环锭纺梳理技术的发展与应用
环锭纺纱技术的发展与创新

论 文PAPER纺纱是纺织产业链的第一道工序,其产品质量档次、生产效率与加工成本在整个产业链中具有十分重要的地位。
随着纺织科学技术的发展,目前在纺纱生产中普遍采用两类纺纱技术,一种是环锭纺文|赵亮 厉勇 李杰 张剑锋 王丽丽环锭纺纱技术的发展与创新近几年来,环锭纺纱技术通过不断改进与技术创新,在多种纺纱技术共同发展中继续保持领先地位。
紧密纺纱与复合纺纱技术显著提升了环锭纺纱线品质档次,并扩宽了环锭纺纱线的应用领域,是对环锭纺技术的发展与创新。
采用带自动落纱的环锭细纱长机与细络联合机是环锭纺技术进一步发展的方向。
要使环锭细纱机实现优质高产、效益最佳,选好主机是基础,配好器材专件是关键。
关键词:环锭纺 紧密纺 复合纺 低扭矩纺 发展 创新纱技术,从发明到应用已有100多年历史。
另一种是新型纺纱技术,如转杯纺、喷气纺、喷气涡流纺等,由于其成纱机理、成纱结构不同于环锭纺,并在纺纱工序缩短、劳动用工减少等方面具有一定优势,故近期得到快速发展,用新型纺纱技术生产的各类纱线比重逐年有较大增加。
但从总体分析,目前用环锭纺纱机生产的纱线仍占主导地位,国内外90%短纤纱线是在环锭纺纱机上加工生产的。
前言1环锭纺纱技术的发展跨入2l 世纪以来,随着纺纱技术的不断进步,环锭纺纱技术不但在纺纱方法上取得了重大突破与改进,而且在纺纱技术装备上运用高科技手段在智能化、自动化、机电一体化技术等方面也有重大创新,环锭纺纱技术正以崭新的面貌展示在纺纱领域,主要反映在以下5个方面。
(1)紧密纺技术(又称集聚纺)的研发成功与投入生产,标志着环锭纺纱技术进入了一个新的历史发展阶段,用紧密纺技术生产的纱线在可纺支数与品质方面比传统环锭纺及新型纺纱均具有明显优势。
(2)在环锭细纱机上采用多种形式复合纺纱技术,使环锭纺纱线不仅呈现原料、色泽多元化,而且形态结构多样化,进一步拓宽了环锭纺生产纱线的应用领域。
(3)围绕减少纺纱用工提高劳动生产率,在环锭细纱机上广泛应用自动化、机电一体化等新技术,在国外带自动落纱细纱长车及细络联已得到广泛应用,在国内带集体络纱的细纱长机也取得长足进步,正在逐步推广应用,并正在向细络联与粗细联延伸,实现纺纱工序的连续化。
环锭细纱机的技术进步

环锭细纱机的技术进步内容摘要:当代环锭细纱机在牵伸加压形式、卷捻技术、传动方式、长车和细络联以及紧密纺纱技术等有了很大的发展,已形成了高科技的环锭纺纱机。
本文对上述几个方面进行了详细的讨论。
关键词伸形式钢领钢丝圈高速锭子变频调速紧密纺纱技术目前全世界约有1.7亿枚棉纺环锭细纱机,800万头转杯纺,其它新型纺纱如喷气纺、涡流纺等容量很少。
但转杯纱产量占全部纱线市场的42%,环锭纱占56%,其它如喷气纺占2%。
环锭纺是传统纺纱方法,工艺技术十分成熟,是纺纱生产中占比例最大、又十分重要的纺纱方式。
新型纺纱技术虽然生产效率高、工艺流程短,品种、纱支适应性好,但成纱结构及性能不如环锭纱,所以在相当长的时期内不可能完全取代环锭纱,因此,环锭纺仍然是现代纺纱生产中最主要的纺纱方式。
在20世纪后半期,环锭纺纱技术有很大进步,细纱机锭速达到25000转/分,一台细纱机锭数已发展到1400锭,牵伸倍数230倍左右,在牵伸形式、加压、锭子、钢领钢丝圈、吸棉、纱管、胶辊、胶圈、传动技术等方面都有了很大发展,在细纱与自动络纱联合技术上也有了新的突破,有不少机型都形成了细络联。
代表国际先进水平的机型有瑞士立达公司、德国绪森公司、意大利马佐里公司及以德国青泽公司生产的各种新型环锭细纱机,在高速、高效、节能、机电一体化及自动控制自动化方面都已达到很高水平。
1999年巴黎展览会上,瑞士立达、德国绪森等公司展出了紧密纺环锭细纱机,这是环锭纺纱技术新的突破,紧密环锭纺纱技术是在细纱牵伸区以外,增加了凝聚细纱须条的机构,消除了加捻三角区,成纱质量更为优越:减少了细纱毛羽,提高细纱强力,改善了细纱条干,为下游工序提高织物质量,减少上浆负担、取消烧毛等创造了条件,与此同时,细纱制成率提高,飞花减少,对提高经济效益及改善生产环境都有明显作用。
我国FA500系列环锭细纱机,在贯彻重加压,强控制、大牵伸的工艺路线上,吸收了国外先进环锭细纱机的经验及特点,结合我国国情进行较大改进,结构比较合理,制造精度有所提高,设备运转可靠性、稳定性也有进一步提高,适纺性能强,纺纱质量进一步提高。
精梳环锭纺的纺纱工艺流程及半制品名称

精梳环锭纺的纺纱工艺流程及半制品名称1. 引言1.1 精梳环锭纺简介精梳环锭纺是一种先进的纺纱技术,采用先进的环锭纺纱机进行生产。
该技术在纺纱过程中能够有效剔除纤维中的短纤维和杂质,使纺出的纱线质量更加优秀。
精梳环锭纺具有纤维长度长、纱线强力高、表面光滑等优点,是高档纺织品生产的关键工艺之一。
精梳环锭纺具有高度自动化生产线,生产效率高,可采用多种类型的纤维原料进行生产。
这种技术在纺织行业中得到了广泛应用,生产出的纱线被广泛用于高档纺织品的生产中。
2. 正文2.1 纺纱工艺流程纺纱工艺流程是整个精梳环锭纺生产过程中至关重要的一部分,可以分为精梳纺前处理、精梳纺和精梳纺半制品名称三部分。
首先是精梳纺前处理,这一步骤主要包括原料的准备和清洗工作。
在精梳环锭纺生产过程中,纺纱的原料通常为棉花,而在进行纺纱之前,需要将棉花进行开松、除杂、除尘等处理,以确保纱线的质量和稳定性。
接下来是精梳纺的过程,这一步骤主要包括梳理、拉幅、精梳和牵伸等工序。
在梳理过程中,通过梳理机将棉花进行细分和剥离,去除短纤维和杂质,使纤维平行排列;而在拉幅和精梳过程中,通过拉伸和精梳机的作用,进一步提高纤维的纯度和平行度,使得纱线更加细长和均匀。
最后是精梳纺半制品名称,经过精梳纺的工艺处理,原料棉花被加工成了半成品纱线,常见的精梳纺半制品名称包括精梳棉纱、精梳纱等,这些半成品纱线可以进一步加工成成品纺织品,如衬衫、床上用品等。
通过以上的纺纱工艺流程,精梳环锭纺的生产过程能够保证纱线的质量和稳定性,为纺织品的生产提供了坚实的基础。
2.2 精梳纺前处理精梳纺前处理是精梳环锭纺纱工艺中非常重要的一部分,它主要包括纱线预处理和原料准备两个环节。
纱线预处理是指对原料进行检查、质量分级、控制纤维长度和漂白等工序,以确保纤维质量达到要求。
原料准备则是指对原料进行均匀混合、开松和精梳等处理,使纤维在进入纺纱机之前达到最佳状态。
在纱线预处理阶段,工人首先会对原料进行检查,检查原料是否存在破损、杂质等问题,确保其质量良好。
国内外环锭纺纱技术的发展与创新

1 环锭纺 纱技 术发展 与创新 的主 要标 志
品质 等方 面 比传 统环 锭 纺及其 他新 型纺 纱均 具有 明
显 优势 。 b )在环 锭细 纱 机 上 采 用 多 种 形 式 复 合 纺纱 技 术 , 环锭 纺纱线 不仅 呈 现原料 色泽 多元 化 , 使 而且 形 态 结构 多样 化 , 一 步 拓 宽 了环锭 纺 生 产 纱 线 的 应 进
e )围绕 在 环 锭 纺 纱 机 上 生 产 高 质 量 、 疵 纱 无 线 , 泛采 用 了优 质胶 辊 ( ) 罗拉 、 架 、 领 、 广 圈 、 摇 钢 钢 丝 圈等优 质 纺 纱 器 材 , 践 证 明 : 选 优 质 纺 纱 器 实 优 材 , 提高 纱线 稳定 性与 一致 性 的有 效 途径 。 是
环锭细纱术进步专题
= — = ===
2 1 年纪代 织校禾第 l 01 、 期
国 内外 环 锭 纺 纱 技 术 的发 展 与 创 新
陈根 才 章友 鹤 。
(. 1 浙江省新型纺织 品研发重点实验室 , 杭州 摘 3 0 0 ;. 10 9 2 浙江 省纺 织工程学会 , 杭州 30 0 ) 1 0 9
d )围绕提 高环锭 纺纱 机 的生 产效 率 , 一步 提 进
高 纺纱速 度 , 加快 了新 型 高 速锭 子 、 直 径 钢 领 、 小 低
纺纱 张力 新技 术 的采 用 与推 广 步 伐 , 国外 细纱 锭 在
速最 高已达 2 5 rmn在 国 内采 用新 型 高速锭 子 . 万 / i, 等措施后 , 环锭纺生产效 率有望提 高 1 ~2%。 5o O / 0
纺纱新技术发展现状及趋势

纺纱新技术发展现状及趋势摘要探讨纺纱新技术的发展现状及趋势。
分析了近年来环锭纺纱新技术和新型纺纱新技术的发展现状,综述了环锭纺、转杯纺和喷气涡流纺在纺纱方法、自动化智能化以及器材与专件等方面的进展,展望了纺纱新技术在全流程连续化、短流程、节能降耗、提高纺纱速度等方面的发展趋势,介绍了梳并联、细纱自动接头、超大牵伸、节能集聚纺、多级气圈、双分梳转杯纺和离心纺等新技术,并给出了对未来纺纱技术的预期。
认为:加强纺纱理论研究是纺纱新技术发展的基础,多学科特别是信息学科与纺纱结合将为纺织行业进步提供强大动力,螺旋式发展模式是纺纱新技术进步的特征。
关键词纺纱新技术;环锭纺;新型纺纱;智能化;短流程;节能纺纱活动伴随着人类文明的推进而发展。
回顾纺纱技术的发展历程,离不开开松、梳理、牵伸和加捻四大原理,目前纺纱技术也基本没有完全突破这些原理,只是在实现方式上有所区别或者在细节方面有所丰富。
从动力驱动和控制技术的角度来看,由于蒸汽机、电动机、变频技术和伺服电机等的应用,极大提高了纺纱效率和成纱质量的稳定性。
当前的纺纱产业界,环锭纺仍占主导地位,而转杯纺和喷气涡流纺也得到了迅速发展,成为新型纺纱中的主力军。
环锭纺的发展出现了集聚纺、低扭矩纺、全聚纺、聚纤纺、赛络纺和数码纺等,而新型纺纱技术中出现了静电纺、转杯纺、摩擦纺、喷气涡流纺、自捻纺和离心纺等新方法。
本文分别就环锭纺纱与新型纺纱两种体系来分析近年来纺纱新技术的进展,并展望未来的发展趋势。
1纺纱新技术的进展1.1环锭纺纱新技术的发展现状迄今为止,环锭纺依然是纺纱技术应用的主体,其优点和不足均非常明显。
环锭纺的优势体现在成纱结构合理、适纺号数范围广等方面,尤其是在特细号纱领域。
其缺点是工序长、纺纱速度受限、卷装尺寸受限、用工相对较多。
以下从3方面阐述环锭纺新技术的发展。
1.1.1环锭纺的改良技术近年来,集聚纺、低扭矩纺(假捻纺)、柔洁纺、复合纺和数码纺等技术的涌现和应用,使环锭纺纱技术得以进步与改良,成纱质量得到提高与改善。
环锭纺、气流纺、喷气纺、涡流纺、赛络纺、紧密纺简介

环锭纺、气流纺、喷气纺、涡流纺、赛络纺、紧密纺简介环锭纺环锭纺纱是现时市场上用量最多,最通用之纺纱方法,条子或粗纱经牵伸后的纤维条通过环锭钢丝圈旋转引入,筒管卷绕速度比钢丝圈快,棉纱被加捻制成细纱.广泛应用于各种短纤维的纺纱工程.如普梳,精梳及混纺,钢丝圈由筒管通过纱条带动绕钢领回转.进行加捻,同时,钢领的摩擦使其转速略小于筒管而得到卷绕.纺纱速度高,环锭纱的形态,为纤维大多呈内外转移的圆锥形螺旋线,使纤维在纱中内外缠绕联结,纱的结构紧密,强力高,适用于制线以及机织和针织等各种产品。
环锭纺(精梳)流程:清花间--梳棉--预并条--条并卷--精梳--头道并条--二道并条--粗纱--细纱--络筒环锭纺(普梳)流程:清花间--梳棉--头道并条--二道并条--粗纱--细纱--络筒气流纺气流纺不用锭子,主要靠分梳辊、纺杯、假捻装置等多个部件。
分梳辊用来抓取和分梳喂入的棉条纤维,同过他的高速回转所产生的离心力可把抓取的纤维甩出。
纺杯是个小小的金属杯子,他的旋转速度比分梳辊高出10倍以上,由此产生的离心作用,把杯子里的空气向外排;根据流体压强的原理,使棉纤维进入气流杯,并形成纤维流,沿着杯的内壁不断运动。
这时,杯子外有一根纱头,把杯子内壁的纤维引出来,并连接起来,再加上杯子带着纱尾高速旋转所产生的钻作用,就好像一边“喂”棉纤维,一边加纱线搓捏,使纱线与杯子内壁的纤维连接,在纱筒的旋绕拉力下进行牵伸,连续不断的输出纱线,完成气流纺纱的过程。
气流纺的特征气流纺纱有速度大、纱卷大、适应性广、机构简单和不用锭子、钢领、钢丝圈的优点,可成倍的提高细纱的产量。
气流纺与环锭纺的区别气流纺与环锭纺一个是新型纺织技术,一个是老式纺纱技术。
气流纺是气流纺纱,而环锭纺则是机械纺,就是由锭子和钢铃、钢丝圈进行加捻,由罗拉进行牵伸。
而气流纺则是由气流方式输送纤维,由一端握持加捻。
一般来说,环锭纱毛羽较少,强度较高,品质较好。
气流纺工序短,原料短绒较多,纱线毛,支数和拈度不能很高,价格也较低。
32支棉纱环锭纺工艺棉花和棉纱的配比
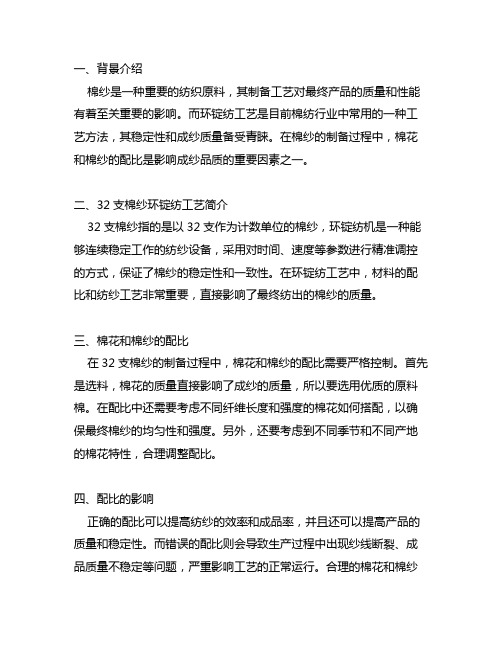
一、背景介绍棉纱是一种重要的纺织原料,其制备工艺对最终产品的质量和性能有着至关重要的影响。
而环锭纺工艺是目前棉纺行业中常用的一种工艺方法,其稳定性和成纱质量备受青睐。
在棉纱的制备过程中,棉花和棉纱的配比是影响成纱品质的重要因素之一。
二、32支棉纱环锭纺工艺简介32支棉纱指的是以32支作为计数单位的棉纱,环锭纺机是一种能够连续稳定工作的纺纱设备,采用对时间、速度等参数进行精准调控的方式,保证了棉纱的稳定性和一致性。
在环锭纺工艺中,材料的配比和纺纱工艺非常重要,直接影响了最终纺出的棉纱的质量。
三、棉花和棉纱的配比在32支棉纱的制备过程中,棉花和棉纱的配比需要严格控制。
首先是选料,棉花的质量直接影响了成纱的质量,所以要选用优质的原料棉。
在配比中还需要考虑不同纤维长度和强度的棉花如何搭配,以确保最终棉纱的均匀性和强度。
另外,还要考虑到不同季节和不同产地的棉花特性,合理调整配比。
四、配比的影响正确的配比可以提高纺纱的效率和成品率,并且还可以提高产品的质量和稳定性。
而错误的配比则会导致生产过程中出现纱线断裂、成品质量不稳定等问题,严重影响工艺的正常运行。
合理的棉花和棉纱配比是环锭纺工艺中不可或缺的一环。
五、优化配比方案为了达到最佳的成纱质量,不断优化棉花和棉纱的配比是非常重要的。
可以通过不断试验和实践,找出适合不同生产环境和不同原料棉的最佳配比方案。
还可以借助先进的数据分析和工艺控制技术,进行精准调控,确保棉纱成品的质量稳定和提高生产效率。
六、总结通过合理的棉花和棉纱配比,可以提高32支棉纱环锭纺工艺的稳定性和成纱质量,为纺织行业的发展和产品质量的提升做出重要的贡献。
深入研究和优化棉花和棉纱的配比方案,对于提高棉纺产业的竞争力和市场表现具有重要意义。
七、环锭纺工艺的优势环锭纺工艺作为目前棉纺行业中常用的一种工艺方法,具有许多优势。
环锭纺机能够实现高速稳定连续工作,保证了生产效率和成品率。
环锭纺机可以对纱线的细度和张力进行精准调控,保证了成纱的均匀性和稳定性。
环锭纺新型纱线开发及其应用述略

大,歪斜越明显 。采用 z捻和 s 捻交替织造是有效克服针织布歪斜的方法之一。生产无缝内衣要注意 z 捻、S 捻纱交织时,要求使用同批号、配棉一致的纱线,以防止出现 “ 黄白档” 。
l 花 式纱 - 3
目 前花式纱使用广、市场空间大、生产已成规模,而且品种繁多。如竹节纱、包芯纱、雪尼尔纱、 大肚纱 、波纹纱 、点子纱 、圈 圈纱 、羽毛纱 、带 子纱 、牙 刷纱 、灯 笼纱 、蜈蚣 纱等 。其 中多数 是在环锭
第 4期第 1 6页
浙江纺织服装职业技术学院学报
21年 1 01 2月
环 锭纺新型纱线开 发及其应用述略
章友鹤
摘
要:环锭纺纱通过不断的工艺技术改进 与创新 ,生产 出了品种 多样、用途各异的新 型纱线 .文章较为具体地介
绍了几种新型纱线及其用途,并且对在环锭 纺机上 色纺纱与半精 纺新型纱线的生产与应 用情 况作 了分析 。
粗 纱可 以用 不同成份纤维 或不 同颜 色纤维 ,使纺成纱 成为混纺 纱或混色 纱 ,在 针织物或机织物 中使用 可 产 生混纺与混色 效。
1 . 竹 节纱 _1 3
竹节纱是利用 纱线 的粗 节纱疵 开发 的一 种新型花 式纱线 。 目前生产 量较 多,使用面 也较 广 。在 短短
的1 0年时间里,竹节纱生产技术迅速提高:由最初的机械间隙传动、步进 电机传动 ,发展到目前采用
P C控制 的伺服 电机传 动 , 生产 工艺 日臻 完善 。 因竹节纱 具有粗细分布 不均匀 的外观 , 以织物花型突 出、 所 风格 别致 、立体感强 ,尤其在 牛仔系列产 品 中大行其 道 。在 针织产 品用竹节 纱有着若 隐若现 的特色 ,深 受年 轻消 费者 的喜爱 。
富有弹 性 ,这 种面料 穿着 舒适 ,用途广泛 ,可 用于夏 季衬 衣 、裙 、睡衣裤 、头 巾、面 纱和绣 花 的底布 、 窗帘等 。 1 反 手纱 ( 捻 )与顺 手纱 ( . 2 S Z捻 ) 纱 线的捻 向对 于织物 的外观和手 感有很大 的影响 。利 用经 、纬纱捻 向不 同和织物 组织 的配 合 ,可 以
- 1、下载文档前请自行甄别文档内容的完整性,平台不提供额外的编辑、内容补充、找答案等附加服务。
- 2、"仅部分预览"的文档,不可在线预览部分如存在完整性等问题,可反馈申请退款(可完整预览的文档不适用该条件!)。
- 3、如文档侵犯您的权益,请联系客服反馈,我们会尽快为您处理(人工客服工作时间:9:00-18:30)。
环锭纺梳理技术的发展与应用王庆球黄锡畴(纺织工业新型纺纱技术开发中心)“梳得好,纺得好”。
梳理技术是棉纺工程中最重要的基本工艺之一,已为国内外纺织界人士共识。
最近20年来,国内外有较大的发展,梳棉是纺织厂的“心脏”。
国内外在高产梳棉机的发展中更有辉煌成就,现叙述国内外高产梳棉机的发展情况。
1 高产梳棉机的发展1978年开始,我国引进国外先进纺织设备,梳棉以瑞士立达(Rieter)公司的C1/3型,德国特吕茨施勒尔公司(Trutzchler)的DK2型,日本丰田(TOYOTA)CK—7C型和CKW型双联梳棉机,英国泼拉脱(Platt)公司600型和克罗斯罗尔(Crosrol)公司MK3/80型双联梳棉机等。
对我国的纺织工业和梳棉机的生产、制造、发展起到很大推动作用。
青纺机械厂在消化吸收了引进设备的基础上,设计制造了FA201型新梳棉机,引进设备对老厂梳棉机改造也起到了很大的促进作用。
20年来国际上高产梳棉机发展很快,瑞士立达公司由C1/3型发展到C4、C10、C50直到目前的C51型,单产达到100kg/台时;德国的特吕茨施勒尔公司由DK2型发展到DK3(DK715)、DK740、DK760、DK803型和最近改进生产的DK903型,采用了多项电子、自动化技术,单产达到较高水平;英国的克罗斯罗尔MK系列梳棉机由MK3型发展到MK4、MK5型和MK5C型,单产号称也超过100kg/台时;英国泼拉脱600型发展到2000型;意大利马佐里(Marzoli)公司由C40、C41发展到C300、CX300和CX400型,产量也有很大提高。
国内青纺机械厂由FA201发展到FA203和FA231型,产量达到80kg/台时;国内不少纺机制造厂已经或正在仿制新型号的高产梳棉机。
归纳起来最新型号的高产梳棉机普遍采用了以下几项主要梳理技术措施。
1.1 采用新型金属针布,有利于梳棉机高速度、强分梳,从而提高梳理效能,这是梳棉机高产的灵魂。
新型金属针布向矮、浅、尖、密、薄、小(工作角)的特点发展,充分发挥其优良的纺纱性能,制造质量上强调“五度”——即锋利度、平整度、光洁度、耐磨度、淬火均匀度,以保证出厂质量。
钢材的选用和热处理技术已是当前提高针布梳理效能和寿命的主要手段。
新型盖板针布要与锡林针布相区配。
增加盖板针布的抗弯性和加固底布,缩短梳针高度、采用异型钢丝,加大钢丝直径和截面尺寸,增厚底布,改变植针排列和减小横向针距减小工作角等。
针布型号和标注方法已向国外靠拢,新型针布的制造和采用已日趋成熟和扩大。
1.2 刺辊给棉采用顺向喂入,给棉板装在给棉罗拉上方,使棉层纤维顺向喂入刺辊,杂质易于分离,喂入棉层的内外层纤维持点至分梳点的长度差异减小,减少纤维损伤。
立达C4型采用后,德国特吕茨施勒尔DK803型也相继采用,这是一个重大的改革。
1.3 提高刺辊、锡林速度,以提高梳棉机的梳理度。
增加刺辊沟槽数和锯齿密度以及采用不同梳针和锯齿的多刺辊又开始得到重视。
如DK803、DK903采用了三刺辊,第一刺辊为针辊,速度为900r/min左右,可以较柔和地开松纤维,减少短绒产生;第二、三刺辊为锯齿辊,速度逐个递增,第二个为1200余r/min,第三刺辊为1700r/min,达到较好的开松进入锡林盖板区间。
近年来锡林速度提高到450~600r/min,刺辊速度提高到1000~1300r/min,刺辊是握持分梳,速度宜采用“高中求低”以减少纤维损伤。
1.4 刺辊下采用锯齿分梳板,已有20多年历史,瑞士立达C1/3型采用后,淘汰了原来的刺辊漏底工艺,立达型以除尘刀与分梳板结合的二组为主,德国特吕茨勒尔以分梳板前加挡板一组结合吸风系统,英国泼拉脱2000型以一块弧形分梳板,刺辊下以除尘刀、分梳板和除尘刀三者组合的工艺。
刺辊下采用分梳板,弥补了喂入棉层底部受梳较弱的缺陷,使进入锡林至盖板分梳区的棉束小而少,减轻了锡林盖板的分梳负荷,淘汰了网眼漏底,避免了小炉底网眼糊塞和经常的清刷工作。
国产FA201系列梳棉机也仿效瑞士立达型梳棉机的二组分梳板。
1.5 回转盖板反转、减小踵趾差为0.56mm,盖板工作面有小平面、盖板用齿形带替代传统链条,工作区盖板有向减少的方向发展。
盖板反向回转,有利于提高锡林盖板间的梳理和除杂作用,盖板正转时工作区头上几块盖板很快被纤维充塞,行至中前区时盖板是在充塞情况下超负荷工作,分梳除杂作用就较差。
盖板反转后,头上几块盖板充塞较多时即行转出,其余中前区盖板负荷均比正转时小,这对分梳除杂作用极为有利,转移给道夫上的纤维梳理度和清洁度较好,棉结、杂质减少。
根据国内一些厂的试验,效果是好的。
缩小盖板踵趾差为0.56(0.022″),盖板工作踵部有小平面(约3mm)国内外新机上已普遍采用。
锡林~盖板间的梳理质量与隔距大小有密切关系,减少踵趾差和增加小平面,实际上缩小了它们间的平均梳理隔距,对分梳、除杂都很有利。
盖板采用齿形带代替传统链条,可减少链条伸长和简化操作。
另外,工作区盖板有减少趋向,DK803型回转盖板为80~84根,工作区为28根左右;克罗斯罗尔MK5回转盖板为89根,工作区28根(其中还牵涉到锡林直径大小的因素);马佐里CX400型回转盖板59根,工作区20根;国产FA203型回转盖板86根,工作区32根;盖板减少可以让出锡林表面,以增装前后固定盖板,这是一个发展方向。
1.6 锡林前后固定盖板的普遍采用,并得到发展。
80年代初,国内外少数机型采用固定盖板,有的是前固定,有的是后固定,不久发展为前后固定盖板都采用,而且逐步增加,并增加除杂系统。
如立达C1/3型开始后罩板处仅装一块宽70mm左右的弧形锯齿分梳板,以后C4采用前后各4块固定盖板,又发展到各6块中间留一空档,增加除尘刀,并备有吸风,以利短绒、尘杂的排除称为“Trex”装置,MK5型纺棉采用4块固定盖板,其中安插圆角除尘刀和控制板,前后相同,布置进风和排风口;纺化纤时后固定为9根,前固定为3根无吸风。
德国DK型从DK715开始采用固定盖板,先是后固定4根,以后发展到前后都装,采用了“KR”吸尘系统。
马佐里CX400型前固定为9根,后固定为14根,因而大大地缩小了工作区盖板;泼拉脱2000型前后固定采用前分梳TM2000和后分梳DS1000的弧形整块锯齿板组成,并分别装有吸尘系统。
1.7 剥棉机构,国内外三罗拉、四罗拉的都有,在提高产量的情况下,都增加了导棉装置,以保护轻定量和出条速度的提高。
式样有多种:有喇叭型导棉扁管、有皮圈集束、导轮集束等,对减少棉网飘逸断头有利。
剥棉罗拉上方都有高速清洁辊,以防止绕花损坏道夫针布。
泼拉脱2000型为刻槽的单罗拉剥棉,罗拉上方配有清洁装置,效果也很好。
1.8 吸尘、吸落棉系统。
国内外高产梳棉机吸尘吸落棉系统日臻完善,风量风压合理,吸点多,管道光洁,盖板花、大漏低落棉都采用吸风,保证了质量和车间环境整洁。
吸风的关键是风量、风压和电耗。
我国吸风过去强调电耗,而忽视吸风效果。
吸尘吸落棉应着眼于管道设计和风量,才能确保高产梳棉机正常生产。
工艺吸点要保证纤维转移,纤维不受损伤和少产生棉结,一般均采用连续常吸。
非工艺性吸点(保护劳动条件和环境)以掌握风量为主,可以采用间歇吸。
风管、风道力求光滑无毛刺,网眼板等加工力求采用新技术,以代替落后的加工方法。
1.9 清梳联和自调均整,国外高产梳棉机基本上都已采用。
德DK803把清梳联喂棉箱部分作为梳棉机的机后部分与梳棉机做成一体。
国内清梳联几年来也有很大进步。
随着清梳联的推广,自调匀整也就相应的在梳棉机上得以采用,使生条重量不匀率得到有效控制。
1.10 圈条器国内外普通式和行星式圈条器都有,自动换筒和无自动换筒并存。
棉条筒采用Φ600~Φ1000mm不等,也有横向移动的增容装置。
为降低机台造价,有的厂不赞成行星式圈条器。
立达公司认为棉条筒Φ600,有自动换筒占地比较经济。
1.11 自停机构更新换代,新机上自停机构比较先进。
一种属工艺性自停:棉层过厚过薄、刺辊速度过低、棉条过粗过细自停等。
另一种防护性自停:喂棉误入杂物、棉条断头、剥棉返花、满筒定长、尘箱充塞、罩壳开启……等等,对针布确保安全防轧和提高出条质量是一项不可缺少的内容。
1.12 机电仪一体化水平普遍得到重视。
变频调速和微机控制已属常规装备,在工艺、设备、运转管理上普遍采用数显技术,并积极发展在线检测和控制,如对清梳生产线的控制,梳棉机生产参数如速度、号数、重不匀、控制片段的不匀率、疵点故障班产量等并都可在荧屏上显示,随意调出参数,对掌握生产、质量起很大作用。
2 老厂梳棉机的维护和技术改造近年来随着我国国民经济的调整,棉纺织厂压锭任务很重,纺织工业面临改革重组调整的处境,1999年开始已走上扭亏转盈积极向上趋势。
加强技术工作,特别是梳棉机维护和技术改造工作必须引起足够重视,对提高成纱质量,增加品种以利出口是十分必要的。
当前梳理新技术逐步在老厂梳棉机改进方面应逐步得到推广和使用。
2.1 清棉要保证对原料的开松度,充分发挥抓包机的作用使棉块尽量减小至100mg以下。
梳针代替角钉,锯齿代替打刀,清棉梳理化达到充分松解、除杂为梳棉机梳理工作做好前期充分准备。
2.2 恢复和发展纺织厂过去行之有效的严格管理,做好梳棉基础工作,特别是“四锐一正”,抓好磨盖板机、刺辊包磨机和长短磨辊的检修工作,使锡林、道夫、刺辊、盖板的平整度和锐度达到理相要求,保证基础工作的落实贯彻,特别是当前新老工人交替之际,更应引起广泛的重视,只有勤勤恳恳、扎扎实实、从上到下安下心来做好各自的本职工作,根据我国的实际情况,设备管理还应认真贯彻以预防为主保全保养并举的传统。
大小修理的计划周期根据机械实际情况适当修改执行。
密切注意三主轴精度,确保“四锐一正”的基础,以保证紧隔距强分梳的要求。
2.3 选好用好金属针布和盖板针布。
我国的金属针布制造已向国际靠拢,新型针布大量生产和大量推广,已有一个较好的起点,但针布用钢材和制造质量与国外还有差距,我们一定要在材料、热处理、耐磨性上提高一步,在目前总量已超过国内需要的情况下,可以走向国外力争出口。
国内老厂根据不同原料、不同纺纱品种、不同锡林速度,不同梳棉单产要求选择金属针布和盖板针布,达到最佳匹配效果,要用好梳棉机上各自停装置,防止针布轧坏,国内不少厂的道夫针布大多是轧坏的,用好自停可以延长针布使用寿命。
2.4 缩小盖板踵趾差和工作面踵部磨出小平面应大力推广,国内外新机都采用了,老机盖板铁骨大平面胶覆钢纸磨砺钢纸或树脂胶修正平面改变踵趾差已有先例,对减少棉结很有利。
解决盖板踵趾差要改变磨盖板机上踵趾板的踵趾差同步进行。
盖板反转是一个方向,但老机改造有一定难度,关键是盖板传动部位调整和盖板花的剥取和吸风配置以盖板花的收集分类回用处理等尚待试验研究和落实,同时盖板链条的伸长和中托脚的调节等要一并解决,建议由机械厂协同配合进行,过去纺织厂独立进行改造的办法,不但改造时间长费用大,效果也不一定好。