焦炉装煤出焦烟气治理工程工艺原理介绍
焦炉烟尘无组织排放及其治理

焦炉烟尘无组织排放及其治理一、焦炉烟尘无组织排放状况焦炉在装煤、炼焦、推焦与熄焦过程中,向大气环境排放大量煤尘、焦尘及有毒有害气体(以下统称烟尘)。
其污染量国外作过统计,吨焦烟尘量达1kg 之多,这个数量对于一个日产近6000t焦炭的焦炉组,每天就有将近6t烟尘排放到大气中,造成对人与环境的严重危害。
焦炉烟尘含有多种污染物,主要是固体悬浮物(TSP)、苯可溶物(BSO)及苯并芘(BaP)等。
烟尘逸出后在大气温度和压力下,迅速冷凝并附着在悬浮微粒表面,随着呼吸微粒进入人体内并沉积于肺部。
目前广泛认为烟尘中BSO和BaP对人体是致癌物,长期持续地吸入含致癌物的微粒,能引发肿瘤。
有研究报告指出,在焦炉区域作业的工人患呼吸系统癌症的危险性比其他钢铁工人高,就焦化而言,炼焦工肺癌或慢性阻塞性肺病,在冶金企业中,是一种仅次于矽肺的职业病。
从70年代起,随着环保要求的不断提出,焦炉烟尘污染与治理技术已引起各发达国家的重视,并相继在焦炉上运用,取得了明显成效。
国内起步较晚,起初除宝钢等少数几家引进消化国外技术,上了环保装备外,国内焦炉环保治理软件、硬件还未得到普及应用,成为当前和今后较长一段时间内冶金行业环境保护亟待解决的重大课题和紧迫任务。
党的十八大以来,以习近平同志为核心的党中央把生态文明建设作为统筹推进“五位一体”总体布局和协调推进“四个全面”战略布局的重要内容,谋划开展了一系列根本性、长远性、开创性工作,推动生态文明建设和生态环境保护从实践到认识发生了历史性、转折性、全局性变化。
先后下发了《中共中央国务院关于全面加强生态环境保护坚决打好污染防治攻坚战的意见》、《炼焦化学工业污染物排放标准》(GB 16171-2012)等文件和法律法规,为污染防治指明了方向、确定了目标。
二、焦炉烟尘污染源分布焦炉烟尘污染源主要分布于炉顶、机焦两侧和熄焦,全部烟尘还应包括加热系统燃烧废气。
按生产过程可把烟尘分为两种:炼焦过程中污染源和机械操作过程污染源。
焦化废气治理
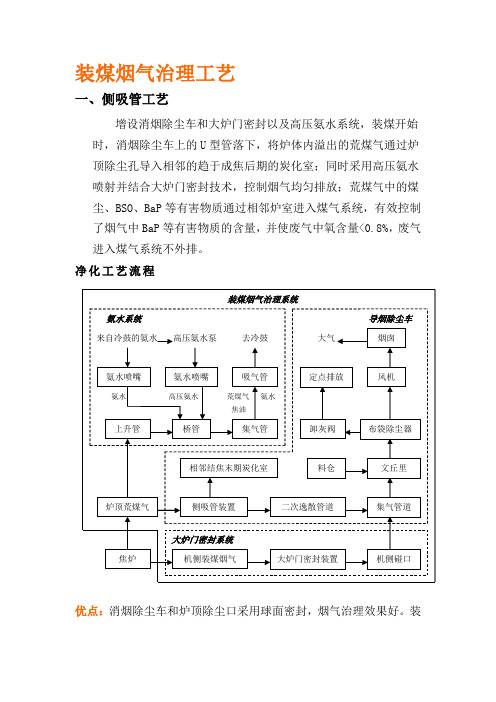
装煤烟气治理工艺一、侧吸管工艺增设消烟除尘车和大炉门密封以及高压氨水系统,装煤开始时,消烟除尘车上的U型管落下,将炉体内溢出的荒煤气通过炉顶除尘孔导入相邻的趋于成焦后期的炭化室;同时采用高压氨水喷射并结合大炉门密封技术,控制烟气均匀排放;荒煤气中的煤尘、BSO、BaP等有害物质通过相邻炉室进入煤气系统,有效控制了烟气中BaP等有害物质的含量,并使废气中氧含量<0.8%,废气进入煤气系统不外排。
净化工艺流程优点:消烟除尘车和炉顶除尘口采用球面密封,烟气治理效果好。
装煤烟气可独立治理,装煤时产生的荒煤气是通过U型管导入焦炉煤气系统,而非燃烧后处理,可为您增加经济效益。
缺点:对焦炉炉况和炉顶操作工的要求比较严格,要做到“三通一活”,及上升管、桥管、集气管要及时清理,保持通畅,翻板阀要转动灵活。
需加装高压氨水系统和集气管压力自动调节系统。
二、燃烧法二合一工艺此工艺的特点是装煤烟气采用燃烧法,燃烧后的烟气与推焦烟气都进入同一套地面站除尘系统处理,而根据装煤烟气和推焦烟气连接汇合的方式不同,又可分为下面三种方案:第一种方案:装煤烟气和推焦烟气各用一套管路,两套管路在炉间台处汇合。
装煤除尘系统由移动和固定装置两部分组成。
移动装置即消烟除尘车。
固定装置包括:机侧炉顶的集气小罩、炉顶集气管道、煤气系统、装煤/出焦二合一集气总管、地面除尘站的除尘设备、风机、烟囱等。
装煤除尘过程为:首先,侧装煤车行走至待装煤的炭化室定位,炉顶烟尘收集车待排气孔盖打开后,将导烟口集气罩与炭化室中心对正,同时向地面除尘系统发出电讯号,风机开始高速运行。
车载煤气燃烧系统与炉顶煤气管道连接,装煤烟气从机侧车载碰口和导烟口集气罩被吸入,缓冲、配风、燃烧、冷却后,再经车载碰口导入炉顶集气管道内,再由装煤、出焦二合一集气总管送至地面站除尘系统净化后,由风机经烟囱排至大气。
地面除尘系统接受信号,风机进入低速运行状态。
优点:无需加装高压氨水系统。
焦炉废气回配的原理和作用
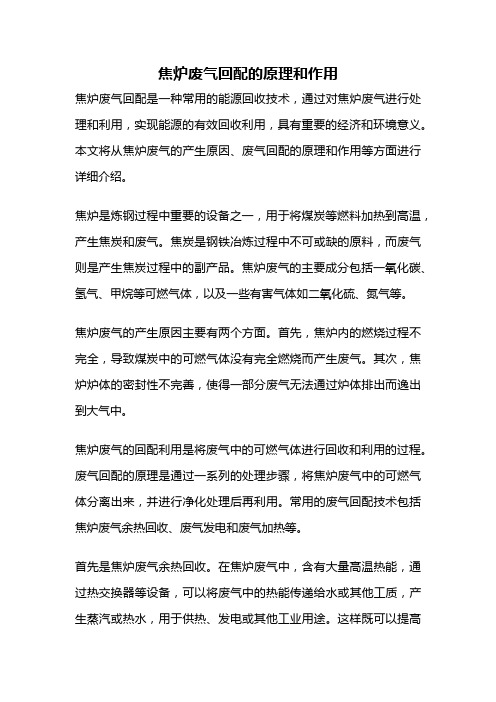
焦炉废气回配的原理和作用焦炉废气回配是一种常用的能源回收技术,通过对焦炉废气进行处理和利用,实现能源的有效回收利用,具有重要的经济和环境意义。
本文将从焦炉废气的产生原因、废气回配的原理和作用等方面进行详细介绍。
焦炉是炼钢过程中重要的设备之一,用于将煤炭等燃料加热到高温,产生焦炭和废气。
焦炭是钢铁冶炼过程中不可或缺的原料,而废气则是产生焦炭过程中的副产品。
焦炉废气的主要成分包括一氧化碳、氢气、甲烷等可燃气体,以及一些有害气体如二氧化硫、氮气等。
焦炉废气的产生原因主要有两个方面。
首先,焦炉内的燃烧过程不完全,导致煤炭中的可燃气体没有完全燃烧而产生废气。
其次,焦炉炉体的密封性不完善,使得一部分废气无法通过炉体排出而逸出到大气中。
焦炉废气的回配利用是将废气中的可燃气体进行回收和利用的过程。
废气回配的原理是通过一系列的处理步骤,将焦炉废气中的可燃气体分离出来,并进行净化处理后再利用。
常用的废气回配技术包括焦炉废气余热回收、废气发电和废气加热等。
首先是焦炉废气余热回收。
在焦炉废气中,含有大量高温热能,通过热交换器等设备,可以将废气中的热能传递给水或其他工质,产生蒸汽或热水,用于供热、发电或其他工业用途。
这样既可以提高能源利用效率,又可以减少对传统能源的消耗,具有显著的经济和环境效益。
其次是废气发电。
通过将焦炉废气中的可燃气体收集起来,经过净化处理后送入燃气发电机组,利用内燃机或燃气轮机发电,将废气中的热能转化为电能。
这种方式不仅可以实现废气的回收利用,还可以为工厂提供可靠的电力供应,降低生产成本。
废气回配还可以用于焦炉炉体的加热。
将焦炉废气经过净化处理后,再送入焦炉炉体中,用于加热煤炭,提高炉温。
这种方式不仅可以减少燃料的消耗,还可以降低炉温的不均匀性,提高焦炭的质量和产量。
焦炉废气回配的作用主要有两个方面。
一方面,废气回配可以实现能源的有效利用,提高能源利用效率,降低能源消耗。
焦炉废气中含有大量的可燃气体和高温热能,通过回收利用,可以将这些能源再次利用,减少对传统能源的依赖,降低能源成本。
焦化废气治理.doc
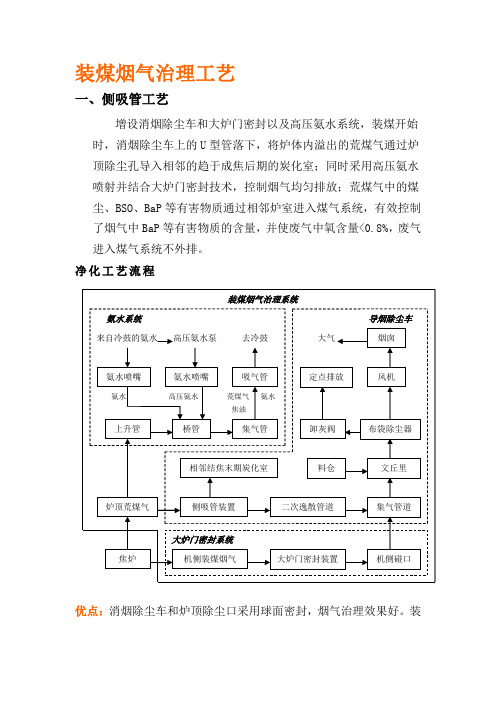
一、侧吸管工艺
增设消烟除尘车和大炉门密封以及高压氨水系统,装煤开始时,消烟除尘车上的U型管落下,将炉体内溢出的荒煤气通过炉顶除尘孔导入相邻的趋于成焦后期的炭化室;同时采用高压氨水喷射并结合大炉门密封技术,控制烟气均匀排放;荒煤气中的煤尘、BSO、BaP等有害物质通过相邻炉室进入煤气系统,有效控制了烟气中BaP等有害物质的含量,并使废气中氧含量<0.8%,废气进入煤气系统不外排。
优点:采用燃烧法,装煤、推焦分别独立运行,可操作性较强,烟气处理效果好。
缺点:一次性投入较大。
推焦烟气治理工艺
焦炉推焦烟气治理一般分为以下几个部分:
1).用以收集推焦时产生的烟尘的集气大罩。
2).用以将烟气引至地面站的集气干管。
3).用以连接集气大罩和集气干管的连接转换装置。
4).用以处理烟气的除尘设备。
优点:无需加装高压氨水系统。装煤烟气在燃烧导烟车中充分燃烧,再进入除尘系统,燃烧后的烟气经除尘系统处理后可完全达标排放。为保证燃烧充分,炉顶配备煤气系统,将净化后的煤气加入燃烧导烟车的套筒处配合燃烧。炉顶设置一套集气管路,装煤烟气经燃烧后经过燃烧导烟车的碰口进入炉顶集气管道,最终被引入地面站。推焦烟气经集气大罩碰口进入燃烧导烟车的冷却系统后也进入炉顶集气管道。省去了一套焦侧集气管道以及管道支架。
优点:无需加装高压氨水系统。装煤烟气在燃烧导烟车中充分燃烧,再进入除尘系统,燃烧后的烟气经除尘系统处理后可完全达标排放。为保证燃烧充分,炉顶配备煤气系统,将净化后的煤气加入燃烧导烟车的套筒处配合燃烧。装煤烟气和推焦烟气各配备一套集气管路,两套管路最终在进入地面站除尘系统前汇合,所以装煤和推焦除尘系统在地面站设备正常运行的情况下可分别独立运行。
净化工艺流程
焦炉侧装煤高压氨水消烟装煤冒烟及氧含量高的原因

装煤冒烟及氧含量超高停电捕问题分析报告一、氧含量超高危害。
仪表王玉平。
1、煤气中氧含量超过2.0%,在经过电捕时,极有可能导致发生爆炸事故,根据相关规定,要求氧含量超过1%报警,达到2%立即自动切断电捕电源。
2、频繁停电捕会导致焦油回收率降低。
3、未捕获焦油会导致后续工段管道、设备、仪表等堵塞,影响安全稳定生产。
3、由于停电捕后无法继续测量煤气含氧量,在启动电捕时容易发生事故。
二、高压氨水除尘原理及过程。
1、原理。
炭化室装煤时集气管压力达到300~400pa,使大量荒煤气外逸。
利用高压氨水在桥管氨水喷头的喷洒,在桥管内喷洒区域的后方及上升管内产生较大的负压,并在炭化室内靠近上升管底部区域形成负压,使荒煤气及烟尘由炭化室经上升管、桥管、吸入集气管内,以避免荒煤气从装煤口处溢出。
2、动作过程。
煤饼进入炭化室500mm时,装煤车司机使用对讲机通知导烟车司机开启高压氨水。
导烟车司机接到通知后马上手动开启N-1号、N号、N+2号炭化室高压氨水阀门。
阀门开启后,风机中控电脑会检测到高压氨水流量,在高压氨水控制投入自动状态时,当检测到流量上升到临界点(可调参数,目前定位7m3/h)后,默认开始装煤,压力在规定时间内(可调参数,目前定位35s)由低压0.6MPa上升到高压(可调参数,2.5MPa-3.3MPa),保持一定时间(可调参数)后,为了避免烟气减少导致过多空气吸入,降到中压(可调参数),装煤完成关闭炉门后,关闭高压氨水,风机中控电脑检测到高压氨水流量降低至临界点后,默认装煤完毕,高压氨水压力降到低压,做好下次装煤准备,完成整个控制过程。
装煤过程中,在高压氨水吸力作用下,一部分烟尘经N号炭化室上升管进入集气管,另一部分经N号炭化室导烟孔由导烟车分别导入N-1、N+2号炭化室,经过N-1、N+2号炭化室上升管进入集气管(边炉除外)。
三、影响消烟效果因素。
1、高压氨水喷头。
根据我公司实际情况,每产生100Pa吸力,需要大概2.5公斤高压氨水压力。
焦炉废气回炉燃烧技术在焦炉工艺调整中的应用

焦炉废气回炉燃烧技术在焦炉工艺调整中的应用随着我国煤炭工业的发展,焦化行业作为重要的煤炭深加工环节,其能源消耗和环境污染问题备受关注。
在焦炉生产过程中,产生大量焦炉废气,若直接排放,会造成严重的环境污染。
研究和应用焦炉废气回炉燃烧技术,对于减少环境污染、提高炉石燃烧利用率、节能减排具有重要的意义。
一、焦炉废气回炉燃烧技术原理焦炉废气回炉燃烧技术是指将焦炉排放的废气通过处理后,再次回炉进行燃烧利用的技术。
其原理主要包括焦炉废气收集、废气净化、废气预热、废气回炉燃烧等过程。
通过提高废气的回炉温度和压力,使其重新参与炉内燃烧过程,有效提高炉内煤气利用率和热效率,达到节能减排的目的。
二、焦炉废气回炉燃烧技术的优势1. 减少污染排放。
采用焦炉废气回炉燃烧技术,可以减少焦炉排放对环境造成的污染,改善空气质量,保护生态环境。
2. 提高能源利用效率。
焦炉废气回炉燃烧技术能够充分利用焦炉废气中的热能,提高能源利用效率,降低企业生产成本,促进技术升级和产业结构调整。
3. 降低对外能源依赖。
通过提高炉内煤气利用率,减少外部能源消耗,特别是对于我国资源短缺、外部依赖度较高的煤炭行业,具有重要的战略意义。
三、焦炉废气回炉燃烧技术在焦炉工艺调整中的应用1. 技术改造升级。
针对现有的焦炉工艺流程,需要对设备进行改造升级,以适应焦炉废气回炉燃烧技术的要求,包括焦炉废气收集系统、废气净化系统、废气预热系统等。
2. 运行优化调整。
在实际生产过程中,需要对焦炉废气回炉燃烧工艺进行运行优化调整,包括废气回炉燃烧过程的温度、压力、气流速度、气氛控制等参数的优化。
3. 系统监测控制。
建立完善的焦炉废气回炉燃烧技术监测控制系统,对废气回炉燃烧过程进行实时监测和控制,确保工艺稳定运行,提高炉内煤气利用率和热效率。
四、焦炉废气回炉燃烧技术的发展趋势1. 技术集成创新。
未来焦炉废气回炉燃烧技术将向多技术集成方向发展,包括化学吸收、膜分离、高效热交换等技术的创新应用,提高系统能源利用效率和净化效果。
焦炉装煤过程冒烟原因及解决方法
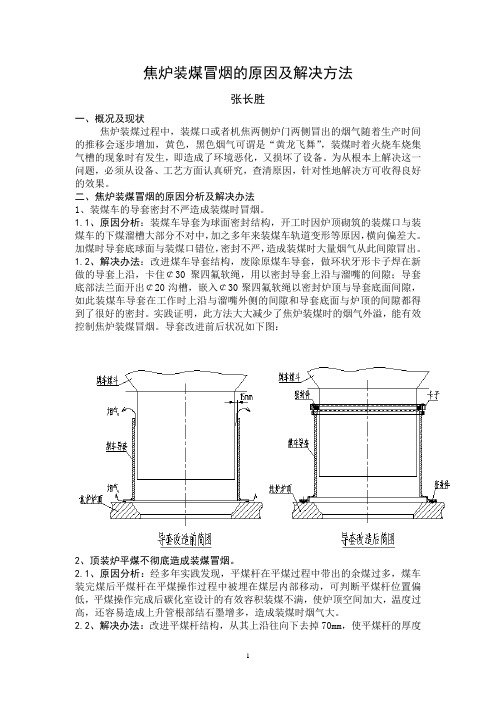
焦炉装煤冒烟的原因及解决方法张长胜一、概况及现状焦炉装煤过程中,装煤口或者机焦两侧炉门两侧冒出的烟气随着生产时间的推移会逐步增加,黄色,黑色烟气可谓是“黄龙飞舞”,装煤时着火烧车烧集气槽的现象时有发生,即造成了环境恶化,又损坏了设备。
为从根本上解决这一问题,必须从设备、工艺方面认真研究,查清原因,针对性地解决方可收得良好的效果。
二、焦炉装煤冒烟的原因分析及解决办法1、装煤车的导套密封不严造成装煤时冒烟。
1.1、原因分析:装煤车导套为球面密封结构,开工时因炉顶砌筑的装煤口与装煤车的下煤溜槽大部分不对中,加之多年来装煤车轨道变形等原因,横向偏差大。
加煤时导套底球面与装煤口错位,密封不严,造成装煤时大量烟气从此间隙冒出。
1.2、解决办法:改进煤车导套结构,废除原煤车导套,做环状牙形卡子焊在新做的导套上沿,卡住¢30聚四氟软绳,用以密封导套上沿与溜嘴的间隙;导套底部法兰面开出¢20沟槽,嵌入¢30聚四氟软绳以密封炉顶与导套底面间隙,如此装煤车导套在工作时上沿与溜嘴外侧的间隙和导套底面与炉顶的间隙都得到了很好的密封。
实践证明,此方法大大减少了焦炉装煤时的烟气外溢,能有效控制焦炉装煤冒烟。
导套改进前后状况如下图:2、顶装炉平煤不彻底造成装煤冒烟。
2.1、原因分析:经多年实践发现,平煤杆在平煤过程中带出的余煤过多,煤车装完煤后平煤杆在平煤操作过程中被埋在煤层内部移动,可判断平煤杆位置偏低,平煤操作完成后碳化室设计的有效容积装煤不满,使炉顶空间加大,温度过高,还容易造成上升管根部结石墨增多,造成装煤时烟气大。
2.2、解决办法:改进平煤杆结构,从其上沿往向下去掉70mm,使平煤杆的厚度由原来的240mm变为170mm,这样就产生了原平煤杆由于强度降低而下挠的问题,可重新设计一套平煤杆,其前段侧壁厚度由原来的10mm、8mm不等改为等厚度14mm;中段侧壁厚度由原来的10mm、14mm不等改为等厚度20mm;尾段侧壁厚度由原来的20mm改为30mm,其宽度和两侧面斜度按原设计不变。
捣固焦炉装煤外逸烟气回收新技术

捣固焦炉装煤外逸烟气回收新技术随着工业的不断发展和生产技术的不断提高,煤炭成为了眼下工业生产中不可或缺的能源。
然而,焦化生产却不可避免的会产生大量的废气。
其中装煤过程中的外逸烟气更是成为了环境治理的难点之一。
为了降低煤炭焦化过程中的环境污染,于是一种全新的技术应运而生,那就是捣固焦炉装煤外逸烟气回收技术。
一、捣固焦炉装煤原理捣固焦炉装煤是指焦炉的煤气化过程是支持段结构,煤粉是以螺旋输送器的方式,通过一个连续的、密封的、锥形螺旋通道输入到配合的焦炉结构中。
新煤粉在喷嘴的作用下与工艺气体混合到喷头前方的工作腔中。
其中,喷嘴收缩形状的特性使得煤气混合更加均匀,并且喷嘴旋转有利于煤粉在炉膛中均匀分布,加快煤粉在炉膛中的燃烧。
二、外逸烟气回收的技术实现为了降低装煤外逸烟气的排放,以往方法是采用启封炉门,在换炉期间人工把炉内废气排放到大气中的方法。
但这种方法会在很大程度上污染环境,并且破坏炉体内部的均匀气流,影响生产效率。
而新型捣固焦炉装煤外逸烟气回收技术则采用了先进的技术手段与设备,包括以下三个方面:1、煤气净化器为了收集炉内喷煤后残余的废气,所产生的烟灰等污染物,需要在煤气净化器中进行物理或化学处理,达到净化废气的目的。
净化器的设计原则是要减少废煤气中的悬浮颗粒、二氧化硫、氯和其他氧化物等有害物质,使其能够安全的进入排放管道。
2、煤气回收系统为了能够回收并利用废气,需要在煤气回收系统中进行集中处理。
系统主要由冷却、脱水和除尘三个步骤组成。
其中,冷却工序是为了降低煤炉排放的气体温度,减轻除尘设备的负担。
而脱水和除尘工序则是为了从煤气中分离出最终的产品气体。
3、煤气利用装置为了让处理好的废气得到更好的利用,可以采用生热设备将煤气进行再利用。
生热设备可以将煤气与其他可燃材料进行混合后,通过特定的反应器产生热能。
这样既能降低焦炉产生的废气的排放问题,又能通过热能的再利用加速生产和节约能源。
三、技术的实际效果到目前为止,捣固焦炉装煤外逸烟气回收技术已经被广泛的应用到了煤化学工业中。
- 1、下载文档前请自行甄别文档内容的完整性,平台不提供额外的编辑、内容补充、找答案等附加服务。
- 2、"仅部分预览"的文档,不可在线预览部分如存在完整性等问题,可反馈申请退款(可完整预览的文档不适用该条件!)。
- 3、如文档侵犯您的权益,请联系客服反馈,我们会尽快为您处理(人工客服工作时间:9:00-18:30)。
焦炉装煤出焦烟气治理工程工艺原理介绍
一、装煤烟气治理
新导烟消烟除尘车,车上装有侧吸管装置、机侧大炉门烟气净化系统、最后两孔咽气净化系统。
侧吸管装置,将炉体内溢出的荒煤气导入相邻的趋于成焦后期的炭化室,机侧侧导管装置,将大炉门让咽气逸咽气引入车载机侧大炉门咽气净化系统处理;同时采用高压氨水喷射并结合顺序装煤技术,控制咽气均匀排放,荒煤气中达的BSO 、BAP 等有害物质通过相邻炉室入煤气系统,有效控制了咽气中BAP 等有害物质的含量并使废报中氧含量小于0.8,废气进入煤气系统不外排放,装煤烟气治理净化工艺流程如下:
二、出焦烟气治理
1#、2#焦炉新增拦焦车热浮力集气大罩两套,拦焦车集气罩碰口两套,出焦烟气集气干管一套,集气干管碰上接口阀;管道支架、管道桁架、风机电机,夜力偶合器、烟筒。
1#、2#焦炉装煤出焦烟气治理系统用除尘系统一套,二次除尘装置一套,地面站控制室一套、风机电机基础一套、除尘系统基础一套、管道支架基础一套、电气系统、仪表控制系统等。
三、出焦烟治理工艺流程
拦焦机二次对位后,使拦焦机上的两个矩形排烟口对接,套筒与焦侧的固定接口阀接通并先于推焦杆动30秒钟向地面除尘系统发出信号,通风机由变濒器控制,开始由低速向高速运行,然后推焦杆运行推焦,出焦时产生的大量阵发性高温含尘烟气,在焦碳热浮力及风机的作用下收入装置在拦焦车上的型吸气罩,然事通过接口翻版阀等特殊的转换设备,使烟气进入集尘干管,送入预除尘系统对较的大颗粒进行相分离,一级处理烟气进入脉中袋式除尘器运行净化,烟气从除尘器中部进风管进集灰斗;气流回转180度进入过滤袋中部箱体,上升气流流速比较均匀,对滤袋无强气流冲击,延长滤袋使用寿命,净化后燃气经通风机,烟排入大气。
出焦烟气治理流程图:
出焦系统设计指标
高压氨水喷射
上升管桥管
荒煤气 除尘孔逸散烟气 侧吸管 相邻炉煤气系统 大炉门逸蒸烟气 大炉门密封装
二次烟气捕集装置 导烟除尘车除尘孔 排空
拦焦棚焦气罩 地面除尘系统 引风机 熄焦车 排放
项目工艺参数处理烟气量190000-----240000NM3/H
烟气入口温度最高220C(除尘器入口处)入口烟气含尘量8--20G/NM3(MAX)
系统装机容量450KW
除尘系统阻力5500PA
滤袋使用寿命18个月
出口烟气含尘量50MG/NM3
烟尘捕集率>=90%
除尘效率>=99.9%。