冷轧弯辊控制原理
冷弯型钢四辊轧制技术_马越峰

图1
二辊式与四辊式成型之比较
( 2) 四辊轧制可以减小辊面与带钢接触部分 的速度差 , 从而减少辊面磨损和对带钢表面可能 产生的划痕, 保证产品的表面质量。 ( 3) 四辊结构形式提供了轧辊组合的灵活性, 为轧辊孔型共用体系的设计提供空间。这种灵活 的轧辊组合配置提供的另一大优点是使生产厂家 能够根据用户的要求, 在不增加轧辊投入的前提 下, 控制高频焊缝在矩形管宽面或高面的位置, 这对一些有特殊后加工要求的用户十分有利。 ( 4) 四辊轧制在深断面产品的成型时 , 可以 减少变形的附加摩擦 , 降低能耗。 3 冷弯四辊轧制技术的应用 从设备角度来说 , 目前国内外能制造四辊插 入式机架的厂家有不少, 但能够充分发挥四辊机 架优势的厂家不多, 问题的关键在于轧辊孔型设 计与设备的结合与配套。在冷弯生产线上, 成型 机组主要由以下部分组成 : 粗成型 ( breakdown) 、 精成型 ( finpass) 、焊接部分 ( HF welding) 、整形 部分 ( sizing & shaping) 。四辊轧制技术主要用于 后三个部分。 3 1 精成型部分 四辊轧制在精成型阶段, 方变方与圆变方工 艺示意见图 2。 圆变方 工艺无法实现孔型的 共用, 一般一个规格一套轧辊; 方变方 工艺 可以做到下辊和侧辊完全共用 , 上辊分档共用。
44
上
海
金
属 产品的加工硬化倾向小。
第 25 卷
表 1 80~ 100 系列方矩形管典型产品规格
80 方系列 80 90 100 110 120 80 70 60 50 40 85 方系列 85 85 90 80 100 70 110 60 120 50 130 40 90 方系列 90 90 100 80 110 70 120 60 130 50 140 40 95 方系列 95 100 110 120 130 140 150 注 : 表中单位均为毫米 ( mm) 95 90 80 70 60 50 40 100 方系列 100 110 120 130 140 150 160 100 90 80 70 60 50 40
新钢冷轧酸轧机组液压弯辊控制模型

新钢冷轧酸轧机组液压弯辊控制模型摘要酸轧机组对板型的要求很高,因此对板型的调节由多个系统共同完成,本文讲述了弯辊控制系统,液压弯辊具有使用灵活、响应速度快、可以有效地减小板凸度、提高生产率等优点,弯辊技术在各种轧机上得到广泛的应用。
关键词冷轧;弯辊力;模型;分析;凸度中图分类号tg33 文献标识码a 文章编号 1674-6708(2013)92-0128-021弯辊系统在新钢冷轧厂的应用新余钢铁公司冷轧厂使用的是五连轧六辊轧机,每个轧机都包括有工作辊弯辊系统,由于每个轧机的主要分工不同,所以每个轧机的弯辊力设定值就不同。
冷轧过程也就是改变带钢内应力的过程,它在改变内应力的同时也就改变了带钢的板型,由于现代产品对带钢的质量要求严格,而板型作为最主要的产品质量指标则要求更加精确,因此弯辊技术也就显得尤为主要。
2弯辊的概念及分类首先了解一下弯辊的概念:弯辊实际上是通过液压缸来控制轧辊两端的受力情况,使轧辊弯曲,产生一定的形变量(凸度)。
当轧辊发生形变时,在同一横截面上,带钢表面所受的轧制力是不同的,如此同时也就达到了改变带钢板型的要求。
弯辊又分为正弯和负弯。
正弯:当两端四个弯辊液压缸往外顶时,产生弯辊力,使得轧辊产生凹下去的变形,从而改变带钢板型。
正弯辊力使得带钢具有中间轧制力或辊缝小,两端大的特点。
适用于调节具有边浪的带钢。
负弯:当两端四个弯辊液压缸往外顶时,产生弯辊力,使得轧辊产生凸起来的变形,从而改变带钢板型。
负弯辊力使得带钢具有中间轧制力或辊缝大,两端小得特点。
适用于调节具有中间波浪的带钢。
3影响弯辊力的因素弯辊又分为中间辊弯辊和工作辊弯辊,下面以工作辊弯辊为例,来论述弯辊的控制。
那么根据什么来设定弯辊力的给定量呢?3.1带钢宽度对弯辊力的影响带钢宽度在轧机轧辊变形中对agc辊缝的影响比较大,主要对轧机的操作侧轧制力和传动侧轧制力的偏差、轧辊辊间单位压力的分布和带钢表面的凸度产生影响,如果在其他参比条件不变的情况下,辊缝凸度会随着带钢宽度的改变而改变,这是应该相应的改变弯辊力的设定值。
控制轧制过程的基本原理

综述铝箔轧制中工作辊的辊形直接影响着辊缝及辊间轧制压力的轴向分布从而影响着铝箔的板形所以, 求算辊缝及轧制压力的轴向分布是分析不同工作辊辊形对铝箔板形影响的前提用解析法求算辊间压力分布的公式很多许多学者专家从不同的附加假设条件出发导出了各种不同的公式但运用这些公式只能求得轧制变形区内沿轧制方向上的轧制压力分布对辊缝处沿轧辊轴向分布的轧制压力的计算尚缺乏针对性[1-3] 用有限元法分析四辊轧机辊系变形时许多文献在施加轧制压力时都采用均布或抛物线假设[4-8] 这大大影响了辊系变形计算结果的准确性本文运用ANSYS 有限元软件分别计算了工作辊辊形为平辊AFW 辊形ZHX 辊形时在冷辊(开始轧制) 和热辊(稳定轧制)状态下铝箔四辊轧机辊系的变形在计算中对工作辊支持辊轧件建立了计算模型以尽可能少的约束条件求得了辊缝内轧辊所受轧制压力的轴向分布规律,并分析了不同工作辊辊形对铝箔板形的影响1 控制轧制过程的基本原理历史背景历史上,碳是提高钢的强度的最重要的化学元素,但碳对许多工艺性能如焊接性能、成型性能有不利的影响。
因此,用碳强化的钢的应用受到限制。
为了保证钢结构的安全性,要求钢的强度和韧性达到优良的配合,这种含碳较高的钢往往要进行成本高的热处理,如淬火加回火。
为了扩大成本低的高强度钢的应用,物理冶金学家们建议用其它强化机制来替代碳的强化。
图1(1)显示,根据d-1/2 规律(2),晶粒细化是同时提高强度和韧性的最有效的方法。
控制轧制工艺是达到此目的的工业技术,该技术把成型过程与显微组织的控制过程结合起来。
均热温度为了使加热工艺易于进行,传统方法是采用较高的均热温度。
因此,轧制工艺从钢坯加热开始就要控制晶粒尺寸,而且其效果是明显的。
人们知道,奥氏体晶粒长大与均热温度决定于均热时要求产生的冶金反应,即使微合金化元素溶于固溶体,其原因将于下面得到解决。
对于钢种而言,最低的均热温度决定于铌、碳含量。
如图2 所示,对于0.10%C、0.03%Nb.的钢来说,其最低均热温度为1150℃。
冷轧机弯辊伺服系统控制方案

自动化控制・ Automatic Control270 •电子技术与软件工程 Electronic Technology & Software Engineering【关键词】液压伺服控制 弯辊系统 正弯 负弯1 液压弯辊伺服系统在原理方面,弯辊伺服系统对板型控制的目的是通过对辊缝形状实现的。
具体到液压弯辊伺服系统则是以作用力于工作辊辊液端液压缸产生一定的推力,此推力再向工作辊辊端轴承座上产生作用力,促使工作辊发生附加弯曲,进而促使轧辊改变有效挠度最终改变辊缝形状,以实现板型修正的最终目的。
液压伺服控制系统的基本组成元件主要有指令输入元件;反馈检测元件;放大、转换、控制元件;比较元件;液压执行元件和控制对象等。
根据不同的分类方式进行分类:(1)以误差信号的产生以及误差信号的传递方式不同为划分依据,可以划分为三类,其一是机械——液压伺服控制系统;其二是气动——液压伺服控制系统;其三是电气——液压伺服控制系统。
(2)以液压控制元件的不同作为划分依据,则可以划分为两类,其一是阀控系统;其二是泵控系统;(3)以被控制物理量不同为依据可以划分为以下几种,其一是位置伺服控制系统;其二是力伺服控制系统;其三则是速度伺服控制系统。
在工程实践中我们选用了新一代的伺服阀,该阀动态响应快,具有很强的抗污染能力,很高的控制精度,这样就能够保证工作的可靠性和系统响应速度、稳定性和高精度的要求。
此外,检测精度很大程度上控制了控制精度,因此,在实践工作中,对于伺服系统而言,在压力检测方面采用了HYDAC 公司的压力传感器。
2 弯辊伺服控制系统的两种组成方式在组成方式方面,作为典型的液压伺服控制系统的液压弯辊控制系统可以进行两种方冷轧机弯辊伺服系统控制方案文/刘敬磊式的划分,其一是手动调节系统;其二是自动调节系统。
在手动调节系统方式中,弯辊力的大小给定灵活,主要是通过操作者根据观测板型、计算或者操作板型的经验进行设定的,不需要任何主控量或者干扰量的反馈调节。
六辊可逆冷轧机横移-弯辊系统的控制
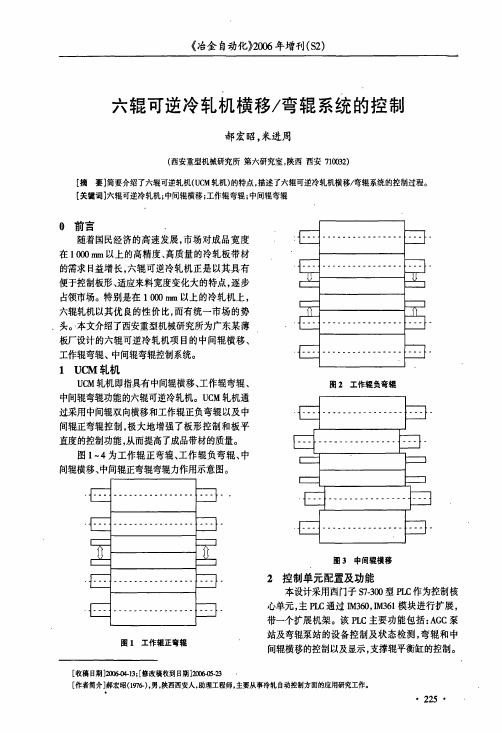
六辊可逆冷轧机横移/弯辊系统的控制
郝宏昭,米进周
(西安重型机械研究所第六研究室,陕西西安710032) [摘要]简要介绍了六辊可逆轧机(UCM轧机)的特点,描述了六辊可逆冷轧机横移/弯辊系统的控制过程。
【关键词]六辊可逆冷轧机;中间辊横移;工作辊弯辊;中间辊弯辊
O前言 随着国民经济的高速发展,市场对成品宽度
带材板形得到了更好的控制。本轧机中间辊只有
正弯辊。
4.1弯辊控制方法、
对弯辊的控制采用压力闭环控制,其控制框
图如图7所示。
[编辑:魏方]
・227・
置,方可进行换辊操作。否则将会损坏轧机辊系。
单独调节,也可以两边同时调节。
4弯辊系统的特点及控制原理
在轧制过程中,弯辊是最为常见的用于对带 刚凸度和板平直度进行连续控制的方法之一。通 过控制轧机轧辊两侧的弯辊力,改变轧辊的辊形。
弯辊控制用于控制轧机出口侧带材的板形。如果 弯辊力使辊缝减小,称之为正弯辊;反之,如果弯
E
此外通过硬线连接方式与AC,C系统通信以协助
AGC系统实现快速卸荷,与工艺PI£之间通过 MPI网通信实现AGC泵站及弯辊泵站的远程起停
匡
r——。一
及故障状态显示,控制框图如5所示。
3中间辊横移系统的特点及控制原理
中间辊横移是控制板形精度的方法之二。它
亡 E
图4中间辊正弯辊
根据带材宽度的不同而轴向移动上下两个中间
馈达到平衡,执行器输出为零,油缸不再动作。当 给定再次增减时,反馈随之增减,执行器驱动油缸
要解决这个控制问题,必须要转换思维方式,
从另外一个角度去看这个问题。首先应该明确, 其实所谓的同步只是从宏观上来说的,它实际上
轧钢生产过程中自动化控制技术的应用
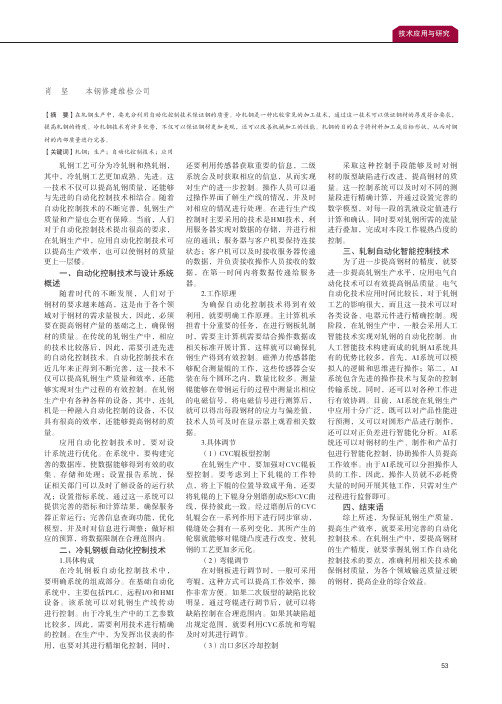
轧钢工艺可分为冷轧钢和热轧钢,其中,冷轧钢工艺更加成熟、先进。
这一技术不仅可以提高轧钢质量,还能够与先进的自动化控制技术相结合。
随着自动化控制技术的不断完善,轧钢生产质量和产量也会更有保障。
当前,人们对于自动化控制技术提出很高的要求,在轧钢生产中,应用自动化控制技术可以提高生产效率,也可以使钢材的质量更上一层楼。
一、自动化控制技术与设计系统概述随着时代的不断发展,人们对于钢材的要求越来越高,这是由于各个领域对于钢材的需求量极大,因此,必须要在提高钢材产量的基础之上,确保钢材的质量。
在传统的轧钢生产中,相应的技术比较落后,因此,需要引进先进的自动化控制技术。
自动化控制技术在近几年来正得到不断完善,这一技术不仅可以提高轧钢生产质量和效率,还能够实现对生产过程的有效控制。
在轧钢生产中有各种各样的设备,其中,连轧机是一种融入自动化控制的设备,不仅具有很高的效率,还能够提高钢材的质量。
应用自动化控制技术时,要对设计系统进行优化。
在系统中,要构建完善的数据库,使数据能够得到有效的收集、存储和处理;设置报告系统,保证相关部门可以及时了解设备的运行状况;设置指标系统,通过这一系统可以提供完善的指标和计算结果,确保服务器正常运行;完善信息查询功能,优化模型,并及时对信息进行调整;做好相应的预算,将数据限制在合理范围内。
二、冷轧钢板自动化控制技术1.具体构成在冷轧钢板自动化控制技术中,要明确系统的组成部分。
在基础自动化系统中,主要包括PLC、远程I/O和HMI 设备。
该系统可以对轧钢生产线传动进行控制。
由于冷轧生产中的工艺参数比较多,因此,需要利用技术进行精确的控制。
在生产中,为发挥出仪表的作用,也要对其进行精细化控制,同时,还要利用传感器获取重要的信息,二级系统会及时获取相应的信息,从而实现对生产的进一步控制。
操作人员可以通过操作界面了解生产线的情况,并及时对相应的情况进行处理。
在进行生产线控制时主要采用的技术是HMI技术,利用服务器实现对数据的存储,并进行相应的通讯;服务器与客户机要保持连接状态;客户机可以及时接收服务器传递的数据,并负责接收操作人员接收的数据,在第一时间内将数据传递给服务器。
冷轧弯辊控制原理

弯辊工艺适用于各种金属材料的冷轧生产,如钢 板、铝板、铜板等,具有广泛的应用前景。
弯辊工艺参数设定与调整
弯辊力设定
根据金属材料的性能、厚度和宽度等因素,合理设定弯辊力的大小。过大的弯辊力可能导 致轧辊过度弯曲,损坏设备;过小的弯辊力则无法有效改善板形质量。
轧辊间隙调整
通过调整轧辊间隙的大小和形状,实现对金属坯料横向厚度分布的控制。轧辊间隙的调整 需要根据金属材料的性能和产品要求进行精确计算和操作。
气动执行机构
以压缩空气为动力源,驱 动气缸完成弯辊动作,适 用于轻载、高速场合。
控制电路设计与实现
主控电路
驱动电路
采用高性能微处理器或DSP芯片作为核心, 负责数据处理、控制算法实现等功能。
根据执行机构类型设计相应的驱动电路, 如电机驱动器、液压阀驱动器等。
信号调理电路
通信接口电路
对传感器输出的微弱信号进行调理,包括 放大、滤波、A/D转换等处理,以满足控制 系统对信号精度和稳定性的要求。
冷轧弯辊控制原理
contents
目录
• 弯辊控制系统概述 • 冷轧弯辊工艺原理 • 弯辊控制系统硬件设计 • 弯辊控制系统软件设计 • 弯辊控制系统性能评估与优化 • 冷轧弯辊技术应用前景展望
01 弯辊控制系统概述
弯辊定义及作用
弯辊定义
弯辊是指在轧制过程中,通过调整轧辊的弯曲程度,从而改变轧制力分布和轧 后板材形状的一种技术。
探索在金属板材、带材、线材 等多种形态金属加工中的应用 可能性。
结合其他金属加工技术,形成 综合性的金属加工解决方案, 满足不同领域的需求。
未来发展趋势预测
冷轧弯辊技术将朝着更高精度、更智 能化的方向发展,实现更加精细的控 制和更高的生产效率。
冷轧机双锥度辊边降控制研究及应用1

冷轧机双锥度辊边降控制研究及应用郑虎平前言:电工钢是一种含碳量极低的硅铁软磁合金,其主要用于制造电动机、发电机、变压器铁芯和各种电讯器材,按质量计占磁性材料用量的90%~95%以上。
随着国家节能减排政策的日趋严厉,各种家用、电器厂家所使用的电工钢“以冷代热”趋势日趋明显,各电工钢用户对带钢的板形精度和厚度精度要求日趋严格,特别是横向厚度精度要求日趋严厉。
冷轧硅钢片作为国家优先发展的高效、节能、用量大的优秀软磁功能材料,是我国钢铁工业品种结构调整的重点,硅钢片用量占全部软磁性材料用量的95%以上。
而低牌号无取向硅钢是目前国内产量最大、用途最广的冷轧硅钢材料。
②宽幅无取向硅钢热轧板形控制技术。
带钢在冷轧或热轧过程中边部很窄区域内厚度发生急剧减小的现象称为边部减薄,亦称边降。
边降可定义为在轧制过程中板带边部在厚度上的减少量,它是由于圆形的轧辊在轧制过程中产生的轧制载荷由加载区至无载区逐渐过渡而造成的结果。
对应于不同的产品厚度、钢种,高速运行的连续冷轧带钢生产线可以通过在线切除产品边部(宽度大于厚度超差部分)来保证板带产品的质量,它是以牺牲板带的成材率为代价,也对能源、人力、财力和物力均造成了浪费。
为适应板带产品的厚度、成材率及产品品种组成多样性的要求,在现代轧钢生产过程中引进了许多新的控制理念及技术。
边降控制(EDC,又称边部减薄控制)成为板形研究与控制技术的新领域。
①冷连轧机边降控制窜辊数学模型研究。
为了控制板带在边部的厚度减小量,在理论上可采用以下措施:1,使用锥形辊;2,轧辊沿板带宽度方向产生适当的温度分布,产生热凸度;3,在板带边部区域对辊子进行弱化。
在理论研究和大量的轧制试验基础上,国外公司最新开发出用于高速冷轧带钢生产线上自动边降控制的两种基本方法(EDC 冷却系统及EDC辊系统),并可在高速运行的冷轧号带钢生产线上联合或单独使用。
目前具体的边降控制手段主要采用单锥形工作辊的K-WRS技术、EDC辊和EDC冷却系统、工作辊即可以交叉又可以横移的T-WRS&C技术、VCR变接触支撑辊等进行控制。