玻璃电熔炉设计
玻璃工业窑炉 第四章电熔窑第四节电极选型与布置

•多用在小型电熔窑上。 •板状电极损坏时可由它代替。 •能产生强烈对流,热量集中在与电极 相接触耐材,易造成耐材损坏。
4.4.4水冷套 (1)水冷套的作用
由于金属钼的耐热性能特别好,可经受 2600℃的温度,属难熔金属。但它的氧化性能在 温度600℃以上明显加剧,因此,为了保护钼电 极,使其不致很快被氧化,必须采用电极水冷却 装置,否则会影响整个熔炉的正常运转,严重时 将迫使电熔窑停产。
•缺点:当防氧化措施不当时易损坏且更换 困难。池底侵蚀严重时有漏料危险。
•全电熔窑不采用。
③板状电极:
•紧贴布置侧墙上,使电流密度和热量分 布都较匀,电极侵蚀较小,适合硼玻璃 熔制及不希望有强烈对流的部位。如流 液洞、供料道上,能在小区域内均匀加 热,不使耐材过分侵蚀,
•缺点:运行间不能更换。
④塞状电极
缺点:只用于具有还原能力的玻璃,易 使玻璃着色(棕色),接触电阻大,允 许电流密度0.1~0.3A/ cm2,电极直径较 大(150~200mm)。
石墨电极通常水平安装在液面下25mm 处左右,玻璃中金属氧化物着色剂会被 还原成金属,沉淀在电极上,或产生碳 化物,改变玻璃色泽。因此,不能用于 熔制硼玻璃、彩色玻璃和铅玻璃。
③二氧化锡电极
•具有抗氧化作用的陶瓷材料,除用于熔 制 铅 玻 璃 , 还 可 熔 制 含 As2O3 、 CoO 、 Fe2O3的玻璃。
•块 状 ( 砖 块 ) 或 粗 棒 状 ( 12mm ) , 密 度6.8 kg/cm3,耐急热急冷性好,但抗拉 强度低。
•氧化锡电导体具有负的特性,在400℃时 电 阻 率 为 0.8~1.2Ω·cm,1000℃ 为 0.0025~0.0045Ω·cm,因此,须在高温下 向电极供电。
玻璃电熔炉冷却循环水系统的设计

第43卷第5期2015年10月玻璃与搪瓷GLASS &ENAMELV d. 43 N f50;2015玻璃电熔炉冷却循环水系统的设计$赵丽丽,马志纯,莫晓庆(承德华富玻璃技术工程有限公司,河北承德067000)摘要:主要介绍了玫璃电熔炉冷却循环水系统的设计要求及设计要点。
关键词!玫璃电熔炉;冷却循环水;设计中图分类号:TQ171.6+23.2 文献标识码:B文章编号=1000-2871(2015)05-0030-04D O I:10.13588/ki.g.e.1000-2871.2015.05.008Desii^n of Cooling Water Circulation Systemfor Glass Electric Melting FurnaceZ H A O L i-li,MA Zhi-chun,MOXia〇-qing〇引言加热原件是全电玻璃电熔炉中的重要组件之一。
玻璃电熔炉一般使用钼电极做为电熔炉的加热原件,钼电极通过玻璃中的钠、钾离子参与导电,所形成的焦耳热效应对玻璃进行熔化和保温。
然而钼电极在空气中受热时容易氧化,在电熔炉运行中,电极需配备特制水套并且确保有连续不断的冷却水输人到水套中对水套进行冷却,这样才可以使水套与电极之间的玻璃液固化,对电极起到密封加固的作用,从而保证钼电极不被氧化。
因此,电熔炉冷却循环水系统是电熔炉系统中非常重要的设计项目之一。
1冷却循环水系统的设计要求(1) 冷却循环水系统的水压要求:0.1~0.2 MPa。
(2) 冷却循环水的水温要求:20~ 40C。
(3) 冷却循环水的硬度要求:小于40X104,由于水套的结构不同,顶插电极水套一般要求循环水的硬不大于25X10—6。
(4) 尽量避免断水,一旦出现断水,必须有应急处理措施。
(5) 纯净度要求:外观清澈,过滤无砂,无悬浮物。
2冷却循环水系统的组成冷却循环水系统的设计必须满足上述要求,我们以15 t钠钙玻璃全电熔炉为主体进行设计,循环水系统图如图1所"。
玻璃熔窑设计三章.池窑尺寸设计
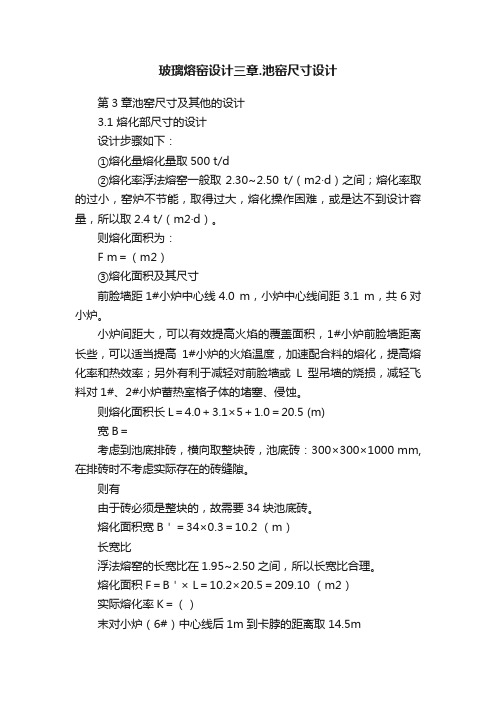
玻璃熔窑设计三章.池窑尺寸设计第3章池窑尺寸及其他的设计3.1 熔化部尺寸的设计设计步骤如下:①熔化量熔化量取500 t/d②熔化率浮法熔窑一般取2.30~2.50 t/(m2·d)之间;熔化率取的过小,窑炉不节能,取得过大,熔化操作困难,或是达不到设计容量,所以取2.4 t/(m2·d)。
则熔化面积为:F m=(m2)③熔化面积及其尺寸前脸墙距1#小炉中心线4.0 m,小炉中心线间距3.1 m,共6对小炉。
小炉间距大,可以有效提高火焰的覆盖面积,1#小炉前脸墙距离长些,可以适当提高1#小炉的火焰温度,加速配合料的熔化,提高熔化率和热效率;另外有利于减轻对前脸墙或L型吊墙的烧损,减轻飞料对1#、2#小炉蓄热室格子体的堵塞、侵蚀。
则熔化面积长L=4.0+3.1×5+1.0=20.5 (m)宽B=考虑到池底排砖,横向取整块砖,池底砖:300×300×1000 mm,在排砖时不考虑实际存在的砖缝隙。
则有由于砖必须是整块的,故需要34块池底砖。
熔化面积宽B'=34×0.3=10.2 (m)长宽比浮法熔窑的长宽比在1.95~2.50之间,所以长宽比合理。
熔化面积F=B'× L=10.2×20.5=209.10 (m2)实际熔化率K=()末对小炉(6#)中心线后1m到卡脖的距离取14.5m则熔化部长L'=14.5+L=35 (m)F熔化部=B'× L'=10.2×35=357.0 (m2)合理。
熔化部的长宽比''3.2 池窑深度池深选取选取h=1.2 m选取浅池的原因是减少玻液的回流,节能效果好;由于上层玻璃液液流厚度与熔化池深成正比,池深变浅,上层液流厚度随之减少,有利于玻璃液澄清,提高玻璃的质量。
但是浮法玻璃含铁量较低,玻璃液热透射性较强,将使池底温度提高较多,池底玻璃液的流动性增强,对池底砖的冲刷加剧,所以在池底结构上要选择较好的铺面砖,本设计选取电熔无缩孔锆刚玉砖。
玻璃熔窑设计规定 日用玻璃熔窑设计的基本规定

日用玻璃熔窑设计的基本规定一、总则1.0.1玻璃熔窑是玻璃工厂中最重要和投资最大的设备。
为了确保熔窑设计质量,避免因设计失误给企业带来损失,制定本规定。
1.0.2新建或改扩建的玻璃熔窑应由有资质的设计单位承担设计或设计后的审核。
窑炉设计中对工艺、土建、风、水、电、仪表控制等专业的具体要求必须与熔窑设计图纸一同存档备案,以作为今后各阶段检查的依据。
1.0.3玻璃熔窑的设计,除应按本规定执行外,还应符合国家现行有关标准的规定。
1.0.4本规定可作为玻璃熔窑设计、施工、质量验收、生产运行直至事故分析各个阶段检查的依据。
二、能源的确定2.0.1玻璃熔窑使用的能源应根据国家能源政策,燃料成本,控制、使用、购入的难易程度以及环保规定等条件进行选择。
鼓励使用含低硫的优质燃料,从源头削减污染。
2.0.2以发生炉煤气为燃料的玻璃熔窑,宜用少量的燃料油、天然气、城市煤气或电作为辅助能源,供熔窑作业部或分配料道单独加热用,但其用量按热量计算不宜超过全窑能耗的5%。
严格限制用发生炉冷、热煤气和水煤气作为作业部或分配料道的加热热源。
三、熔窑规模的确定3.0.1以重油、天然气、发生炉煤气为主要燃料的新建玻璃熔窑应达到表3-1中所列规模。
3.0.2利用现有厂房的改造项目,应尽可能在满足表3-1所列的条件下,根据现有厂房、现有能源等条件确定熔窑规模。
四、玻璃熔窑主要技术指标的确定4.1玻璃熔制质量新建或改扩建玻璃熔窑的玻璃熔制质量应达到表4-1中所列要求。
4.2玻璃熔化能耗4.2.1玻璃熔化能耗(kgce/t玻璃液)系指玻璃熔窑每熔化1t玻璃液所消耗的能源转化为千克标准煤(kgce)。
其计算公式为:玻璃熔化能耗(kgce/t玻璃液)=全年玻璃液能耗(kgce)/年熔化玻璃液数量(t)(1)计算公式是以熔窑投产后第三年度实际运行数据为考核基准,其它年度的玻璃液熔化能耗应按每减增一年相应减增1.5%,折算成第三年度的能耗指标。
(2)地区气温对玻璃熔化能耗基准值的影响按下列原则修正:长江以南地区减少2%,长城以北地区增加2%,其它地区不变。
高硼硅玻璃全电熔窑炉设计分析

高硼硅玻璃全电熔窑炉设计分析摘要:随着社会的发展,高硼硅玻璃逐渐得到广泛使用。
高硼硅玻璃具有多种生产方式,其中全电熔窑炉具有操作便捷、维护成本低、环保等特点,因此,许多玻璃生产企业都采用这种方法生产该种玻璃。
基于此,本文简单讨论高硼硅玻璃生产工艺的控制要点,并对全电熔窑炉的设计策略进行分析,以供参考。
关键词:高硼硅玻璃;全电熔窑炉;玻璃生产工艺引言:高硼硅玻璃不但具有高硬度与高强度,还具备高透光率,且化学性质稳定,因此受到了广泛的应用。
目前,高硼硅玻璃主要应用于日常生活、化工、军事等各个方面。
因此,对于高硼硅玻璃要选择合适的生产方式,并加强生产工艺的控制,才能使玻璃的质量得以保证。
1.高硼硅玻璃生产工艺的控制要点1.1料层厚度的控制在高硼硅玻璃进行熔化的时候,需要较高的温度,且不易澄清,因此,无法使用传统的澄清剂对其澄清。
在实际过程中,要使用NaCl进行澄清,但是,由于其沸点为1465℃,所以在高温状态下NaCl易扩散到玻璃液的残留气泡中,最后溢出。
在高硼硅玻璃的生产过程中,由于料层的厚度过大,NaCl蒸气会在溢出时在料层上凝结,并在表层的配料内部残留。
NaCl具有较好的导电性,且熔点较低,因此,表层材料中的NaCl在不断累积的过程中,会导致窑炉内的电流集中在表层,使表层的温度升高,进而出现红顶现象。
因此,为了避免这种问题的出现,要将料层的厚度控制在1cm到1.5cm左右[1]。
1.2硼挥发的控制关于硼挥发的控制,首先要进行料道溢流的设计,使其不但能够符合流体流动的原理,还能够符合玻璃变质层对专用的溢流结构中的黏度与温度的需要。
由于玻璃变质层黏度较强,因此不易溢流,为此,要在溢流的位置设置燃烧器,并使用电加热的手段升高温度,使得溢流能够顺利进行。
其次,要想避免出现通路中的硼出现挥发问题,要对料道进行封闭。
由于玻璃液会对耐火材料产生腐蚀,因此要采用合适的盖板砖,并降低玻璃液的温度,从而能够最大程度上减少腐蚀现象的发生。
平板玻璃熔窑电助熔设计与计算

0引言玻璃液在高温熔融状态下是一种电导体。
电熔化已在玻璃行业广泛使用,电助熔热效率高、玻璃的热稳定性和均匀性好,具有提高玻璃质量和降低能耗等优点,有广阔的发展空间。
传统大型平板玻璃熔窑电助熔负荷未超过10%,节能效果有限,实现节能减排技术性突破,增大电助熔负荷势在必行。
平板玻璃熔窑稳定的玻璃液流和合理的液流位置及形态对玻璃熔窑的操作至关重要,电助熔玻璃熔窑的电功率输入及位置设计同样要以保证玻璃熔窑的配合料层、环流Ⅰ、环流Ⅱ以及生产流的稳定为前提。
电助熔功率分配和分区设计及电极布置是电助熔玻璃熔窑的设计难点和设计关键,需结合火焰空间热负荷保证工艺制度和温度梯度,为保证设计合理,必要时需借助数学模拟或物理模型等辅助手段。
1电助熔玻璃熔窑的设计与计算(1)电助熔加热功率及装机功率计算普通平板玻璃(12%碎玻璃)理论熔化热由以下几部分组成:①生成硅酸盐耗热:272 kJ/kg玻璃液;②玻璃液加热至1400 ℃所需热量:1842 kJ/kg玻璃液;③生成玻璃耗热:314 kJ/kg玻璃液;④蒸发水分耗热:104 kJ/kg玻璃液;理论熔化总热耗:2533 kJ/kg玻璃液(不含玻璃液生成气加热耗热),转换为电能为0.7 kWh/kg玻璃液,考虑到电极水套及变压器等能量损失,电助熔的热效率可达85%~90%,那么玻璃液所需输入功率为32~34 kW/t玻璃液(不包含窑炉散热损失),装机功率按40~45 kVA/t玻璃液配置。
(2)电助熔分区设计投料口区域池底温度低,一般理所当然地认为电助熔大部分功率应增设在该区域,事实上国内确实有厂家这样分区布置电助熔,但效果并不理想。
对此做数学模拟,方案1:前置四区均布电极,装机功率3600 kVA;方案2:前区均布三排电极,装机功率1500 kVA,热障区两排电极,装机功率2100 kVA 。
图1为600 t/d颜色玻璃电助熔数学模拟玻璃液流示意图。
图1 600 t/d颜色玻璃电助熔数学模拟玻璃液流示意图数学模拟对比显示,方案1池底热点前移,较大地改变了玻璃窑炉纵向液流形态,不利于玻璃的熔化和澄清。
Pylex玻璃熔窑设计概述
作者简介 作者于1 年毕业于山东 7 9 9 轻工业学院.同 年入力诺集团有限资任公司工作至今, 先后从事车间工艺员、 窑炉设计和 施工、车间 主任等工作,现任窑炉工程部部长,负资窑炉设计、 施工等工作.
图 1我公司 3 平方米蓄热室马蹄焰燃天然气池窑示愈图 7
考虑,卜 部为气孔率小于 1 的低气孔粘土砖, 5 % 上部为气孔率小于 1 的低气孔粘土砖,实践证明, 3 % 此 种砖材使用周期约为 1 个月,一个周期后要进行热换, 8 影响生产5 天。 至6
32小炉 .
321小炉内倾角度 . . 我公司 开始几台池窑小炉内 倾角度 ( 即小炉中 心线与池炉纵向中心线之间的夹角)为0 在池炉 0, 运行过程中发现挂勾砖烧损严重,于是将内 倾角调整为 3 调整后虽然增加了砌筑难度, 0, 但达到了 预 期的效果,挂勾砖的烧损大大的减轻了。 322小炉口尺寸 .. 原设计单个小炉口 宽度为 1 0 3 毫米,在运行过程中,大炉火焰较长,对前墙烧损严重: 0 通过调整 天然气喷枪,虽也能将火焰缩短, 但火焰形状不够理想。在以后的设计中, 将小炉口宽度调整为 1 0 3 5 毫米,高 度不变, 如此, 喷火口 面积增大, 助燃风喷出 速度减小, 火焰相应缩短。
因Plx ye 玻璃熔化难度较大, 且在池深方向容易分层, 故在池深的设计方面较为谨慎。 池深较小, 玻璃液面与池底温差小, 玻璃液分层趋向小, 但熔化率小: 池深较大,玻璃液面与池底温差大, 玻璃液 分层趋向 大, 但如果池深设计恰当, 熔化率会增加。 初始设计时池深为70 0 毫米. 运行一段时间 无问 题 后作了 调整,窑坎后熔化区设为80 0 毫米, 窑坎前澄清区仍保持 70 0 毫米,运行中 取得了 一定的效果。
熔化温度高
理论熔化温度 ( =1 帕 ・ q 0 秒时)可达 18` 60 C,比普通钠钙硅玻璃高出将近 30 0' C.
全电熔窑炉课程设计
课程设计说明书日产8吨硼硅玻璃全电熔窑炉的设计班级:无机1001姓名:***学号:**********指导教师:***时间:2013.7目录前言 (3)1.电熔窑概述 (4)1.1玻璃电熔窑原理 (4)1.2电熔窑的优点 (5)2.设计任务与要求 (5)3.电熔窑的设计 (6)3.1电熔窑的形状与尺寸 (6)3.2电极的选择与布置 (7)3.3供电方式 (7)4.电熔窑的计算 (7)4.1 各原料用料的计算 (7)4.2电熔窑的热——电平衡 (10)4.2.1 生料熔化耗热量的计算 (10)4.2.2熟料加热熔融耗热量的计算 (12)4.2.3配合料水分蒸发耗热量的计算 (13)5.窑体散热计算 (13)5.1窑墙散热计算 (14)5.2窑底散热计算 (16)5.3窑炉上部结构热损失 (16)6.冷却水带走的热量 (17)7.结语 (17)参考文献 (18)前言自从 1902年德国沃尔克 (Voker)利用离子高温导电取得玻璃电熔技术专利后,世界上就揭开了玻璃电熔的一页。
在 1920~ 1925年间, 瑞典、挪威先后将电熔窑投入生产后, 玻璃电熔就正式进入了工业领域。
随着全球能源危机加剧,引起世界各国对能源有效开发利用的高度重视。
玻璃制造业是一个高耗能的行业,使用传统的火焰炉生产高硼硅玻璃,一次性投入成本高,产品实现过程中仅能源运行成本就占总成本的 40% ,且受熔炉结构影响,产品质量的制约因素较多。
由于电熔窑具有独特明显的优越性,发展迅猛, 遍及世界各地,尤其是在电源丰富、电价低廉的地区和生产特种难熔的制品时。
进入 21世纪后,更成为玻璃熔窑改革的一个主要方向。
各种计算机辅助设计软件,如AUTOCAD,提供了强有力的绘图、设计、图像编辑和变换功能,能绘制各种二维和三维图形,能有效的帮助设计人员表达设计思路。
计算机辅助设计在机械、化工、建筑、电气、造船、轻工等部门都得到了广泛的应用,并且取得了巨大的经济效应。
玻璃熔窑设计
合肥学院Hefei University无机非金属材料工艺课程设计题目:浮法平板玻璃熔窑生产设计系别:化工系专业:无机非金属学号:1203031001姓名:彭冲导师:张全争2015年12月摘要设计介绍了一套规模为900t/d浮法玻璃生产线的工艺流程,在设计过程中,原料方面,对工艺流程中的配料进行了计算;熔化工段方面,参照国内外的资料和经验,对窑的各部位的尺寸、热量平衡和设备选型进行了计算;分析了环境保护重要性及环保措施参考实习工厂资料,在运用相关工艺布局的基础下,绘制了料仓、熔窑、锡槽、成品库为主的厂区平面图,具体对熔窑的结构进行了全面的了解,绘制了熔窑的平面图和剖面图,还有卡脖结构图,整个设计参照目前浮法玻璃生产的主要设计思路,采用国内外先进技术,进行全自动化生产,反映了目前浮法生的较高水平。
关键词:浮法玻璃、熔窑工段、设备选型、工艺计算AbstractThe design introduced the technical process of 900t/d float glass production line. During the planning, for the raw material, the computation of material has been made; and for the melt section, the melting kiln various spots size, The heat balance and the choose of the equipment have been calculated with reference to the domestic and foreign materials and the experience, the environmental protection importance and environmental protection measure have been analyzed. With reference to factory date, under the technology arrangement correlation knowledge foundation, the factory horizontal plan about the storage, the melting kiln, the tin trough and product storage has been finished. The melting kiln structure has been concretely introduced, the horizontal plan and the sectional drawing of the melting kiln, small mouth composition and card neck structure drawing have been draw up. The entire design consulted the main design mentality of present float glass production; took the domestic and foreign advanced technologies; carried on the entire automated production; reflected at present floats production to compare the high level.keywords: float glass; melting section; choose of the equipment; process calculation.目录前言 (1)第一章浮法玻璃工艺方案的选择与论证 (2)1.1平板玻璃工艺方案 (2)1.1.1有曹垂直引上法 (2)1.1.2垂直引上法 (2)1.1.3压延玻璃 (2)1.1.4 水平拉制法 (3)1.2浮法玻璃工艺及其产品的优点 (3)1.3浮法玻璃生产工艺流成图见图1.1 (4)图1.1 (4)第二章设计说明 (5)2.1设计依据 (5)2.2工厂设计原则 (6)第三章配料计算 (7)3.1于配料计算相关的参数 (7)3.2浮法平板玻璃配料计算 (7)3.2.1设计依据 (8)3.2.2配料的工艺参数; (8)3.2.3计算步骤; (10)3.3平板玻璃形成过程的耗热量的计算 (14)第四章熔窑工段主要设备 (15)4.1浮法玻璃熔窑各部 (16)4.2熔窑主要结构见表4.1 (16)4.3熔窑主要尺寸 (18)4.4熔窑部位的耐火材料的选择 (19)4.4.1熔化部材料的选择见表4.3 (19)4.4.2卡脖见表4.4 (20)4.4.3冷却部表4.5 (20)4.4.4蓄热室见表4.6 (20)4.4.5小炉见表4.7 (20)4.5玻璃熔窑用隔热材料及其效果见表4.8 (21)第五章玻璃的形成及锡槽 (23)第六章玻璃的退火及成品的装箱 (25)第七章除尘脱硫工艺 (26)7.1除尘工艺 (26)7.2烟气脱硫除尘 (26)参考文献 (27)前言英国Pilkington兄弟在20世纪50年代浮法玻璃生产技术的发明付出了坚持不懈的努力,自1953年开始到1959年取得了成功耗时7年,投入了400万英镑。
日产700吨平板玻璃电助熔窑炉设计
J I A N G S U U N I V E R S I T Y本科毕业论文日产700吨平板玻璃的电助熔窑炉的设计Design of Electric Boosting for Daily Output 700 Tons ofFlat Glass学院名称:专业班级:学生姓名:指导教师姓名:指导教师职称:2015年6月日产700吨平板玻璃的电助熔窑炉的设计专业班级:学生姓名:指导老师:职称:摘要:在我国,平板玻璃已被国务院列为六大产能过剩行业之一,成为淘汰落后产能的重点目标。
因此,如何低污染、低排放地生产出能与欧美家国相媲美的玻璃成为行业研究的重点。
本文根据近几年的研究成果,介绍了一种经济环保同时又能提高玻璃质量和产量的技术——玻璃电助熔技术,并尝试应用在南方玻璃厂横火池窑上,使其在原有基础上增产达到日产700吨优质平板玻璃。
本文介绍了玻璃电助熔窑炉的发展状况,并且根据原始资料以及查阅的相关文献,进行热工计算、电工参数计算确定了电极的选用和布置,并应用AUTO CAD作出了电极布置图。
针对玻璃窑炉的高能耗问题,本文进行用能分析,提供节能途径进行改善。
关键词:平板玻璃横火池电助熔电极耗能节能Design of Electric Boosting for Daily Output 700 Tons ofFlat GlassAbstract In China, the flat glass has been listed as one of the six major industries of the State Council, has become the focus of the elimination of backward production targets.Therefore, how to low pollution, low emission production can be comparable with the European and American domestic glass become the focus of industry research.The according to the research results in recent years, introduces the economic environmental protection and can improve the technique of glass quality and yield of glass electric melting technology, and try to application in the Southern Glass Factory cross fire pool kiln, making it in the original basis yield reached Nissan 700 tons of high quality flat glass.The development of glass electric melting furnace is introduced in this paper, and according to the original data and access to relevant literature, thermal calculation, electrical parameter calculation to determine the selection and arrangement of the electrode, and the application of Auto CAD made electrode layout.In view of the energy consumption of glass furnace, this paper can analyze and provide energy saving way to improve.Keywords: Flat glass Cross-fired Electric-Boosting ElectrodeEnergy-guzzling Energy-saving目录第一章绪论 (1)1.1引言 (1)1.2玻璃电熔的原理 (2)1.3玻璃熔窑的分类 (3)1.4玻璃电熔的分类 (4)1.4.1全电熔窑炉 (4)1.4.2电气混合窑炉 (5)1.4.3电助熔窑炉 (5)第二章火焰池窑的电助熔的意义 (5)2.1池窑电助熔的优缺点 (5)2.1.1大幅度提高熔化率 (5)2.1.2 提高玻璃的熔化质量 (6)2.1.3减弱上部火焰空间的燃烧强度、延长炉龄 (6)2.1.4灵活调节出料量 (6)2.1.5稳定点和加强有效对流 (7)2.1.6节能环保 (7)2.1.7缺点 (7)2.2电助熔技术的经济分析 (7)第三章电助熔池窑的设计 (6)3.1 设计依据 (8)3.2热工计算 (10)3.3电助熔加热功率的计算 (11)3.4电极 (12)3.4.1电极选用 (12)3.4.2电极布置 (13)3.4.3电工参数计算 (15)3.4.4电极水套 (17)3.5电助熔池窑耐火材料的选择 (18)第四章设计结果 (19)第五章节能分析与改进措施 (20)5.1节能分析 (20)5.1.1能耗分析 (20)5.1.2节能途径 (21)5.2改进措施 (21)总结 (22)致谢 (23)参考文献 (24)第一章绪论1.1引言平板玻璃也称白片玻璃或净片玻璃,大部分属于钠钙硅酸盐玻璃。
- 1、下载文档前请自行甄别文档内容的完整性,平台不提供额外的编辑、内容补充、找答案等附加服务。
- 2、"仅部分预览"的文档,不可在线预览部分如存在完整性等问题,可反馈申请退款(可完整预览的文档不适用该条件!)。
- 3、如文档侵犯您的权益,请联系客服反馈,我们会尽快为您处理(人工客服工作时间:9:00-18:30)。
窑炉课程设计说明书题目:年产3000吨高硼硅玻璃电熔窑炉的设计目录前言 ............................................................................................................................ 错误!未定义书签。
一、设计任务及原始资料 (3)1.1 设计题目: (3)1.2 设计技术指标、参数: (3)二、窑型选择 (4)三、窑体主要尺寸选择 (5)3.1 熔化池面积 (5)3.2熔化池的长度和宽的 (6)3.3 熔化池的深度 (7)四、电极材料的选择及插入方式 (8)4.1 电极材料的选择 (8)4.2 电极尺寸的选择 (9)4.3 电极插入方式选择 (10)4.2 电极连接方式选择 (11)五、耐火材料的选择与计算 (12)5.1耐火材料的选择 (12)5.2耐火材料的计算 (13)六、窑炉电工热工计算 (14)6.1玻璃熔化热计算 (14)6.2 玻璃耗电量计算 (15)6.3玻璃热效率计算 (15)七、小结 (16)参考文献 (16)前言玻璃电熔技术是目前国际上最先进的熔制工艺,是玻璃生产企业提高产品质量,降低能耗,从根本上消除环境污染的十分有效的途径。
对于15t/d以下的小型玻璃熔窑来说,在电力充足和电价适中的地区,用电熔工艺来生产各类玻璃制品的综合经济效益是很理想的;在电价较高的地区,对于彩色玻璃、乳浊玻璃、硼硅酸盐玻璃、铅玻璃、高挥发组分玻璃或特种玻璃生产也是合算的。
过去我国小型电熔窑的应用一直进展不太大,主要原因有两条:首先是人们普遍认为电熔的价格昂贵,熔制成本高,忽视了电熔可带来的整体效益;其次,以往引进的国外电熔窑由于包含大量的技术费用,选材过于讲究,因而投资很大,一座熔化面积不到2m2,日产量4吨的小型电熔窑,少则二三百万元,多则近千万,对于生产一般玻璃制品来说,是难以接受的。
即使引进了也往往因为折旧费用过高而被迫停用。
我们设计的电熔窑,以我国的国情为基础,根据产品特点确定适当的窑龄,着重考虑综合经济效益,大量采用国产优质材料,在满足产品质量要求的前提下,大大降低了电熔窑的造价。
以上述规模的电熔窑为例,包括电极和全套电熔自动控温装置在内的设备投资只需约100万元,每次冷修费用也不过十余万元,为玻璃全电熔技术的广泛应用创造了条件。
玻璃熔窑有如下优点:没有废气,防止空气污染;降低挥发性配合料组分的挥发;玻璃均匀;降低因结石造成的产品损失;在节假日停产后恢复生产的1困难较少;熔窑大修较快;在整个窑期内可始终保持满负荷的出料量;占地面积小;二氧化碳的回收;热量散失减少;玻璃质量好、效率高、成本低;建设投资少;全电熔窑易于调节控制,操作范围广,热工制度比池炉稳定。
总之,在环保要求严格、电价低兼、玻璃熔化困难、玻璃质量要求高、生产规模小时可考虑全电熔窑。
2一、设计任务及原始资料1.1设计题目:年产3000吨高硼硅玻璃电熔窑炉的设计1.2设计技术指标、参数:1、坯料的化学组成(%):2.熔窑生产能力: G=3000/300=10t/d;3.熔化率:k=1500kg/(m2・d);4.k系数:K=0.3;5.玻璃熔化温度:t=1450 ℃;6.玻璃液密度:ρ=2.4 t/m3;7.窑炉长宽比:L/B=1~1.5;3二、窑型选择我国熔制硼硅酸盐玻璃的电熔窑大多为小型窑,冷顶电熔窑与火焰窑相比具有节能、提高质量、降低成本等显著的优越性。
(1)小型电熔窑有较好的经济性,以日产2.0吨的高硼硅玻璃球窑为例,从燃料和硼挥发两顶进行比较如表1表1(2)玻璃质量好,在火焰池窑中由于窑温、窑压、气氛和产量等工艺条件发生变化,都要引起硼的挥发率的变化,使玻璃不均匀。
同时火焰窑和热顶电熔窑,硼的挥发严重腐蚀了上部结构,不但缩短了窑炉的寿命,而且碹滴落入玻璃窑内,影响了玻璃质量。
冷顶电熔窑完全可以避免上述弊病,获得高质量的玻璃。
本窑炉产量为10t/d。
选用小型电窑。
4三、窑体主要尺寸的确定3.1 熔化池面积在确定电熔窑主要尺寸之前,首先要知道所熔制的玻璃成分和窑的日熔化量,电熔窑的熔化率取决于玻璃的种类、电熔窑的大小。
玻璃电熔窑的热量是通过所熔化的玻璃的整个体积引入的,应以每天、每立米的体积熔化量来确定电熔窑的结构。
表2是现有的一些全电熔窑的面积熔化率。
表2 5由于配合料的熔化过程仍在窑池表面进行。
因此,熔窑的融化池面积让可以用下式计算:F熔 =G/K式中:G ——熔窑的生产能力,kg/d;K ——熔化率,kg/(m2・d)。
则:F熔=10/1.5=6.67(m2)。
3.2熔化池的长度与宽度L/B越大,投入窑炉的玻璃原料从熔化到完成澄清,其间的玻璃“行程”越长,也越有利于熔化和澄清。
早期设计的单元窑熔他是很长的,日产量在8—50t/d,(L/B)5—4。
随着单元窑配合料微粉化及熔制工艺和鼓泡技术的发展与成熟,以及窑体耐火材料的质量提高和采用保温技术等措施,使熔池长宽比在3左右,也同样可以获得满意的玻璃质量。
为了提高熔窑的热效率,熔窑的散热比表面积应比较小,熔化池的长度L和宽度B之比,应符合下面条件:L/B=1~1.5取L/B=1则:L=2.58 m,B= 2.58 m。
63.3熔化池的深度电熔窑的深度H取决于在其中连续进行熔化、澄清和冷却三个层次的厚度。
很明显,玻璃的熔化率将影响各个层次的厚度,而不同组分的玻璃的熔化率是由配合料的熔透速度和玻璃液完全排除气泡在高温区逗留时间决定的。
因此,电熔窑窑深(或高度)H,可由下列经验公式计算:H=0.1+h1+h2+h3式中:0.1——通常控制的配合料层高度,m;H1——配合料与熔体接触面到上排电极上边缘的距离,m;H2——高温区的高度,m;H3——下排电极下边缘至窑底得距离,m。
配合料与熔体接触面到上排电极上边缘的距离,可以按下式计算H1=kb=0.3*成对电极之间的距离=0.3*1.38=0.414 mH2=0.84*k/ρ=0.525 mH3=1.1 m则:H=0.1+h1+h2+h3=0.1+0.414+0.525+1.1=2.1 m7四、电极选择及插入方式4.1电极材料选择金属电极中以钼电极最为普遍,除含铅玻璃外,是对多种玻璃熔制都适用的材料。
钼的熔点高,导电性好,机械强度大,热膨胀系数底,加工容易,不污染玻璃液,是比较理想的电极材料。
1986年某厂从Sorg公司引进一座铅晶质玻璃全电熔窑,该电熔窑的熔化池呈六角形,电极分布在三面池墙上,按△接法或Y接法与三相变压器连接。
其优点是允许三相有均衡的负荷。
电熔窑横截面电流分布比较均匀。
有利于配合料均匀熔化。
熔化池与澄清池面积基本相同。
熔化池装有三层直径48mm的钼电极。
设计熔化能力5.4~6.6T/d。
该电熔窑容量大,玻璃液在熔化池逗留时间较长。
熔化率为2.6T/m2·d,单耗为1.12kW·h/kg玻璃。
该电熔窑的熔化量具有较大的潜力。
其“翻转限”仅比最大熔化量低20%。
在熔制铅玻璃时,由于钼和氧化铅等发生氧化—还原反应,使钼电极受到腐蚀。
所以应适当降低电流密度,以减少钼电极损耗,相应减少铅损失,提高玻璃质量,延长窑炉寿命。
84.2电极尺寸选择(1) 玻璃液电阻率与温度有关a=3.8306+0.003761*0.8+0.0326*0.12+0.08514*0.003+0.1776*0.051=5.4 706;b=1.7738+6.254*100000*0.8+0.0087*0.12+0.058*0.003-0.0539*0.051=1.6257。
.则:=12.88 Ω・cm;两根水平放置的棒状电极间玻璃液电阻为:R=n1*n2*(ρ)/(3.14*l)*Ln(b/r)=1.1*1.3*12.88/3.14/100*Ln(138/2.5)=0.24Ω;(2)电熔窑总功率PP=G*q=10000/24*2.4=1000 kw(3) 电熔窑电压 V和电熔窑电流 I电熔窑通常采用隔离变压器供电。
一次电压采用可控硅恒温、恒压(或恒流)控制仪控制,变压器二次侧通过电极向熔体供电。
计算出的电压和电流,既能供操作时参考,又能用来复核事先选定电极大小和布置位置是否合适。
电熔窑的电流、电压按下式计算:9=⨯103式中P为电极功率,R为电阻。
=⨯103,I P RV PR电压的选择原则:小于耐火材料的最低击穿电压。
在保证安全的情况下,尽可能选用高电压,以便降低二次电流。
这有利于降低变压器的负载和电极的成本。
电压、电流在可控范围内调节的幅度应有较大余量。
则:上层电极电压电流,V PR=⨯103=268.3 vI P=⨯103=1118 AR下层电极电压电流,V PR=⨯103=219.1 vI P=⨯103=912.9 AR(4)电极电流密度 jJ上=I/A=1118/(3.14*2.5*2.5+3.14*5*60)/2=0.6 (A/cm2)J下=I/A=912.9/(3.14*2.5*2.5+3.14*5*60)/2=0.5 (A/cm2)4.3电极插入方式选择电极插入深度与电极性质、数量、电流密度、电熔窑结构等因素有关。
如圆柱形氧化锡电极采取垂直安装方式,插入深度约为250mm,在电熔窑运行期间电极不能推进。
如棒状钼电极水平安装,插入深度为300~600mm。
随着钼电极逐渐消耗,电极间玻璃电阻不断增加,变压器电压不断升高(使电流10保持恒定)。
当变压器电压调到极限,应推进钼电极,电流、功率诸参数才能恢复正常。
水平棒状电极是最普遍的布置方式之一。
电极或电极对相对布置,电流密度呈层状分布。
电极间的距离必须大一些,可避免电流前驱电流密度过大。
电极端部之间的自由距离应大于电极插入部分长度的两倍。
电极长度与其直径之比应小于20.电极于池深1/3~1/2侧墙处插入窑内50~90cm。
采用两层四对电极供应,第一层电极与第二层电极的负荷分配之比为60:40。
4.4电极连接方式当采用单相电源,电流从窑炉的一侧墙流向另一侧墙。
不论采用板状或棒状电极,电流从池壁的一侧流向另一侧,都能达到均匀分布的温度场。
单相系统多用于正方形或长方形、低容量的电熔窑上,即日产量不超过30T,功率可达1500Kw,一般不会出现相负荷的平衡问题,即使出现也可以使用相平衡设备。
板状或棒状电极间的距离,可根据需要来调节,以达到均匀且较小的电流密度。
为整个窑池内创造均匀熔化和澄清的良好条件。
11五、耐火材料选择与计算5.1耐火材料的选择合理选用全电熔窑各部位耐火材料,以满足熔制工艺上的要求,直接关系到电熔窑的产量、玻璃的质量、电熔窑的寿命、投资的成本。
因此必须充分重视。
全电熔窑对耐火材料的要求:(1)对玻璃无污染或污染程度很小,(2)在正常使用温度下,必须具有很高的化学稳定性,能抗配合料和玻璃液的侵蚀,相邻耐火材料之间无接触反应。