浅谈复合材料自动铺带机的系统控制
复合材料自动铺带工艺中的纤维导向性控制研究

复合材料自动铺带工艺中的纤维导向性控制研究复合材料是一种由两种或多种不同材料组合而成的材料,具有较高的强度、刚度和韧性,被广泛应用于航空航天、汽车、建筑等领域。
自动铺带工艺是一种常用于制造复合材料的工艺,通过自动化设备将纤维预浸料沿着预定路径铺放在模具上,形成复合材料的结构。
纤维导向性是指纤维在复合材料中的方向分布。
研究纤维导向性控制是为了实现材料性能的优化,提高复合材料的力学性能和使用寿命。
以下将介绍复合材料自动铺带工艺中的纤维导向性控制的研究。
首先,纤维导向性控制的研究在工艺参数的选择上起着重要作用。
工艺参数包括纤维预浸料的黏度、纤维排列方向、铺带速度等。
黏度的选择应该能够保证纤维在铺带过程中的排列紧密,且能够保持一定的流动性,以便铺带过程中纤维的排列受到控制。
纤维排列方向的选择是非常关键的,它决定了复合材料的力学性能和细观结构。
铺带速度也需要合理选择,过快的铺带速度容易导致纤维排列的不均匀性。
其次,纤维导向性控制的研究还涉及到铺带工艺中辅助设备的改进。
自动铺带工艺需要使用自动化设备将纤维预浸料铺放在模具上,而这些设备的性能和精度会对纤维导向性控制产生影响。
因此,改进设备的控制系统、传动系统和定位系统等方面,提高设备的稳定性和精确度,对纤维导向性的控制具有重要意义。
另外,材料科学领域中涌现出许多新的纤维导向性调控方法,例如电场辅助法、磁场辅助法和声场辅助法等。
这些方法可以通过改变外界的物理场来调控纤维的方向,以实现纤维导向性的控制。
这些新的方法不仅可以提高复合材料的力学性能,还可以控制材料的微观结构。
此外,纤维导向性控制的研究还需要关注其实际应用中的工艺难题。
在自动铺带工艺中,由于纤维预浸料在铺放过程中的流变性质的变化,纤维的纵向伸长性质会发生改变,从而影响纤维排列的方向。
因此,需要研究如何在铺带工艺中解决纤维纵向伸长性质的变化对纤维导向性控制的影响,并通过优化工艺参数和改进设备来实现纤维导向性的精确控制。
碳纤维复材自动铺贴原理

碳纤维复材自动铺贴原理一、引言碳纤维复材是一种轻质高强度的复合材料,由碳纤维和树脂基体组成。
它具有重量轻、强度高、刚性好、耐腐蚀等优点,在航空航天、汽车制造、体育器材等领域得到广泛应用。
而碳纤维复材的自动铺贴技术是一种高效、精准的生产工艺,本文将探讨碳纤维复材自动铺贴的原理和应用。
二、碳纤维复材自动铺贴原理碳纤维复材自动铺贴是指通过机器人或自动化设备,将预先裁剪好的碳纤维布料按照设计要求精确地贴合在工件表面上。
其原理主要包括以下几个方面:1. 碳纤维布料的预处理在自动铺贴之前,需要对碳纤维布料进行预处理。
首先,将碳纤维布料进行裁剪,根据工件的形状和尺寸进行合理的切割。
其次,对碳纤维布料进行预浸渍处理,使其具有一定的柔韧性和可塑性,便于在铺贴过程中贴合到工件表面。
2. 工件表面的准备在进行自动铺贴之前,需要对工件表面进行准备。
首先,清洁工件表面,确保无尘、无污染。
然后,根据设计要求,在工件表面涂覆一层适当的胶粘剂,以提供粘结力和附着力,使碳纤维布料能够牢固地粘贴在工件表面。
3. 自动铺贴机器人的控制自动铺贴过程中,机器人是关键的执行工具。
机器人通过预先编程的路径和规则,在工件表面上按照设计要求进行碳纤维布料的铺贴。
机器人配备的传感器可以实时检测工件表面的形状和尺寸,确保铺贴的准确性和精度。
同时,机器人的控制系统可以实时调整铺贴的速度和力度,以适应不同形状和曲率的工件表面。
4. 质量控制和质检自动铺贴完成后,需要进行质量控制和质检。
通过对铺贴质量的检测和评估,可以及时发现并修复可能存在的问题,确保产品的质量和性能。
三、碳纤维复材自动铺贴的应用碳纤维复材自动铺贴技术在航空航天、汽车制造、体育器材等领域有着广泛的应用。
1. 航空航天领域碳纤维复材具有高强度和轻质的特点,广泛应用于飞机的结构件,如机翼、机身等。
自动铺贴技术可以确保碳纤维布料在飞机结构上的精确贴合,提高飞机的结构强度和整体性能。
2. 汽车制造领域碳纤维复材具有优异的刚性和耐腐蚀性能,广泛应用于汽车制造中的车身和底盘部件。
自动铺带技术在复合材料加工中的误差分析与校正

自动铺带技术在复合材料加工中的误差分析与校正自动铺带技术是一种广泛应用于复合材料加工中的先进制造技术。
利用机器人系统,该技术能够实现快速、精确地将预浸料纤维带自动铺设在模具上,形成复合材料结构件。
然而,由于制造过程中存在各种误差,如机器人姿态误差、纤维带张力变化等,导致最终产品中可能存在不可忽视的误差。
因此,对自动铺带技术中的误差进行分析和校正是提高加工精度和质量的重要步骤。
首先,自动铺带技术中的误差可以分为几个方面。
机器人姿态误差是指由于控制系统不稳定或机械结构刚度不足等原因导致的机器人末端工具姿态与期望姿态之间的偏差。
纤维带张力误差则是由于张力传感器精度不高、张力控制系统不稳定等造成的纤维带张力变化不均匀。
此外,还存在其他误差源,如纤维带宽度和厚度的不均匀性、模具表面的几何变形等。
针对机器人姿态误差,可以通过提高控制系统的稳定性和增强机械结构的刚度来减小误差。
采用先进的机器视觉系统,能够实时获取铺带工具的位置和姿态信息,并与期望姿态进行比较,通过调整机器人控制指令来实现姿态误差的校正。
此外,引入自适应控制算法和传感器反馈控制系统,能够进一步提高铺带过程中的精度和稳定性。
对于纤维带张力误差,可以采用多传感器监测系统来实时监测纤维带的张力变化情况,并通过自适应控制算法来调整张力控制系统,使张力变化更加均匀稳定。
此外,对张力传感器进行校准和精度提高也是减小纤维带张力误差的关键措施。
除了机器人姿态误差和纤维带张力误差,纤维带宽度和厚度的不均匀性以及模具表面的几何变形也对最终产品的精度产生影响。
为了减小这些误差,可以在铺带前对纤维带进行预处理,通过切割和裁剪等方式将其调整为均匀宽度和厚度。
同时,在模具制造过程中,需要采用高精度的数控加工设备,并进行严格的质量控制,以减小模具表面的几何变形。
此外,误差分析与校正还需要借助先进的测量设备和方法。
利用三维扫描仪、光学显微镜等设备,能够实现对复合材料件的形状、尺寸和表面质量等的精确测量和分析。
自动铺带技术在复合材料制造中的应用探索
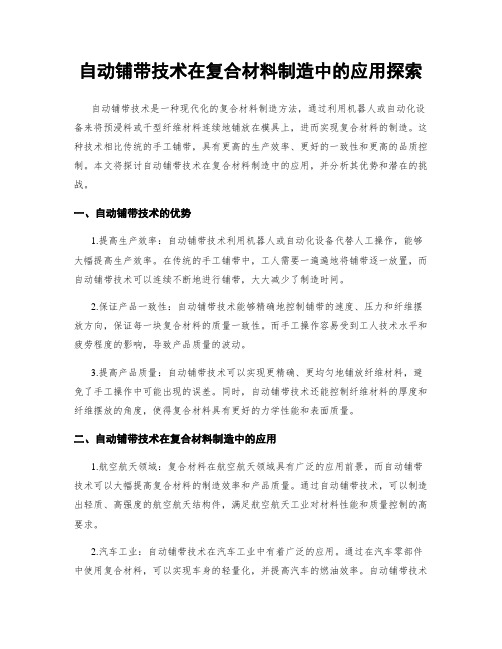
自动铺带技术在复合材料制造中的应用探索自动铺带技术是一种现代化的复合材料制造方法,通过利用机器人或自动化设备来将预浸料或干型纤维材料连续地铺放在模具上,进而实现复合材料的制造。
这种技术相比传统的手工铺带,具有更高的生产效率、更好的一致性和更高的品质控制。
本文将探讨自动铺带技术在复合材料制造中的应用,并分析其优势和潜在的挑战。
一、自动铺带技术的优势1.提高生产效率:自动铺带技术利用机器人或自动化设备代替人工操作,能够大幅提高生产效率。
在传统的手工铺带中,工人需要一遍遍地将铺带逐一放置,而自动铺带技术可以连续不断地进行铺带,大大减少了制造时间。
2.保证产品一致性:自动铺带技术能够精确地控制铺带的速度、压力和纤维摆放方向,保证每一块复合材料的质量一致性。
而手工操作容易受到工人技术水平和疲劳程度的影响,导致产品质量的波动。
3.提高产品质量:自动铺带技术可以实现更精确、更均匀地铺放纤维材料,避免了手工操作中可能出现的误差。
同时,自动铺带技术还能控制纤维材料的厚度和纤维摆放的角度,使得复合材料具有更好的力学性能和表面质量。
二、自动铺带技术在复合材料制造中的应用1.航空航天领域:复合材料在航空航天领域具有广泛的应用前景,而自动铺带技术可以大幅提高复合材料的制造效率和产品质量。
通过自动铺带技术,可以制造出轻质、高强度的航空航天结构件,满足航空航天工业对材料性能和质量控制的高要求。
2.汽车工业:自动铺带技术在汽车工业中有着广泛的应用。
通过在汽车零部件中使用复合材料,可以实现车身的轻量化,并提高汽车的燃油效率。
自动铺带技术可以大幅提高复合材料零部件的制造效率,满足汽车工业对大规模生产和高品质产品的需求。
3.建筑领域:自动铺带技术也可以应用于建筑领域的复合材料制造。
复合材料在建筑领域有着广泛的应用前景,可以用于制造建筑结构件、装饰材料等。
自动铺带技术可以提高建筑材料的生产效率,同时保证产品的一致性和质量,满足建筑行业对快速和高质量产品的需求。
基于机器学习的复合材料自动铺带工艺质量预测研究

基于机器学习的复合材料自动铺带工艺质量预测研究引言:随着复合材料在航空、汽车以及其他领域中的广泛应用,提高复合材料构件的制造质量和效率成为一项重要任务。
自动铺带工艺是目前最常用的复合材料制造技术之一,该技术可以快速、高效地制造复材构件。
然而,如何准确预测铺带工艺的质量仍然是一个具有挑战性的问题。
机器学习作为一种强大的数据分析工具,可以通过学习大量的铺带数据和相关参数来预测铺带工艺的质量。
本文将探讨基于机器学习的复合材料自动铺带工艺质量预测的研究。
一、复合材料自动铺带工艺的基本原理和挑战复合材料自动铺带工艺是一种基于纤维或片材的加工技术,通过自动机械系统将纤维或预浸料片材按照预定的路径和层压顺序,精确地叠加摆放在模具上,最终制成复合材料构件。
该工艺可以提高生产效率,减少材料浪费,并且可以制造各种复材构件的复杂形状。
然而,复合材料自动铺带工艺也面临一些挑战。
首先,铺带路径的规划需要考虑复材构件的形状、尺寸和层压顺序等因素,这使得自动铺带工艺的路径规划变得复杂。
其次,复材构件的制造质量受到多个参数的影响,如铺带速度、张力、温度和环境湿度等。
这些参数的选择和控制对于复材构件的性能具有重要影响,但其关系难以建模。
因此,如何实现对铺带工艺质量的准确预测成为一个关键问题。
二、机器学习在复合材料自动铺带工艺的应用机器学习是一种通过从数据中学习模式和关系来进行预测和决策的方法。
在复合材料自动铺带工艺中,机器学习可以通过学习大量的铺带数据和相关参数,建立复材构件制造质量的预测模型。
1. 数据收集与预处理机器学习的第一步是收集和整理铺带数据,包括工艺参数(如铺带速度、张力、温度等)和质量数据(如平整度、厚度均匀性等)。
收集到的数据需要进行预处理,包括数据清洗、去除异常值和缺失值处理等。
2. 特征工程特征工程是机器学习中一个重要的环节,它能够将原始数据转化为适合机器学习算法处理的特征。
在复合材料自动铺带工艺中,特征可以包括铺带路径的形状特征、工艺参数的统计特征和质量数据的频谱特征等。
自动铺带技术对复合材料构件性能的影响研究
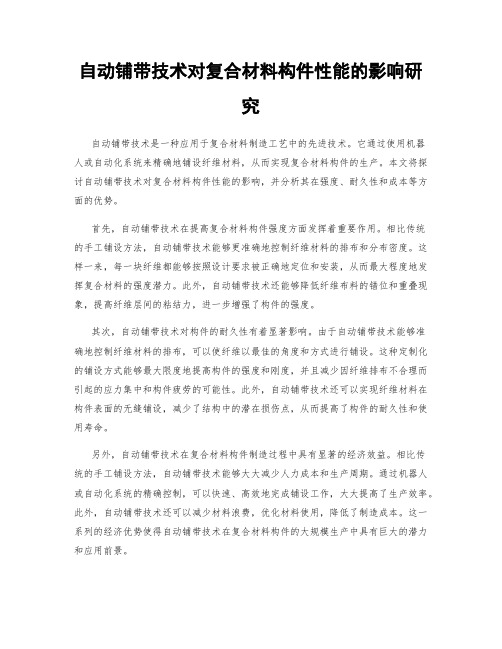
自动铺带技术对复合材料构件性能的影响研究自动铺带技术是一种应用于复合材料制造工艺中的先进技术。
它通过使用机器人或自动化系统来精确地铺设纤维材料,从而实现复合材料构件的生产。
本文将探讨自动铺带技术对复合材料构件性能的影响,并分析其在强度、耐久性和成本等方面的优势。
首先,自动铺带技术在提高复合材料构件强度方面发挥着重要作用。
相比传统的手工铺设方法,自动铺带技术能够更准确地控制纤维材料的排布和分布密度。
这样一来,每一块纤维都能够按照设计要求被正确地定位和安装,从而最大程度地发挥复合材料的强度潜力。
此外,自动铺带技术还能够降低纤维布料的错位和重叠现象,提高纤维层间的粘结力,进一步增强了构件的强度。
其次,自动铺带技术对构件的耐久性有着显著影响。
由于自动铺带技术能够准确地控制纤维材料的排布,可以使纤维以最佳的角度和方式进行铺设。
这种定制化的铺设方式能够最大限度地提高构件的强度和刚度,并且减少因纤维排布不合理而引起的应力集中和构件疲劳的可能性。
此外,自动铺带技术还可以实现纤维材料在构件表面的无缝铺设,减少了结构中的潜在损伤点,从而提高了构件的耐久性和使用寿命。
另外,自动铺带技术在复合材料构件制造过程中具有显著的经济效益。
相比传统的手工铺设方法,自动铺带技术能够大大减少人力成本和生产周期。
通过机器人或自动化系统的精确控制,可以快速、高效地完成铺设工作,大大提高了生产效率。
此外,自动铺带技术还可以减少材料浪费,优化材料使用,降低了制造成本。
这一系列的经济优势使得自动铺带技术在复合材料构件的大规模生产中具有巨大的潜力和应用前景。
除了上述优势,自动铺带技术还具有一些辅助性的影响。
例如,自动铺带技术能够实现对纤维材料的自动切割和粘接,减少了人工操作的繁琐程度,提高了生产效率。
同时,自动铺带技术还能够在铺设过程中实时监测和调节纤维材料的张力和排布,避免了因人为因素引起的误差,提高了构件的一致性和准确性。
这些辅助性的特点进一步加强了自动铺带技术在复合材料构件制造领域的竞争力和应用优势。
自动铺带技术在复合材料结构件制造中的应用案例分析
自动铺带技术在复合材料结构件制造中的应用案例分析引言复合材料作为一种重要的材料,在航空航天、汽车、船舶等领域中得到了广泛应用。
复合材料的制造过程对于最终产品的质量和性能至关重要。
其中,自动铺带技术作为一种高效、精确的制造方法,被广泛应用于复合材料结构件的生产。
本文将分析自动铺带技术在复合材料结构件制造中的应用案例,并通过实例探讨其优势和挑战。
1. 自动铺带技术简介自动铺带技术是一种将预浸料纤维布按照设计要求排列、覆盖在模具上的制造方法。
该技术主要包括铺带过程、固化过程和模具脱模过程。
铺带过程中,机器人根据CAD文件或数控编程指令精确控制铺带头的运动,将预浸料纤维布覆盖在模具上。
固化过程中,通过烘烤或加热使得预浸料纤维布固化成为强度和刚度较高的复合材料。
脱模过程中,复合材料从模具上剥离,并进行后续加工。
2. 自动铺带技术在飞机制造中的应用案例2.1 A380机身板制造欧洲航天防务集团(EADS)使用自动铺带技术制造A380机身板。
铺带机器人根据设计要求,精确控制铺带头和纤维布的运动,将预浸料铺到模具上。
该技术不仅提高了生产效率,还保证了复合材料结构件的质量和一致性。
同时,相比于传统的手工操作,自动铺带技术减少了人力成本和人为误差,提高了产品质量。
2.2 波音787机翼制造波音公司采用自动铺带技术制造787机翼。
自动铺带机器人可以精确控制铺带头的运动,并快速、准确地排列纤维布。
该技术不仅提高了工作效率,还避免了手工操作中可能产生的纤维布错位、损坏等问题。
通过自动铺带技术,波音公司实现了大规模、高质量的机翼制造,为航空业带来了突破性的创新。
3. 自动铺带技术的优势和挑战3.1 优势(1)高效准确:自动铺带技术可以实现高速而精确的铺带,提高了生产效率和产品质量。
(2)一致性和可重复性:机器人通过程序控制,可以确保每次铺带过程的一致性,减少了人为误差。
(3)节约成本:相比于传统的手工操作,自动铺带技术可以减少人力成本,并大幅提高生产效率。
复合材料自动化制造过程的质量控制
复合材料自动化制造过程的质量控制【摘要】本文以某型机尾翼壁板为例,探讨了自动化制造过程的质量管控重点以及风险点,从原材料、铺贴、装配组合以及数字化检测四方面对自动化实现过程提出质量管控措施。
【关键词】自动化制造质量控制1.前言复合材料技术是当前航空制造领域的关键技术之一,尤其是纤维增强树脂基复合材料,以其比强度大、比刚度高、抗疲劳性能好、各向异性以及材料性能可设计等特点,在航空领域的应用日益广泛。
传统的复合材料零件制造工艺以手工铺叠为主,零件的铺叠、周转、组合都依靠人工操作完成,零件生产周期长且质量稳定性难以保证,因此在复材制造行业,越来越强调自动铺丝、自动铺带、热隔膜成型等自动化制造技术的应用[1]。
某型机尾翼壁板属于加筋结构,由蒙皮和T型长桁组成,采用自动化制造,即自动铺带+热隔膜成型+共固化热压罐成型技术,蒙皮采取手工铺贴+自动铺带组合的方式进行,预浸料织物和防雷击膜在成型模上采用手工铺贴,碳带采用自动铺带机铺贴后平移至成型工装与织物和防雷击膜进行抽真空压实,长桁采用自动铺带+超声波自动铣切模式,通过热隔膜进行预成型后通过新设计的翻转设备与蒙皮“杯锥”组合精确装配组合定位。
“杯锥”组合在很大程度上可减少共固化过程长桁发生偏移进而导致固化后轴线度超差的质量问题,制造过程见图1。
图1 尾翼壁板自动化制造过程示意图2.自动化制造过程质量控制2.1质量控制要素及风险点自动化制造过程涉及流程多且各个环节控制要素多,其中材料、铺贴、装配组合、数字化检测四大类为质量控制关键控制项目。
表1 复材制件质量控制要素及风险点3.2原材料控制复合材料的原材料大都是温度和时间敏感材料,对于低温材料,在运输、储存、使用的全过程中控制并记录材料所处环境的温湿度。
原材料质量是复材制件质量保证的前提处于复材制造的源头,因此必须列为关键控制项目进行重点管控。
3.3铺贴过程在铺带过程中,需检查预浸料卷的直径,不宜偏差过大,同时要注意进行废料检查。
复合材料构件自动铺带数控编程系统技术应用
复合材料构件自动铺带数控编程系统技术应用复材构件手工成型时,预浸带经剪裁后手工铺叠、压实到模具表面。
随着复材构件在现代大型飞机上广泛应用,人工铺放工艺已难以满足实际需要,急需自动铺带技术来提高生产效率,改善制造过程的可控制性,降低成本以及提高产品质量。
自动铺带技术利用数控技术实现预浸带剪裁、定位、铺叠的自动化。
与手工相比,自动铺带技术可降低制造成本30%~50%,主要适用于各种大尺寸、小曲率部件的制造。
与传统的数控加工不同,自动铺带技术属于典型的增料制造技术,由装备技术、软件技术和工艺技术构成,国外均已形成相关的工业产品。
在自动铺带CAD/CAM软件方面,西方发达国家经过几十年的研究,已经开发了多套商用自动铺放CAD/CAM软件,并形成了完备的复合材料设计制造解决方案。
其中,Tapelay软件应用比较成熟,Tapelay软件是由空中客车公司(AIRBUS)与法国应用数学中心(CIMPA)以航空航天领域广泛采用的CATIAV5软件为平台,基于CATIACAAV5技术联合开发的自动铺带CAD/CAM软件。
该软件可直接集成到CATIAV5系列软件中,包括自动铺带CAD部分的TapeGeneration模块和CAM部分的T apeManufacturing模块。
TapeManufacturing模块则能针对部分一步法铺带机与两步法铺带机生成相应的加工NC代码[1]。
目前,国内报道可见的自动铺带CAD/CAM技术研究主要集中在轨迹规划和加工仿真的基础理论方面。
CATIA/CAA二次开发自动铺带数控编程系统采用组件应用架构(ComponentApplicationArchitecture,CAA)C++二次开发实现。
AutomationAPI(自动化应用接口)与CAAC++是CATIA二次开发常用的两种方法,AutomationAPI入门容易,但功能限制大,CAAC++入门困难,但提供的接口全面,开发的程序效率高,能够满足用户深层次专业化的要求。
航空复合材料零件自动铺带技术研究
航空复合材料零件自动铺带技术研究航空航天复合材料由于其高强度、高比刚度、良好的疲劳性能和设计而被广泛用于航空航天工程,例如飞机材料。
随着科学技术的发展,航空复合材料制造技术逐渐趋于一体化、自动化、成本化,复合材料的质量逐渐成为各大飞机制造商竞争的重要举措。
因此航空航天复合材料的研发和应用是非常重要的。
标签:航空复合材料;设计与制造;发展趋势引言在我国,航空航天复合材料于20世纪60年代引入,并且越来越广泛地被广泛使用。
空间科学技术的发展促进了飞机在高空、高速、智能化方向和成本方向上的不断发展,航空航天复合材料的发展,实现了制造技术和材料特性的突破。
我国航天复合材料的研究时间较晚,复合材料的设计和制造不足,复合材料的种类较少。
并且整体性能较差,因此要进行有效生产,必须付出很大的努力来提高设计和制造水平。
一、当前的发展趋势目前大型外国军用、民用飞机复合部件的份额迅速上升,波音787客机使用超过50%的复合部件结构,A350复合部件将占结构重量的52%,俄罗斯MC21的发展,复合材料量也將是结构重量的40%至45%。
A400 M军用输送机上的复合材料数量已达到结构重量的35%。
国产复合材料在ARJ21并未广泛使用,大型零件仅在舵上使用复合材料。
大型飞机正在开发中,考虑到目前和飞机制造与国际先进水平存在差距,相对于国外A380、波音787、A350、A400 M、MC21和其他大型飞机落后至少7-8年。
以及国内设计能力、试验能力、生产设备和技术水平条件有限,对大型飞机复合构件的核算至少不小于25%(重量),采用机翼或水平舵复合结构。
同时对于复合材料零件的生产,自动铺带技术是目前最有效的制造工艺。
二、自动铺带技术的发展所谓的自动铺带技术,是利用数控设备帘布层,通过数字化,复合预浸料的自动化手段,连续自动切割和自动胶带放置。
主要工艺:复合预浸料卷安装在贴装头中,预浸材料由一组辊组成,由压辊按压机构或保形层制成或在工具上平面化。
- 1、下载文档前请自行甄别文档内容的完整性,平台不提供额外的编辑、内容补充、找答案等附加服务。
- 2、"仅部分预览"的文档,不可在线预览部分如存在完整性等问题,可反馈申请退款(可完整预览的文档不适用该条件!)。
- 3、如文档侵犯您的权益,请联系客服反馈,我们会尽快为您处理(人工客服工作时间:9:00-18:30)。
浅谈复合材料自动铺带机的系统控制
发表时间:2019-08-05T09:13:13.313Z 来源:《基层建设》2019年第15期作者:周英赵青华贾敏梅龙
[导读] 摘要:自动铺放技术在先进复合材料制造领域占有举足轻重的地位,发达国家自动铺带技术已相当成熟,大规模应用于多种主要机型制造:如F16,F22,B717,B787,A340,A380等。
航空工业西飞质量管理部特种工艺检验站陕西西安 710089
摘要:自动铺放技术在先进复合材料制造领域占有举足轻重的地位,发达国家自动铺带技术已相当成熟,大规模应用于多种主要机型制造:如F16,F22,B717,B787,A340,A380等。
自动铺带机已经商品化,其数控系统有在通用数控系统基础上开发的铺带数控系统和专用铺放数控系统等。
目前国内复合材料制造技术还停留在手工铺放水平,自动铺带尚处在样机的研究阶段。
相比手工铺放,自动铺带机不论在效率还是在精度上,都远远优于前者。
据统计:国外自动铺带效率是手工铺带的十倍以上,自动铺放定位精度高于手工定位精度两个量级以上。
文章主要围绕复合材料自动铺带机的系统设置进行了分析,从而达到保证自动铺带机设备的加工能力及产品质量的目的。
关键词:开放式数控系统;铺带机
引言:为实现复合材料自动铺带机对数控系统的特殊要求,以可编程多轴控制器作为运动控制核心,采用可编程数字I/O卡控制开关量,提出了基于开放式数控系统的铺带机专用CNC硬件体系结构的设计方案。
为提高系统中与加工过程密切相关的实时任务的实时性,采用随动控制方式,实现了数控系统软件中的运动控制及其与开关动作量之间的协调联动的任务。
完成了各控制器的驱动程序、用户图形界面和数控代码编译模块的设计。
该系统能很好解决铺带机多轴运动控制精度要求较高、运动量与较多动作量联动实时性等设计难点。
1.铺带机数控硬件系统控制
复合材料铺放的工艺特性决定了铺带机数控系统的硬件结构体系,铺带机专用数控系统由工控机(IPC)、可编程多轴控制器、开关量控制板卡(PCL-725,PCL-730)、I/O接口、伺服驱动装置和电源驱动装置组成。
作为数控系统的核心,工控机(IPC)负责整个控制系统的信息处理与后台操作;并向各下位机发出命令,协调运动量与开关动作量的联合操作。
运动控制器接收上位机的控制指令,以此控制各轴电机运动实现数控加工。
本系统采用PMAC作为运动控制单元,它使用的CPU是DSP56001/56002数字信号处理器(40MHz),可同时控制8个运动轴同步实现联动。
除了能够实现运行程序外,还能监控PLC后台程序,两者由于时序不同并不相互冲突。
在执行运动程序之前,PMAC必须对运动性指令和非运动性指令进行预先计算,从而协调执行机构的实际运动。
本系统采用PMACⅡ型卡,通过扩展功能模块(ACC-8ES,ACC-8FS)可同时连接伺服电机驱动器与步进电机驱动器,同时实现对伺服电机与步进电机的联动。
所选用的是交流伺服电机与国产步进电机,PMAC与上位的连接采用ISA总线方式。
铺带数控系统开关动作量作为辅助加工,需要与运动量协调联动。
为保证两者实时性,选用PCL-725,PCL-730数字I/O板卡分别对铺带数控系统的手动输入操作与开关动作输出量实施控制。
由于两者都是以ISA总线通讯方式与上位工控机连接,数据传输效率得以保证。
2.铺带数控软件系统控制
2.1铺带数控系统的软件结构
铺带机数控系统软件是一个实时多任务软件系统,按照任务与加工控制过程的触发频繁程度,数控软件可分为实时任务和非实时任务两大类:直接与数控加工相关的任务为实时任务,除此之外的辅助任务为非实时任务。
根据任务执行的时间不同,还可以分为周期性任务和突发任务:周期任务为有规律的按照时间间隔周期性地执行,突发任务在时间上是随机的。
如图1所示,实时周期性任务主要包括运动控制和动作控制任务,它们是铺带加工过程中的核心任务,必须优先执行,不允许被其他任务强占。
实时突发性任务主要包括手动开关控制与故障处理,当这些任务被触发时,系统应立即中断正在执行的任务,转入对这些事件的处理,处理完再恢复到中断前的状态。
非实时周期性任务主要为界面显示刷新任务,它周期性地更新当前加工状态和各轴位置等显示信息,其主要目的是使操作者可以监控当前的系统信息。
非实时性任务的优先级较低,只有当实时任务完全执行之后才能得到运行。
非实时突发性任务是指实时性要求很低的任务,主要包括系统参数管理、数控文件管理、加工仿真、代码预处理及其他辅助性操作。
2.2运动控制任务和动作控制任务联合实现
铺带工艺的特殊性要求在铺放加工过程中运动量与动作量同时或交替进行,这两者都是关键任务,必须作为实时任务来实现。
但他们通过不同的CPU进行处理:运动控制任务由PMAC执行,而开关动作量由PCL-725输出同步指令。
这两个任务由上位机协调联动,通讯方式为ISA总线。
由于PMAC运动程序中可以编写PLC逻辑指令,运动指令与动作指令可以联合编写在PMAC程序中,通过不断访问PMAC寄存器内开关量的状态并将其更新到数字输出板卡PCL-725中,就可以保证在铺带运动同时辅助动作量的联动实现。
数据的传送完全由上位机协调实现。
以下语句为PMAC中运动与动作量联调程序以及在系统主应用程序中数据传输实现。
图1.控制系统软件与功能
2.3主运动与随动的实现
铺带加工的运动控制存在主运动和随动运动两种情况,主运动是指系统直接运行的运动程序,不受任何其他条件限制,PMAC与传统数控加工运动控制卡类似也具有直线插补和圆弧插补运动方式,而直线插补运动方式最多可以支持8轴联动;此外,PMAC还提供了3次样条插补运动的功能,可实现在曲面上的高精度加工,这样也使5轴沿规定曲线联动成为可能。
而随动是指相对于主运动程序中某一个或多个轴的运动按某种规律精确跟随运动。
铺带的工艺要求预浸带超声切割系统与5轴定位机械平台既相对独立而又在某些特殊情况下必须跟随其运动的一个子系统,所以切割系统的运动方式必须采用随动系统来实现。
这两种运动程序由代码解释器根据用户输入的数据自动生成,并通过PMAC设备驱动
程序下载到PMAC中。
运动程序执行的切换由PMAC运动程序中编写的PLC程序来实现[1]。
2.4系统运动精度与联动实时性
系统精度与实时性主要由相应的运动控制板卡PMAC与动作量数字板卡PCL-725来保证,在PMAC卡中,运动量控制的基本单位是脉冲,经系统传动比例折算,X,Y,Z轴每运动1mm相对应PMAC卡发给电机的脉冲数为6000~12000,而PMAC中后台PLC控制程序运行周期在1ms以内。
这与PCL动作量板卡的实时扫描周期基本同步,动作量的延时也可得到保证。
结论:
简而言之,针对铺带机用数控系统的特殊性,进行了铺带机硬软件系统的设计,采用PMAC,PCL-725,PCL-730分别作为运动量与动作量的控制单元,很好地解决了多轴运动精度要求较高和运动动作联动协调性等问题。
以Windows2000作为系统核心平台,在BCB环境下编写了铺带机软件应用系统,确保了数控加工关键任务的实时性,从而使加工任务更有效地执行,实现了自动铺带的基本功能[2],从而保证了自动铺带机设备的加工能力及产品质量。
参考文献:
[1]叶佩青,廖文和,周来水,等.基于PC平台的计算机数控(CNC)系统开发[J].南京航空航天大学学报,2017,29(2):125-130.
[2]罗华丽,李斌,汤志斌.开放式数控系统中的软件PLC技术研究[J].组合机床与自动化加工技术,2017(2):38-40.。