旋转弯曲疲劳试验机
旋转弯曲疲劳试验机的工作原理
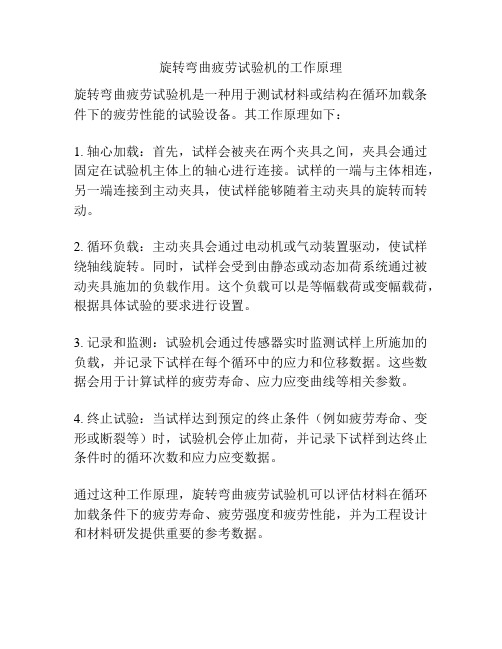
旋转弯曲疲劳试验机的工作原理
旋转弯曲疲劳试验机是一种用于测试材料或结构在循环加载条件下的疲劳性能的试验设备。
其工作原理如下:
1. 轴心加载:首先,试样会被夹在两个夹具之间,夹具会通过固定在试验机主体上的轴心进行连接。
试样的一端与主体相连,另一端连接到主动夹具,使试样能够随着主动夹具的旋转而转动。
2. 循环负载:主动夹具会通过电动机或气动装置驱动,使试样绕轴线旋转。
同时,试样会受到由静态或动态加荷系统通过被动夹具施加的负载作用。
这个负载可以是等幅载荷或变幅载荷,根据具体试验的要求进行设置。
3. 记录和监测:试验机会通过传感器实时监测试样上所施加的负载,并记录下试样在每个循环中的应力和位移数据。
这些数据会用于计算试样的疲劳寿命、应力应变曲线等相关参数。
4. 终止试验:当试样达到预定的终止条件(例如疲劳寿命、变形或断裂等)时,试验机会停止加荷,并记录下试样到达终止条件时的循环次数和应力应变数据。
通过这种工作原理,旋转弯曲疲劳试验机可以评估材料在循环加载条件下的疲劳寿命、疲劳强度和疲劳性能,并为工程设计和材料研发提供重要的参考数据。
旋转纯弯曲疲劳试验机检定方法
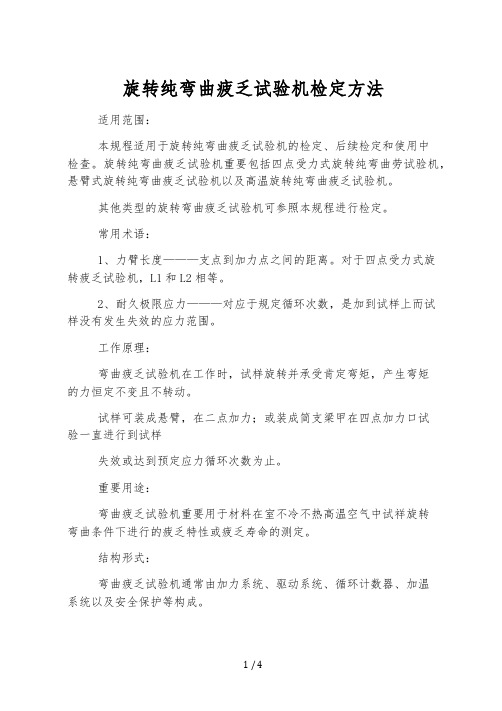
旋转纯弯曲疲乏试验机检定方法适用范围:本规程适用于旋转纯弯曲疲乏试验机的检定、后续检定和使用中检查。
旋转纯弯曲疲乏试验机重要包括四点受力式旋转纯弯曲劳试验机,悬臂式旋转纯弯曲疲乏试验机以及高温旋转纯弯曲疲乏试验机。
其他类型的旋转弯曲疲乏试验机可参照本规程进行检定。
常用术语:1、力臂长度———支点到加力点之间的距离。
对于四点受力式旋转疲乏试验机,L1和L2相等。
2、耐久极限应力———对应于规定循环次数,是加到试样上而试样没有发生失效的应力范围。
工作原理:弯曲疲乏试验机在工作时,试样旋转并承受肯定弯矩,产生弯矩的力恒定不变且不转动。
试样可装成悬臂,在二点加力;或装成简支梁甲在四点加力口试验一直进行到试样失效或达到预定应力循环次数为止。
重要用途:弯曲疲乏试验机重要用于材料在室不冷不热高温空气中试祥旋转弯曲条件下进行的疲乏特性或疲乏寿命的测定。
结构形式:弯曲疲乏试验机通常由加力系统、驱动系统、循环计数器、加温系统以及安全保护等构成。
计量性能要求:1、加力系统A、左,右夹头土轴同轴度弯曲疲乏试验机夹紧试样时,左、右夹头主轴同轴度为0.02mm。
B、左、右夹头高度差弯曲疲乏试验机夹紧试样时,左、右夹头的高度差不应超过0.1mm。
C、主轴箱动态径向跳动量弯曲疲乏试验机夹紧试样(不加祛码)运转时。
土轴箱施力部位的动态径向跳动量不超过0.06mm。
D、力加载机构①力臂弯曲疲乏试验机力臂长度的扣对误差不超过0.3%。
②初始弯矩弯曲疲乏试验机的初始弯矩应尽可能小,初始弯矩不应大于疲乏试验机zui大弯矩的}10%。
③弯矩重复性和对误差弯曲疲乏试验机从zui大弯矩的10%开始,至疲乏试验机zui大弯矩,其弯矩示值相对误差不大于1%。
④弯矩示值相对误差弯曲疲乏试验机从zui大弯炬的10%开始,至疲乏试验机zui大弯矩,其弯矩示值相对误差的zui大允许值为1%。
⑤左、右弯矩相对误差左右两边施加弯矩的疲乏试验机,其左、右弯矩应相等,左、右弯矩相对误差不应超过单边弯矩标称值的1%。
摩托车车轮旋转弯曲疲劳试验

摩托车车轮旋转弯曲疲劳试验
摩托车车轮旋转弯曲疲劳试验是一种模拟摩托车在行驶过程中车轮承受反复弯曲应力的试验。
该试验通常使用专用的摩托车车轮旋转弯曲疲劳试验机进行。
在试验中,车轮将被固定在试验机的旋转装置上,并承受模拟摩托车行驶过程中的反复弯曲应力。
通过这种方式,可以测试车轮的耐久性和可靠性,以及其在反复弯曲应力下的疲劳寿命。
这种试验对于评估摩托车车轮的质量和安全性非常重要,特别是在设计、生产或材料改进过程中。
通过这种试验,可以检测出车轮可能存在的弱点和缺陷,并及时采取措施进行改进和优化,以确保摩托车车轮在各种行驶条件下都能保持安全和可靠。
具体而言,在进行摩托车车轮旋转弯曲疲劳试验时,需要注意以下几点:
1. 选择适当的试验参数:如弯曲应力、转速、温度等,这些参数需要根据车轮的实际情况和试验要求进行选择。
2. 确保试验机的精度和稳定性:试验机需要具有高精度和稳定性,以确保测试结果的准确性和可靠性。
3. 测试过程中需要注意安全:由于摩托车车轮旋转弯曲疲劳试验涉及到高强度的机械运动和应力,因此需要采取必要的安全措施,如佩戴防护眼镜、手套等。
4. 测试结果的分析和处理:试验结束后,需要对测试结果进行分析和处理,以评估车轮的性能和质量。
根据测试结果,可以对车轮的设
计、材料或工艺进行改进和优化。
总之,摩托车车轮旋转弯曲疲劳试验是一种重要的测试方法,用于评估摩托车车轮的耐久性和可靠性。
通过这种试验,可以确保摩托车车轮的安全性和可靠性,为消费者的安全提供保障。
金属疲劳试验
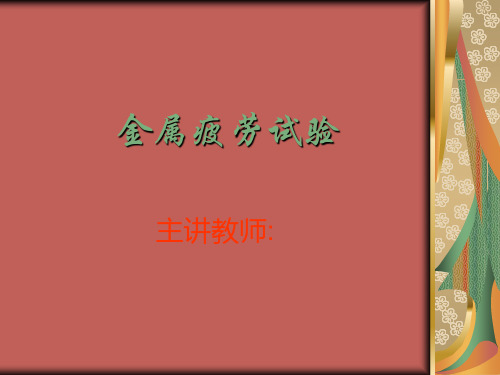
金属疲劳试验主讲教师:一、实验目的1. 了解疲劳试验的基本原理。
2. 掌握疲劳极限、S-N曲线的测试方法。
二、实验原理1.疲劳抗力指标的意义目前评定金属材料疲劳性能的基本方法就是通过试验测定其S-N曲线(疲劳曲线),即建立最大应力σmax 或应力振幅σα与其相应的断裂循环周次N之间的关系曲线。
不同金属材料的S-N曲线形状是不同的,大致可以分为两类,如图1所示。
其中一类曲线从某应力水平以下开始出现明显的水平部分,如图1(a)所示。
这表明当所加交变应力降低到这个水平数值时,试样可承受无限次应力循环而不断裂。
这表明当所加交变应力降低到这个水平数值时,试样可承受无限次应力循环而不断裂。
因此将水平部分所对应的应力称之为金属的疲劳极限,用符号σR 表示(R为最小应力与最大应力之比,称为应力比)。
若试验在对称循环应力(即R=-1)下进行,则其疲劳极限以σ-1表示。
中低强度结构钢、铸铁等材料的S-N曲线属于这一类。
对这一类材料在测试其疲劳极限时,不可能做到无限次应力循环,而试验表明,这类材料在交变应力作用下,如果应力循环达到107周次不断裂,则表明它可承受无限次应力循环也不会断裂,所以对这类材料常用107周次作为测定疲劳极限的基数。
另一类疲劳曲线没有水平部分,其特点是随应力降低,循环周次N不断增大,但不存在无限寿命。
如图1(b)所示。
在这种情况下,常根据实际需要定出一定循环周次(108或5×107…)下所对应的应力作为金属材料的“条件疲劳极限”,用符号σR(N)表示。
2.S-N 曲线的测定(1) 条件疲劳极限的测定测试条件疲劳极限采用升降法,试件取13根以上。
每级应力增量取预计疲劳极限的5%以内。
第一根试件的试验应力水平略高于预计疲劳极限。
根据上根试件的试验结果,是失效还是通过(即达到循环基数不破坏)来决定下根试件应力增量是减还是增,失效则减,通过则增。
直到全部试件做完。
第一次出现相反结果(失效和通过,或通过和失效)以前的试验数据,如在以后试验数据波动范围之外,则予以舍弃;否则,作为有效数据,连同其他数据加以利用,按下列公式计算疲劳极限:()11n R N i i i v m σσ==∑ 1式中m——有效试验总次数;n—应力水平级数;—第i级应力水平;—第i级应力水平下的试验次数。
扭转疲劳试验机标准

扭转疲劳试验机标准疲劳是指某种活动和条件下的物理精疲力竭的情况,它是大多数行业的常见问题,因此开发疲劳试验机变得尤为重要。
扭转疲劳试验机是一种专门用于研究和测试材料、结构和机械零件扭转疲劳强度的实验设备。
疲劳试验机的常规标准包括机器结构,加载装置,控制电路,扭腾学测试,运行参数的设定,信号控制,数据记录和安全管理等。
1.器结构:扭转疲劳试验机的机器结构应采用简单,牢固,实用,人性化设计,使操作、维护和检查更加方便快捷。
2.载机制:扭转疲劳试验机应采用多节加载机制,能够进行不同类型的试验,实现载荷的自动控制,自动调整载荷曲线,以满足不同材料、结构和机械零件扭转疲劳性能检测需求。
3.制电路:扭转疲劳试验机使用电路控制装置,可精确调节载荷,让设备更精确地完成测试,提高测试质量。
4.转测试:通过支撑杆,旋转滑动支撑点,进行扭转,实现测试加载,获取材料、结构和机械零件的扭转疲劳性能参数。
5.行参数设定:扭转疲劳试验机可以设定多种不同的运行参数,如测试时间,扭转角度,温度,湿度等,以满足不同材料和测试需求。
6. 信号控制:扭转疲劳试验机采用运动控制系统,可以自动控制和监控实验过程,满足实验要求。
7.据记录:扭转疲劳试验机应具备记录试验过程中的相关数据功能,如扭转次数,变形量,断裂次数,等。
8.全管理:扭转疲劳试验机要实现安全管理,二次回路安全继电器等设备应由专业安装公司安装,以确保安全性。
以上是关于扭转疲劳试验机标准的概述,试验机的设计,加载机制,控制电路,扭转测试,运行参数设定,信号控制,数据记录和安全管理等,都可以根据实验室的具体要求和场景进行调整,使试验结果更准确。
除此之外,还要注意扭转疲劳试验机的安全性。
疲劳试验应在安全的环境中进行,以防出现安全事故;在实验过程中,应保持合理的温度和湿度,防止因不适当的条件影响实验结果;在使用过程中,应注意安全管理,确保实验室安全。
扭转疲劳试验机的使用可以更加有效地检测和研究材料和结构疲劳性能,准确测试材料抗疲劳特性,发现隐藏在材料中的来源,以及了解材料的破坏特性,从而更好地推进材料及机械零件的开发。
试验六疲劳试验示范
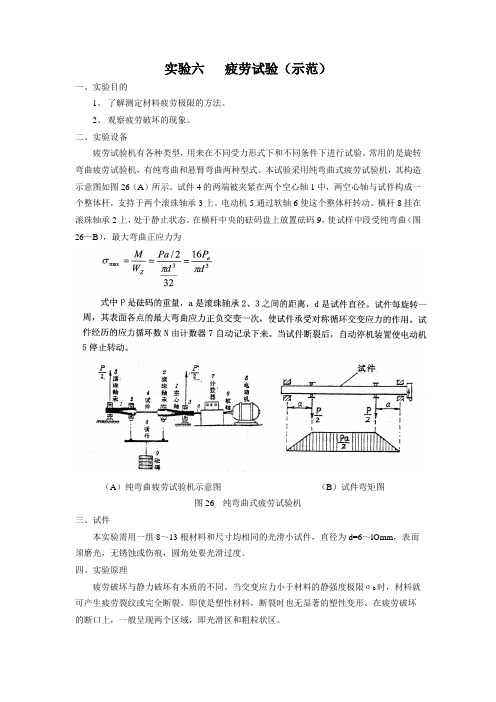
实验六疲劳试验(示范)一、实验目的1、了解测定材料疲劳极限的方法。
2、观察疲劳破坏的现象。
二、实验设备疲劳试验机有各种类型,用来在不同受力形式下和不同条件下进行试验。
常用的是旋转弯曲疲劳试验机,有纯弯曲和悬臂弯曲两种型式。
本试验采用纯弯曲式疲劳试验机,其构造示意图如图26(A)所示。
试件4的两端被夹紧在两个空心轴1中,两空心轴与试件构成一个整体杆,支持于两个滚珠轴承3上。
电动机5通过软轴6使这个整体杆转动。
横杆8挂在滚珠轴承2上,处于静止状态。
在横杆中央的砝码盘上放置砝码9,使试样中段受纯弯曲(图26—B),最大弯曲正应力为(A)纯弯曲疲劳试验机示意图(B)试件弯矩图图26 纯弯曲式疲劳试验机三、试件本实验需用一组8~13根材料和尺寸均相同的光滑小试件,直径为d=6~lOmm,表而须磨光,无锈蚀或伤痕,圆角处要光滑过度。
四、实验原理疲劳破坏与静力破坏有本质的不同。
当交变应力小于材料的静强度极限σb时,材料就可产生疲劳裂纹或完全断裂。
即使是塑性材料,断裂时也无显著的塑性变形。
在疲劳破坏的断口上,一般呈现两个区域,即光滑区和粗粒状区。
材料断裂前所经历的循环次数称为疲劳寿命N,试件所受应力愈小,则疲劳寿命愈长。
对钢和铸铁等黑色金属,如果在某一交变应力下经受107次循环仍不破坏,则实际上可以承受无限次循环而不会发生破坏。
所以,对这些金属以试件能承107循环所对应的最大应力σ值作为疲劳极限σ-1。
maX五、实验步骤1、试件准备取8~13根试件,检查试件表面加工质量,如有锈蚀或擦伤,用细砂纸或砂布沿试件轴向抛光加以消除。
测量试件的直径。
2、装夹试件安装试件时必须很仔细,避免灰尘和杂质进入空心轴的锥孔中。
将试件牢固夹紧,使试件与试验机的转轴保持良好的同心度。
试件安装好后用手慢慢旋转试验机的转轴,用百分表在试件上测得的径向跳动量应不大于0.03mm。
然后空载运转,试件的径向跳动量应不大于0.06mm。
3、进行试验第一根试件的交变应力的最大值约取材料强度极限的60%,即σlmax=0.6而砝码重量P1二0.6σbπd3/16a。
金属材料疲劳试验旋转弯曲方法

金属材料疲劳试验旋转弯曲方法金属材料疲劳试验旋转弯曲方法是一种常用的疲劳试验方法,旨在评估金属材料在不同应力水平下的疲劳寿命和破坏机理。
本文将介绍旋转弯曲试验的原理、实验装置、实验步骤和一些应注意的问题。
旋转弯曲试验的原理是通过在金属试样上施加交变弯曲载荷,使其产生疲劳破坏。
与拉伸、压缩等加载方式相比,弯曲加载更接近实际工作条件下的应力状态,因此旋转弯曲试验更加符合实际应用。
通过控制试样的几何尺寸和加载条件,可以得到金属材料在一定应力水平下的疲劳寿命和疲劳曲线。
实验装置的主要组成部分包括试样夹持装置、负载装置和数据采集系统。
试样夹持装置通常采用夹具或夹具+滚动装置的方式,以确保试样在加载过程中不产生滑动。
负载装置通过电机驱动试样产生旋转弯曲载荷,可利用电机的控制系统调节载荷大小和频率。
数据采集系统用来记录试验过程中的试样应变和载荷变化,以便后续分析。
旋转弯曲试验的实验步骤如下:1.准备试样:根据实验要求,根据标准规范或自定义设计制作试样。
试样的几何形状和尺寸要符合实验要求,通常为长条形或圆柱形。
2.安装试样:将试样固定在试样夹持装置中,并确保试样的几何形状和尺寸不会发生变形或损坏。
3.设置实验参数:根据实验目的和要求,设置加载频率、载荷幅值和载荷比等参数,可以在实验中逐步增加载荷或设置不同的载荷比,以得到不同应力水平下的疲劳寿命和曲线。
4.开始实验:启动负载装置,使试样产生旋转弯曲载荷。
在实验过程中,连续记录试样的应变和载荷变化,并查看试样的破坏情况。
5.终止实验:当试样出现破坏或达到预设的实验次数时,停止负载装置,结束实验。
记录试样的破坏形态和位置,以便进一步分析。
在进行旋转弯曲试验时,还需要注意以下几个问题:1.试样的几何尺寸和材料特性应符合实验要求,避免试样在实验加载过程中出现松动、变形或损坏的情况。
2.实验过程中要及时记录试样的应变和载荷变化,以便后续分析。
可以使用应变计、力传感器等装置进行实时监测和数据采集。
旋转弯曲疲劳试验机检定规程
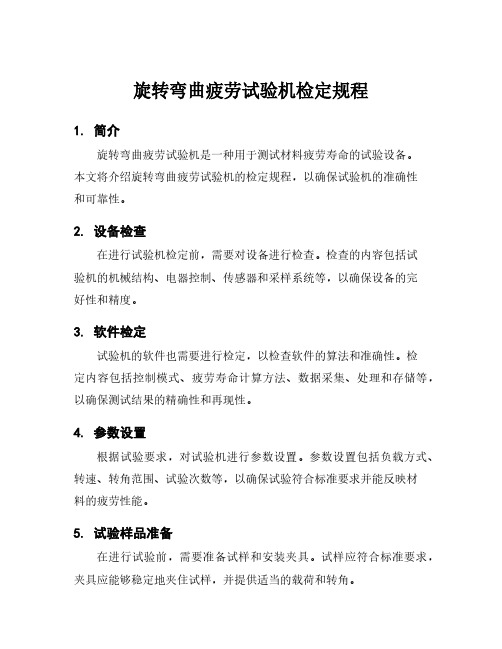
旋转弯曲疲劳试验机检定规程1. 简介旋转弯曲疲劳试验机是一种用于测试材料疲劳寿命的试验设备。
本文将介绍旋转弯曲疲劳试验机的检定规程,以确保试验机的准确性和可靠性。
2. 设备检查在进行试验机检定前,需要对设备进行检查。
检查的内容包括试验机的机械结构、电器控制、传感器和采样系统等,以确保设备的完好性和精度。
3. 软件检定试验机的软件也需要进行检定,以检查软件的算法和准确性。
检定内容包括控制模式、疲劳寿命计算方法、数据采集、处理和存储等,以确保测试结果的精确性和再现性。
4. 参数设置根据试验要求,对试验机进行参数设置。
参数设置包括负载方式、转速、转角范围、试验次数等,以确保试验符合标准要求并能反映材料的疲劳性能。
5. 试验样品准备在进行试验前,需要准备试样和安装夹具。
试样应符合标准要求,夹具应能够稳定地夹住试样,并提供适当的载荷和转角。
6. 试验操作进行试验操作前,需要将试样放置到夹具上,并按照试验要求设置试验参数。
试验过程中需要定期检查试验机的状态和数据采集系统,以确保试验的完整性和精确性。
7. 数据处理与分析试验结束后,需要对数据进行处理和分析。
数据处理包括数据采集、去噪处理、数据对齐和数据导出等。
数据分析包括疲劳寿命计算、曲线拟合和统计分析等。
8. 结论和建议根据试验结果,得出结论和建议。
结论应从疲劳寿命、疲劳裂纹形态、断口形态、机械性能变化等方面进行说明。
建议应包括试样制备、试验参数设置、试验过程操作和设备维护等方面的建议。
9. 检定报告最后,需要编制检定报告,记录试验过程、试验数据和试验结果等内容。
检定报告的内容应详尽、准确,以便后续的维护、更新和改进。
- 1、下载文档前请自行甄别文档内容的完整性,平台不提供额外的编辑、内容补充、找答案等附加服务。
- 2、"仅部分预览"的文档,不可在线预览部分如存在完整性等问题,可反馈申请退款(可完整预览的文档不适用该条件!)。
- 3、如文档侵犯您的权益,请联系客服反馈,我们会尽快为您处理(人工客服工作时间:9:00-18:30)。
一、旋转弯曲疲劳试验机简介:
馥勒FLPLX系列旋转弯曲疲劳试验机主要用于对金属及合金材料在室温条件下进行反复交变弯曲应力作用下的弯曲疲劳试验,测定金属圆形横截面试样在旋转状态下承受弯曲力矩时的疲劳性能。
满足GB/T4337-2008《金属材料疲劳试验旋转弯曲方法》、ISO 1143:2010《metallic materials-Rotating bar bending fatigue testing》、、BS EN 13261:2009《Railway applications-Wheelsets and bogies-Axles-Product requirements》等试验标准方法。
二、疲劳试验机主要技术规格:
1、旋转速度:1000r/min~5000r/min
2、转速波动度:≤±0.5%FS
3、加力点径向跳动量:跳动量≤0.05mm
4、加载方式:组合砝码加载载荷350N
5、加载砝码系列质量:350N,精度≤+/-1%
6、弯曲应力800-900MPa,弯矩相对误差≤±1%
7、疲劳次数显示:≥100000000
8、试样装夹方式:高速精密弹性夹具
9、试样夹持端形式:圆形;试样夹持端直径范围Φ10mm-Φ20mm
10、适用试样直径规格Φ6mm、Φ7.5mm、Φ9.5mm
11、配置高速主轴箱,高精度进口轴承,具有完善的润滑及冷却装置,适用于在承受旋转弯矩条件下长期高速驱动试样旋转
12、安全防护:系统具有断电、驱动马达及主轴箱过热、试验次数到达设定值、试样断裂等停机或报警保护功能
13、系统检验:设备出厂前对系统进行检验、操作和标定
14、安装调试及培训:服务工程师在用户现场进行安装和功能调试并对用户提供培训。