烧结基础知识
烧结钕铁硼基础知识培训教材

坯料生产流程F:
烧结与时效
剥油、烧结工艺: 注意点:氧含量、真空度、温度、升降温速率 时间:氢碎料高温烧结20-22h,时效5~14h
在烧结过程中,成型毛坯粉末颗粒的物理连接 转变为化学连接,磁体收缩而致密,从而使磁体具 有所需要的物理性能,如磁性能、力学性能、耐腐 蚀性能。
坯料生产流程G:
二、烧结钕铁硼永磁材料产品生产工序
坯料生产——生产出性能符合客户要求且具有 一定形状的坯料;
机械加工——按客户图纸对坯料进行加工,加 工出形状满足客户要求的产品;
表面处理——按客户要求对磁体进行表面处 理,使产品具有客户要求的防腐蚀能力;
包装——按客户要求对产品进行包装,确保产 品完好的传递到客户手中。
撞而破碎
1. 主轴 2. 加料口 3. 侧喷嘴 4. 研磨加料 5. 底喷嘴 6. 涡轮分级器 7. 出料口 8. 测重传感器 9. 粉料碰撞区
坯料生产流程E:成 型 压 制
目前我司采用钢模加等静压的生产方
式,粉料松装密度一般在1.8g/cm3左右,
成型后的密度控制在4.0~4.2g/cm3
等静压完成后的密度一般在4.5~
ห้องสมุดไป่ตู้
4.9g/cm3左右,成型三个方向在烧结后的
收缩比如下: 压 制 方 向 约
取向方向约1.365
1.18
模宽方向约1.21
成型工艺
生产步骤:压机、模具准备(高性能氧含量控制)- 称粉-加料-充磁-压制成形-退磁-保压脱模-封 装-检查-等静压-清洗、检查
压机:南通、山西、宁波压机 模具:组合模具、自动模具 压制方式:手动、自动;垂直、平行 压机充磁场强度:1.2-1.8T 坯料规格:圆柱、方块为主
烧结基础知识

1. 烧结基础知识2. 烧结的含义将含铁粉状料或细粒料进行高温加热,在不完全熔化的条件下烧结成块的过程。
铁矿粉烧结就是一种人造富矿的过程。
2.1. 烧结的方法(1)鼓风烧结:烧结锅,平地吹;(2)抽风烧结:(a)连续式:带式烧结机与环式烧结机等;(b)间歇式:固定式烧结机,如盘式烧结机与箱式烧结机;移动式烧结机,如步进式烧结机;(3)在烟气中烧结:回转窑烧结与悬浮烧结。
2.2. 烧结生产的工艺流程一般包括:原燃料的接受、贮存,溶剂、燃料的准备,配料,混合,制粒,布料,点火烧结,热矿破碎,热矿筛分,热矿冷却,冷矿筛分,铺底料、成品烧结矿及返矿的贮存、运输等工艺环节。
机上冷却工艺不包括热矿破碎与热矿筛分。
现代烧结工艺流程不再使用热矿工艺,应使用冷矿工艺。
在冷矿工艺中,宜推广具有铺底料系统的流程。
2.3. 烧结厂主要技术经济指标烧结厂的主要技术经济指标包括利用系数、作业率、质量合格率、原材料消耗定额等。
2.3.1. 利用系数每台烧结机每平方米有效抽风面积(m2)每小时(h)的生产量(t)称烧结机利用系数,单位为t/(m2*h)。
它用台时产量与烧结机有效抽风面积的比值表示:利用系数==台时产量就是一台烧结机一小时的生产量,通常以总产量与运转的总台时之比值表示。
这个指标体现烧结机生产能力的大小,它与烧结机有效面积的大小无关。
利用系数就是衡量烧结机生产效率的指标,它与烧结机有效面积的大小无关。
2.3.2. 烧结机作业率作业率就是设备工作状况的一种表示方法,以运转时间占设备日历时间的百分数表示:设备作业率=×100%日历台时就是个常数,每台烧结机一天的日历台时即为24台时。
它与台数、时间有关。
日历台时=台数×24×天数事故率就是指内部事故时间与运转时间的比值,以百分数表示:事故率=×100%设备完好率就是衡量设备良好状况的指标。
按照完好设备的标准,进行定期检查。
设备完好率就是全厂完好设备的台数与设备总台数的比值,用百分数表示:设备完好率=×100%2.3.3. 质量合格率烧结矿的化学成分与物理性能符合原冶金部YB/T421标准要求的叫烧结矿合格品,不符合的烧结矿叫出格品。
烧结基础知识

烧结基础知识烧结是把粉状物料转变为致密体,是一个传统的工艺过程。
那么你对烧结了解多少呢?以下是由店铺整理关于烧结知识的内容,希望大家喜欢!烧结的定义宏观定义:在高温下(不高于熔点),陶瓷生坯固体颗粒的相互键联,晶粒长大,空隙(气孔)和晶界渐趋减少,通过物质的传递,其总体积收缩,密度增加,最后成为具有某种显微结构的致密多晶烧结体,这种现象称为烧结。
微观定义:固态中分子(或原子)间存在互相吸引,通过加热使质点获得足够的能量进行迁移,使粉末体产生颗粒黏结,产生强度并导致致密化和再结晶的过程称为烧结。
烧结的方法及测量将试条放入烘箱内,在105~110℃下烘干至恒重。
在干燥器内冷却至室温后备用。
在天平上称取干燥后的试样重。
称取饱吸煤油后在煤油中试样重。
饱吸煤油后在空气中的试样重。
将称好重量的试样放入105~110℃烘箱内排除煤油,直至将试样中的煤油排完为止。
按编号顺序将试样装入高温炉中,装炉时炉底和试样之间撒一层薄薄的煅烧石英粉或Al2O3粉。
装好后开始加热,并按升温曲线升温,按预定的取样温度取样。
在每个取样温度点保温15min,然后从电炉内取出试样迅速地埋在预先加热的石英粉或Al2O3粉中,以保证试样在冷却过程中不炸裂。
冷至接近室温后,将试样编号,取样温度记录于表中,检查试样有无开裂、粘砂等缺陷。
然后放入105~110℃烘箱中烘至恒重。
取出试样放入干燥器内,冷却至室温。
将试样分成两批,900℃以下为第一批,测定其饱吸煤油后在煤油后在空气中重,900℃以上的试样为第二批,测定其饱吸水后在水中重及饱吸水后在空气重。
按公式算出各温度点的结果后,以温度为横坐标,气孔率和收缩率为纵坐标,画出收缩率和气孔率曲线,并从曲线上确定烧结温度和烧结温度范围。
烧结的意义烧结时的温度称为烧结温度,烧结温度和开始过烧温度之间的温度范围称为烧结温度范围,在烧结过程中若不确定烧结温度和烧结温度范围继续升温,则坯体开始变形、软化、过烧膨胀,造成烧结事故。
烧结理论基础知识考试题A卷

烧结理论基础知识考试题A卷(满分150分)姓名: 得分:一, 推断题(正确记“√”, 错误记“×”)每题2分, 共20分1, 若倒数第二个风箱的废气温度低于倒数第一个风箱的废气温度说明烧结“终点”滞后(√)。
2, 烧结的点火强度低, 可通过延长点火时间或加大煤气流量来提高(√)3, 当料层厚度及抽风量肯定时, 真空度愈高, 则料层透气性愈好。
(×)4, 煤气爆炸主要是由于空气和煤气形式爆炸的混合气体, 同时混合气体达到必要的温度(着火点)或遇上明火造成, 二者缺一不可(√)5, 氧化亚铁是低价铁, 还原性能好, 因此烧结矿中FeO越高, 还原性越好(×)6, 点火后料面呈清黑色, 并有金属光泽局部熔融为最好(×)7, 配料计算将返矿视为常数, 计算时不考虑返矿这是传统的配料计算方法。
(√)8, 当电子秤不准, 电子秤实际配比及微机给定配比不符, 生产上常将不准的电子秤的配比加大或缩小, 来保证电子秤下料量及微机给定的下料量相符, 这种方法临时应急是可行的(√)9, 磁铁矿的主要化合物是四氧化三铁Fe3O4。
(√)10, 赤铁矿的主要化合物是Fe2O3, 3H2O(×)1、二, 填空题。
每空1分, 共30分2、严格限制烧结三点温度, 即点火温度, (终点温度), (总管废气温度)4、在运行混合料抽风烧结的过程中, 沿整个料层高度将呈现出性质不同的五个带为(烧结矿带), (燃料燃烧带), (预热带), (干燥带), (过湿带)5、配料室五勤一准操操作内容是: (勤检查), (勤联系), (勤分析推断)(勤计算调整), (勤总结沟通), 一准为: (配料精确)6、返矿加水的目的是降低返矿的(温度), 稳定混合料水粉, 以利于造球。
7、网目数是指在(1英寸或2.54cm)筛网上的筛孔数, 这是英国泰勒标准筛的表示方法;8、烧结生产工艺流程大体可分为八个部分, 受料系统, 原料打算系统, (配料系统), (混合制粒系统), (烧结系统)抽风系统, (成品处理系统), 除尘系统9、烧结厂用燃料粒度一般标准是≤3mm的部分大于(80)%为合格。
烧结新入职员工安全培训
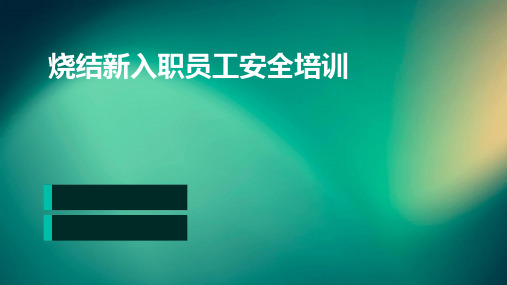
contents
目录
• 安全培训介绍 • 烧结安全基础知识 • 个人防护与应急处理 • 安全规章制度与法律法规 • 安全培训总结与反馈
01 安全培训介绍
安全培训的重要性
01
02
03
预防事故发生
通过安全培训,新员工可 以了解工作场所的安全规 定和操作规程,从而降低 事故发生的概率。
件。
记录管理
建立员工安全培训档案,记录员 工参加培训的时间、内容和考核
成绩等信息。
定期复训
规定员工定期参加复训,确保其 安全知识和技能得到及时更新和
提高。
THANKS FOR WATCHING
感谢您的观看
通过加强安全培训,可以降低事故发 生的概率,减少企业生产损失和人员 伤亡。
提高企业安全管理水平
通过定期开展安全培训,企业的安全 管理水平将得到提升,能够更好地保 障员工的人身安全和财产安全。
02 烧结安全基础知识
烧结工艺简介
01
烧结工艺是钢铁生产中的重要环 节,通过将铁矿粉、焦炭等原料 进行高温熔炼,除去其中的杂质 ,得到具有一定性能的生铁。
员工应积极参与安全文化建设,主动学习安全知识,增强 安全意识,确保个人和团队的安全。
05 安全培训总结与反馈
安全培训总结
培训目标
确保新员工掌握基本的安 全知识和技能,提高安全 意识,预防事故发生。
培训内容
包括烧结生产安全规章制 度、安全操作规程、应急 救援措施、个人防护用品 使用等。
培训方式
采用集中授课、现场演示、 模拟演练等多种形式,注 重理论与实践相结合。
详细描述
新入职员工应了解烧结工应急处理流程,包括事故报告、紧急疏散、急救措施等。在遇到突发事件时 ,能够迅速采取正确的应对措施,如火灾、机械故障等,确保自身和他人安全。同时,应积极配合相 关部门的应急处理工作,按照统一指挥进行行动。
《陶瓷材料的烧结》课件

对废弃的陶瓷材料进行回收和再利用,实现资源的循环利用,降 低对自然资源的依赖。
THANKS。
致密度、均匀性和性能。
烧结设备的改进
03
随着技术的进步,烧结设备的性能和效率也将得到提升,为陶
瓷材料的制备提供更好的设备支持。
环保和可持续发展在陶瓷烧结领域的应用
环保材料的研发
为了降低陶瓷产业对环境的影响,未来将大力研发环保型的陶瓷 材料,如低毒陶瓷、可降解陶瓷等。
节能减排技术的应用
通过采用新型的节能技术,降低陶瓷烧结过程中的能耗和排放, 实现低碳、环保的生产。
04
陶瓷材料的烧结性能
烧结密度和孔隙率
烧结密度
烧结后的陶瓷材料密度,影响材料的 机械性能和热学性能。
孔隙率
陶瓷材料内部孔隙的多少,与材料的 强度、热导率和绝缘性能有关。
烧结陶瓷的力学性能
01
硬度
烧结陶瓷的硬度取决于其成分和 显微结构,硬度高的陶瓷耐磨、 耐划痕。
02
03
抗弯强度
韧性
陶瓷抵抗弯曲应力的能力,与材 料的成分、显微结构和制备工艺 有关。
航天器结构材料
陶瓷材料具有轻质、高强度和耐高温的特性,适用于航天器结构材料,如卫星天线骨架、太阳能电池板支架等。
06
未来展望
新型陶瓷材料的开发
高性能陶瓷
随着科技的发展,对陶瓷材料性能的要求越来越高,未来 将开发出具有更高强度、硬度、耐磨性、耐高温等高性能 的新型陶瓷材料。
多功能陶瓷
除了传统的结构陶瓷外,未来还将开发出具有多种功能如 导电、导热、压电、磁性等功能的新型陶瓷材料。
05
陶瓷材料的烧结应用
在电子行业的应用
电子封装
烧结生产基础知识

第六节物理基本知识2—62简述物料堆密度的含义,它起什么作用?答:物料堆密度是指单位体积物料的质量,以t/m3(吨/米3)表示。
它是计算皮带运输机,混料机,烧结机等设备生产率或料仓储存量及其排出口上的压力时不可缺少的参数。
2—63 试述物料的自然堆角(安息角)、静自然堆角和动自然堆角的含义?写出烧结厂常用物料堆密度和自然堆角数字?答:自然堆角反映出散状物料之间的活动性。
如果将散状物料自然地放在一水平面上,沿堆尖作一垂直面,则散料堆出现如图2-2的剖面,散料与水平面呈一夹角φ,该角称自然堆角,又叫安息角。
不同的散料其堆角不同。
上述自然堆角又称静自然堆角。
若将自然堆放的散料沿垂直方向振动后,其堆角称为动自然堆角φ动,一般φ动=0.7 φ。
烧结厂常用物料堆密度和自然堆角见表2-6。
2-64简述重度的含义。
答:单位体积物体的重量称为重度,用符号γ表示,单位为N/m3或kg·S2/m4。
2-65 简述密度和重度的关系,比重的含义。
答:单位体积的物体质量称为密度,用符号ρ表示,单位为kg/m3。
密度与重度的关γρg=系为,g为重力加速度。
各种物质的重度与水的重度之比叫做比重,比重是没有单位的,在气体力学中比重常用δ来表示。
2-66简述设备的温度与温升有何区别。
答:温度指设备本身的温度,温升则指设备温度与环境温度之差。
2-67简述绝对温度的含义。
答:绝对温度是热力学温度的俗称。
它的单位是开[尔文],单位符号为K。
零下273℃为绝对温度的零度,摄氏零度即为绝对温度273K,100℃则为绝对温度(100+273)373K。
2-68什么叫绝对湿度和相对湿度?答:空气水分含量一般以绝对湿度和相对湿度来表示,每立方米湿空气所含水蒸气之质量称为空气之绝对湿度,湿蒸气中水蒸气分压与同温度下完全饱和的空气中水蒸气分压之比的百分数称为相对湿度。
2-69简述压力和压强的含义。
答:物质的分子运动产生的作用力叫做压力。
压力的大小与受力面积的大小有关,物理学上用压强来表示单位面积上所受力的大小,也就是工程上所说的压力。
材料科学基础重点知识

《材料科学基础》重要知识点1、在离子晶体中,正、负离子的配位数大小由结构中正、负离子半径的比值决定。
2、聚合物的形成过程是分化和缩聚同时进行的一种动态平衡过程。
3、硅酸盐熔体的结构特点:多种聚合物同时并存,而不是一种独存。
正是由于这个特点,硅酸盐熔体的结构是长程无序的。
但每一个聚合体又是具有晶体结构的,即硅酸盐熔体中存在短程有序的负离子团。
4、影响聚合物聚合程度的因素(1)温度的影响:随温度升高,低聚合物浓度增加,而高聚合物浓度降低。
(2)熔体组成的影响:R为O/Si比的大小。
O/Si比R越大,低聚合物浓度越大,高聚合物浓度越小。
5、影响熔体粘度的主要因素是温度和化学组成。
粘度---温度关系:温度升高,粘度减小。
粘度—组成关系(1) O/Si比:硅酸盐熔体的粘度首先取决于硅氧四面体网络的聚合程度,即随O/Si比的上升而下降。
(2)一价碱金属氧化物①加入碱金属氧化物(Li2O、Na2O、K2O、Rb2O、Cs2O)降低硅酸盐熔体的粘度。
②碱金属氧化物的含量越高,硅酸盐熔体的粘度越小。
③不同的碱金属氧化物对粘度的影响大小也与碱金属氧化物的含量有关。
当R2O含量较低时(O/Si较低),加入的正离子半径越小,降低粘度的作用越大,其次序是:Li+>Na+>K+>Rb+>Cs+。
当熔体中R2O含量较高(O/Si比较高)时,R2O对粘度影响的次序是Li+<Na+<K+。
(3)二价金属氧化物:二价碱土金属氧化物(ⅡA族)一般降低硅酸盐熔体的粘度。
但不同的氧化物降低粘度的程度不同,其降低粘度的次序是:Ba2+>Sr2+>Ca2+>Mg2+,所以粘度大小次序为:Ba2+<Sr2+<Ca2+<Mg2+。
(4)阳离子配位数:阳离子配位数对粘度的影响是通过B2O3的研究而取得的。
①当B2O3含量较少(即Na2O/B2O3>1)时,粘度随含量升高而增加。
这是因为此时“游离”氧充足,故B3+处于[BO4]四面体状态,结构紧密。
- 1、下载文档前请自行甄别文档内容的完整性,平台不提供额外的编辑、内容补充、找答案等附加服务。
- 2、"仅部分预览"的文档,不可在线预览部分如存在完整性等问题,可反馈申请退款(可完整预览的文档不适用该条件!)。
- 3、如文档侵犯您的权益,请联系客服反馈,我们会尽快为您处理(人工客服工作时间:9:00-18:30)。
1. 烧结基础知识2. 烧结的含义将含铁粉状料或细粒料进行高温加热,在不完全熔化的条件下烧结成块的过程。
铁矿粉烧结是一种人造富矿的过程。
2.1. 烧结的方法(1)鼓风烧结:烧结锅,平地吹;(2)抽风烧结:(a)连续式:带式烧结机和环式烧结机等;(b)间歇式:固定式烧结机,如盘式烧结机和箱式烧结机;移动式烧结机,如步进式烧结机;(3)在烟气中烧结:回转窑烧结和悬浮烧结。
2.2. 烧结生产的工艺流程一般包括:原燃料的接受、贮存,溶剂、燃料的准备,配料,混合,制粒,布料,点火烧结,热矿破碎,热矿筛分,热矿冷却,冷矿筛分,铺底料、成品烧结矿及返矿的贮存、运输等工艺环节。
机上冷却工艺不包括热矿破碎和热矿筛分。
现代烧结工艺流程不再使用热矿工艺,应使用冷矿工艺。
在冷矿工艺中,宜推广具有铺底料系统的流程。
2.3. 烧结厂主要技术经济指标烧结厂的主要技术经济指标包括利用系数、作业率、质量合格率、原材料消耗定额等。
2.3.1. 利用系数每台烧结机每平方米有效抽风面积(m2)每小时(h)的生产量(t)称烧结机利用系数,单位为t/(m2*h)。
它用台时产量与烧结机有效抽风面积的比值表示:利用系数=台时产量(t/h)有效抽风面积(m²)=总产量(t)总生产台时(t)×总有效面积(m²)台时产量是一台烧结机一小时的生产量,通常以总产量与运转的总台时之比值表示。
这个指标体现烧结机生产能力的大小,它与烧结机有效面积的大小无关。
利用系数是衡量烧结机生产效率的指标,它与烧结机有效面积的大小无关。
2.3.2. 烧结机作业率作业率是设备工作状况的一种表示方法,以运转时间占设备日历时间的百分数表示:设备作业率=运转台时日历台时×100%日历台时是个常数,每台烧结机一天的日历台时即为24台时。
它与台数、时间有关。
日历台时=台数×24×天数事故率是指内部事故时间与运转时间的比值,以百分数表示:事故率=事故台时运转台时×100%设备完好率是衡量设备良好状况的指标。
按照完好设备的标准,进行定期检查。
设备完好率是全厂完好设备的台数与设备总台数的比值,用百分数表示:设备完好率=完好设备台数×100%设备总台数2.3.3. 质量合格率烧结矿的化学成分和物理性能符合原冶金部YB/T421标准要求的叫烧结矿合格品,不符合的烧结矿叫出格品。
根据部颁标准的规定,实际生产检验过程及工艺试验中出现的一部分未检验品和试验品,不参加质量合格率的计算。
因此:质量合格率=总产量−未验品量−试验品量−出格品量×100%总产量−未验品量−试验品量质量合格率是衡量烧结矿质量好坏的综合指标。
烧结矿合格品、一级品或出格品的判定根据其物理化学性能的检验结果而定,主要包括烧结矿全铁(TFe)、氧化亚铁(FeO)、硫(S)含量、碱度(CaO/SiO2)、转鼓指数(≥6.3mm)、粉末(<5mm)等,有的厂还包括氧化镁(MgO)、氟(F)、磷(P)等。
一级品率=一级品量×100%合格品量×100%转鼓指数=检测粒度(≥5mm)的重量试样重量×100%筛分指数=筛分后粒度(≤5mm)的的重量试样重量2.3.4. 烧结矿的原料、燃料、材料消耗定额生产一吨烧结矿所消耗的原料、燃料、动力、材料等的数量叫消耗定额,包括含铁原料、熔剂料、燃料、煤气、重油、水、电、炉蓖条、胶带、破碎机锤头、润滑油、蒸气等。
2.3.5. 生产成本与加工费生产成本是指生产一吨烧结矿所需的费用,由原料费及加工费两部分构成。
加工费是指生产一吨烧结矿所需的加工费用(不包括原料费)。
它包括辅助材料费(如燃料、润滑油、胶带、炉蓖条、水、动力费等),工人工资,车间经费(包括设备折旧费、维修费等)。
2.3.6. 劳动生产率劳动生产率是指每人每年生产烧结矿的吨数。
这个指标反映工厂的管理水平和生产技术水平,它又称全员劳动生产率(全员包括工人和干部)。
另外,还有工人劳动生产率,即每个工人每年生产烧结矿的吨数。
3. 烧结物理化学过程3.1. 基本概念烧结过程是许多物理化学变化的综合过程。
这个过程不仅错综复杂,而且瞬息万变,在几分钟甚至几秒钟内,烧结料就因强烈的热交换而从70℃以下被加热到1200~1400℃,与此同时,它还要从固相中产生液相,然后液相又被迅速冷却而凝固。
这些物理化学变化包括:(1)燃料的燃烧和热交换;(2)水分的蒸发及冷凝;(3)碳酸盐的分解,燃料中挥发分的挥发;(4)铁矿物的氧化、还原与分解;(5)硫化物的氧化和去除;(6)固相间的反应与液相生成;(7)液相的冷却凝结和烧结矿的再氧化等。
3.2. 燃料的燃烧和热交换3.2.1. 烧结矿生产使用的燃料烧结生产使用的燃料分为点火燃料和烧结燃料两种。
3.2.1.1. 点火燃料现在烧结使用的点火燃料有气体燃料(高炉煤气、焦炉煤气、发生炉煤气和天然气等)和液体燃料(重油)两种,发生炉煤气在这里不再介绍,因固体燃料已经不再使用,在这里也不做介绍。
3.2.1.1.1.气体燃料3.2.1.1.1.1.高炉煤气高炉煤气是高炉冶炼时的一种副产品。
高炉每炼一吨生铁可以获得3500~4000m³的高炉煤气。
其成分随冶炼时所采用的燃料种类及高炉操作条件而不同。
一般含有大量氮、二氧化碳等气体(约占63~70%)。
因此,它的发热量不高,约为850~1100千卡/标m³(其成分见表2-1),若不经过预热,高炉煤气燃烧温度达不到1250,高炉煤气中一般含尘量为50~80毫克/m³,所以必须除尘后才能应用。
做为烧结点火用的煤气含尘量不应大于30毫克/m³,经过除尘后高炉煤气含尘量可以降至5~20毫克/m³,煤气温度在40℃以下。
输送到烧结厂的煤气压力一般为300毫米水柱左右。
表3-1高炉煤气成分3.2.1.1.1.2.焦炉煤气焦炉煤气是炼焦过程产生的副产品。
平均每吨干煤炼焦时可产生320m ³的焦炉煤气,约占全部产品的17.6%,经过洗涤后的煤气含焦油量为0.00~0.02克/标m³,用于烧结的焦炉煤气的发热量为4000×4.1868kJ/m³左右(其成分见表2-2)。
表3-2焦炉煤气成分3.2.1.1.1.3.天然气天然气是由地下开采出来的可燃性气体,它的发热量很高可达8000~9000×4.1868kJ/m³,主要可燃物质是甲烷(CH4)(其成分见表2-3)。
表3-3天然气气成分3.2.1.1.2.液体燃料石油是天然的液体燃料,也称为原油。
它基本上由炭、氢、氮、氧、硫五种元素组成。
将石油加热分馏后,比重最大的残留物就是重油。
重油具有发热值高(大于9000×4.1868kJ/kg)、粘性大等特点。
呈黑褐色或绿褐色的粘稠液状,比重约为0.9~0.96kg/L。
重油的灰分含量非常低,一般不超过0.3%。
重油按粘度不同,可分为20号、60号、200号几种,重油粘度越大,含氢量越少,重油含的杂质主要是少量的硫化物、氧化物、水分以及混入的机械杂质。
我国重油的含硫量都在1%以下,重油的着火点约为500~600℃。
3.2.1.2. 烧结燃料烧结燃料主要指在料层内燃烧的固体燃料,最常用的是碎焦粉粉末和无烟煤等。
3.2.1.2.1.碎焦粉末焦碳是炼焦煤在隔绝空气高温加热后的固体产物。
碎焦粉末是高炉用的焦碳的筛下物,粒度一般小于25毫米。
焦碳的质量的好坏,主要从它的化学成分、物理机械性能、物理化学性质几方面来衡量。
焦碳的化学成分通常以工业分析测得。
主要有固定炭、灰分、挥发分和含硫量。
焦碳的物理机械性能主要指机械强度(如耐磨性和抗冲击强度、抗压强度)及筛分粒度组成。
焦碳的物理化学性质是指其燃烧性和反应性。
燃烧性是指焦碳与氧在一定温度下的反应速度。
反应速度越快,燃烧反应性越高,一般反应性好的焦碳燃烧性也好。
3.2.1.2.2.无烟煤随着煤炭化的程度不同,煤中的挥发物含量的差别是很大的。
炭化程度越高,它的挥发分含量也就越少。
无烟煤是各种煤中炭化最好的烧结燃料,在生产上要求无烟煤的发热量大于6000千卡/公斤,挥发分小于10%,灰分小于15%,硫小于2.5%,进厂的粒度小于40毫米。
挥发分高的煤不宜做烧结燃料,因为煤在烧结中的挥发物会被抽入抽风机和抽风系统,冷凝后使除尘器、抽风机等挂泥结垢。
3.2.1.2.3.兰炭兰炭也称为半焦,表3-4兰炭质量要求全水分不作为考核指标;1、兰炭用作化肥、气化是考核指标;2、兰炭用作铁合金时考核该指标;3、兰炭用作高炉喷吹时考核该指标;4、兰炭用作电石、铁合金时考核该指标。
3.3. 烧结生产对燃料物理化学性能的要求烧结过程必须在一定的高温下才能进行,而高温是由燃料的燃烧产生的。
温度的高低,燃烧速度的快慢,燃烧带的宽窄,以及烧结料中的气氛等都将影响烧结过程的进行和烧结矿的产、质量。
而这些因素又都与燃料的物化性能、用量有关。
因此,燃料的物化性能是影响烧结过程的重要因素。
3.3.1. 对燃料质量的要求烧结要求燃料的灰分尽可能低些,因为燃料中灰分含量增多必然引起烧结料含铁量降低和酸性氧化物增多(灰分中SiO2的数量高达50%以上),因而必然相应需要增加溶剂的消耗量。
使用无烟煤做烧结燃料时,要求它挥发分的含量不能太高,以免燃料中的挥发物质在温度较低的地方凝结下来恶化料层透气性和粘结在集气管及抽风机的叶片上,影响烧结过程的正常进行。
此外,燃料中的挥发分在着火前即已挥发出去,不能在烧结过程中被利用。
所以,烧结生产使用的燃料最好选用固定碳高、灰分低、挥发分低及含硫量低的优质燃料。
3.3.2. 对燃料粒度的要求燃料的粒度过大时,会带来一系列的不良影响:a.燃烧带变宽,从而使烧结料层透气性变坏。
b.燃料在料层中分布不均匀,以至在大颗粒燃料的周围熔化得很厉害,而离燃料颗粒较远的地方的物料则不能很好地烧结。
c.粗粒燃料周围,还原性气氛较强,而没有燃料地方空气得不到利用。
d.在向烧结机布料时,易产生燃料偏析现象,大颗粒燃料集中在料层的下部,再加上烧结料层下部的蓄热作用,使烧结料层的温度差异更大,以至造成上层烧结矿的强度差,下层过熔FeO含量偏高。
燃料粒度过小,烧结速度快,燃烧所产生的热量难以使烧结料达到所需的高温,从而使烧结矿的强度下降。
同时,小的燃料颗粒(小于0.5毫米)使烧结料层的透气性变坏,并有可能被气流带走。
研究表明,燃料最适宜的粒度为0.5~3毫米,而日本规定燃料粒度下限为0.25毫米,但在我国实际生产条件下,仅仅能保证粒度上限,难以保证粒度下限。
因为在生产过程中要避免0.5~0毫米粒级是难以达到的。
所以,一般烧结厂只要求控制其燃料粒度在3~0毫米范围内。