现代氰化提金工艺
全泥氰化提金工艺简介
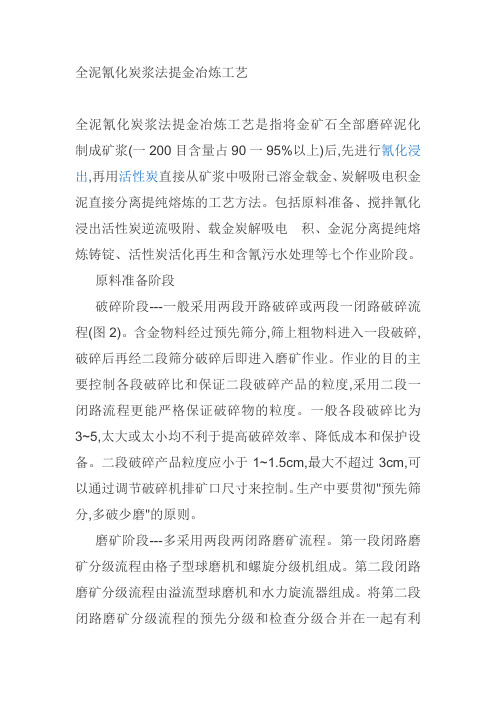
全泥氰化炭浆法提金冶炼工艺全泥氰化炭浆法提金冶炼工艺是指将金矿石全部磨碎泥化制成矿浆(一200目含量占90一95%以上)后,先进行氰化浸出,再用活性炭直接从矿浆中吸附已溶金载金、炭解吸电积金泥直接分离提纯熔炼的工艺方法。
包括原料准备、搅拌氰化浸出活性炭逆流吸附、载金炭解吸电积、金泥分离提纯熔炼铸锭、活性炭活化再生和含氰污水处理等七个作业阶段。
原料准备阶段破碎阶段---一般采用两段开路破碎或两段一闭路破碎流程(图2)。
含金物料经过预先筛分,筛上粗物料进入一段破碎,破碎后再经二段筛分破碎后即进入磨矿作业。
作业的目的主要控制各段破碎比和保证二段破碎产品的粒度,采用二段一闭路流程更能严格保证破碎物的粒度。
一般各段破碎比为3~5,太大或太小均不利于提高破碎效率、降低成本和保护设备。
二段破碎产品粒度应小于1~1.5cm,最大不超过3cm,可以通过调节破碎机排矿口尺寸来控制。
生产中要贯彻"预先筛分,多破少磨"的原则。
磨矿阶段---多采用两段两闭路磨矿流程。
第一段闭路磨矿分级流程由格子型球磨机和螺旋分级机组成。
第二段闭路磨矿分级流程由溢流型球磨机和水力旋流器组成。
将第二段闭路磨矿分级流程的预先分级和检查分级合并在一起有利于提高磨矿效率和保证产品细度。
破碎好的含金物料经过第一段闭路磨矿分级流程后,矿浆中一200目含量为55%一65%。
再经过第二段闭路磨矿分级流程后矿浆中一200目物料含量就可达90%一95%以上,符合全泥氰化工艺的细度要求。
本段作业主要控制磨矿浓度、溢流浓度和溢流细度。
一般磨矿浓度:第一段为75%一80%,第二段为60%~65%;溢流浓度:第一段为25%~30%,第二段为14%一20%;溢流细度(一200目含量):第一段为55%~65%,第二段为90写一95%以上。
磨矿浓度的控制主要通过调节给水量、给矿量和返砂比等,若磨矿浓度偏高,则增加给水量、减少给图3两段两闭路磨矿流程矿量,增大返砂比等,反之亦然。
氰化法提金工艺

氰化法提金工艺嘿,朋友们!今天咱来聊聊氰化法提金工艺,这可真是个有趣又重要的玩意儿呢!你想想看,金子啊,那可是闪闪发光让人眼馋的宝贝呀!而氰化法就是能把金子从各种矿石里给弄出来的厉害手段。
就好像是一个神奇的魔法,能把隐藏起来的金子给变出来。
氰化法提金呢,简单来说,就是利用氰化物的特性来和金子发生反应。
这就好比是两个好朋友,一见面就紧紧拥抱在一起啦。
氰化物就像是个热情的小伙伴,紧紧抱住金子不撒手。
不过呢,这个过程可不能马虎。
就像做饭一样,得掌握好火候和调料的用量。
氰化物的浓度呀,反应的时间呀,温度呀等等,都得恰到好处。
不然,要么金子提不出来,要么可能会出啥岔子呢。
咱再打个比方,这氰化法提金就像是一场精密的手术。
医生得小心翼翼地操作,不能有一点差错。
在这个过程中,每一个环节都得精心照料,稍有不慎可能就前功尽弃啦。
而且呀,这氰化法提金可不是随随便便就能干的。
得有专业的设备和技术人员。
这可不是小孩子过家家,得认真对待才行呢!你说要是设备不行,那不就像是战士上战场没带好武器一样嘛,怎么能打胜仗呢?还有啊,安全问题可不能忽视。
氰化物可不是好惹的,要是不小心弄不好,那可是会出大问题的。
就像家里的电老虎,你不注意它就会咬你一口。
所以呀,操作的时候一定要万分小心,做好各种防护措施。
但是呢,一旦掌握好了这个工艺,那可就厉害啦!能把那些藏在矿石里的金子都给弄出来,那感觉,就像是发现了一个大宝藏!总的来说,氰化法提金工艺是个很有意思也很有挑战性的事情。
它就像是一个神秘的宝库,等待着我们去探索和发现。
只要我们认真对待,小心操作,就一定能从里面掏出大把大把的金子来!不是吗?。
现代氰化提金工艺
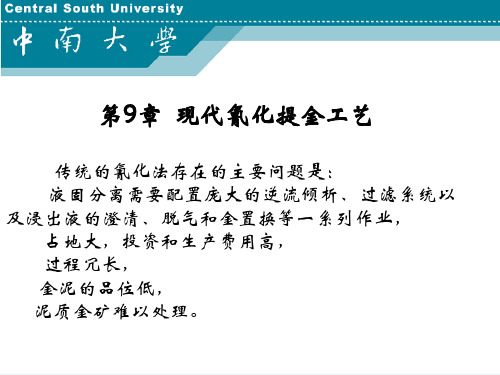
⑶ 矿浆浓度 表9-3 矿浆浓度对活性炭吸附金速度的影响
0 矿浆浓度(%) 速度常数(h-1) 2070 1860 1480 1250 1190 10 20 30 50
条件:离子强度:0; 搅拌速度:1250r/min; pH 7; 炭粒度:0.50~0.70mm 条件:离子强度: 搅拌速度: 炭粒度:
矿浆pH pH值 ⑸ 矿浆pH值
表9-4 氰化矿浆pH值对金吸附速度和平衡容量的影响 11.3 矿浆pH值 速度常数(h-1) 吸附容量(ppm) 3010 3000 3660 3900 4420 4880 75000 86000 92000 122000 143000 216000 9.1 7.1 4.2 3.1 1.5
8.1.2 活性炭吸附金的机理
⑴ 以金属形态被吸附 活性炭从金氯配合物(AuCl4-)溶液中吸附金后,可明显地看到 在炭的表面有黄色的金属金。以此推断金氰配合物也可被炭还 原。这种观点认为,炭上吸附的还原气体,如CO,可把金还原。 采用现代的分析技术X射线光电子能谱(XPS)对炭上被吸 附物中的金的价态的研究表明,被吸附的金的表观价态为 +0.3价。
1) 在活性炭的巨大表面上和微孔中,吸附Mn+[Au(CN)2-]n离子对或中性分子, 也可吸附Au(CN)-2 ; 2) Au(CN)2-在吸附过程中分解成不溶性的AuCN,AuCN保留在微孔中; 3) Au(CN)2-部分还原成某种0价至1价之间的金混合物。
8.1.3 炭浆法提金工艺
炭浆法由预筛、氰化浸出、吸附、解吸、电解(电 积)和炭的再生等几个主要作业组成。
⑷ 以AuCN沉淀 早期有人认为在活性炭的孔隙中能沉淀出不溶性的AuCN。 AuCN的产生是氧化CN-的结果: KAu(CN)2+0.5O2=AuCN+KCNO 也有人认为是酸分解的结果: Au(CN)2- +H+=AuCN+HCN
氰化法提金的基本原理21212
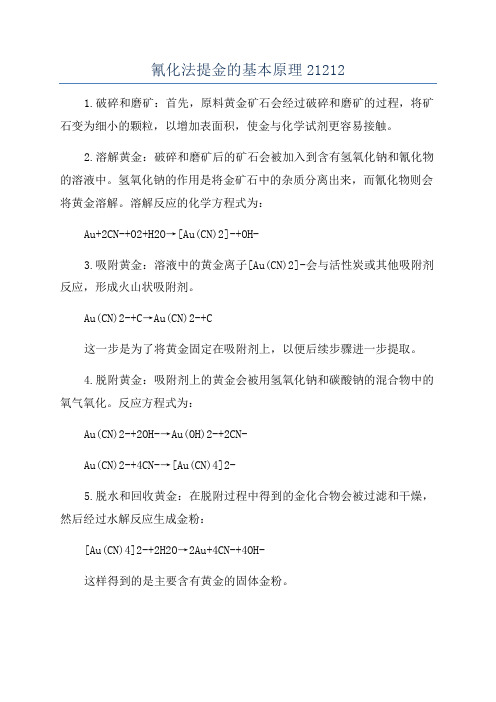
氰化法提金的基本原理21212
1.破碎和磨矿:首先,原料黄金矿石会经过破碎和磨矿的过程,将矿石变为细小的颗粒,以增加表面积,使金与化学试剂更容易接触。
2.溶解黄金:破碎和磨矿后的矿石会被加入到含有氢氧化钠和氰化物的溶液中。
氢氧化钠的作用是将金矿石中的杂质分离出来,而氰化物则会将黄金溶解。
溶解反应的化学方程式为:
Au+2CN-+O2+H2O→[Au(CN)2]-+OH-
3.吸附黄金:溶液中的黄金离子[Au(CN)2]-会与活性炭或其他吸附剂反应,形成火山状吸附剂。
Au(CN)2-+C→Au(CN)2-+C
这一步是为了将黄金固定在吸附剂上,以便后续步骤进一步提取。
4.脱附黄金:吸附剂上的黄金会被用氢氧化钠和碳酸钠的混合物中的氧气氧化。
反应方程式为:
Au(CN)2-+2OH-→Au(OH)2-+2CN-
Au(CN)2-+4CN-→[Au(CN)4]2-
5.脱水和回收黄金:在脱附过程中得到的金化合物会被过滤和干燥,然后经过水解反应生成金粉:
[Au(CN)4]2-+2H2O→2Au+4CN-+4OH-
这样得到的是主要含有黄金的固体金粉。
总结:氰化法提金的基本原理是先将黄金矿石破碎和磨矿,使黄金更易溶解。
然后将矿石放入氢氧化钠和氰化物的溶液中进行溶解反应,形成黄金离子。
接下来,通过吸附剂将黄金离子固定在活性炭等吸附剂上。
脱附步骤将黄金离子转化为黄金化合物,然后脱水和回收黄金,得到最终的金粉。
该方法具有高效、高回收率和相对较低的成本,并被广泛应用于金矿加工。
提金技术工艺大全(专利)
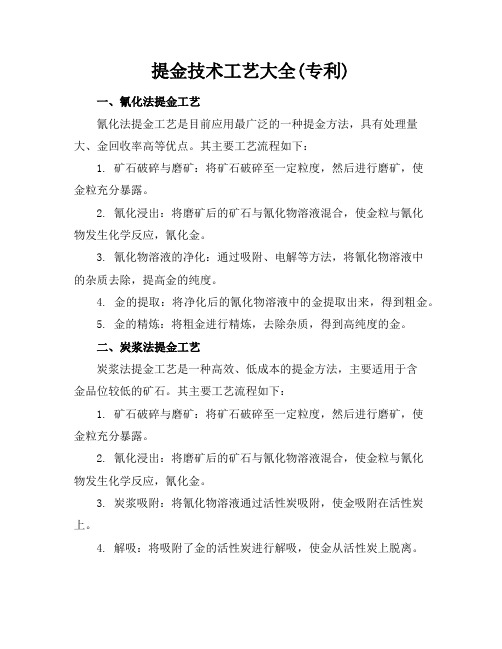
提金技术工艺大全(专利)一、氰化法提金工艺氰化法提金工艺是目前应用最广泛的一种提金方法,具有处理量大、金回收率高等优点。
其主要工艺流程如下:1. 矿石破碎与磨矿:将矿石破碎至一定粒度,然后进行磨矿,使金粒充分暴露。
2. 氰化浸出:将磨矿后的矿石与氰化物溶液混合,使金粒与氰化物发生化学反应,氰化金。
3. 氰化物溶液的净化:通过吸附、电解等方法,将氰化物溶液中的杂质去除,提高金的纯度。
4. 金的提取:将净化后的氰化物溶液中的金提取出来,得到粗金。
5. 金的精炼:将粗金进行精炼,去除杂质,得到高纯度的金。
二、炭浆法提金工艺炭浆法提金工艺是一种高效、低成本的提金方法,主要适用于含金品位较低的矿石。
其主要工艺流程如下:1. 矿石破碎与磨矿:将矿石破碎至一定粒度,然后进行磨矿,使金粒充分暴露。
2. 氰化浸出:将磨矿后的矿石与氰化物溶液混合,使金粒与氰化物发生化学反应,氰化金。
3. 炭浆吸附:将氰化物溶液通过活性炭吸附,使金吸附在活性炭上。
4. 解吸:将吸附了金的活性炭进行解吸,使金从活性炭上脱离。
5. 金的精炼:将解吸后的金进行精炼,去除杂质,得到高纯度的金。
三、树脂法提金工艺树脂法提金工艺是一种新型、高效的提金方法,具有处理量大、金回收率高等优点。
其主要工艺流程如下:1. 矿石破碎与磨矿:将矿石破碎至一定粒度,然后进行磨矿,使金粒充分暴露。
2. 氰化浸出:将磨矿后的矿石与氰化物溶液混合,使金粒与氰化物发生化学反应,氰化金。
3. 树脂吸附:将氰化物溶液通过树脂吸附,使金吸附在树脂上。
4. 解吸:将吸附了金的树脂进行解吸,使金从树脂上脱离。
5. 金的精炼:将解吸后的金进行精炼,去除杂质,得到高纯度的金。
四、生物法提金工艺生物法提金工艺是一种环保、低成本的提金方法,主要适用于含金品位较低的矿石。
其主要工艺流程如下:1. 矿石破碎与磨矿:将矿石破碎至一定粒度,然后进行磨矿,使金粒充分暴露。
2. 生物氧化:将磨矿后的矿石与生物氧化剂混合,使金粒与氧化剂发生反应,可溶性金。
几种氰化法提金介绍
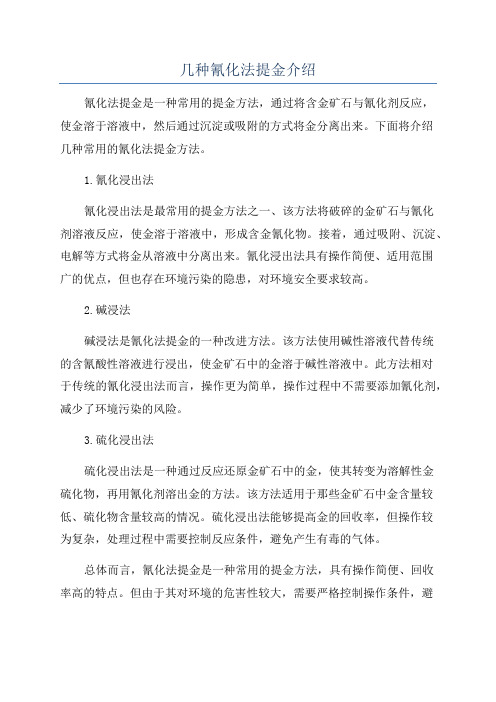
几种氰化法提金介绍
氰化法提金是一种常用的提金方法,通过将含金矿石与氰化剂反应,
使金溶于溶液中,然后通过沉淀或吸附的方式将金分离出来。
下面将介绍
几种常用的氰化法提金方法。
1.氰化浸出法
氰化浸出法是最常用的提金方法之一、该方法将破碎的金矿石与氰化
剂溶液反应,使金溶于溶液中,形成含金氰化物。
接着,通过吸附、沉淀、电解等方式将金从溶液中分离出来。
氰化浸出法具有操作简便、适用范围
广的优点,但也存在环境污染的隐患,对环境安全要求较高。
2.碱浸法
碱浸法是氰化法提金的一种改进方法。
该方法使用碱性溶液代替传统
的含氰酸性溶液进行浸出,使金矿石中的金溶于碱性溶液中。
此方法相对
于传统的氰化浸出法而言,操作更为简单,操作过程中不需要添加氰化剂,减少了环境污染的风险。
3.硫化浸出法
硫化浸出法是一种通过反应还原金矿石中的金,使其转变为溶解性金
硫化物,再用氰化剂溶出金的方法。
该方法适用于那些金矿石中金含量较低、硫化物含量较高的情况。
硫化浸出法能够提高金的回收率,但操作较
为复杂,处理过程中需要控制反应条件,避免产生有毒的气体。
总体而言,氰化法提金是一种常用的提金方法,具有操作简便、回收
率高的特点。
但由于其对环境的危害性较大,需要严格控制操作条件,避
免对生态环境造成污染。
在实际应用中,还可以结合其他方法,如浮选、压磨等,来提高金的提取率和回收率,降低环境风险。
全泥氰化工艺
二、搅拌氰化浸出阶段 矿浆在搅拌槽中进行预浸(3槽,氰化钠溶 液提前加入磨矿机中也属预浸)。关键是控 制CN-浓度(万分之5~5.5)和氧含量(充气 量0.02m3/m3· min和充气压力100kPa,调节各 气阀门),矿浆表面均匀弥散5~15mm直径气 泡为宜。
三、活性炭逆流吸附阶段 边浸边吸作业,即活性炭的加炭、串炭和 提炭操作经提炭器的运移方向与矿浆流向相 反。 1、矿浆氰根浓度:万分之3~5,且沿矿浆流 向降低,由各槽氰化钠用量控制。 2炭逆流吸附阶段 5、串炭量:为保持吸附系统金总量平衡和各 槽内槽间炭吸附性能,串炭量一般占槽内总 量的10~20%,通过调节串炭时间来控制。 6、炭载金量:为综合回银,控制炭载金量在 900~1000g/t,通过调节提炭量来控制。
三、活性炭逆流吸附阶段 7、尾液含金量:控制尾液含金量在0.07g/m3 以下,过高则说明活性炭吸附率降低了,可 通过增加底炭密度、降低载金炭含量和缩短 串炭时间等来控制。 8、尾矿品位:要求一厂小于0.24g/t、二厂小 于0.22g/t,原则上可通过提高磨矿细度、降低 矿浆浓度、减少处理量和延长浸出时间等来 控制。
四、尾矿尾水处理 尾矿→压滤→ 尾矿库(堆存) →尾水(压滤水、澄清水)→ 生 产高位水池(回用)
全泥氰化炭浆法提金工艺 一、原料准备作业 1、破碎阶段:将原矿石由500~0mm破碎至 250~0mm。 2、磨矿阶段:采用半自磨(一段)和球磨 (二段)与旋流器分级组成闭路系统,保证 氰化浸出所需要的细度(-200目占92%以上, 磨矿细度由矿石性质决定,主要是保证金的 单体解离度)。
一、原料准备作业 3、除屑作业:遵循由粗到细除屑的原则进行 多级除屑流程,破碎前人工捡出木屑杂物, 磨机出料口设圆筒筛,渣浆泵池前设细筛网 (一般20目),旋流器溢流设圆筒筛(24~28 目)。 4、调浆阶段:在浓密机中进行,满足氰化的 条件:控制浓度35%~38%、pH值10~11(浓 度由浓密机底流量和添加絮凝剂用量控制, pH值由原矿中石灰用量和浓密机中氢氧化钠 用量控制)。
氰化法提金工艺
氰化法提金工艺1、氰化物溶金机理氰化法是用氰化物从矿石中浸取金并把溶液中的金分离出来的方法,其基本化学反应式为:4AU+8NaCN+O2+2H2O→4Na AU(CN)2+4NaOH它包括氧的吸收溶解,其组分扩散到金表面,吸附,电化学反应等步骤。
其中O2和CN –的扩散对金的浸出速率起到至关重要的作用。
2、浸出药剂可用于溶金的氰化物有:KCN、NaCN、NH4CN、Ca(CN)2选择氰化物时,应综合考虑氰化物对金的溶解能力、化学稳定性、耗量及价格等。
我国黄金矿山大多采用NaCN。
3、保护碱氰化物损耗除了机械原因外,还有化学原因:一是氰化物的水解生成HCN气体挥发造成损失和危害;二是溶液中存在的二氧化碳及硫化物氧化生成的酸(H2SO3,H2SO4)也与氰化物作用生成HCN气体;三是黄铁矿氧化时,除生成H2 SO4外,还生成一些硫酸亚铁(Fe SO4),与氰化物作用生成Fe (CN)6 ,而当溶液中有碱和氧时,Fe SO4可氧化为Fe2(SO4)3,再与碱作用生成Fe(OH)3沉淀,Fe(OH)3不与氰化物反应,因而,加入碱起到保护氰化物的作用,加入的碱叫做保护碱。
生产中通常用石灰作保护碱。
4、影响金溶解速度的主要因素4.1、氰化物和氧的浓度氰化物的浓度和溶液中溶解氧的浓度是决定金溶解速度两个主要因素。
金在稀氰化物溶液中溶解速度大,这是因为氧在稀氰化物溶液中溶解度较大,扩散速度也较快,因而保证了溶金需要的最低氧浓度。
不同矿石的氰化物耗量不同是因为矿石中含有不同量消耗氰化物的杂质。
常规的氰化物浓度一般在0.03%~0.10%之间。
4.2、温度金在氰化液中的溶解速度与温度有关,通常温度高溶解速度快,在无特殊工艺要求的条件下,使矿浆温度维持在150C~250C即可满足浸出的要求。
4.3、金粒的大小和形状金的溶解速度与金粒暴露的表面积成正比,因此氰化作业的磨矿粒度要比浮选更细一些。
4.4、矿浆浓度和矿泥矿浆浓度和矿泥含量直接影响溶剂的扩散速度和溶剂与金粒的接触。
金矿选矿氰化-炭浆吸附法选矿工艺流程
金矿选矿氰化-炭浆吸附法选矿工艺流程在多种金矿选矿工艺中,最常见的有重选、混汞、浮选、氰化法,不常见的有炭浆吸附法、离子交换法、高温焙烧法。
河南省荥阳市矿山机械制造厂专家在本文为广大用户讲解金矿氰化法及金矿炭浆吸附法的详细工艺流程和具体操作方法。
1、金矿氰化法:氰化工艺也要经过鄂式破碎机、圆锥破碎机两段闭合破碎、球磨机磨矿、浮选机浮选等流程,再用浓缩机脱去含金硫精矿的多余水分,提高矿浆浓度,同时脱去矿浆中有害氰化的浮选药剂。
然后送去细磨,使金粒进一步解离,再用稀的氰化物溶液,在充氧的条件下,在进出槽中搅拌浸出金,浸出矿浆经过洗涤,使含金溶液与固体分离,得出贵液和氰尾。
贵液再经净化脱氧处理后,用金属锌置换产出金泥和贫液。
金泥送炼金房熔炼得到合质金,或进一步加工或纯度更高的金锭,贫液可以返回流程再用,或经净化处理后排放。
2、金矿炭浆吸附法:炭浆法提金工艺是氰化提金的方法之一。
是含金物料氰化浸出完成之后,一价金氰化物进行炭吸附的工艺过程。
炭浆法提金主要适用于矿泥含量高的含金氧化矿石,由矿石含泥高,固液分离困难,活性炭可以从溶液中吸附贵金属,可直接从低化矿浆中吸附金,这样就省去了固液分离作业。
碳浆法提金工艺流程:把含金物料碎磨至适于氰化粒度,一般要求小于28目并除去木屑等杂质,经浓缩脱水使浸出矿浆浓度达到45~50%为宜;一般用5-8个搅拌槽搅拌浸出,氰化矿浆进入搅拌吸附槽,实现活性炭和矿浆逆向流动,吸附矿浆中已溶的金;载金炭解吸;载金炭解吸可得到含金达600克/米3的高品位贵液,经电积卖锌置换法得到金粉,并送熔炼得到金锭。
载金炭解吸的方法有哪些:1、热苛性氰化钠溶液解吸;2、除浓度苛性氰化钠溶液加酒精解吸;3、在加温加压条件下用苛性氰化钠溶液解吸;4、高浓度苛性氰化钠溶液解吸。
活性炭的再生利用:解吸后的活性炭先用稀硫酸(硝酸)酸洗,以除去碳酸盐等聚积物,经几次返回使用后需进行热力活化以恢复炭的吸附活性。
全泥氰化提金工艺设计与生产实践
全泥氰化提金工艺设计与生产实践一、工艺流程设计泥氰化提金工艺是一种常用的金属提取工艺,主要用于提取含金废物中的金属成分。
下面是一个典型的泥氰化提金工艺流程设计:1.前处理:将含金废物进行粉碎与破碎,使其颗粒大小均匀,并去除其中的杂质和有机物。
2.浸泡:将经过前处理的含金废物浸入氰化溶液中,进行化学反应。
反应时间根据废物的性质和废物含金量而定,一般为24小时至72小时。
3.沉淀:将反应后的溶液经过沉淀处理,使其中的金属成分沉淀下来。
4.过滤:将沉淀后的溶液进行过滤,去除其中的固体杂质。
5.再溶解:将过滤后的固体沉淀添加到盐酸等溶液中进行再溶解,使其中的金属成分溶解于溶液中。
6.萃取:将再溶解后的溶液进行萃取处理,利用有机溶剂提取其中的金属成分。
萃取条件为温度控制在50-70摄氏度,时间控制在2-4小时。
7.还原:将经过萃取的有机溶剂中的金属成分进行还原处理,得到金属纯度较高的金属产品。
8.精炼:将还原后的金属产品进行精炼处理,提高其纯度。
以上是一个典型的泥氰化提金工艺流程设计,根据实际情况,工艺流程中的各个环节还可以进行调整,以提高提金效率和产品的纯度。
二、生产实践在实际生产过程中,需要注意以下几个方面:1.设备选择:根据生产规模和工艺流程要求,选择合适的设备,如破碎机、浸泡槽、沉淀槽、过滤设备、萃取塔等。
设备选择要考虑生产效率、产品质量、安全性和经济性等因素。
2.溶液控制:泥氰化提金工艺中的浸泡和萃取环节涉及到溶液控制,需要严格控制溶液的温度、浓度、pH值等参数,以提高金属提取率和产品纯度。
3.杂质处理:在泥氰化提金过程中,含金废物中通常会存在一些杂质,如铜、银、铅等,需要根据具体情况采取相应的处理方法,如溶解、沉淀、萃取等,以提高产品的纯度。
4.安全保护:在泥氰化提金生产中,由于涉及到氰化物的使用,需要加强安全保护工作,严格遵守操作规程,提供足够的通风和防护设施,确保操作人员和环境的安全。
5.产品质量检测:在生产过程中,需要对产品的质量进行检测,包括金属纯度、杂质含量、产品外观等指标的检测,以确保产品符合质量要求。
- 1、下载文档前请自行甄别文档内容的完整性,平台不提供额外的编辑、内容补充、找答案等附加服务。
- 2、"仅部分预览"的文档,不可在线预览部分如存在完整性等问题,可反馈申请退款(可完整预览的文档不适用该条件!)。
- 3、如文档侵犯您的权益,请联系客服反馈,我们会尽快为您处理(人工客服工作时间:9:00-18:30)。
图9-2 pH值对活性炭吸附 金容量的影响
综合的机理:
1) 在活性炭的巨大表面上和微孔中,吸附Mn+[Au(CN)2-]n离子对或中性分子, 也可吸附Au(CN)-2 ;
2) Au(CN)2-在吸附过程中分解成不溶性的AuCN,AuCN保留在微孔中; 3) Au(CN)2-部分还原成某种0价至1价之间的金混合物。
1~4
化学 吸附 特性
比表面(BET法)/m2/g 碘值/mg/g 四氯化碳值/%
1050~1200 1000~1500
60~70
苯值/%
36~40
选用炭浆法活性炭最重要的条件,一是它对金应具有 良好的吸附性能,二是炭粒应当具有很强的耐磨性能。良好 的炭浆法活性炭,除了具备表9-1的性能外,通常还可用下列 三项技术指标来确定。
活性炭的元素组成以碳为主,有少量的氧和氢。 它们中常有一部分与活性炭表面结合,以官能团的 形式存在。活性炭中常见的官能团有羧基、酚羟基和 醌型羰基,也发现有普通内酯、荧光素型内酯、羟酸 酐和环状过氧化物等。它们位于活性炭层中环状网的 破裂边缘上,这些表面氧化物对活性炭的化学吸附起 着重要作用。
活性炭的活性,是巨大的比表面和存在于 表面的官能团二者结合所产生的。
吸附强度取决于金属阳离子,其顺序为: Ca2+> Mg2+> H+> Li+> Na+> K+ 这样活性炭灰分中的Ca2+及溶液中的Ca2+、H+都可能取 代Na+、K+,如: 2KAu(CN)2+Ca(OH)2+2CO2=Ca(Au(CN)2)2 +2KHCO3
⑷ 以AuCN沉淀 早期有人认为在活性炭的孔隙中能沉淀出不溶性的AuCN。 AuCN的产生是氧化CN-的结果: KAu(CN)2+0.5O2=AuCN+KCNO 也有人认为是酸分解的结果:
采用现代的分析技术X射线光电子能谱(XPS)对炭上被吸 附物中的金的价态的研究表明,被吸附的金的表观价态为 +0.3价。
⑵ 以Au(CN)2-配离子形式被吸附 这种理论认为,炭表面上存在带正电荷的格点,这些正电荷 格点是这样产生的:活性炭在室温下与空气中的氧接触,形成 具有碱性特征的表面氧化物,这种氧化物在炭上的结合是不牢 固的。当炭与水作用时,它会转入溶液中并形成OH-离子,这 样炭表面带上正电荷: C+O2+2H2O=C2++2OH-+H2O2
⑴ 在含金1mg/L溶液中平衡吸附24h,活性炭的载金容 量应达25g/kg。
⑵ 在含金10mg/L溶液中搅拌吸附1h,活性炭对金的吸 附率应达60%。
⑶ 将活性炭置于瓶中在摇滚机上翻滚24h,磨损率应小于 2%。
8.1.2 活性炭吸附金的机理
⑴ 以金属形态被吸附
活性炭从金氯配合物(AuCl4-)溶液中吸附金后,可明显地看到 在炭的表面有黄色的金属金。以此推断金氰配合物也可被炭还 原。这种观点认为,炭上吸附的还原气体,如CO,可把金还原。
8.1.3 炭浆法提金工艺
炭浆法由预筛、氰化浸出、吸附、解吸、电解(电 积)和炭的再生等几个主要作业组成。
预筛的作用
除去矿浆中的杂物,避免以后与载金炭混在一起。一般 采用28目(0.6mm)的筛子,预筛的筛上物主要是木屑。
木屑易使分离矿浆和载金炭的筛子堵塞。此外在磨矿时, 金粒、石英等矿粒嵌入木屑中,使得其含金量常常很高; 氰化过程中,木屑往往会吸附金氰配合物,而且用一般的 洗涤方法,很难把木屑上吸附的金洗脱下来。同时在炭浆 法中,吸附槽存在少量木屑,会降低活性炭的吸附效率。
吸附金的活性炭是采用高温热活化方法制得的,将椰壳或果 核等在500~6000C下,用惰性气体(隔绝空气)保护进行脱水和 炭化,然后再在800~11000C下用CO、CO2、H2O或它们的混 合气体进行活化。在活化过程中,大约有20%的炭被气化:
C+CO2=2CO C+H2O=CO+H2
图9-1 活性炭孔隙结 构示意图
向矿浆中加入活性炭,同时进行浸出和金吸附的“炭 浸法”(Carbon in leaching,简写为CIL)。
1967年发展了“堆浸法”(Heap leaching),即将金矿石 筑成堆进行氰化物溶液的喷淋浸出。
新工艺,
与炭浆法相似的另一工艺是“树脂浆法”(Resin in pulp, 简写为RIP),它是由前苏联开发的,1967年在乌兹别克斯 坦的穆龙陶大型露天金矿建成投产。
8.1 炭浆法
炭浆法保留了氰化浸出的主体工序,取消了液固 分离和加锌置换两个后续工序,代之以炭吸附、解吸 和电解。
8.1.1 活性炭 用于生产活性炭的原料有果壳、果核、树木、 煤炭等,用于从氰化矿浆中吸附金的活性炭也是一种 专用炭,目前的最佳品种为椰壳炭,其次是杏核、 橄榄核、桃核等果核炭。 活性炭没有确定的结构式或化学组成,不同产 品通常只能由它们的吸附特性来区分。根据X射线衍 射,活性炭的典型结构与石墨的典型结构相似。
研究证明,炭对下列离子的吸附强度顺序为: Au(CN)2->Ag(CN)2->CN-
⑶ 以离子对被吸附 提出这一机理是基于以下事实:氰化物溶液中存在阴离子
(如Cl-, ClO4-),甚至其浓度高达1.5mol/L,也不降低金的吸附容 量。但是当溶液中有中性分子(如煤油)存在时,会使金的吸附量 下降
表9-1 典型提金椰壳活性炭的物理和化学特性
分类
技术特性
指标
物 颗粒密度/g/mL
理 特
堆密度/g/mL
性
孔穴大小/nm
孔穴体积/ mL/g
0.8~0.85 0.48~0.54 1.0~2.0 0.7~0.8
球盘硬度/%
97~99
粒度/mm(目)
1.16~2.35(14~ 8)
灰分/%
2~4
水分/%
第9章 现代氰化提金工艺
传统的氰化法存在的主要问题是: 液固分离需要配置庞大的逆流倾析、过滤系统以 及浸出液的澄清、脱气和金置换等一系列作业, 占地大,投资和生产费用高, 过程冗长, 金泥的品位低, 泥质金矿难以处理。
一些新的氰化方法: 活性炭从氰化浸出矿浆中吸附金的“炭浆法”(Carbon
in pulp,简写为CIP),它于1973年在美国投入生产,随后在 全世界得到广泛应用。