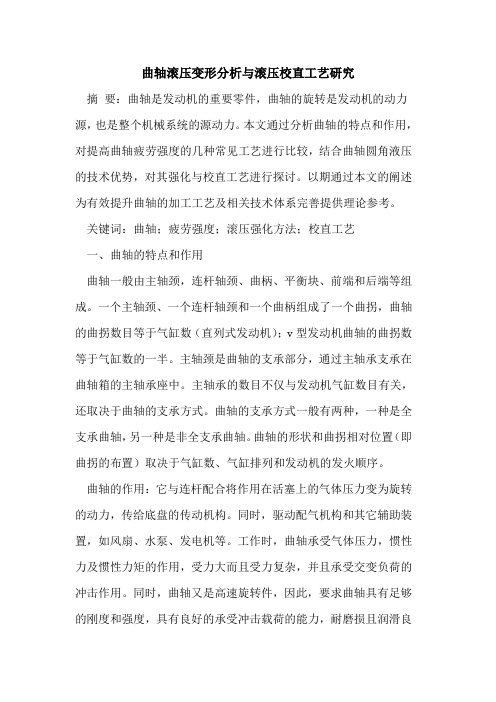
曲轴滚压变形分析与滚压校直工艺研究摘要:曲轴是发动机的重要零件,曲轴的旋转是发动机的动力源,也是整个机械系统的源动力。
本文通过分析曲轴的特点和作用,对提高曲轴疲劳强度的几种常见工艺进行比较,结合曲轴圆角液压的技术优势,对其强化与校直工艺进行探讨。
以期通过本文的阐述为有效提升曲轴的加工工艺及相关技术体系完善提供理论参考。
关键词:曲轴;疲劳强度;滚压强化方法;校直工艺一、曲轴的特点和作用曲轴一般由主轴颈,连杆轴颈、曲柄、平衡块、前端和后端等组成。
一个主轴颈、一个连杆轴颈和一个曲柄组成了一个曲拐,曲轴的曲拐数目等于气缸数(直列式发动机);v型发动机曲轴的曲拐数等于气缸数的一半。
主轴颈是曲轴的支承部分,通过主轴承支承在曲轴箱的主轴承座中。
主轴承的数目不仅与发动机气缸数目有关,还取决于曲轴的支承方式。
曲轴的支承方式一般有两种,一种是全支承曲轴,另一种是非全支承曲轴。
曲轴的形状和曲拐相对位置(即曲拐的布置)取决于气缸数、气缸排列和发动机的发火顺序。
曲轴的作用:它与连杆配合将作用在活塞上的气体压力变为旋转的动力,传给底盘的传动机构。
同时,驱动配气机构和其它辅助装置,如风扇、水泵、发电机等。
工作时,曲轴承受气体压力,惯性力及惯性力矩的作用,受力大而且受力复杂,并且承受交变负荷的冲击作用。
同时,曲轴又是高速旋转件,因此,要求曲轴具有足够的刚度和强度,具有良好的承受冲击载荷的能力,耐磨损且润滑良好。
二、提高曲轴疲劳强度常见的工艺曲轴服役工况条件恶劣,其失效形式一般是轴颈磨损和疲劳断裂。
疲劳断裂往往是破坏性的,涉及安全方面,必须高度重视。
提高曲轴疲劳强度常见的强化工艺大致有以下五种:1、氮化曲轴氮化包括气体软氮化、离子氮化和盐浴氮化等。
氮化能提高曲轴疲劳强度的20%-60%,适用于各类曲轴。
2、喷丸曲轴经喷丸处理后能提高疲劳强度的20%-40%,但因喷丸时须保护轴颈表面,故采用较少。
3、圆角与轴颈同时感应淬火该强化方式应用于球铁曲轴时,能提高疲劳强度的20%,而应用于钢轴时,则能提高100%以上,故在钢轴中应用比较普遍。
滚压校直机简介
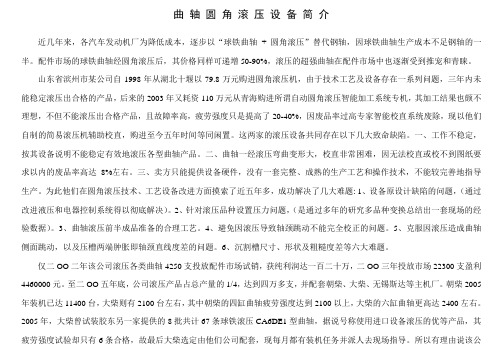
曲轴圆角滚压设备简介近几年来,各汽车发动机厂为降低成本,逐步以“球铁曲轴+ 圆角滚压”替代钢轴,因球铁曲轴生产成本不足钢轴的一半。
配件市场的球铁曲轴经圆角滚压后,其价格同样可递增50-90%,滚压的超强曲轴在配件市场中也逐渐受到推宠和青睐。
山东省滨州市某公司自1998年从湖北十堰以79.8万元购进圆角滚压机,由于技术工艺及设备存在一系列问题,三年内未能稳定滚压出合格的产品,后来的2003年又耗资110万元从青海购进所谓自动圆角滚压智能加工系统专机,其加工结果也颇不理想,不但不能滚压出合格产品,且故障率高,疲劳强度只是提高了20-40%,因废品率过高专家智能校直系统废除,现以他们自制的简易滚压机辅助校直,购进至今五年时间等同闲置。
这两家的滚压设备共同存在以下几大致命缺陷。
一、工作不稳定,按其设备说明不能稳定有效地滚压各型曲轴产品。
二、曲轴一经滚压弯曲变形大,校直非常困难,因无法校直或校不到图纸要求以内的废品率高达8%左右。
三、卖方只能提供设备硬件,没有一套完整、成熟的生产工艺和操作技术,不能较完善地指导生产。
为此他们在圆角滚压技术、工艺设备改进方面摸索了近五年多,成功解决了几大难题: 1、设备原设计缺陷的问题,(通过改进液压和电器控制系统得以彻底解决)。
2、针对滚压品种设置压力问题,(是通过多年的研究多品种变换总结出一套现场的经验数据)。
3、曲轴滚压前半成品准备的合理工艺。
4、避免因滚压导致轴颈跳动不能完全校正的问题。
5、克服因滚压造成曲轴侧面跳动,以及压槽两端肿胀即轴颈直线度差的问题。
6、沉割槽尺寸、形状及粗糙度差等六大难题。
仅二OO二年该公司滚压各类曲轴4250支投放配件市场试销,获纯利润达一百二十万,二OO三年投放市场22300支盈利4460000元。
至二OO五年底,公司滚压产品占总产量的1/4,达到四万多支,并配套朝柴、大柴、无锡斯达等主机厂。
朝柴2005年装机已达11400台,大柴则有2100台左右,其中朝柴的四缸曲轴疲劳强度达到2100以上,大柴的六缸曲轴更高达2400左右。
- 1、下载文档前请自行甄别文档内容的完整性,平台不提供额外的编辑、内容补充、找答案等附加服务。
- 2、"仅部分预览"的文档,不可在线预览部分如存在完整性等问题,可反馈申请退款(可完整预览的文档不适用该条件!)。
- 3、如文档侵犯您的权益,请联系客服反馈,我们会尽快为您处理(人工客服工作时间:9:00-18:30)。
1曲轴滚压校直原理曲轴滚压校直是根据曲轴的滚压变形规律,针对被校直曲轴的具体变形情况,在计算机专家系统指导下对该曲轴的轴颈圆角的某些部位施加适当的压力进行滚压,使其产生与原变形方向相反的变形,以达到校直的目的[1]。
实践证明,滚压校直后的工件基本上克服了变形回复的缺点,而且使被滚压的轴颈圆角部分得到了表面强化处理,提高了工件的疲劳强度和承载能力。
多缸发动机曲轴的轴颈和曲拐较多,弯曲刚度较低,而且在圆周方向上各向异性,加上材料的不均匀性,以及冷热加工中变形和残余应力等综合因素的影响,使得曲轴的弯曲变形十分复杂,其轴线是一条任意的空间曲线。
因而在应用滚压校直这一新技术时,建立科学的校直专家系统来指导滚压加工是问题的关键所在。
专家系统根据被测曲轴的具体情况,通过分析,解决如下问题:在曲轴的哪些轴颈、轴颈的哪个部位施加滚压力;施加滚压力的角度范围,以及在各角度下该施加多大的滚压力;施加滚压力的滚压圈数。
滚压校直后需要对曲轴再进行测量,如果仍然超差,则进行新一轮的滚压校直,直到合格为止。
22)滚压力和滚压圈数的影响。
在确定了需要滚压的轴颈及其角度范围后,还要确定在各滚压区域该施加多大的滚压力。
各主轴颈的径向跳动量与滚压力的大小有关,但两者之间并不成线性关系,而且存在较大的不确定性。
分析产生这一现象的原因,除了材料本身在塑性范围内的受力与变形不成线性比例外,还与工件的残余应力、缺陷、材质不均以及工件的结构尺寸偏差等因素有关。
因此,难以用简单的数学公式对滚压力与曲轴的弯曲变形之间的关系进行精确的表达。
另外,是用较大的滚压力、较少的滚压圈数,还是反之,二者之间为辨证关系。
从提高工效的角度考虑,前者为好;从减少回复变形量出发,后者为佳。
专家系统需要选择一个最优方案。
(3)曲轴结构尺寸的影响。
在其它条件固定的前提下,曲轴结构尺寸对曲轴滚压所产生的弯曲变形的总体影响趋势为:轴颈之间开档宽度越小,圆角尺寸越大,则弯曲变形就越大,并且轴颈开档尺寸对变形的影响大于轴颈圆角半径的影响。
通过对不同型号的曲轴进行滚压,并测量其弯曲变形,以取得大量的实验数据。
在此基础上建立经验关系数据库。
该数据库还应考虑由于曲轴的滚压变形受曲轴毛坯质量和加工工艺的影响很大,使得变形与校直工艺之间很难有一成不变的准确对应关系。
为了提高滚压校直的成功率,专家系统应具有自学习能力。
在运行过程中,根据实际情况对数据库进行修改,即将生产实践中的成功滚压校直的实例不断地动态补充到数据库中,去掉数据库中的不理想数据。
使系统具有一定的自适应能力,更有效地指导滚压校直。
3一、自动平衡校正技术与计算机辅助修正技术为了消除动力机械中作高速运动的关键零件由于自身不平衡而引起的振动,减少零部件的磨损,以确保产品的性能和质量,在这些零件的制造过程中往往设置有平衡校正工序。
在大批量生产情况下,为提高工效和校正质量,更需要采用各种自动平衡校正技术。
曲轴、转子等的动平衡,连杆、活塞的称重去重和某些轴类、杆类零件的自动校直就是自动平衡修正技术的代表性应用。
自动校直过程包括自动测定工件的校直量、自动实施校直操作和事后的检验。
应该指出,在精确地求出变形矢量的方向后,能实施规范化的修正操作。
因此,从理论上讲,只要检测结果准确,修正措施控制得当,修正的目标一定能够达到。
尤其是由于采用了微机化的、已逐步产品化了的专用设备,这些自动平衡校正作业已变得十分有效,并成为现代机械制造技术(在批量生产条件下的)一个重要组成部分。
计算机辅助修正技术所解决的则是另一类问题, 此时,检测结果的量值与需要修正的量值之间没有确定的函数关系,甚至没有确定的实施修正作业的方向。
这项技术的出现,一方面是加工工艺的发展所促成的,另一方面也是检测技术与计算机应用技术相结合的产物。
它的实质是理论分析和实践经验综合的工业化“专家系统”的实际应用,是计算机软件技术在加工业应用的一个新的领域。
计算机辅助修正技术现已用于不少场合,并取得了较好的效果,其中很典型的一个实例就是在发动机制造业滚压、校直工艺中的成功应用。
二、曲轴的滚压、校直技术曲轴是汽油机、柴油机的心脏,其制造质量要求很高。
曲轴又是典型的非均质结构的轴类零件,它的弯曲刚度较低,而且各向异性。
这一种结构特点,加上曲轴材料的不均匀性, 冷、热加工工序客观条件以及加工中所产生的残余应力等因素的综合影响。
使其在制造过程中出现的弯曲变形问题,远比一般轴类零件复杂。
它既可能是较简单的平面圆弧,也可能是很复杂的空间曲线。
上面提到的对轴类零件的校直工序,特别在批量生产情况下的自动校直,已是曲轴加工中不可缺少的一道关键工序。
曲轴的滚压、校直工艺是八十年代末才发展起来的一种新技术,九十年代开始在一些大企业逐步获得应用。
这一先进技术的形成和完善并非偶然。
众所周知,曲轴(拐)圆角滚压强化具有成本低、效率高和强化效果显著的优点,因而在发动机曲轴加工中应用日益广泛。
曲轴在加工过程(包括圆角滚压强化工序)中,难免要发生弯曲变形,为此校直是曲轴加工中不可缺少的工序。
而目前普遍采用的压力校直方法,尽管通过应用先进的检测技术和微机技术,已大大提高了校直质量和工效,但压力校直这一传统方式的工作机理决定了其存在的若干不足:在校直过程中产生的塑性变形,使工件强度的薄弱环节——轴颈圆角处产生拉应力,造成工件损伤甚至压裂压断。
还存在校直后的工件容易产生变形回复的问题。
曲轴的滚压校直技术是对曲轴圆角滚压强化工艺的补充和完善,它巧妙地将滚压强化和自动校直两道工序在一台高效专用设备中予以实现。
该设备是一种高性能的机电一体化系统,它首先对工件实施圆角滚压强化,然后通过在线检测,获得曲轴的变形规律。
再针对被校工件变形的具体情况,在计算机专家系统指导下,用适当的压力对工件的某些部位(圆角处)进行滚压,使工件产生与原变形方向相反的变形,从而达到校直的目的。
采用这种先进的工艺方法,不仅进一步提高了生产效率,尤其是使工件的被校部位得到了强化,从而提高了曲轴的整体强度和可靠性。
而且,滚压校直工艺对于被校工件在校正前的变形程度的限制远远低于传统的压力校直,表明其适用范围更大。
确实,这是一种处于九十年代国际先进水平的工艺。
三、曲轴弯曲变形滚压校直的数学模型和工作机理为了便于研究发动机曲轴的弯曲变形,引入了变形矢量的概念来描述主轴颈的变形状态。
规定各主轴颈的最大径向跳动量作为它们的变形矢量的模,在最大径向跳动量所处点的横截面上,圆心与最大跳动量的点的连线所指的方向为变形矢量的方向。
假定变形后各主轴颈的轴线仍保持与工件的轴线平行,则各主轴颈变形矢量可简化为一组与工件轴线体变形状态(D0),从数据库中寻找合适的校正矢量(rc),通过一次或多次的校直操作,(8)成立,并最终实现式软件需要注意如下事项。
由于多缸发动机曲轴变形状态十分复杂,轴颈变形矢量的方向往往不同,在大多数情况下,一个工件的校直需要采用多个校正矢量才能满足式(5)难是,首先在运用某一校正矢量时,颈的径向跳动量出现此消彼长的现象,能是多样的。
它要求专家系统能根据具体情况,相应的判断,控制校直运算进行的程度。
个工位:“A”和“B”。
其中,左侧“A”为待料工位,右侧“B”为加工工位,即滚压校直工位。
待料工位“A ”与生产线上的前后加工工位处于同一直线,在正常工作时,布置在车间空中的输送机构机械手4 (图3)首先把经前道工序加工后的曲轴放入位于工件“A”滑台1上的托架2内。
托架上设有一个叉形定位装置,当它在油缸推动下升起时,就将工件的圆周位置固定在曲柄平面处于垂直的状态。
然后滑台1在驱动机构作用下右移,托架2携带已定位的曲轴进入工位“B”,随即该设备的头、尾顶尖伸出,将工件固定,见图2b所示。
在滑台退回后,如图1所示的9组滚压头同时作用在5挡主轴颈和4挡连杆轴颈的退刀槽处,在液压系统施力下系统工作实施强化滚压(见图2a中的3)。
由油缸产生的液压力在对曲轴与主轴进行滚压时,压力为恒定值,范围在11000—14 000N之间,相当60~80bar的液压系统工作压力。
对工件4挡连杆轴颈的退刀槽实施滚压时,随动的滚压头作上下摆动,所设计的工艺规定,此时的压力不再为恒定值,而在一个规定的幅度内变化,其最大值与最小值所对应的圆周位置(矢径极角)是预先设定的。
滚压力范围在70 50—14150N之间,相当于40—82bar的液压系统工作压力。
在强化滚压过程中,工件需回转11转。
在这台专用设备的前部,即靠近工位A的地方还设置有一套电感测量系统3,安装在一个液压驱动的摆杆机构2的顶端,如图3所示。
当强化滚压过程结束后,滚压头脱开工件, 上述带有5个电感传感器的摇臂在油缸推动下回转到达加工工位,侧端分别与工件5个主轴颈的表面相接触。
接着,工件从一确定方位回转二周,依靠径向的电感测头和设备主轴系统中的角度编码器,或求出各主轴颈的变形矢量,也就是最大径向跳动量以及所处的方向——圆周范围内的指向。
如几处的主轴颈的跳动量不超过规定的工艺要求,则不再需要进行校直,但若出现一处或数处跳动超差的情况,就需要通过纠偏。
根据强化滚压后进行的检测所获得的曲轴变形规律,本文第二节中谈到的该高效专用设备所配置ab1、滑台2、支承托架3、滚压头4、液压机构图2曲轴滚压校直工艺的典型设备结构简图图14缸机曲轴滚压部位示意图1、滑台2、摆杆机构3、电感测量系统4、输送机构图3曲轴滚压校直工艺设备工作示意图图4流程图(下转第5页)的计算机专家系统将展开工作,针对工件变形超差的具体情况,某个滚压头将以适当的压力对曲轴的对应轴颈实施滚压,使工件产生与原变形方向相反的变形,从而达到校直的目的。
第一次滚压校直结束后,电感测量系统再次对工件的5挡主轴颈进行检测,以判断各处跳动量是否在规定的范围内。
如仍有超差现象,则还需要进行第二次校直滚压。
图4是曲轴滚压校直工艺的流程,简洁地描述了其运行的全计算机专家系统还有这样一个功能,若连续多次出现对工件的校直滚压都发生在同一轴颈这种情况,则专家系统就会自动修正设备开始运行时设定的工作参数,比如适当增大某一挡轴颈做强化滚压时的工作压力。
综上所述,曲轴的滚压校直工艺由于综合应用了当代的种种先进技术,使发动机“ 心脏”的一道关键工序出现了突破,无论是产品质量还是工作效率都得到了实质性的提高。
(上接第61页)一种九十年代先进制造工艺——曲轴滚压校直$上海大众汽车有限公司!201805 @朱正德具有九十年代国际先进水平的曲轴滚压校直工艺,是计算机辅助修正技术的典型应用。
本文就这种工艺的特点、工作原理、实施方法等作了较全面的论述,并介绍了应用实例。
<1>王植槐、朱正德等.汽车制造检测技术(P420).北京理工大学出版社.2000.11锤蒙璞傅耐贰⑽捕ゼ馍斐?将工件固定,见图2b所示。