循环水泵叶片断裂的原因分析与处理
循环泵叶片断裂问题原因分析与治理

循环泵叶片断裂问题原因分析与治理刘启民摘要:由于设计原因导致循环泵叶轮连续断裂,经过多次审核泵体设计方案、叶片强度计算以及原因分析,采取了重新修正设计与完善泵体方案等措施,治理后循环泵各振动指标达到合格标准,可以长周期连续运行。
关键词:叶片振动断裂汽蚀1 概述国华陈家港发电公司2×660MW机组循环水泵自2011年5月16日开始试运,期间循环泵振动情况:径向振动达到良好,但轴向振动偏大。
机组通过168试运后,至2012年3月12日正常运行中,2B循环泵第一次发生首次叶片断裂。
截止2012年年10月份,循环泵叶片断裂5次/台(其中最终加厚叶片断裂2次),发现裂纹2次,解体检修9次/台。
日立泵业经过多次复核设计方案、强度计算与原因分析,采取重新修正设计与完善泵体设计方案等措施,,叶片厚度由初始17.6mm、25.3mm最终增加至35.1mm,截止2012年8月20日最终确定了治理方案,并付诸实施。
截止2012年10月20日,治理后的1A、2A、2B循环泵,径向、轴向振动均达合格标准,各项运行指标与其它发电公司循环泵状态类似,就目前1A、2A、2B循环泵运行(2B备用)情况看,可以尝试长期连续运行,叶片断裂的可能性大幅度降低,但还需时间考验。
1B循环泵正在进行永久方案的隐患治理中,预计10月28日具备试运条件。
2 故障现象(1)泵轴向振动较大,振动值在100~160um波动;(2)运行中叶片断裂。
3 故障原因2012年3月2B循环泵叶片首次断裂后,日立泵业分析原因为叶片强度不足,并连续增加了叶片的厚度,经过实践考验,叶片又发生2次断裂。
经过多次解体检查及运行状态分析,最终确定了循环泵轴向振动大与叶片断裂的主要原因。
(一)判定依据:(1)泵入口处漩涡增大,造成作用在叶片上的交变应力增加,实验室模型试验测量结果显示,漩涡作用在叶片上的交变载荷与无漩涡状态比较,最大约1.7倍程度;(2)泵入口汽蚀使得叶片交变载荷增加,试验结果为无汽蚀状态约3.7倍;(3)喇叭口处电极孔(直径100mm)加剧了入口处水流态的绝缘板恶化,使得作用在叶片根部的交变应力过大,试验结果显示增加叶片交变载荷1.4倍;(二)原因分析(1)设计、制造原因①叶片疲劳强度不足叶轮材料采用双相不锈钢,双向铸钢叶轮设计的疲劳强度无试验值,日立泵业参照该种材料钢板的疲劳强度数值(400MPa)进行设计,日方按照经验取值为:400*0.6*0.92=221MPa,即叶片设计疲劳强度为221MPa。
循环水泵叶片断裂的原因分析与处理
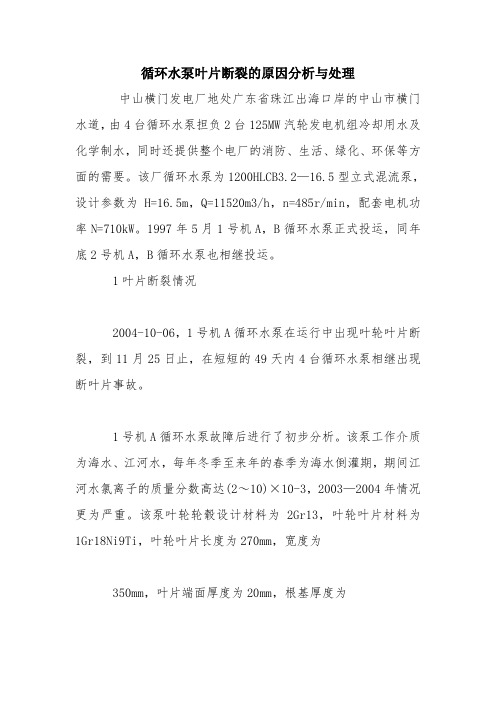
循环水泵叶片断裂的原因分析与处理中山横门发电厂地处广东省珠江出海口岸的中山市横门水道,由4台循环水泵担负2台125MW汽轮发电机组冷却用水及化学制水,同时还提供整个电厂的消防、生活、绿化、环保等方面的需要。
该厂循环水泵为1200HLCB3.2—16.5型立式混流泵,设计参数为H=16.5m,Q=11520m3/h,n=485r/min,配套电机功率N=710kW。
1997年5月1号机A,B循环水泵正式投运,同年底2号机A,B循环水泵也相继投运。
1叶片断裂情况2004-10-06,1号机A循环水泵在运行中出现叶轮叶片断裂,到11月25日止,在短短的49天内4台循环水泵相继出现断叶片事故。
1号机A循环水泵故障后进行了初步分析。
该泵工作介质为海水、江河水,每年冬季至来年的春季为海水倒灌期,期间江河水氯离子的质量分数高达(2~10)×10-3,2003—2004年情况更为严重。
该泵叶轮轮毂设计材料为2Gr13,叶轮叶片材料为1Gr18Ni9Ti,叶轮叶片长度为270mm,宽度为350mm,叶片端面厚度为20mm,根基厚度为20mm,根部焊接宽度为180mm,共7个叶片组成叶轮组。
运行中发现该泵电机上导轴承振动突然增大而紧急停泵,经解体检查,发现该泵叶轮叶片断裂一片,断口在叶片根部,呈亮白色,有金属的光泽,断面上带有明显的“人”字型纹路,属脆性断裂。
除断的1片外,其余6片中的5片根部都有明显的深浅程度不一的断裂源。
对7片叶片受力面进行显微组织分析,除1片外,其余6片均有纵横交错的龟裂纹。
由上所述,判断造成循环水泵叶片断裂的原因,是典型的奥氏体不锈钢受晶间腐蚀、焊缝热裂纹及电化学等综合影响的结果。
2断裂原因分析2.1合金元素贫乏化由于铬镍奥氏体不锈钢在加热过程中晶界容易析出碳化物第2相,造成晶界某成分的贫乏化,如:1Gr18Ni9Ti不锈钢因晶界析出沉淀相Gr23C6,使晶界附近留下贫铬区。
由于该类钢加热和冷却不发生α-γ相变,不能淬火强化,强度、硬度低,当在450~850℃温度内保温或缓慢冷却,然后在一定腐蚀介质中暴露一定时间,就会产生晶间腐蚀,在650~750℃范围内加热一定时间,这类钢的晶间腐蚀更为敏感,普遍认为在上述温度范围内,将沿奥氏体晶界析出Gr23C6,从而使奥氏体晶界附近区域的含铬量低于11.7%。
循环水泵叶片故障的原因分析及预防
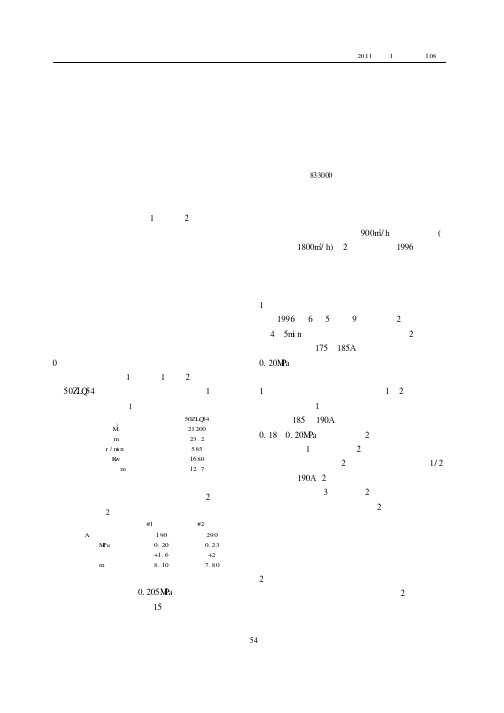
0 概况
元宝山发电厂 1 号机组 1 号、2 号循环水泵皆
为 50ZLQ54 型轴流泵,其规范特性如表 1:
表1
型号 流量 M3 扬程 m 转速 r / mi n 功率 Kw 汽蚀余量 m
循环泵规范 50ZLQ54 21 200 23. 2 5 85 16 80 12. 7
在叶轮叶在整个叶栅上逐个叶 片地传播,产生旋转脱流。
(a)零冲角流动;(b)冲角增大,尾部出现旋涡;(c)严 重脱流
图 2 流体绕流叶型脱流的产生
K点的位置取决于液流在叶片进口处的冲角和 叶片轴与泵的夹角。
根据理论分析和试验结果,拟采用 l =A·cos( B·i ) 式中 A和 B是试验确定的经验数,它们随角的 不同而变化。若忽略重力的影响,并认为离心力矩 在旋转脱流现象中变化不大,则叶片上水力矩的变 化即为总力矩的变化。 反洗滤网前时,阻力增加,流量减少,沿叶型 流动的流体冲角增大,在某些叶片上首先发生了脱 流。随着流量的不断减少,冲角越来越大,叶片的 工作面和非工作面压差增大,出现汽蚀现象,有汽 蚀噪声。同时旋转脱流的频率迅速接近叶片的固有 频率,叶片发生共振,发出闷响的声音。 共振使得流道更加堵塞,流量下降。当流量小 到扬程曲线最高点 K相应的流量时,水泵发生喘振 现象,流量在一定范围内波动,因此 2 号循环水泵
2 事故原因分析 事故发生后进行了分析,认为:2 号循环水泵
发生三声闷响是由于水旋转脱流的频率接近叶片
· 54 ·
新疆电力技术
2011 年第 1 期 总第 108 期
的固有频率,叶片发生共振造成的;2 号循环水泵 电流下降,出口压力降低,是叶片共振后,流量减 少,循环水泵发生喘振引起。 2.1 旋转脱流
混流式水轮机转轮裂纹原因分析及预防措施

混流式水轮机转轮裂纹原因分析及预防措施混流式水轮机转轮裂纹原因分析及预防措施水轮机转轮,特别是中、高比速混流式水轮机转轮中的裂纹现象,在世界各地普遍存在。
国外的例子有埃及的阿斯旺高坝、美国的大古力700 MW机,俄罗斯的布拉茨克等。
国内有岩滩、李家峡、小浪底、五强溪、二滩等大型水电站,在投运后水轮机转轮都不同程度的浮现了裂纹。
转轮裂纹严重影响电站的安全运行和经济效益,引起人们的极大关注。
1转轮裂纹的产生原因转轮为什么会产生裂纹,人们对此做过许多研究,不时地提出一些假设。
笔者把转轮裂纹分为规律性裂纹和非规律性裂纹两类。
规律性裂纹是指不同叶片上的裂纹具有大体一致的规律,所有叶片都开裂,裂纹的部位和走向也大致相同。
非规律性裂纹或者只在个别叶片上发生,或者不同叶片上裂纹的部位、走向和其他特征各不相同。
其产生的普通原因分述如下。
1.1规律性裂纹失效分析结果表明-绝大多数规律性裂纹是疲劳裂纹,断口呈现明显的贝壳纹。
叶片疲劳来源于作用其上的交变载荷,而交变载荷又由转轮的水力自激振动引起,这可能是卡门涡列、水力弹性振动或者水压力脉动所诱发。
1.1.1卡门涡列(1)黄坛口水电站1958年投运的4台HL310-LJ-230水轮机,运行不久转轮叶片出水边根部即发生总计67条裂纹。
后来查明,在某些水头下,当机组出力在5~8 MW时,叶片出水边卡门涡列频率与叶片自振频率耦合而引起共振,动应力急剧增加,使叶片疲劳开裂。
采取修整叶片出水边厚度和形状,提高卡门涡列频率,避开了共振,转轮安全运行多年,再没有发生问题。
(2)小浪底水电站水头范围68~141 m,额定出力306 MW。
水轮机转轮上冠和下环为13.5不锈钢铸件,叶片由13.5不锈钢热模压后数控加工,再用309 L奥氏体不锈钢焊丝焊成整体。
由于是异种钢焊接,转轮焊后不进行消除应力处理。
为适应电站水头变幅大和多泥沙的运行条件,水轮机供应商采取了低比转速,小的出口直径(D 2/D 1=0.88),较大的导叶相对高度(b 0/D 1=0.236),肥大的叶片头部,较厚的叶片出水边(δ=38 mm),喷涂碳化钨和设置筒形阀等技术措施。
水轮机叶片裂纹原因分析及现场修复措施
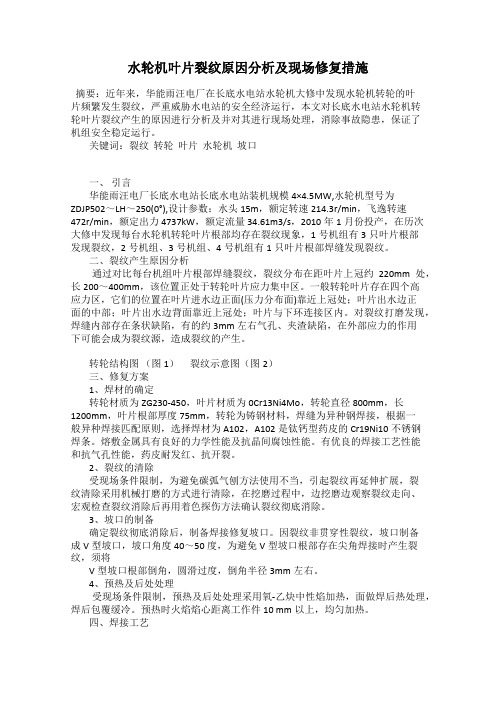
水轮机叶片裂纹原因分析及现场修复措施摘要:近年来,华能雨汪电厂在长底水电站水轮机大修中发现水轮机转轮的叶片频繁发生裂纹,严重威胁水电站的安全经济运行,本文对长底水电站水轮机转轮叶片裂纹产生的原因进行分析及并对其进行现场处理,消除事故隐患,保证了机组安全稳定运行。
关键词:裂纹转轮叶片水轮机坡口一、引言华能雨汪电厂长底水电站长底水电站装机规模4×4.5MW,水轮机型号为ZDJP502~LH~250(0°),设计参数:水头15m,额定转速214.3r/min,飞逸转速472r/min,额定出力 4737kW,额定流量 34.61m3/s,2010年1月份投产,在历次大修中发现每台水轮机转轮叶片根部均存在裂纹现象,1号机组有3只叶片根部发现裂纹,2号机组、3号机组、4号机组有1只叶片根部焊缝发现裂纹。
二、裂纹产生原因分析通过对比每台机组叶片根部焊缝裂纹,裂纹分布在距叶片上冠约220mm处,长200~400mm,该位置正处于转轮叶片应力集中区。
一般转轮叶片存在四个高应力区,它们的位置在叶片进水边正面(压力分布面)靠近上冠处;叶片出水边正面的中部;叶片出水边背面靠近上冠处;叶片与下环连接区内。
对裂纹打磨发现,焊缝内部存在条状缺陷,有的约3mm左右气孔、夹渣缺陷,在外部应力的作用下可能会成为裂纹源,造成裂纹的产生。
转轮结构图(图1)裂纹示意图(图2)三、修复方案1、焊材的确定转轮材质为ZG230-450,叶片材质为0Cr13Ni4Mo,转轮直径800mm,长1200mm,叶片根部厚度75mm,转轮为铸钢材料,焊缝为异种钢焊接,根据一般异种焊接匹配原则,选择焊材为A102,A102是钛钙型药皮的Cr19Ni10不锈钢焊条。
熔敷金属具有良好的力学性能及抗晶间腐蚀性能。
有优良的焊接工艺性能和抗气孔性能,药皮耐发红、抗开裂。
2、裂纹的清除受现场条件限制,为避免碳弧气刨方法使用不当,引起裂纹再延伸扩展,裂纹清除采用机械打磨的方式进行清除,在挖磨过程中,边挖磨边观察裂纹走向、宏观检查裂纹消除后再用着色探伤方法确认裂纹彻底消除。
150MW火电机组循环水泵轴断裂原因分析
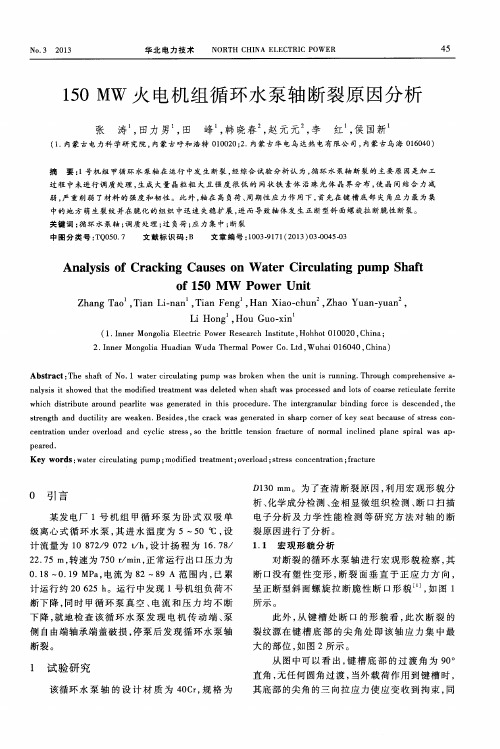
Abs t r a c t : Th e s h a f t o f No . 1 wa t e r c i r c u l a t i n g p u mp wa s b r o k e n wh e n t h e u n i t i s r u n n i n g . T h r o u g h c o mp r e h e n s i v e a - n a l y s i s i t s h o we d t h a t t h e mo d i f i e d t r e a t me n t wa s d e l e t e d wh e n s h a f t wa s p r o c e s s e d a n d l o t s o f c o a r s e r e t i c u l a t e f e r r i t e wh i c h d i s t r i b u t e a r o u n d p e a r l i t e wa s g e n e r a t e d i n t h i s p r o c e d u r e . T h e i n t e r g r a n u l a r b i n d i n g f o r c e i s d e s c e n d e d, t h e s t r e n g t h a n d d u c t i l i t y a r e we a k e n . Be s i d e s , t h e c r a c k wa s g e n e r a t e d i n s h a r p c o r n e r o f k e y s e a t b e c a u s e o f s t r e s s c o n —
p e a r e d. Ke y wo r d s : wa t e r c i r c u l a t i n g p u mp; mo d i f i e d t r e a t me n t ; o v e r l o a d; s t r e s s c o n c e n t r a t i o n; f r a c t u r e
水轮机转轮叶片裂纹成因及对策分析

使水流环量大小和方 向发 生变 化 , 在转 轮叶片 出水边 、 尾水管 内形成不稳定旋涡 。 当水流绕流 叶片 , 由出 口边( 圆形出水边) 出时 , 流 便会 在 出 口边产生卡 门涡列 , 涡交替 出现形成对叶 片 旋 侧向的交变力 , 并形成有规则 的周期 性振动 , 其 振动频率 与 叶片出 口边 的厚度 及流速有 一定 的关系 ,当 冲击频率与 叶片 自 频率相 同便产 振
这些 脉动压 力将引起叶 片的交变应力 。有资料 表明俄 罗斯 克拉斯诺雅尔斯克水 电站水 轮机转 轮 在非设 计 工况 下 ,动应力 达最 大 静应 力 的 1%。可见尾水管压 力脉动能 引起 一定幅值 的 5 交变应力 ,若这种激振频 率与叶片或下环 的固
有频率耦合 时 , 必将诱 发更大的动应力 , 造成 叶
片开裂。
3裂纹无损探伤检查 在大修时对转 轮进行无损探伤检查 , 时 及
处理 缺陷 , 消除事故 隐患是十分必要 的。 严重 的 和表面发现缺 陷的部位进行超声波探伤 。检验 裂纹 等缺 陷用 肉 眼和放 大镜 外 观检 查 即可 发 中发现 的裂纹等危险 陛缺陷应进行处理。 4裂纹处理 现 ,但较细小 的缺 陷和内部的缺陷必须用无 损 探 伤检查。 常用的无 损检测方法有以下几种 : 磁 4 . 1阻止裂纹延伸 粉探伤 、 渗透探伤 、 超声波探 伤 、 金属磁记忆 、 射 通常裂纹的两端尾部 内应力接近材料 的极 线检测等。 裂纹易于产生的应力集 中部位 , 叶 限强度 , 如 在外力或热 应力的影响下还会继续延 必须在裂纹两 端打止裂孑 , L孔径应不 片进水边正面 ( 压力分 布圃 靠近上冠处 、 叶片出 伸 。因此 , a r 水边 正面的 中部 、 出水边 背面靠近上冠 处 、 小于 6 m,裂纹清理过程 中如发现纹路有新 的 叶片 叶片与下环连接 区等部位 ,由于 透照布置 比较 的发展趋势应停 止清理 , 加止裂孔 , 再追 一般孔 困难 , 不能用射线透照法进行无损探伤 。 根据水 深应 比裂纹深度大 4 6 m -m 。 轮机转轮叶片表 面比较粗糙 、结构复杂 和厚度 4 . 2裂纹清理及开坡 口 变化 大的特点 , 一般应 采用渗 透 、 磁粉 、 超声 波 裂纹铲 除常用 两种方 法 : 风铲和炭弧气刨。 和金属磁记 的方法进行无损检测。 风铲铲 除裂 纹所形成的坡 口较规则 ,易于保证 31超声波检测 . 焊接 质量 , 劳动强度 大 , 但 速度 慢 , 铲头 可根据 超声波探伤方法对裂纹 、 未熔合等 面积 型 裂纹 深度的不同而选用 ,坡 口要求规则平 滑并 缺陷 的检 出率 较高 , 宜检验较大厚度 的工件 , 用 3% 的硫酸或硝酸酒精清洗 ; 适 0 炭弧气刨 可对 但是对 于铸钢 、 氏体 不锈钢材 , 奥 由于粗 大晶粒 较深 的裂纹 进行多次吹割 , 这种方法操作 简便 , 的晶界会反射声 波 , 幕上出现大量 的“ 在屏 草状 速度快 , 口内往往 有渗碳层 , 但坡 要用异型砂轮 回波” 容易 与缺陷波混 淆 ,影响检测可 靠性 , 磨削 。 , 为了防止过热 引起变形 和裂纹扩展 , 炭弧 限制 了超声波 探伤方法在铸钢制水轮机 转子叶 气刨 必须间断使用 。坡 口的形式应遵守焊 接工 片上无损检测 的应用 。 探测频率越高 , 杂波就越 艺的一般要求 ,主要 根据裂纹情况 、 部位 和铲 显著 , 为了减小 晶界反 射波的影响 , 我们采用 了 除及施 焊方 便而定。裂纹清除后应进行着 色探 低频探头(5 z 2 MH) .  ̄ 转子进行超声 波探伤 , 伤 以确认裂纹是否全部清除干净 。 发现反射信 号以后再用高 频探头( z S ) 定 MH 进行 4 . 3补焊工艺 量 , 证明这是可行 的。 实践 铸钢件超声波探伤衰 叶片补焊可采用 两种 方法 , 是同种材料 一 减很大 , 探伤时 只有满 足以下条件才 能检 测 , 则 热焊 , 方法工艺较 复杂 , 这种 要进行焊前 预热 和 底波与林状 回波至少应有 3 分贝差。 O 焊后 热处理 , 接条件较恶劣 , 焊 但是 由于补 焊焊 3 2渗透探 伤 缝 的填充材料和被补焊母材基本一 致 , 因此 , 在 渗透探伤方法简单易行 , 直观 , 于 使用 过程中出现问题 的可能性较小 ;另一 种是 显示 适合 大型和不规则 工件 的检查和现场检修检 查。但 奥氏体焊条进行冷焊 。 冷补焊 工艺简单 , 生产周 是 ,渗透探伤方法是利用 渗透能力强的彩色 渗 期短 。 补焊焊接过程 中不发生相变 , 冷 且焊缝的 透液渗入到裂纹 等缺陷的缝隙 中,再利用 吸附 塑性较 好。因此 , 案可不预热 , 该方 简化 了补焊 能力强 的白色显像 剂 , 渗透液吸 出来 以显示 工艺 , 了铸 钢件受到大的热作用 , 将 避免 从而减小 缺陷的 ,因此 , 只能检查表面开 口的缺陷。 了被 焊件的应 力和变形 。奥 氏体焊条冷焊 工艺 3 - 3磁粉探 伤 简单 , 但是补焊 金属强度低于母材 , 由于不预 且 磁粉探伤方法是利用工件磁化后 , 在材料 热冷焊 , 区的冷却 速度较大 , 近缝 不可避免在补 中的不连续部位( 包括缺陷造成 的不连续 性和结 焊 的近缝 区产生淬硬组织 ,给补焊接头 的性能 构、 形状 、 等原 因造成 的不 连续性) 材质 , 磁力 线 带来不利影响 。 会发生畸变 ,部分磁 力线有可能逸 出材料表 面 4 . 冷焊工艺 .1 3 形成漏磁场 , 这时在工件上撒上 磁粉 , 漏磁场 就 裂纹确认清除 干净 、 开坡 口 , 后 按下列顺序 会 吸附磁粉 , 形成与缺 陷形状 相近的磁粉堆 积 , 进行补焊 : 从而显示缺陷。 因此 , 粉探伤适 用于铁磁材料 磁 a 补焊 区域进行 预热 , ) 对 预热温度 为 10 0 探伤 , 可以检出表面和 近表面缺陷 , 但是有些部 10C , q 对挖补 区域可采用局部 加热 , 5 可用履带 位由于难以磁 化而无 法探 伤。 加热器进行 加热 , 履带加热器 , 若无 也可用 乙炔 综 上 所述 ,为 了保 证水 电机 组 的安 全运 焰在坡 口处来 回移动加热。 行 , 到各种探伤 的优 点和局限性 , 考虑 水轮机转 b A37 ) . 焊条进 行补焊 , 用 0 �
排涝水泵叶片断裂事故分析及处理措施
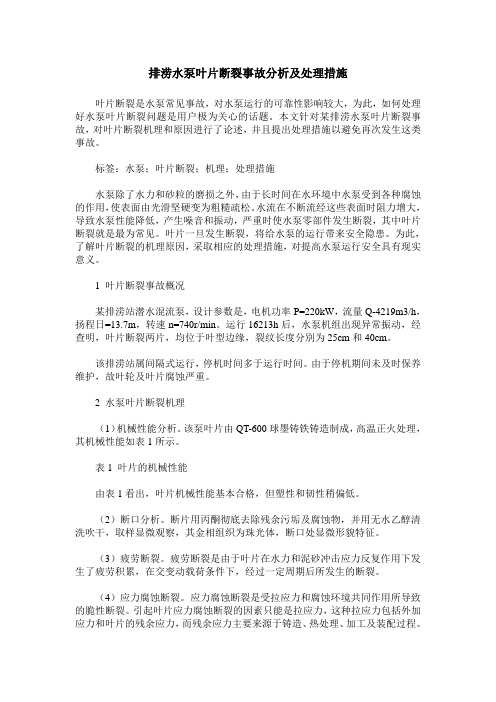
排涝水泵叶片断裂事故分析及处理措施叶片断裂是水泵常见事故,对水泵运行的可靠性影响较大,为此,如何处理好水泵叶片断裂问题是用户极为关心的话题。
本文针对某排涝水泵叶片断裂事故,对叶片断裂机理和原因进行了论述,并且提出处理措施以避免再次发生这类事故。
标签:水泵;叶片断裂;机理;处理措施水泵除了水力和砂粒的磨损之外,由于长时间在水环境中水泵受到各种腐蚀的作用,使表面由光滑坚硬变为粗糙疏松。
水流在不断流经这些表面时阻力增大,导致水泵性能降低,产生噪音和振动,严重时使水泵零部件发生断裂,其中叶片断裂就是最为常见。
叶片一旦发生断裂,将给水泵的运行带来安全隐患。
为此,了解叶片断裂的机理原因,采取相应的处理措施,对提高水泵运行安全具有现实意义。
1 叶片断裂事故概况某排涝站潜水混流泵,设计参数是,电机功率P=220kW,流量Q-4219m3/h,扬程日=13.7m,转速n=740r/min。
运行16213h后,水泵机组出现异常振动,经查明,叶片断裂两片,均位于叶型边缘,裂纹长度分別为25cm和40cm。
该排涝站属间隔式运行,停机时间多于运行时间。
由于停机期间未及时保养维护,故叶轮及叶片腐蚀严重。
2 水泵叶片断裂机理(1)机械性能分析。
该泵叶片由QT-600球墨铸铁铸造制成,高温正火处理,其机械性能如表1所示。
表1 叶片的机械性能由表1看出,叶片机械性能基本合格,但塑性和韧性稍偏低。
(2)断口分析。
断片用丙酮彻底去除残余污垢及腐蚀物,并用无水乙醇清洗吹干,取样显微观察,其金相组织为珠光体,断口处显微形貌特征。
(3)疲劳断裂。
疲劳断裂是由于叶片在水力和泥砂冲击应力反复作用下发生了疲劳积累,在交变动载荷条件下,经过一定周期后所发生的断裂。
(4)应力腐蚀断裂。
应力腐蚀断裂是受拉应力和腐蚀环境共同作用所导致的脆性断裂。
引起叶片应力腐蚀断裂的因素只能是拉应力,这种拉应力包括外加应力和叶片的残余应力,而残余应力主要来源于铸造、热处理、加工及装配过程。
- 1、下载文档前请自行甄别文档内容的完整性,平台不提供额外的编辑、内容补充、找答案等附加服务。
- 2、"仅部分预览"的文档,不可在线预览部分如存在完整性等问题,可反馈申请退款(可完整预览的文档不适用该条件!)。
- 3、如文档侵犯您的权益,请联系客服反馈,我们会尽快为您处理(人工客服工作时间:9:00-18:30)。
循环水泵叶片断裂的原因分析与处理
集团公司文件内部编码:(TTT-UUTT-MMYB-URTTY-ITTLTY-
循环水泵叶片断裂的原因分析与处理中山横门发电厂地处广东省珠江出海口岸的中山市横门水道,由4台循环水泵担负2台125MW汽轮发电机组冷却用水及化学制水,同时还提供整个电厂的消防、生活、绿化、环保等方面的需要。
该厂循环水泵为1200HLCB3.2—16.5型立式混流泵,设计参数为H=16.5m,
Q=11520m3/h,n=485r/min,配套电机功率N=710kW。
1997年5月1号机A,B循环水泵正式投运,同年底2号机A,B循环水泵也相继投运。
1叶片断裂情况
2004-10-06,1号机A循环水泵在运行中出现叶轮叶片断裂,到11月25日止,在短短的49天内4台循环水泵相继出现断叶片事故。
1号机A循环水泵故障后进行了初步分析。
该泵工作介质为海水、江河水,每年冬季至来年的春季为海水倒灌期,期间江河水氯离子的质量分数高达(2~10)×10-3,2003—2004年情况更为严重。
该泵叶轮轮毂设
计材料为2Gr13,叶轮叶片材料为1Gr18Ni9Ti,叶轮叶片长度为270mm,宽度为
350mm,叶片端面厚度为20mm,根基厚度为
20mm,根部焊接宽度为180mm,共7个叶片组成叶轮组。
运行中发现该泵电机上导轴承振动突然增大而紧急停泵,经解体检查,发现该泵叶轮叶片断裂一片,断口在叶片根部,呈亮白色,有金属的光泽,断面上带有明显的“人”字型纹路,属脆性断裂。
除断的1片外,其余6片中的5片根部都有明显的深浅程度不一的断裂源。
对7片叶片受力面进行显微组织分析,除1片外,其余6片均有纵横交错的龟裂纹。
由上所述,判断造成循环水泵叶片断裂的原因,是典型的奥氏体不锈钢受晶间腐蚀、焊缝热裂纹及电化学等综合影响的结果。
2断裂原因分析
2.1合金元素贫乏化
由于铬镍奥氏体不锈钢在加热过程中晶界容易析出碳化物第2相,造成晶界某成分的贫乏化,如:1Gr18Ni9Ti不锈钢因晶界析出沉淀相
Gr23C6,使晶界附近留下贫铬区。
由于该类钢加热和冷却不发生α-γ相变,不能淬火强化,强度、硬度低,当在450~850℃温度内保温或缓慢冷却,然后在一定腐蚀介质中暴露一定时间,就会产生晶间腐蚀,在650~750℃范围内加热一定时间,这类钢的晶间腐蚀更为敏感,普遍认为在上述温度范围内,将沿奥氏体晶界析出Gr23C6,从而使奥氏体晶界附近区域的含铬量低于11.7%。
然而,贫铬区宽度很窄,如:18~8奥氏体不锈钢在650℃敏化处理2h,贫铬区总宽度为150~200nm,其中贫铬严重区宽度不到50nm,导致沿奥氏体晶界附近产生腐蚀,所以不锈钢的机体中铬的质量分数不得低于11.7%。
该厂循环水泵叶片材质为奥氏体
1Gr18Ni9Ti
不锈钢,在叶片的制造、加工固溶处理时,如果该叶片在450~850℃区间内停留一定的时间后,将促进[Fe,Gr]C在晶界析出,其中的铬
主要来自晶粒表层,而内部的铬来不及补充,使晶界的晶粒表层的含铬量下降,形成贫铬区。
而贫铬区的含铬量远低于钝化所需的极限值,其电势比晶粒内部的电势低,更低于碳化物的电势。
贫铬区和碳化物是紧密相连的,遇到一定的腐蚀介质,就会发生短路电池效应。
该厂循环水泵叶轮在氯离子含量很高的江水中长期运行,这种情况下,碳化铬和晶粒呈阴极,使呈阳极的贫铬区被迅速侵蚀,引起力学性能下降,在受力时沿晶界断裂。