数控机床几何误差与热误差综合建模
五轴数控机床综合误差建模分析
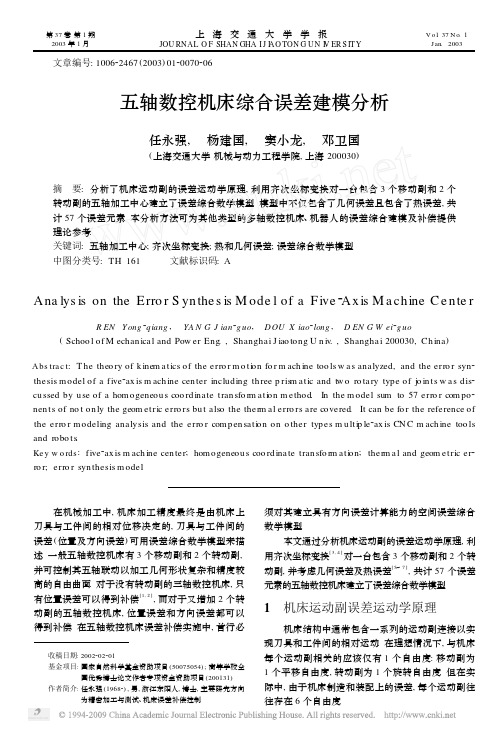
F ig. 5 F ive2ax is m ach in ing cen ter
2. 1 基坐标系的选择及坐标系统的设定
与工作台摆转的轴线重合, 并设在初始状态, 其 x
根据基坐标系方向的选择分析, 设定基坐标系 轴与基坐标系的 x 轴平行, y 轴与 x、z 轴构成笛卡
W 的第 1 轴与 X ′轴拖板移动副的参考轴平行; 设定 儿坐标系. 坐标系 C 的零点位于 O 2, O 2 为工作台面
第 1 期
任永强, 等: 五轴数控机床综合误差建模分析
71
1. 1 移动副误差运动学原理 如图 1 所示, 拖板沿着坐标系U 的 x 轴方向运
动时有 3 个平移运动误差分量, 即名义运动方向的 线 性 位 移 误 差 ∆x (x ) 及 y、z 方 向 的 直 线 度 误 差 ∆y (x )、∆z (x ) ; 还有 3 个转角运动误差分量, 即滚转 误差 Εx (x )、俯仰误差 Εy (x ) 和偏摆误差 Εz (x ). 其中, 下标 x , y , z 表示误差运动方向. 实际中, 因直线度 误差难以直接定义和测量, 通常用误差曲线的线性 拟合及其残差组合来描述, 拟合后的直线度误差参 考轴 (文中称为移动副参考轴) 在 xy 及 y z 坐标平面 的投影与 x 轴分别成一小角度 Ηzx 和 Ηyx , 如图 2 所 示. 其中, 下标 z、y 为直线度误差参考轴投影的旋转 运动方向, x 为拖板的名义运动方向, 并且将残差定 义为直线度误差∆y (x )、∆z (x ).
72
上 海 交 通 大 学 学 报
第 37 卷
差运动学原理分析可得 Ηxy = Ηzx = 0. (2) 选择基坐标系的第 2 轴 y 轴, 使其位于沿 y
数控机床几何误差与热误差综合建模及其实时补偿_王维

(a) y 轴丝杆螺母
(b) y 轴丝杆座
1
1.1
机床误差数据的采集
定位误差测量 采用激光干涉仪对立式加工中心的移动轴进 行定位误差的检测,如图 1 所示。为了减少检测过 程中的随机误差,每个轴的正方向、反方向分别重 复检测 3 次,取测量平均值作为测量结果[3]。 本文以机床的 y 轴定位误差的测量、建模和补 偿为例进行说明。y 轴行程范围为 400 mm,测量起
图 3 各定位误差测量时的温度变化
2
误差建模
图5 基准误差曲线拟合
这里以 y 轴正向的建模过程为例。图 4 为 y 轴 在冷态,温度升高 10~120 min 共 7 次测得的 7 条 定位误差曲线。由图 4 可见在不同温度状态下测得 的定位误差有很大的变化。这就是为何一般补偿的 效果不好的原因[6],即不能按一条定位误差曲线进 行补偿,而应该对于不同的温度,根据不同的定位 误差曲线进行补偿。
0 ——y 轴机床坐标零点
几何误差部分用多项式进行拟合。热误差部分 与机床上的某些热关键点温度有关,其与各条误差 曲线的拟合直线斜率相关[7]。 2.1 几何误差建模 将图 4 中的 7 条误差曲线均旋转到水平,即令 一次拟合曲线斜率为 0,然后求这 7 条误差曲线的 平均值,从而可得基准误差曲线,如图 5 所示。
(School of Mechanical Engineering, Shanghai Jiaotong University, Shanghai 200240)
Abstract:In order to improve the machine accuracy, a synthesis modelling method of geometric and thermal error is presented. Machine error distribution law is obtained through the analysis of machine error data at varying temperatures. Based on the different characteristics of geometric error and thermal error, error separation is carried out. Synthesis mathematical model for geometric and thermal error is proposed by using polynomial fitting and linear fitting. Online real-time error compensation is implemented by applying the computer numerical control(CNC) external machine coordinate system shift function and a novel developed synthesis error real-time compensation system. This error compensation method concerns the geometric error and its variations at different temperatures, thus a comprehensive analysis is made on the error and its regularity in the overall temperature rise to the heat steady-state. The inspection certificates that the maximum positioning error in normal temperature is reduced from 44.1 μm to 3.6 μm by applying the error compensation method and real-time compensation system, which is compensated 91.8% compared with no compensation. After the temperature rise, the maximum positioning error in normal temperature is reduced from 26.0 μm to 5.1 μm, which is compensated 80.4% compared with no compensation. The machine accuracy is effectively improved. Key words:Geometric error Thermal error Synthesis error compensation system Real-time error compensation
精密研抛数控机床几何误差与热误差复合建模及其补偿研究

精密研抛数控机床几何误差与热误差复合建模及其补偿研究∗张恩忠;李刚;林洁琼;冉同欢【期刊名称】《组合机床与自动化加工技术》【年(卷),期】2016(000)003【摘要】为了提高精密研抛数控机床的加工精度,对研抛数控机床的几何误差与热误差进行了研究与分析,发现随着机床相关部件温度的不断升高直至热稳态,机床的定位误差也不断增加到稳态值,验证了几何误差和热误差是精密及超精密加工误差的主要来源。
综合考虑了机床复合误差的不同特点并进行误差分离,提出了基于牛顿插值算法和最小二乘法的几何与热复合误差建模方法,依据复合误差模型进行补偿实验,补偿后机床冷态下定位误差值从3.5μm 降至1.2μm,误差降低了65.7%,热稳态后定位误差值从12.2μm降至1.9μm,误差降低了84.4%,实验结果证明复合误差模型计算简单、预测精度高、具有较好的鲁棒性,为提高机床的加工精度提供了理论与实践依据。
【总页数】4页(P78-81)【作者】张恩忠;李刚;林洁琼;冉同欢【作者单位】长春工业大学机电工程学院,长春130012;长春工业大学机电工程学院,长春130012;长春工业大学机电工程学院,长春130012;长春工业大学机电工程学院,长春130012【正文语种】中文【中图分类】TH166;TG659【相关文献】1.数控机床热误差建模及补偿研究 [J], 纪学军2.双转台五轴数控机床热误差建模、检测及补偿实验研究 [J], 王秀山;杨建国;余永昌;邹彩虹3.基于最小二乘支持向量机的精密数控机床热误差建模与补偿研究 [J], 张恩忠;程亚平;齐月玲;林洁琼4.数控机床的热误差建模与补偿研究 [J], 刘旦;于博;吴波;金绍江;李海波5.数控机床几何误差与热误差综合建模及其实时补偿 [J], 王维;杨建国;姚晓栋;范开国;李自汉因版权原因,仅展示原文概要,查看原文内容请购买。
对于数控机床热误差建模的初步认识(精)教学总结

对于数控机床热误差建模的初步认识伴随着科技发展和社会进步,人类对机械制造技术提出了更新和更高的要求,计算机数字控制技术(Computer Numerical Control)随之高速发展,数控机床的性能日趋完善,其应用领域也日益扩大,它的广泛应用给机械制造业的生产方式、产业结构、管理方式带来深刻的变化。
数控技术是制造业实现自动化、柔性化、集成化生产的基础,现代CAD/CAM、FMS、CIMS等也都是以数控技术为基础。
因此数控技术水平的高低已成为衡量一个国家工业自动化的重要标志。
二十一世纪数控机床的发展趋势是:高速化、高精度化、柔性化化、智能化、开放化、并联驱动化、网络化、绿色化。
高效、高速、高精度是二十一世纪制造业的基本需求。
但是,产品更新的速度越来越快,在实际加工中遇到的复杂零件越来越多,加工难度越来越大,精度要求也越来越高。
这就使得现在装备制造业要不断地满足新的需求,朝着柔性化、高速化和高精度化发展。
现代工业的不断发展,使得现代制造业对机械产品的质量要求也越来越高,机械零件的精度取决于机床的加工精度。
而热误差则是影响机床精度最重要的因素之一。
机床内部和外部的热源对机床的热干扰导致机床产生热变形,从而产生热误差。
机床的误差主要有几何误差、热误差和切削力误差,其中热误差占机床总误差量的40%—70%左右,而对于超精密机床而言,高的甚至达到89%。
热误差对高精度机械产品的尺寸精度影响较大,进而也会影响产品加工过程质量、生产效率和成本。
随着机床制造技术的发展,几何误差已得到较好的解决,热误差成为影响机床加工精度的最主要因素,也是难以解决的问题。
目前,学术界和工业界正努力寻求可靠、实用的方法来评估热误差,进而减小并避免热误差。
1、数控机床热误差产生的原因研究表明,机床热误差的情况复杂,具有多变量、长时滞、非线性、强耦合的特点。
热误差的产生因素多,形式多样,具体变现为:(1) 机床热误差受内外部热源的共同影响。
数控机床热误差建模及补偿技术探讨报告

很大代价才能达到的精度水平,满足了一定的精度要求,又降低了仪器和设备制 造的成本,具有显而易见的经济效益。因此,热变形误差补偿技术以其强大的技 术生命力迅速被各国学者、专家所认识,并使之得以迅猛发展和推广。 热误差补偿目前有两种方法:温度场补偿法和位移补偿法。温度场补偿法是 指在某些关键部位安装一些加热元器件或者在某些构件内加入可流动循环的冷 却液,并且对这些温度点进行监测和控制,使温度场的温度得到平衡,使之达到 减少或消除热误差的目的。但是不足之处是难以对每个热误差点进行有效的控 制。位移补偿法是通过对每个坐标轴附加位移来补偿因为热误差}fU 导致刀具和 工件间的偏移误差。这种补偿法是现在使用最多的一种方法。1975 年,口本的 Okushima 公司提出利用温度检测位移补偿法,并将此方法应用于数控加工中心 来实现热误差补偿。80 年代中期,柏林工业大学将这种位移补偿法应用在数控 机床上, 在不同主轴和不同进给速度下试验得出了热误差和特征点之间的关于温 度的函数关系,并建立了误差补偿模型,只需要知道特征点的温度用补偿模型就 可以得到补偿值,然后经过数控机床的伺服进给系统附加位移来实现补偿。 目前,数控机床热误差补偿技术的研究主要体现在以下几个方面: (1)数控 机床热误差温度检测点的选择,即温度传感器摆放位置的研究及检测技术的研 究; (2)获得建立精确性比较强的数控机床热误差补偿的数学模型的研究; ( 3) 数控机床热误差实时补偿技术推广应用的研究。 目前国内外学者对这些方面问题做了大量的研究, 在温度检测点的选择方面 常用的方法有: (1)逐步线性回归方法; (2)热误差模态分析方法; (3)模糊聚 类分析方法; (4)灰色系统理论的关联度分析方法。在机床热误差补偿建模方面 突破常规建模思路,采用 BY 神经网络和 RBF 神经网络及改进的神经网络等非 线性方法,可以更好的解决了数控机床误差补偿的应用问题。
双转台五轴数控机床热误差建模_检测及补偿实验研究

双转台五轴数控机床热误差建模 、检测及补偿实验研究 ———王秀山 杨建国 余永昌等
丝杠处的 2 号传感器 、Y 轴溜板上端面靠近丝杠 处的 24 号传感器 、Z 轴溜板上端面靠近丝杠处的 21 号传感器的温度数据和机床热误差间存在最 大的相关性 ,如表 2 所示 。而且这 4 个传感器也分 布在机床的主要发热区 。因此选取 2 、15 、21 、24 号 传感器的所在位置为最优敏感热源点 。
回归方程 :
yi = a0 + a1 x i,1 + a2 x i,2ቤተ መጻሕፍቲ ባይዱ+ … + an x i, n
(2)
式中 , a0 、a1 、…、an 为待估计的参数 。
令
n
∑ M =
[ yi - ( a0 + a1 x i,1 + a2 x i,2 + … + an x i , n) ]2
i =1
(3)
并用最小二乘的方法求解方程 , 获得相应的方程 系数 ,即令
结合的方法求得 ,最常用的方法是相关分析法 。相
关分析是数理统计学最常用的数据分析方法之
一 ,用来描述两个变量 (离散点) 之间相互关联程 度 , 常用相关系数ρX , Y 表示 X 与 Y 的关联程度[8 ] :
ρX , Y =
Cov ( X , Y) D( X) · D( X)
(1)
本文中各温度测点的数据和热误差间的相关
系数通过编程由 MA TL AB 求得 。对 1 ~ 24 号传
感器的采样数据和热误差作相关分析 , 得到相应
的相关系数 ,24 个温度传感器读数θ与 X 、Y 、Z 方向 的误差数据间的平均相关系数ρθ, X = 01732 047 , ρθ, Y = 01745 667 ,ρθ, Z = 01721 504。
数控机床几何与热误差研究方法综述
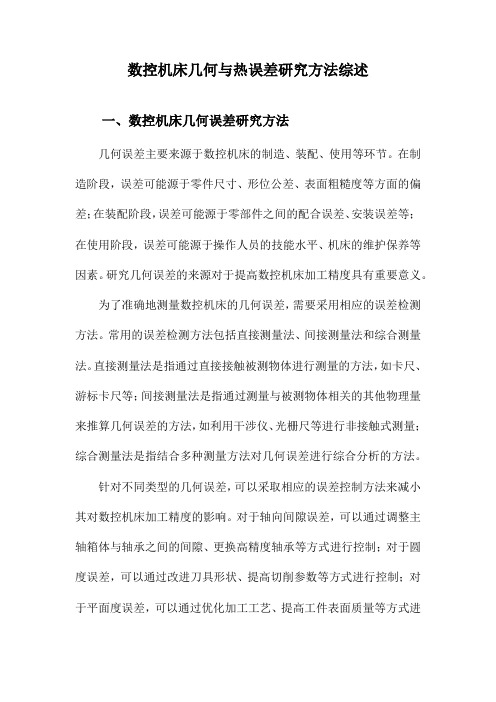
数控机床几何与热误差研究方法综述一、数控机床几何误差研究方法几何误差主要来源于数控机床的制造、装配、使用等环节。
在制造阶段,误差可能源于零件尺寸、形位公差、表面粗糙度等方面的偏差;在装配阶段,误差可能源于零部件之间的配合误差、安装误差等;在使用阶段,误差可能源于操作人员的技能水平、机床的维护保养等因素。
研究几何误差的来源对于提高数控机床加工精度具有重要意义。
为了准确地测量数控机床的几何误差,需要采用相应的误差检测方法。
常用的误差检测方法包括直接测量法、间接测量法和综合测量法。
直接测量法是指通过直接接触被测物体进行测量的方法,如卡尺、游标卡尺等;间接测量法是指通过测量与被测物体相关的其他物理量来推算几何误差的方法,如利用干涉仪、光栅尺等进行非接触式测量;综合测量法是指结合多种测量方法对几何误差进行综合分析的方法。
针对不同类型的几何误差,可以采取相应的误差控制方法来减小其对数控机床加工精度的影响。
对于轴向间隙误差,可以通过调整主轴箱体与轴承之间的间隙、更换高精度轴承等方式进行控制;对于圆度误差,可以通过改进刀具形状、提高切削参数等方式进行控制;对于平面度误差,可以通过优化加工工艺、提高工件表面质量等方式进行控制。
还可以采用补偿技术、自适应控制技术等方法对几何误差进行实时修正和调整。
数控机床几何误差的研究方法涉及多个学科领域,需要综合运用理论分析、实验研究和实际应用等多种手段。
通过对几何误差的研究和控制,可以有效提高数控机床的加工精度和稳定性,为现代制造业的发展提供有力支持。
1. 传统误差分析方法在数控机床几何与热误差研究中,传统误差分析方法主要包括有限元法、边界元法和接触单元法等。
这些方法主要通过对机床结构、刀具和工件的几何形状进行离散化处理,建立数学模型,然后通过求解线性方程组或非线性方程组来计算误差。
有限元法是一种将连续体分割为有限个单元,通过求解各单元上的微分方程组成的积分方程来描述整个系统的运动和变形过程的方法。
《2024年多轴数控机床精度建模与误差补偿方法研究》范文
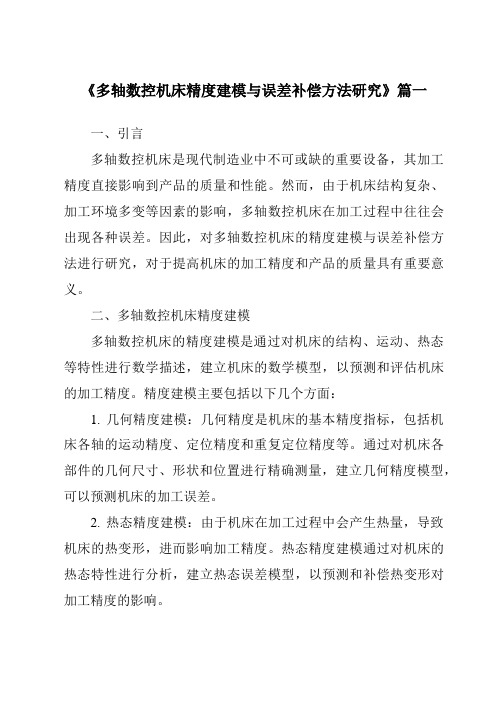
《多轴数控机床精度建模与误差补偿方法研究》篇一一、引言多轴数控机床是现代制造业中不可或缺的重要设备,其加工精度直接影响到产品的质量和性能。
然而,由于机床结构复杂、加工环境多变等因素的影响,多轴数控机床在加工过程中往往会出现各种误差。
因此,对多轴数控机床的精度建模与误差补偿方法进行研究,对于提高机床的加工精度和产品的质量具有重要意义。
二、多轴数控机床精度建模多轴数控机床的精度建模是通过对机床的结构、运动、热态等特性进行数学描述,建立机床的数学模型,以预测和评估机床的加工精度。
精度建模主要包括以下几个方面:1. 几何精度建模:几何精度是机床的基本精度指标,包括机床各轴的运动精度、定位精度和重复定位精度等。
通过对机床各部件的几何尺寸、形状和位置进行精确测量,建立几何精度模型,可以预测机床的加工误差。
2. 热态精度建模:由于机床在加工过程中会产生热量,导致机床的热变形,进而影响加工精度。
热态精度建模通过对机床的热态特性进行分析,建立热态误差模型,以预测和补偿热变形对加工精度的影响。
3. 综合误差建模:综合误差建模是将几何精度建模和热态精度建模结合起来,考虑机床的各种误差源,建立综合误差模型。
通过对综合误差模型进行分析,可以更准确地预测机床的加工误差。
三、误差补偿方法针对多轴数控机床的误差,需要采取相应的误差补偿方法。
常见的误差补偿方法包括:1. 软件补偿法:软件补偿法是通过在数控系统中加入补偿算法,对机床的误差进行实时补偿。
软件补偿法具有灵活性高、成本低等优点,是当前误差补偿的主要方法。
常见的软件补偿算法包括插补算法、逆补偿算法等。
2. 硬件补偿法:硬件补偿法是通过在机床结构中加入补偿装置,如误差传感器、调整机构等,对机床的误差进行直接补偿。
硬件补偿法具有补偿精度高、稳定性好等优点,但成本较高。
3. 混合补偿法:混合补偿法是结合软件补偿法和硬件补偿法的优点,通过在数控系统中加入补偿算法,同时结合硬件装置对机床的误差进行综合补偿。
- 1、下载文档前请自行甄别文档内容的完整性,平台不提供额外的编辑、内容补充、找答案等附加服务。
- 2、"仅部分预览"的文档,不可在线预览部分如存在完整性等问题,可反馈申请退款(可完整预览的文档不适用该条件!)。
- 3、如文档侵犯您的权益,请联系客服反馈,我们会尽快为您处理(人工客服工作时间:9:00-18:30)。
数控机床几何误差与热误差综合建模
本文在对一台立式加工中心进行误差检测分析的基础上,应用多项式及线性拟合方法建立机床几何误差与热误差的误差综合数学模型,通过外部实时补偿系统与机床数控系统实时通信,实现误差实时补偿。
该方法能有效并经济地大幅度提高机床的加工精度。
1..数据采集
1.1 定位误差测量
采用激光干涉仪对立式加工中心的移动轴进行定位误差的检测,如图 1 所示。
为了减少检测过程中的随机误差,每个轴的正方向、反方向分别重复检测 3 次,取测量平均值作为测量结果。
本文以机床的y 轴定位误差的测量、建模进行说明。
y 轴行程范围为400 mm,测量起点为数控机床坐标零点。
每25 mm 取一个测量点,全程共有17 个测量点。
图 1 定位误差测量
为使机床的定位误差得到综合评估,分别测量了机床不同温度状态下的定位误差与温度变化。
首先在机床冷态(即刚开机)下测量定位误差,测量后,快速移动三根运动轴使机床温度特别是丝杆和螺母的温度升高,然后再测量、再温升如此重复至机床各温度变化趋于稳定,即机床达到热平衡状态结束测量,其中温升过程从温升10~120 min 直至机床达到热稳定状态(前面温度变化较大故温升时间要短些)。
1.2 温度误差测量
在测量定位误差的同时,还要测量机床的温度,使之每一次定位误差数据对应一组温度数据。
为此,在该加工中心上共布置了9 个温度传感器,其中对y 轴热误差影响最大的测量点为y 轴丝杆螺母、y 轴丝杆座及y 轴床身,有关y 轴的温度传感器布置如图 2 所示(传感器用圆圈标出)。
(a) y 轴丝杆螺母(b) y 轴丝杆座
(c) y 轴床身
图2 y 轴温度传感器布点
在整个温升过程中,采用基于LabVIEW 的自动温度采集软件对温度场进行实时监控,并记录下常温、温升10~120 min 时的测点温度,测量结
果如图3 所示。
图 3 各定位误差测量时的温度变化表1为集合误差与热误差原始数据数据
2 误差建模
这里以 y 轴正向的建模过程为例。
图 4 为 y 轴在冷态,温度升高 10~120 min 共 7 次测得的 7 条定位误差曲线。
由图 4 可见在不同温度状态下测得的定位误差有很大的变化。
这就是为何一般补偿的效果不好的原因,即不能按一条定位误差曲线进行补偿,而应该对于不同的温度,根据不同的定位误差曲线进行补偿。
图4 y 轴全部误差曲线
再由图 4 可知,随着机床温度的升高,误差曲线形状变化不大而曲线的斜率有变化。
因此,这种误差元素可分离成如下两部分:
y =
+t εεε (1) 式中 ε--------总误差
y ε-------线性定位误差的几何部分,只与 y 轴机床坐标位置有关
t ε--------线性定位误差的热部分,与机床的温度有关
()0=t y εαδδ-
α--------对应误差曲线的一次线性拟合斜率 y δ-------机床所在位置的 y 轴机床坐标 0δ--------y 轴机床坐标零点
几何误差部分用多项式进行拟合。
热误差部分与机床上的某些热关键点温度有关,其与各条误差曲线的拟合直线斜率相关。
2.1 几何误差建模
将图 4 中的 7 条误差曲线均旋转到水平,即令一次拟合曲线斜率为 0,然后求这 7 条误差曲线的平均值,从而可得基准误差曲线,如图 5 所示。
图 5 基准误差曲线拟合
根据最小二乘理论,对所得基准误差曲线进行一元四次拟合,可得到如式(2)所示基准误差模型:
26394=0.02807-0.005450.00055 3.12310 4.710y y y y y εδδδδ--++⨯+⨯(2)
误差拟合曲线如图 5 所示。
2.2 热误差建模
对图 4 中的 7 条误差曲线分别进行一次线性拟合,可得到如式(3)所示的 7 条拟合直线。
0 2.0588-0.0509x ϕ=- 1 1.0945-0.0240x ϕ=-
2 0.2985-0.0091x ϕ=
3 1.5807+0.0035x ϕ=(3)
4 2.0276+0.0246x ϕ=
5 2.2332+0.0454x ϕ=
6 3.5934+0.0631x ϕ=
0ϕ~6ϕ为拟合直线 0~6,x 为横坐标,拟合结果如图 6 所示。
图 6 误差曲线的线性拟合
选取对热误差影响相对较大的y 轴丝杆螺母与 y 轴丝杆座作为热关键点。
为了提高热误差模型的鲁棒性,减少机床环境温度变化对模型的影响,选取丝杆螺母温度 t 的变化量s t ∆与丝杆座温度变化量r t ∆,结合表2建模得:
表2斜率与温度统计表
-0.62530.02220.0105s r t t α=+∆+∆(4)
式中s t ∆-------丝杆螺母温度变化量
s s e t t t ∆=-
s t ---------丝杆螺母温度 e t ---------环境温度
r t ∆-------丝杆座温度变化量 r r e t t t ∆=-
r t ——丝杆座温度
则热误差模型为
()0(-0.62530.02220.0105)0.9400t s r y t t εδδ=+∆+∆⨯--(5)
2.3 综合误差建模
结合上述几何误差模型和热误差模型,将式(2)、(5)代入式(1)中,得到误差的综合模型为
26394=-0.91193-0.005450.00055 3.12310 4.710(-0.62530.02220.0105)
y y y y s r t t εδδδδ--++⨯+⨯+
+∆+∆ (6)
建模结果如图 7 所示。
图7 误差综合模型的拟合效果
7 条误差曲线共有17×7=119 个误差点,将这些误差值汇总,图8 为7 条误差曲线的总体残差示意图。
其中,前17 个点是常温误差曲线的残差点,后面以此类推。
图8 残差示意图
根据总体残差示意图,找出其中最小与最大的极限值,可得到该建模方法的建模精度在[–4.27μm,7.75μm]范围内。
3 总结
该方法的特点:①考虑了机床不同温度状态下误差的全面变化而进行机床温度和误差数据的采集和分析,即以实际测量的机床误差数据为依据,分析了机床温升与误差变化之间的关系,建立了几何误差与热误差的综合数学模型,实现了主要机床误差的补偿,综合考虑了机床在温升前的冷态状态下以及在整个温升过程中直至热稳态之后的误差变化情况;②几何误差和热误差的分离和综合,即根据几何误差和热误差的不同特性进行误差分离,应用多项式拟合与线性拟合的方法分别建模再综合可得到几何与热的复合误差综合数学模型,该方法概念清晰,方便快捷,模型拟合精度高,计算量小,易于程序设计,可用于机床误差在线实时补偿。