六西格玛管理经典案例
六西格玛管理项目案例
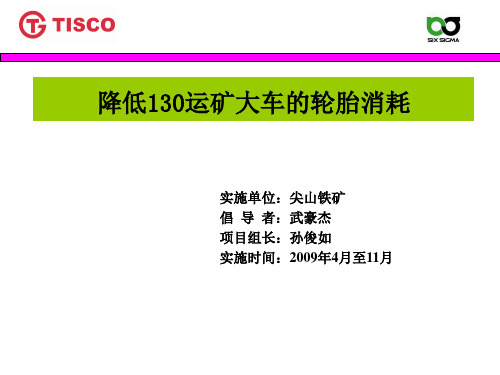
研究日期: 报表人: 产品名称: 其他:
2009年4月28日 杨泰泉 轮胎
检验员与标准
100
90
95.0% 置信区间 百分比
样品 1
2 3 4 5 6 7
测试者 王君山
王君山 王君山 王君山 王君山 王君山 王君山
判定 NG
OK OK OK OK OK NG
标准 NG
NG OK OK OK NG NG
分析:2006年开始,尖山铁矿购入130运矿大车,130运矿大车呈逐年上升的趋势,逐步 取代7548D和7555B。
10
D5 Y的缺陷定义
DMA I C
一、定义、公式 缺陷的定义:
1、磨损—运矿大车在载重行驶过程中胎面与地面摩擦引起的胎面磨平、裂纹、 剥落、掉块、分离、轻微溶胀等现象。
2、刺破——运矿大车在载重行驶过程中由于路面锋利浮石和岩角来回切割引起 的胎侧、胎肩异常划伤或轮胎爆炸现象。
降低130运矿大车的轮胎消耗
实施单位:尖山铁矿 倡 导 者:武豪杰 项目组长:孙俊如 实施时间:2009年4月至11月
项目团队
DMA I C
总倡导者:武豪杰 项目组长:孙俊如
项目发起人:杨忠林
工艺
点检
生产
设备
姓名 郑永泉 姜振望 杨泰泉 刘永政 候效伟 闫四虎
部门 设备能源科 调度室 采矿点检站 运输作业区 筑排作业区 采矿作业区
NG
60
60
2
宋建平
OK
NG
2
宋建平
OK
NG
3
宋建平
OK
OK
3
宋建平
OK
OK
50
50
4
宋建平
六西格玛经典案例

六西格玛经典案例在六西格玛质量管理方法中,通过分析和改进业务流程,以减少缺陷和提高效率,从而实现优秀质量和高度效益。
以下是三个经典的六西格玛案例。
1. Motorola的六西格玛实践Motorola是六西格玛的奠基者之一、20世纪80年代,Motorola采用六西格玛方法,以改进生产过程并提高质量。
在一个以缺陷率而不是零缺陷为标准的产业中,Motorola在一年内将缺陷率从超过三十万个降低到每百万个产品中只有5个。
六西格玛的成功引起了其他公司的注意,并成为其他公司实施质量管理的典范。
2. General Electric(GE)的六西格玛实施GE是六西格玛的早期采用者,它将六西格玛引入公司的各个部门和业务领域。
公司的首席执行官杰克·韦尔奇在1995年将六西格玛作为公司的战略重点。
GE在实施过程中的一个成功案例是其航空发动机业务部门,该部门通过六西格玛方法降低了生产过程中的缺陷率,并提高了航空发动机的性能和可靠性。
GE的成功证明了六西格玛可以在各种行业中实现卓越的结果。
3.美国政府的六西格玛应用六西格玛方法不仅在企业界取得成功,而且在政府部门中也有很好的应用。
美国政府决定在1995年引入六西格玛方法,以提高效率并减少浪费。
例如,美国联邦航空管理局(FAA)使用六西格玛方法改进了飞行管制和管理过程,减少了航班延误和事故。
美国海军也采用了六西格玛方法来改善军舰维护和修理过程,提高了战斗力和减少了成本。
以上是六西格玛的三个经典案例,它们都展示了通过六西格玛方法来实现质量改进和效益提高的潜力。
这些案例证明了六西格玛是一个非常有力的质量管理方法,可以在各个领域带来显著的结果。
无论是在制造业、服务业还是政府部门,六西格玛都能够提供一个可靠的框架来解决质量和效率方面的挑战。
控制案例
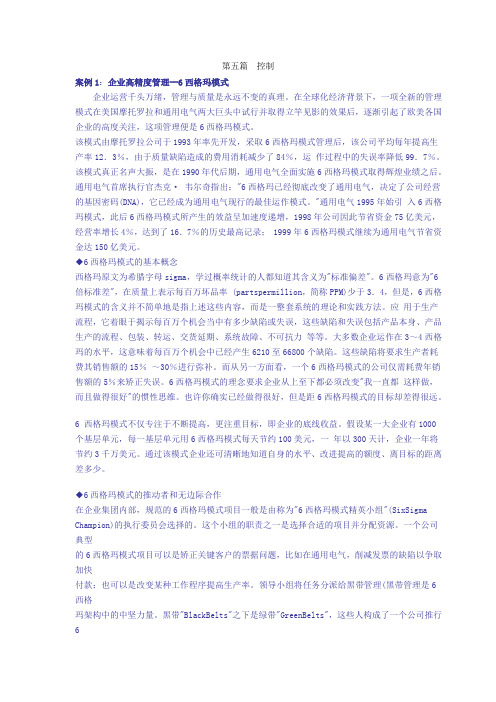
第五篇控制案例1:企业高精度管理--6西格玛模式企业运营千头万绪,管理与质量是永远不变的真理。
在全球化经济背景下,一项全新的管理模式在美国摩托罗拉和通用电气两大巨头中试行并取得立竿见影的效果后,逐渐引起了欧美各国企业的高度关注,这项管理便是6西格玛模式。
该模式由摩托罗拉公司于1993年率先开发,采取6西格玛模式管理后,该公司平均每年提高生产率12.3%,由于质量缺陷造成的费用消耗减少了84%,运作过程中的失误率降低99.7%。
该模式真正名声大振,是在1990年代后期,通用电气全面实施6西格玛模式取得辉煌业绩之后。
通用电气首席执行官杰克·韦尔奇指出:"6西格玛已经彻底改变了通用电气,决定了公司经营的基因密码(DNA),它已经成为通用电气现行的最佳运作模式。
"通用电气1995年始引入6西格玛模式,此后6西格玛模式所产生的效益呈加速度递增,1998年公司因此节省资金75亿美元,经营率增长4%,达到了16.7%的历史最高记录; 1999年6西格玛模式继续为通用电气节省资金达150亿美元。
◆6西格玛模式的基本概念西格玛原文为希腊字母sigma,学过概率统计的人都知道其含义为"标准偏差"。
6西格玛意为"6倍标准差",在质量上表示每百万坏品率 (partspermillion,简称PPM)少于3.4,但是,6西格玛模式的含义并不简单地是指上述这些内容,而是一整套系统的理论和实践方法。
应用于生产流程,它着眼于揭示每百万个机会当中有多少缺陷或失误,这些缺陷和失误包括产品本身、产品生产的流程、包装、转运、交货延期、系统故障、不可抗力等等。
大多数企业运作在3~4西格玛的水平,这意味着每百万个机会中已经产生6210至66800个缺陷。
这些缺陷将要求生产者耗费其销售额的15%~30%进行弥补。
而从另一方面看,一个6西格玛模式的公司仅需耗费年销售额的5%来矫正失误。
6西格玛平安案例

6西格玛平安案例案例1一个半导体簿膜设备制造商在"6-Sigma"实施前的状况是:由于设计研发周期太长,该公司老是不能及时将产品推入市场,而且由于故障率太高,致使售后效劳和维修本钱太高。
售后效劳和维修本钱包括:(1)顾客埋怨、投诉和保修本钱;(2)客户维修本钱;(3)延迟发货和停产损失。
该公司一台设备的平均单价是US$7500K。
该公司希望通过"6-Sigma"的改进运作,能使公司赶上其竞争对手,如Toshiba,Actel,Applied,Material等公司。
该公司的"6-Sigma"运作是从建立"6-Sigma"团队开始的。
核心团队由研发工程、应用工程及可靠性工程组成,其它部门(如市场、制造、财务、质量等)负责支持与协助。
公司的总裁直接领导一个"6-Sigma"负责人,该"6-Sigma"负责人是由公司的副总裁担任。
在"6-Sigma"负责人之下,是"6-Sigma"黑带委员会(包括MBB黑带师、研发总监、技术总监)、"6-Sigma"财务委员会、研发系统1#、研发系统2#、研发系统3#和两个黑带项目团队。
该公司"6-Sigma"的推进步骤如下:由管理高层确定"6-Sigma"的开展计划和管理结构,选定KPI,然后进行管理高层的培训和"6-Sigma"BB培训。
在培训过程中,BB黑带项目也要同时选定和实施,最后是项目的审核。
选定的KPI是:(1)研发周期缩短2个月;(2)生产过渡期合格率由65%提高到80%;(3)减少客户报怨和维修率80%;(4)预计财务回报:通过降低研发周期可创造亿美元(US$350KK);通过提高合格率可创造2亿美元(US$200KK);通过降低维修成本可节约4亿美元(US$400KK)。
六西格玛案例分析
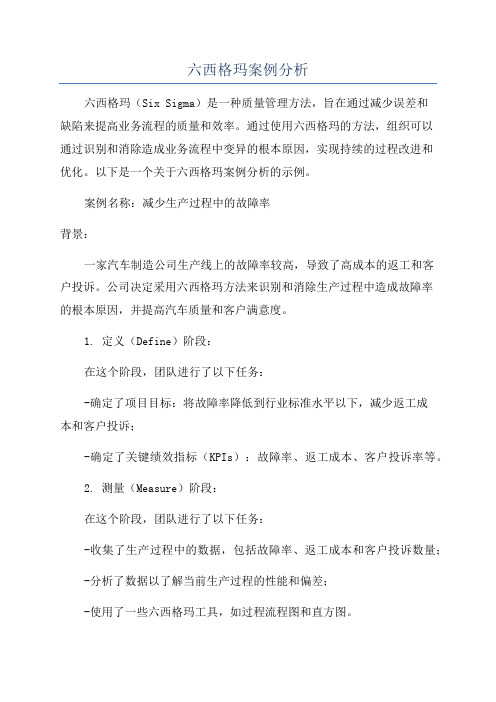
六西格玛案例分析六西格玛(Six Sigma)是一种质量管理方法,旨在通过减少误差和缺陷来提高业务流程的质量和效率。
通过使用六西格玛的方法,组织可以通过识别和消除造成业务流程中变异的根本原因,实现持续的过程改进和优化。
以下是一个关于六西格玛案例分析的示例。
案例名称:减少生产过程中的故障率背景:一家汽车制造公司生产线上的故障率较高,导致了高成本的返工和客户投诉。
公司决定采用六西格玛方法来识别和消除生产过程中造成故障率的根本原因,并提高汽车质量和客户满意度。
1. 定义(Define)阶段:在这个阶段,团队进行了以下任务:-确定了项目目标:将故障率降低到行业标准水平以下,减少返工成本和客户投诉;-确定了关键绩效指标(KPIs):故障率、返工成本、客户投诉率等。
2. 测量(Measure)阶段:在这个阶段,团队进行了以下任务:-收集了生产过程中的数据,包括故障率、返工成本和客户投诉数量;-分析了数据以了解当前生产过程的性能和偏差;-使用了一些六西格玛工具,如过程流程图和直方图。
3. 分析(Analyze)阶段:在这个阶段,团队进行了以下任务:-确定了导致故障率升高的根本原因;-使用了五力分析和鱼骨图等工具,以识别可能的原因;-根据数据和分析结果,确定了一个或多个关键影响故障率的因素。
4. 改进(Improve)阶段:在这个阶段,团队进行了以下任务:-开发了改进计划,包括减少故障率的具体措施和时间表;-实施了改进措施,并记录了结果。
5. 控制(Control)阶段:在这个阶段,团队进行了以下任务:-实施了独立检查和监控措施,以确保改善措施的可持续性;-追踪关键绩效指标,如故障率、返工成本和客户投诉;-确立了持续改进的机制,以确保过程持续优化。
通过使用六西格玛方法,该汽车制造公司成功降低了生产过程中的故障率。
在实施改进措施后,故障率从10%降低到行业标准的3%以下,成功降低了返工成本和客户投诉率。
此外,公司在生产线上建立了严格的质量控制措施和监控机制,以确保持续改进和优化。
精益六西格玛案例

精益六西格玛案例
精益六西格玛是一种管理方法,它结合了精益生产和六西格玛的优点,旨在提
高效率和质量。
下面我们来看一个实际的案例,了解精益六西格玛是如何在实践中发挥作用的。
某汽车零部件制造公司在生产过程中遇到了一些问题,导致了生产效率低下和
产品质量不稳定。
经过分析,他们决定引入精益六西格玛方法来改善生产流程。
首先,他们进行价值流分析,找出了生产过程中的浪费和瓶颈。
然后,他们采
用精益工具,如5S和Kanban,对生产车间进行了重新布局和标准化。
同时,他们
还对员工进行了培训,让他们更好地理解和运用精益工具。
在改善生产流程的同时,公司还引入了六西格玛的方法,通过数据分析和流程
控制,找出了造成产品质量不稳定的根本原因,并采取了相应的改进措施。
经过一段时间的努力,公司取得了显著的成效。
生产效率得到了提高,产品质
量稳定性也得到了保障。
公司的客户满意度得到了提升,市场竞争力也得到了增强。
通过这个案例,我们可以看到精益六西格玛在实际中的应用效果。
它不仅可以
帮助企业提高效率和质量,还可以带来客户满意度和市场竞争力的提升。
综上所述,精益六西格玛是一种非常有效的管理方法,它可以帮助企业解决生
产过程中的问题,提高效率和质量,实现持续改进和持续增长。
希望更多的企业能够引入精益六西格玛,实现可持续发展。
管理学经典案例管理理念
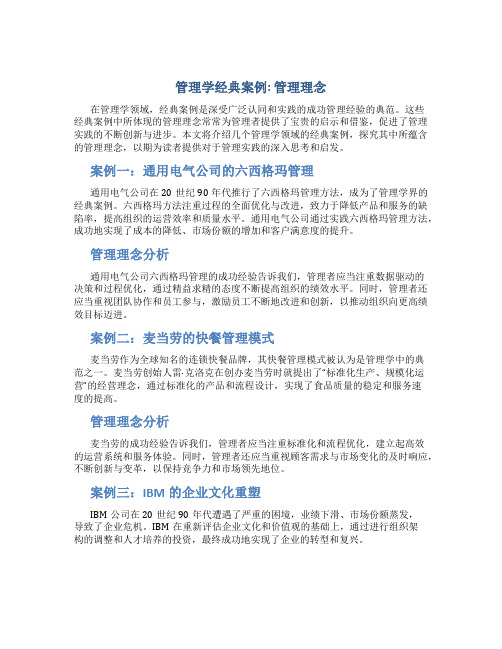
管理学经典案例: 管理理念在管理学领域,经典案例是深受广泛认同和实践的成功管理经验的典范。
这些经典案例中所体现的管理理念常常为管理者提供了宝贵的启示和借鉴,促进了管理实践的不断创新与进步。
本文将介绍几个管理学领域的经典案例,探究其中所蕴含的管理理念,以期为读者提供对于管理实践的深入思考和启发。
案例一:通用电气公司的六西格玛管理通用电气公司在20世纪90年代推行了六西格玛管理方法,成为了管理学界的经典案例。
六西格玛方法注重过程的全面优化与改进,致力于降低产品和服务的缺陷率,提高组织的运营效率和质量水平。
通用电气公司通过实践六西格玛管理方法,成功地实现了成本的降低、市场份额的增加和客户满意度的提升。
管理理念分析通用电气公司六西格玛管理的成功经验告诉我们,管理者应当注重数据驱动的决策和过程优化,通过精益求精的态度不断提高组织的绩效水平。
同时,管理者还应当重视团队协作和员工参与,激励员工不断地改进和创新,以推动组织向更高绩效目标迈进。
案例二:麦当劳的快餐管理模式麦当劳作为全球知名的连锁快餐品牌,其快餐管理模式被认为是管理学中的典范之一。
麦当劳创始人雷·克洛克在创办麦当劳时就提出了“标准化生产、规模化运营”的经营理念,通过标准化的产品和流程设计,实现了食品质量的稳定和服务速度的提高。
管理理念分析麦当劳的成功经验告诉我们,管理者应当注重标准化和流程优化,建立起高效的运营系统和服务体验。
同时,管理者还应当重视顾客需求与市场变化的及时响应,不断创新与变革,以保持竞争力和市场领先地位。
案例三:IBM的企业文化重塑IBM公司在20世纪90年代遭遇了严重的困境,业绩下滑、市场份额蒸发,导致了企业危机。
IBM在重新评估企业文化和价值观的基础上,通过进行组织架构的调整和人才培养的投资,最终成功地实现了企业的转型和复兴。
管理理念分析IBM的成功经验告诉我们,管理者应当注重企业文化的塑造和组织价值观的建立,激发员工的团队合作和创新创造力。
六西格玛改进案例

六西格玛改进案例以六西格玛改进案例为题,列举如下10个案例:1. 生产流程改进案例:在一个制造业公司,生产流程中存在着许多瑕疵品。
为了提高产品质量,该公司采用了六西格玛方法进行改进。
通过分析生产过程中的关键环节,确定了引起瑕疵品的主要原因,并通过改进工艺和设备,减少了瑕疵品的产生率。
2. 供应链管理改进案例:一家零售公司的供应链管理存在着库存过剩和缺货的问题,导致了销售额下降。
为了解决这个问题,该公司运用了六西格玛方法,对供应链中的各个环节进行了优化。
通过提高库存预测的准确性,优化订货策略,以及改进供应商管理,该公司成功解决了库存过剩和缺货问题。
3. 客户投诉处理改进案例:一家电信运营商的客户投诉率较高,影响了公司的声誉。
为了改善客户满意度,该公司运用了六西格玛方法,对客户投诉处理流程进行了改进。
通过提高投诉处理的效率和质量,该公司成功降低了客户投诉率,并提升了客户满意度。
4. 销售流程改进案例:一家保险公司的销售流程存在着繁琐和低效的问题,导致了销售人员的工作效率低下。
为了提高销售业绩,该公司采用了六西格玛方法,对销售流程进行了改进。
通过简化流程、优化销售工具和培训销售人员,该公司成功提升了销售人员的工作效率和销售业绩。
5. 质量管理改进案例:一家制药公司的质量管理体系存在着缺陷,导致了产品质量不稳定。
为了提高产品质量,该公司采用了六西格玛方法,对质量管理体系进行了改进。
通过加强质量控制、改进检验方法和加强员工培训,该公司成功提升了产品质量的稳定性。
6. 项目管理改进案例:一个IT项目存在着进度延误和成本超支的问题,导致了项目无法按时交付。
为了解决这个问题,该公司采用了六西格玛方法,对项目管理进行了改进。
通过优化项目计划、加强资源管理和改进沟通机制,该公司成功提高了项目的进度控制和成本控制能力。
7. 售后服务改进案例:一家家电企业的售后服务存在着响应速度慢和问题解决率低的问题,导致了客户的不满意。