高周疲劳失效分析
新型低成本钛合金高周疲劳性能和断裂韧度
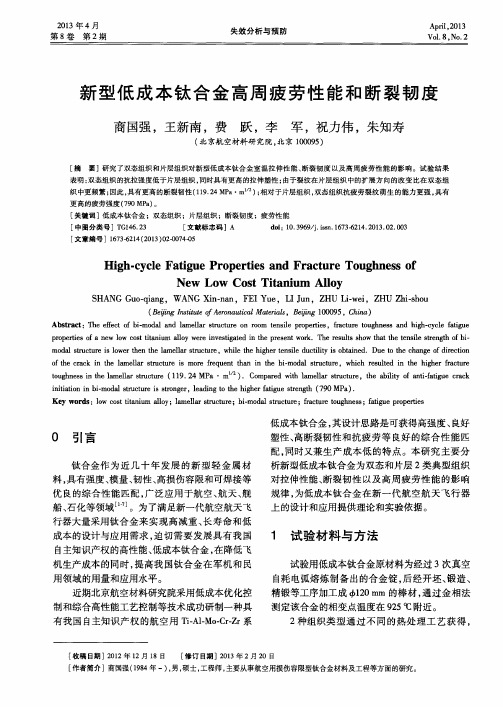
( B e n g I n s t i t u t e o fA e r o n a u t i c a l Ma t e r i a l s ,B e n g 1 0 0 0 9 5 , C h i n a ) Ab s t r a c t : T h e e f f e c t o f b i - mo d a l a n d l a me l l a r s t r u c t u r e o n r o o m t e n s i l e p r o p e r t i e s ,f r a c t u r e t o u g h n e s s a n d h i h— g c y c l e f a t i g u e
更 高的疲劳强度 ( 7 9 0 MP a ) 。 [ 关键词 ]低成本钛合金 ;双态组织 ;片层组织 ;断裂韧度 ;疲劳性能 [ 中闰分 类号]T G 1 4 6 . 2 3 [ 文献标 志码 ]A d o i : 1 0 . 3 9 6 9 / j . i s s n . 1 6 7 3 - 6 2 1 4 . 2 0 1 3 . 0 2 . 0 0 3 [ 文章 编号]1 6 7 3 62 - 1 4 ( 2 0 1 3 ) 0 2 - 0 0 7 4 - 0 5
p r o p e r t i e s o f a n e w l o w c o s t t i t a n i u m a l l o y w e r e i n v e s t i g a t e d i n t h e p r e s e n t w o r k .T h e r e s u l t s s h o w t h a t t h e t e n s i l e s t r e n g t h o f b i — mo d l a s t r u c t u r e i s l o w e r t h e n t h e l a me l l a r s t r u c t u r e,w h i l e he t h i g h e r t e n s i l e d u c t i l i t y i s o b t a i n e d .Du e t o t h e c h a n g e o f d i r e c t i o n
失效分析知识点

失效分析知识点第一章概论1.失效的定义:当这些零件失去其应有的功能时,则称该零件失效。
2.失效三种情况:(1).零件由于断裂、腐蚀、磨损、变形等从而完全丧失其功能;(2).零件在外部环境作用下,部分的失去其原有功能,虽然能工作,但不能完成规定功能,如由于磨损导致尺寸超差等;(3).零件能够工作,也能完成规定功能,但继续使用时,不能确保安全可靠性。
3. 失效分析定义:对失效产品为寻找失效原因和预防措施所进行的一切技术活动。
也就是研究失效的特征和规律,从而找出失效的模式和原因。
4. 失效分析过程:事前分析(预防失效事件的发生)、事中分析(防止运行中设备发生故障)、事后分析(找出某个系统或零件失效的原因)。
5. 失效分析的意义:(1).失效分析的社会经济效益:失效将造成巨大的经济损失;质量低劣、寿命短导致重大经济损失;提高设备运行和使用的安全性。
(2).失效分析有助于提高管理水平和促进产品质量提高;(3).失效分析有助于分清责任和保护用户(生产者)利益;(4).失效分析是修订产品技术规范及标准的依据;(5).失效分析对材料科学与工程的促进作用:材料强度与断裂;材料开发与工程应用。
第二章失效分析基础知识一.机械零件失效形式与来源:1.按照失效的外部形态分类:(1)过量变形失效:扭曲、拉长等。
原因:在一定载荷下发生过量变形,零件失去应有功能不能正常使用。
(2)断裂失效:一次加载断裂(静载荷):由于载荷或应力超过当时材料的承载能力而引起;环境介质引起的断裂:环境介质和应力共同作用引起的低应力脆断;疲劳断裂(交变载荷):由于周期作用力引起的低应力破坏。
(3)表面损伤失效:磨损:由于两物体接触表面在接触应力下有相对运动,造成材料流失所引起的一种失效形式;腐蚀: 环境气氛的化学和电化学作用引起。
(4).注:断裂的其他分类断裂时变形量大小:脆性断裂、延性断裂;裂纹走向与晶相组织的关系:穿晶断裂、沿晶断裂;2.失效的来源:(1).设计的问题:高应力部位存在沟槽、机械缺口及圆角半径过小等;应力计算错误;设计判据不正确。
材料失效分析(第五章-疲劳)

§2
疲劳裂纹萌生与扩展机理(模型)
一、疲劳裂纹萌生机理 1、挤出挤入模型—Wood模型
10
金属表面形成的挤出脊与挤入沟
11
2、位错销毁模型—藤田模型
两列平行的异号刃位错,在相距几个原子间隔 (约10埃)的两平行滑移面上互相对峙塞积;
由于这种位错排列所产生的高拉应力引起原子 面分离,形成孔洞
12
20
锯齿形断口或棘轮花样
轴类零件在交变扭转应力作用下产生的 有应力集中(轴颈)+扭矩作用
多源裂纹
裂纹以螺旋状方式向前扩展,最后汇合于轴的中央 若为单向交变扭转应力——棘轮花样 若为双向交变扭转应力——锯齿状断口
21
锯齿形断口
棘轮花样
22
3、瞬断区
形貌:具有断口三要素(放射区、剪切唇)的特征
对于塑性材料,断口为纤维状、暗灰色 对于脆性材料,断口为结晶状 位置:自由表面 断面中心
7
4、疲劳断裂过程
疲劳裂纹的萌生: 表面(次表面、内部) 疲劳裂纹的扩展(两个阶段)
8
第一阶段:裂纹起源于材料表面,向内部扩展
范围较小,约2—5个晶粒之内 显微形貌不好分辨 与拉伸轴约成45°角,裂纹扩展主要是由于τ 的作用
扩展速度很慢,每一应力循环只有埃数量级
第二阶段:断面与拉伸轴垂直,凹凸不平 裂纹扩展路径是穿晶的 扩展速度快,每一应力循环微米数量级 显微特征:疲劳辉纹
3、空穴模型—Mott模型
由于螺位错围绕着环形通道,进行连续交叉滑移运动, 结果从表面上挤出了材料的一个舌片,并相应地形成 了一个空穴,这个空穴就是疲劳裂纹源
13
4、位错交叉滑移模型—Cottrell和Hull模型
14
二、疲劳裂纹扩展模型
什么是低周期疲劳和高周期疲劳

什么是高周疲劳、低周疲劳?为便于分析研究,常按破坏循环次数的高低将疲劳分为两类:①高循环疲劳(高周疲劳)。
作用于零件、构件的应力水平较低,破坏循环次数一般高于104~105的疲劳,弹簧、传动轴等的疲劳属此类。
②低循环疲劳(低周疲劳)。
作用于零件、构件的应力水平较高,破坏循环次数一般低于104~105的疲劳,如压力容器、燃气轮机零件等的疲劳。
实践表明,疲劳寿命分散性较大,因此必须进行统计分析,考虑存活率(即可靠度)的问题。
具有存活率p(如95%、99%、99.9%)的疲劳寿命Np的含义是:母体(总体)中有p的个体的疲劳寿命大于Np。
而破坏概率等于(1-p )。
常规疲劳试验得到的S-N曲线是p=50%的曲线。
对应于各存活率的p的S-N曲线称为p-S-N曲线。
疲劳(2)fatigue材料、零件和构件在循环加载下,在某点或某些点产生局部的永久性损伤,并在一定循环次数后形成裂纹、或使裂纹进一步扩展直到完全断裂的现象。
研究简史有记载的最早进行疲劳试验是德国的W.A.艾伯特。
法国的J.-V.彭赛列首先论述了疲劳问题并提出“疲劳”这一术语。
但疲劳研究的奠基人则是德国的A.沃勒,他在19世纪50~60 年代最早得到表征疲劳性能的S-N曲线并提出疲劳极限的概念。
20世纪50年代P.J.E.福赛思首先观察到疲劳过程中在滑移带内有金属薄片挤出的现象。
随后N.汤普孙等人发现这种滑移带不易用电解抛光去掉,称为“驻留滑移带”。
后来证明,驻留滑移带常常成为裂纹源。
1924年德国的J.V.帕姆格伦在估算滚动轴承寿命时,假设轴承的累积损伤与其转动次数成线性关系。
1945年美国M.A.迈因纳明确提出了疲劳破坏的线性损伤累积理论,也称为帕姆格伦- 迈因纳定律,简称迈因纳定律。
此后,断裂力学的进展丰富了传统疲劳理论的内容,促进了疲劳理论的发展。
用概率统计方法处理疲劳试验数据,是20世纪20年代开始的。
60年代后期,概率疲劳分析和设计从电子产品发展到机械产品,于是在航空、航天工业的先导下,开始了概率统计理论在疲劳设计中的应用。
机械设计中的疲劳分析与寿命预测
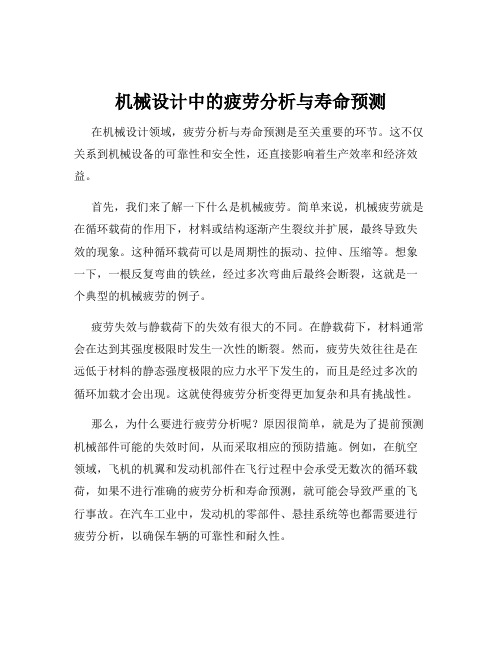
机械设计中的疲劳分析与寿命预测在机械设计领域,疲劳分析与寿命预测是至关重要的环节。
这不仅关系到机械设备的可靠性和安全性,还直接影响着生产效率和经济效益。
首先,我们来了解一下什么是机械疲劳。
简单来说,机械疲劳就是在循环载荷的作用下,材料或结构逐渐产生裂纹并扩展,最终导致失效的现象。
这种循环载荷可以是周期性的振动、拉伸、压缩等。
想象一下,一根反复弯曲的铁丝,经过多次弯曲后最终会断裂,这就是一个典型的机械疲劳的例子。
疲劳失效与静载荷下的失效有很大的不同。
在静载荷下,材料通常会在达到其强度极限时发生一次性的断裂。
然而,疲劳失效往往是在远低于材料的静态强度极限的应力水平下发生的,而且是经过多次的循环加载才会出现。
这就使得疲劳分析变得更加复杂和具有挑战性。
那么,为什么要进行疲劳分析呢?原因很简单,就是为了提前预测机械部件可能的失效时间,从而采取相应的预防措施。
例如,在航空领域,飞机的机翼和发动机部件在飞行过程中会承受无数次的循环载荷,如果不进行准确的疲劳分析和寿命预测,就可能会导致严重的飞行事故。
在汽车工业中,发动机的零部件、悬挂系统等也都需要进行疲劳分析,以确保车辆的可靠性和耐久性。
在进行疲劳分析时,需要考虑多个因素。
材料的特性是其中的关键之一。
不同的材料具有不同的疲劳性能,比如强度、韧性、硬度等。
此外,材料的表面质量也会对疲劳寿命产生影响。
一个表面粗糙的零件相比于表面光滑的零件,更容易产生疲劳裂纹。
载荷的特征也是重要的考虑因素。
载荷的大小、频率、波形等都会影响疲劳寿命。
比如,高频的载荷往往会导致更短的疲劳寿命。
零件的几何形状和尺寸同样不容忽视。
尖锐的转角、孔、槽等部位容易产生应力集中,从而加速疲劳裂纹的形成。
为了进行准确的疲劳分析和寿命预测,工程师们通常会采用多种方法和技术。
实验方法是其中一种常见的手段。
通过对实际零件进行疲劳试验,可以直接获得其疲劳寿命的数据。
然而,这种方法往往成本高、周期长,而且对于一些大型复杂的结构不太适用。
涡轮叶片高低周疲劳分析方法总结论文综述

本次毕业设计论文的内容是涡轮叶片高低周疲劳分析方法的总结与对比。
涡轮叶片是航空发动机工作环境最恶劣 ,结构最复杂的零件之一 ,也是发动机断裂故障多发件之一。
由于发动机工作时涡轮叶片始终在高温下承受复合载荷的作用,因此它的高周疲劳寿命和低周疲劳寿命的计算至关重要。
高周疲劳是指破坏循环数大于104~105的疲劳,高周疲劳的情况下,其应力水平低于弹性极限,没有明显的宏观塑性变形,应力与应变呈线性关系。
低周疲劳是指破坏循环数小于104~105的疲劳,低周疲劳的情况下,其应力水平高于弹性极限,有明显的宏观塑性变形,应力与应变呈非线性关系。
在《高周疲劳和低周疲劳统一的能量表征方法研究》一文中,对高周疲劳和低周疲劳预测模型进行了研究,提出了一种能够将高周疲劳和低周疲劳统一表征的能量形式参量。
用统一的能量形式表征参量对高温合金GH141的760摄氏度高周疲劳和低周疲劳数据进行处理,得到理想的能量-寿命方程。
用1Cr11Ni2W2MoV 钢500摄氏度和粉末盘材料FGH95d 600摄氏度高温低周疲劳和高周疲劳数据对统一表征方法进行验证,验证结果表明,用能量形式的表征参量能够得到理想的能量-寿命方程。
疲劳试验通常可以通过控制应变或控制应力来进行。
按照控制方式可以将疲劳分为应力疲劳和应变疲劳。
材料发生了塑性变形进入屈服阶段后,小的应力变化将引起大的变形,此时进行疲劳试验时多采用应变控制,材料的疲劳寿命一般比较短,因此通常也叫低周疲劳而当材料在没有进入屈服阶段前,采用应力和采用应变都可以进行疲劳试验,通常控制应力来进行疲劳实验,材料的疲劳寿命一般比较长,因此,通常也叫高周疲劳。
三参数幂函数能量方法寿命预测模型:采用应力控制的方式进行高周疲劳实验,用应力参量来表征高周疲劳的寿命特征;采用应变控制的方式进行低周疲劳实验,用应变参量或能量参量来表征低周疲劳的寿命特征。
如果能够用能量参量来表征高周疲劳的寿命特征,那就可以将高周疲劳和低周疲劳统一起来用一个表征参量进行表征,从而就不需将疲劳划分为高周疲劳和低周疲劳,但能量表征同时需要应力和应变参量。
混凝土结构的疲劳性能评估方法

混凝土结构的疲劳性能评估方法一、前言混凝土结构是建筑中常见的结构之一,而疲劳是混凝土结构在使用过程中常见的问题之一。
疲劳会导致混凝土结构的损坏和失效,因此评估混凝土结构的疲劳性能是必要的。
本文旨在介绍混凝土结构疲劳性能评估的方法。
二、疲劳的概念和分类疲劳是指材料或结构在受到交替或周期性荷载作用下,经过一定次数的循环荷载后产生的变形和损伤。
混凝土结构的疲劳主要分为高周疲劳和低周疲劳两种。
1.高周疲劳高周疲劳是指在频率较高(大于10Hz)的循环荷载下,混凝土结构受到的疲劳损伤。
高周疲劳对混凝土结构的影响主要是引起裂缝的产生和扩展。
2.低周疲劳低周疲劳是指在频率较低(小于10Hz)的循环荷载下,混凝土结构受到的疲劳损伤。
低周疲劳对混凝土结构的影响主要是引起变形和破坏。
三、疲劳性能评估方法评估混凝土结构的疲劳性能需要进行疲劳试验和分析。
下面分别介绍疲劳试验和分析的具体方法。
1.疲劳试验疲劳试验是评估混凝土结构疲劳性能的重要手段。
疲劳试验需要在实验室中进行,其具体方法如下:(1)试件制备:按照规定的尺寸、材料和配合比制备试件。
(2)荷载加载:按照规定的荷载幅值、频率和循环次数进行荷载加载。
(3)观察记录:观察记录试件的变形和损伤情况,包括裂缝产生和扩展、变形增量等。
(4)分析结果:根据试验结果,分析试件的疲劳性能,包括疲劳寿命、疲劳裂缝扩展速率等指标。
2.疲劳分析疲劳分析是评估混凝土结构疲劳性能的重要手段。
疲劳分析需要进行理论分析和计算,其具体方法如下:(1)建立模型:建立混凝土结构的有限元模型,并根据荷载幅值、频率和循环次数进行模拟加载。
(2)分析结果:根据模拟结果,分析结构的疲劳性能,包括疲劳寿命、疲劳裂缝扩展速率等指标。
(3)修正参数:根据试验结果和分析结果,对模型进行修正和调整,以提高分析精度。
四、疲劳性能评估指标疲劳性能评估需要依据一定的指标进行。
下面介绍常用的疲劳性能评估指标。
1.疲劳寿命疲劳寿命是指混凝土结构在循环荷载下能够承受的循环次数。
滚动轴承常见的失效形式及原因分析
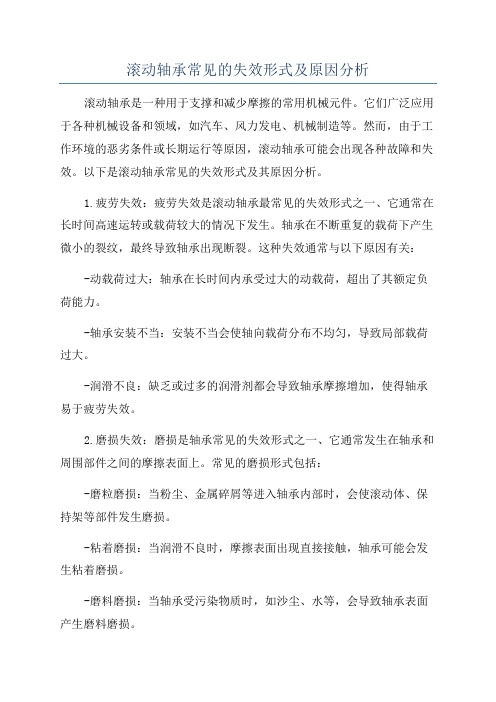
滚动轴承常见的失效形式及原因分析滚动轴承是一种用于支撑和减少摩擦的常用机械元件。
它们广泛应用于各种机械设备和领域,如汽车、风力发电、机械制造等。
然而,由于工作环境的恶劣条件或长期运行等原因,滚动轴承可能会出现各种故障和失效。
以下是滚动轴承常见的失效形式及其原因分析。
1.疲劳失效:疲劳失效是滚动轴承最常见的失效形式之一、它通常在长时间高速运转或载荷较大的情况下发生。
轴承在不断重复的载荷下产生微小的裂纹,最终导致轴承出现断裂。
这种失效通常与以下原因有关:-动载荷过大:轴承在长时间内承受过大的动载荷,超出了其额定负荷能力。
-轴承安装不当:安装不当会使轴向载荷分布不均匀,导致局部载荷过大。
-润滑不良:缺乏或过多的润滑剂都会导致轴承摩擦增加,使得轴承易于疲劳失效。
2.磨损失效:磨损是轴承常见的失效形式之一、它通常发生在轴承和周围部件之间的摩擦表面上。
常见的磨损形式包括:-磨粒磨损:当粉尘、金属碎屑等进入轴承内部时,会使滚动体、保持架等部件发生磨损。
-粘着磨损:当润滑不良时,摩擦表面出现直接接触,轴承可能会发生粘着磨损。
-磨料磨损:当轴承受污染物质时,如沙尘、水等,会导致轴承表面产生磨料磨损。
3.返现失效:轴承返现是指滚动体和滚道之间的剥离、严重滚道表面损伤或磨擦减小所引起的失效。
返现失效的原因主要有:-轴承清洗不当:清洗过程中使用的溶剂或清洁剂残留在轴承内部,导致润滑性能下降,滚动体容易返现。
-轴承热胀冷缩:当轴承受到温度变化时,轴承和轴承座之间的配合间隙有可能发生变化,导致轴承返现。
-润滑不良:缺乏或过多的润滑剂会导致轴承受到不均匀的载荷分布,容易引起轴承返现。
4.偏磨失效:偏磨是指轴承滚动体在滚道上发生偏磨,导致滚道表面形变或表面破坏。
-不均匀载荷:长期承受不均匀载荷会导致滚动体在滚道上的位置发生偏移,从而引起偏磨失效。
-润滑不良:过多或过少的润滑剂会导致轴承滚动体和滚道之间的摩擦增加,从而引起偏磨。
- 1、下载文档前请自行甄别文档内容的完整性,平台不提供额外的编辑、内容补充、找答案等附加服务。
- 2、"仅部分预览"的文档,不可在线预览部分如存在完整性等问题,可反馈申请退款(可完整预览的文档不适用该条件!)。
- 3、如文档侵犯您的权益,请联系客服反馈,我们会尽快为您处理(人工客服工作时间:9:00-18:30)。
发动机叶片高周疲劳失效分析090605 鲍海滨摘要:为了降低航空发动机叶片的高循环疲劳失效。
分析了导致高循环疲劳失效的原因、失效准则,以及一种研究材料多轴高周疲劳的新途径。
关键词:航空发动机叶片高循环疲劳失效1 引言航空发动机结构完整性和可靠性设计,对满足现代高性能航空发动机高推重比(高功质比)、高适用性、高可靠性、耐久性和低成本的要求起着至关重要的作用。
采用先进的气动设计和先进结构、新材料、新工艺是现代高性能航空发动机最重要的特征,而无论是先进的气动设计,还是先进的结构、材料和工艺,都必须建立在结构完整性和可靠性的基础上。
航空发动机结构完整性和可靠性方面的不足严重地制约着在研发动机的研制目标和周期。
在中国航空发动机研制过程中,科研人员最深刻的体会是,相对而言实现发动机性能指标的周期要短一些,也有一些有效的办法,而大量的结构完整性和可靠性问题特别是叶片断裂故障却显著地影响着发动机的质量和设计定型的周期。
导致叶片断裂失效的原因是多方面的[1,2],根据不同的参考标准和参量,疲劳断裂二级失效模式如图1所示[3]据统计,在燃气涡轮发动机中,由高循环疲劳引发的事故约占总事故的25%。
因此,最大限度地降低航空发动机叶片高循环疲劳失效是最现实、亟待解决的任务。
根据频率根据应力大小根据温度穿晶型疲劳断裂沿晶型疲劳断裂剪切型疲劳断裂正断型疲劳断裂晶格型非晶格型机械疲劳断裂热疲劳断裂拉—压疲劳断裂弯曲疲劳断裂扭转疲劳断裂接触疲劳断裂低温疲劳断裂高温疲劳断裂机械疲劳断裂腐蚀疲劳断裂应力疲劳断裂应变疲劳断裂高周疲劳断裂低周疲劳断裂高频疲劳断裂低频疲劳断裂室温疲劳断裂图1 疲劳二级失效模式分类2 高周疲劳失效的影响因素2.1名义应力的影响很早的时候就确认名义应力会引起失效。
125年前Wohler[4]发现随着名义拉应力的增加引起失效的交变应力幅将随之减少。
后来Gerber[5]提出抛物线关系理论,即应力幅与名义应力间存在着抛物线关系,相应于零幅值交变应力的名义应力极限等于材料的拉伸极限。
Goodmen用对称交变应力和名义应力的线性关系代替抛物线关系增加了设计的安全裕度。
事实上,设计中很多有疲劳极限低于此直线值,Goodmen曲线实为一种保守设计。
Miller用循环应力代替但相对屈服应力对这一理论作了另一种解释。
令人惊讶的是,这些理论中的关系式没有一条被试验验证。
而我们却已把这些理论广泛用于工程实际,因此使用诸如Goodmen这些保守理论并非有什么不合理。
还有一种情况我们引起注意,即压应力并不减少改变许用的交变载荷。
事实上,平均压应力常会增加疲劳强度,所以对于设计计算,疲劳强度考虑成与零平均应力的疲劳强度相一致。
2.2 表面光洁度疲劳裂纹主要生产在材料的自由表面,因此表面因素的性质举足轻重。
经机械加工的表面特性,我们考虑以下三种因素:(1)不规则的表面划伤或表面粗糙度(2)表层中有残余应力(3)塑性变形和材料表面的微观结构1)表面粗糙度机械加工表面的粗糙度可用轮廓度计量,一般表示为偏离中心线的平均值(CLA)现在常用Ra值表示,Ra 值的范围从0.25的研磨光洁度至7.5微米的车削光洁度。
比较车削或者粗研与细研或抛光表面,对碳钢,表面粗糙度使疲劳强度降低大约10~25% ,而对高强度钢,表面租糙度的影响更加明显。
2)残余应力喷丸能够改变零件的疲劳强度已经被证实。
由于它对表面光洁度影响不大,很明显喷丸的引入是增加表面残余压应力有良性作用。
所以表面残余应力状态对疲劳强度有重要改善。
3)塑性变形和微观结构微观结构影响材料的疲劳特性广为人知,晶粒大小的影响更为重要。
然而在大型转子的制造过程中,考察材料基体是否变异的渠道少得可怜,而结构的选择考虑常常依附于从锻造到如何加工至最后形状相联系的工艺难易程度。
2.3 尺寸、应力梯度由于设计引起的应力集中影响尺寸影响被说成一种或多种因素,但最为人们接受的是如下观点:1)应力梯度影响:很清楚对于有同样表面应力的转轴,直径大的则应力梯度小,一旦疲劳萌生于次表层的危险区域内,那么大型转轴刚处于非常高的名义应力水平,继而疲劳强度降低。
这种解释适用于没有拉一压状况。
2)概率影响:因为疲劳萌生于表面薄弱处而强度受表面面积影响,所以面积愈大,强度愈低。
不管平板试件的疲劳强度受尺寸影响的真实情况如何,人们都相信切口平板试件的疲劳强度与尺寸关系甚为密切,小试件的最高疲劳强度趋干平板无切口试件的强度。
最大试件的强度趋于深切口敏感状态的强度,即疲劳强度为σ /K t ,其中σ是无切口平板的疲劳强度,Kt 为应力集中系数。
2.4 环境影响人们在许多年前就知道环境是影响金属疲劳强度的重要因素。
其影响分为两类,其一是疲劳强度的变化不受材料表面严重的腐蚀影响;其二是强度变化由腐蚀或蚀点引起。
第二类情况很难用实验定量分析,因为腐蚀贯穿于试件寿命的始终,也即许多年,而一般疲劳试验几个小时就完成了。
另外,腐蚀疲劳的特性与空气中的试验不一样,它的S —N 曲线常常是趋于连续向下,甚至在108个循环下也是如此,即没有疲劳极限。
2.5 微动影响众所周知,微动使得材料的疲劳强度急剧下降,例如用En 26钢 ( 0 .43 C ,2.56 Ni ,0.62 Cr ,0.54 Mo ),热处理至强度极限为1043MPa ,发现其微动疲劳强度降至±32MPa ,即仅为拉伸极限的3.1 % ,或者说无微动棒的疲劳强度的 1/17 。
比较公允的事实是相对滑移幅在8~14x10-8 毫米的范围内时,疲劳强度下降最低。
3 高周疲劳失效准则1)Gough 准则的Lee 修正式[5](/)(/)A A a a R b S t + (1) 其中A=2(1+BsinU ),Ra ,Sa 分别为分别为弯曲正应力幅和扭转应力幅, b 是指定寿命N 下的弯曲疲劳极限,t 是指定寿命N 下的剪切疲劳极限,U 为非比例加载时弯曲和扭转的相位差,B 为材料常数。
该准则在比例加载与非比例加载下均适用,比例加载条件下,Lee 修正式即Gough 准则。
2)Crossland 准则[6],,()H m H a K R R + (2)其中2121212,3(/1/,a K t f K t J =-=为应力偏量第二不变的幅值,,,H m H a R R ,分别为第一应力不变量的幅值和均值,2121t f ,分别为材料在对称扭转和弯曲时的疲劳强度。
该准则适用于2121/f t 的金属材料。
3)Mcdiarmid 准则[7](B)n max /t +/(2)a A f S R R , (3)式中Sa ,n max R ,为临界面上的剪切应力幅和最大正应力,(B)t A 分别为出现拉伸(剪切)破坏时的剪切疲劳强度f R 为材料在拉伸时的疲劳强度。
通过对EN24T 钢的管状试件进行弯扭实验表明,该准则在比例和非比例两种情况下都适用。
4) Papadopoulos 准则[8]a max ,,H m H a A+(T )(R +R ) (4)其中21max 21a a 21t ()3t f a T A C R S ⎡===⎢⎣,,,分别为弯曲正应力幅和扭转应力幅,,,H m H a R ,R 分别为第一应力不变量的幅值和均值,2121t f ,分别为材料在对称扭转和弯曲的疲劳强度。
该准则适用于2121/f t 的金属材料。
5) Susmel 准则[9]**n max 21a 21*a 2R R S S S ⎡⎤+-⎢⎥⎣⎦, (5) 式中*a S 为最大剪应力平面上的剪切应力幅,*n max R ,为临界面上的最大正应力,21S 为扭转疲劳极限21R ,为拉伸疲劳极限。
该准则在比例加载与非比例加载下均适用。
6) Liu 准则[10](6)其中22121k 9/4[3(/f )]t =-, ac R ,ac S ,I 分别为临界面上的正应力幅、 剪应力幅、 静水应力幅。
21t ,21f 分别为材料在对称扭转和弯曲的疲劳强度。
该准则适用于2121/f t 的金属材料。
4 研究高周疲劳的方法目前,确定叶片的疲劳寿命,从应力疲劳的角度讲[11],主要借助于应力一寿命的幂函数关 系或指数函数关系,从应变疲劳的角度讲,主要通过反映应变一寿命的Manson —coffi n 公式。
利用这些应力一寿命或应变一寿命关系,首先要确定叶片上的最大振动应力或最大振动应变[8],通常采用粘贴在叶片上的电阻应变片来确定叶片上的最大振动应力或最大振动应变。
测量过程中, 要求贴片位于叶片最大振动应力部位,要做到这一点,事实上是十分困难的,因为,叶片振动时最大应力部位与所出现的叶片振型有关,与叶片所受的其它负荷引起的应力有关,同时旋转下的叶片合成应力,使得最大应力区有所改变,所以,测量结果很难准确地反映最大振动应力或最大振动应变。
如欲提高测试精度,只好在最大应力区多贴几片,逐点测量,观测其中最大值,显然这样做工作量太大。
另外,叶片振动过程中,其上应力一应变处于弹性、三轴状态,在这种情况下,前述应力一寿命或应变一寿命关系的适用性及精确性值得怀疑,为解决这些困难,提出了af 值( 叶尖振幅与叶片固有振动频率乘积)的概念,af 值能够反映叶片上的最大应力和最大应变,它的提出,一方面,解决了在叶片上寻找最大应力部位的困难,另一方面,测量低阶振动与高阶振动一样,都不需要寻求最大振动应力部位。
既然af 值反映了叶片上的最大振动应力和最大振动应变,它也一定与叶片疲劳寿命存在关系。
经过研究得到:1 ) 航空发动机压气机叶片振动状态下,af 值与叶片疲劳寿命 N 的关系为 1c afd be N -=() 其中:b 、c 、d 是由试验确定的常数,它们不仅与叶片材料有关,而且还与叶片形状有关。
与传统的应力疲劳的数学模型相比,af 值与叶片疲劳寿命N 的关系既不是幂函数,也不是简单的指数函数。
2 ) a f 值与叶片疲劳寿命 N 的关系提供了确定叶片振动疲劳寿命的可能。
3 ) a f 值与叶片疲劳寿命 N 的关系提供了研究材料多轴高周疲劳行为的新途径。
5 结束语随着工业技术的发展,很多可能产生疲劳破坏的发动机叶片的设计寿命越来越高,因此,金属高周疲劳甚至超高范围疲劳成为一个值得关注的课题。
虽然在过去几十年已经展开了一些研究,但是所得到的结果和建立的理论还不能满足疲劳设计的需要。
6 参考文献[1] Wang WeiHua , Wang R J , Li F Y , etal. Elastic constants and their pressure dependence of Zr 41Ti 14Cu 12. 5Ni 9Be 22.5C1bulk metallic glass. Applied Physics Letters ,1999,74(13) :1803~ 1805。