热处理检验方法和规范修订稿
AMS_2759-2C_低合金钢零件的热处理

3.3.1 零件类型:
热处理操作人员应确定零件类型。 1 类:热处理后所有表面机加余量大于等于 0.020 英寸(0.51mm)的零件以及具锻造,铸造,
热轧表面,热处理后须机加掉的零件。除非被告知零件所有表面都留有 0.020 英寸 (0.51mm)加工余量,否则热处理操作人员应将其视为无加工余量并按相应的 2、3 或 4 类另件进行控制。
4.1.1 收试验:
除 AMS 2759 规定的试验项目外,对每炉批零件应作(3.5.1 节)表面污染试验,假如 碳势为自动控制并有指示或记录,则可代之以 4.2 节规定的办法定期进行表面污染 检测。
4.1.2 试生产试验:
除 AMS 2759 规定的试验项目外,在热处理生产前应对每个炉子,每种使用的气氛 以及 B 级气氛在小于等于 0.40%和大于 0.40% 二种碳势情况下进行(3.5.1 节)的 表面污染试验。
-2-
AMS 2759/2C
3.3.1.1 假如不能确定另件的类型,则按 3 类另件处理。
3.3.2 气氛级别:
A 级:氩气、氢气、氦气、氮气、氮-氢混合气体、真空或中性盐浴。不允许使用由 氨气分解成的氮气。
B 级:吸热型、放热型或含碳的氮基气氛(见 8.2 节)。
C 级:空气或燃烧产品(氧化性气氛)
-3-
AMS 2759/2C
3.4.4 不完全退火:在硬化之前,将零件加热到 1150-1250℉(621-677℃)保温至表 4 规定的时间,然后冷却至室温。9Ni-4Co 类钢零件应按表 2 规定采用不完全退火。
3.4.5 硬化前的应力释放:零件在硬化前将其加热到 1000-1250℉(538-677℃)保温至不 少于表 4 规定的时间,然后冷却至室温。
热处理件表面检验验收标准

热处理件表面质量检验验收标准一、目的为保障产品的质量,建立和规范热处理件表面质量的检验方法,对热处理件产品生产、出厂或外购的外观检验提供科学、客观的依据,以保证检验结果一致性、全面性及准确性,同时防止材料表面缺陷影响后道工序的生产及品质,特制定本标准。
二、适用范围本标准适用于湘重公司生产及外购或委外加工的热处理件表面质量检验及验收三、规范性引用文件下列文件中的条款通过本标准的引用而成为本标准的条款。
凡是注日期的引用文件,其随后所有的修改单(不包括勘误的内容)或修订版均不适用于本标准,然而,鼓励根据本标准达成协议的各方研究是否可使用这些文件的最新版本。
凡是不注日期的引用文件,其最新版本适用于本标准。
GB/T15822 磁粉探伤方法GB/T226 钢的低倍组织及缺陷酸蚀检验法GB/T3721 磁粉探伤机JB/T9218 渗透探伤GB/T 231 《布氏硬度试验方法》GB/T 230 《金属洛氏硬度试验方法》GB/T 17394 《金属里氏硬度试验方法》GB/T4340 《金属维氏硬度试验方法》GB/T4341 《金属肖氏硬度试验方法》GB/T18449 《金属努氏硬度试验方法》GB/T 6402 《超声波探伤标准》四、表面质量检验项目及验收标准4.1对于生产或购买的热处理件,表面质量具体检验项目及标准如表1:表一表面质量检验项目及验收标准4.2热处理件有上述缺陷,允许清理,但表面清理深度不得大于5mm,清理处应圆滑无棱角,清理宽度和长度分别不得小于清理深度6和8倍,清理处的残存钢渣应予以铲除。
4.3其它未尽事宜,可由供方与需方协商解决处理。
五、热处理件表面质量检验方法5.1 对于生产或购买的热处理件,表面质量具体检验方法如表2:表二表面质量检验方法5.2 热处理件尺寸检验5.2.1 长度尺寸检验可用直尺、卡钳、卡尺或游标卡尺等通用量具进行测量。
5.2.2 高度(或横向尺寸)与直径检验一般情况用卡钳或游标卡尺测量,如批量大,可用专用极限卡板测量。
热处理工艺规范

➢ 本规范规定了本公司常用的金属的热处理 设备、工艺与质量检验方法
1
热处理工艺规范
目录
➢ 前言 1 规范范围 2 规范性引用文件 3 常用热处理方式定义 4 工艺分类代号 5 工件举例 6 热处理设备 7 工作要求 8 规范 9 热处理后工件的质量检验
2
热处理工艺规范
前言
本标准由技术部提出。 本标准由技术部起草。 本标准主要起草人:xx 本标准审核人:xx 本标准批准人:xx 本标准由技术部部归口并负责解释。 本标准于2019年10月首次发布,于2020年3月第一次修订。
14
热处理工艺规范
6 热处理设备 • 6.1 加热炉有效加热区实际温度偏差值(指炉罐内)
不应超过±20℃。 • 6.2 加热炉的每个加热区应配有温度测定及温度控制
自动记录装置。 • 6.3 加热炉的维护保养必须按制订的制度进行,并妥
善保管有关记录。
15
热处理工艺规范
7 工作要求 • 7.1 检查设备、仪表是否正常,并应事先将炉膛清理
干净。 • 7.2 核对材料与图样是否相符,了解零件的技术要求
和工艺规定。 • 7.3 选择好合适的工夹具,并考虑好装出炉的方法。
16
热处理工艺规范 8 规范 8.1 工艺的制定。应根据工件的特征(材料的牌号、处 理前的状态及形状、尺寸等)、热处理 目的、批量、热处理设备等具体条件来制定合理的热处 理工艺。 8.2 热处理工艺曲线见图1、图2
• 8.4 冷却时应以适当的速度,使工件各部分均匀冷 却。
• 8.5 如采用空冷,应在空气中散开冷却,不允许堆 放或置于潮湿的地上冷却。
20
热处理工艺规范 • 8.6 作为热处理后的辅助工序,清除工件的氧化皮
JB 8434—96 热处理环境保护技术要求

热处理环境保护技术要求JB 8434—96中华人民共和国机械工业部1996—09—03批准1997—07—01实施前言本标准为贯彻《中华人民共和国环境保护法》,防止和控制热处理对环境的污染而制订。
本标准由机械工业部环境保护机械标准化技术委员会提出并归口。
本标准负责起草单位:机械工业部武汉材料保护研究所。
本标准主要起草人:张炼、郦振声。
本标准于1996年9月3日首次发布。
1 范围本标准规定了热处理环境污染的分类及污染物的控制与排放标准等技术要求。
本标准适用于从事热处理生产的车间和工厂。
2 引用标准下列标准所包含的条文,通过在本标准中引用而构成为本标准的条文。
本标准出版时,所示版本均为有效。
所有标准都会被修订,使用本标准的各方应探讨使用下列标准最新版本的可能性。
GBJ 4—73 工业“三废”排放试行标准GB 87—85 工业企业噪声控制设计规范GB 3095—82 大气环境质量标准GB 5085—85 有色金属工业固体废物污染控制标准GB 5086—85 有色金属工业固体废物浸出毒性试验方法标准GB 5087—85 有色金属工业固体废物腐蚀性试验方法标准GB 5088—85 有色金属工业固体废物急性毒性初筛试验方法标准GB 8702—88 电磁辐射防护规定GB 8978—88 污水综合排放标准GB 12348—90 工业企业厂界噪声标准GB 14500—93 放射性废物管理规定JB/T 5073—91 热处理车间空气中有害物质的限值JB/T 6074—92 热处理盐浴有害固体废物无害化处理方法TJ 36—79 工业企业设计卫生标准ZB J71 00l一90 热处理盐浴有害固体废物污染管理的一般规定3 热处理环境污染的分类和来源热处理的环境污染分为化学性污染和物理性污染。
化学性污染来自原料、中间反应产物及废弃物中的各种行害物质,主要以废气、废水和固体废物的形式存在;物理性污染主要为噪声和电磁辐射。
其分类和米源列于表1。
CQI-9热处理系统评估在汽车零部件热处理过程中的应用

CQI-9热处理系统评估在汽车零部件热处理过程中的应用刘宏磊;李昌海【摘要】通过对CQI-9热处理系统评估进行简要的介绍,分析了CQI-9热处理系统评估在汽车零部件热处理过程中应用的必要性,对比第3版CQI-9热处理系统评估与前两版的主要区别.笔者结合长期从事热处理工作及进行CQI-9热处理系统评估工作,提出了一些审核技巧和应用中暴露出来的问题.【期刊名称】《金属加工:热加工》【年(卷),期】2016(000)013【总页数】3页(P18-20)【关键词】CQI-9热处理系统评估;汽车零部件;热处理过程【作者】刘宏磊;李昌海【作者单位】中信戴卡股份有限公司;中信戴卡股份有限公司【正文语种】中文热处理系统评估C Q I-9: Special Process: Heat Treat System Assessment (HTSA)由美国汽车工业行动集团AIAG的热处理工作小组开发,AIAG于2006年3月发布;2007年8月发布了第2版;2011年10月发布了第3版。
HTSA 提出的热处理要求是来自顾客和产品标准的附加要求。
热处理系统评审适用于评审一个组织满足HTSA的要求及顾客要求、政府法规要求和组织自身要求的能力;也适用于对供应商的评审。
HTSA的目标是在供应链中建立持续改进,强调缺陷预防,减少变差和浪费的热处理管理系统。
HTSA与国际认可的质量管理体系以及适用的顾客特殊要求相结合,规定了热处理管理系统的基本要求,旨在为汽车生产件和相关服务件组织建立热处理管理体系提供一个通用的方法。
美国戴姆勒克莱斯勒、福特、通用三大汽车公司在其顾客特殊要求中均对热处理系统评审提出要求,凡是热处理供应商都必须按CQI-9做过程审核。
热处理作为一个特殊的工艺过程,由于其材料特性的差异性、工艺参数的复杂性和过程控制的不确定性,以及其产品检验为破坏性抽样检验,及加大检验频次的不经济性,长期以来一直视为汽车零部件制造业的薄弱环节,并在很大程度上直接导致整车产品质量的下降和召回风险的上升。
GB5099修订版与GB5099-94_版主要变化2011
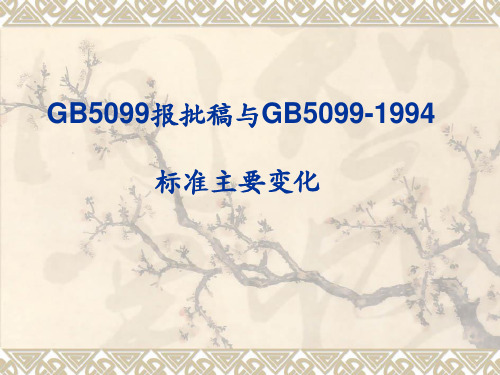
20
瓶口普通螺 纹设计要求
无
21
钢瓶组批
22
瓶阀装配扭 矩
GB5099报批稿与GB 5099-94主要变化
序号 修订内容 GB 5099-94 GB 5099-报批稿
23
无损检测要 求
淬火后回火热 处理的瓶体应 逐只进行超声 或磁粉检测
淬火后回火热处理的抗拉强度小于 1100MPa的钢瓶应进行超声检测, 但对于筒体长度小于200mm的钢瓶 可用磁粉检测代替; 正火处理用来充装氢气及其他具有 致氢脆性、毒性或腐蚀性介质的, 或淬火后回火热处理的抗拉强度小 于880MPa的钢瓶,应逐只进行超声 检测或磁粉检测。
充装混合气体 与不适用于具 有氢脆危险或 应力腐蚀倾向 介质 灭火用的气瓶
GB 5099-94
GB 5099-报批稿
GB5099.1钢瓶不适用于具有氢 脆危险或应力腐蚀倾向的介质; GB5099.1和GB5099.4的钢瓶 盛装介质增加可用于混合气体。
5
无
6
不适用于“灭火用 的气瓶” 一般地区钢瓶的使 用环境温度为20~60℃, 寒冷地区的使用环 境温度为-40~ 60℃。
GB5099报批稿与GB5099-1994 标准主要变化
GB5099报批稿与GB 5099-94主要变化
序号 修订内容 GB 5099-94 GB 5099-报批稿 根据不同热处理方式及强度范围分为4部 分: GB5099.1《第1部分:淬火后回火处理的 抗拉强度小于1100MPa的钢瓶》 GB5099.2《第2部分:淬火后回火处理的 抗拉强度大于或等于1100MPa的钢瓶》 GB5099.3《第3部分:正火处理的钢瓶》 GB5099.4《第4部分:淬火后回火处理的 抗拉强度小于880MPa的钢瓶》
Q-ZZ 30021锻件热处理验收规范-2011(下发 版)

Q/ZZ锻件热处理验收规范中国重型汽车集团有限公司发布前 言本标准代替QZZ 30021—1996《锻件热处理验收规范》。
本标准与QZZ 30021—1996相比,主要变化如下:——标准的编排格式按GB/T 1.1—2009《标准化工作导则 第1 部分:标准的结构和编写》的规定 进行了调整;——对原标准中3.2条、3.3条进行了修订,并取消了原标准中5.3.2条;——删除原标准3.4条对等温退火工艺晶粒度检测,增加调质工艺;——对原标准3.5条增加了“如没有规定,一般锻件按取样部位处总脱碳层深度,每边应小于或等于有效厚度的1%”——对原标准中3.6条进行了修订,增加了“但当锻件尺寸不够取拉伸试样时,则应按强度与硬度值进行换算后,对该锻件在取拉伸试样部位进行硬度检测。
”——对原标准中5.3.3条进行了修订,取消金相组织半级的规定;——在新标准中增加了3.8条和3.9条对过热和过烧的规定;——原标准中规定了拉伸性能,在新标准中修订为力学性能,并增加了对冲击韧性的检验规定; ——新标准中增加了非调质钢的有关规定;——取消了原标准5.3.2中所列出的各种具体钢号;——因GB/T 13320-2007较91版作了很大的改动,故金相组织评级图参照GB/T 13320-2007; ——原标准中取样位置已经不适用,对力学性能的取样位置按DIN EN 10083-1:2006-10重新作了规定;——增加了5.4.1和5.4.2条款,对热处理硬度的测定位置进行了明确规定;——对金相试样的取样位置重新作了规定,取消原标准中对边部和心部金相组织的判定依据; ——取消了原标准5.5.3中对金相试样的硬度检测;——因GB6397已取消,所以本标准中取消了GB6397标准;——本次修订删除了原标准中的“斯达—斯太尔汽车”、“等温退火”等词语;—— 增加了GB/T 229冲击试验标准和DIN EN 10083-1:2006-10 力学性能取样标准;——对原标准的附录A进行了修订。
热处理行业规范条件

热处理行业规范条件(报批稿)一、总则(一)为贯彻落实科学发展观,规范热处理生产经营秩序和投资行为,在保证产品质量和安全生产的基础上,改进企业组织方式,合理配置资源,加快淘汰落后产能和抑制低水平重复建设,推进节能减排清洁生产,引导热处理行业向精密、优质、清洁的集约化、专业化、规模化、现代化方向发展,根据国家有关法律法规和产业政策,特制定热处理行业规范条件。
二、建设条件和企业布局(二)投资新建或改扩建的热处理加工、热处理设备制造和热处理工艺材料生产企业(厂、点)要符合国家产业政策和产业规划,符合地区工业发展规划、产业发展导向和区域功能。
新建或改扩建的热处理加工企业生产能力应具有大于(含)1000万元/年产值的生产能力。
(三)热处理的生产场所一般应设置在地区规划部门规定的区域内,禁止设立在居民区、商业区、旅游区、蔬菜、粮食等农作物种植区与水源保护区。
(四)所有热处理专业化加工厂点的设立要坚决淘汰落后产能,要以加快“发展先进工艺,限制陈旧工艺,淘汰落后工艺”为导向。
推动企业转型升级,确保安全生产,强化节能减排。
促进开发低碳技术项目,发展高技术附加值的热处理企业。
三、工艺装备及工艺材料(五)热处理加工企业或厂点应采用先进技术装备,加热设备的有效加热、保温及炉温均匀性应满足工艺要求,少无氧化的热处理加热设备比例达50%或以上。
不得使用国家明令禁止和淘汰的热处理工艺和设备(参见《产业结构调整目录》、《工业和信息化部高耗能落后机电设备(产品)淘汰目录》、《部分工业行业淘汰落后生产工艺装备和产品指导目录》)。
(六)热处理加热设备应符合相应的电炉能耗分级标准,炉体表面温升、空炉升温时间和空炉损耗功率比应符合GB/T15318《热处理电炉节能监测》要求。
电阻炉加热效率不得低于70%,燃料炉综合热效率不得低于60%。
(七)热处理的加热设备应使用陶瓷纤维等性能优良的绝热、保温材料,禁止使用石棉类材料,保证设备和工艺的能耗符合国家、行业的相关标准要求。
- 1、下载文档前请自行甄别文档内容的完整性,平台不提供额外的编辑、内容补充、找答案等附加服务。
- 2、"仅部分预览"的文档,不可在线预览部分如存在完整性等问题,可反馈申请退款(可完整预览的文档不适用该条件!)。
- 3、如文档侵犯您的权益,请联系客服反馈,我们会尽快为您处理(人工客服工作时间:9:00-18:30)。
热处理检验方法和规范公司标准化编码 [QQX96QT-XQQB89Q8-NQQJ6Q8-MQM9N]热处理检验方法和规范金属零件的内在质量主要取决于材料和热处理。
因热处理为特种工艺所赋予产品的质量特性往往又室补直观的内在质量,属于“内科”范畴,往往需要通过特殊的仪器(如:各种硬度计、金相显微镜、各种力学性能机)进行检测。
在GB/T19000-ISO9000系列标准中,要求对机械产品零部件在整个热处理过程中一切影响因素实施全面控制,反映原材料及热处理过程控制,质量检验及热处理作业条件(包括生产与检验设备、技术、管理、操作人员素质及管理水平)等各方面均要求控制,才能确保热处理质量。
为此,为了提高我公司热处理产品质量,遵循热处理相关标准,按零件图纸要求严格执行,特制定本规范一、使用范围:本规范适用于零件加工部所有热处理加工零件。
二、硬度检验:通常是根据金属零件工作时所承受的载荷,计算出金属零件上的应力分布,考虑安全系数,提出对材料的强度要求,以强度要求,以强度与硬度的对应关系,确定零件热处理后应具有大硬度值。
为此,硬度时金属零件热处理最重要的质量检验指标,不少零件还时唯一的技术要求。
1、常用硬度检验方法的标准如下:GB230金属洛氏硬度试验方法 GB231金属布氏硬度试验方法GB1818金属表面洛氏硬度试验方法 GB4340 金属维氏硬度试验方法GB4342金属显微维氏硬度试验方法 GB5030 金属小负荷维氏试验方法2、待检件选取与检验原则如下:为保证零件热处理后达到其图纸技术(或工艺)要求,待检件选取应有代表性,通常从热处理后的零件中选取,能反映零件的工作部位或零件的工作部位硬度的其他部位,对每一个待检件的正时试验点数一般应不少于3个点。
通常连续式加热炉(如网带炉):应在连续生产的网带淬火入回火炉前、回火后入料框前的网带上抽检3-5件/时。
且及时作检验记录。
同时,若发现硬度超差,应及时作检验记录。
同时,若发现硬度越差,应及时进行工艺参数调整,且将前1小时段的零件进行隔离处理(如返工、检)。
通常期式加炉(如井式炉、箱式炉):应在淬火后、回火后均从料框的上、中、下部位抽检6-9件/炉,且及时作检验记录。
同时,若发现硬度超差,应及时进行工艺参数调整,且将该炉次的零件进行隔离处理(如返工、逐检)。
通常感应淬火工艺及感应器与零件间隙精度调整,经首件(或批)感应淬火合格后方可生产,且及时作检验记录。
3、硬度测量方法:各种硬度测量的试验条件,见下表1:测量硬化层深度不同的零件表面硬度时,硬度试验方法与试验力的一般选择,见表2:经不同热处理工艺处理后的表面硬度测量方法及其选择,见小表3:(2)若确定的硬度试验方法有几种试验力可供选择时,应选用试验条件允许的最大试验力。
4、检验设备与人员:所有硬度计及标准硬度试块均应在计量部门检定的有效期内使用,不允许在无检定合格证书或超过检定的有效期使用。
应设立专职检验人员,且经正规培训与考核,具有正式的资格证书;生产线的操作人员检验,应经一定培训,在专职检验人员的认可或指导下进行。
5、测量数据的表示与记录:硬度值的表示应按相应国家标准硬度试(检)验方法的规定,一般以硬度范围法表示,标出上、下限值,如60-65HRC;特殊情况液可以只标下限值或上限值,应用不小于或不大于表示,如不大于229HBS;若记录换算硬度值时,应在换算值后面加括号注明实测值【如:()】;若记录硬度平均值时,应在硬度值平均值后米那加括号注明计算平均值所用的各测点硬度值【如:(、、)】检验报告记录,包括零件名称、材料、检验数量、检验结果及检验人员与日期。
三、金相试验金相分析时用金相显微镜观察金属内部的组成相及组织组成物的内型以及它们的相对量、大小、形态及分布等特征。
材料的性能取决于内部的组织形态,而组织又取决于化学成分及加工工艺,热处理时改变组织的主要工艺手段,因此,金相分析是材料及热处理质量检验与控制的重要方法。
1、通常金相检验方法的标准如下:GB/T11354-1989 钢铁零件渗氮层深度测测定和金相组织检验GB/T9450-1988 钢铁渗碳淬火有效硬化层深度的测定与校核GB/T9451-1988 钢件薄表面总硬化层深度或有效硬化层深度的测定GB/T5617-1985 钢的感应淬火或火焰火后有效硬化层深度的参定JB/T9204-1999 钢件感应淬火金相检验JB/T9211-1999 中碳钢与中碳合金结合钢马氏体等级JB/T7710-1995 薄层碳氮共渗或薄层渗碳显微组织检验GB/T13298-1991 金相显微组织检验方法GB/T13299-1991 钢的显微组织评定方法GB6394-86 金属平均晶粒度测定法NJ309-83 内燃机连杆螺栓金相检验标准NJ326-84 内燃机活塞销金相检验标准2、金相试样的选取与检验步骤:金相试样的选取:2.1.1纵向取样:纵向取样是指沿着刚材的锻扎方向进行取样。
主要检验内容为:非金属夹杂物的变形程度、晶粒畸变程度、碳化物网、变形后的各种组织形貌、热处理的全面情况等。
横向取样横向取样指垂直于钢材的锻扎方向进行取样。
主要检验内容为:金属材料从表层到中心的组织、显微组织状态、晶粒度级别、碳化物网、表面缺陷深度、氧化层深度、腐蚀层深度、表面化学热处理及镀层厚度等。
缺陷或失效分析取样:截取缺陷分析的试样,应包括零件的缺陷部分在内;或在缺陷部分附近的正常部位取样进行比较。
为此,通常检验零件的最重要项目为表层显微组织观察和硬化层深度测定,应横向取样;但紧固体的螺纹部分的渗层检验需要纵向取样。
金相检验步骤:选样——金相切割机(或线切割机)取样—镶嵌机加热镶嵌-磨抛机磨光/抛光-化学腐蚀(通常用4%硝酸酒精溶液)-金相观察/硬化层深度(或显微硬度)测定-出具检验报告取样数量:通常连续式加热炉(如网带炉):1件/4小时通常周期式加热炉(如井式炉、箱式炉):2-3件/炉(装炉夹具不同部位)备注:(1)金相试样以磨面面积小于400MM2,高度15-20MM为宜。
(2)试样的制备过程中,部允许因受热而导致组织变化,应避免试样边缘出现圆角并防止改变斜截面试样的角度。
3、金相组织观察于判别:渗碳或碳氮共渗:适用于08F、Q235AF、20、20Cr等低碳或低合金钢的零件。
试样应从渗碳或碳氮共渗零件上切取。
液可用于钢件的材质,热处理状态,有效厚度一致,避过经同炉渗碳或碳氮共渗处理的试样。
薄层碳氮共渗件(层深≤),表层碳含量应不低于%,氮含量应不低于%。
薄层渗碳钢件(层深≤)表层碳含量应不低于%渗层显微组织评级在淬火状态下进行(放大倍率为400倍)。
针状马氏体级别及残余奥氏体级别评定:当渗层显微组织主要为针状马氏体时,依据JB/T7710-1995标准图谱共分1-5级,其中1-2级合格。
板条马氏体级别评定:当渗层显微组织主要为板条马氏体时,依据JB/T7710-1 995标准图谱共分1-5级,其中1-2级合格。
渗层(层深≤)碳化物级别评定:依据NJ326-84标准图谱共分1-5级,其中1-3级合格。
心部铁素体级别评定:依据JB/T7710-1995标准图谱共分1-5级,其中一般零件1-4级合格,重要零件1-3级合格。
渗氮或碳氮共渗(软氮化):3.2.1渗氮前调质组织的检验:渗氮前调质组织级别(对大工件可在表面2mm深度范围内检查),依据GB/T11 354-1989标准图谱(放大倍率为500倍),回火索氏体中游离体素体数量共分1-5级,其中一般零件1-3级为合格,重要零件1-2级为合格。
渗氮零件的工作面部允许由脱碳层或粗大的回火索氏体组织。
试样应从渗碳零件上垂直于渗氮表面切取,也可用与零件的材料、处理条件、加工精度相同,并经同炉渗氮处理的试样;检验部位应具有代表性,若检查渗氮层脆性的试样,表面粗糙度要求>-0.63mm,但不允许把化合物磨掉。
渗氮层脆性检验:经气体渗氮的零件,必须进行脆性的检验。
依据GB/T11354-1989标准图谱(放大倍率为100倍),渗氮层脆性级别按维氏硬度压痕边角碎裂程度共分1-5级,其中一般零件1-3级为合格,重要零件1-2级为合格。
检验渗氮层脆性,采用维氏硬度计,试验力规定用(10kgf),加载必须缓慢(在5-9s内完成),加载后停留5-10s,然后去载荷,同时,每制件至少测3点,其中2点以上处于相同级别时,才能定级,否则,需重新测定一次。
如由特殊情况经有关各方协商,亦可采用(5kgf)或(30kgf)的试验力,但需按下表4的值换算。
由磨量的零件也可在磨去加工余量后表面上测定。
渗氮层疏松检验:经氮碳共渗(软氮化)的零件,必须进行疏松检验。
依据GB/T11354-1989标准图谱(放大倍率为500倍)取其疏松最严重的部位,渗氮层疏松级别按表面化合物内微孔的形状、数量、密集程度共分1-5级,其中一般零件1-3级为合格,重要零件1-2级为合格。
渗氮扩散层中氮化物检验:气体渗氮的零件必须进行氮化物检验。
依据GB/T11354-1989标准图谱(放大倍率为500倍),去其组织中最差的部位,渗氮层中氮化物级别按情况共分1-5级,其中一般零件1-3级合格,重要零件1-2级为合格。
感应淬火:适用于中碳碳素钢(如45钢)和中碳合金钢(如40Cr)的机械零件。
零件淬火后,表面不应有裂纹,灼伤等缺陷。
零件经淬火,低温回火(≤200℃),金相组织按GB/T5617-1985标准共分1-1 0级,规定如下:硬度下限≥55HRC时,3-7级为合格。
硬度下限<55HRC时,3-9级为合格。
4、硬化层深度的测定方法:硬化层深度的测定方法分为金相法和硬度法两种,有争议时,以硬度法作为仲裁方法。
测定表面淬火【如感应淬火】、化学热处理【如渗碳、碳氮共渗、渗氮、氮碳共渗(软氮化)】及其他各种表面强化层深度时金相检验的重要内容。
根据硬化层深可以分为大于0.3mm的两种情况。
金相法:层深>0.3mm的表面硬化层测定方法:从零件表面垂直方向测量到规定的某种显微组织边界的距离。
测定层深时,各种强化工艺所规定的特征组织,见下表5:从表面垂直方向测量到与基体金属间的显微组织没有明显变化处的距离,即总硬化层深度。
硬度法:从零件表面垂直方向测量到规定的显微硬度硬化层处的距离。
测定层深时,各种强化工艺下有效硬化层评定的参数,见下表6:强化工艺有效硬化层界限硬度(HV)推荐试验力/N国家标准感应淬火DS2GB5617-1985渗C,CN共渗DC550GB9450-1988渗N,NC共渗(软氮化)DN比基体硬度高50说明1HVMS为技术要求规定的最低表面硬度2 ( )内的数值为允许试验力范围渗碳和碳氮共渗共渗有效硬化层(DC),经热处理至最终硬度值后,离表面三倍于有效硬化层处硬度小于450HV的零件,可采用比550HV大的界限硬度值(以25HV为一级)来测定有效硬化层深度。