液相循环加氢技术
减压蜡油全液相加氢处理技术的工业应用
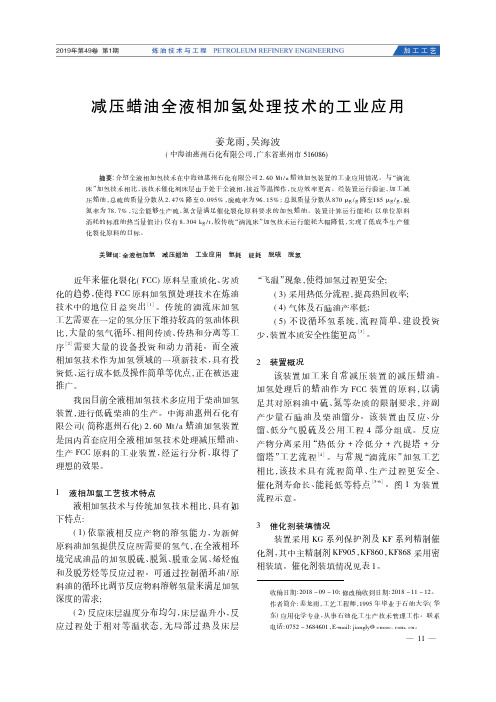
图 2 反应器升温曲线 Fig. 2 Curve of heating reactor
5 催化剂预硫化情况 9 月 28 日 16 ∶ 00,开始催化剂湿法预硫化。
因低分气中硫化氢含量非常高,低分气采取一次 通过操作,不循环回补充氢压缩机入口。考虑到 硫化过程中会生成大量水,开循环油泵后,生成水 会在 反 应 器 中 循 环,无 法 彻 底 带 出,随 着 温 度 升 高,可能会损坏催化剂。经与催化剂厂家及专利 商沟通,确定硫化期间不开循环油泵,采用提高反 应进料量来增加溶解氢的硫化方案。
减压蜡油全液相加氢处理技术的工业应用
姜龙雨,吴海波
( 中海油惠州石化有限公司,广东省惠州市 516086)
摘要: 介绍全液相加氢技术在中海油惠州石化有限公司 2. 60 Mt / a 蜡油加氢装置的工业应用情况。与“滴流 床”加 氢 技 术 相 比 ,该 技 术 催 化 剂 床 层 由 于 处 于 全 液 相 ,接 近 等 温 操 作 ,反 应 效 率 更 高 。 经 装 置 运 行 验 证 ,加 工 减 压蜡油,总硫的质量分数从 2. 47% 降至 0. 095% ,脱硫率为 96. 15% ; 总氮质量分数从 870 μg / g 降至185 μg / g,脱 氮率为 78. 7% ,完全能够生产硫、氮含量满足催化裂化原料要求的加氢蜡油。装置计算运行能耗( 以单位原料 消耗的标准油热当量值计) 仅有 8. 304 kg / t,较传统“滴流床”加氢技术运行能耗大幅降低,实现了低成本生产催 化裂化原料的目标。
下特点: ( 1) 依靠液相反应产物的溶氢能液相环 境完成油品的加氢脱硫、脱氮、脱重金属、烯烃饱 和及脱芳烃等反应过程。可通过控制循环油 /原 料油的循环比调节反应物料溶解氢量来满足加氢 深度的需求;
液相加氢技术的应用现状

C-NUM 液相加氢技术的应用对象也是航煤原料,这种原 料本身的性质和状态比常规的柴油等油料更好,加氢效果更 佳,整个精制过程的对循环系统、反应环境的要求比较小。在面 对航煤原料时,C-NUM 技术应用装置取消了循环油系统,有效 降低了循环泵可能带来的安全风险和成本、动力消耗;反应温 度为 245 ℃,压力为 3.5 MPa,氢油比在 12~13 范围内,属于较 为理想的反应过程。但如果面对的是原料性质、状态更差一些 的焦化柴油等柴油种类时,C-NUM 技术装置能否顺利加氢,能 否顺利完成精制反应获得符合标准的产品油,还需要进一步的 实践和验证分析。
目前来看,液相加氢技术始终存在氢气消耗量高、循环加 氢能耗较高、循环泵安全风险较高、催化剂使用寿命较低等问 题。想要改善这些问题需要通过特殊的设备装置,提高氢气与 原料油的混合程度,实现原料油中的氢气饱和状态[3]。想要达 到氢气饱和的理想状态,可能需要超重力、微米气泡等类型的 装置,使原料油中的氢气溶解量远超于实际需求量。如果能够 解决溶氢过程中的氢气饱和问题,就能够真正节约掉循环加氢 的装置和能耗,并且规避掉循环泵可能带来的安全风险和泄露 风险。这是液相加氢技术未来发展的主要方向,突破这一难题 就能够促进液相加氢技术的有效发展,扩大液相加氢技术的应 用范围。目前的液相加氢技术还不能代替气相滴流等技术的应 用,在原料油精制反应中还不能占据更大的主动性[4]。
LI Nong, LI Hai-feng, ZHAO Xin-quan, LI Guo-qi (Sinochem Changhe Technology Co., Ltd., Dongying 257335, China)
Abstract: Liquid phase hydrogenation technology is a process to maintain high hydrogen-oil ratio, which can effectively improve the heat transfer effect between phases, can improve the reaction eff iciency of oil, reduce the power consumption in the application process of diesel oil, kerosene and other feedstock oils, and produce more environmentally friendly clean oil. In the process of liquid phase hydrogenation, the amount of hydrogen dissolved in oil is the key problem, which affects the energy consumption and production eff iciency of the technology. This paper mainly analyzes the application status and application prospect of this technology.
气相加氢与液相加氢工艺在柴油加氢中的对比分析
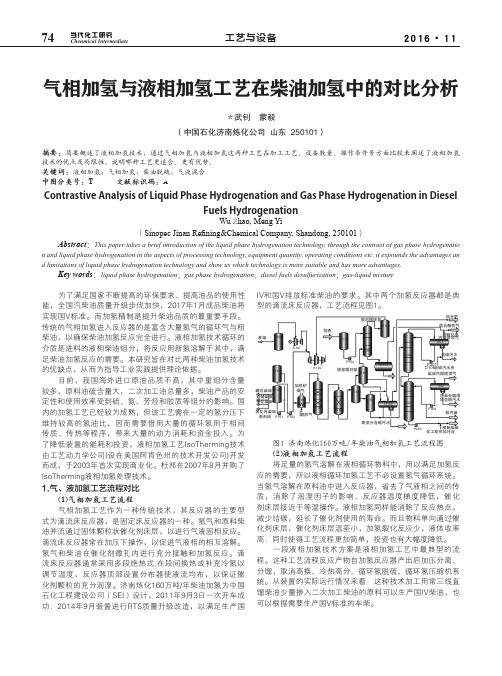
IV和国V排放标准柴油的要求。其中两个加氢反应器都是典 型的滴流床反应器,工艺流程见图1。
新氢 D108
K101
D102
贫液
D110
脱后循环氢 D107
K102
C101
P104 脱前循环氢
D105
D117
低分气
混合酸性气
汽脱提硫塔化顶氢气 D01
C201
含硫污水
P201 D106含硫污水来
柴油汽提塔顶气
2016·11
工艺与设备
75 当 代 化 工 研 究
Chenmical Intermediate
反应排气出装置 酸性水出装置
混合柴油
新氢
低分油至分馏塔 低分气出装置
低分油至分馏塔
图2 一段液相加氢流程 2.气、液加氢工艺主要设备对比
设备 热高压分离器 冷高压分离器 循环氢脱硫塔 循环氢压缩机入口
Fuels Hydrogenation
Wu Zhao, Meng Yi (Sinopec Jinan Refining&Chemical Company, Shandong, 250101) Abstract:This paper takes a brief introduction of the liquid phase hydrogenation technology, through the contrast of gas phase hydrogenatio
目前,我国海外进口原油品质不高,其中重组分含量 较多,原料油硫含量大,二次加工油总量多,柴油产品的安 定性和使用效率受到硫、氮、芳烃和胶质等组分的影响。国 内的加氢工艺已经较为成熟,但该工艺需在一定的氢分压下 维持较高的氢油比,因而需要借用大量的循环氢用于相间 传质、传热等程序,带来大量的动力消耗和资金投入。为 了降低装置的能耗和投资,液相加氢工艺IsoTherming技术 由工艺动力学公司(设在美国阿肯色州的技术开发公司)开发 而成,于2003年首次实现商业化。杜邦在2007年8月并购了 IsoTherming液相加氢处理技术。
柴油液相循环加氢技术的工业应用
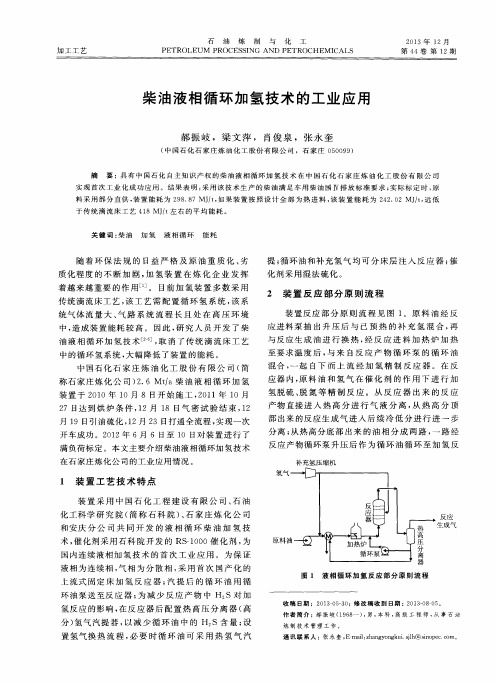
称石 家 庄炼 化 公 司 ) 2 . 6 Mt / a柴 油 液 相 循 环 加 氢
装 置于 2 0 1 0年 1 0月 8 日开 始 施 工 , 2 0 1 1年 1 O月
氢脱硫 、 脱 氮 等 精 制 反 应 。从 反 应 器 出 来 的反 应
产物直 接 进 入 热 高 分 进 行 气 液 分 离 。 从 热 高 分 顶 部 出来 的反应 生成 气 进 入后 续 冷 低 分 进 行 进 一 步 分离 ; 从 热高 分底 部 出来 的油 相 分 成 两 路 , 一 路 经 反应 产物 循环 泵 升压 后 作 为循 环油 循 环 至 加 氢 反
中的循 环 氢 系统 , 大幅 降低 了装 置 的能耗 。
中 国石化 石 家 庄 炼 油 化 工 股 份 有 限公 司 ( 简
至要 求 温 度 后 , 与 来 自反 应 产 物 循 环 泵 的 循 环 油 混合 , 一 起 自下 而 上 流 经 加 氢 精 制 反 应 器 。在 反 应器内, 原 料 油 和 氢 气 在 催 化 剂 的作 用 下 进 行 加
环油 泵送 至 反 应器 ; 为减少反应产物中 H S对 加
图1 液 相 循 环 加 氢 反 应 部 分原 则 流 程
反 应 生 成 气
氢反 应 的影 响 , 在 反 应 器后 配 置 热 高 压分 离 器 ( 高
分) 氢气 汽 提器 , 以 减少 循 环 油 中的 H S含 量 ; 设 置 氢气 换 热 流 程 , 必 要 时循 环 油 可 采 用 热 氢 气 汽
补 充 氢 压 缩 机
2 7日达 到烘 炉条 件 , 1 2月 1 8日气 密试 验 结 束 , 1 2
月 1 9日引 油 硫 化 , 1 2月 2 3日打 通 全 流 程 , 实 现 一 次
硝基苯液相催化加氢制苯胺技术进展
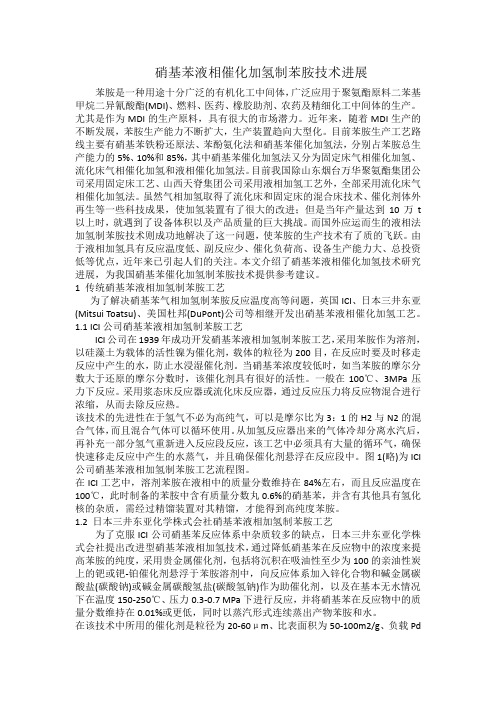
硝基苯液相催化加氢制苯胺技术进展苯胺是一种用途十分广泛的有机化工中间体,广泛应用于聚氨酯原料二苯基甲烷二异氰酸酯(MDI)、燃料、医药、橡胶助剂、农药及精细化工中间体的生产。
尤其是作为MDI的生产原料,具有很大的市场潜力。
近年来,随着MDI生产的不断发展,苯胺生产能力不断扩大,生产装置趋向大型化。
目前苯胺生产工艺路线主要有硝基苯铁粉还原法、苯酚氨化法和硝基苯催化加氢法,分别占苯胺总生产能力的5%、10%和85%,其中硝基苯催化加氢法又分为固定床气相催化加氢、流化床气相催化加氢和液相催化加氢法。
目前我国除山东烟台万华聚氨酯集团公司采用固定床工艺、山西天脊集团公司采用液相加氢工艺外,全部采用流化床气相催化加氢法。
虽然气相加氢取得了流化床和固定床的混合床技术、催化剂体外再生等一些科技成果,使加氢装置有了很大的改进;但是当年产量达到10万t 以上时,就遇到了设备体积以及产品质量的巨大挑战。
而国外应运而生的液相法加氢制苯胺技术则成功地解决了这一问题,使苯胺的生产技术有了质的飞跃。
由于液相加氢具有反应温度低、副反应少、催化负荷高、设备生产能力大、总投资低等优点,近年来已引起人们的关注。
本文介绍了硝基苯液相催化加氢技术研究进展,为我国硝基苯催化加氢制苯胺技术提供参考建议。
1 传统硝基苯液相加氢制苯胺工艺为了解决硝基苯气相加氢制苯胺反应温度高等问题,英国ICI、日本三井东亚(Mitsui Toatsu)、美国杜邦(DuPont)公司等相继开发出硝基苯液相催化加氢工艺。
1.1 ICI公司硝基苯液相加氢制苯胺工艺ICI公司在1939年成功开发硝基苯液相加氢制苯胺工艺,采用苯胺作为溶剂,以硅藻土为载体的活性镍为催化剂,载体的粒径为200目,在反应时要及时移走反应中产生的水,防止水浸湿催化剂。
当硝基苯浓度较低时,如当苯胺的摩尔分数大于还原的摩尔分数时,该催化剂具有很好的活性。
一般在100℃、3MPa压力下反应。
采用浆态床反应器或流化床反应器,通过反应压力将反应物混合进行浓缩,从而去除反应热。
液相加氢技术进展
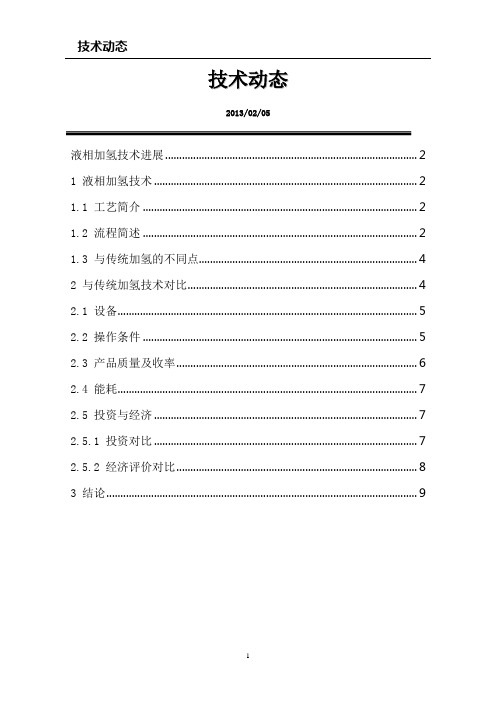
技术动态2013/02/05液相加氢技术进展 (2)1 液相加氢技术 (2)1.1 工艺简介 (2)1.2 流程简述 (2)1.3 与传统加氢的不同点 (4)2 与传统加氢技术对比 (4)2.1 设备 (5)2.2 操作条件 (5)2.3 产品质量及收率 (6)2.4 能耗 (7)2.5 投资与经济 (7)2.5.1 投资对比 (7)2.5.2 经济评价对比 (8)3 结论 (9)液相加氢技术进展在现代炼油行业,加氢处理装置往往由于操作条件较为苛刻,所以装置投资很大。
为此,为生产满足环保要求的清洁的石油产品,世界各国炼油技术人员开发了很多加氢技术,以降低装置的投资和能耗。
其中液相加氢技术是近几年发展起来的一种成熟的突破性加氢技术。
1 液相加氢技术1.1 工艺简介在加氢技术中,反应是以液相进行的。
传统加氢技术大量的富氢气循环气与进料一起进入反应器,以确保反应所要求的氢气被转换成液相。
液相加氢工艺技术反应部分不设置氢气循环系统,依靠液相产品循环以溶解足量的氢气,满足加氢反应的需要。
由于取消了氢气循环系统,节省了循环压缩机系统、高分系统及其相应设备,可以大大节约投资和能耗。
同时由于液相加氢工艺技术可以消除催化剂的润湿因子影响,而且循环油的比热容大,从而提高催化剂的利用效率,大大降低反应器的温升,降低裂化等副反应。
1.2 流程简述原料油自装置外来,通过原料油过滤器进行过滤,然后与精制柴油换热,进入滤后原料油缓冲罐,再经反应进料泵升压后,在流量控制下,与少量补充氢混合作为混合进料(图1)。
混合进料经过与一部分反应产物换热后,进入反应进料加热炉加热至所需温度,加热后的进料再与一定量的反应循环产物及一定量的补充新氢混合后进入加氢精制反应器第一催化剂床层,在催化剂作用下进行脱硫、脱氮、烯烃饱和、芳烃饱和等反应,加入到第一催化剂床层进料中的氢气量由进料液体的饱和限度决定,加入足够的氢气,直到第一催化剂床层有少量的尾气排出,这样可以确保氢气被完全饱和。
国产循环泵在航煤液相循环加氢装置的应用

表 1 循环泵操作参数
项目 介质 流量(/ m3·h-1) 扬程/m 入口表压/MPa 入口温度/℃ 密度(/ kg·m-3)
炼油与化工
2021 年 第 3 期
REFINING AND CHEMICAL INDUSTRY
49
国产循环泵在航煤液相循环加氢装置的应用
倪晓斌,高小妮,秦广华,王应虎
(陕西延长石油(集团)有限责任公司榆林炼油厂,陕西 榆林 718500)
摘要:某炼油厂以典型液相加氢技术为基础,对技术进行了改造升级,形成了航煤液相循环加
Ni Xiaobin,Gao Xiaoni,Qin Guanghua,Wang Yinghu
(Shaanxi Yanchang Petroleum(group)Yulin Refinery,Yulin 718500,China) Abstract:Based on the typical liquid-phase hydrogenation technology, a refinery reformed and upgraded the technology, and formed the aviation kerosene liquid-phase circulating hydrogenation process technology, which provided the hydrogen needed for the hydrogenation reaction as taking fresh feedstock into the reaction system when recycling of liquid-phase products that improved the product uniformity and stability. Yulin refinery selected domestic circulating pump in aviation kerosene unit for the first time, and there was no standby circulating pump. The actual operation results showed, domestic circulating pump had reliable quality, sta⁃ ble operation, low investment cost and operation cost, which was a better technology to realize oil quality upgrading at low cost. Keywords:domestic;circulating pump;liquid-phase hydrogenation;aviation kerosene
烃油液相循环加氢专利技术进展

5液相循环物流 的净化
液相循 环 加氢 的实 质是 在催 化剂 与氢 气接 触前 ,使 加氢 反应 所 需 的氢气 溶解 在 液相 中。对大 多数 原料 而言 ,反 应所 需氢气 量 远 比在反应 器操 作 条件 下溶解 于液 相 中氢气 量 多, 因此需 要使加
( 下转 第 4 2页)
【 中图分类 霉 Q
叠 蓦 誊 誊【 曩 ≮ 誊 ・ 文献标识硬 A 差 誊 誊 警 誊 蓦 【 蓐 妻 叠 文章编号】 o; s o 醮I 一l l7 (l o3 O s 2 o O
P tn r gesnH d 0 rcs n d oab nOib iudC ruain ae t o rs i y rp oes g P i Hy r cr o l y q i i lt L c o
一
,
置在 隔 离板 上面 ,这种 混合 器 结构 简单 ,可有 效地 增加 气液 相 间 接触 面 ,使氢 气 溶解 在混 合油 中 ,促进 反应 ,大 大提 高加氢 的效 率 。 同时脱 除 了反应 生成 的硫 化氢 和氨 ,避 免 了这些有 害杂 质对 下 一步 反应 的不 利影 响 ,增 加 了工 艺 的灵活 性 ,提 高 了原料 适应 性 。 一
- 1、下载文档前请自行甄别文档内容的完整性,平台不提供额外的编辑、内容补充、找答案等附加服务。
- 2、"仅部分预览"的文档,不可在线预览部分如存在完整性等问题,可反馈申请退款(可完整预览的文档不适用该条件!)。
- 3、如文档侵犯您的权益,请联系客服反馈,我们会尽快为您处理(人工客服工作时间:9:00-18:30)。
SRH液相循环加氢技术的开发背景
➢ 液相循环加氢稀释了原料中的杂质含量 –有机氮化物是加氢催化剂的毒物,对加氢脱氮、 加氢脱硫和加氢脱芳反应有明显的抑止作用。 ➢装置取消了循环氢压缩机系统、高压换热器、 高压空冷器、高压分离器、循环氢脱硫塔,热 量损失小,大幅度降低装置能耗。同时投资费 用和操作费用均低,是低成本实现油品质量升 级的较好技术。
SRH液相循环加氢技术 开发与工业应用
中国石化抚顺石油化工研究院 2011年10月
内容提要
一、SRH液相循环加氢技术的开发背景 二、SRH液相循环加氢技术开发 三、SRH液相循环加氢技术工业应用 四、结论
SRH液相循环加氢技术的开发背景
➢ 环保法规日益严格,柴油的硫含量标准在逐年修订,发 展和使用超低硫甚至无硫柴油是当今世界范围内清洁燃 料发展的趋势[1]。例如欧盟法规规定2009年车用柴油的 硫含量在10g/g以下,美国2006年限制车用柴油的硫含 量在15g/g以下。我国轻柴油规格标准GB252-2000对柴 油硫含量的要求是不大于2000g/g,城市车用柴油国家 标准GB-T19147-2003参照欧洲Ⅱ类标准制定,其硫含量 要求小于500g/g,2011年7月1日参照欧Ⅲ标准执行硫 含量小于350g/g。北京、上海等城市已率先执行参照 欧Ⅳ制定的京标C、沪Ⅳ标准,即要求硫含量小于 50g/g。为应对新排放标准柴油的生产,开发装置投资 低、操作费用低的柴油深度加氢技术非常必要。
SRH液相循环加氢技术的开发
➢ 研究结果表明: 压力提高气体溶解度提高 温度提高利于氢气溶解 温度提高不利于硫化氢、氨等气体的溶解
H 溶解度,m% 2
H2S 溶解度,m%
0.35
3.0MPa
0.30
4.0MPa
6.0MPa
0.25
8.0MPa
10.0MPa
12.0MPa
0.20
0.15
0.10
0.05
条件1
常一线油 0.7886
146~233 1258
1.8 220 6.6 精制油 0.7881 142~232 1088 通过
99.7 1
1.15 -61
6.5 1
0.75 -60 0.05
条件2 1.8 230 8.0 精制油 0.7885 148~232 1095 通过 9.7
1 0.97 -60 0.05
100
150
200
250
300
ቤተ መጻሕፍቲ ባይዱ350
400
温度,℃
图1 H2 在柴油中的饱和溶解度曲线
90
80
3.0MPa
4.0MPa
70
6.0MPa
8.0MPa
60
10.0MPa
50
40
30
20
10
0
100
150
200
250
300
350
温度,℃
图2 H2S在柴油中的饱和溶解度曲线
SRH液相循环加氢技术的开发
➢ 研究结果表明:
工艺条件 反应压力,MPa 反应温度,℃ 体积空速,h-1
油品性质 密度(20℃)/g.cm-3 馏程范围/℃ 硫/g.g-1 博士试验 硫醇硫/g.g-1 实际胶质/mg.100mL-1 溴价/gBr.100g-1 冰点/℃
化学氢耗,m%
SRH液相循环加氢中试研究
表1 直馏煤油高空速SRH加氢试验结果
SRH液相循环加氢技术的开发
SRH液相循环加氢中试研究
表2 直馏柴油SRH液相循环加氢试验结果
原料
工艺条件
反应压力/MPa
反应温度/℃ 体积空速(新鲜进料)/h-1
循环比
生成油性质 密度(20℃)/gcm-3 馏程(ASTMD-86)/℃ S/gg-1 N/gg-1
原料 0.8225 168-342 3500
SRH液相循环加氢技术的开发背景
➢ FRIPP开发的SRH液相循环加氢技术的优点是可 以消除催化剂的润湿因子影响,大大提高催化 剂的利用效率。原料油浸泡整个催化剂床层, 不需要额外工艺设备来确保氢气与油混合、液 相在催化剂上获得良好分散
➢ 循环油的比热容大,从而使催化剂床层接近等 温操作,延长催化剂寿命,降低裂化等副反应, 提高产品收率。
24
直馏轻柴油
6.4
6.4
350
350
3.0
4.5
1:1
1:1
生成油
0.8132
0.8122
5
9.5
1.0
1.0
直馏重柴油
原料 0.8569 220-379 17750
140
10.0 360 1.5 2:1 生成油 0.8210
30 1.0
SRH液相循环加氢技术的开发背景
➢ 在常规氢气循环固定床加氢工艺过程中,通常采 用较大的氢油体积比。反应后富余氢气经循环氢 压缩机增压并与新氢混合后继续作为反应的氢气 进料。循环氢压缩机的投资占整个加氢装置成本 的比例较高,氢气换热系统能耗较大。
➢ FRIPP开发的SRH液相循环加氢技术,依靠液相产 品大量循环时携带进反应系统的溶解氢来提供新 鲜原料进行加氢反应所需要的氢气。
2.6
2.4
3 MPa
4 MPa
2.2
6MPa
2.0
8MPa
1.8
10MPa
1.6
1.4
1.2
1.0
0.8
0.6
0.4
0.2
100
150
200
250
300
350
Temperature,℃
图3 NH3 在柴油中的饱和溶解度曲线
3.5
3 MPa
4 MPa
6MPa
3.0
8MPa
10MPa
2.5
2.0
1.5
氨在柴油中的饱和溶解度随着温度提高而降低,在高温区压力对饱和溶解度影响小; 甲烷在柴油中的饱和溶解度随着温度变化影响不是很大,压力升高溶解度增大; 乙烷、丙烷及丁烷在柴油中的溶解度(图省略)远大于甲烷且随着温度提高而略降
低,压力升高溶解度增大。
NH solubility,m% 3
CH solubility,m% 4
1.0
0.5
100
150
200
250
300
350
Temperature,℃
图4 CH4在柴油中的饱和溶解度曲线
SRH液相循环加氢技术的开发
SRH液相循环加氢中试研究
新氢
混氢器1
混氢器2
A反应器
B反应器
进料
原料油泵
循环油
循环油泵 P-7
低分 精制油
图5 SRH液相循环加氢中型试验装置流程简图
SRH液相循环加氢技术的开发
SRH液相循环加氢技术的开发
➢ SRH液相循环加氢技术创新点 抚顺石油化工研究院经过对液相循环加氢工
艺技术的深入研究,已经申请了17件专利。 主要创新点:
➢ 开发了分两路循环的SRH液相循环加氢工艺技术; ➢ 采用反应器顶部排气和反应器出口流量控制液位
的控制系统; ➢ 在反应器上部设置特殊内构件和气体排放设施。