金的浸出工艺综述
黄金提取工艺综述
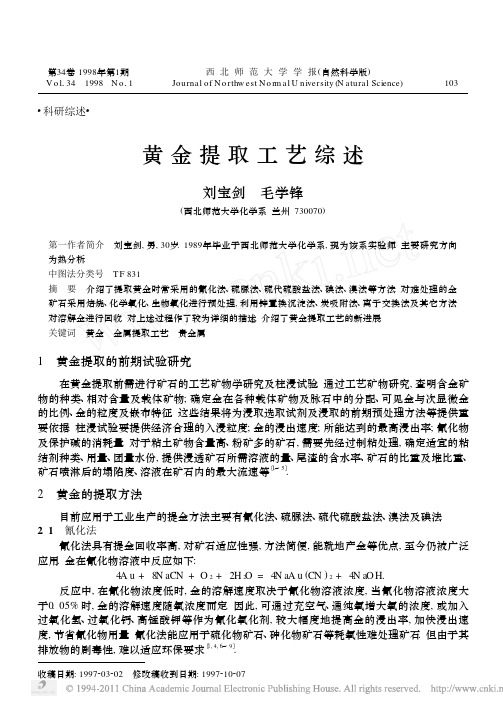
第34卷1998年第1期V o l 134 1998 N o 11 西北师范大学学报(自然科学版)Journal of N o rthw est N o r m al U niversity (N atural Science ) 103 收稿日期:1997203202 修改稿收到日期:1997210207科研综述黄金提取工艺综述刘宝剑 毛学锋(西北师范大学化学系兰州730070)第一作者简介 刘宝剑,男,30岁.1989年毕业于西北师范大学化学系,现为该系实验师.主要研究方向为热分析.中图法分类号 T F 831摘 要 介绍了提取黄金时常采用的氰化法、硫脲法、硫代硫酸盐法、碘法、溴法等方法.对难处理的金矿石采用焙烧、化学氧化、生物氧化进行预处理,利用锌置换沉淀法、炭吸附法、离子交换法及其它方法对溶解金进行回收.对上述过程作了较为详细的描述.介绍了黄金提取工艺的新进展.关键词 黄金 金属提取工艺 贵金属1 黄金提取的前期试验研究在黄金提取前需进行矿石的工艺矿物学研究及柱浸试验.通过工艺矿物研究,查明含金矿物的种类、相对含量及载体矿物;确定金在各种载体矿物及脉石中的分配、可见金与次显微金的比例、金的粒度及嵌布特征.这些结果将为浸取选取试剂及浸取的前期预处理方法等提供重要依据.柱浸试验要提供经济合理的入浸粒度;金的浸出速度;所能达到的最高浸出率;氰化物及保护碱的消耗量.对于粘土矿物含量高、粉矿多的矿石,需要先经过制粘处理,确定适宜的粘结剂种类、用量、团量水份,提供浸透矿石所需溶液的量、尾渣的含水率、矿石的比重及堆比重、矿石喷淋后的塌陷度、溶液在矿石内的最大流速等〔1~5〕.2 黄金的提取方法目前应用于工业生产的提金方法主要有氰化法、硫脲法、硫代硫酸盐法、溴法及碘法.2.1 氰化法氰化法具有提金回收率高,对矿石适应性强,方法简便,能就地产金等优点,至今仍被广泛应用.金在氰化物溶液中反应如下:4A u +8N aCN +O 2+2H 2O =4N aA u (CN )2+4N aO H. 反应中,在氰化物浓度低时,金的溶解速度取决于氰化物溶液浓度,当氰化物溶液浓度大于0.05%时,金的溶解速度随氧浓度而定.因此,可通过充空气、通纯氧增大氧的浓度,或加入过氧化氢、过氧化钙、高锰酸钾等作为氰化氧化剂,较大幅度地提高金的浸出率,加快浸出速度,节省氰化物用量.氰化法能应用于硫化物矿石、砷化物矿石等耗氧性难处理矿石.但由于其排放物的剧毒性,难以适应环保要求〔1,4,6~9〕.2.2 硫脲法金也能溶解在酸性硫脲溶液中,形成阳离子络合物.反应式为:A u +2CS (N H 2)2A u 〔CS (N H 2)2〕+2+e. 硫脲浸金的介质为盐酸、硫酸及硝酸,并加入氧化剂如二硫甲醚、双氧水、过氧化钠或溶于水的氧气、Fe 3+、O 3和M nO 2等.实验表明,在硫脲的酸性溶液中,在氧化剂的作用下,金的浸出率远远高于普通氰化钠溶液的浸出率.对于用硫脲法难以浸取的金矿,大多倾向于进行预处理.对于毒砂矿先用硫酸浸出砷后,再用酸性硫脲浸取金,浸出率大于95%〔1,7,10,11〕.2.3 硫代硫酸盐法硫代硫酸盐、多硫化钠可用作浸金溶剂直接浸金.该法具有浸出速度快,试剂无毒等特点.反应式为:6A u +2S 2-+S 2-4=6A uS -;8A u +3S 2-+S 2-5=8A uS -;6A u +2H S -+2OH -+S 2-4=6A uS -+2H 2O ;8A u +3H S -+3OH -+S 2-5=8A uS -+3H 2O. 硫代硫酸盐法具有试剂廉价、浸取速度快、浸出率高、安全无毒等特点〔1,12〕.是一种极具推广前景的方法.2.4 碘法碘液具有提取黄金的潜力.碘无毒,与金形成稳定络合物,可以在低浓度下从矿石浸金.它能穿透岩石,尤其是覆盖层.碘很难被脉石吸附,试剂消耗量低,可降低生产成本.其反应如下:2A u +I -+I -32A u I -2. 用碘与碘盐反应生成三碘络合物来氧化矿石中的金,而碘盐由含有食盐的饱和碘溶液与贱金属硫化物反应生成.浸出的金用活性炭回收,碘盐用隔膜电解方法再生.碘法的实际应用尚待开发〔1〕.2.5 溴法溴是一种较强的浸金试剂,其反应式如下:4A u +3B r (DM H )+10N aB r +6H 2O =4N aA uB r 4+6N aO H +3H 2(C M H ).式中,DM H 表示脱溴二甲基乙丙酰脲.溴法浸取速度快、无毒、对pH 值变化的适应性强.溴法和氰化法二者的试剂费用差不多,但溴法具有溶解速度快和回收费用低的优点,预计其经济指标比氰化法优越,缺点是试剂消耗偏高.溴法的研究较为活跃,其工业应用还有待于进一步研究〔1〕.综上所述,氰化法具有经济实用、工艺简便的优点,在黄金提取工业中是一种成熟的方法,但对环境易造成污染.而且有些矿石本身就难以用常规氰化法处理.这就使得许多能与金形成络合物的试剂如硫脲、硫代硫酸盐、卤盐、丙二腈和多硫化合物的研究显得异常活跃,但其真正用于实际生产还需更进一步的研究.3 难处理金矿石的预处理黄铁矿型难处理矿石的传统处理方法是对浮选精矿进行氧化焙烧.氧化焙烧法对于各种401 Journal of N o rthw est N o r m al U niversity (N atural Science ) V o l 134加热参数和给料组成非常敏感,一旦偏离最佳操作条件,就会导致金的释放率降低.氧化焙烧在目前不失为一种最佳工业方法.除氧化焙烧外还有还原焙烧、硫化焙烧等方法.现在已经研究出了另外一些氧化方法,如化学氧化法、加压氧化法、微生物氧化法以及专门处理锑矿物的高压低碱氧化法等〔1,2,4,8〕.3.1 氧化焙烧氧化焙烧通常在沸腾炉中进行,温度介于450~750℃,并保持过氧气氛.如果矿石中同时含有碳和金属硫化物,需严格控制焙烧温度,以避免矿石中的铜、镍、铅和锑等金属矿物生成铁酸盐或者出现“吸附损耗”而降低金的回收率.从经济方面考虑,焙烧反应必须是自热的,因而要求矿石中硫和碳的含量相当高,否则就要经过选矿富集.焙烧会产生含硫、锑、钾和汞的烟气,需使用除尘设备,以达到环保要求〔8,13〕.3.2 化学氧化化学氧化法分为常压和加压法.其工艺流程包括双氧化法,即首先加入碳酸钠,同时鼓入空气,然后再氯化;或先在常压下通入空气或氧气,用硫酸或氨水浸出回收铜或锑,然后再用氰化法回收金.新近研究出的N ifrox 工艺可以使金的回收率从30%提高到90%.该工艺是先将矿石在常压并鼓入空气的条件下用硝酸浸制1~2h ,使黄铁矿和毒砂得到氧化,然后再用氰化法提金〔14〕.加压氧化的优点是对有害元素如铅、锑不敏感,金的回收率较高〔2〕.难浸含硫金矿溶液加压氧化的研究已进行30余年.硫化矿物通常在酸性或碱性介质中加压氧化后再进行氰化处理,能大幅度提高金的回收率.处理黄铁矿2砷铁矿精矿回收金的方法是,先在600℃下无氧焙烧,使黄铁矿、毒砂受热分解成气态元素硫、砷和硫化钾,产生出磁黄铁矿焙砂,然后在100℃和500kPa 条件下,浸5h ,使磁黄铁矿中的硫氧化成单质硫,将单质硫与浸渣分离之后再氰化处理回收金.高压低碱氰化被认为是处理非常难浸的含锑金矿,尤其是辉锑金矿最经济最有效的方法.金的回收率通常能达到82%~87%〔2,14〕.与此相比较,采用常规氰化处理时,金的回收率较低.加压氧化法处理高硫高碳的含金硫化矿还存在一些问题,高硫矿物加压氧化时产生了大量的硫酸,这就需要增加容器的体积,增加中和费用.当矿石中含有大量有机物,加压氧化温度低于200℃时,就会出现“吸附损耗”现象〔2〕.用液氨或次氯酸盐氧化含碳难浸金矿是较为有效的预处理方法,与直接氰化法6%~32%的回收率相比,金的回收率平均大于95%.氯化法的出现〔14〕,使金的回收率平均提高6%,而每盎司金的氯气消耗减少25%,从而降低了生产成本.氯化时缓慢通入氯气的同时加入氢氧化钠或石灰可以提高金的氰化浸出率,并能将氯的逸出减至最低限度.另一种新工艺是电化学氧化法,直接在矿浆中产生次氯酸根,这种工艺实际上就是矿浆中加入N aC l ,插入通电电极〔1,2,6,15〕.3.3 生物氧化生物氧化是用细菌氧化硫化矿和砷化矿,释放出被它们包裹的贵金属.硫化矿的生物氧化,特别是T 氧化铁杆菌、T 硫化杆菌的作用,可按两种机理进行:①细菌直接侵蚀原子结构;②在细菌作用下,Fe ( )再生成Fe ( )间接侵蚀原子结构.黄铁矿的细菌氧化反应如下: 直接细菌氧化2FeS 2+H 2O +5O 2Fe 2(SO 4)3+H 2SO 4.5011998 N o 11 T he developm ent of go ld abstract 间接细菌氧化FeS 2+Fe 2(SO 4)33FeSO 4+2S;2FeSO 4+12O 2+H 2SO 4Fe 2(SO 4)3+32H 2O ;2S +3O 2+2H 2O 2H 2SO 4. 细菌通过铁和硫的氧化获取生成的能量.它们自身适应于在含金属的强酸(pH 1~3)溶液中生活,且在30~40℃最活跃.某些铵盐形式的氨是这些细菌的食物.为了确保最佳的浸出性能,需要能适应于通常硫化物给料的细菌.生物浸出可用于矿石或精矿,也可以进行堆浸或搅拌浸出〔14〕.这种方法的动力学过程较慢,堆浸仅适合于不能获得合格精矿的矿石;在生物堆浸后,再进行氰化堆浸可以回收金.该方法的优点是,优先溶解砷黄铁矿和破坏颗粒边界区.因为某些矿石中的细粒金大都贮存在这些部位,优先浸出如果被削弱,需要向流出液中添加铁盐,以沉淀出稳定的砷酸铁化合物.从长远观点来看,对各种有害影响,如细菌在机械设备上的积累、细菌对金属的吸附、对C IP 工艺性能的损坏等仍需进行研究和评价.难浸金矿的预处理方法已有许多新进展,加压氧化法确立了工业应用的地位.采用微生物浸出法可以节省投资,但与焙烧以外的其它方法相比较,其在成本方面并不具备优势.对于粘土含量高的金矿石,直接堆浸时溶液的渗透性差,而将破碎后的矿石进行制粒预处理之后再堆浸,效果较好.4 溶解金的回收溶解金的回收一般采用锌置换法和炭吸附法,树脂吸附技术也开始用于工业生产.一些其它方法如溶剂萃取也在积极研究开发中〔3,15,16〕.4.1 锌置换沉淀法锌置换沉淀法〔1〕也称为M errill 2C row e 法,金的回收率一般可达97.5%以上,且反应速度快,金滞留量小.该法的主要缺点是只能用在澄清液中,因而需要对矿浆进行高成本低效率的固液分离,并需在置换前对澄清液减压脱氧.但是在处理A g A u 大于10 1的矿石时,回收大量银需传输洗提和再生的炭量很大;处理金银含量均很高的矿石时,若相当金浓度大于10~15g L ,而又无影响锌置换的杂质时,回收一定量的金属,需处理的矿浆和溶液体积较小,减少了固液分离和减压脱氧的负荷;当提金厂规模小,每天回收的金量小于800g 时,由于炭的洗提与再生成本比较高,炭吸附厂的总成本不甚合理.4.2 炭吸附法包括炭吸附法(C IP )与炭浸出法(C I L )〔13〕.C IP 是在浸出完成后将活性炭加入专门的吸附槽中,从矿浆中吸附金,吸附时间大约为浸出时间的1 5;C I L 则是把炭加在浸出槽中吸附金.实践中往往采用二者某种形式的结合,即在浸出过程的某一点加入活性炭.与低品位矿石堆浸提金技术发展相适应的另一种炭吸附技术——炭柱法(C I C )迅速成为从堆浸溶液中回收金的主要手段.C I C 法是将活性炭填充在吸附柱中,使浸出液通过柱中的炭层吸附回收其中的金.实践表明,采用4~5级C I C 吸附,可回收金浓度为1×10-6左右的浸出液中96%~99%的金.1t 溶液的炭耗量在1~30g 之间.601 Journal of N o rthw est N o r m al U niversity (N atural Science ) V o l 134 与活性炭在提金工业应用的巨大成就形成鲜明对照的是,人们对金氰化物在活性炭上吸附与洗脱的机理所知甚少.近年来在这方面做了不少开发工作,发现其机理为:①A u (CN )-2还原成单质金;②M +A u (CN )-2离子对的形式吸附;③A u (CN )-2与阳离子的双电层吸附在电荷表面,A u (CN )-2部分还原为簇形化合物;④A u (CN )-2吸附后降解成不溶的A uCN .C IP 虽然明显优于锌置换法,但它也有明显的不足.首先,载金炭的洗提作业复杂,费用高,易被腐殖质及其它有机物中毒,易碎裂磨损,造成炭及其吸附金损失;其次,炭的活化投资费用可观〔4,16,17,18,19〕.4.3 离子交换法(R IP )阳离子交换树脂一般制成强碱性、弱碱性或二者的混合树脂.强碱性树脂吸附能力强,但无选择性且难洗脱;弱碱性树脂的优点是只需控制pH 值即可洗脱,但它需先质子化才能吸附金,因而不能在氰化体系的自然pH 值下使用.在较低的pH 值下,吸附的选择性被严重破坏,且许多弱碱性树脂并不能靠调节pH 值完全洗脱金.有几种胍类树脂,其碱性介于强碱性与弱碱性之间,可在pH 高达12.0左右萃取金氰化物.在常压、100℃下用氢氧化钠溶液洗脱,载金能力选择性高于一般活性炭及树脂.离子交换纤维材料作为树脂技术的发展,为吸附金的官能团提供了更大的附着面积,吸附时间一般小于10m in ,比通常树脂颗粒快得多.这项技术刚刚起步,但结果令人鼓舞.树脂技术与炭吸附相比具有以下优点:①R IP 厂吸附槽可在高树脂浓度(可占矿浆体积20%~30%)下有效作业,而C IP 的吸附槽中炭不超过矿浆体积3%~6%,因此,R IP 厂吸附槽体积只需C IP 厂的1 5长;②树脂形状规则,表面光滑易过筛、泵送、磨损少,减少了树脂及其吸附金的损失;③树脂可在常压、60℃以下洗脱,且树脂不受有机物中毒,不受某些粘土矿物影响,无须热酸洗及定期热活化;④树脂可吸附其它金属的氰化物,从而产生对环境无害的尾矿,同时循环过量氰化物〔7〕.4.4 其它回收方法溶剂萃取相比固体离子交换剂提金有速度快、选择性好、抗中毒等优点.生物吸附剂的开发也取得了进展〔20〕.斜生珊藻是金的一种优良吸附剂,吸附速度快,吸附量大,选择性高,在30m in 吸附可达平衡.从溶液中回收金的炭吸附方法成本和投资较低.其它方法若要用于工业生产仍需做大量的研究〔20〕.5 金的解吸从载金炭中解吸金的方法有:①扎德拉法(Zadra )〔1〕:在含1%N aOH 和0.2%N aCN ,温度95~100℃的热溶液中进行解吸,解吸时间48~72h .若在500~600kPa 、135~140℃下操作,解吸时间为10~12h .②英美研究实验室(AA RL )解吸法〔1〕:先用0.5~1床体积,含5%N aCN ,1%N aOH 的热溶液预处理载金炭1h ,然后用热去离子水洗涤,该法通常在8~10h 完成解吸.③有机溶剂解吸法:在1%的N aCN ,1%N aOH 溶液中加40%~50%乙醇或乙腈,在60~80℃下,10~15h 完成解吸,有机溶剂的回收率在85%以上.该法所用解吸液体积小,贵液品位高达600~900m g L .载金炭所得的贵液一般用电积法回收金银〔1,6〕. 参考文献〔1〕 U dupa A R .黄金提金工艺进展.国外金属矿选矿,1992,(1):34~447011998 N o 11 T he developm ent of go ld abstract〔2〕 钱惠明.难选金矿的压力氧化处理.矿产保护与利用,1992,(1):36~41〔3〕 方兆珩,马 其,谢慧琴.细微炭质金矿的预处理和氰化浸取研究.黄金,1993,14(4):28~31〔4〕 王本仪,唐苏英,丁桐森,等.常德县金矿浮选金精矿氰化浸出——炭吸附提金工艺试验研究.铀矿开采,1991,(1):9~16〔5〕 张肇宏.金矿堆浸化学分析.黄金,1993,11(14):46~49〔6〕 孙鑫良,龚钰秋.过氧化物辅助浸出(PAL )的氰化提金工艺.黄金,1993,3(4):41~43〔7〕 甘尉棠,张毓凡,刘六战,等.用BPR 树脂从氰化液中提金.离子交换与吸附,1992,8(2):172~177〔8〕 肖松文,梁径冬,邱良邦.难浸金矿加熟石灰焙烧——氰化浸出新工艺研究.黄金,1993,14(10):31~35〔9〕 胡春融,李 海.老柞山难浸金矿石提金工艺生产实践.黄金,1994,15(6):41~43〔10〕 张清波.加温硫脲炭浸法提金新工艺研究.黄金,1993,14(12):23~26〔11〕 李进善.浸金体系中影响硫脲消耗因素的研究.化工冶金,1994,15(3):229~233〔12〕 杨天足,陈希鸿,宾万达,等.多硫化钠浸金研究.中南矿业学院学报,1992,23(6):687~692〔13〕 胡 斌.改革工艺流程提高金的回收率.黄金,1993,14(1):23~27〔14〕 Kenneth G T hom as .难处理金矿石的碱法和酸法高压浸出.湿法冶金,1992,(2):26~32〔15〕 邓 彤.氰化浸出体系中金的溶剂萃取.黄金,1994,15(6):36~40〔16〕 田钟荃,翁元声.活性炭强制放电再生技术在炭浆法提金工艺中的应用.黄金,1993,14(3):32~37〔17〕 张 箭,兰新哲,丁 峰,等.一种新的非氰提金方法.黄金,1993,14(10):40~43〔18〕 殷丰礼,张永凤.花牛山选金厂边磨边浸生产实践.吉林冶金,1991,(6):9~11〔19〕 袁廷芬,汤 琦.制粒堆浸提金在龙王山金矿的生产实践.黄金,1994,15(5):39~42〔20〕 唐 莉,李家熙.藻吸附金属离子的研究——斜生栅藻富集金.岩矿测试,1994,13(3):161~165T he developm en t of go ld ab stractL iu B ao jian M ao Xuefeng(D epartm ent of Chem istry ,N o rthw est N o r m al U niversity 730070L anzhou PRC )Abstract It is repo rted that cyanogenati on ,su lou reaing th i o su lfating ,b rom in ing and i odin 2ing m ethod in ex tracting go ld .H eating ,chem ical ox idati on and b i o logy ox idati on are u sed in go ld o re p revi ou s treatm en t .It is m o re com p rehen sively show n that disso lved go ld is recov 2ered by zinc rep lacem en t sedi m en t ,carbon ab so rp ti on ,iron in terchanging and o ther m ethods .T he new developm en t of go ld ex tracting is p rovided .Key words go ld techn ique of ex tracting m etal nob le m etal(责任编辑 陈广仁) 801 Journal of N o rthw est N o r m al U niversity (N atural Science ) V o l 134。
黄金冶炼技术综述
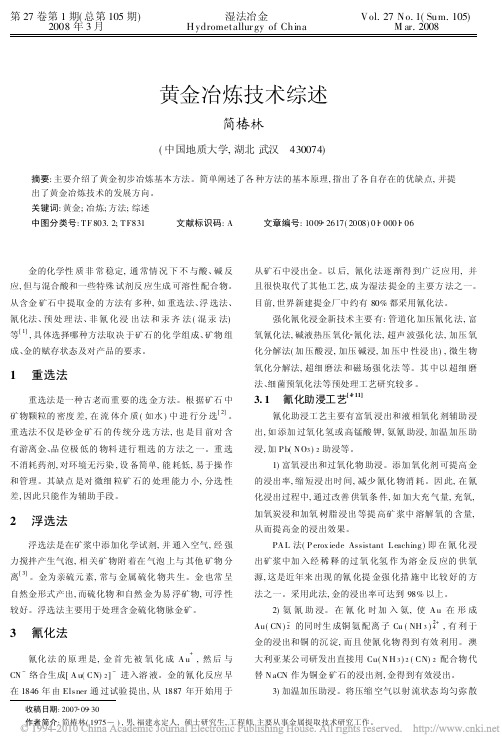
从矿石中浸出金。以 后 , 氰化 法逐 渐得 到广 泛应 用 , 并 且很快取代了其他工艺 , 成 为湿法 提金的 主要方 法之一。 目前 , 世界新建提金厂中约有 80% 都采用氰化法。 强化氰化浸金新技术主要 有 : 管道化 加压氰化 法 , 富 氧氰化法 , 碱液热压 氧化 氰化 法 , 超声 波强化 法 , 加压 氧 化分解法 ( 加 压酸 浸 , 加压 碱浸 , 加 压中 性浸 出 ) , 微生 物 氧化分解法 , 超细 磨法 和磁 场强 化法 等。其 中以 超细 磨 法、 细菌预氧化法等预处理工艺研究较多 。
到矿浆中 , 形 成强 力旋 搅 , 使固、 液、 气 三相 充分 接 触 , 使 浸出所需的氧气和氰化物迅速扩 散到矿 物表面 并发生 氰 化反应。加温加压可缩短浸出 时间 , 显著 提高金 浸出率。 1978 年 , 西德鲁奇化学冶金公 司研究 了加温 加压 管道 氰 化浸出工艺 , 浸出 15 min, 金浸出率即达 94% ~ 96% 。 4) 加 Pb( NO3 ) 2 助浸。浸 出过程 中加 入 Pb( NO3 ) 2 , 不但可使钝化的金粒表面恢复活性 , 还可沉淀可溶 性的硫 化物及其他金属离子 , 从而提高金的浸出率。 5) 机械 活化浸金。机械活化 就是在 磨矿的 同时加 入 浸金剂进行氰化浸出。球磨能使 金粒充 分暴露 且保持 新 鲜。在细磨过程 中 , 机械 作用 可导 致矿 物发 生物 理化 学 性质的 变化 , 不仅 能改 善浸出 状况 , 缩 短浸出 时间 , 也 能 提高浸出率。
3
-
氰化法
氰化 法 的 原 理 是 , 金 首 先 被 氧 化 成 A u , 然 后 与
+ -
大利亚某公司研发出直接用 Cu( N H 3 ) 2 ( CN) 2 配合物 代 替 N aCN 作为铜金 矿石的浸出剂 , 金得到有效浸出。 3) 加温加压助浸。将压缩 空气以射 流状态 均匀弥 散
黄金冶炼工艺流程

黄金冶炼工艺流程我国黄金资源储量丰富,分布较广,黄金冶炼方法很多。
其中包括常规的冶炼方法和新技术。
冶炼方法、工艺的改进,促进了我国黄金工业的发展。
目前我国黄金产量居世界第五位,成为产金大国之一。
黄金的冶炼过程一般为:预处理、浸取、回收、精炼。
1.黄金冶炼工艺方法分类1.1矿石的预处理方法分为:焙烧法、化学氧化法、微生物氧化法、其他预处理方法。
1.2浸取方法浸取分为物理方法、化学方法两大类。
其中,物理方法又分为混汞法、浮选法、重选法。
化学方法分为氰化法(又分:氰化助浸工艺、堆浸工艺)与非氰化法(又分:硫脲法、硫代硫酸盐法、多硫化物法、氯化法、石硫合剂法、硫氰酸盐法、溴化法、碘化法、其他无氰提金法)。
1.3溶解金的回收方法分为:锌置换沉淀法、炭吸附法、离子交换法、其它回收方法。
1.4精炼方法主要有全湿法,它包括电解法、王水法、液氯法、氯化法、还原法火法、湿法一火法联合法。
2.矿石的预处理随着金矿的大规模开采,易浸的金矿资源日渐枯竭,难处理金矿将成为今后黄金工业的主要资源。
在我国已探明的黄金储量中,有30%为难处理金矿。
因此,难处理金矿的预处理方法成为当前黄金工业提金的关键问题。
难处理金矿,通常又称为难浸金矿或顽固金矿,它是指即使经过细磨也不能用常规的氰化法有效地浸出大部分金的矿石。
因此,通常所说的难处理金矿是对氰化法而言的。
2.1焙烧法焙烧是将砷、锑硫化物分解,使金粒暴露出来,使含碳物质失去活性。
它是处理难浸金矿最经典的方法之一。
焙烧法的优点是工艺简单,操作简便,适用性强,缺点是环境污染严重。
含金砷黄铁矿一黄铁矿矿石中加石灰石焙烧,可控制砷和硫的污染;加碱焙烧可以有效固定S、As等有毒物质。
美国发明的在富氧气氛中氧化焙烧并添加铁化合物使砷等杂质进入非挥发性砷酸盐中,国内研发的用回转窑焙烧脱砷法,哈萨克斯坦研发的用真空脱砷法以及硫化挥发法,微波照射预处理法,俄罗斯研发的球团法等都能有效处理含砷难浸金矿石。
湿法冶炼中的浸出与萃取

搅拌强度对混合效率和传质速率有重 要影响,搅拌强度不足会影响传质效 果,导致分离效率降低。
料液的浓度
料液中目标物质的浓度直接影响萃取 效果,浓度过高或过低都会影响分离 效果。
搅拌强度
温度和压力的变化会影响萃取剂的溶 解度和目标物质的挥发性,进而影响 萃取效果。
04
浸出与萃取的比较与选择
浸出与萃取的优缺点比较 浸 01
原料性质
对于某些特定原料,如 高品位矿石或易浸出的 矿物,浸出可能更合适
。
产品要求
如果需要高纯度产品, 萃取可能更合适。
生产规模
大规模生产时,浸出可 能更具优势。
浸出与萃取的联合流程
1 2
3
先浸出后萃取
原料经过浸出处理后,浸出液中的目标组分再进行萃取分离 。
先萃取后浸出
原料经过萃取处理后,萃取液中的目标组分再进行浸出处理 。
锌的浸出与萃取
锌的浸出
在锌的湿法冶炼过程中,通常采用硫酸作为浸出剂,将锌矿石中的锌离子浸出到溶液中。硫酸与矿石 中的锌反应生成硫酸锌,同时伴有其他金属离子的浸出。
锌的萃取
浸出液中的锌离子通过萃取剂(如环己酮)的选择性吸附作用,从浸出液中被提取出来。萃取剂将锌 离子从浸出液转移到有机相中,实现锌与其他金属离子的分离。
根据萃取剂的种类,萃取过程可分为 有机溶剂萃取、离子交换萃取和协同 萃取。
VS
有机溶剂萃取是利用有机溶剂对目标 物质的溶解度进行萃取分离;离子交 换萃取是利用离子交换剂对溶液中的 离子进行交换分离;协同萃取是利用 两种或多种萃取剂的协同作用进行萃 取分离。
萃取过程的设备
萃取设备主要包括混合器、分离器和 洗涤器。
同时浸出与萃取
-贵金属金的选矿、提取及浸出工艺的研究-

贵金属金的选矿、提取及浸出工艺的研究摘要:主要介绍了国内贵金属黄金选矿工艺(包括破碎、磨矿、重选、浮选等)的最新进展、强化氰化浸出(包括氧化剂、氨氰和加温加压、新型设备强化浸出等)和堆浸工艺、非氰化提取金、难处理矿石的预处理技术。
一、黄金现代选矿技术(破碎、磨矿、重选、浮选等)的最新进展黄金选冶技术的研究和发展方向主要包括:对成熟的技术工艺进行深入研究与改进,研究开发新工艺、新技术、新设备和新药剂等。
国内外黄金选冶行业在理论研究、工艺技术、新设备、新药剂的使用等方面近十几年来取得了令人瞩目的进展。
破碎磨矿费用约占选冶厂总成本的40%一60%。
因此,如何提高破磨效率,降低能耗,减少成本,是促进破碎磨矿技术向前发展的关键。
“多碎少磨”是粉碎工程领域普遍公认的节能降耗的重要途径,国内外黄金矿山破碎设备都朝着大破碎比、超细碎等方向发展,大多数选矿厂均降低了入磨粒度,不同程度地提高了球磨机的处理能力和磨矿效率。
西澳大利亚研制出的Wescone破碎机破碎比更大,能取替典型的两段磨矿回路中的第一段磨矿。
德国Krupp—polysius和KHD Humboldt公司研制的高压辊磨机,不仅破碎比高,所需功率比旋转磨机低,能达到更好的解离效果。
近几年,振动磨矿机(有效冲击能达到磨机容积的50—60%)。
、Krupp Polysius双向旋转球磨机(工作效率可达99.5%)、中心驱动智能节能磨机、立式磨机、塔式磨机旧1等相继研制成功,获得了很好的效果。
重选是砂金矿石的传统选矿方法,也是目前含有游离金、品位极低的物料进行粗选的唯一方法。
例如,赖切特多层圆锥选矿机和螺旋选矿机,前者已在南非和澳大利亚的一些选厂成功应用,最具代表性的是加拿大Lee Mar工业公司研制开发的尼尔森选矿机(Knelson),与其它设备相比,对几微米的粒级来说,能够获得更高的金回收率,生产能力为40t/h,寓集比可达1 000。
津巴布韦一矿山使用该设备后,氰化尾渣中可溶金的含量从o.25 g/t降至0.12 g/t。
含金矿石的机械活化浸出工艺研究

第27卷第2期2005年6月甘肃冶金GANS U M ETALLURGYV o.l27N o.2Jun.,2005文章编号:1672-4461(2005)02-013-03含金矿石的机械活化浸出工艺研究王越1,李骞2(1.西北矿冶研究院冶金新材料研究所,甘肃白银730900;2.中南大学资源生物学院,湖南长沙410083)摘要:本文进行了机械活化法强化氰化浸金的研究。
对现场生产中需要采用两段共48h浸出的金精矿,采用磨浸仅3h即可达到53%以上的浸出率,若辅以过氧化氢和氨水联合助浸,则磨浸2h即可达近70%的浸出率。
在此基础上,提出了磨浸-搅拌联合浸出的工艺路线,磨浸1h后再搅拌12h即可达93%以上的浸出率,极大地加快了浸金速率,缩短了浸金时间。
为氰化浸金这一传统工艺提供了一条崭新的发展思路。
关键词:氰化;浸出;机械活化;金矿石中图分类号:TF803.21文献标识码:A作为当今最重要的提金方法,氰化法具有工艺成熟、流程简单、回收率高、对矿石适应性强以及成本低等优点。
然而,氰化法也有浸出周期过长的不足之处。
这主要是因为氰化浸金过程中充当浸出剂的CN–和O2由液相扩散到达金粒表面的速度比较慢,从而造成整个过程的反应速度缓慢。
近年来,机械活化在强化湿法冶金过程中的作用逐渐被人重视。
矿物经机械活化后,反应性增强,可大大强化浸出过程。
同时,过氧化氢、氨水作为助浸剂在国内外也有研究报道。
本研究基于对机械活化浸金工艺的认识,以某含铜浮选金精矿为对象进行了试验研究,旨在对氰化浸金过程中的强化措施进行一些探索,从而为提高浸金效率寻找一些新的突破口。
1原料性质与试验研究方法氰化浸金试料为某浮选金精矿,A u、A g品位比较高。
浮选金精矿多元素分析结果见表1。
此外,较高含量的磁黄铁矿、白铁矿和辉铜矿、斑铜矿分别属于快速氧化铁和氰化易溶铜,对氰化过程有严重危害。
表1含铜金精矿多元素分析结果(%)元素Au Ag Cu Fe S Zn Pb 含量57.8g/t1020g/t 1.0531.1038.201.370.47试验中所用试剂主要有氰化钠、生石灰、过氧化氢和氨水。
陕西某黄金冶炼厂焙烧氰化浸渣提金方法研究报告
陕西某黄金冶炼厂焙烧氰化浸渣提金方法研究报告本文研究了陕西某黄金冶炼厂焙烧氰化浸渣提金方法,分析了该方法的优缺点,并从工艺流程、操作技术、设备应用等方面对该方法进行了详细阐述。
一、工艺流程本研究采用的焙烧氰化浸渣提金方法主要由以下几个步骤组成:1. 氰化浸渣焙烧:将氰化浸渣送入焙炉中进行高温处理,使其得到充分焙烧,达到剥离金属的效果。
2. 氰化浸渣破碎:将焙烧后的氰化浸渣进行破碎,得到较小的颗粒状物料。
3. 搅拌:将破碎后的氰化浸渣与水一起搅拌,使其形成悬浮液。
4. 沉淀:将悬浮液静置一段时间,使其沉淀,得到含金泥浆。
5. 过滤:将含金泥浆进行过滤,去除杂质。
6. 洗涤:将过滤后的含金泥浆用水进行洗涤,使其去除残留杂质。
7. 烘干:将洗涤后的含金泥浆放入焙炉中进行烘干,得到金粉末。
二、操作技术1. 焙烧操作温度的选择:在本研究中,焙烧时采用了950℃的高温,能够使氰化浸渣得到充分焙烧,并且可以保证金属与其他杂质迅速分解。
2. 破碎操作:在氰化浸渣破碎时,应采用适当的粉碎机,能够将氰化浸渣破碎成较小的颗粒状物料。
3. 悬浮液搅拌操作:搅拌时间和强度应根据浸出效果进行调整。
4. 沉淀时间的选择:沉淀时间应根据泥浆中悬浮颗粒的大小、颗粒浓度等因素进行调整。
5. 过滤操作:过滤应选用细孔滤纸,过滤时应逐渐加压。
三、设备应用本研究采用了较新的设备,包括高温焙炉、永磁搅拌器、温度控制系统等。
这些设备的应用,不仅能够提高提金效率,而且能够保证产品质量。
四、优缺点分析本研究采用的焙烧氰化浸渣提金方法具有以下优点:1. 提金效率高:在保证产品质量的前提下,可以达到较高的提金效率。
2. 工艺流程简单:焙烧氰化浸渣提金方法的工艺流程相对简单,易于操作。
3. 环保性好:焙烧氰化浸渣提金方法的环保性好,能够减少对环境的影响。
但该方法也存在一些缺点,主要包括:1. 能源消耗大:焙烧氰化浸渣需要较高的温度,因此消耗的能源较大。
矿石浸出与金属冶炼技术
近年来,随着环保要求的提高和资源利用率的提升,生物浸出、联合浸出等新型浸 出技术得到了广泛的应用和发展。
未来,随着科技的进步和环保意识的提高,浸出技术将继续朝着高效、环保、低成 本的方向发展。
应用场景
在新能源领域,矿石浸出 与金属冶炼技术可用于核 能发电厂、太阳能电池制 造厂等。
05
矿石浸出与金属冶炼的挑战
与前景
技术挑战与解决方案
挑战
矿石品位下降,冶炼难度增加 ;环保要求提高,生产成本上
升。
解决方案
研发高效浸出和冶炼技术,提 高金属回收率;推广绿色生产 工艺,降低能耗和排放。
挑战
不同矿石类型和复杂组分对浸 出和冶炼技术提出更高要求。
矿石浸出与金属冶炼 技术
汇报人:可编辑 2024-01-05
• 矿石浸出技术概述 • 矿石浸出原理 • 金属冶炼技术 • 矿石浸出与金属冶炼的应用 • 矿石浸出与金属冶炼的挑战与前
景
目录
01
矿石浸出技术概述
浸出技术的定义
浸出技术是指通过化学或物理方法将 矿石中的有价金属或非金属元素从矿 石中溶解或分离出来,从而实现金属 的提取和富集的一种技术。
浓度差
浸出过程中,浓度差是推动力,提高有用组分 的浓度差可以提高浸出速率。
催化剂
某些催化剂可以降低活化能,加快化学反应速率。
浸出过程的优化方法
01
选择合适的酸、碱或氧化剂、还 原剂,以提高浸出效率。
02
控制温度、压力等工艺条件,以 获得最佳的浸出效果。
优化浸出流程,如采用多级浸出 、逆流浸出等方式,提高浸出效 率。
难处理金矿的浸出技术研究现状
难处理金矿的浸出技术研究现状难处理金矿的浸出技术研究现状近年来,随着世界经济的发展,我国的黄金储备已达1054吨。
目前我国黄金资源量有1.5~2万吨,保有黄金储量为4634吨,其中岩金2786吨,沙金593吨,伴生金1255吨,探明储量排名世界第7位。
但在这些已探明的金矿资源中,约有1000吨都属于难浸金矿,占到了总量的近1/4。
难浸金矿石是指矿石经细磨后仍有相当一部分金不能用常规氰化法有效浸出的金矿石。
这类金矿石中的金由于物理包裹或化合结合,故不能与氰化液接触,导致浸出率很低。
难浸金矿石分为三种类型:(1)非硫化物脉石包裹金,这类矿石中金粒太小,无法用磨矿解离,金粒很难接触氰化液;(2)金被包裹在黄铁矿和砷黄铁矿等硫化矿物中,细磨也不能使包裹金粒接触浸出液;(3)碳质金矿石,金浸出时,金氰络合和被矿石中的活性有机炭从溶液中“劫取”⑴。
1.难浸矿石的预处理大部分难浸矿石直接用氰化钠进行搅拌浸出时的浸出率都在10%~20%左右,浸出率低。
研究人员通过对原料进行预处理的方法使难浸金矿石的浸出率得到很大提高。
具体方法有氧化焙烧、热压氧化法、生物氧化法、硝酸催化氧化法等。
1.1焙烧焙烧可使硫化物分解、砷和锑以氧化态挥发、含碳物质失去活性、显微细粒状的金富集。
该工艺具有适应性较强、操作费用较低、综合回收效果好的优点。
缺点是容易造成过烧和欠烧,生成的SO2及As2O3会对环境造成污染。
生产中常用的焙烧方法有两段焙烧、固硫固砷焙烧和球团包衣焙烧。
两段焙烧工艺采用两个焙烧炉,第一段是低温焙烧,温度为450~500℃,主要用于除砷。
第二段是高温氧化,温度是600~650℃以除去硫;固硫固砷焙烧是加入固定剂使矿样中的砷形成硫酸盐和砷酸盐,该工艺既不放出有毒气体,又可使被包裹的金充分暴露。
采用的固定剂有氧化钙、氢氧化钙、碳酸钠、氢氧化钠、氧化镁、碳酸镁等;球团包衣焙烧是将砷硫精矿和粘结剂形成的球团表面覆盖一层由砷硫固定剂组成的包衣层,焙烧时产生的As2O3、SO2气体被固定剂形成的砷酸钙和硫酸钙包裹起来以防止向外扩散污染环境⑶。
金属冶炼过程中的浸出技术
还原浸
总结词
通过加入还原剂将矿石中的金属离子浸出到溶液中的过程。
详细描述
还原浸出通常使用还原剂如碳、氢气等,将矿石中的高价金 属离子还原为低价态或零价态,使其从矿石中溶解出来,然 后从浸出液中提取金属。
钴的浸
要点一
总结词
钴的浸出是利用酸或碱溶液将矿石中的钴转化为可溶性钴 离子,再通过提取和沉淀的方法获得纯钴的过程。
要点二
详细描述
钴的浸出通常采用硫酸作为浸出剂,在高温高压条件下, 将矿石中的钴转化为硫酸钴溶液,然后通过电解或还原等 方法获得纯钴。浸出过程中需要控制好温度、压力、浓度 等参数,以确保浸出效率和钴的回收率。
02
浸出技术是一种重要的金属冶炼 手段,广泛应用于铜、镍、钴、 金等金属的提取和纯化。
浸出技术的分类
根据浸出剂的不同, 浸出技术可分为酸浸 、碱浸、盐浸等。
根据浸出方式的不同 ,浸出技术可分为搅 拌浸出、渗滤浸出、 堆浸等。
根据浸出温度的不同 ,浸出技术可分为常 温浸出和高温浸出。
浸出技术的原理
锌的浸
总结词
锌的浸出是利用酸或碱溶液将矿石中的锌转化为可溶性锌离子,再通过提取和沉淀的方法获得纯锌的 过程。
详细描述
锌的浸出通常采用硫酸作为浸出剂,在高温高压条件下,将矿石中的锌转化为硫酸锌溶液,然后通过 电解或还原等方法获得纯锌。浸出过程中需要控制好温度、压力、浓度等参数,以确保浸出效率和锌 的回收率。
03
浸出技术在金属冶炼 中的应用
铜的浸
总结词
铜的浸出是利用酸或碱溶液将矿石中的铜转化为可溶性铜离子,再通过提取和沉淀的方法获得纯铜的过程。
- 1、下载文档前请自行甄别文档内容的完整性,平台不提供额外的编辑、内容补充、找答案等附加服务。
- 2、"仅部分预览"的文档,不可在线预览部分如存在完整性等问题,可反馈申请退款(可完整预览的文档不适用该条件!)。
- 3、如文档侵犯您的权益,请联系客服反馈,我们会尽快为您处理(人工客服工作时间:9:00-18:30)。
金的多种浸出工艺综述原矿品位低于10克/吨的矿石是常见的,而且某些尾矿再处理作业所处理的品位在1克/吨以下。
较大的颗粒状金,现在都用机械方法回收。
但是,较小的金颗粒常常分散在整块矿石中,因而只能用化学方法回收,也就是浸出。
1.1氰化物浸金法氰化法仍是目前国内外主要的提金方法。
氰化法之所以经久不衰,主要是因为它工艺简便、成本低廉。
一、溶金原理现已公认,氰化法浸金是金的电化学自溶解过程,即金腐蚀过程,为一共扼电化学反应,它遵循电化学动力学规律。
氰根一金溶解反应一般写成如下形式:根据电化学机理,阳极反应为金的溶解:阴极反应为:在碱性氰化体系中,金阳极溶解的可逆性较大,氧阴极还原可逆性小而极化较大。
若NaCN浓度低于0.05%时,金溶解受CN-扩散控制,当NaCN浓度大于0.05%时,金的溶解速度由氧阴极还原反应所决定。
我国氰化浸金时,NaCN浓度大多大于0.05%,控制步骤主要为氧阴极还原过程。
二、氰化法浸金实践氰化浸金的最大缺点之一就是浸出速度太慢,一般需要24一48h才能达到浸出终点。
随着氰化浸金工艺的发展,人们逐渐认识到,矿浆中溶解氧的含量是影响浸金速度的一个重要因素,并为提高溶解氧的浓度采取了一系列切实可行的措施。
早期的氰化浸金都是通过鼓入空气来提供金溶解所需的氧。
就改善供氧条件来说,使气体充分弥散或用纯氧代替压缩空气的方法,虽也能达到一定的效果,但还很难构成突破性的进展。
最近几年的研究和生产实践表明,真正的突破性进展是通过加入各类化学氧化剂(H2O2,Na2O2,BaO2,O3,KmnO4)而实现的,其中尤以H2O2:和Na2O2:等过氧试剂效果更为明显。
这是因为过氧试剂除能大大提高矿浆中的溶解氧含量以外,还具有活性氧利用率高等优点。
德国Degussa公司于1987年开发了过氧化氢助剂(PAL)法,同年9月在南非Fairview金矿试用成功。
实践表明,PAL法可大大加快浸出速度,缩短浸出时间,降低氰化物耗量。
Fairview金矿氰化物消耗量从17kg/t降到lokg/t,金浸出率提高12%;澳大利亚的PineGreek 金矿采用过氧化氢以后,氰化物耗量从17kg/t降到10kg/t,金浸出率提高7%,尾渣金品位从o.79g/t降到0.629/t。
目前全世界已有20多个工厂采用了H2O2:助浸工艺。
我国山西某金矿投产10多年来未采用专门的充气设备,故浸出率不高,总回收率在70%左右。
往浸出液中加入H2O2:后收到了明显效果,可以不用混汞,一次浸出率达90%以上,且工艺过程简单易行。
需要指出的是,过氧化氢助浸时,溶液中溶解氧的含量并不一定比充入纯氧时高,但仍能达到很好的助浸效果。
例如,有一家选金厂原先使用纯氧,在溶解氧的体积分数为30xl0-6的条件下,浸出过程达到了最佳化。
但后来在进行过氧化氢助浸试验时,矿浆中溶解氧的体积分数仅保持在12xl0-6,尽管含氧量较低,但浸出速率仍比使用传统充气工艺时提高了7%。
南非一家工厂原先采用空气搅拌浸出槽,其中氧的体积分数为8xl0-6~10xl0-6,在采用过氧化氢助浸工艺并改成机械搅拌后,在氧的体积分数为9xl0-6的条件下进行浸出,金的浸出率却提高了50%。
对于这种现象,文献中有几种不同的解释:①过氧化氢直接参与的溶金反应起主导作用;②过氧化氢新分解出来的活性氧具有很强的反应活性,加速了浸金过程;③浸金过程的自由基反应机理认为,过氧化氢被催化分解出来的具有极强反应活性的自由基,促使了浸金反应的发生。
最近的研究表明,在充入纯氧的基础上配合使用过氧化氢,可进一步强化氰化工艺。
在澳大利亚进行的工业试验表明,这两种试剂的作用方式是不同的。
每一种试验都比另一种更适合处理某些类型的矿石,所以在某些情况下,将两种试剂配合使用可能是更经济有效的办法。
为了提高浸出率,浸出设备也有了很大的改进,传统的充气式搅拌机己逐渐被高强度的机械搅拌机所取代,加压、升温等强化措施也在氰化浸金中不断得到应用。
南非多姆矿业公司采用密闭反应器在强搅拌并充氧的条件下浸出重选粗精矿,其反应温度、pH值和氰化物浓度都比常规氰化时高。
由于提高了浸出动力学速率,所以氰化17h,就使金的浸出率超过97%。
美国Kamyr公司发明的连续逆流塔浸出工艺(Kamyr法)已取得专利,在南非Buffelsfontein金矿成功地进行了大规模的浸金试验。
该工艺的全部浸出和液固分离步骤在一个塔内进行,因此工程投资和生产费用较低,并且实现了浸出条件的最佳化,因而大大提高了出率。
南非和加拿大的一些选金厂采用高压釜进行氰化浸金,强化了浸出过程。
德国Lurgy公司将管道化反应器引入氰化浸金作业,对管道加压氰化进行了实验室和半工业试验,在2.04MPa的氧压下,经30min氰化浸出,金浸出率达到了96%。
值得一提的是,高压釜和管式反应器的加压浸出一般都在高于常温但低于85℃的条件下进行。
三、氰化物浸金法存在的问题最常用的浸出剂氰化物大约是100年前应用于采矿工业中,由于其经济效益卓越、成本低、卫艺条件成熟和矿石适应性好,因此在黄金生产领域占据统治地位。
但氰化物浸金法一直存在着下列问题:(1)浸出剂剧毒:由于氰化物剧毒,已对环境和人类造成了严重污染和危害(2)对金的浸出速度慢,并且易受杂质干扰。
(3)处理难处理矿石(如硫化矿)效果很差,需要复杂的预处理工序。
因此,从氰化法问世起就有学者探索代替氰化法的工艺,主要集中在硫脉浸金法、硫代硫酸盐浸金法、卤化法等。
1.2硫脲浸金法硫脲的酸性溶液可以溶解金。
在环境污染日趋严重,难处理金矿的问题越来越突出的20世纪80年代,硫脉浸金法已被提到研究日程上来,苏联、美国、澳大利亚和加拿大等国都进行了工业实验以观察硫脲浸金法的药剂消耗、对矿石的适应能力和提金成本等因素。
硫脉脲浸金法是作为半个世纪以来研究的十分广泛的一种方法,其主要原因是:(l)硫脲溶解金的速率比氰化物要快得多;且有很高的浸出率,溶解中生成的硫脲一金属络合物在本质上属于阳离子,这就使它适合用溶剂萃取法和离子交换法来回收金;(2)硫脲的毒性比氰化物要小得多;其最终降解产物是元素硫和氨睛,后者可用作肥料;(3)硫脲溶解金需要在酸性介质中进行,这使它适用于浸出某些难浸矿物;(4)硫脉浸出是在酸性条件下进行的,因此,可从那些在碱性溶液中不稳定的物料中或能够直接与氰化物反应的物料中提取金银,这些物料中含有不稳定的砷矿物和锑矿物(例如辉锑矿和黝铜矿)。
一、浸金原理硫脉溶解金的基本反应式通常写成如下形式:但是,上述反应式仅仅是全部反应历程的一部分,而且,为了得到适当的反应速率,需要有氧化剂存在。
事实上,硫腺容易发生二聚发应,生成二硫化甲眯:该反应是可逆的,二硫化甲眯是一种很活泼的氧化剂。
确实,人们认为,硫脉溶解金的反应需要有二硫化甲胖的存在,联合方程式(1)和(2)就可以得到关于生成阳离子型金一硫脉络离子的以下化学方程式:反应的标准电极电势为0. 04伏,其自由能变化为△rGm。
一7712)/mol。
硫脲浸取黄金的电位远比氰化法高,因此需要一种较强的氧化剂。
已经研究了不同于二硫化甲眯的氧化剂的作用,其中有空气、氧、过氧化氢、过氧化钠、高锰酸钾和铁离子。
除铁离子外,其它几种化合物均无使用价值。
空气或氧只能成功地用来浸出那些可在酸浸时浸出铁离子的矿石,而那些氧化能力较强的氧化剂则会引起硫脉迅速地、不可逆转地破坏。
在大多数情况下,以Fe3+离子作为氧化剂可获得较高的浸取速度,且金银的回收率高,反应方程式如下:反应中,金与硫脉形成阳离子而溶解,金的浸出率随着硫脉浓度增大而上升。
但是硫脉浓度过高时,Fe3+易与硫脉反应生成不稳定的[FeSO4SCN2H4]+,从而消耗了大部分硫脲,使参加金溶解的硫脲量减少,反应方程式如下:在硫酸盐介质中,铁离子可以生成一种稳定的共配合络离子;此类粒种可能是反应的中间体,或它的生成只是单纯地减缓了硫脉的分解,这样就可避免金被硫脲的降解产物所钝化,从而可得到明显快得多的浸出速率。
金的溶解速率既依赖于络合剂一硫脲的浓度,也取决于铁离子的浓度。
而铁离子的浓度存在一最佳浓度,浓度过高,会引起金的提取率下降,且在反应中,氧化剂Fe3+不但氧化金,而且可与硫脲进行氧化还原反应。
由此可知,硫脉氧化成二硫甲眯的趋势也随着硫脉的浓度增大而增大,而提高溶液的酸度即降低溶液的pH值,可提高硫脉被氧化的平衡电位,减少硫脉的氧化分解,从而提高硫脉的游离浓度。
同时,在反应中,二硫化甲眯会降解:由于这两个反应不可逆转,使硫脲浸出遇到两大困难:(1)由于浸出过程必须在氧化条件下进行,因此,在金的浸出过程中硫脲的消耗量比较高。
(2)生成的元素硫分散的很细,因而很容易包覆在矿物的表面,使金钝化并延缓或乃至完全阻止金的进一步浸出。
二、硫脲浸金实践为了减少硫脉的氧化损失,尽可能的降低试剂消耗,减少成本,许多研究者提出了有效的改进工艺,有专利指出,在溶液中加入Fe3+络合剂,这些络合剂包括二梭酸或三梭酸、磷酸和磷酸盐、硫氰酸盐、氟化物、硅氟酸、硅氟酸盐、EDTA和EDTA盐及其混合物,特别对草酸申请了专利。
浸出温度为10一90o C,溶液pH=0.5一4.5、含铁0.0025~0.lmol/L、硫脲0.006一o.4mol/L和Fe,+络合剂0.01一1mol/L、浸出电位350一700mV,这些络合剂可降低硫脉被三价铁离子的氧化降解作用,但不影响金的溶解速度。
KEPLE公司提出加入碱金属的硫酸氢盐和硫酸氢钱作酸催化剂来降低硫脲消耗,硫脲消耗量可降低30%。
Mensah 一Bi。
cyk提出用丙氨酸作为还原剂,来降低硫脲消耗,硫脲消耗量可降低20%。
中国科学院化工冶金研究所提出用金属铁防止硫脉氧化,并置换回收金。
研究表明:在0056mol/dm3硫脲,0.05一o.05mol/dm3Fe3+的溶液中插入金属铁丝可以使溶液的电位稳定在0.2一0.22伏之间。
而无铁丝时随Fe3+浓度不同,电位从0.18伏增加到0.29伏。
研究分析表明,加入铁丝可减少硫脲氧化。
兰新哲提出了扩散控制硫脲浸金速率表达式,从试剂的最佳匹配入手,以降低试剂消耗及操作成本,提出了优化工艺,使主试剂消耗降到常规硫脲法的1/3到1/5。
张钦发对贫细含金褐铁矿石用硫脲法浸金进行了研究,结果表明:中温培烧不但可以提高硫脲浸金速度和金的浸出率,而且可使硫脲的单耗降低5一6倍,使每吨矿石的硫服用量降800g/t,这主要因为培烧后,[Fe3+]/Fe2+比值在一个合适的范围内,从而改善硫脲的浸出,降低硫脲的消耗。
同时着重研究了椰壳炭对金的吸附及影响吸附和浸出的因素;同时对其吸附动力学进行了探讨。
研究结果表明:对贫细微含金褐铁矿石采用硫脲一炭浆法提金新工艺,浸出时间短(共6h),浸出率86%,炭吸附率98%,解吸率98%,使金的总回收率达82%,硫脉单耗为800g/t。