低成本高效炼铁的生产实践
2024年炼铁厂降本增效总结

2024年炼铁厂降本增效总结一、引言随着国内炼铁行业竞争的日益激烈,降本增效已成为炼铁企业的重要任务之一。
在____年,我公司积极响应国家政策,积极开展降本增效工作。
本文将对____年炼铁厂的降本增效工作进行总结,并提出下一步的工作思路。
二、工作概况在____年的降本增效工作中,我公司主要从以下几个方面入手:1.优化原材料成本通过与供应商合作,我公司成功降低了原材料的采购成本。
与此同时,我们加强原材料的分析和检测工作,提高了原材料的利用率和品质。
2.提高能源利用效率通过改善设备和工艺参数,我公司成功提高了能源利用效率。
同时,我们还加强了能源管理,提高了员工的能源意识,进一步减少了能源浪费。
3.改善生产流程我公司对生产流程进行了全面梳理和改进,优化了工艺参数和操作规程,降低了生产成本。
我们还引入了一些先进的生产技术和设备,提高了生产效率。
4.推动技术创新我公司积极推动技术创新,加大研发投入,引进了一些新技术和设备,提高了生产效率和产品质量。
同时,我们还加强了员工的培训,提高了他们的技术水平和工作能力。
5.加强管理和监控为了确保降本增效工作的顺利进行,我公司加强了管理和监控工作。
我们建立了一套完善的监控系统,及时发现问题并采取措施解决。
我们还加强了对员工的管理,提高了他们的工作积极性和责任心。
三、主要成效在____年的降本增效工作中,我公司取得了显著的成效:1.降低了生产成本通过采取一系列措施,我公司成功降低了生产成本。
我们的总成本下降了10%,其中材料成本下降了8%,能源成本下降了6%,人工成本下降了5%。
2.提高了生产效率通过优化生产流程和引入新技术设备,我公司成功提高了生产效率。
我们的年产量增加了10%,同时减少了废品率。
这不仅提高了产品的质量,也提高了企业的竞争力。
3.改善了环境和安全状况在降本增效工作中,我公司注重环境和安全问题。
通过加强管理和监控,我们降低了废气、废水和废渣的排放量,改善了环境状况。
完善电炉冶炼工艺降低冶炼成本
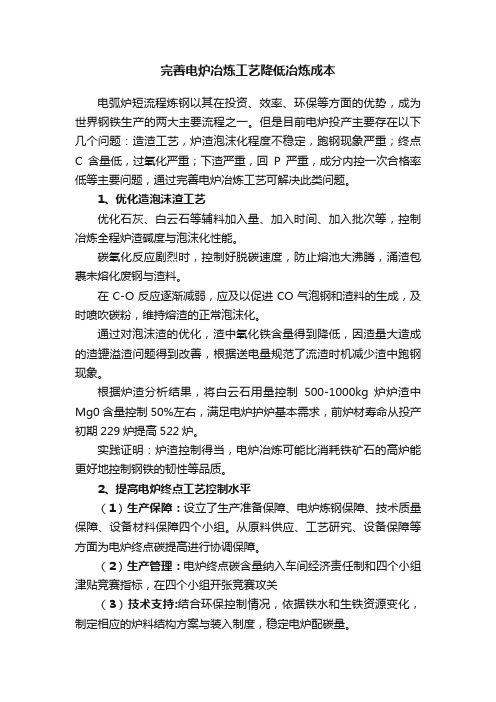
完善电炉冶炼工艺降低冶炼成本电弧炉短流程炼钢以其在投资、效率、环保等方面的优势,成为世界钢铁生产的两大主要流程之一。
但是目前电炉投产主要存在以下几个问题:造渣工艺,炉渣泡沫化程度不稳定,跑钢现象严重;终点C含量低,过氧化严重;下渣严重,回P严重,成分内控一次合格率低等主要问题,通过完善电炉冶炼工艺可解决此类问题。
1、优化造泡沫渣工艺优化石灰、白云石等辅料加入量、加入时间、加入批次等,控制冶炼全程炉渣碱度与泡沫化性能。
碳氧化反应剧烈时,控制好脱碳速度,防止熔池大沸腾,涌渣包裹未熔化废钢与渣料。
在C-O反应逐渐减弱,应及以促进CO气泡钢和渣料的生成,及时喷吹碳粉,维持熔渣的正常泡沫化。
通过对泡沫渣的优化,渣中氧化铁含量得到降低,因渣量大造成的渣罐溢渣问题得到改善,根据送电量规范了流渣时机减少渣中跑钢现象。
根据炉渣分析结果,将白云石用量控制500-1000kg炉炉渣中Mg0含量控制50%左右,满足电炉护炉基本需求,前炉材寿命从投产初期229炉提高522炉。
实践证明:炉渣控制得当,电炉冶炼可能比消耗铁矿石的高炉能更好地控制钢铁的韧性等品质。
2、提高电炉终点工艺控制水平(1)生产保障:设立了生产准备保障、电炉炼钢保障、技术质量保障、设备材料保障四个小组。
从原料供应、工艺研究、设备保障等方面为电炉终点碳提高进行协调保障。
(2)生产管理:电炉终点碳含量纳入车间经济责任制和四个小组津贴竞赛指标,在四个小组开张竞赛攻关(3)技术支持:结合环保控制情况,依据铁水和生铁资源变化,制定相应的炉料结构方案与装入制度,稳定电炉配碳量。
(4)操作工艺:完善了不同炉料装入结构时的送电制度、氧燃就比模式、(4)吹炼模式:确定了吹氧量与配碳量之间的规律;根据炉衬侵蚀情况,调整氧枪使用。
(5)炉型维护:利用更换出钢口对电炉炉型进行进一步维护,保证熔池均匀,提高操作稳定性。
3、多功能炉壁碳氧喷枪技术电炉采用当代最先进的多功能炉壁碳氧喷枪技术,以最简便、最有效的方式向电炉炼钢提供化学能,实现强化供氧、消除EBT冷区,有效缩短冶炼周期、降低电耗、提高金属收得率,达到降低生产成本和提高生产率的目的。
实习报告新钢炼铁厂

一、实习背景为了更好地了解钢铁生产过程,提高自身实践能力,我于2021年7月15日至2021年8月15日在新钢炼铁厂进行了为期一个月的实习。
实习期间,我在厂内各部门进行了轮岗学习,深入了解炼铁工艺流程、设备操作、安全管理等方面的知识。
二、实习目的1. 了解炼铁工艺流程,掌握炼铁生产的基本原理和操作方法。
2. 熟悉炼铁厂各生产环节,提高对钢铁生产的感性认识。
3. 培养团队协作精神,提高实际操作技能。
4. 为今后从事相关工作奠定基础。
三、实习内容1. 实习单位简介新钢炼铁厂位于我国江西省新余市,是一家集炼铁、炼钢、轧钢为一体的大型钢铁生产企业。
厂区占地面积约5000亩,拥有现代化炼铁生产线,年产量达500万吨。
2. 实习岗位及工作内容(1)炼铁车间实习期间,我在炼铁车间进行了为期两周的实习。
主要工作内容包括:1)学习高炉操作流程,了解高炉的构造、原理和运行参数。
2)观察高炉炉况,掌握炉况变化规律,为高炉操作提供依据。
3)协助操作人员进行高炉配料,确保高炉生产稳定。
4)学习高炉渣处理工艺,了解高炉渣的性质和处理方法。
(2)烧结车间在烧结车间实习了一周,主要工作内容包括:1)学习烧结工艺流程,了解烧结矿的制备过程。
2)观察烧结机运行情况,掌握烧结矿的质量指标。
3)协助操作人员进行烧结配料,确保烧结矿质量。
4)学习烧结废气处理工艺,了解烧结过程的环境保护措施。
(3)焦化车间在焦化车间实习了一周,主要工作内容包括:1)学习焦化工艺流程,了解焦炭的生产过程。
2)观察焦炉运行情况,掌握焦炭质量指标。
3)协助操作人员进行焦炭配煤,确保焦炭质量。
4)学习焦炉废气处理工艺,了解焦炭生产过程中的环境保护措施。
3. 安全管理在实习过程中,我深刻认识到安全管理的重要性。
厂内严格执行安全操作规程,定期进行安全教育培训,确保生产安全。
四、实习收获1. 理论知识与实践相结合,加深了对炼铁工艺流程的理解。
2. 掌握了炼铁生产的基本操作技能,为今后从事相关工作奠定了基础。
降本增效工作总结高炉炼铁
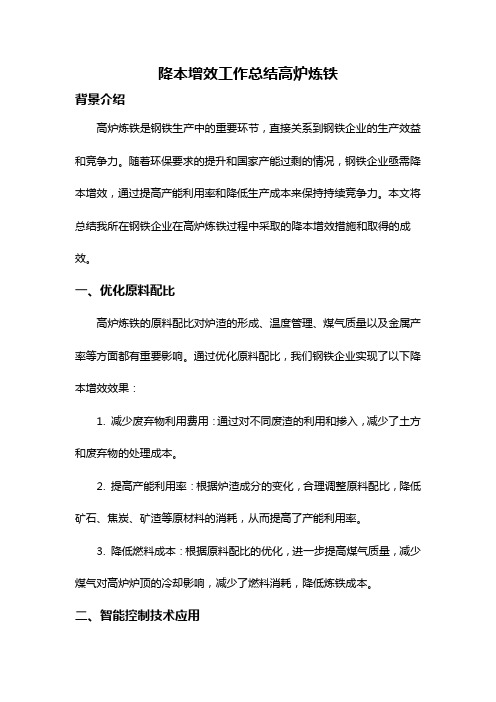
降本增效工作总结高炉炼铁背景介绍高炉炼铁是钢铁生产中的重要环节,直接关系到钢铁企业的生产效益和竞争力。
随着环保要求的提升和国家产能过剩的情况,钢铁企业亟需降本增效,通过提高产能利用率和降低生产成本来保持持续竞争力。
本文将总结我所在钢铁企业在高炉炼铁过程中采取的降本增效措施和取得的成效。
一、优化原料配比高炉炼铁的原料配比对炉渣的形成、温度管理、煤气质量以及金属产率等方面都有重要影响。
通过优化原料配比,我们钢铁企业实现了以下降本增效效果:1. 减少废弃物利用费用:通过对不同废渣的利用和掺入,减少了土方和废弃物的处理成本。
2. 提高产能利用率:根据炉渣成分的变化,合理调整原料配比,降低矿石、焦炭、矿渣等原材料的消耗,从而提高了产能利用率。
3. 降低燃料成本:根据原料配比的优化,进一步提高煤气质量,减少煤气对高炉炉顶的冷却影响,减少了燃料消耗,降低炼铁成本。
二、智能控制技术应用智能控制技术是钢铁生产中的重要手段,通过对高炉炼铁过程中的数据采集、分析和优化控制,我们钢铁企业实现了以下降本增效效果:1. 实时监控和控制:通过传感器对高炉各个关键参数进行实时监测,并结合先进的控制算法,实现炉温、气体流量、矿石供给等参数的自动控制,提高了生产效率。
2. 优化温度管理:采用先进的热风控制系统,实现对高炉内部温度的精确控制,避免了煤气的过冷和过热现象,提高了炉渣的流动性和炉渣产率。
3. 预测维修:通过对高炉设备的运行数据进行分析和建模,可以提前预测设备的故障和维修周期,做到计划性维修,避免了紧急维修带来的生产停工和维修成本的增加。
三、能耗管理与节能措施能耗是钢铁企业的重要成本之一,通过能耗管理和节能措施,我们钢铁企业实现了以下降本增效效果:1. 能耗优化:通过实施能耗检测和监控系统,对高炉各个能耗环节进行实时监测、统计和分析,并根据能耗数据制定合理的优化方案,减少了电力、煤气和水的消耗。
2. 温度回收利用:通过在高炉排烟和炉渣等排放口设置热交换器,将高温废气和废热进行回收利用,用于预热燃烧所需的空气或产生蒸汽,提高能源利用效率。
炼铁实习报告三篇

炼铁实习报告三篇炼铁实习报告篇1通过对炼铁实业部的实习,基本上弄懂了作为炼铁支柱的高炉炼铁系统有了深入的了解。
之前在炼钢实习中,了解到炼钢没有铁水就没办法炼钢了,因此,炼铁厂与炼钢厂息息相关,只有保证了有充足的铁水才能保证转炉炼钢的顺利进行,也为轧钢的提供了原材料,而高炉的副产品也为球团、烧结、铸管、轧钢等提供了源源不断的煤气。
在炼铁外调三位师傅的带领下,开启了我在炼铁厂实习的序幕。
在师傅的指导下,明白了调度员每天都做什么工作,什么事该做什么事不该做,遇到问题后怎么样处理。
在一个多月的时间我掌握了本岗位的职责,基本上具备了调度员的能力和责任,在工段上遇到不懂的问题及时的向师傅们请教,不碍于面子向员工请教,学习了各种设备的操作规程及熟悉了解工艺流程。
在高炉炼铁生产中,高炉是工艺流程的主体。
从其上部装入的铁矿石、燃料和熔剂向下运动,下部鼓入空气。
燃烧燃料产生大量的高温,还原性气体向上运动。
炉料经过加热、还原、熔化、造渣、渗碳、脱硫等一些列的物理化学过程,最后炉顶部分回收高炉煤气,炉缸生成炉渣和液态生铁的工艺过程。
炼铁实业部现共有四座高炉分别为1#高炉有效容积580m3、2#高炉有效容积120m3 、3#高炉有效容积180m3及4#高炉有效容积380m3 高炉炼铁设备。
1#高炉中使用自动化控制系统,为炼铁最大的高炉日产生铁1700吨以上,日消耗矿石等近3千吨,焦炭等燃料900吨。
一、高炉的主要组成部分高炉炉壳:炉壳的作用是固定冷却设备,保证高炉砌体牢固,密封炉体,有的还承受炉顶载荷、热应力和内部的煤气压力,有时要抵抗崩料、坐料甚至可能发生的煤气爆炸的突然冲击,因此要有足够的强度。
炉喉:高炉本体的最上部分,呈圆筒形。
炉喉既是炉料的加入口,也是煤气的导出口。
它对炉料和煤气的上部分布起控制和调节作用。
炉身:高炉铁矿石间接还原的主要区域,呈圆锥台简称圆台形,由上向下逐渐扩大,用以使炉料在遇热发生体积膨胀后不致形成料拱,并减小炉料下降阻找力。
钢铁企业如何实现降本增效

钢铁企业如何实现降本增效在当今竞争激烈的市场环境下,钢铁企业面临着诸多挑战,如原材料价格波动、市场需求变化、环保压力增大等。
为了保持竞争力和可持续发展,实现降本增效成为钢铁企业的重要任务。
本文将从多个方面探讨钢铁企业如何实现这一目标。
一、优化生产流程1、提高设备利用率设备是钢铁生产的基础,确保设备的稳定运行和高效利用对于降低成本至关重要。
钢铁企业应建立完善的设备维护保养制度,定期对设备进行检修和维护,减少设备故障停机时间。
同时,通过技术改造和升级,提高设备的性能和自动化水平,增加设备的生产能力。
2、减少生产环节中的浪费在生产过程中,存在着各种形式的浪费,如原材料的浪费、能源的浪费、时间的浪费等。
钢铁企业应通过精细化管理,对生产流程进行深入分析,找出浪费的环节并加以改进。
例如,优化配料方案,减少原材料的剩余;加强能源管理,提高能源利用效率;合理安排生产计划,减少生产等待时间。
3、推进智能制造随着信息技术的发展,智能制造成为钢铁企业提高生产效率和质量的重要手段。
通过引入先进的自动化控制系统、工业机器人、大数据分析等技术,实现生产过程的智能化监控和优化,提高生产的准确性和一致性,降低人工成本和废品率。
二、降低原材料成本1、优化采购策略原材料采购是钢铁企业成本的重要组成部分。
企业应建立科学的采购体系,加强对市场的研究和预测,把握原材料价格的波动趋势,选择合适的采购时机和供应商。
同时,通过与供应商建立长期稳定的合作关系,争取更有利的采购价格和付款条件。
2、提高原材料的利用率在钢铁生产中,原材料的利用率直接影响成本。
企业应通过技术创新和工艺改进,提高原材料的收得率和转化率。
例如,改进炼铁工艺,提高铁水的质量和产量;优化炼钢过程中的配料和造渣工艺,减少渣量和金属损失。
3、开发替代材料为了降低对传统原材料的依赖,钢铁企业可以积极开发和应用替代材料。
例如,利用废钢、生铁等再生资源作为原料,不仅可以降低成本,还能减少对环境的影响。
莱钢3200m 3高炉高效低耗生产实践
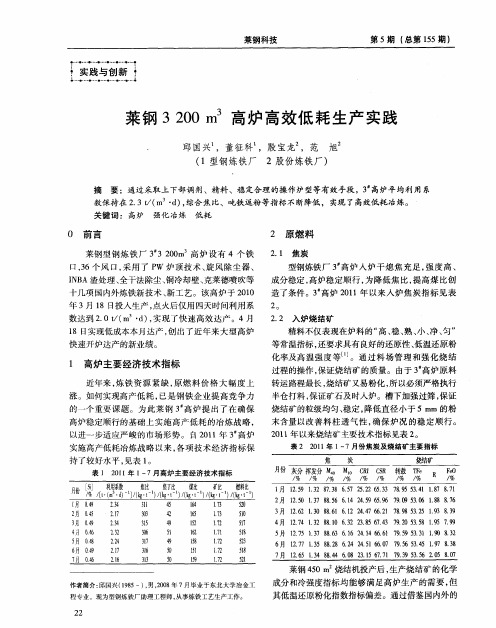
2 3 炉 料 结构 .
高炉的生产实践和研究表明, 采用高碱度烧结 矿配加酸性球团矿和部分块矿是 当前我国高炉冶炼 炉料结构较 为理想 的发展模式 。 目前 3高炉 采 J 用此模式 , 熟料 比稳定在 9 % , 5 为提高高炉利用 系
莱钢 40I 烧结机投产后 , 5 l l 生产烧结矿的化学
作者简介 : 邱国兴( 95一), ,0 8年 7月毕业于东北大学 冶金 工 18 男 20
成分和冷强度指标均能够满足高炉生产 的需要 , 但 其低温还原粉化指数指标偏差。通过借鉴 国内外 的
程专业。现为型钢炼铁厂助理工程师 , 事炼铁工艺生产工作 。 从
5月 1.5 .7 86 61 2.4 6.1 95 33 19 83 27 13 8.3 .6 4 1 66 7.95.1 .o .2 6月 1.7 .5 82 62 2.16.7 95 34 19 83 27 13 8.8 .4 45 60 7 .65.5 .7 .8
7 1. 1 4 8.4 60 2.56.l 93 5.6 20 80 月 26 . 8 . 31 77 5 3 4 8 7 . 35 . .7 9 5
型钢炼铁厂 3 高炉入炉干熄焦充足 , 强度高 、
IB N A渣处理、 全干法除尘 、 铜冷却壁 、 克莱德喷吹等
十几项国内外炼铁新技术 、 新工艺。该高炉于 2 1 00
年 3月 1 8日投人 生产 , 火后 仅用 四天 时 间利 用 系 点
成分稳定 , 高炉稳定顺行 , 为降低焦 比, 提高煤 比创
末 含 量 以改 善 料 柱 透 气 性 , 保 炉 况 的稳 定 顺 行 。 确 2 1 以来烧结 矿 主要技 术指 标见 表 2 0 1年 。
安钢炼铁厂1号高炉降低生铁成本的实践
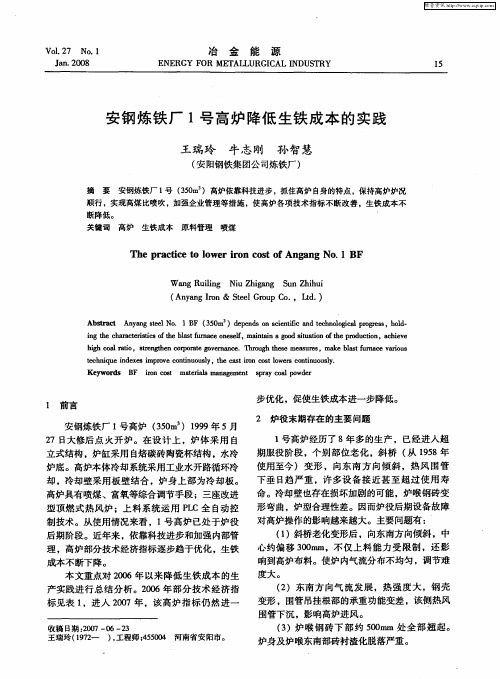
hg o lr t ih c a a o,sr n t e o p r t o en n e h o g h e eme s r s i t g h n c r o aeg v r a c .T r u ht s e au e ,ma e b a t u n c a iu k ls f r a e v r s o
理,高炉部分技术经济指标逐步趋于优化,生铁 成本 不 断下 降 。 本文重点对 20 06年 以来降低生铁成本 的生 产实践进行总结分析。20 06年部分技术经济指
标见表 l ,进 入 20 07年 ,该 高炉指标仍然进一
收稿 日期 :07— 6— 3 20 0 2 王瑞玲 ( 9 2 17 一 ) 工程师 ;50 4 河南省安 阳市。 , 450
tc n q e i d x s i r v o t u u l h a t rn c s lw r o t u u l . e h i u n e e mp o e c n n o sy,t e c s o o t o e sc n i o sy i i n Ke wo d B i n c s mae il n g me t s ry c a o d r y rs F r o t o tr s ma a e n p a o lp w e a
The pr c i e t o r i o c s fAng ng No 1 BF a tc o l we r n o to a .
W a g Rui n Ni i a g Su i u n l g i u Zh g n n Zh h i
( n agI n& Sel ru o ,Ld ) A y o n r t o pC . t. eG
维普资讯
V0 7 No 1 L2 . JI 2 0 a1 0 8 .
- 1、下载文档前请自行甄别文档内容的完整性,平台不提供额外的编辑、内容补充、找答案等附加服务。
- 2、"仅部分预览"的文档,不可在线预览部分如存在完整性等问题,可反馈申请退款(可完整预览的文档不适用该条件!)。
- 3、如文档侵犯您的权益,请联系客服反馈,我们会尽快为您处理(人工客服工作时间:9:00-18:30)。
低成本高效炼铁的生产实践张卫华吴儇(芜湖新兴铸管有限责任公司)摘要2016年,面对新的经济形势, 芜湖新兴铸管炼铁部以高效炼铁为核心,重点围绕混合喷吹、块矿使用、高风温节能等技术,深入开展对标挖潜、指标改进攻关活动,铁水成本重夺长江流域第一。
关键词高炉、优化炉料、技术创新、管理、降成本前言芜湖新兴铸管公司炼铁部目前有两座1280立方米高炉,具备年产270万吨的生产产能。
一年来,炼铁部贯彻执行公司经营理念和决策部署,先后多次到先进民企考察、对标学习,通过加强原燃料管理,优化原燃料结构,提高顶压、利用高风温等一系列措施,完善高炉操作制度,强化设备管理,确保高炉长期稳定顺行,实现高炉生产技术指标不断进步,炼铁系统工序能源消耗不断降低,从而在降本提质增效方面取得显著效果,为芜湖新兴铸管提高盈利水平做出了突出贡献。
1 严把原燃料质量关,加强原燃料质量监督管理。
强化原燃料的超前延伸管理,日常生产中,加大原燃料、辅料进厂监督管理,加大抽检频次和力度,及时掌控烧结、高炉用原燃料的品质及资源信息,从源头上杜绝一切不合格产品入厂、入炉。
加强日常原燃料管理,保证供料准确。
做好焦碳及块矿筛分、原燃料抽查监督工作,加强质量全程监督管控。
定期更换烧结冷筛筛板,提高烧结矿筛分效率。
严格入炉料质量管理,加强入炉原燃料筛分,针对不同的炉料,采用不同的筛型、筛网,提高筛分整粒的效果。
对焦筛进行改造,增大焦筛实现焦碳分级入炉,控制筛分过程的料流速度,减少粉末入炉,提高料柱透气性,提高煤气利用,促进燃料比降低。
2 优化高炉炉料结构,降低入炉原料成本。
在炼铁总成本中,原燃料费用占的比重比较大,为了实现优质、高产、低耗、低成本的冶炼目标,分析生产数据和技术指标,结合原燃料的实际状况,进一步优化高炉炉料结构和烧结配料结构,分析铁前原料构成及烧结矿强度、铁矿品位、高炉焦比、煤比等质量效益的最佳结合点,并根据下道工序铸管生产要求和炼钢品种钢冶炼需求,及时调整生产,确保优质铁水供应。
2.1推进精益生产降低烧结成本在高炉炉料结构中,烧结矿占整个炉料结构的80%。
要想实现低成本经济冶炼,降低烧结矿成本是关键。
为此,制订了几项措施,经过持续攻关,取得了明显成效。
2.1.1与采购中心充分联动,加大开辟非主流料市场力度,在平衡好铝、锌、钾、磷各微量元素、保证高炉顺行的基础上,大力推进非主流铁料及大比例澳粉使用,根据原料场地库存情况以及各种原料的烧结特性,优化了配矿结构,加大了低品质含铁原料和回收杂料的比例,合理增加了低品质原料消耗,为烧结矿成本的降低打基础。
2.1.2推行生产满负荷,仓满停机72小时生产模式。
对熔剂拖拉皮带进行改造,减少熔剂下料量波动。
改善布料方式,进一步提高料层厚度。
优化配料结构,改善料层透气性,确保烧结矿产量提高。
2.1.3提高焦粉破碎合格率,优化原料结构、结合厚料低碳烧结等措施,降低固体燃料。
控制终点、加强了堵漏风工作,提高蒸汽回收。
通过优化生产模式、厚料层烧结、提高设备开机作业率等措施,降低电耗,进一步降低烧结加工费。
2.1.4落实包机制,提高点巡检和维修质量,加强设备改造、保养和维护工作,大幅改善相关设备问题,降低非计划检修频次,提高利用系数。
2.1.5加强了工艺纪律监督、劳动纪律检查,烧结工序过程保持在受控状态下稳定运行,使各质量控制点的控制符合相关标准、要求,确保生产质量稳定的烧结矿,满足高炉生产需求。
2.1.6将提产降耗目标纳入到工部经济责任制中,在两个烧结工部八个班组开展劳动竞赛,提高单位时间产量,有效改善电耗、煤气消耗、固体燃耗等经济技术指标,确保加工费成本的有效降低。
2.2 优化高炉炉料结构,精细核算铁水成本。
炼铁的实际生产中,根据炼钢和铸管对铁水成份的要求不同,采取一炉一策的方法,制定不同的炉料结构方案,经过精确的计算和对结果的分析比较,在确保入炉原料冶金性能的同时,选择出满足高炉炼铁要求的最低成本炉料结构。
1#高炉生产炼钢用铁水,3#高炉主要生产铸管用铁水,在满足铸管生产的前提下,适当调整配比生产炼钢铁水,降低入炉原料成本。
认真分析生产数据和技术指标,结合原燃料的实际状况,进一步优化高炉炉料结构和烧结矿配矿结构,分析铁前原料构成及烧结矿强度、铁矿品位、高炉焦比、煤比等质量效益的最佳结合点,并根据下道工序铸管生产要求和炼钢品种钢冶炼需求,及时调整生产,确保优质铁水供应。
在保证炉料结构满足高炉稳定顺行的前提下,由精料向经济料模式转变,增加烧结矿比例,调整烧结矿碱度,用低价格的块矿替代高价格的球团矿,降低炉料结构成本,实现炼铁的低成本运行。
3 优化操作,加强高炉炼铁工序的技术进步。
3.1 依靠技术创新,全面调整优化为促进指标持续改善,结合原燃料实际,以技术创新为核心动力,强化工艺技术管理和精细化操作,重点在提高品位、优化燃料结构、优化入炉料配比等方面开展突破性研究,寻求最优原料结构、最优原料成本。
入炉品位和块矿使用比例是影响生产成本的主要原因,根据两座高炉实际状况,摸索高炉操作特点,结合外围条件分阶段对顶压、风压、装料制度和炉料结构展开攻关,在确保入炉品位不低于57.5%的基础上,提高烧结矿比例到82%,,降低价格较高的外购球团配比到8%,增加块矿比例到12%,实现主材成本下降5元的目标,降低主材成本。
优化、主攻炉料结构,在提高生矿的比例的同时,提高焦丁粒度,增加焦丁比例到30%,降低焦比,增加煤比和烟煤混喷,提高顶压、提高煤气利用率,降低入炉燃料成本。
3.2 强化工序稳定,改善高炉指标把对标挖潜贯彻于强化管理和技术创新工作中,从技术操作调整上寻求指标改善突破口,以各工序稳定促高炉指标改善、成本降低。
白灰生产保证产量完成计划,确保粉灰供应,满足烧结要求。
烧结生产服从高炉需要,执行仓满停机和分品种生产的模式,努力提高烧结矿碱度稳定率,确保综合合格率达到99.5%以上,转鼓强度提高到76%以上,高炉检测的<5mm粒级低于3%。
高炉生产以顺行为基础,两座高炉以日产“小目标”,促进月计划产量完成,通过产量增加促进单位固定成本降低。
为提高生产稳定性,促进成本进一步降低,重点围绕炼铁燃料比和烧结固体燃耗这两个核心高价值指标展开攻关,明确期限、要实现的目标、责任人,分三个阶段实施,高炉燃料比从520 kg/t,逐步降到515 kg/t,再降到510 kg/t,烧结固体燃耗从63 kg/t,逐步降到59 kg/t,再降到55 kg/t。
4 推进创新,打赢提质增效攻坚战。
4.1 不断优化创新,提升经营质量从抓原料成本入手,通过细化配料的每一项细节,找到烧结矿质量和配料结构的平衡点,充分利用原燃料之间的差价,降低生产原料的成本费用。
在保证烧结矿质量和产量的前提下,增加成大粗精粉、伊朗粉等非主流料使用量,重点消耗各类高微量杂料,加大落地返矿使用量,确保零库存。
在有效控制好烧结矿铝含量的前提下,消化含铝较高印度粉3万吨,优化料场铁料堆放、活化资金。
烧结矿质量对高炉稳定顺行影响很大,因此,烧结矿质量是技术攻关的重要内容。
工作中,通过改造混合机扬料板,提高混合料成球率,提高利用系数;优化烧结配料结构,加强工艺操作管理,稳定生产过程控制,杜绝成份波动;推行低温厚料层烧结,严格控制烧结机机速。
提高熔剂消化器工技术操作水平,稳定熔剂消化过程。
控制烧结矿碱度,保证烧结矿品位稳定,转鼓指数达标,满足高炉冶炼需求。
推进高炉提产量、提指标、降消耗专项工作,重点围绕焦比、煤比、燃料比、风温、顶压等技术经济指标,开展生产技术攻关活动。
加大原料结构管控,开展经济料配加研究,强化工艺控制和技术攻关,在保持炉况稳定顺行的前提下,提高生矿配比,降低高价球团用量,稳定烧结矿碱度。
狠抓关键岗位操作,努力提高风温使用水平,提高炉顶压力。
采取富氧喷煤,烟煤混喷,低硅冶炼等多种措施,促进产量逐步提高,入炉焦比稳步降低。
4.2 立足生产实际,着力挖潜降耗白灰工序根据下道工序需要和市场变化情况,优化生产模式,在保证白灰质量前提下强化对煤气消耗控制;通过对预热器推杆孔、烟管和下料管等改造治漏,提高热利用率,降低煤气消耗。
在保证工艺稳定顺行情况下,将上料振动筛由目前的12*12mm方孔筛改为10*10mm方孔筛,降低原料单耗。
推进降低焦炉煤气、石灰石单耗和电耗等降本攻关工作,实现降本增效。
1-9月份累计增效79.39万元。
烧结工序根据高炉需求组织生产,确保产量满足高炉烧结矿80%的配比,围绕改善烧结矿质量开展攻关,稳定烧结矿碱度和转鼓强度,降低5mm以下入炉粒级比例,为高炉稳定顺行创造良好条件。
跟踪粗精粉与粗粉价格,优先选择价格较为便宜的粗粉,达到最优成本管理模式。
在性价比相等及炉渣铝负荷范围内,提高澳粉中的高品位铁料使用量,增加非主流料金布巴与阿特拉斯等铁料的混匀使用,确保高品、中烧损原料结构,降低固体燃耗。
推行厚料层烧结,降低燃料消耗0.2%,增加高炉重力除尘灰使用,控制好煤焦比例、水份和粒度,千方百计降低燃料消耗。
炼铁工序实施精细化操作,控制炉温硅偏差,加强炉前管理,抓好炉前三率,出尽渣铁;控制合理的铁水成份,保证下道工序生产需求;加强铁水罐管理,控制铁损在1%以下。
开展小粒铁回收、高炉使用焦丁比、降低铁损、降低辅料、提高烟煤(市场煤)比率、提高铁水合格率、降低燃料比和电耗等降本增效、攻关创效活动,深挖内部潜力,促进成本进一步降低。
4.3 加强费用控制,有效降低运输费。
炼铁、烧结生产原料品种繁多,每年有近480万吨的物流量。
由于资源庞杂、运输方式各异,运输协同优势未能最大限度发挥。
将降低运输费作为提质增效重点工作之一,聚焦制约运输费用降低的重点问题和关键环节,有序组织炼铁和烧结生产区域进厂原料倒运重点指标的管理和突破,加强汽运费、进厂原料区域倒运费的管控。
优化原燃料堆放,提高堆取料机作业率,充分利用皮带运输,减少内部物料倒运。
减少汽运、铲车、挖掘机进料费用,全年运输费比计划降低265.24万元。
外委运输费通过招标、比价,采取吨矿和吨铁的结算方式,拓展降本空间。
4.4 创新技术改造,挖潜节流增效。
充分认识科技创新在提高生产效率、降成本增效益、促进企业发展等方面发挥的重要作用,鼓励引导技术人员以解决制约各环节生产问题为突破口,积极开展创新改造项目攻关活动。
4.4.1 码头利旧皮带改造对闲置的江边码头焦化来煤皮带实施改造,使其兼具料场落地料上料的功能,在原有运输量基础上,增加落地料3000吨/日的运输量,有效解决了雨季露天料场爬坡皮带打滑供料困难的瓶颈问题,消除了铁、烧原料输送线受限制环节,保证了稳定连续生产。
4.4.2 中转仓改造对供料6#、7#中转仓的出料方式进行改造,使成品烧结矿通过皮带输送直接进入高炉的中转仓,降低烧结矿返矿率,节省落地矿筛分费用,减少内循环返矿运输费用,年增效91.68万元。