Isotherming液相循环加氢技术的工业应用-金澳 1
液相循环加氢(SRH)技术在柴油加氢装置中的推广应用

液相循环加氢(SRH)技术在柴油加氢装置中的推广应用发表时间:2019-11-14T12:11:38.420Z 来源:《科学与技术》2019年第12期作者:周卫锋田端强[导读] 为满足质量升级的要求,胜利石化总厂引进中石化开发的液相循环加氢(SRH)技术在100万吨/年的柴油加氢装置推广应用。
摘要:为满足质量升级的要求,胜利石化总厂引进中石化开发的液相循环加氢(SRH)技术在100万吨/年的柴油加氢装置推广应用。
结果表明:液相循环加氢(SRH)技术后与传统柴油加氢技术相比,装置一次投资少;产品达到Ⅵ柴油标准,可生产出符合国Ⅵ标准的车用清洁柴油;节能效果明显,能耗比传统加氢装置节约3-3.5kg标油/吨原料具有明显的经济效益和社会效益。
关键词:液相循环加氢(SRH)硫含量加氢节能前言环境问题是中国21世纪面临的最严峻挑战之一,保护环境是保证经济长期稳定增长和实现可持续发展的基本国家利益。
环境问题解决得好坏关系到中国的国家安全、国际形象、广大人民群众的根本利益,以及全面小康社会的实现。
保护环境是中国长期稳定发展的根本利益和基本目标之一,实现可持续发展依然是中国面临的严峻挑战。
企业在人类社会发展进程中同时扮演着保护环境与破坏环境的双重角色,负有不可推卸的环境责任。
硫是在铅之后最值得关注的油品质量指标,因为它可能引起癌症、心血管疾病等,尤其是它衍生的颗粒污染物会对呼吸道带来非常严重的影响。
联合国环境署一项在撒哈拉以南地区的研究显示,对炼油设备每投资30亿美元改善油品质量,可以带来250亿美元的健康效益。
“对于任何一个国家来说,这都是一项很好的投资。
”车用柴油质量升级,主要是通过柴油加氢来实现。
目前柴油加氢精制脱硫率为95%左右,如果达到国四硫含量要求(50ppm), 加氢精制脱硫率需要达到99%;而要生产国五硫含量标准的车用柴油(10ppm), 加氢精制脱硫率要达到99.9%以上。
如果再考虑提高十六烷值的问题, 则需要提高加氢的反应温度, 降低空速。
减压蜡油全液相加氢处理技术的工业应用
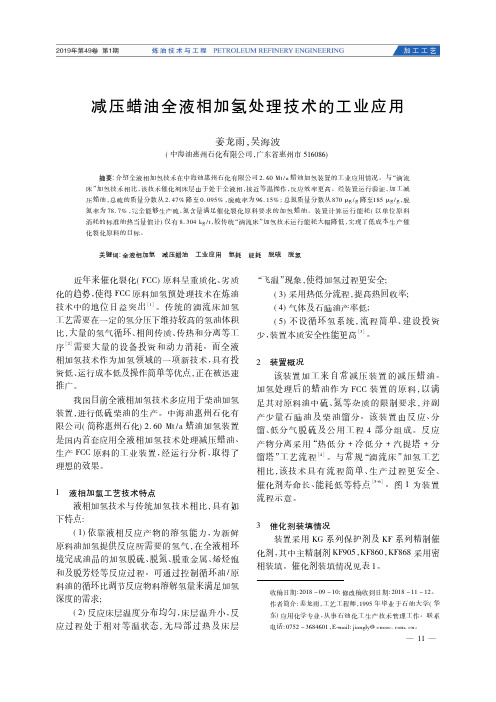
图 2 反应器升温曲线 Fig. 2 Curve of heating reactor
5 催化剂预硫化情况 9 月 28 日 16 ∶ 00,开始催化剂湿法预硫化。
因低分气中硫化氢含量非常高,低分气采取一次 通过操作,不循环回补充氢压缩机入口。考虑到 硫化过程中会生成大量水,开循环油泵后,生成水 会在 反 应 器 中 循 环,无 法 彻 底 带 出,随 着 温 度 升 高,可能会损坏催化剂。经与催化剂厂家及专利 商沟通,确定硫化期间不开循环油泵,采用提高反 应进料量来增加溶解氢的硫化方案。
减压蜡油全液相加氢处理技术的工业应用
姜龙雨,吴海波
( 中海油惠州石化有限公司,广东省惠州市 516086)
摘要: 介绍全液相加氢技术在中海油惠州石化有限公司 2. 60 Mt / a 蜡油加氢装置的工业应用情况。与“滴流 床”加 氢 技 术 相 比 ,该 技 术 催 化 剂 床 层 由 于 处 于 全 液 相 ,接 近 等 温 操 作 ,反 应 效 率 更 高 。 经 装 置 运 行 验 证 ,加 工 减 压蜡油,总硫的质量分数从 2. 47% 降至 0. 095% ,脱硫率为 96. 15% ; 总氮质量分数从 870 μg / g 降至185 μg / g,脱 氮率为 78. 7% ,完全能够生产硫、氮含量满足催化裂化原料要求的加氢蜡油。装置计算运行能耗( 以单位原料 消耗的标准油热当量值计) 仅有 8. 304 kg / t,较传统“滴流床”加氢技术运行能耗大幅降低,实现了低成本生产催 化裂化原料的目标。
下特点: ( 1) 依靠液相反应产物的溶氢能液相环 境完成油品的加氢脱硫、脱氮、脱重金属、烯烃饱 和及脱芳烃等反应过程。可通过控制循环油 /原 料油的循环比调节反应物料溶解氢量来满足加氢 深度的需求;
液相加氢技术的应用现状

C-NUM 液相加氢技术的应用对象也是航煤原料,这种原 料本身的性质和状态比常规的柴油等油料更好,加氢效果更 佳,整个精制过程的对循环系统、反应环境的要求比较小。在面 对航煤原料时,C-NUM 技术应用装置取消了循环油系统,有效 降低了循环泵可能带来的安全风险和成本、动力消耗;反应温 度为 245 ℃,压力为 3.5 MPa,氢油比在 12~13 范围内,属于较 为理想的反应过程。但如果面对的是原料性质、状态更差一些 的焦化柴油等柴油种类时,C-NUM 技术装置能否顺利加氢,能 否顺利完成精制反应获得符合标准的产品油,还需要进一步的 实践和验证分析。
目前来看,液相加氢技术始终存在氢气消耗量高、循环加 氢能耗较高、循环泵安全风险较高、催化剂使用寿命较低等问 题。想要改善这些问题需要通过特殊的设备装置,提高氢气与 原料油的混合程度,实现原料油中的氢气饱和状态[3]。想要达 到氢气饱和的理想状态,可能需要超重力、微米气泡等类型的 装置,使原料油中的氢气溶解量远超于实际需求量。如果能够 解决溶氢过程中的氢气饱和问题,就能够真正节约掉循环加氢 的装置和能耗,并且规避掉循环泵可能带来的安全风险和泄露 风险。这是液相加氢技术未来发展的主要方向,突破这一难题 就能够促进液相加氢技术的有效发展,扩大液相加氢技术的应 用范围。目前的液相加氢技术还不能代替气相滴流等技术的应 用,在原料油精制反应中还不能占据更大的主动性[4]。
LI Nong, LI Hai-feng, ZHAO Xin-quan, LI Guo-qi (Sinochem Changhe Technology Co., Ltd., Dongying 257335, China)
Abstract: Liquid phase hydrogenation technology is a process to maintain high hydrogen-oil ratio, which can effectively improve the heat transfer effect between phases, can improve the reaction eff iciency of oil, reduce the power consumption in the application process of diesel oil, kerosene and other feedstock oils, and produce more environmentally friendly clean oil. In the process of liquid phase hydrogenation, the amount of hydrogen dissolved in oil is the key problem, which affects the energy consumption and production eff iciency of the technology. This paper mainly analyzes the application status and application prospect of this technology.
气相加氢与液相加氢工艺在柴油加氢中的对比分析
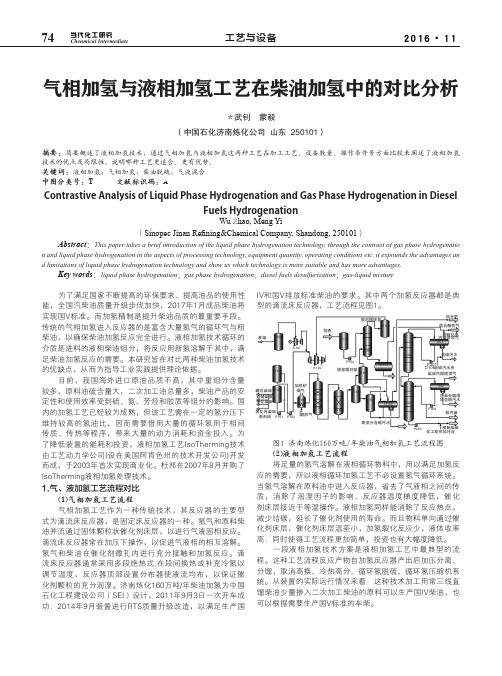
IV和国V排放标准柴油的要求。其中两个加氢反应器都是典 型的滴流床反应器,工艺流程见图1。
新氢 D108
K101
D102
贫液
D110
脱后循环氢 D107
K102
C101
P104 脱前循环氢
D105
D117
低分气
混合酸性气
汽脱提硫塔化顶氢气 D01
C201
含硫污水
P201 D106含硫污水来
柴油汽提塔顶气
2016·11
工艺与设备
75 当 代 化 工 研 究
Chenmical Intermediate
反应排气出装置 酸性水出装置
混合柴油
新氢
低分油至分馏塔 低分气出装置
低分油至分馏塔
图2 一段液相加氢流程 2.气、液加氢工艺主要设备对比
设备 热高压分离器 冷高压分离器 循环氢脱硫塔 循环氢压缩机入口
Fuels Hydrogenation
Wu Zhao, Meng Yi (Sinopec Jinan Refining&Chemical Company, Shandong, 250101) Abstract:This paper takes a brief introduction of the liquid phase hydrogenation technology, through the contrast of gas phase hydrogenatio
目前,我国海外进口原油品质不高,其中重组分含量 较多,原料油硫含量大,二次加工油总量多,柴油产品的安 定性和使用效率受到硫、氮、芳烃和胶质等组分的影响。国 内的加氢工艺已经较为成熟,但该工艺需在一定的氢分压下 维持较高的氢油比,因而需要借用大量的循环氢用于相间 传质、传热等程序,带来大量的动力消耗和资金投入。为 了降低装置的能耗和投资,液相加氢工艺IsoTherming技术 由工艺动力学公司(设在美国阿肯色州的技术开发公司)开发 而成,于2003年首次实现商业化。杜邦在2007年8月并购了 IsoTherming液相加氢处理技术。
柴油液相循环加氢技术的工业应用
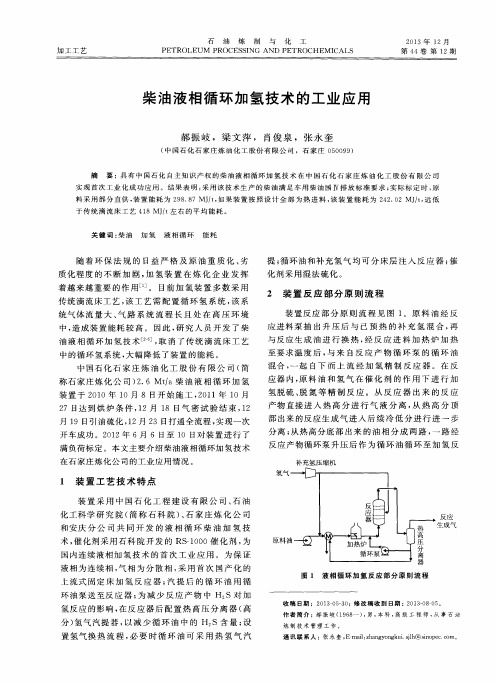
称石 家 庄炼 化 公 司 ) 2 . 6 Mt / a柴 油 液 相 循 环 加 氢
装 置于 2 0 1 0年 1 0月 8 日开 始 施 工 , 2 0 1 1年 1 O月
氢脱硫 、 脱 氮 等 精 制 反 应 。从 反 应 器 出 来 的反 应
产物直 接 进 入 热 高 分 进 行 气 液 分 离 。 从 热 高 分 顶 部 出来 的反应 生成 气 进 入后 续 冷 低 分 进 行 进 一 步 分离 ; 从 热高 分底 部 出来 的油 相 分 成 两 路 , 一 路 经 反应 产物 循环 泵 升压 后 作 为循 环油 循 环 至 加 氢 反
中的循 环 氢 系统 , 大幅 降低 了装 置 的能耗 。
中 国石化 石 家 庄 炼 油 化 工 股 份 有 限公 司 ( 简
至要 求 温 度 后 , 与 来 自反 应 产 物 循 环 泵 的 循 环 油 混合 , 一 起 自下 而 上 流 经 加 氢 精 制 反 应 器 。在 反 应器内, 原 料 油 和 氢 气 在 催 化 剂 的作 用 下 进 行 加
环油 泵送 至 反 应器 ; 为减少反应产物中 H S对 加
图1 液 相 循 环 加 氢 反 应 部 分原 则 流 程
反 应 生 成 气
氢反 应 的影 响 , 在 反 应 器后 配 置 热 高 压分 离 器 ( 高
分) 氢气 汽 提器 , 以 减少 循 环 油 中的 H S含 量 ; 设 置 氢气 换 热 流 程 , 必 要 时循 环 油 可 采 用 热 氢 气 汽
补 充 氢 压 缩 机
2 7日达 到烘 炉条 件 , 1 2月 1 8日气 密试 验 结 束 , 1 2
月 1 9日引 油 硫 化 , 1 2月 2 3日打 通 全 流 程 , 实 现 一 次
91.液相加氢技术现状及发展前景_王萌(1)

第42卷第4期 当 代 化 工 Vol.42,No.4 2013年4月 Contemporary Chemical Industry April,2013液相加氢技术现状及发展前景王 萌1, 金月昶2, 王铁刚2, 李国萍3(1. 辽宁石油化工大学,辽宁 抚顺 113001; 2. 中国寰球工程公司辽宁分公司,辽宁 抚顺 113006;3. 中国石油抚顺石化公司石油三厂,辽宁 抚顺 113001)摘 要:简要概述了液相加氢技术的发展现状,介绍了Iso Therming液相加氢技术、SRH液相循环加氢技术在加氢技术中的突破。
对两种技术的工艺流程及技术特点进行分析,并将液相加氢技术与常规加氢技术对比,得出液相加氢技术在工业生产中的突出优势及其发展前景。
关 键 词:液相加氢;柴油加氢装置;Iso Therming技术;能耗;循环泵中图分类号:TE 624 文献标识码: A 文章编号: 1671-0460(2013)04-0436-03Development Prospect and PresentSituation of the Liquid Phase Hydrogenation TechnologyWANG Meng1, JIN Yue-chang2, WANG Tie-gang2,LI Guo-ping3(1. Liaoning Shihua University, Liaoning Fushun 113001,China;2. HQC Liaoning Branch, Liaoning Fushun 113006,China;3. CNPC, Fushun Petrochemical Company No.3 Refinery . Liaoning Fushun 113001, China)Abstract: Present situation of the liquid phase hydrogenation technology was introduced. The breakthrough of IsoTherming liquid phase hydrogenation technology and SRH liquid circulation hydrogenation technology was discussed.The process flow and technical characteristics of two kinds of technology were analyzed. And they were comparedwith conventional hydrogenation technologies. The results show that the liquid phase hydrogenation technology hasprominent advantages and brilliant development prospect in industrial production.Key words: Liquid phase hydrogenation; Diesel hydrotreating unit; Iso Therming technology; Energy consumption;Circulation pump随着环保法规日益严格,全球燃料清洁化的总趋势是汽油向低硫、低烯烃、低芳烃、低苯和低蒸汽压发展;柴油向低硫、低芳烃(主要是稠环芳烃)、低密度和高十六烷值发展。
液相循环加氢技术
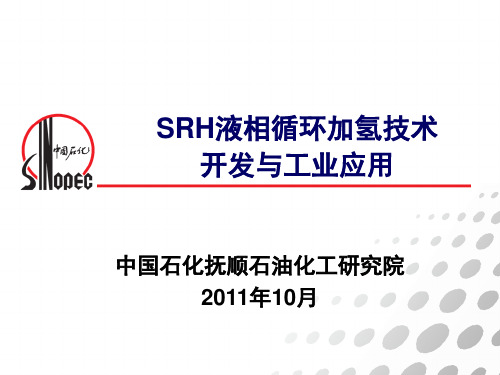
SRH液相循环加氢技术的开发背景
➢ 液相循环加氢稀释了原料中的杂质含量 –有机氮化物是加氢催化剂的毒物,对加氢脱氮、 加氢脱硫和加氢脱芳反应有明显的抑止作用。 ➢装置取消了循环氢压缩机系统、高压换热器、 高压空冷器、高压分离器、循环氢脱硫塔,热 量损失小,大幅度降低装置能耗。同时投资费 用和操作费用均低,是低成本实现油品质量升 级的较好技术。
SRH液相循环加氢技术 开发与工业应用
中国石化抚顺石油化工研究院 2011年10月
内容提要
一、SRH液相循环加氢技术的开发背景 二、SRH液相循环加氢技术开发 三、SRH液相循环加氢技术工业应用 四、结论
SRH液相循环加氢技术的开发背景
➢ 环保法规日益严格,柴油的硫含量标准在逐年修订,发 展和使用超低硫甚至无硫柴油是当今世界范围内清洁燃 料发展的趋势[1]。例如欧盟法规规定2009年车用柴油的 硫含量在10g/g以下,美国2006年限制车用柴油的硫含 量在15g/g以下。我国轻柴油规格标准GB252-2000对柴 油硫含量的要求是不大于2000g/g,城市车用柴油国家 标准GB-T19147-2003参照欧洲Ⅱ类标准制定,其硫含量 要求小于500g/g,2011年7月1日参照欧Ⅲ标准执行硫 含量小于350g/g。北京、上海等城市已率先执行参照 欧Ⅳ制定的京标C、沪Ⅳ标准,即要求硫含量小于 50g/g。为应对新排放标准柴油的生产,开发装置投资 低、操作费用低的柴油深度加氢技术非常必要。
SRH液相循环加氢技术的开发
➢ 研究结果表明: 压力提高气体溶解度提高 温度提高利于氢气溶解 温度提高不利于硫化氢、氨等气体的溶解
H 溶解度,m% 2
H2S 溶解度,m%
0.35
3.0MPa
0.30
4.0MPa
蜡油全液相加氢技术的工业应用

加工工艺石 油 炼 制 与 化 工PETROLEUMPROCESSINGANDPETROCHEMICALS2021年4月 第52卷第4期 收稿日期:2020 10 15;修改稿收到日期:2021 01 10。
作者简介:徐秋鹏,大学本科,工程师,从事加氢裂化、液相加氢、渣油加氢装置的生产管理工作。
通讯联系人:徐秋鹏,E mail:xuqp2@cnooc.com.cn。
¡>¢ £./vw4XYDE徐 秋 鹏(中海油惠州石化有限公司,广东惠州516086)摘 要:中海油惠州石化有限公司二期项目2.6Mt?a蜡油全液相加氢装置于2017年建成投产。
该装置采用杜邦公司的IsoTherming全液相加氢技术设计,是国内首套采用全液相加氢技术的蜡油加氢装置。
经过两年多的运转,该装置虽然经历多次开停工,但仍表现出较好的操作便利性和经济性。
装置运行2年多后的标定结果表明:对于硫质量分数大于2.7%、氮质量分数大于500 g?g的沙特中质原油减压蜡油原料,加氢蜡油产品的硫质量分数小于1000 g?g、氮质量分数小于100 g?g,均满足催化裂化装置对进料的要求;装置标定期间的综合能耗为274.63MJ?t,不但低于传统滴流床蜡油加氢装置,而且优于装置设计指标;装置整体运行情况达到设计要求。
关键词:全液相 蜡油 加氢 IsoTherming 循环油泵 综合能耗在现代炼油行业,加氢处理装置往往由于操作条件较为苛刻,所以装置投资很大。
为生产满足环保要求的清洁石油产品,世界各国炼油技术人员开发了很多加氢技术,以降低装置的投资和能耗。
其中液相加氢技术是近几年发展起来的一种突破性加氢技术。
在液相加氢技术中,反应是以液相进行的。
传统滴流床加氢技术需要大量的富氢气循环气与进料一起进入反应器,以确保反应所需的氢气被充分溶解至液相中。
液相加氢工艺技术反应部分不设置氢气循环系统,依靠液相产品循环以溶解足量的氢气,满足加氢反应的需要[1 2]。
- 1、下载文档前请自行甄别文档内容的完整性,平台不提供额外的编辑、内容补充、找答案等附加服务。
- 2、"仅部分预览"的文档,不可在线预览部分如存在完整性等问题,可反馈申请退款(可完整预览的文档不适用该条件!)。
- 3、如文档侵犯您的权益,请联系客服反馈,我们会尽快为您处理(人工客服工作时间:9:00-18:30)。
Isotherming®液相循环加氢技术的工业应用湖北省潜江市433100)摘要DuPont™IsoTherming®液相循环加氢技术通过循环加氢处理过的液流为反应器提供反应需要的氢气,同时也作为冷源维持反应的接近等温条件,从而避免不受控的裂化反应,降低轻组分的生成。
IsoTherming®液相加氢技术可以处理不同来源的柴油并在适宜的工艺条件下生产满足规格的清洁柴油产品。
化工有限公司1.0Mton/a柴蜡油加氢改质装置采用杜邦公司的IsoTherming®液相加氢技术,原料为直馏柴油,催化柴油,焦化柴油,焦化蜡油的混合物,在体积空速1.52 h-1,循环比3.54,反应器入口温度351.5℃的条件下,加工高硫原料时的脱硫率可以达到98%。
可以生产满足国Ⅲ柴油质量标准的清洁柴油。
同时该装置的长期稳定运行表明IsoTherming®液相循环加氢技术及其关键设备成熟可靠。
关键词:IsoTherming®;液相加氢;清洁柴油;1引言随着环保法规的日趋严格,车用柴油的硫含量标准逐年在修订。
我国普通柴油规格标准GB252-2011要求硫含量不大于2000μg/g,在2013年7月1日以后要求不大于350μg/g。
为应对满足越来越严格的排放标准,生产低硫和超低硫柴油已经成为炼油加氢装置的目标。
在传统的氢气循环加氢工艺过程中,为满足液相中反应所需要的氢,必须采用较大的氢油体积比,循环氢压缩机的投资占整个加氢装置成本的较大比例,换热系统能耗较大。
我公司经过考察采用杜邦专利的Isotherming® 液相循环加氢技术,该技术不需要设置氢气循环系统,依靠高温循环油泵循环一定比例的加氢产物至反应器顶部来携带进反应所需的溶解氢,同时高压设备数量也大大减小,占地空间也相应减小,是降低操作成本的同时实现油品质量升级的较好的技术【1】。
2装置概况该装置隶属于化工有限公司全液相柴蜡油加氢改质装置,设计能力100万吨/年,设计原料为直馏柴油,催化柴油,焦化柴油,焦化蜡油按比例的混合物,采用进口加氢精制催化剂,主要目的是为了改善公司原有催化裂化装置原料油的性质,同时对不同来源柴油原料进行加氢精制以满足本区域市场对柴油硫含量的环保要求。
IsoTherming®加氢工艺原理如图1所示,实际装置由一个保护反应器加一个主反应器组成。
装置于2012年4月18日开始催化剂预硫化,4月20日预硫化完成,整个催化剂硫化过程平稳,反应器床层温升在3℃以下。
4月24日一次投料开车成功,产品硫含量满足国III标准。
截止2013年3月30日止,整个装置运行平稳,关键工艺设备如进料泵,高温高压液相循环泵,新氢压缩机等稳定可靠。
收稿日期:2013-04-10*通讯联系人:图1 Isotherming®液相循环加氢工艺原理图Figure1. Isotherming® liquid phase hydrogenation process2.1 装置运行情况自装置2012年4月开车以来,由于受到原料供应紧张的影响,在上游常减压装置中原油比例小,不得不掺炼M100、180#、280#、380#燃料油,同时直馏柴油产量少,相应的作为加氢装置进料的四种柴油质量比设计指标均有较大幅度的降低,各组分密度明显增加,硫含量大幅升高。
几组装置的典型操作条件和原料/产品分析指标见表1和表2。
根据工厂的生产调度安排及本区域产品的市场需要,大部分操作时间内装置反应区间操作温度和操作压力均低于设计值。
如表1数据1所示,当反应器入口温度只有315℃时,脱硫率仍然达到97.7%,产品硫含量满足国III 标准。
当加工高硫原料(数据2)时,在适当降低装置进料量的同时,产品中硫含量仍能够满足国III 标准,脱硫率可以达到98%,同时装置的操作温度和操作压力仍有较大的提升空间。
当原料硫含量过高(数据3所示),并且其中重组分含量大大增加时,对装置的脱硫率有一定影响,同时由于循环比的降低,导致脱硫率降低到90.7%表1柴油混合进料不同的操作条件Table1 Operation condition for different mixed diesel feed 项目数据1数据2数据3进料量, t/h10271.4100预反应器2.19 1.52 2.10入口315351.5342出口317.5354345反应器入口压力, Mpa 8.98.88.8主反应器0.710.490.68入口317353345出口323359352.5反应器入口压力, Mpa 8.68.38.2循环比 (体积比) 3.37 3.54 2.37原料比例,直柴/催柴/焦柴/蜡油25/46/29/036/21/43/025/10/30/35反应温度,℃反应器温度,℃空速, h -1空速表2柴油混合进料及产品的分析Table2 Analysis results of diesel feed and product项目原料产品原料产品原料产品密度,,g/cm3872.7849.5881.7858.3895.7858.2硫含量,μg/g 720016715159302173511605馏程,℃初馏点19719518318648618510%22821522021522021450%27826428326531626990%339332349340>40033995%351344361355357闪点,℃7165腐蚀1b 1b 1b凝点,℃-8<-8<-814<-8色度8<2.0 4.0<2.0>8.0水白色脱硫率,%97.798.090.7数据1数据2数据32.2影响因素反应温度对产品硫含量的影响如图2所示,在进料流率,进料性质和其他操作条件稳定的情况下,和传统的气体循环加氢工艺一样,随着反应温度的升高,柴油产品中的硫含量不断降低,当反应温度超过360℃时,随着反应温度的进一步升高,产品质量改善的增益将有所降低。
20030040050060070080090010008000900010000110001200013000140001500016000330.0340.0350.0360.0370.0380.0精制柴油硫含量,μg /g 原料硫含量,μg /g 反应温度,℃原料中硫含量精制柴油硫含量图2. 反应温度对产品硫含量的影响Figure2. The effect of reaction temperature on sulfur content of product图3显示了反应器温升随着装置进料量和平均床层温度的影响,可以看出,根据不同的进料量和操作温度,反应器1的温升在1~3℃之间,反应器2的温升在4~8℃之间,并且总进料量对反应器温升的影响要比操作温度的变化显著。
相对于传统的氢气循环加氢工艺,反应温升较低,操作平稳,容易控制。
24681050100150200250300350400温升,℃反应器平均床层温度,℃总进料量平均床层温度反应器1的温升反应器2的温升图3总进料量和平均床层温度对反应器温升的影响Figure3. The effect of Total feed and W ABT on the ΔT of reactor3结论1. 工业生产实践表明采用Isotherming®液相循环加氢技术的装置,可以有效的对不同来源的柴油原料及其混合物进行加氢脱硫,相对于传统的气体循环加氢精制工艺,减少了高压设备的投资,降低了操作成本和操作复杂性。
2. Isotherming®液相循环加氢工艺所采用的高温高压液相循环泵性能稳定可靠,能够满足装置的长周期运行;3. 体积空速2.19h -1,循环比3.37,反应器入口温度315℃的条件下,脱硫率可以达到97.7%;体积空速1.52 h -1,循环比3.54,反应器入口温度351.5℃的条件下,加工高硫原料时的脱硫率可以达到98%;体积空速2.1 h -1,循环比2.37,反应器入口温度342℃时,加工高硫原料的脱硫率为90.7%;4. 根据近一年的生产实践,进料组分可以根据生产调度和区域市场需求灵活调整,大大增加了操作弹性;5. 当其他操作条件保持稳定时,提高反应温度可以进一步降低精制柴油产品中的硫含量,当温度超过360℃时,继续升高温度时,产品硫含量改善的幅度降低。
6. 随着进料量和平均床层温度的变化,反应系统的总温升在5~8℃之间变化,相对于传统的气体循环加氢精制工艺,床层温升大大降低,避免了飞温带来的催化剂失活和产品质量波动,提高了装置运行的可靠性。
参考文献:[1] A ntony Stanislaus, Abdulazeem Marafi, Mohan S. Rana . Recent advances in the science and technology of ultra low sulfur diesel (ULSD) production [J]. Catalyst Today, 2010, 153:1-68.COMMERCIAL APPLICATION OF ISOTHERMING® LIQUID-PHASEHYDROPROCESSING TECHNOLOGYBai Danjiang Wen Bin Zheng Tao(Jinao(Hubei) Science & Technology Chemical Industry Co., Ltd. Hubei Qianjiang 433100)Abstract The heart of DuPont™IsoTherming® liquid-phase hydroprocessing technology is the ability to provide hydrogen necessary for the reactions using a liquid recycle stream. The liquid phase also acts as a heat sink for the exothermic reactions. The reactor operates closer to isothermal conditions, which reduces uncontrolled cracking reactions and thus lowers light ends make. IsoTherming® liquid-phase hydroprocessing technology can treat diesel from different sources and produce clean diesel within specifications under proper process conditions. Hydrotreater of Jinao(Hubei) Science & Technology Chemical Industry Co., Ltd. adopts DuPont™IsoTherming® liquid-phase hydroprocessing technology. The feed is composed of straight run diesel, light cycle oil, light coker diesel and heavy coker gas oil in proportion. Under the process condition of volumetric space velocity of 1.52h-1, recycle ratio of 3.54, reactor inlet temperature of 351.5℃, the percentage of desulphurization can reach 98% when treating high-sulfur feed. The clean diesel product can meet the specification of Standard Three. The stable operation of unit indicates the high reliability of IsoTherming® liquid-phase hydroprocessing technology as well as the key equipments.Keywords IsoTherming®,liquid-phase hydroprocessing, clean diesel。