自硬砂树脂砂工艺问答
酸自硬呋喃树脂砂的工艺要点及缺陷防止

表 4 国产常用磺酸 固化 剂技术 指标
型 号\ /・ 一 ge m
1 原材 料 的选择
般依据铸件 的大小和材质以及成本来选择不
同含氮量的呋喃自硬树脂 , 参见表 2和表 3 。此外 ,
对其粘度 、 游离甲醛含量、 H值等技 术指标也应提 P
出严格要求 。综合考虑 , 一般灰铸铁件和球铁件用 呋喃树脂的含氮量应控制在表 2 所示范围内。目前
自硬砂对原材料 的品质极为敏感 , 铸件质量必 须从原材料抓起。
O3 .
5O . 3O .
1 3 固化 剂和 硅烷 .
4 。对甲苯磺酸的缺点是在温度控制条件较差 的情 况下 , 冬季使用 时固化往往很缓慢. 故某些树脂厂在 冬季用固化剂 中或为降低成本有时可能会采用硫酸 乙脂。这是冬季树脂砂球铁件废品率上升的一个原
因。
游离酸
固化剂对型砂的重要性并不次于树脂。一般都 选用对甲苯磺酸水或醇溶液作 固化剂。通常用 固化 剂的总酸度来衡量其涪 l大小 , 生 固化剂的含量越多 , 其活性越大。国产常用磺酸固化剂 的技术指标见表
1 2 酸硬 化 呋喃 自硬 树 脂( 醛呋 喃树 脂 ) . 尿
一
量不高 、 砂铁 比较小的情 况。但 由于原辅材料性能 不稳定 , 旧砂再生工艺完整性差 , 使用者对 自硬砂的 特点和关键技术认识不足 , 加上疏于工艺控制 和管 理, 所以能实现正 常化生产 的尚不多。 以下简述该 工艺生产铸铁件的若干要点及缺陷防止 。
≥10 .
球铁 、 一般铸钢
D 低氮 ) (
> . ~ . O 3 2O
混合料中加入粘结剂的质量分数为 1 %时所具有的抗 拉强 度 , 它是衡 量树脂粘 结效 率高低的指标 。
树脂自硬砂烘干工艺
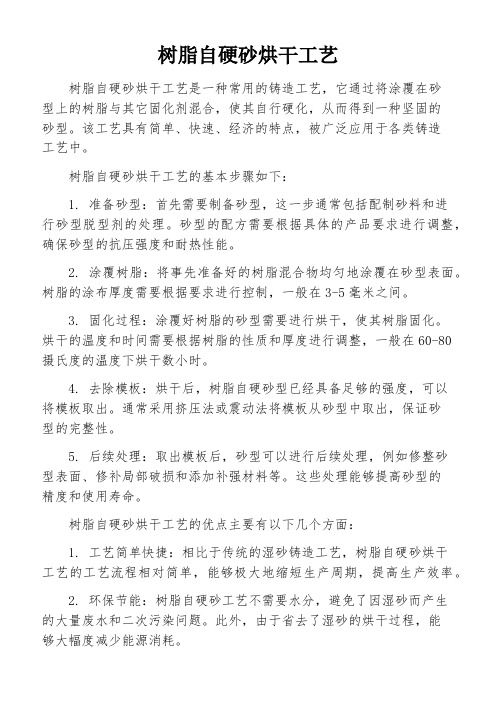
树脂自硬砂烘干工艺树脂自硬砂烘干工艺是一种常用的铸造工艺,它通过将涂覆在砂型上的树脂与其它固化剂混合,使其自行硬化,从而得到一种坚固的砂型。
该工艺具有简单、快速、经济的特点,被广泛应用于各类铸造工艺中。
树脂自硬砂烘干工艺的基本步骤如下:1. 准备砂型:首先需要制备砂型,这一步通常包括配制砂料和进行砂型脱型剂的处理。
砂型的配方需要根据具体的产品要求进行调整,确保砂型的抗压强度和耐热性能。
2. 涂覆树脂:将事先准备好的树脂混合物均匀地涂覆在砂型表面。
树脂的涂布厚度需要根据要求进行控制,一般在3-5毫米之间。
3. 固化过程:涂覆好树脂的砂型需要进行烘干,使其树脂固化。
烘干的温度和时间需要根据树脂的性质和厚度进行调整,一般在60-80摄氏度的温度下烘干数小时。
4. 去除模板:烘干后,树脂自硬砂型已经具备足够的强度,可以将模板取出。
通常采用挤压法或震动法将模板从砂型中取出,保证砂型的完整性。
5. 后续处理:取出模板后,砂型可以进行后续处理,例如修整砂型表面、修补局部破损和添加补强材料等。
这些处理能够提高砂型的精度和使用寿命。
树脂自硬砂烘干工艺的优点主要有以下几个方面:1. 工艺简单快捷:相比于传统的湿砂铸造工艺,树脂自硬砂烘干工艺的工艺流程相对简单,能够极大地缩短生产周期,提高生产效率。
2. 环保节能:树脂自硬砂工艺不需要水分,避免了因湿砂而产生的大量废水和二次污染问题。
此外,由于省去了湿砂的烘干过程,能够大幅度减少能源消耗。
3. 砂型精度高:树脂自硬砂具有优异的粘结力和抗压强度,能够确保砂型的精度和表面质量。
这对于一些对尺寸精度要求较高的铸件来说是非常重要的。
4. 重复使用性强:由于树脂自硬砂的固化剂能够在烘干过程中实现自行硬化,砂型可以反复使用。
这对于批量生产相同零件的铸造工艺来说可以大大降低生产成本。
总之,树脂自硬砂烘干工艺是一种简单、快捷、经济并且环保的铸造工艺。
它能够满足各类铸造产品对精度和表面质量的要求,提高铸造产品的质量和生产效率,是现代工业中广泛采用的一种重要工艺。
树脂砂工艺
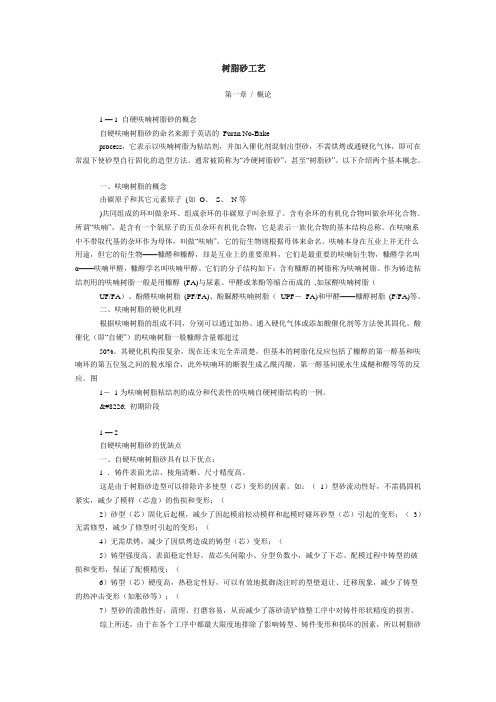
树脂砂工艺第一章/ 概论1 — 1 自硬呋喃树脂砂的概念自硬呋喃树脂砂的命名来源于英语的Furan No-Bakeprocess,它表示以呋喃树脂为粘结剂,并加入催化剂混制出型砂,不需烘烤或通硬化气体,即可在常温下使砂型自行固化的造型方法。
通常被简称为“冷硬树脂砂”,甚至“树脂砂”。
以下介绍两个基本概念。
一、呋喃树脂的概念由碳原子和其它元素原子(如O、S、N等)共同组成的环叫做杂环、组成杂环的非碳原子叫杂原子。
含有杂环的有机化合物叫做杂环化合物。
所谓“呋喃”,是含有一个氧原子的五员杂环有机化合物,它是表示一族化合物的基本结构总称。
在呋喃系中不带取代基的杂环作为母体,叫做“呋喃”,它的衍生物则根据母体来命名。
呋喃本身在互业上并无什么用途,但它的衍生物——糠醛和糠醇,却是互业上的重要原料,它们是最重要的呋喃衍生物,糠醛学名叫α——呋喃甲醛,糠醇学名叫呋喃甲醇。
它们的分子结构如下:含有糠醇的树脂称为呋喃树脂。
作为铸造粘结剂用的呋喃树脂一般是用糠醇(FA)与尿素、甲醛或苯酚等缩合而成的,如尿醛呋喃树脂(UF/FA)、酚醛呋喃树脂(PF/FA)、酚脲醛呋喃树脂(UPF-FA)和甲醛——糠醇树脂(F/FA)等。
二、呋喃树脂的硬化机理根据呋喃树脂的组成不同,分别可以通过加热、通入硬化气体或添加酸催化剂等方法使其固化。
酸催化(即“自硬”)的呋喃树脂一般糠醇含量都超过50%。
其硬化机构很复杂,现在还未完全弄清楚,但基本的树脂化反应包括了糠醇的第一醇基和呋喃环的第五位氢之间的脱水缩合,此外呋喃环的断裂生成乙酰丙酸,第一醇基间脱水生成醚和醛等等的反应。
图1-1为呋喃树脂粘结剂的成分和代表性的呋喃自硬树脂结构的一例。
• 初期阶段1 — 2自硬呋喃树脂砂的优缺点一、自硬呋喃树脂砂具有以下优点:1 .铸件表面光洁、棱角清晰、尺寸精度高。
这是由于树脂砂造型可以排除许多使型(芯)变形的因素。
如:(1)型砂流动性好,不需捣固机紧实,减少了模样(芯盒)的伤损和变形;(2)砂型(芯)固化后起模,减少了因起模前松动模样和起模时碰坏砂型(芯)引起的变形;(3)无需修型,减少了修型时引起的变形;(4)无需烘烤,减少了因烘烤造成的铸型(芯)变形;(5)铸型强度高、表面稳定性好,故芯头间隙小、分型负数小,减少了下芯、配模过程中铸型的破损和变形,保证了配模精度;(6)铸型(芯)硬度高,热稳定性好,可以有效地抵御浇注时的型壁退让、迁移现象,减少了铸型的热冲击变形(如胀砂等);(7)型砂的溃散性好,清理、打磨容易,从而减少了落砂清铲修整工序中对铸件形状精度的损害。
有关树脂自硬砂的几个问题

有关树脂自硬砂的几个问题中国铸造协会李传栻目前,我国铸造行业中树脂自硬砂工艺应用很广,中、大型铸件基本上都用树脂自硬砂生产,中、小型铸件采用者也很多。
为了进一步提高铸件质量,保持产品质量稳定、一致,有必要对树脂自硬砂生产工艺的各个环节有进一步的了解,并在生产中予以认真的控制。
中国铸造协会之所以要组织这样的会议,目的就在如此。
本文将从生产现场的工艺要求出发,以保证产品质量和降低生产成本为中心,就树脂自硬砂的粘结特点、对原砂的要求、造型制芯工艺的控制要点等方面提出粗浅的看法,供大家分析、议论。
一、树脂自硬砂的粘结特点砂粒越细,其比表面积(单位质量砂粒的表面面积)越大。
假如砂粒是均匀的球体,则比表面积与其平均直径成反比。
也就是说:筛分时停留在100号筛上的球体,其表面面积是停留在70号筛上、相同质量的球体的2倍;是停留在50号筛上、相同质量的球体的2倍。
砂粒虽然不是均匀的球体,但大致可以用这一规律作定性的评估。
集中于70/140筛的原砂,砂粒表面的总面积大约是集中于50/100号筛的等量原砂的2倍,是集中于40/70号筛的等量原砂的2倍。
如果加入的树脂量相同,70/140号筛砂粒表面粘结膜的厚度,大约是40/70号筛砂粒的1/2。
在这种情况下,砂粒之间粘结桥的尺寸当然就会相应地减小,这是使型砂强度降低的因素。
另一方面,改用较细的砂粒后,相同容积内砂粒的数量增加。
虽然粘结桥的尺寸减小,但粘结桥的数量大为增加。
这又是使型砂强度提高的因素。
原砂粒度对树脂自硬砂强度的影响,是这两种因素综合作用的结果。
为了进一步探明原砂粒度对型砂强度的影响,笔者在实验室用单筛砂进行过一系列的对比试验,试验结果的要点如下:分别用停留在40、50和70号筛上的三种单筛砂进行对比试验时,在加入质量分数相同的树脂的条件下,三种粒度不同的型砂的抗拉强度基本上相同。
也就是说,对于粒度中等的原砂(40号筛~70号筛),由粗砂改为细砂,粘结桥尺寸减小所导致的强度下降,可以由粘结桥数量增加而得到补偿,粒度在此范围内改变对型砂的强度基本上没有影响;分别用停留在20、30和40号筛上的三种单筛砂进行对比试验时,在加入质量分数相同的树脂条件下,原砂粒度较细的型砂抗拉强度较高。
树脂自硬砂烘干工艺
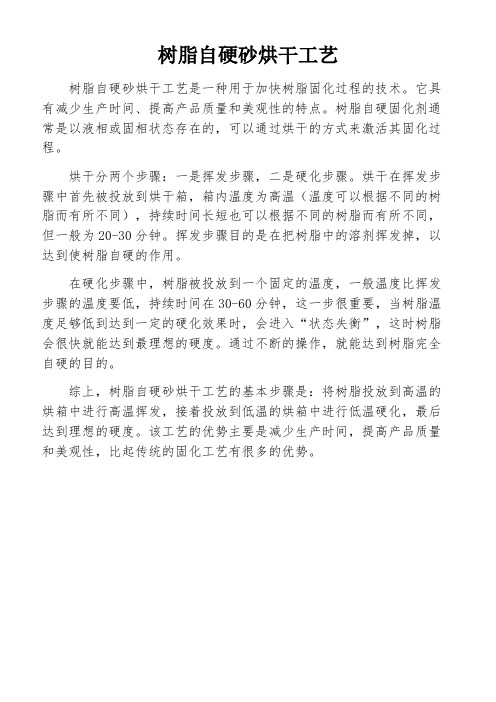
树脂自硬砂烘干工艺
树脂自硬砂烘干工艺是一种用于加快树脂固化过程的技术。
它具有减少生产时间、提高产品质量和美观性的特点。
树脂自硬固化剂通常是以液相或固相状态存在的,可以通过烘干的方式来激活其固化过程。
烘干分两个步骤:一是挥发步骤,二是硬化步骤。
烘干在挥发步骤中首先被投放到烘干箱,箱内温度为高温(温度可以根据不同的树脂而有所不同),持续时间长短也可以根据不同的树脂而有所不同,但一般为20-30分钟。
挥发步骤目的是在把树脂中的溶剂挥发掉,以达到使树脂自硬的作用。
在硬化步骤中,树脂被投放到一个固定的温度,一般温度比挥发步骤的温度要低,持续时间在30-60分钟,这一步很重要,当树脂温度足够低到达到一定的硬化效果时,会进入“状态失衡”,这时树脂会很快就能达到最理想的硬度。
通过不断的操作,就能达到树脂完全自硬的目的。
综上,树脂自硬砂烘干工艺的基本步骤是:将树脂投放到高温的烘箱中进行高温挥发,接着投放到低温的烘箱中进行低温硬化,最后达到理想的硬度。
该工艺的优势主要是减少生产时间,提高产品质量和美观性,比起传统的固化工艺有很多的优势。
树脂自硬砂烘干工艺
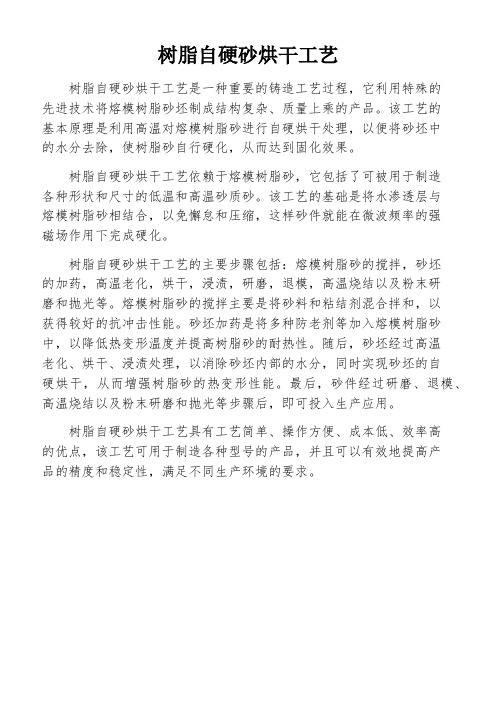
树脂自硬砂烘干工艺
树脂自硬砂烘干工艺是一种重要的铸造工艺过程,它利用特殊的
先进技术将熔模树脂砂坯制成结构复杂、质量上乘的产品。
该工艺的
基本原理是利用高温对熔模树脂砂进行自硬烘干处理,以便将砂坯中
的水分去除,使树脂砂自行硬化,从而达到固化效果。
树脂自硬砂烘干工艺依赖于熔模树脂砂,它包括了可被用于制造
各种形状和尺寸的低温和高温砂质砂。
该工艺的基础是将水渗透层与
熔模树脂砂相结合,以免懈怠和压缩,这样砂件就能在微波频率的强
磁场作用下完成硬化。
树脂自硬砂烘干工艺的主要步骤包括:熔模树脂砂的搅拌,砂坯
的加药,高温老化,烘干,浸渍,研磨,退模,高温烧结以及粉末研
磨和抛光等。
熔模树脂砂的搅拌主要是将砂料和粘结剂混合拌和,以
获得较好的抗冲击性能。
砂坯加药是将多种防老剂等加入熔模树脂砂中,以降低热变形温度并提高树脂砂的耐热性。
随后,砂坯经过高温
老化、烘干、浸渍处理,以消除砂坯内部的水分,同时实现砂坯的自
硬烘干,从而增强树脂砂的热变形性能。
最后,砂件经过研磨、退模、高温烧结以及粉末研磨和抛光等步骤后,即可投入生产应用。
树脂自硬砂烘干工艺具有工艺简单、操作方便、成本低、效率高
的优点,该工艺可用于制造各种型号的产品,并且可以有效地提高产
品的精度和稳定性,满足不同生产环境的要求。
树脂自硬砂工艺设计

树脂自硬砂工艺设计引言:树脂自硬砂是一种常用于金属铸造的砂型材料,其优点包括高精度、高稳定性和良好的表面质量。
在树脂自硬砂工艺设计中,主要考虑材料的选择、模具设计和工艺参数调整等方面。
本文将详细介绍树脂自硬砂工艺设计的相关内容。
一、材料的选择1.酚醛树脂:酚醛树脂具有良好的流动性和耐高温性能,适用于制造复杂形状的铸件。
但由于其收缩率较大,容易导致铸件尺寸不稳定。
2.酚醛砂:酚醛砂是酚醛树脂与石英砂按一定比例混合而成的砂型材料,具有较好的热稳定性和耐磨性。
但由于其粘度较高,需要使用较大的压力来填充砂型。
3.环氧树脂:环氧树脂具有优异的机械性能、耐腐蚀性和耐高温性能,适用于制造耐磨、耐腐蚀的铸件。
但由于环氧树脂的固化时间较长,需要较长的工艺周期。
根据具体的铸造要求和制造工艺的特点,选择合适的树脂自硬砂材料。
二、模具设计模具设计是树脂自硬砂工艺设计的关键环节。
正确的模具设计可以确保砂型的精度和稳定性。
1.模具结构:选择合适的模具结构,包括上、下模板和型腔,以及冷却系统。
模具结构应考虑砂型的填充性能和铸件的脱模要求。
2.模具材料:模具材料应具有良好的耐用性和热稳定性,以保证模具的寿命和工艺稳定性。
常用的模具材料包括铸铁、钢和铝合金等。
3.冷却系统:冷却系统的设计可以有效控制模具温度,以提高铸件的尺寸精度和表面质量。
冷却系统应考虑水道的布置和尺寸。
三、工艺参数调整工艺参数调整是树脂自硬砂工艺设计的核心任务,包括树脂与硬化剂的配比、充填压力和固化时间等。
1.树脂与硬化剂的配比:树脂与硬化剂的配比直接影响到树脂的流动性和固化时间。
配比不当会导致砂型填充不充分或固化不完全,从而影响铸件的精度和质量。
2.充填压力:充填压力影响树脂与砂型之间的接触和渗透性。
充填压力过大会破坏砂型,造成铸件表面粗糙;充填压力过小则会导致砂型填充不完全。
3.固化时间:固化时间是树脂自硬砂固化的关键参数,影响铸件的凝固和收缩过程。
固化时间应根据具体的铸件形状和尺寸进行调整,以确保铸件的质量。
自硬砂树脂砂工艺问答

自硬砂树脂砂工艺问答1.为什么磷酸多用作高氮呋喃自硬树脂的固化剂,而很少用作低氮呋喃自硬树脂的固化剂?这是因为低氮高糠醇树脂,采用酸做固化剂时,硬化速度慢,脱模时间长,且强度很低。
高氮低糠醇树脂使用磷酸做固化剂可获得必要的硬化速度。
而且,高氮低糠醇树脂采用磷酸作催化剂可获得很好的终强度。
造成这种结果的原因主要是由于磷酸与糠醇的互溶性差,而与水的亲和力大,使得树脂和催化剂中所含的水分以及树脂在缩聚反应中生成的水不易扩散排出而以磷酸为核心生成水滴残存于树脂膜中,破坏了树脂膜的致密性,故强度较低。
而高氮树脂与水的互溶性好,各种水分不易以磷酸为核心集中为水滴,树脂膜结构好,强度高。
2.为什么酚脲脘自硬树脂的硬透性比呋喃自硬树脂砂好?因为酚脲脘树脂的固化过程是聚合反应,固化过程中不产生小分子的水,不存在因型内外水分的挥发速度不同使其内外固化速度不一致的问题,而呋喃自硬树脂的固化过程是缩聚反应,反应过程中产生水分,因型芯内外的水分蒸发速度不同,导致了其内外固化速度不同,故其硬透性差些。
这也是呋喃自硬树脂砂的固化速度受空气相对湿度影响较大的原因。
3.为什么生产铸铝,铸铜件可以选用高氮呋喃树脂?由于铝、铜金属液对氮几乎不溶解,因此,即使使用高氮树脂在浇注过程中树脂分解产生的氮,也不会被铝、铜金属液吸收,也就不会在凝固过程中因析出氮而形成氮气孔。
因此,生产铸铝、铸铜件可以为潢足溃散性的需要而选用高氮树脂。
4.为什么自硬树脂砂生产重量大的铸件,浇注系统宜于用陶瓷管制作?采用自硬树脂砂造型,当生产重量较大的铸件时,由于浇注时间长,浇注系统在高温金属液的长时间热作用下,易使树脂砂过早溃散丧失强度,造成冲砂缺陷,因此,对重量较大的铸件,浇注系统宜用陶管制作,同时使浇注系统特别是直浇道不易上涂料的问题得到解决。
5.采用自硬树脂砂造型、制芯时,如何确定树脂砂的可使用时间是否满足要求?当采用间歇式混砂机时,树脂砂的可使用时间要大于树脂砂从混好卸砂到用完的这段时间;当采用连续式混砂机造型、制芯时,树脂砂的可使用时间要大于从混砂机的出砂口起始放砂位置到又回到该位置连续放砂的这段时间。
- 1、下载文档前请自行甄别文档内容的完整性,平台不提供额外的编辑、内容补充、找答案等附加服务。
- 2、"仅部分预览"的文档,不可在线预览部分如存在完整性等问题,可反馈申请退款(可完整预览的文档不适用该条件!)。
- 3、如文档侵犯您的权益,请联系客服反馈,我们会尽快为您处理(人工客服工作时间:9:00-18:30)。
自硬砂树脂砂工艺问答---摘自网上供学习
济南圣泉1.为什么磷酸多用作高氮呋喃自硬树脂的固化剂,而很少用作低氮呋喃自硬树脂的固化剂?这是因为低氮高糠醇树脂,采用酸做固化剂时,硬化速度慢,脱模时间长,且强度很低。
高氮低糠醇树脂使用磷酸做固化剂可获得必要的硬化速度。
而且,高氮低糠醇树脂采用磷酸作催化剂可获得很好的终强度。
造成这种结果的原因主要是由于磷酸与糠醇的互溶性差,而与水的亲和力大,使得树脂和催化剂中所含的水分以及树脂在缩聚反应中生成的水不易扩散排出而以磷酸为核心生成水滴残存于树脂膜中,破坏了树脂膜的致密性,故强度较低。
而高氮树脂与水的互溶性好,各种水分不易以磷酸为核心集中为水滴,树脂膜结构好,强度高。
2.为什么酚脲脘自硬树脂的硬透性比呋喃自硬树脂砂好?因为酚脲脘树脂的固化过程是聚合反应,固化过程中不产生小分子的水,不存在因型内外水分的挥发速度不同使其内外固化速度不一致的问题,而呋喃自硬树脂的固化过程是缩聚反应,反应过程中产生水分,因型芯内外的水分蒸发速度不同,导致了其内外固化速度不同,故其硬透性差些。
这也是呋喃自硬树脂砂的固化速度受空气相对湿度影响较大的原因。
3.为什么生产铸铝,铸铜件可以选用高氮呋喃树脂?由于铝、铜金属液对氮几乎不溶解,因此,即使使用高氮树脂在浇注过程中树脂分解产生的氮,也不会被铝、铜金属液吸收,也就不会在凝固过程中因析出氮而形成氮气孔。
因此,生产铸铝、铸铜件可以为潢足溃散性的需要而选用高氮树脂。
4.为什么自硬树脂砂生产重量大的铸件,浇注系统宜于用陶瓷管制作?采用自硬树脂砂造型,当生产重量较大的铸件时,由于浇注时间长,浇注系统在高温金属液的长时间热作用下,易使树脂砂过早溃散丧失强度,造成冲砂缺陷,因此,对重量较大的铸件,浇注系统宜用陶管制作,同时使浇注系统特别是直浇道不易上涂料的问题得到解决。
5.采用自硬树脂砂造型、制芯时,如何确定树脂砂的可使用时间是否满足要求?当采用间歇式混砂机时,树脂砂的可使用时间要大于树脂砂从混好卸砂到用完的这段时间;当采用连续式混砂机造型、制芯时,树脂砂的可使用时间要大于从混砂机的出砂口起始放砂位置到又回到该位置连续放砂的这段时间。
6.自硬树脂砂用模样的拨模斜度为什么要比粘土砂大些?树脂砂型芯在起模时已具有一定的硬化强度,无退让性,一般不能通过敲击模样和芯盒框使砂型或砂芯壁来达到松动模样,起模时摩擦力较大;树脂砂型与砂芯的可修补性差,起模时,砂型,芯一旦不完整,较难修补。
7.树脂砂工艺生产铸铁为什么宜少设被缩冒口,多设出气冒口?树脂砂型刚度好,浇注初期砂型强度高,这就有条件利用铸铁凝固过程的石墨化膨胀,有效地消除缩孔、缩松缺陷,实现灰铸铁、球墨铸铁件的少冒口、无冒口铸造。
但树脂砂的发气量在,为了便于浇注过程中型腔中的大量气体能顺利排出,必须多设出气冒口,原则上要求∑F冒>∑F内。
8.为什么含糠醇70%-80%的呋喃自硬树脂的常温终强度最大?从理论上讲,呋喃树脂中的脲醛树脂比例越高,其常温终强度越大,因此当糠醇含量大于70%~80%时,糠醇含量越高,即含氮量越低,常温终强度越低。
但随着脲醛树脂的增加,呋喃树脂的含水量相对增高,又会降低硬化速度和终强度。
当糠醇含量低于70%~80%时,树脂终强度的下降趋势超过了上升趋势。
因而一般情况下,糠醇含70%~80%时,呋喃自硬树脂砂的常温终强度最大。
9.为什么采用催化活性过强固化剂和过多的固化剂加入量。
会导致树脂砂的终强度下降?采用催化活性过强的固化剂或过多的固化剂,会导致预固化阶段过短,树脂中无规则卷曲线团状预聚物尚未充分伸展和有序化,就被已经交联的预聚物阻塞在体形结构中,使线团中的大量活性基未能参与反应,不能形成聚合度很大的聚合物。
所以尽管树脂砂硬化较快,初强度较高,却必然导致终强度的明显降低。
10.为什么自硬树脂砂的旧砂需要再生回用时,不宜用磷酸做固化剂?用磷酸做固化剂的砂型、芯在浇注后,磷酸不能在金属液的热作用下分解破坏,而生成磷酸盐沉积在砂粒表面,较难通过再生去除,导致再生砂配制的树脂砂的强度下降很多,并且增加铸型膨胀,使夹砂倾向增加。
11.为什么酸硬化的甲阶酚醛树脂自硬砂宜选用游离酸含量低,总酸高的有机酸做固化剂,不通用无机酸做固化剂?由于酸硬化的甲阶酚醛树脂中含水量高,因此发生交联反应时,除树脂本身缩聚产生水外,还将释放数量很多的水,这些水将起稀释硬化剂的作用,使反应很慢。
增加硬化剂的游离酸含量,才会使硬化速度变快,但会使自硬砂的强度下降很多,因此要保证硬化速度,又不使树脂砂的强度下降较大,只能增加固化剂的总酸值。
由于无机酸的游离酸一般都较高,所以对于酸硬化的甲阶酚醛树脂,宜选用总酸度高,游离酸含量低的有机酸做固化剂。
12.为什么酸固化甲阶酚醛树脂砂的固化剂
加入量宜以占树脂的百分数表示?这是由于酸固化甲阶酚醛树脂是由苯酸和甲醛在碱性催化剂作用下缩合而成的,出厂前用酸将碱性催化剂中和并使其成弱酸性。
因此树脂对酸性硬化剂不如呋喃树脂那样敏感,在酸浓度相当高时才发生交联反应。
另外,此种树脂的含水量很高,一般都在某些方面15%左右或更高。
发生交联反应时,除树脂本身综合产生水分外,还要释放很多原与树脂互溶的水。
这些水将硬化剂稀释,自硬砂中树脂加入量越多,此种稀释作用就越强,因而要保持同样的固化速度,不得不增加硬化剂的加入量。
所以对于甲阶酚醛树脂自硬砂,硬化剂的加入量以占树脂的百分数计算为宜,也就是对酸硬化的甲阶酚醛树脂砂固化剂的加入量要随树脂加入量的增加而增加。
13.为什么刚起模的型芯及刚修补过的地方不宜立刻上涂料?因为刚起模及刚修补过的型、芯中的树脂硬化反应还处于初期阶段,若遇到水基涂料中的水分(溶剂)会影响硬化的正常进行(对于酚脲烷自硬树脂,则未反应的二组分聚异氰酸酯可与水分反应而失效);如使用醇基涂料,施涂料后后需立刻点燃,也会使未反应的树脂过烧。
这些都会影响型、芯的表面稳定性。
14.为什么碱性酚醛树脂砂的旧砂再生较困难?由于碱性酚醛树脂的碱性很高(基PH值通常为11-13),树脂中含有较多的碱(一般为氢氧化钾),浇注时,树脂中的碱易与硅砂作用生成低熔点的硅酸盐,熔融的硅酸盐牢固的粘附在砂粒上,不易去除,造成较难去除,造成旧砂再生较为困难。
15.选择树脂的类型时,应考虑铸件的哪些因素?选择树脂的类型时,应考虑铸件的以下因素:(1)铸件的材质。
铸件(铸钢件、高合金铸铁件)的材质产生氮气孔的倾向大时,宜选择低氮或无氮树脂;当铸件(球墨铸铁件、灰铸铁件)的材质为产生氮气孔的倾向小的黑色金属时,可选择中氮树脂;对氮不溶解的铜、铝件要选择高氮树脂。
(2)铸件的重、壁厚、及浇注温度。
当铸件的重较大,壁较厚,浇注温度较高时,应选择糠醇含量高、脲醛含量低的树脂,使型芯的高温强度满足需要;浇注温度低、重量轻,薄壁的铸件,需要的高温强度低,可以选择脲醛含量高些的树脂,以降低成本。
(3)铸件的结构。
铸件易出现热裂,宜先用高温度低的树脂作粘结剂。
对易出现热裂的铸钢件,宜选项用碱性酚醛树脂,不宜选用呋喃无氮树脂为粘结剂;铸件易出现冷裂,宜选用溃散性好的做粘结剂。
共三组,1为苯基醚酚醛树脂,2为聚异氰酸脂,两者加入量是砂量的1.4~1.6%。
3为催化剂(为芳香族胺,加入量为1组的1~5%)。
除了催化剂种类和加入方法与三乙胺略有不同外,前两组份都一样。