半导体制造工艺_10离子注入(下)
离子注入工艺原理

离子注入工艺原理离子注入(Ion Implantation)是一种常用的半导体加工技术,通过将选择性的离子注入到半导体材料中,来改变其电学性质,实现各种功能。
离子注入工艺原理可以分为三个主要步骤:离子产生,离子加速以及离子注入。
首先,离子产生是离子注入过程的第一步。
离子源是离子加速的关键,通常使用离子源来产生所需的离子种类。
离子源有许多类型,包括离子脱附(sputtering)源、电离源(ionization)或者离子化(ionized)源等。
其中较为常见的是离子脱附源,通过将砷、硼等半导体材料投放在高能量粒子(如氩离子)中,来脱离砷或硼原子产生相应离子。
这些离子会进一步被加速,并被注入到半导体材料中。
接下来,是离子加速的过程。
离子会通过一种电场来加速,通常是一个加速器。
这个电场可以是一个电势差,通过与离子之间形成的电场将离子加速到高能量。
在离子注入中,通常使用的是加速电势差。
离子源中的离子在电场的作用下,获得足够的能量,从而达到所需的注入深度。
最后,是离子注入的过程。
一旦离子获得足够的能量,它们会进入到半导体材料中,并通过对材料进行注入来改变其电学性质。
离子注入的深度可以通过加速电压和荷质比等参数来控制,通过调整参数可以实现不同深度的注入。
离子注入技术的原理在于将特定的离子种类注入到半导体材料中,从而改变其性质。
原子尺寸的改变可以影响材料的电学、磁学和光学性质。
例如,将掺杂硼离子注入到硅材料中可以将其掺杂变成P类型半导体,而将掺杂磷离子注入到硅材料中可以将其掺杂变成N类型半导体。
这种通过离子注入调整材料性质的能力,使得离子注入成为了半导体工业中不可或缺的一部分。
离子注入工艺有许多应用,包括集成电路制造和半导体器件制造。
通过离子注入,可以改变材料的导电性、控制晶体中的通道形成、增加或改变半导体材料中的杂质等。
这对于集成电路芯片和其他电子元件的设计和制造至关重要,使其具有所需的电学性质和性能。
总之,离子注入工艺通过离子源的产生、离子加速和离子注入等步骤,将特定的离子注入到半导体材料中,从而改变其性质。
半导体制造技术导论离子注入工艺

• 阈值电压控制:通过离子注入工艺调节PMOS和NMOS
区
的阈值电压
• NMOS器件:N型半导体作为沟道,P型半导体作为源漏
• 掺杂区形成:通过离子注入工艺形成PMOS和NMOS的
区
源漏区
离子注入工艺在光电二极管中的应用
光电二极管的结构特点
• P-N结:由P型半导体和N型半导体组成的结
• 光敏区:位于P-N结附近的区域,对光敏感
• 掺杂浓度均匀性:如何实现更均匀的掺杂,提高器件性能
• 注入损伤:离子注入过程中如何减少对半导体材料的损伤
• 工艺集成:如何将离子注入工艺与其他工艺集成,提高生产效率
解决方案
• 优化离子注入设备和工艺:提高掺杂浓度的均匀性和降低注入损伤
• 采用新型离子注入技术:如扫描离子注入、等离子体浸入离子注入等,提高工艺效
• 多离子注入技术的发展:实现多种元素的共注入,提高器件的性能和可靠性
离子注入工艺的发展方向
• 精确控制掺杂:实现更精确的浓度控制和更均匀的掺杂
• 降低能耗优化离子注入设备和工艺,降低能耗
• 环保减排:减少离子注入过程中的污染排放,提高环保水平
离子注入工艺面临的挑战及解决方案
离子注入工艺面临的挑战
果
• 加强工艺集成:与光刻、刻蚀等工艺进行集成,提高生产效率
离子注入工艺在未来半导体制造中的应用前景
离子注入工艺在集成电路制造中的应用
• 提高晶体管、二极管等器件的性能,提高集成电路的整体性能
• 实现新型器件的制作,如鳍式场效应晶体管(FinFET)等
离子注入工艺在光电二极管制造中的应用
• 提高光电二极管的光电转换效率,提高光电传感器的性能
• 大电流器件:需要承受大电流的器件
半导体工艺 离子注入 沉积

半导体工艺离子注入沉积半导体工艺是一种制造半导体器件的过程,它包括多个步骤,其中离子注入和沉积是两个重要的工艺步骤。
离子注入是一种将离子束注入到半导体材料中的过程。
它是通过加速器将离子加速到高速,并在一个非常小的区域内注入到半导体材料中。
这些注入的离子会改变半导体材料的电学性质,从而实现器件的功能。
离子注入可以用于掺杂半导体材料,改变其导电性能,或者形成浅层或深层的掺杂区域。
离子注入通常在高真空条件下进行,以确保离子束的稳定性和精度。
沉积是一种在半导体表面上沉积材料的过程。
沉积可以用于制备各种薄膜材料,如金属、氧化物、多晶硅等。
这些薄膜材料可以用于制造晶体管、电容器、电阻器等器件。
沉积过程可以通过化学气相沉积(CVD)或物理气相沉积(PVD)来实现。
CVD是一种通过化学反应在半导体表面上沉积材料的方法,而PVD是一种通过物理过程将材料沉积在半导体表面上的方法。
沉积过程中的温度、压力和气体流量等参数都对沉积薄膜的性质有重要影响。
离子注入和沉积是半导体工艺中不可或缺的步骤。
离子注入可以用于形成掺杂区域,改变半导体材料的导电性能。
而沉积可以制备各种薄膜材料,用于制造半导体器件的不同部分。
这两个工艺步骤的精确控制和优化可以提高器件的性能和可靠性。
在离子注入和沉积过程中,需要考虑多个因素来实现最佳的工艺结果。
首先,离子注入过程中需要选择合适的离子种类和能量,以达到所需的掺杂浓度和深度。
其次,沉积过程中需要选择合适的沉积条件,如温度、压力和气体流量,以获得均匀且致密的薄膜。
同时,需要注意控制沉积速率和薄膜厚度,以满足器件的要求。
离子注入和沉积是半导体工艺中的两个重要步骤,它们在制造半导体器件中起着关键的作用。
离子注入可以改变半导体材料的电学性质,而沉积可以制备各种薄膜材料。
通过优化这两个工艺步骤,可以提高器件的性能和可靠性,推动半导体技术的发展。
半导体制造工艺_10离子注入(下)

半导体制造工艺基础
第七章 离子注入 (下)
什么是注入损伤 晶格损伤:高能离子注入硅片后与靶原子发生一系列碰
撞,可能使靶原子发生位移,被位移原子还可能把能量依 次传给其它原子,结果产生一系列的空位-间隙原子对及 其它类型晶格无序的分布。这种因为离子注入所引起的简 单或复杂的缺陷统称为晶格损伤。
5
(Si)SiSiI + SiV
精确控制掺杂,浅结、 浅掺杂,纯度高,低温, 多种掩模,… 非晶靶。能量损失为两个彼 此独立的过程(1) 核阻止与(2) 电子阻止之和。能量为E的入 射粒子在密度为N的靶内走 过x距离后损失的能量。
C * xm CB
半导体制造工艺基础
第七章 离子注入 (下)
2
总阻止本领(Total stopping power)
第七章 离子注入 (下) 损伤退火 (Damage Annealing)
被注入离子往往处于半导体晶格的间隙位置,对 载流子的输运没有贡献;而且也造成大量损伤。 注入后的半导体材料: 杂质处于间隙 n<<ND;p<<NA 晶格损伤,迁移率下降;少子寿命下降 热退火后:n n=ND (p=NA)
半导体制造工艺基础
第七章 离子注入 (下)
6
损伤的产生
• 移位原子:因碰撞而离开晶格位置的原子。 • 移位阈能Ed:使一个处于平衡位置的原子发生 移位,所需的最小能量. (对于硅原子, Ed15eV) • 注入离子通过碰撞把能量传给靶原子核及其电 子的过程,称为能量传递过程
半导体制造工艺基础
第七章 离子注入 (下)
半导体制造工艺基础
第七章 离子注入 (下) 离子注入损伤估计
8
100KeV B离子注入损伤 初始核能量损失:30eV/nm, 硅晶面间距: 0.25nm, 每穿过一个晶面 能量损失: 30eV/nm X 0.25nm=7.5eV <Ed (15eV). 当能量降到50KeV, 穿过一个晶面能量损失为15eV, 该能量所对应的射程为: 150nm. 位 移原子数为: 150/0.25=600, 如果移位距离为: 2.5nm, 那么损伤体积: (2.5)2 X150=3X10-18cm3. 损伤密度: 2X1020 cm-3, 大约是原子密度 0.4%. 100KeV As离子注入损伤 平均核能量损失:1320eV/nm,损伤密度: 5X1021 cm-3, 大约是原子密 度10%, 该数值为达到晶格无序所需的临界剂量, 即非晶阈值.
半导体制造工艺之离子注入原理课件

Z12
3
Z
2 2
3
m1 m2
摘自J.F. Gibbons, Proc. IEEE, Vol. 56 (3), March, 1968, p. 295
例如:磷离子Z1 = 15, m1 = 31 注入硅 Z2 = 14, m2 = 28, 计算可得:
Sn ~ 550 keV-mm2
电子阻止本领
局部电子阻止 非局部电子阻止
减少沟道效应的措施
❖ 对大的离子,沿沟道轴向(110)偏离7-10o
❖用Si,Ge,F,Ar等离子注入使表面预非晶 化,形成非晶层(Pre-amorphization)
❖增加注入剂量(晶格损失增加,非晶层形成, 沟道离子减少)
❖表面用SiO2层掩膜
典型离子注入参数
离子:P,As,Sb,B,In,O 剂量:1011~1018 cm-2 能量:1– 400 keV 可重复性和均匀性: ±1% 温度:室温 流量:1012-1014 cm-2s-1
1) 试估算注入离子的投影射程,投影射程标准偏差、 峰 值浓度、结深
2) 如注入时间为1分钟,估算所需束流。
【解】1) 从查图或查表 得
Rp=4289 Å=0.43 mm Rp855 Å0.086 mm 峰值浓度
Cp=0.4Q/Rp=0.4×5×1014/(0.086×10-4)=2.34×1019 cm-3
110
111
100
倾斜旋转硅片后的无序方向
沿<100>的沟道效应
产生非晶化的剂量
浓度分布 由于沟道效应的存在,在晶体中注入将偏
离LSS理论在非晶体中的高斯分布,浓度分布中出现 一个相当长的“尾巴”
表面非晶层对于沟道效应的作用
半导体制造工艺离子注入下
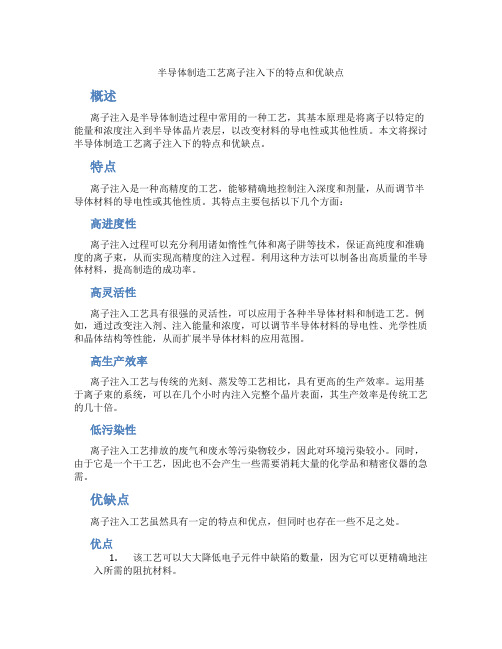
半导体制造工艺离子注入下的特点和优缺点概述离子注入是半导体制造过程中常用的一种工艺,其基本原理是将离子以特定的能量和浓度注入到半导体晶片表层,以改变材料的导电性或其他性质。
本文将探讨半导体制造工艺离子注入下的特点和优缺点。
特点离子注入是一种高精度的工艺,能够精确地控制注入深度和剂量,从而调节半导体材料的导电性或其他性质。
其特点主要包括以下几个方面:高进度性离子注入过程可以充分利用诸如惰性气体和离子阱等技术,保证高纯度和准确度的离子束,从而实现高精度的注入过程。
利用这种方法可以制备出高质量的半导体材料,提高制造的成功率。
高灵活性离子注入工艺具有很强的灵活性,可以应用于各种半导体材料和制造工艺。
例如,通过改变注入剂、注入能量和浓度,可以调节半导体材料的导电性、光学性质和晶体结构等性能,从而扩展半导体材料的应用范围。
高生产效率离子注入工艺与传统的光刻、蒸发等工艺相比,具有更高的生产效率。
运用基于离子束的系统,可以在几个小时内注入完整个晶片表面,其生产效率是传统工艺的几十倍。
低污染性离子注入工艺排放的废气和废水等污染物较少,因此对环境污染较小。
同时,由于它是一个干工艺,因此也不会产生一些需要消耗大量的化学品和精密仪器的急需。
优缺点离子注入工艺虽然具有一定的特点和优点,但同时也存在一些不足之处。
优点1.该工艺可以大大降低电子元件中缺陷的数量,因为它可以更精确地注入所需的阻抗材料。
2.离子注入技术可以在按照如果更有创新性和精雕细琢地制造半导体设备和电子设备,能够加快成本效益的提高。
3.该工艺可以提高半导体的可靠性和稳定性,使电子元件精度更高,导致更小的误差和更强的稳定性。
缺点1.离子注入工艺的过程复杂,需要大量的设备和材料,劳动力成本也很高,因此成本也很高。
2.由于注册过程涉及精确的器件结构,所以还需要很高的制造技术水平,否则可能出现制造问题,导致获得不优质的产品。
3.温度也必须表现出较高的精度,否则难以控制受影响的组件表面及器件的结构。
半导体工艺之离子注入
半导体离子注入工艺09电科A柯鹏程 0915221019离子注入法掺杂和扩散法掺杂对比来说,它的加工温度低、容易制作浅结、均匀的大面积注入杂质、易于自动化等优点。
当前,离子注入法已成为超大规模集成电路制造中不可缺少的掺杂工艺。
离子注入是一种将带点的且具有能量的粒子注入衬底硅的过程。
注入能量介于1eV到1MeV之间,注入深度平均可达10nm~10um。
相对扩散工艺,粒子注入的主要好处在于能更准确地控制杂质参杂、可重复性和较低的工艺温度。
1.离子注入原理:离子是原子或分子经过离子化后形成的,即等离子体,它带有一定量的电荷。
可通过电场对离子进行加速,利用磁场使其运动方向改变,这样就可以控制离子以一定的能量进入wafer内部达到掺杂的目的。
离子注入到wafer中后,会与硅原子碰撞而损失能量,能量耗尽离子就会停在wafer中某位置。
离子通过与硅原子的碰撞将能量传递给硅原子,使得硅原子成为新的入射粒子,新入射离子又会与其它硅原子碰撞,形成连锁反应。
杂质在wafer中移动会产生一条晶格受损路径,损伤情况取决于杂质离子的轻重,这使硅原子离开格点位置,形成点缺陷,甚至导致衬底由晶体结构变为非晶体结构。
2.离子射程离子射程就是注入时,离子进入wafer内部后,从表面到停止所经过的路程。
入射离子能量越高,射程就会越长。
投影射程是离子注入wafer内部的深度,它取决于离子的质量、能量,wafer的质量以及离子入射方向与晶向之间的关系。
有的离子射程远,有的射程近,而有的离子还会发生横向移动,综合所有的离子运动,就产生了投影偏差。
3.离子注入剂量注入剂量是单位面积wafer表面注入的离子数,可通过下面的公式计算得出 Q=It/enA ,式中,Q是剂量;I是束流,单位是安培;t是注入时间,单位是秒;e是电子电荷,1.6×10-19C;n是电荷数量;A是注入面积,单位是。
4.离子注入工艺(1)沟道效应入射离子与wafer之间有不同的相互作用方式,若离子能量够高,则多数被注入到wafer内部;反之,则大部分离子被反射而远离wafer。
半导体离子注入技术解析
半导体离子注入技术解析摘要离子注入技术是当今半导体行业对半导体进行掺杂的最主要方法。
本文从对该技术的基本原理、基本仪器结构以及一些具体工艺等角度做了较为详细的介绍,同时介绍了该技术的一些新的应用领域。
关键字离子注入技术半导体掺杂1绪论离子注入技术提出于上世纪五十年代,刚提出时是应用在原子物理和核物理究领域。
后来,随着工艺的成熟,在1970年左右,这种技术被引进半导体制造行业。
离子注入技术有很多传统工艺所不具备的优点,比如:是加工温度低,易做浅结,大面积注入杂质仍能保证均匀,掺杂种类广泛,并且易于自动化。
离子注入技术的应用,大大地推动了半导体器件和集成电路工业的发展,从而使集成电路的生产进入了大规模及超大规模时代(ULSI)。
由此看来,这种技术的重要性不言而喻。
因此,了解这种技术进行在半导体制造行业以及其他新兴领域的应用是十分必要的。
2 基本原理和基本结构2.1 基本原理离子注入是对半导体进行掺杂的一种方法。
它是将杂质电离成离子并聚焦成离子束,在电场中加速而获得极高的动能后,注入到硅中而实现掺杂。
离子具体的注入过程是:入射离子与半导体(靶)的原子核和电子不断发生碰撞,其方向改变,能量减少,经过一段曲折路径的运动后,因动能耗尽而停止在某处。
在这一过程中,涉及到“离子射程”、“”等几个问题,下面来具体分析。
2.1.1 离子射程图2.1.1(a ) 离子射程模型图图2.1.1(a )是离子射入硅中路线的模型图。
其中,把离子从入射点到静止点所通过的总路程称为射程;射程的平均值,记为R ,简称平均射程 ;射程在入射方向上的投影长度,记为p x ,简称投影射程;投影射程的平均值,记为p R ,简称平均投影射程。
入射离子能量损失是由于离子受到核阻挡与电子阻挡。
定义在位移x 处这两种能量损失率分别为n S 和e S :nn xdE S d =(1)ee e dE S k E dx==(2)则在dx 内总的能量损失为:()n e n e dE dE dE S S dx =+=+(3)P0000P 0n ed d d d d R E E E ER x E x S S ===+⎰⎰⎰(4)n S 的计算比较复杂,而且无法得到解析形式的结果。
半导体离子注入的概念
半导体离子注入是半导体制程中关键的工艺技术,主要涉及将杂质元素以离子形态注入到硅晶圆中,以改变晶圆衬底材料的化学性质。
具体来说,这一过程通过将气体形态的掺杂化合物原材料导入反应腔,加入电场和磁场交作用形成电浆等离子体,然后离子束从反应腔萃取出来后,受到电场牵引而加速前进,并在通过磁场后进行二次加速,提高离子束射程。
在加速过程中,高能量离子束与材料中的原子或分子发生物理和化学相互作用,最终导致注入的离子停留在材料中,并引起材料表面成分、结构和性能的变化。
离子注入技术具有许多优点,例如能够精确控制注入剂量、注入角度、注入深度和横向扩散等,使得其在半导体制造中被广泛应用。
与传统的热扩散工艺相比,离子注入技术具有更高的精度和灵活性。
在集成电路制造工艺中,离子注入通常应用于深埋层、倒掺杂阱、阈值电压调节、源漏注入、多晶硅栅掺杂等。
这一技术的应用提高了材料表面的载流子浓度和导电类型,为现代电子设备的微型化和高性能化奠定了基础。
如需更多关于“半导体离子注入”的信息,建议咨询半导体相关专家或查阅相关专业文献。
半导体制造工艺之离子注入原理
半导体制造工艺之离子注入原理引言离子注入是半导体制造工艺中的一种重要方法,广泛应用于半导体器件的加工和制造过程中。
离子注入工艺通过将高能离子注入到半导体晶体中,改变材料的物理和化学性质,实现半导体器件的特定功能和性能。
本文将详细介绍离子注入的原理以及其在半导体制造中的应用。
离子注入原理离子注入是利用离子束对半导体材料进行信息改变的过程,其原理基于以下几个关键步骤:1.离子源生成:离子注入过程首先需要一个稳定的离子源。
常见的离子源包括离子源装置和离子源材料。
离子源装置通过电离气体产生离子束,而离子源材料通常是一种固体材料,通过加热或溶解的方式释放离子。
2.离子加速:生成的离子束经过电场加速,增加其能量和速度。
加速电场的大小决定了离子注入的能量和深度。
3.汇聚和对准:离子束通过极板或磁场对准系统,确保离子束准确地注入到半导体材料的目标区域。
4.离子注入:离子束与半导体材料进行相互作用,离子穿过材料表面,在材料内部形成注入层。
离子注入的能量和剂量可以控制和调节,影响着半导体的特性和性能。
5.后续处理:注入完成后,需要进行一系列的后续处理步骤,如退火、清洗等,以恢复和优化器件的电学性能。
离子注入的应用离子注入在半导体制造中有着广泛的应用,主要体现在以下几个方面:1.掺杂:离子注入可在半导体材料中引入杂质原子,从而改变材料的电学性质。
通过控制离子注入的能量和剂量,可以实现器件中的PN结、N型、P型等区域。
2.改变表面特性:离子注入还可用于改变半导体材料表面的化学和物理特性。
例如,在CMOS制造中,通过离子注入改变材料表面的电导率,形成NMOS、PMOS等区域。
3.改善电子迁移率:离子注入还可用于改善半导体器件中电子的迁移率,提高器件的性能。
通过注入低能量离子,形成浅表层,可以减少晶格缺陷,提高电子的迁移率。
4.修复损伤:半导体材料在制造过程中往往会受到损伤,如晶格位错、空位等。
离子注入可用于修复这些损伤,提高材料的完整性和性能。
- 1、下载文档前请自行甄别文档内容的完整性,平台不提供额外的编辑、内容补充、找答案等附加服务。
- 2、"仅部分预览"的文档,不可在线预览部分如存在完整性等问题,可反馈申请退款(可完整预览的文档不适用该条件!)。
- 3、如文档侵犯您的权益,请联系客服反馈,我们会尽快为您处理(人工客服工作时间:9:00-18:30)。
重离子每次碰撞传输给靶的能量较 大,散射角小,获得大能量的位移 原子还可使许多原子移位。注入离 子的能量损失以核碰撞为主。同时, 射程较短,在小体积内有较大损伤。 重离子注入所造成的损伤区域小, 损伤密度大。
半导体制造工艺基础
第七章 离子注入 (下)
8
离子注入损伤估计
100KeV B离子注入损伤 初始核能量损失:30eV/nm, 硅晶面间距: 0.25nm, 每穿过一个晶面 能量损失: 30eV/nm X 0.25nm=7.5eV <Ed (15eV). 当能量降到50KeV, 穿过一个晶面能量损失为15eV, 该能量所对应的射程为: 150nm. 位 移原子数为: 150/0.25=600, 如果移位距离为: 2.5nm, 那么损伤体积: (2.5)2 X150=3X10-18cm3. 损伤密度: 2X1020 cm-3, 大约是原子密度
漏电流大
半导体制造工艺基础
第七章 离子注入 (下)
14
a) 退火
一定温度下,通常在Ar、N2或真空条件下 退火温度取决于注入剂量及非晶层的消除。 修复晶格:退火温度600 oC以上,时间最长可达数小时 杂质激活:退火温度650-900 oC,时间10-30分钟
* 方法简单 * 不能全部消除缺陷 * 对高剂量注入激活率不够高 * 杂质再分布
掩膜层能完全阻挡离子的条件:
C *xm CB
射粒子在密度为N的靶内走 过x距离后损失的能量。
半导体制造工艺基础
第七章 离子注入 (下)
2
总阻止本领(Total stopping power)
核阻止和电 子阻止相等 的能量
❖ 核阻止本领在低能量下起主要作用(注入分布的尾端) ❖ 电子阻止本领在高能量下起主要作用
晶格损伤:高能离子注入硅片后与靶原子发生一系列碰
撞,可能使靶原子发生位移,被位移原子还可能把能量依 次传给其它原子,结果产生一系列的空位-间隙原子对及 其它类型晶格无序的分布。这种因为离子注入所引起的简 单或复杂的缺陷统称为晶格损伤。
(Si)SiSiI + SiV
半导体制造工艺基础
第七章 离子注入 (下)
半导体制造工艺基础
第七章 离子注入 (下)
15
b)快速热退火, Rapid Thermal Processing(RTP) 。高功率激光束辐照
。电子束
。高强度的光照
。其它辐射
RTP主要优点是掺杂的再分布大大降低, 对制备浅结器件特别有利
半导体制造工艺基础
第七章 离子注入 (下)
半导体制造工艺基础
第七章 离子注入 (下)3 Nhomakorabea射程终点(EOR) 处晶格损伤大
表面处晶格 损伤较小
半导体制造工艺基础
第七章 离子注入 (下)
4
EOR damage
Courtesy Ann-Chatrin Lindberg (March 2002).
半导体制造工艺基础
第七章 离子注入 (下)
5
什么是注入损伤
6
损伤的产生
• 移位原子:因碰撞而离开晶格位置的原子。
• 移位阈能Ed:使一个处于平衡位置的原子发生
移位,所需的最小能量. (对于硅原子, Ed15eV)
• 注入离子通过碰撞把能量传给靶原子核及其电 子的过程,称为能量传递过程
半导体制造工艺基础
第七章 离子注入 (下)
7
损伤区的分布
质量较靶原子轻的离子传给靶原子 能量较小,被散射角度较大,只能 产生数量较少的位移靶原子,因此, 注入离子运动方向的变化大,产生 的损伤密度小,不重叠,但区域较 大。呈锯齿状。
半导体制造工艺基础
第七章 离子注入 (下)
1
上节课主要内容
Cx Cp
exp
1 2
xR Rp
p
2
CP
0.4Q R p
离子注入的主要特点? LSS理论?阻止能力的含义?
精确控制掺杂,浅结、 浅掺杂,纯度高,低温, 多种掩模,…
离子注入的杂质分布?退火后? 非晶靶。能量损失为两个彼
掩蔽膜的厚度?
此独立的过程(1) 核阻止与(2) 电子阻止之和。能量为E的入
半导体制造工艺基础
第七章 离子注入 (下)
13
✓该{311}缺陷带在较高温度下(800~1000 C)即可退
火修复,但是释放出大量填隙原子I。
TED
✓损伤小于临界值,这些{311}缺陷可以完全分解,回复 完美晶体。
✓损伤高于临界值,则{311}缺陷可能变成稳定的位错环,
该位错环位于EOR,并难以去除。
半导体制造工艺基础
第七章 离子注入 (下)
12
损伤恢复机制 (Damage Recovery Mechanism)
Annihilation: recombination Frenkel I-V pairs
SiI + SiV (Si)Si
Monte Carlo模拟的 I-V 复合结 果:短时间内(10-2秒)800 C 下,体内的 V 在表面复合迅速 完成,产生剩余的 I ,其表面 复合相对较缓慢。在400 C以 上,这些 I 可接合入{311}面形 成棒/带状缺陷,并可以稳定较 长时间。
注入后的半导体材料: 杂质处于间隙 n<<ND;p<<NA 晶格损伤,迁移率下降;少子寿命下降
热退火后:n n=ND (p=NA)
bulk 0
半导体制造工艺基础
第七章 离子注入 (下)
11
损伤退火的目的
去除由注入造成的损伤,让硅晶格恢复其原有完美晶体结构 让杂质进入电活性(electrically active) 位置-替位位置。 恢复电子和空穴迁移率 注意:退火过程中应避免大幅度的杂质再分布
0.4%. 100KeV As离子注入损伤
平均核能量损失:1320eV/nm,损伤密度: 5X1021 cm-3, 大约是原子密 度10%, 该数值为达到晶格无序所需的临界剂量, 即非晶阈值.
半导体制造工艺基础
第七章 离子注入 (下)
9
非晶化(Amorphization)
注入离子引起的晶格损伤 有可能使晶体结构完全破 坏变为无序的非晶区。
与注入剂量的关系 – 注入剂量越大,晶格损 伤越严重。 – 临界剂量:使晶格完全 无序的剂量。 – 临界剂量和注入离子的 质量有关
半导体制造工艺基础
第七章 离子注入 (下)
10
损伤退火 (Damage Annealing)
被注入离子往往处于半导体晶格的间隙位置,对 载流子的输运没有贡献;而且也造成大量损伤。