复合材料自动铺带技术应用及方案示例
大型复合材料筒形结构自动铺带技术
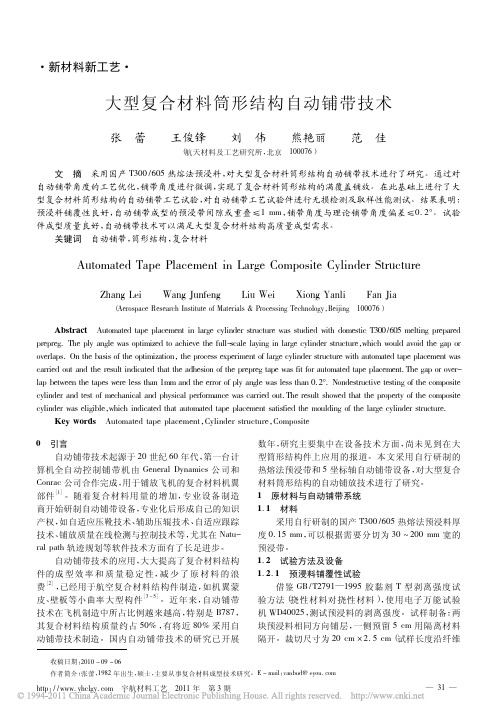
·新材料新工艺·收稿日期:2010-09-06作者简介:张蕾,1982年出生,硕士,主要从事复合材料成型技术研究。
E -mail :vanbud@eyou.com大型复合材料筒形结构自动铺带技术张蕾王俊锋刘伟熊艳丽范佳(航天材料及工艺研究所,北京100076)文摘采用国产T300/605热熔法预浸料,对大型复合材料筒形结构自动铺带技术进行了研究。
通过对自动铺带角度的工艺优化,铺带角度进行微调,实现了复合材料筒形结构的满覆盖铺放。
在此基础上进行了大型复合材料筒形结构的自动铺带工艺试验,对自动铺带工艺试验件进行无损检测及取样性能测试。
结果表明:预浸料铺覆性良好,自动铺带成型的预浸带间隙或重叠≤1mm ,铺带角度与理论铺带角度偏差≤0.2ʎ。
试验件成型质量良好,自动铺带技术可以满足大型复合材料结构高质量成型需求。
关键词自动铺带,筒形结构,复合材料Automated Tape Placement in Large Composite Cylinder StructureZhang LeiWang JunfengLiu WeiXiong YanliFan Jia(Aerospace Research Institute of Materials &Processing Technology ,Beijing 100076)Abstract Automated tape placement in large cylinder structure was studied with domestic T300/605melting preparedprepreg.The ply angle was optimized to achieve the full-scale laying in large cylinder structure ,which would avoid the gap or overlaps.On the basis of the optimization ,the process experiment of large cylinder structure with automated tape placement was carried out and the result indicated that the adhesion of the prepreg tape was fit for automated tape placement.The gap or over-lap between the tapes were less than 1mm and the error of ply angle was less than 0.2ʎ.Nondestructive testing of the composite cylinder and test of mechanical and physical performance was carried out.The result showed that the property of the compositecylinder was eligible ,which indicated that automated tape placement satisfied the moulding of the large cylinder structure.Key words Automated tape placement ,Cylinder structure ,Composite 0引言自动铺带技术起源于20世纪60年代,第一台计算机全自动控制铺带机由General Dynamics 公司和Conrac 公司合作完成,用于铺放飞机的复合材料机翼部件[1]。
复合材料自动铺带工艺中的脚手架支撑设计与优化
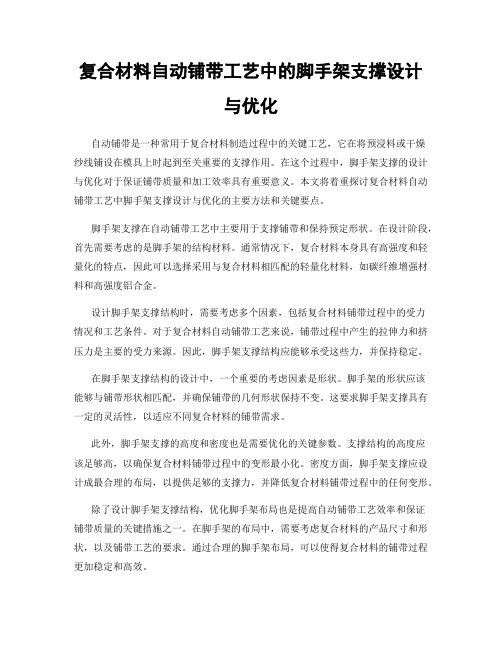
复合材料自动铺带工艺中的脚手架支撑设计与优化自动铺带是一种常用于复合材料制造过程中的关键工艺,它在将预浸料或干燥纱线铺设在模具上时起到至关重要的支撑作用。
在这个过程中,脚手架支撑的设计与优化对于保证铺带质量和加工效率具有重要意义。
本文将着重探讨复合材料自动铺带工艺中脚手架支撑设计与优化的主要方法和关键要点。
脚手架支撑在自动铺带工艺中主要用于支撑铺带和保持预定形状。
在设计阶段,首先需要考虑的是脚手架的结构材料。
通常情况下,复合材料本身具有高强度和轻量化的特点,因此可以选择采用与复合材料相匹配的轻量化材料,如碳纤维增强材料和高强度铝合金。
设计脚手架支撑结构时,需要考虑多个因素,包括复合材料铺带过程中的受力情况和工艺条件。
对于复合材料自动铺带工艺来说,铺带过程中产生的拉伸力和挤压力是主要的受力来源。
因此,脚手架支撑结构应能够承受这些力,并保持稳定。
在脚手架支撑结构的设计中,一个重要的考虑因素是形状。
脚手架的形状应该能够与铺带形状相匹配,并确保铺带的几何形状保持不变。
这要求脚手架支撑具有一定的灵活性,以适应不同复合材料的铺带需求。
此外,脚手架支撑的高度和密度也是需要优化的关键参数。
支撑结构的高度应该足够高,以确保复合材料铺带过程中的变形最小化。
密度方面,脚手架支撑应设计成最合理的布局,以提供足够的支撑力,并降低复合材料铺带过程中的任何变形。
除了设计脚手架支撑结构,优化脚手架布局也是提高自动铺带工艺效率和保证铺带质量的关键措施之一。
在脚手架的布局中,需要考虑复合材料的产品尺寸和形状,以及铺带工艺的要求。
通过合理的脚手架布局,可以使得复合材料的铺带过程更加稳定和高效。
在脚手架布局中,可以采用两种常见的方式:平面布局和立体布局。
平面布局适用于平面产品的铺带,可通过将脚手架设置在产品的底部和两侧来提供全方位的支撑。
立体布局则适用于曲面或复杂形状的产品,可通过将脚手架从不同的角度放置在模具中,以实现对产品形状的全面支撑。
碳纤维复材自动铺贴原理

碳纤维复材自动铺贴原理碳纤维复材是一种由碳纤维和树脂基体复合而成的材料,具有高强度、高刚度、低密度等优良性能,在航空航天、汽车、船舶等领域有广泛的应用。
而碳纤维复材的制备过程中,自动铺贴技术是其中一项关键技术。
碳纤维复材自动铺贴是指通过机器设备将预浸有树脂的碳纤维布料按照设计要求精确地铺贴到模具上,形成复材的制备过程。
它不仅能提高生产效率,还能保证产品的一致性和精度。
下面将从机器设备、铺贴过程和质量控制三个方面介绍碳纤维复材自动铺贴的原理。
一、机器设备碳纤维复材自动铺贴一般采用自动化设备,包括铺贴机、导向系统、切纤机和控制系统等。
铺贴机是核心设备,通过控制系统控制铺贴头的运动,实现精确的铺贴。
导向系统用于确保碳纤维布料的正确位置,防止偏移。
切纤机用于切割碳纤维布料,以适应不同形状的模具。
二、铺贴过程碳纤维复材的铺贴过程一般分为预处理、铺贴和压实三个步骤。
首先,对碳纤维布料进行预处理,包括裁剪和配置。
然后,将预处理后的碳纤维布料通过铺贴机铺贴到模具上。
在铺贴过程中,控制系统根据设计要求控制铺贴头的运动轨迹,确保碳纤维布料的正确位置和覆盖面积。
最后,通过压实工艺,将树脂浸透碳纤维布料,并使其固化。
三、质量控制碳纤维复材自动铺贴过程中,质量控制是非常重要的环节。
首先,需要对碳纤维布料进行检查,确保其质量符合要求。
其次,在铺贴过程中,要严格控制铺贴头的运动轨迹和速度,以及模具的温度和压力,保证铺贴的精度和一致性。
此外,还需要对铺贴后的复材进行检查,包括检测厚度、密度、孔隙率等指标,以保证产品的质量。
碳纤维复材自动铺贴是一项关键技术,通过机器设备、铺贴过程和质量控制三个方面的配合,实现了碳纤维布料的精确铺贴,保证了复材产品的质量和性能。
随着自动化技术的不断发展,碳纤维复材自动铺贴技术将进一步提高生产效率和产品质量,推动碳纤维复材在各个领域的应用。
基于自动铺带技术的复合材料结构件强度评估研究

基于自动铺带技术的复合材料结构件强度评估研究引言:复合材料是一种由两种或两种以上材料组成的复合体,具有优异的力学性能和工程应用潜力。
在航空航天、汽车工业、能源等领域中,复合材料的应用广泛,其中复合材料结构件的强度评估是一个关键问题。
本文旨在研究基于自动铺带技术的复合材料结构件强度评估方法与技术。
一、自动铺带技术的原理与应用自动铺带技术是一种将预浸复合材料纤维排列在设计规定位置的技术。
其主要原理是通过控制复合材料纤维与树脂的比例、面积密度和纤维层次,实现复合材料结构件的定向排列和强度提升。
自动铺带技术具有高效、高精度和低浪费等优点,因此在航空航天和汽车工业等领域广泛应用。
二、复合材料结构件强度评估的重要性复合材料结构件的强度评估是确保结构件在实际工况下能够承受预期载荷的关键。
在设计和制造复合材料结构件之前,强度评估能够提前预测结构件的破坏行为,指导结构优化和性能改进。
因此,开展复合材料结构件强度评估研究具有重要的理论和实践意义。
三、基于自动铺带技术的复合材料结构件强度评估方法1. 宏观力学模型基于自动铺带技术的复合材料结构件强度评估可以采用宏观力学模型进行。
通过建立合适的力学模型,将复合材料结构件视为多层板,进行强度评估和应力分析。
该方法能够较为准确地预测结构件的破坏行为和强度性能。
2. 细观力学模型细观力学模型是一种更加精细的强度评估方法,通过考虑复合材料纤维和树脂的微观结构与相互作用,建立复杂的力学模型。
该方法考虑了材料的非线性和破坏行为,可以提供更为精确的强度评估结果。
然而,由于模型的复杂性,该方法对计算资源和计算时间的要求较高。
3. 数值模拟与有限元分析数值模拟与有限元分析是一种较为常用的强度评估方法。
通过将复合材料结构件离散化为多个小单元,利用有限元方法对结构件进行力学分析和强度评估。
该方法能够较为准确地模拟复合材料结构件在复杂载荷下的响应,定量地评估结构件的强度。
四、复合材料结构件强度评估的关键因素1. 材料性能复合材料的性能对结构件的强度评估具有重要影响。
自动铺带技术在复合材料制造中的应用探索
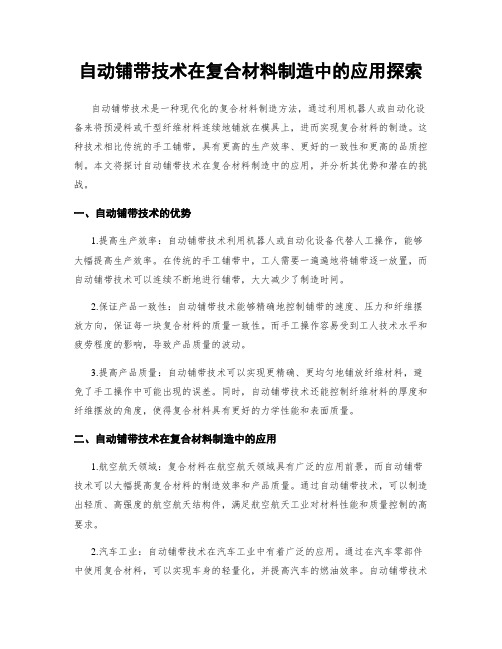
自动铺带技术在复合材料制造中的应用探索自动铺带技术是一种现代化的复合材料制造方法,通过利用机器人或自动化设备来将预浸料或干型纤维材料连续地铺放在模具上,进而实现复合材料的制造。
这种技术相比传统的手工铺带,具有更高的生产效率、更好的一致性和更高的品质控制。
本文将探讨自动铺带技术在复合材料制造中的应用,并分析其优势和潜在的挑战。
一、自动铺带技术的优势1.提高生产效率:自动铺带技术利用机器人或自动化设备代替人工操作,能够大幅提高生产效率。
在传统的手工铺带中,工人需要一遍遍地将铺带逐一放置,而自动铺带技术可以连续不断地进行铺带,大大减少了制造时间。
2.保证产品一致性:自动铺带技术能够精确地控制铺带的速度、压力和纤维摆放方向,保证每一块复合材料的质量一致性。
而手工操作容易受到工人技术水平和疲劳程度的影响,导致产品质量的波动。
3.提高产品质量:自动铺带技术可以实现更精确、更均匀地铺放纤维材料,避免了手工操作中可能出现的误差。
同时,自动铺带技术还能控制纤维材料的厚度和纤维摆放的角度,使得复合材料具有更好的力学性能和表面质量。
二、自动铺带技术在复合材料制造中的应用1.航空航天领域:复合材料在航空航天领域具有广泛的应用前景,而自动铺带技术可以大幅提高复合材料的制造效率和产品质量。
通过自动铺带技术,可以制造出轻质、高强度的航空航天结构件,满足航空航天工业对材料性能和质量控制的高要求。
2.汽车工业:自动铺带技术在汽车工业中有着广泛的应用。
通过在汽车零部件中使用复合材料,可以实现车身的轻量化,并提高汽车的燃油效率。
自动铺带技术可以大幅提高复合材料零部件的制造效率,满足汽车工业对大规模生产和高品质产品的需求。
3.建筑领域:自动铺带技术也可以应用于建筑领域的复合材料制造。
复合材料在建筑领域有着广泛的应用前景,可以用于制造建筑结构件、装饰材料等。
自动铺带技术可以提高建筑材料的生产效率,同时保证产品的一致性和质量,满足建筑行业对快速和高质量产品的需求。
自动铺带技术与大飞机复合材料结构成型

自动铺带技术与大飞机复合材料结构目前,飞机上的复合材料使用量已经成为衡量其先进性的重要标准。
波音787、空客A380飞机都大量采用复合材料,空客A350上复合材料的用量更超过50%。
作为中国拥有完全知识产权的大型民用客机项目,为了保证其客机的市场竞争力并促进国内复合材料产业的发展,也必将大量采用先进复合材料。
而自动铺带技术则是使用复合材料的关键技术之一。
先进复合材料的历史先进复合材料是20世纪60年代早期以单向带的形式推出的。
起初用手工铺贴,其工艺是劳动密集型的,容易引起质量问题。
20世纪60年代中期,航空工业的发展极大地推动了其自动化进程。
早期的设备是航空公司或加工车间在材料供应商的指导下自己制造的。
设备的构型涵盖了从手工辅助台式的原型机到由美国空军牵头、通用动力和Conrac公司合作研发的第一台全数控龙门式铺带机。
这台设备被用来为F-16生产复合材料零件,使用的是75mm 宽的带子。
20世纪70年代末期至80年代初,设备制造者生产了第一台商业化的平面和曲面数控铺带机,这些设备被用在军事项目上(如B-1和B-2轰炸机)制造飞机的零件。
曲面上带宽范围为75~150mm,平面可以高达300mm。
20世纪80年代末期,自动铺带开始广泛的使用于商用飞机上。
整个20世纪90年代,设备、编程技术、铺带技术和ATL复合材料的进一步发展使铺带工艺操作更简单、性能更可靠、界面更友好。
复合材料工艺综述单向碳环氧预浸带是在衬纸上成卷供应的,典型的宽度有75mm、150mm和300mm三种规格。
曲面应用使用75mm和150mm带宽,平面应用使用150mm和300mm带宽。
材料卷被装载在铺带的头部。
铺带头在平面应用时被安放在4轴台架上,曲面应用时安放在5轴台架上。
1 优点碳环氧预浸带极大地减少了手工铺层。
在平面装料的情况下,相对于手工铺贴,碳环氧预浸带可以减少的人工劳动时间高达70%~85%,铺层效率可以高达1000kg/周。
复合材料自动铺丝计算机辅助设计软件的设计与应用
复合材料自动铺丝计算机辅助设计软件的设计与应用复合材料自动铺丝计算机辅助设计软件的设计与应用摘要:随着科技的发展和工业制造的进步,复合材料在航空、汽车、船舶等领域的应用越来越广泛。
本文设计了一款复合材料自动铺丝计算机辅助设计软件,并探讨了该软件在航空领域的应用案例。
软件具备自动优化铺丝路径的功能,提高了铺丝效率和质量,为航空工程师和设计师提供了便利。
关键词:复合材料;自动铺丝;计算机辅助设计;软件1. 引言复合材料在航空航天领域的应用越来越广泛,因为它具有高强度、轻质和耐腐蚀性等优点。
在飞机制造过程中,铺丝是一项重要的工艺,在复材的制造过程中扮演着至关重要的角色。
然而,传统的手工铺丝方式效率低下,无法满足大规模生产的需求。
因此,本文将设计一款复合材料自动铺丝计算机辅助设计软件,旨在提高铺丝效率和质量,为航空工程师和设计师提供便利。
2. 设计方法本软件采用了自适应遗传算法和机器学习方法。
首先,通过遗传算法对铺丝路径进行优化。
遗传算法模拟了自然界中的生物进化过程,通过选择、交叉和变异的操作,不断优化铺丝路径。
然后,通过机器学习算法,提高铺丝的准确性。
机器学习模型通过学习大量的铺丝数据,提高了软件的智能化程度。
3. 软件功能本软件具有以下主要功能:(1) 自动铺丝路径生成:根据设计要求和复材的特性,软件能够自动生成最优的铺丝路径,提高铺丝效率和质量。
(2) 工艺模拟:软件能够模拟复材的不同特性和材料的变化情况,为工程师提供了参考和决策依据。
(3) 优化算法:软件采用了自适应遗传算法,能够自动优化铺丝路径,提高了铺丝效率。
(4) 界面友好:软件界面简洁直观,易于操作和使用。
4. 应用案例本软件已成功应用于某型号客机的复合材料铺丝工艺中。
航空工程师使用该软件生成了最优的铺丝路径,并对路径进行了仿真模拟。
通过软件的帮助,工程师发现了一些潜在的问题并进行了修正,确保了复材在飞行过程中的安全性和稳定性。
5. 结果与讨论与传统的手工铺丝相比,本软件在铺丝效率和质量上都取得了显著的改进。
复合材料纤维铺放技术及其应用
复合材料纤维铺放技术及其应用摘要:先进复合材料比传统材料具有诸多优点,例如轻质量、高强度、低密度、高模量、抗疲劳、耐腐蚀、设计制造一体化等等。
复合材料对减轻结构重量、提高经济性和可靠性具有不可替代的作用。
复合材料已经广泛应用于制造领域,尤其是航空航天领域,在航空航天设备上的用量和应用部位已经成为衡量航空航天器结构先进性的重要标志之一。
关键词:复合材料;纤维铺放技术;应用一、纤维铺放技术的成型原理和特点纤维铺放技术是树脂基复合材料制造技术中的一种,其工作原理是将连续的纤维丝束或纤维带通过预浸胶或树脂之后,按照设定好的路径铺放到芯模上,最后在一定温度下固化,制成所需形状的制品。
复合材料纤维铺放成型技术(Fiber placementFP)是自动窄带铺放成型技术(Automanted tep placement, ATP)和自动铺丝束成型技术(Automated tow placement, ATP)的总称。
纤维铺放技术的成型工艺是在纤维铺放机上将平行的纤维丝束或纤维带预浸处理,通过铺放头装置将预浸过的纤维束压到需要加工的工件或芯模表面。
纤维铺放与纤维缠绕和带铺放不同,它不是按照测地线在芯模或模具上布纱;纤维铺放可精确控制丝束宽度,且各丝束可单独铺放,通过切断、重续等工序控制铺放厚度的增减。
此外,纤维丝束是通过纤维铺放机上的铺放头压在模具上的,能保证铺放每一层紧密贴合避免出现分层现象。
总结纤维铺放技术的优点有:(1)通过铺丝头剪断丝束、重新开始等,可以对铺放厚度进行精确控制;(2)工艺过程中铺丝头可调节施加力,实时加压密实;(3)铺放精度高,不易出现孔隙;(4)纤维铺放角度可以调节,不受限制;(5)铺放材料利用率高,浪费少。
二、复合材料纤维铺放技术应用1.加热工艺研究。
在自动纤维铺放过程中,为提高铺放效率,通常设置预加热及主加热2 个加热环节。
在这2 个环节中,都会涉及到选择热源、建立加热模型及确定加热温度三方面的问题。
自动铺带技术在复合材料结构件制造中的应用案例分析
自动铺带技术在复合材料结构件制造中的应用案例分析引言复合材料作为一种重要的材料,在航空航天、汽车、船舶等领域中得到了广泛应用。
复合材料的制造过程对于最终产品的质量和性能至关重要。
其中,自动铺带技术作为一种高效、精确的制造方法,被广泛应用于复合材料结构件的生产。
本文将分析自动铺带技术在复合材料结构件制造中的应用案例,并通过实例探讨其优势和挑战。
1. 自动铺带技术简介自动铺带技术是一种将预浸料纤维布按照设计要求排列、覆盖在模具上的制造方法。
该技术主要包括铺带过程、固化过程和模具脱模过程。
铺带过程中,机器人根据CAD文件或数控编程指令精确控制铺带头的运动,将预浸料纤维布覆盖在模具上。
固化过程中,通过烘烤或加热使得预浸料纤维布固化成为强度和刚度较高的复合材料。
脱模过程中,复合材料从模具上剥离,并进行后续加工。
2. 自动铺带技术在飞机制造中的应用案例2.1 A380机身板制造欧洲航天防务集团(EADS)使用自动铺带技术制造A380机身板。
铺带机器人根据设计要求,精确控制铺带头和纤维布的运动,将预浸料铺到模具上。
该技术不仅提高了生产效率,还保证了复合材料结构件的质量和一致性。
同时,相比于传统的手工操作,自动铺带技术减少了人力成本和人为误差,提高了产品质量。
2.2 波音787机翼制造波音公司采用自动铺带技术制造787机翼。
自动铺带机器人可以精确控制铺带头的运动,并快速、准确地排列纤维布。
该技术不仅提高了工作效率,还避免了手工操作中可能产生的纤维布错位、损坏等问题。
通过自动铺带技术,波音公司实现了大规模、高质量的机翼制造,为航空业带来了突破性的创新。
3. 自动铺带技术的优势和挑战3.1 优势(1)高效准确:自动铺带技术可以实现高速而精确的铺带,提高了生产效率和产品质量。
(2)一致性和可重复性:机器人通过程序控制,可以确保每次铺带过程的一致性,减少了人为误差。
(3)节约成本:相比于传统的手工操作,自动铺带技术可以减少人力成本,并大幅提高生产效率。
航空复合材料零件自动铺带技术研究
航空复合材料零件自动铺带技术研究航空航天复合材料由于其高强度、高比刚度、良好的疲劳性能和设计而被广泛用于航空航天工程,例如飞机材料。
随着科学技术的发展,航空复合材料制造技术逐渐趋于一体化、自动化、成本化,复合材料的质量逐渐成为各大飞机制造商竞争的重要举措。
因此航空航天复合材料的研发和应用是非常重要的。
标签:航空复合材料;设计与制造;发展趋势引言在我国,航空航天复合材料于20世纪60年代引入,并且越来越广泛地被广泛使用。
空间科学技术的发展促进了飞机在高空、高速、智能化方向和成本方向上的不断发展,航空航天复合材料的发展,实现了制造技术和材料特性的突破。
我国航天复合材料的研究时间较晚,复合材料的设计和制造不足,复合材料的种类较少。
并且整体性能较差,因此要进行有效生产,必须付出很大的努力来提高设计和制造水平。
一、当前的发展趋势目前大型外国军用、民用飞机复合部件的份额迅速上升,波音787客机使用超过50%的复合部件结构,A350复合部件将占结构重量的52%,俄罗斯MC21的发展,复合材料量也將是结构重量的40%至45%。
A400 M军用输送机上的复合材料数量已达到结构重量的35%。
国产复合材料在ARJ21并未广泛使用,大型零件仅在舵上使用复合材料。
大型飞机正在开发中,考虑到目前和飞机制造与国际先进水平存在差距,相对于国外A380、波音787、A350、A400 M、MC21和其他大型飞机落后至少7-8年。
以及国内设计能力、试验能力、生产设备和技术水平条件有限,对大型飞机复合构件的核算至少不小于25%(重量),采用机翼或水平舵复合结构。
同时对于复合材料零件的生产,自动铺带技术是目前最有效的制造工艺。
二、自动铺带技术的发展所谓的自动铺带技术,是利用数控设备帘布层,通过数字化,复合预浸料的自动化手段,连续自动切割和自动胶带放置。
主要工艺:复合预浸料卷安装在贴装头中,预浸材料由一组辊组成,由压辊按压机构或保形层制成或在工具上平面化。
- 1、下载文档前请自行甄别文档内容的完整性,平台不提供额外的编辑、内容补充、找答案等附加服务。
- 2、"仅部分预览"的文档,不可在线预览部分如存在完整性等问题,可反馈申请退款(可完整预览的文档不适用该条件!)。
- 3、如文档侵犯您的权益,请联系客服反馈,我们会尽快为您处理(人工客服工作时间:9:00-18:30)。
度和铺叠位置、方向、角度的准确性, 发自动铺带设备,完成了小型铺带机
(2)该 设 备 在 铺 层 时 能 够 对 铺
从而避免了人为铺放产生的偏差,如 的研制,并应用于复合材料结构件 层路径进行手动和自动设置,自动功
产品出现缺陷的几率大、零件制造质 的研制;北京航空制造工程研究所 能具有最佳的铺层路径,每层带可在
虽 然 备采用龙门式结构,主要包括带装夹
国 内 自 动 和释放 ( 开卷 ) 系统、衬纸带回卷系
铺 带 技 术 统、带缺陷检测传感系统、带对中和
研 究 起 步 导向系统、切带系统、铺带和压实系
较 晚,但 在 统、工作区域安全系统、铺带监控系
技术研究和 统、带卷装卸系统、工装定位及自动
空客西班牙Illescas用铺带工艺制造的平尾、方向舵
自动铺带作为典型的增料加工 成型技术,其成型设备的制造技术涉 及机电装备技术、C A D / C A M 软件 技术和材料工艺技术等多个研究领
大飞机复合材料制造技术 Composite Manufacturing Technology for Large Commercial Jet
域,可实现:
许多型号飞机上。
量重复性差、质量分散性大,以及尺 与 Forest-Line 公司合作研制的大 ±90°之间采取任意角度和任意方
寸精度和铺放位置准确度不能满足 型复合材料自动铺带机的调试工作 向的铺放。
大尺寸、高精度零件制造的要求等问
题。采用复合材料自动铺带技术可
在提高质量的同时,大幅度地节省原
材料,降低制造成本。同时,由于可
MTM44-1/HTS(12K)-134-35%RW MTM44-1/E-IMS65-24K 194-32%RW
M21/34%/UD268/AS7-12K M21/34%/UD194/IMA-12K AS4/8552/RC34%/AW194 AS7/8552/RC34%/AW268
公司 CYTEC CYTEC CYTEC ACG ACG HEXCEL HEXCEL HEXCEL HEXCEL
软件 FiberSIM、CPD、COVERS 等。
化(180℃)两大类。
制造方法:应用先进的自动化 3 机翼翼盒典型设
设 备(自 动 铺 带 机、自 动 下 料 机、热
计结构
成 型 设 备、柔 性 复 合 材 料 专 用 切 钻
为了便于采用复合材料自动铺
设备和大型 C 扫查设备等)符合复 带技术,在设计上最好避免使用蜂窝
自动铺带技术的发展
所谓自动铺带技术,就是采用数 控铺层设备,通过数字化、自动化的 手 段 实 现 复 合 材 料 预 浸 布、带 的 连 续自动切割和自动铺放。主要工作 过程为:将复合材料预浸料卷安装 在铺放头中,预浸材料由一组滚轮导 出,并由压紧滚轮或可随形机构压紧 在工装或上一层已铺好的材料上,切 割刀将材料按设定好的方向切断,能 保证铺放的材料与工装的外形相一 致。铺放的同时,回料滚轮将背衬材 料回收。
已接近尾声,有望在“十二五”实现
(1)最 大 限 度 地 利 用 单 向 预 浸
目前,美洲、欧洲、亚洲的几十家 应用,可以满足小曲率大型壁板类复
带(优于手工铺层采用的预浸布),并 制造商在应用自动铺带技术制造复 合材料构件的制造;国内开展自动
可减轻结构重量;
合材料结构。空客法国 N a t e 工厂 铺带技术研究的还有武汉理工大学、
统(或硬夹持工装)切边和钻孔。然 后进行外形、尺寸的无损检测;合格 后,即可进行下一步的装配。经过这 一个复杂的过程,即完成了自动铺带 复合材料壁板的制造。
公 司 等)在 飞 机 复 合 材 料 构 件 的 制
造中均已广泛采用复合材料自动铺
带成型技术。采用该技术制造的复
合材料零、部件已安装于现今生产的
大型飞机复合材料应用情况
2009 年第 22 期·航空制造技术 51
论坛 FORUM
(3)能够铺放复杂切割路径的 量。
铺层和零件局部加强铺层。
2 选材方案
合材料自动化低成本化制造趋势, 结构。因此在结构设计时,主要采用
由此可以保证复合材料结构产品质 层板结构,但层板结构抗弯性能不
量稳定可靠,并能提高产品性能、设 好,为提高层板结构抗弯和抗扭能
计许用值和劳动效率,减轻结构重 力,需要采用加强筋类结构来提高结
国外几种主要的铺带预浸料
材料牌号 CYCOM 977-2-35-12KHTS-268-600 CYCOM X850 MRZ60-12K 190/35.5 5/97” CYCOM X850 TRZ50-24K 190/35.5 5.97”
52 航空制造技术·2009 年第 22 期
论坛 FORUM
用复合材料专用铣床及柔性装夹技 术。
工装类型主要有壁板蒙皮的铺 放成型工装,蒙皮壁板的共固化或共 胶接成型工装,梁、肋的热成型工装、 成型工装。蒙皮壁板切割可采用专 用切钻夹持工装或采用柔性夹具,而 梁、肋不适宜采用柔性夹具夹持,最 好设计制造专用夹持工装。
经验和供应渠道等
舵面或机翼铺带制造方案
Hale Waihona Puke 多方面因素,是综合 考虑的结果,国外主
1 设计制造原则
要的几种铺带预浸
设计理念:在复合材料结构整 料见上表。
个设计过程中始终贯穿设计与工艺
国 产 的 C C F -1
制造一体化、并行工程的设计理念, 碳纤维,树脂可选择
使复合材料结构件在设计、分析、成 北京航空材料院或
第二步,蒙皮铺放。由于蒙皮曲 率较小,可直接采用自动铺带机铺放 在成型工装上;
第三步,蒙皮长桁组合成壁板。 长桁定位放置在蒙皮壁板的共固化 或共胶接成型工装上,无论格栅式整 体壁板还是长桁加筋式整体壁板都 可通过共胶接或共固化技术成型。
然后,将组合后的壁板和工装一 起送入大型热压罐加温加压固化成 型。脱模之后,需去除无用的产品余 量,一般采用五轴铣床和柔性夹具系
Illescas 工厂有 6 台铺带机在运行;
2007 年,哈 飞 集 团 从 西 班 牙
日本三菱重 M . T o r r e s 公司购买了一台复合材
工、富 士 重 料自动铺带机,并已开展了复合材
工等也已应 料自动铺带制造技术应用研究,将
用了此项技 在 2010 年初与空客公司合作,进行
术。
A320 方向舵前、后梁的生产。该设
以实现整个结构的零剩余强度设计,
结构重量大大减轻。
自动铺带技术于 20 世纪 70 年
代由 Boeing、Cincinnati Milacron、
H e r c u l e s 等公司联合开发,已经经
历近 40 年的发展。目前,世界上复
合 材 料 制 造 技 术 较 先 进 的 公 司(如
B o e i n g 公 司、A I R B U S 公 司、E C F
接来完成。 上下壁板制造过程一般包括长
桁造型、蒙皮铺放、蒙皮长桁组装、固 化、切 钻、外 形 尺 寸 检 测、无 损 检 测 等。上下壁板的成型过程分 3 步进 行:
第一步,制作长桁。可用大型通 用平台,在平台上铺带,形成具有一 定厚度的平板铺层,用自动裁床按长 桁尺寸剪裁,一次可剪裁多条长桁, 再用热成型工艺分别造型;
(4)铺 带 机 构 能 按 零 件 程 序 顺
材料体系选择
应形面,以可控制的压力将带平顺铺 是复合材料结构设
放和碾实、无褶皱、无气泡和具有程 计的基础,涉及到承
编规定的带与带间隙。
载和使用功能要求、
(5)所 铺 带 宽 规 格 分 为 75m m、 工艺性、成本、使用
150mm 和 300mm 三种。
型、装配、检测、使用、维护和修理等 北京航空制造工程
各环节找到最佳的平衡点。
研究所生产的环氧
设计手段:采用数字化的设计 或双马树脂,可供选
手段,保证设计数据是唯一的产品数 用的树脂按固化温
据源,实现复合材料构件 100% 的计 度分类,有中温固化
算机辅助设计。适宜采用专用设计 (125 ℃)和 高 温 固
论坛 FORUM
复合材料自动铺带 技术应用及方案示例
Application and Proposal Sample of Composite Automatic Tape-Laying Technology
中航工业哈尔滨飞机工业(集团)有限责任公司 徐福泉 高大伟 杨楠楠
具有高效率、高质量和低成本优点的自动铺带铺放技 术已经成为发达国家航空复合材料构件的成熟制造技术, 这一制造技术在国内的引进和发展,也必将在国产大飞机 的研制和生产中占有重要的地位,为国产大飞机的顺利升 空提供强有力的技术支撑。
(2)可更自由地设计铺层,发挥 中,现有十几台铺带机在生产线上 天津工业大学等多所大学,包括铺放
复合材料可设计性优势,在应力梯度 运行;空客德国 Stade 工厂有一条 4 机构、数控系统和人机交互等研究工
和应力异常的区域选择性铺放补强, 台铺带机组生产线;空客西班牙的 作。
实现了整个结构的零剩余强度;
徐福泉 高级工程师,毕业于北京航空航天
大学飞行器制造专业。现为中航工业 哈飞复合材料厂副主任。从事过工装 设计、先进复合材料结构制造等工作, 曾参与多个型号复合材料结构件制造 以及波音、空客产品转包生产。
大飞机复合材料的应用
国 外 大 型 军 用、民 用 飞 机 中 复 合 材 料 构 件 的 比 重 迅 速 增 加,波 音 787 的复合材料构件已占结构重量 的 50% 以 上, A350 复 合 材 料 构 件 将 占 结 构 重 量 的 52%,俄 罗 斯 开 发
50 航空制造技术·2009 年第 22 期
中的 M C21,复合材料用量也将占结 构 重 量 的 40% ~ 45%,A400M 军 用 运输机上复合材料用量已达结构重 量的 35%。