沸腾炉的设计年产6万吨锌冶炼沸腾焙烧炉设计
鲁奇式大型焙烧炉的参数分析与结构改进

精矿 含硫 量 的低 限。
床能率 由综 合 因 素 决 定 , 大 小 取 决 于 流态 化 其
层 的操 作 气流 速度 、 鼓风 量和 流化 层 内的温 度 , : 即
Ⅱ=8 0 操 /V ( +p 层) 64 0 作 1 t
下降 , 反之亦 然 。 因此 , 在设 计 中确定 床 能 率 和 日处
理量 时 , 特别 注意精 矿含 硫量 的稳 定性 , 宜选 择 要 不
作者简介 : 袁富明( 9 9 , , 16 一)男 高级工程师 , 主要从事冶金炉窑及土 建的设计 、 工 、 施 监理工作 。
反 应愈 充分 , 砂质 量愈 好 ; 焙 另可 使 流 化层 物 料 容量
锌精 矿流 态 化 焙 烧 炉 正 常 生 产 时 , 化 层 是 变 流
化 的 , 化层 高度 一般 由炉 料在 炉 内停 留 时间 、 化 液 流
速度 、 风量 ) 变 的条 件 下 , 精 矿 中的 含硫 量 增 鼓 不 若 加, 而鼓入 空 气 量不 变 , 脱 硫 量 不 能增 加 , 维 持 则 为
增 加 , 内的热 容 量增 加 , 态 化 状 况 稳 定 , 于操 层 流 易
作, 方便 布 置排 热 装 置 ; 是 流 化 层 过 高 , 必 增 加 但 势 鼓 风机 压力 , 力消耗 增 大 。而 流化 层 高 度过 低 , 动 容
湖 南有 色金 属
第2 6卷
易产 生气 沟 , 常稳定 的流 态化难 以维 持 。 正 根 据锌 精 矿 焙 烧 物 料 在 流 化 层 内平 均 停 留时 间 , 以确定 流化 层高 度 , : 可 即
锌沸腾焙烧炉工艺操作规程
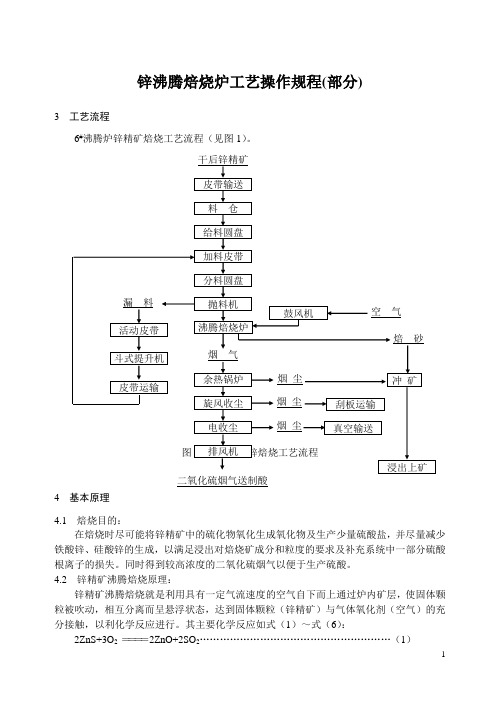
锌沸腾焙烧炉工艺操作规程(部分)3 工艺流程6#沸腾炉锌精矿焙烧工艺流程(见图1)。
44.1 焙烧目的:在焙烧时尽可能将锌精矿中的硫化物氧化生成氧化物及生产少量硫酸盐,并尽量减少铁酸锌、硅酸锌的生成,以满足浸出对焙烧矿成分和粒度的要求及补充系统中一部分硫酸根离子的损失。
同时得到较高浓度的二氧化硫烟气以便于生产硫酸。
4.2 锌精矿沸腾焙烧原理:锌精矿沸腾焙烧就是利用具有一定气流速度的空气自下而上通过炉内矿层,使固体颗粒被吹动,相互分离而呈悬浮状态,达到固体颗粒(锌精矿)与气体氧化剂(空气)的充分接触,以利化学反应进行。
其主要化学反应如式(1)~式(6):2ZnS+3O2 ====2ZnO+2SO2 (1)ZnS+2O2====ZnSO4 (2)3ZnSO4+ZnS====4ZnO+4SO2 (3)2SO2+O2 2SO3 (4)ZnO+SO3 ZnSO4 (5)XZnO+YFe2O3XZnO.YFe2O3 (6)5 原材料质量要求5.1 入炉混合锌精矿:应符合Q/ZYJ06.05.01.01—2005《混合锌精矿》的规定。
5.1.1 化学成分(%):Zn≥47 S:28~32,Fe≤12,SiO2≤5,Pb≤1.8,Ge≤0.006,A s≤0.45 ,Sb≤0.07,Co≤0.015 Ni≤0.004。
5.1.2 水分:6%~8%。
5.1.3 粒度小于14mm,无铁钉、螺帽等杂物。
5.2 工业煤气(%):应符合Q/ZYJ15.02.01—2003《工业煤气》的规定。
要求煤气压力在3000Pa以上,煤气流量不小于6500m3/h。
6 工艺操作条件6.1 沸腾焙烧6.1.1 鼓风量:14000 Nm3/h~30000Nm3/h6.1.2 鼓风机出口压力:12kPa~16kPa6.1.3 沸腾层温度:840℃~920℃6.1.4 炉气出口负压:0~30Pa6.2 余热锅炉6.2.1 出口烟气温度:340℃~390℃6.2.2 出口烟气压力:-100Pa~-200Pa6.2.3 汽包工作压力:4.01MPa±0.3MPa6.2.4 过热器出口蒸汽温度:380℃~450℃6.2.5 给水温度:100℃~105℃6.3 旋涡收尘器6.3.1 入口烟气温度:330℃~380℃6.3.2 出口烟气温度:320℃±10℃6.3.3 入、出口烟气压差:800Pa~1200Pa6.4 电收尘6.4.1 入口烟气温度:280℃~340℃6.4.2 出口烟气温度:≥235℃6.4.3 出口烟气压力:-2450Pa~-2700Pa6.5 排风机6.5.1 入口烟气温度:210℃~300℃6.5.2 入口烟气压力:-2650Pa~-2900 Pa6.5.3 出口烟气温度:≥210℃7 岗位操作法7.1 司炉岗位7.1.1 开炉操作7.1.1.1 开炉前做好设备、安全和环保方面的检查工作:应对所有设备进行一次全面细致的检查,确认各设备、仪表完全具备开炉条件;要对烟气系统各阀门、人孔门,煤气和供水、排水排汽系统进行检查,确认其符合安全环保要求。
沸腾炉的设计
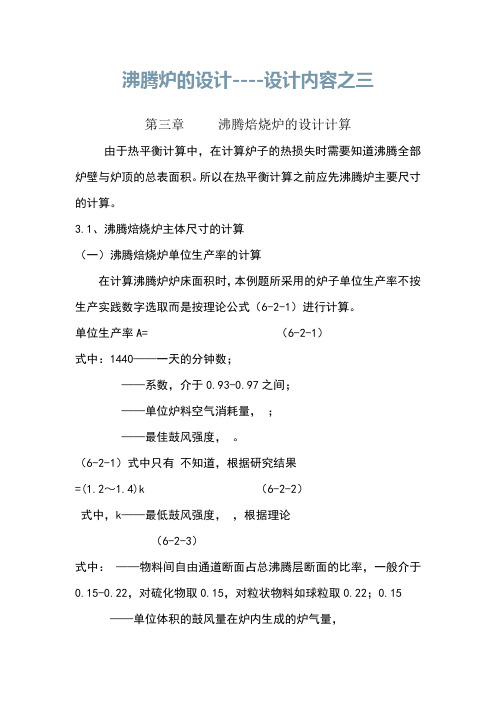
沸腾炉的设计----设计内容之三第三章沸腾焙烧炉的设计计算由于热平衡计算中,在计算炉子的热损失时需要知道沸腾全部炉壁与炉顶的总表面积。
所以在热平衡计算之前应先沸腾炉主要尺寸的计算。
3.1、沸腾焙烧炉主体尺寸的计算(一)沸腾焙烧炉单位生产率的计算在计算沸腾炉炉床面积时,本例题所采用的炉子单位生产率不按生产实践数字选取而是按理论公式(6-2-1)进行计算。
单位生产率A= (6-2-1)式中:1440——一天的分钟数;——系数,介于0.93-0.97之间;——单位炉料空气消耗量,;——最佳鼓风强度,。
(6-2-1)式中只有不知道,根据研究结果=(1.2~1.4)k (6-2-2)式中,k——最低鼓风强度,,根据理论(6-2-3)式中:——物料间自由通道断面占总沸腾层断面的比率,一般介于0.15-0.22,对硫化物取0.15,对粒状物料如球粒取0.22;0.15——单位体积的鼓风量在炉内生成的炉气量,——炉料的比重,4000 ;——炉气重度, = =1.429 ;——通过料层炉气的算术平均温度,= =460℃;——物料粒子平均粒度,米。
根据已知精矿的粒度组成,精矿中大粒部分:粒度 0.323㎜ 10%(33%)0.192㎜ 20%(67%)共计 30%(100%)=0.9=0.9(0.67×0.192+0.33×0.323)=0.212㎜精矿中细粒部分:粒度 0.081㎜ 35%(50%)0.068㎜ 35%(50%)共计 70%(100%)=0.9=0.9(0.50×0.068+0.50×0.081)=0.067㎜对全部精矿:大粒部分 0.212㎜ 30%细粒部分 0.067㎜ 70%= × =0.32物料粒子平均粒度按经验公式计算,对混合料,≤0.415 时,平均粒度根据小粒体积含量按下式计算:=5% +95%=0.05×0.212+0.95×0.067=0.074㎜=74×把上述数字代入(6-2-3)式:=(1.2~1.4)k,选用系数1.2,则最佳鼓风强度 =1.2k=1.2×7.403=8.884现在就可以计算炉子的单位生产率:A= =6.925沸腾炉的单位生产率(床能力)与操作气流速度有关,因此也可按以下公式计算求得:A= (6-2-4)式中:——操作气流速度,米/秒。
沸腾炉的特性及优化
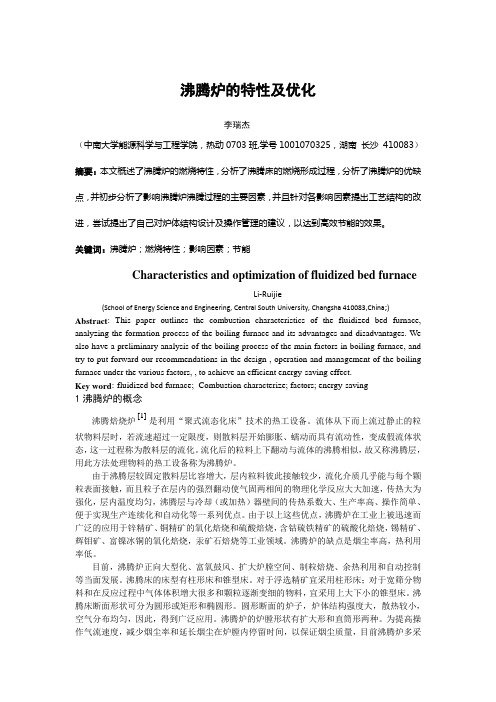
沸腾炉的特性及优化李瑞杰(中南大学能源科学与工程学院,热动0703班,学号1001070325,湖南长沙 410083)摘要:本文概述了沸腾炉的燃烧特性,分析了沸腾床的燃烧形成过程,分析了沸腾炉的优缺点,并初步分析了影响沸腾炉沸腾过程的主要因素,并且针对各影响因素提出工艺结构的改进,尝试提出了自己对炉体结构设计及操作管理的建议,以达到高效节能的效果。
关键词:沸腾炉;燃烧特性;影响因素;节能Characteristics and optimization of fluidized bed furnaceLi-Ruijie(School of Energy Science and Engineering, Central South University, Changsha 410083,China;) Abstract: This paper outlines the combustion characteristics of the fluidized bed furnace, analyzing the formation process of the boiling furnace and its advantages and disadvantages. We also have a preliminary analysis of the boiling process of the main factors in boiling furnace, and try to put forward our recommendations in the design , operation and management of the boiling furnace under the various factors, , to achieve an efficient energy-saving effect.Key word:fluidized bed furnace;Combustion characterize; factors; energy-saving1沸腾炉的概念沸腾焙烧炉[1]是利用“聚式流态化床”技术的热工设备。
丹霞冶炼厂沸腾焙烧制酸改造综述

丹霞冶炼厂沸腾焙烧制酸改造综述李莎【摘要】丹霞冶炼厂原有焙烧、制酸系统工艺流程存在缺陷,设备陈旧,无法保证新建10万吨电锌厂的焙砂需求量,满足不了日益严格的安全环保要求.通过对该系统的技术改造,改造后的设备成熟、可靠、节能,注重了循环经济,加强了环境保护,并且提供了水的循环利用,减少废水排放,力求再生使用.【期刊名称】《有色冶金设计与研究》【年(卷),期】2010(031)005【总页数】3页(P20-21,24)【关键词】焙烧;硫酸生产;冶炼烟气;改造【作者】李莎【作者单位】深圳市中金岭南有色金属股份有限公司丹霞冶炼厂,广东,韶关,512325【正文语种】中文【中图分类】TQ111.16中金岭南公司丹霞冶炼厂焙烧及制酸系统是新建10万t电锌厂配套工程,主要目的是向10万t系统提供足够的焙砂用于中和,沸腾焙烧系统改造目标是使锌精矿(干基)的日处理能力从110.28 t上升到143.36t,硫酸生产能力从3.6万t上升到4.7万t,对废水、废气、废渣进行有效处理,做到达标排放。
该系统始建于1995年,年生产2万t电锌、3万t硫酸,采用二级动力波加泡沫塔稀酸洗、两转两吸工艺。
原料来自凡口铅锌矿生产的富含镓、锗、银等有价金属的锌精矿。
锌精矿成分见表1,锌精矿粒径分布见表2。
经多年使用,该系统目前已处于报废的边缘,设备出现腐蚀、变形,自动化程度低,尾气排放达不到国家新标准要求。
(1)工艺流程工艺流程见图1。
①焙烧工序。
沸腾焙烧是利用具有一定气流速度的空气自下而上通过炉内矿层,使固体颗粒被吹动,相互分离而呈悬浮状态,达到固体颗粒(锌精矿)与气体氧化剂(空气)的充分接触,有利于化学反应进行。
为维持工艺生产的热量平衡,焙烧炉外移热量采用设置蒸发管束的方法,蒸发管束共设6组,每3组为1个循环回路,与余热锅炉汽包组成自然循环系统,体现出循环经济的效果。
由焙烧炉产出的1000℃左右的烟气,经余热锅炉回收余热产生蒸汽,使烟气降温至400℃左右,然后进入一二级旋风收尘器进行粗收尘,再进入电收尘器除尘净化,使其含尘浓度达到0.5 g/Nm3以下。
锌冶炼项目控制方案

锌冶炼项目控制方案:工艺简介湿法炼锌的实质是以稀硫酸溶剂溶解锌矿中的锌,使锌尽可能全部地溶入溶液中,生成硫酸锌溶液;此溶液进行净化以除去溶液中的杂质;然后从硫酸锌溶液中电解析出锌;电解析出的阴极锌再熔铸成为湿法炼锌的成品。
从上述可知,湿法炼锌过程可分为浸出、净液、电解、和熔铸四个阶段。
该项目锌冶炼包括火法和湿法两大部分:主要工艺流程如下::控制要求1.焙烧控制的重点和难点:沸腾焙烧的控制对生产过程来说,是三稳定:稳定的风量、稳定的料量和稳定的温度。
控制系统也是三稳定,来控制的。
有以下主要控制回路:1、炉膛温度控制调节回路;2、鼓风量控制调节回路;3、加料控制调节回路;4、沸腾炉微负压控制调节回路;5、炉底鼓风静压。
沸腾焙烧余热锅炉是利用沸腾炉的余热产生蒸气的过程,有以下主要控制回路:1 强制循环泵产生的沸腾炉埋管和沸腾炉烟道埋管的流量;2 余热锅炉汽包水位控制调节;3 饱和蒸气压力控制调节;4 除氧器温度控制调节;5 除氧器水位调节。
焙烧工段主要检测回路:沸腾焙烧:1. 焙烧炉沸腾层上中下部温度检测,并根据中部温度调节炉顶喷水装置。
2.炉顶温度,烟气出口,流态化冷却器及高效圆筒冷却器出水温度以及焙砂,及流态化冷却器温度检3.精矿贮仓料位检测及报警。
4.炉顶烟气压力,风箱压力,烧嘴油压,压缩空气,燃烧风压力及流态冷却器压缩空气冷却水压力及圆筒冷却器冷却水压力检测。
5.鼓风流量,烧嘴流量,燃烧风空气流量,及流态冷却器压缩空气流量冷却水流量及高效圆筒冷却器水流量检测。
6.精矿给料量控制。
焙烧炉炉膛负压控制。
焙烧炉鼓风量控制。
7.鼓风机,刮板输送机,流态化冷却器,高效圆筒冷却器冷却水回水温度,断流检测报警。
余热锅炉:1. 锅炉汽包的水位,压力检测,除氧器除氧水箱水位检测。
2. 锅炉蒸汽出口温度,压力和流量检测。
3. 减压后蒸汽温度,压力检测。
4. 给水泵,循环泵进出口压力检测。
5. 余热锅炉进出口及对流区温度,压力检测等6. 汽包,除氧水箱水位自动调节。
锌精矿焙烧课计
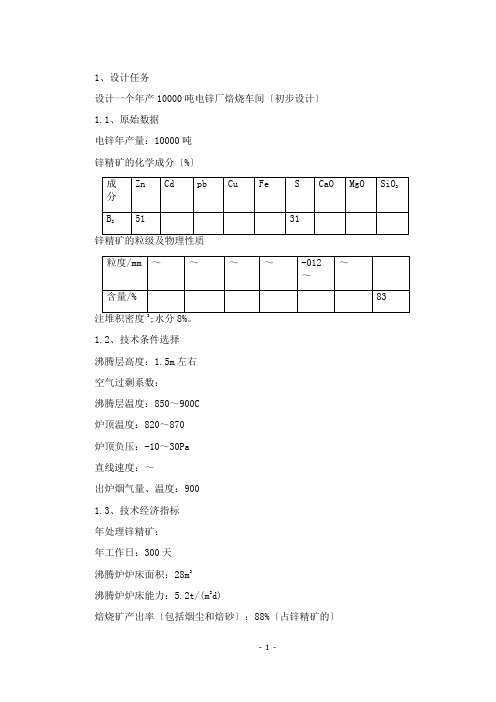
1、设计任务设计一个年产10000吨电锌厂焙烧车间〔初步设计〕1.1、原始数据电锌年产量:10000吨锌精矿的化学成分〔%〕1.2、技术条件选择沸腾层高度:1.5m左右空气过剩系数:沸腾层温度:850~900C炉顶温度:820~870炉顶负压:-10~30Pa直线速度:~出炉烟气量、温度:9001.3、技术经济指标年处理锌精矿:年工作日:300天沸腾炉炉床面积:28m2沸腾炉炉床能力:5.2t/(m2d)焙烧矿产出率〔包括烟尘和焙砂〕:88%〔占锌精矿的〕烟尘含锌量:54.89%焙砂含锌量:1%焙烧料含锌量:48%脱硫率:93.6%焙烧锌直收率:52%冶炼总回收率:95%出炉烟尘含量:35%〔占焙烧矿的〕量:9365%〔体积百分数〕出炉烟气SO2烟尘含Ss量:1.73%焙砂含Ss量:0.4%2-量:2.14%烟尘含Sso42-量:1.10%焙砂含Sso42、原始资料、锌矿的分布及品位截至2002年,全世界查明锌储量为20000万吨,储量根底为45000万吨,现有储量和储量根底的静态保证年限为23年和51年。
锌储量和储量根底占锌资源量的%和%。
中国锌的储量和储量根底均居世界首位,已成为世界最大的铅锌资源国家。
根据统计资料,在我国铅锌储量中铅锌平均品位只有 4.66%,而根据目前铅锌价格水平和本钱水平,只有铅锌(1:2.5)合计地质品位在7%~8%以上的地质储量才是能经济利用的储量,目前我国能经济利用的铅锌合计储量只有万吨,仅占总储量的 42.6%。
锌在自然界多以硫化物的状态存在,主要矿物是闪锌矿〔ZnS〕,但这种硫化矿的形成过程中有FeS固溶体,成为铁闪锌矿〔nZnSmFeS〕.含铁高的闪锌矿会使提取冶炼过程复杂化。
流化床的地表部位还常有一部打分被氧化的氧化矿,如菱锌矿〔ZnCO3〕、硅锌矿〔Zn2SiO4〕、导极矿〔H2Zn2SiO5〕等。
我国铅锌储量较多的省(区)主要是云南、广东、甘肃、四川、广西、内蒙古、湖南和青海等八省(区),其铅锌储量占全国总储量的80.7%。
湿法炼锌中沸腾焙烧过程的研究进展
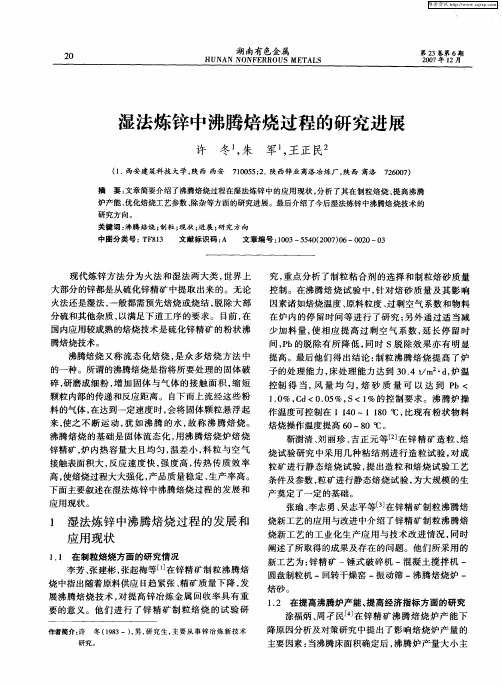
少 加 料 量 , 相 应 提 高 过 剩 空 气 系数 , 长停 留时 使 延 间 ,b的脱 除 有 所 降 低 , 时 S脱 除效 果 亦 有 明 显 P 同
腾焙烧 技术 。
沸腾焙烧又称流态化焙烧 , 是众 多焙烧方 法 中 的一种 。所谓 的沸腾焙 烧是 指将 所 要 处理 的 固体破
国内应 用较 成熟 的焙烧 技 术是 硫 化锌 精 矿 的粉 状 沸
究, 重点分析 了制粒粘合剂 的选择和制粒焙砂质量 控制 。在沸腾焙烧试验 中, 针对焙砂质量及其影响 因素 诸如焙 烧 温度 、 原料粒 度 、 剩空 气 系 数 和物 料 过
在 炉 内 的停 留 时 间等 进 行 了 研究 ; 另外 通过 适 当减
第 6期
许
冬 , : 法炼锌 中沸 腾焙 烧过 程 的研 究进展 等 湿
2 1
要取决于焙烧强度 的高低。焙烧强度越 高 , 炉子产 量越大 ; 焙烧 强度 越低 , 子产 量 越 小 。而 焙烧 强度 炉
取决 于单位 时 间内从 炉 内沸腾 层 移走 热 量 的 多少 和
物 料反应 速度 的快 慢 。在 原料 成 分 、 理规 格 、 烧 物 焙
碎, 研磨 成细 粉 , 加 固体 与 气 体 的接 触 面 积 , 短 增 缩 颗粒 内部 的传递 和反应距 离 。 自下 而上 流 经 这 些粉 料 的气体 , 在达 到 一定速 度 时 , 将 固体 颗 粒悬 浮起 会 来 , 之 不 断 运 动 , 如 沸 腾 的水 , 称 沸 腾 焙 烧 。 使 犹 故 沸腾 焙 烧 的基 础是 固体 流 态 化 , 沸 腾焙 烧 炉 焙 烧 用 锌精矿 , 内 热容 量 大且 均 匀 , 炉 温差 小 , 粒 与 空 气 料
中图分类 号:T 8 3 F 1
- 1、下载文档前请自行甄别文档内容的完整性,平台不提供额外的编辑、内容补充、找答案等附加服务。
- 2、"仅部分预览"的文档,不可在线预览部分如存在完整性等问题,可反馈申请退款(可完整预览的文档不适用该条件!)。
- 3、如文档侵犯您的权益,请联系客服反馈,我们会尽快为您处理(人工客服工作时间:9:00-18:30)。
江西理工大学课程设计音问久疏,唯愿一切康适。
沸腾焙烧炉设计题目年产6万吨锌冶炼沸腾焙烧炉设计专业冶金工程班级冶金093姓名华仔学号31指导教师万林生- 1 -目录第一章设计概述 (1)1.1设计依据 (1)1.2设计原则和指导思想 (1)1.3毕业设计任务 (1)第二章工艺流程的选择与论证 (1)2.1原料组成及特点 (1)2.2沸腾焙烧工艺及主要设备的选择 (1)第三章物料衡算及热平衡计算 (3)3.1锌精矿流态化焙烧物料平衡计算 (3)3.1.1锌精矿硫态化焙烧冶金计算 (3)3.1.2烟尘产出率及其化学和物相组成计算 (4)3.1.3焙砂产出率及其化学与物相组成计算 (6)3.1.4焙烧要求的空气量及产出烟气量与组成的计算 (7)3.2热平衡计算 (9)3.2.1热收入 (9)3.2.2热支出 (12)第四章沸腾焙烧炉的选型计算 (13)4.1床面积 (13)4.2前室面积 (14)4.3炉膛面积和直径 (13)4.4炉膛高度 (14)4.5气体分布板及风帽 (15)4.5.1气体分布板孔眼率 (15)4.5.2风帽 (15)4.6沸腾冷却层面积 (15)4.7水套中循环水的消耗量 (14)4.8风箱容积 (15)4.9加料管面积 (15)4.10溢流排料口 (15)4.11排烟口面积 (15)参考文献 (15)- I -第一章设计概述1.1设计依据根据《冶金工程专业课程设计指导书》。
1.2设计原则和指导思想对设计的总要求是技术先进;工艺上可行;经济上合理,所以,设计应遵循的原则和指导思想为:1、遵守国家法律、法规,执行行业设计有关标准、规范和规定,严格把关,精心设计;2、设计中对主要工艺流程进行多方案比较,以确定最佳方案;3、设计中应充分采用各项国内外成熟技术,因某种原因暂时不上的新技术要预留充分的可能性。
所采用的新工艺、新设备、新材料必须遵循经过工业性试验或通过技术鉴定的原则;4、要按照国家有关劳动安全工业卫生及消防的标准及行业设计规定进行设计;5、在学习、总结国内外有关厂家的生产经验的基础上,移动试用可行的先进技术;6、设计中应充分考虑节约能源、节约用地,实行自愿的综合利用,改善劳动条件以及保护生态环境。
1.3毕业设计任务一、沸腾焙烧炉专题概述二、沸腾焙烧三、沸腾焙烧热平衡计算四、主要设备(沸腾炉和鼓风炉)设计计算五、沸腾炉主要经济技术指标第二章工艺流程的选择与论证2.1原料组成及特点本次设计处理的原料锌精矿成分如下表所示。
2.2沸腾焙烧工艺及主要设备的选择金属锌的生产,无论是用火法还是湿法,90%以上都是以硫化锌精矿为原料。
硫化锌不能被廉价的、最容易获得的碳质还原剂还原,也不容易被廉价的,并且在浸出—电积湿法炼锌生产流程中可以再生的硫酸稀溶液(废电解液)所浸出,因此对硫化锌精矿氧化焙烧使之转变成氧化锌是很有必要的。
焙烧就是通常采用的完成化合物形态转变的化学过程,是冶炼前对矿石或精矿进行预处理的一种高温作业。
硫化物的焙烧过程是一个发生气固反应的过程,将大量的空气(或富氧空气)通入硫化矿物料层,在高温下发生反应,氧与硫化物中的硫化合产生气体SO2,有价金属则变成为氧化物或硫酸盐。
同时去掉砷、锑等杂质,硫生成二氧化硫进入烟气,作为制硫酸的原料。
焙烧过程得到的固体产物就被称为焙砂或焙烧矿。
焙烧过程是复杂的,生成的产物不尽一致,可能有多种化合物并存。
一般来说,硫化物的氧化反应主要有:1)硫化物氧化生成硫酸盐MeS + 2 O2 = MeSO42)硫化物氧化生成氧化物MeS + 1.5 O2 = MeO + SO23)金属硫化物直接氧化生成金属MeS + 2 O2 = MeO + SO24)硫酸盐离解MeSO4 = MeO + SO3SO3 = SO2+ 0.5 O2此外,在硫化锌精矿中,通常还有多种化合价的金属硫化物,其高价硫化物的离解压一般都比较高,故极不稳定,焙烧时高价态硫化物离解成低价态的硫化物,然后再继续进行其焙烧氧化反应过程。
在焙烧过程中,精矿中某种金属硫化物和它的硫酸盐在焙烧条件下都是不稳定的化合物时,也可能相互反应,如:FeS + 3FeSO4 = 4FeO + 4SO2由上述各种反应可知,锌精矿中各种金属硫化物焙烧的主要产物是MeO、MeSO4以及SO2、SO3和O2。
此外还可能有MeO·Fe2O3,MeO·SiO2等。
沸腾焙烧炉炉体(下图)为钢壳内衬保温砖再衬耐火砖构成。
为防止冷凝酸腐蚀,钢壳外面有保温层。
炉子的最下部是风室,设有空气进口管,其上是空气分布板。
空气分布板上是耐火混凝土炉床,埋设有许多侧面开小孔的风帽。
炉膛中部为向上扩大的圆锥体,上部焙烧空间的截面积比沸腾层的截面积大,以减少固体粒子吹出。
沸腾层中装有的冷却管,炉体还设有加料口、矿渣溢流口、炉气出口、二次空气进口、点火口等接管。
炉顶有防爆孔。
操作指标和条件主要有焙烧强度、沸腾层高度、沸腾层温度、炉气成分等。
① 焙烧强度 习惯上以单位沸腾层截面积一日处理含硫35%矿石的吨数计算。
焙烧强度与沸腾层操作气速成正比。
气速是沸腾层中固体粒子大小的函数,一般在 1~3m/s 范围内。
一般浮选矿的焙烧强度为15~20t/(d m ⋅);对于通过3×3mm 的筛孔的破碎块矿,焙烧强度为30t/(d m ⋅)。
② 沸腾层高度 即炉内排渣溢流堰离风帽的高度,一般为0.9~1.5m 。
③ 沸腾层温度 随硫化矿物、焙烧方法等不同而异。
例如:锌精矿氧化焙烧为1070~1100℃,而硫酸化焙烧为900~930℃;硫铁矿的氧化焙烧温度为850~950℃。
④ 炉气成分 硫铁矿氧化焙烧时,炉气中二氧化硫13%~13.5%,三氧化硫≤0.1%。
硫酸化焙烧,空气过剩系数大,故炉气中二氧化硫浓度低而三氧化硫含量增加。
特点:①焙烧强度高;②矿渣残硫低;③可以焙烧低品位矿;④炉气中二氧化硫浓度高、三氧化硫含量少;⑤可以较多地回收热能产生中压蒸汽,焙烧过程产生的蒸汽通常有35%~45%是通过沸腾层中的冷却管获得;⑥炉床温度均匀;⑦结构简单,无转动部件,且投资省,维修费用少;⑧操作人员少,自动化程度高,操作费用低;⑨开车迅速而方便,停车引起的空气污染少。
但沸腾炉炉气带矿尘较多,空气鼓风机动力消耗较大。
第三章 物料衡算及热平衡计算3.1锌精矿流态化焙烧物料平衡计算3.1.1锌精矿硫态化焙烧冶金计算根据精矿的物相组成分析,精矿中各元素呈下列化合物形态Zn 、Cd 、Pb 、Cu 、Fe 分别呈ZnS 、CdS 、PbS 、2CuFeS 、87S Fe 2FeS ;脉石中的Ca 、Mg 、Si 分别呈3CaCO 、3MgCO 、2SiO 形态存在。
以100kg 锌精矿(干量)进行计算。
1.ZnS 量 :kg 02.744.654.977.49=⨯ 其中Zn :49.7kg S :24.32kg2.CdS 量:kg 28.04.1124.14422.0=⨯ 其中 Cd :0.22kg S :0.06kg3.PbS 量:kg 60.12.2072.23939.1=⨯ 其中:Pb :1.39kg S :0.21kg4.2CuFeS 量:kg 81.05.6335.18328.0=⨯ 其中:Cu :0.28kg Fe :0.25kg S :0.28kg5. 2FeS 和87S Fe 量:除去2CuFeS 中Fe 的含量,余下的Fe 为8.22kg 0.25-8.47=,除去ZnS 、CdS 、PbS 、2CuFeS 中S 的含量,余下的S 量为Kg 74.5)28.021.006.032.24(61.30=+++-。
此S 量全部分布在2FeS 和87S Fe 中,设2FeS 中Fe 为x kg ,S 量为y kg ,则872S Fe FeS ⎪⎪⎩⎪⎪⎨⎧⨯-=⨯-⨯=83274.5785.5522.823285.55yx y x解得:x =0.72kg ,y =0.83kg 即2FeS 中:Fe=0.72kg 、S=0.83kg 、2FeS =1.55kg 。
87S Fe 中:Fe :8.22-0.72=7.5kg S :5.74-0.83=4.91kg 87S Fe :12.41kg6. 3CaCO 量:kg 87.11.561.10005.1=⨯ 其中CaO :1.05kg 2CO :0.82kg7. 3MgCO 量:kg 75.03.403.8436.0=⨯ 其中MgO :0.36kg 2CO :0.39kg表3-1 混合精矿物相组成,kg3.1.2烟尘产出率及其化学和物相组成计算焙烧矿产出率一般为锌精矿的88%,烟尘产出率取50%,则烟尘量为:44公斤。
镉60%进入烟尘,锌48%进入烟尘,其它组分在烟尘中的分配率假定为50%,空气过剩系数 1.25。
烟尘产出率及烟尘物相组成计算: Zn kg 856.2348.007.49=⨯ Cd kg 132.060.022.0=⨯ Pb kg 695.050.039.1=⨯ Cu kg 14.050.028.0=⨯ Fe kg 235.450.047.8=⨯ CaO kg 525.0.050.005.1=⨯ MgO kg 18.050.036.0=⨯2SiO kg 605.250.021.5=⨯ s S 0.761x kg 4SO S 0.942x kg其他 kg 355.150.071.2=⨯各组分化合物进入烟尘的数量为:1.ZnS 量:xkg 316.2324.97761.0=⨯ 其中:Zn 1.555kg S 0.761kg2.4ZnSO 量:kg 751.4324.161942.0=⨯ 其中:Zn 1.925kg S 0.942kg O 1.884kg3.32O Fe ZnO ⋅量:烟尘中Fe 先生成32O Fe ,其量为:kg 055.67.1117.159235.4=⨯,32O Fe 有31与ZnO 结合成32O Fe ZnO ⋅,其量为:kg 018.231055.6=⨯。
32O Fe ZnO ⋅量为kg 046.37.1591.241018.2=⨯ 其中:Zn0.82kg Fe 1.411kg O 0.815kg 余下的32O Fe 的量:6.055-2.018=4.037kg 其中:Fe 2.824 kg O 1.213kg 4.ZnO 量:Zn 23.856-(1.555+1.925+0.82)=19.556kg ZnO kg 34.244.654.81556.19=⨯ O 24.34-19.556=4.784kg5.CdO 量:kg 151.04.1124.128132.0=⨯ 其中:Cd 0.132kg O 0.019kg6.CuO 量:kg 175.0.05.635.7914.0=⨯ 其中:Cu 0.14kg O 0.035kg7.2SiO PbO ⋅量:PbO ,kg 749.02.2072.223695.0=⨯ 其中:Pb 0.695kg O 0.054kg与PbO 结合的2SiO 量:kg 201.0.02.22360749.0=⨯剩余的2SiO 量:2.605-0.201=2.404kg表3-2烟尘产出率及其化学和物相组成,kg3.1.3焙砂产出率及其化学与物相组成计算焙砂中S SO4取1.10%,S S 取0.4%,S SO4和S S 全部与Zn 结合;PbO 与SiO 2结合成 PbO ˙SiO 2;其他金属以氧化物形态存在。