较完整的六西格玛案例
六西格玛经典案例

六西格玛经典案例在六西格玛质量管理方法中,通过分析和改进业务流程,以减少缺陷和提高效率,从而实现优秀质量和高度效益。
以下是三个经典的六西格玛案例。
1. Motorola的六西格玛实践Motorola是六西格玛的奠基者之一、20世纪80年代,Motorola采用六西格玛方法,以改进生产过程并提高质量。
在一个以缺陷率而不是零缺陷为标准的产业中,Motorola在一年内将缺陷率从超过三十万个降低到每百万个产品中只有5个。
六西格玛的成功引起了其他公司的注意,并成为其他公司实施质量管理的典范。
2. General Electric(GE)的六西格玛实施GE是六西格玛的早期采用者,它将六西格玛引入公司的各个部门和业务领域。
公司的首席执行官杰克·韦尔奇在1995年将六西格玛作为公司的战略重点。
GE在实施过程中的一个成功案例是其航空发动机业务部门,该部门通过六西格玛方法降低了生产过程中的缺陷率,并提高了航空发动机的性能和可靠性。
GE的成功证明了六西格玛可以在各种行业中实现卓越的结果。
3.美国政府的六西格玛应用六西格玛方法不仅在企业界取得成功,而且在政府部门中也有很好的应用。
美国政府决定在1995年引入六西格玛方法,以提高效率并减少浪费。
例如,美国联邦航空管理局(FAA)使用六西格玛方法改进了飞行管制和管理过程,减少了航班延误和事故。
美国海军也采用了六西格玛方法来改善军舰维护和修理过程,提高了战斗力和减少了成本。
以上是六西格玛的三个经典案例,它们都展示了通过六西格玛方法来实现质量改进和效益提高的潜力。
这些案例证明了六西格玛是一个非常有力的质量管理方法,可以在各个领域带来显著的结果。
无论是在制造业、服务业还是政府部门,六西格玛都能够提供一个可靠的框架来解决质量和效率方面的挑战。
精益六西格玛的改善案例

精益六西格玛的改善案例案例:汽车制造流程改善背景:汽车制造公司在生产过程中遇到了一些问题。
产品质量不稳定,交付时间延长,成本高涨,因此需要通过改善流程来提高生产效率和降低成本。
目标:-提高产品质量稳定性,降低缺陷率-缩短交付时间,提高客户满意度-降低制造成本,提高利润率方法:1.项目选择:选择一个关键的制造流程进行改善。
在该公司中,组装过程是最关键且容易出现问题的环节,因此选择组装流程作为改善项目。
2.流程分析:通过流程图和价值流图,对组装流程进行详细分析。
识别出每个环节中的瓶颈和浪费,如等待时间、运输时间、不必要的重复工作等。
3.数据收集:收集关于缺陷率、交付时间和成本的数据。
这些数据将成为决策的基础。
4.根本原因分析:使用工具如鱼骨图、五力模型、因果图等,找出导致问题的根本原因。
可能的原因包括不合理的工作流程、不合适的设备、员工技能不足等。
5.解决方案设计:根据根本原因分析的结果,设计出改进方案。
例如,通过优化工作流程、提高设备质量、加强员工培训等。
6.实施改进:在一定范围内进行试点实施改进方案,收集数据并评估效果。
根据数据的结果,对方案进行调整和改进,直到达到预期的效果。
7.控制改进:建立一套监控体系,确保改进效果能够持续。
通过设立关键绩效指标(KPI)和改进计划,对改进方案进行监控和调整。
结果:经过精益六西格玛方法学的改进,该汽车制造公司取得了显著的效果:-产品质量稳定性得到明显提高,缺陷率显著降低。
-交付时间缩短,客户满意度有了显著提升。
-制造成本明显降低,利润率得以提高。
结论:。
六西格玛案例分析
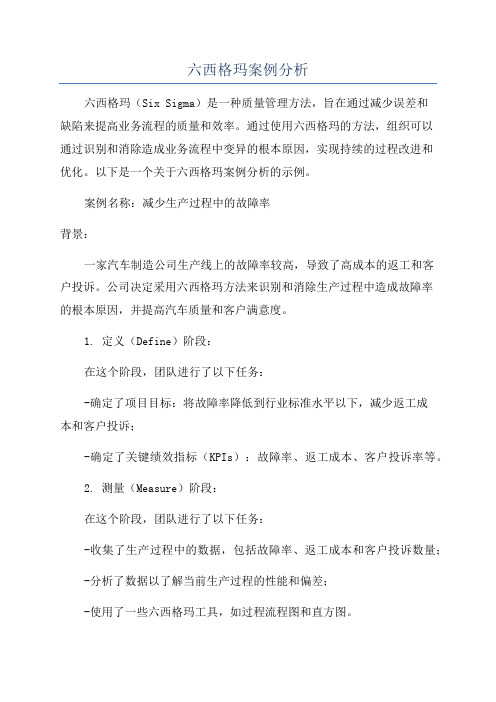
六西格玛案例分析六西格玛(Six Sigma)是一种质量管理方法,旨在通过减少误差和缺陷来提高业务流程的质量和效率。
通过使用六西格玛的方法,组织可以通过识别和消除造成业务流程中变异的根本原因,实现持续的过程改进和优化。
以下是一个关于六西格玛案例分析的示例。
案例名称:减少生产过程中的故障率背景:一家汽车制造公司生产线上的故障率较高,导致了高成本的返工和客户投诉。
公司决定采用六西格玛方法来识别和消除生产过程中造成故障率的根本原因,并提高汽车质量和客户满意度。
1. 定义(Define)阶段:在这个阶段,团队进行了以下任务:-确定了项目目标:将故障率降低到行业标准水平以下,减少返工成本和客户投诉;-确定了关键绩效指标(KPIs):故障率、返工成本、客户投诉率等。
2. 测量(Measure)阶段:在这个阶段,团队进行了以下任务:-收集了生产过程中的数据,包括故障率、返工成本和客户投诉数量;-分析了数据以了解当前生产过程的性能和偏差;-使用了一些六西格玛工具,如过程流程图和直方图。
3. 分析(Analyze)阶段:在这个阶段,团队进行了以下任务:-确定了导致故障率升高的根本原因;-使用了五力分析和鱼骨图等工具,以识别可能的原因;-根据数据和分析结果,确定了一个或多个关键影响故障率的因素。
4. 改进(Improve)阶段:在这个阶段,团队进行了以下任务:-开发了改进计划,包括减少故障率的具体措施和时间表;-实施了改进措施,并记录了结果。
5. 控制(Control)阶段:在这个阶段,团队进行了以下任务:-实施了独立检查和监控措施,以确保改善措施的可持续性;-追踪关键绩效指标,如故障率、返工成本和客户投诉;-确立了持续改进的机制,以确保过程持续优化。
通过使用六西格玛方法,该汽车制造公司成功降低了生产过程中的故障率。
在实施改进措施后,故障率从10%降低到行业标准的3%以下,成功降低了返工成本和客户投诉率。
此外,公司在生产线上建立了严格的质量控制措施和监控机制,以确保持续改进和优化。
精益六西格玛案例

精益六西格玛案例
精益六西格玛是一种管理方法,它结合了精益生产和六西格玛的优点,旨在提
高效率和质量。
下面我们来看一个实际的案例,了解精益六西格玛是如何在实践中发挥作用的。
某汽车零部件制造公司在生产过程中遇到了一些问题,导致了生产效率低下和
产品质量不稳定。
经过分析,他们决定引入精益六西格玛方法来改善生产流程。
首先,他们进行价值流分析,找出了生产过程中的浪费和瓶颈。
然后,他们采
用精益工具,如5S和Kanban,对生产车间进行了重新布局和标准化。
同时,他们
还对员工进行了培训,让他们更好地理解和运用精益工具。
在改善生产流程的同时,公司还引入了六西格玛的方法,通过数据分析和流程
控制,找出了造成产品质量不稳定的根本原因,并采取了相应的改进措施。
经过一段时间的努力,公司取得了显著的成效。
生产效率得到了提高,产品质
量稳定性也得到了保障。
公司的客户满意度得到了提升,市场竞争力也得到了增强。
通过这个案例,我们可以看到精益六西格玛在实际中的应用效果。
它不仅可以
帮助企业提高效率和质量,还可以带来客户满意度和市场竞争力的提升。
综上所述,精益六西格玛是一种非常有效的管理方法,它可以帮助企业解决生
产过程中的问题,提高效率和质量,实现持续改进和持续增长。
希望更多的企业能够引入精益六西格玛,实现可持续发展。
六西格玛改进案例

六西格玛改进案例以六西格玛改进案例为题,列举如下10个案例:1. 生产流程改进案例:在一个制造业公司,生产流程中存在着许多瑕疵品。
为了提高产品质量,该公司采用了六西格玛方法进行改进。
通过分析生产过程中的关键环节,确定了引起瑕疵品的主要原因,并通过改进工艺和设备,减少了瑕疵品的产生率。
2. 供应链管理改进案例:一家零售公司的供应链管理存在着库存过剩和缺货的问题,导致了销售额下降。
为了解决这个问题,该公司运用了六西格玛方法,对供应链中的各个环节进行了优化。
通过提高库存预测的准确性,优化订货策略,以及改进供应商管理,该公司成功解决了库存过剩和缺货问题。
3. 客户投诉处理改进案例:一家电信运营商的客户投诉率较高,影响了公司的声誉。
为了改善客户满意度,该公司运用了六西格玛方法,对客户投诉处理流程进行了改进。
通过提高投诉处理的效率和质量,该公司成功降低了客户投诉率,并提升了客户满意度。
4. 销售流程改进案例:一家保险公司的销售流程存在着繁琐和低效的问题,导致了销售人员的工作效率低下。
为了提高销售业绩,该公司采用了六西格玛方法,对销售流程进行了改进。
通过简化流程、优化销售工具和培训销售人员,该公司成功提升了销售人员的工作效率和销售业绩。
5. 质量管理改进案例:一家制药公司的质量管理体系存在着缺陷,导致了产品质量不稳定。
为了提高产品质量,该公司采用了六西格玛方法,对质量管理体系进行了改进。
通过加强质量控制、改进检验方法和加强员工培训,该公司成功提升了产品质量的稳定性。
6. 项目管理改进案例:一个IT项目存在着进度延误和成本超支的问题,导致了项目无法按时交付。
为了解决这个问题,该公司采用了六西格玛方法,对项目管理进行了改进。
通过优化项目计划、加强资源管理和改进沟通机制,该公司成功提高了项目的进度控制和成本控制能力。
7. 售后服务改进案例:一家家电企业的售后服务存在着响应速度慢和问题解决率低的问题,导致了客户的不满意。
6西格玛课题优秀案例
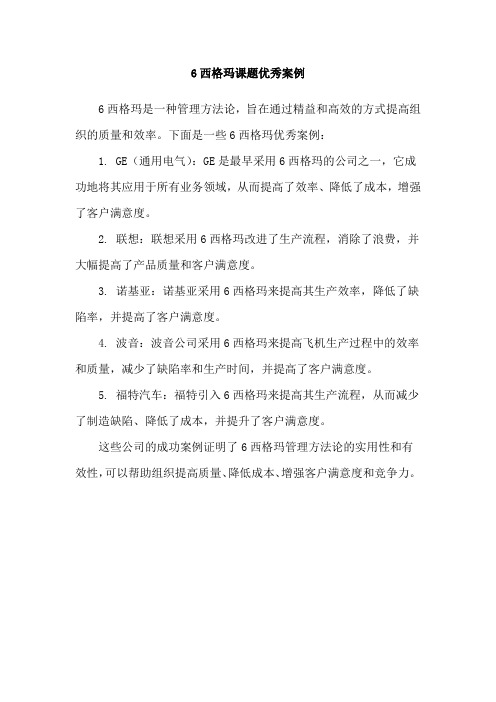
6西格玛课题优秀案例
6西格玛是一种管理方法论,旨在通过精益和高效的方式提高组织的质量和效率。
下面是一些6西格玛优秀案例:
1. GE(通用电气):GE是最早采用6西格玛的公司之一,它成功地将其应用于所有业务领域,从而提高了效率、降低了成本,增强了客户满意度。
2. 联想:联想采用6西格玛改进了生产流程,消除了浪费,并大幅提高了产品质量和客户满意度。
3. 诺基亚:诺基亚采用6西格玛来提高其生产效率,降低了缺陷率,并提高了客户满意度。
4. 波音:波音公司采用6西格玛来提高飞机生产过程中的效率和质量,减少了缺陷率和生产时间,并提高了客户满意度。
5. 福特汽车:福特引入6西格玛来提高其生产流程,从而减少了制造缺陷、降低了成本,并提升了客户满意度。
这些公司的成功案例证明了6西格玛管理方法论的实用性和有效性,可以帮助组织提高质量、降低成本、增强客户满意度和竞争力。
6西格玛课题优秀案例

6西格玛课题优秀案例
六西格玛是一种质量管理方法,旨在通过统计学的方法和工具来降低产品和服务的缺陷率,提高生产效率和降低成本。
下面是一些六西格玛课题的优秀案例:
1. LG 电子的微波炉门泄漏问题:LG 电子在制造微波炉时遇到
了门泄漏问题,这严重影响了产品质量和品牌形象。
通过使用六西格玛方法,LG 电子的团队确定了问题的根本原因,并制定了改进计划,最终成功解决了这个问题。
2. 波音公司的飞机维修成本降低:波音公司使用六西格玛方法来降低飞机的维修成本,通过分析和测量,确定了问题的的根本原因,并采取了一系列措施来减少维修成本。
这项改进不仅降低了公司的运营成本,还提高了飞机的可靠性和安全性。
3. 沃尔玛的库存管理优化:沃尔玛使用六西格玛方法来优化库存管理,通过测量和分析问题,制定了一套优化方案,成功地降低了库存成本和提高了供应链的效率。
4. 通用电气的生产效率提高:通用电气使用六西格玛方法来提高生产效率,通过分析和测量,确定了问题的根本原因,并采取了一系列措施来提高效率,最终提高了公司的盈利能力。
这些案例展示了六西格玛方法在各个领域的应用和成功的结果,不仅提高了产品或服务的质量,还降低了成本和提高了生产效率。
6SIGMA某工作案例1精编版

Code
Factor
Levels
最佳值
A
Nut Dim
+1
4.1
B
C/L Dim
-1
3.6
D
Bond
+1
3
E
Point Height
+1
Байду номын сангаас0.5
Nut 拔出力越大越好,为了得到最大Nut Force,(Max Y) 调整X’s 的水准 .并进行Confirming Test.
NOV-23-2000
I-Phase 小结
Nut 业体更换, Diameter 尺寸保证,Nut 成型情况改善;Carriage Lower设计改善,Bond涂抹量标准化;Carriage Lower设计改善,增加与Nut 接触面积;对不良C/L Diameter进行改善,全部采用现地化部品;对Nut 拔出力进行管理,确保Nut 与C/L的结合情况。
在此种条件下对100ea 测试Nut Force ,对Data 进行Process Capability Analysis.
NOV-23-2000
I
工程能力:改善前:6438PPM改善后:493PPM向上率:92.4%
Process Capability Analysis for Nut Force
改善前
改善后
6,438PPM
493PPM
NOV-23-2000
I-Phase 小结
Nut 业体更换, Diameter 尺寸保证,Nut 成型情况改善;Carriage Lower设计改善,Bond涂抹量标准化;Carriage Lower设计改善,增加与Nut 接触面积;对不良C/L Diameter进行改善,全部采用现地化部品;对Nut 拔出力进行管理,确保Nut 与C/L的结合情况。
- 1、下载文档前请自行甄别文档内容的完整性,平台不提供额外的编辑、内容补充、找答案等附加服务。
- 2、"仅部分预览"的文档,不可在线预览部分如存在完整性等问题,可反馈申请退款(可完整预览的文档不适用该条件!)。
- 3、如文档侵犯您的权益,请联系客服反馈,我们会尽快为您处理(人工客服工作时间:9:00-18:30)。
0
厂家分类
投入数分类
09年2月共分析不良芯片35块,其中8541机芯不 良共27块。占机芯总不良的77.5%。 9/76
百分比
60
60
D5 机芯不良分析(2)
8541市场PIN分类(3.3V/1.8V)
Define-M-A-I-C
8541 model分类
8541 原因分类
10/76
D5 焊接不良分析
SMT、预装、总装工序ESD/EOS问题、机芯板焊接问题。
2/76
目录
- D1 项目背景
Define
Measure
Analyze Improve Control
- D2 客户声音VOC及CTQ陈述 - D3 项目范围 - D4 Y的定义 - D5 Y的初步分析 - D6 Y的缺陷现象描述 - D7 Y的基线 - D8 Y的目标 - D9 财务效果预估
6.商业案情/背景(Business Case):
R3系列(宝蓝)是海尔电子08年-09年主推机型,芯产量超过20万台。市场不良率为1.5%,其中机芯不良为0.67%,所以机芯不良是事业部急需改善的项目。
7.问题陈述(Problem Statement)(现象/目的): 平板电视生产中芯片不良、焊接不良、元件不良为前三位问题,通过对市场和现场前80%问题的改善来减少质量成本。 8.Y定义和缺陷陈述(Y &Defining Defect): R3系列机芯市场/现场不良率 9.项目范围(Project Scope): 机芯板制造流程和总装生产流程 10.预想原因变量(X′S)是什么?
y21 =虚焊 y21= HDMI 焊接不良 y22 =连焊 y22 =U2 焊接不良
12/76
D6 Y的缺陷现象描述
Define-M-A-I-C
y1数字板芯片不良 现象描述
EOS不良
ESD不良
y2数字板焊接不良 现象描述
焊接不良
13/76
D8 Y的目标陈述
Define-M-A-I-C
R3系列市场不良率 6709 PPM
0.6
60
百分比
D2 客户声音VOC及CTQ陈述
R3系列机芯板 内部顾客 财务部
Define-M-A-I-C
外部顾客宝蓝系列机芯板用户 来自OC机芯板不能正常工作
VOB
机芯板不良占R3系列市场问 题的,影响公司降损失降不良 率项目的完成
CTP
机芯板加工流程改善……
CTQ
芯片不良、焊接不良
6/76
D3项目范围
Control
18/76
M1 y的流程能力分析
D-Measure-A-I-C
07 年 6 月 -08 年 2 月 I-MR 控制图
日期 2008年8月 2008年9月
不良量 188 312
产量 2605 6324
不良率 7.22%
单独值
1
UCL=2.19% 2.00% _ X =1.45%
4.93%
0.1 0.0 机芯 百分比 百分比 累积 % 8541 机芯 0.68 73.1 73.1 WX68 机芯 0.12 12.9 86.0 AX68 机芯 0.07 7.5 93.5 MSTAR 机芯 0.06 6.5 100.0 0
机芯模块
100
的
Pareto
图
100
按不良现 象分
80
80
不良率
40
UCL=0.91% 0.80% 0.60% 0.40% 0.20%
0.97% 0.47% 0.28%
__ MR=0.28%
0.00% 1 2 3 4 5 观测值 6 7 8 9
LCL=0.00%
通过现场机芯板的月度不良数的I-MR控制图可以看出,现场流程趋于 稳定,除08年6月新品上市不良率较高外没有较大的变异点及异常点。
现场不衣率
10600 市场不良率 3000 PPM 现场不良率 4500PPM
市场不良率 2000 PPM 现场不良率 2500PPM
BASE
GOAL
ENT
14/76
D9 财务效果预估
预期的项目收益 财务效果计算方法
Define-M-A-I-C
年预期财务效果=(改善前-改善后)*月平均生产量*12个月*材料单价项目投入(现场改善费用+培训费用) =(6709-3000)*5*12*3000/1000000-10 =210万元
六西格玛黑带(BB)项目
降低R3系列机芯 不良50%
事业部: 青岛电子事业部 倡导者: 解韦奇 指导者: 张德华 黑带: 刘学顺 项目成员:刘本根、乔艳军、孟建成、 金鹏飞、王军、朱红蕊 推进日期:2009.02-2009.06
1/76
海尔集团六西格玛项目注册表
1.基本信息(General Information)
16/76
D11 项目计划
项 目
阶 段
2月24日-2月29日
Define-M-A-I-C
推
3月
进
活
4月
动
计
5月
划
6月
DEFINE MEASURE
ANALYZE IMPROVE CONTROL
课题情报收集 问题点整理
测量DATA制作计划 PROCEE MAPPING分析 C&E FMEA分析 对工程进行DATA统计分析 团队合作,集体讨论分析,得出结论 向后计划拟定
焊接不良 的 P a r e t o 图
0.9 0.8 0.7 0.6 80 100
Define-M-A-I-C
不良率
0.5 0.4 0.3 0.2 0.1 0.0 焊接不良 不良率 百分比 累积 % 虚焊 0.45 52.3 52.3 连焊 0.21 24.4 76.7 偏移 0.12 14.0 90.7 损坏 0.08 9.3 100.0
SMT机芯板加工流程、总装制造流程
外一: 权纯泽 内一:刘学顺 团队成员:刘本根、乔艳军、孟建成、金鹏飞、王军、朱红蕊
2. 现状与目标(Baseline and Goal)
关键质量特性 (CTQ) 市场不良率 现场不良率 单位 PPM PPM 现水平 6709 12000 目标水平 3000 5000 母本水平 2000 3000
现场机芯不良率 Y2:按现场在扫描调试工序检出的 机芯不良总数/生产的产品总数* 1000000计算,单位 PPM;
8/76
D5 机芯不良分析(1)
100
Define-M-A-I-C
机芯模块 的 Pareto 图
100
80
80
不良率
40
40
20
20
0
机芯模块 不良率 百分比 累积 % 数字板芯片不良 焊接不良 62.1 14.2 62.4 14.3 62.4 76.7 软件不良 11.7 11.8 88.4 部品不良 7.0 7.0 95.5 其他 4.5 4.5 100.0
D1.2项目背景
R3系列机芯不良情况
G8541机芯是青岛电
百分比
模块
120
Define-M-A-I-C
的
Pareto
图
100
100 80 80 60 40 60 40 20
子事业部的主导机芯,
08年、09年市场畅销 产品海尔宝蓝系列产品 全部采用此机芯,因此 该机芯的生产加工质量
按模块分
20 0 模块 百分比 百分比 累积 %
1.50%
2008年10月
2008年11月 2008年12月 2009年1月 2009年2月 2009年3月 2009年4月
103
11 21 73 3 7 6
3380
3383 750 3284 310 1478 2145
3.05%
0.33% 2.80% 2.22%
移动极差
1.00% LCL=0.70% 0.50% 1 2 3 4 5 观测值 6 7 8 9
电源 35.7 32.6 32.6
屏模组 27.2 24.9 57.5
机芯板 24.7 22.6 80.1
外观 18.6 17.0 97.1
其他 3.2 2.9 100.0
0
机芯
0.9 0.8 0.7
的
Pareto
图
100
80
百分比
0.5 0.4 0.3 0.2 20 40
厂的生产效率和交货质 量,更直接关系到海尔 彩电在市场终端的美誉 度。因此必须提升 G8541机芯的生产加工 质量,以确保海尔彩电 在生产和市场的竞争力。
工艺处
刘本根(GB) 1.工艺制作 2.现场问题改善 3.市场问题改善 4.不良品分析
静电改善
纪玉杰 1.静电防护标准制定 2.防静电遵守点检 3.改善静电设备 4.静电危害宣传
部品品质
王军(GB) 1.材料可靠检查 2.供应协调 3.材料管理点检 4.生产线材料确认
品质改善
孟建成(GB) 1.工程品质调查 2.设备改善确认 3.顽固不良消除 4.工程技术改善
•设计品质的验证体制 •样品 Qualification •可靠性品质的保证体制 •综合品质的评价体制
–确立 Line Stop制 –System board 改善 制造品质的保证
设计品质的保证
市场调查,顾客满意度的分析
部品品质的保证
订立所期望的制品形象
建立不接收不良,不制造不良,不流出不良的体制 (全员参与,创造用户感动) 4/76
- D10 项目团队
- D11 项目计划 - D12 操作平台
3/76
D1.1项目背景 (战略目标)
想法 变化
综合品质的一流化
变化
顾客 满意
市场品质的保证