第七节 选择性催化氧化
第七节 选择性催化氧化
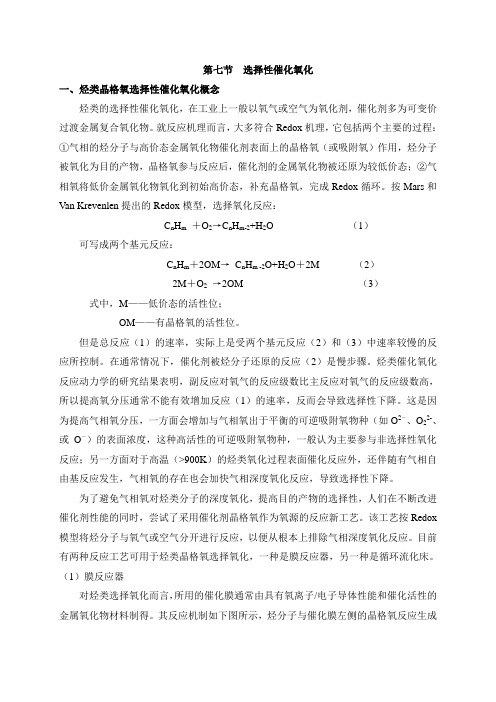
第七节选择性催化氧化一、烃类晶格氧选择性催化氧化概念烃类的选择性催化氧化,在工业上一般以氧气或空气为氧化剂,催化剂多为可变价过渡金属复合氧化物。
就反应机理而言,大多符合Redox机理,它包括两个主要的过程:①气相的烃分子与高价态金属氧化物催化剂表面上的晶格氧(或吸附氧)作用,烃分子被氧化为目的产物,晶格氧参与反应后,催化剂的金属氧化物被还原为较低价态;②气相氧将低价金属氧化物氧化到初始高价态,补充晶格氧,完成Redox循环。
按Mars和Van Krevenlen提出的Redox模型,选择氧化反应:C n H m+O2→C n H m-2+H2O (1)可写成两个基元反应:C n H m+2OM→C n H m -2O+H2O+2M (2)2M+O2→2OM (3)式中,M——低价态的活性位;OM——有晶格氧的活性位。
但是总反应(1)的速率,实际上是受两个基元反应(2)和(3)中速率较慢的反应所控制。
在通常情况下,催化剂被烃分子还原的反应(2)是慢步骤。
烃类催化氧化反应动力学的研究结果表明,副反应对氧气的反应级数比主反应对氧气的反应级数高,所以提高氧分压通常不能有效增加反应(1)的速率,反而会导致选择性下降。
这是因为提高气相氧分压,一方面会增加与气相氧出于平衡的可逆吸附氧物种(如O2-、O22-、或O-)的表面浓度,这种高活性的可逆吸附氧物种,一般认为主要参与非选择性氧化反应;另一方面对于高温(>900K)的烃类氧化过程表面催化反应外,还伴随有气相自由基反应发生,气相氧的存在也会加快气相深度氧化反应,导致选择性下降。
为了避免气相氧对烃类分子的深度氧化,提高目的产物的选择性,人们在不断改进催化剂性能的同时,尝试了采用催化剂晶格氧作为氧源的反应新工艺。
该工艺按Redox 模型将烃分子与氧气或空气分开进行反应,以便从根本上排除气相深度氧化反应。
目前有两种反应工艺可用于烃类晶格氧选择氧化,一种是膜反应器,另一种是循环流化床。
07醇选择性氧化

25
Sarett和Collins试剂 三氧化铬加入到吡啶中形成CrO3 2Py结晶。 CrO3 2Py的吡啶溶液--Sarett试剂。是一个很有效的仲醇 氧化成酮的试剂;在无水条件下也可以把伯醇氧化成醛。 CrO3 2Py的二氯甲烷溶液--Collins试剂。条件更温和。
制备这两种试剂要特别小心,必须把CrO3加入到吡啶中,否 则会发生爆炸。
NaHCO3-调节体系pH CH2Cl2 / H2O两相体系
0oC下,3分钟将伯醇氧化成醛;醛氧化成酸的速度很慢;
7-10分钟将仲醇氧化成酮。
浙江工业大学化学工程与材料学院
59
TEMPO的类型
浙江工业大学化学工程与材料学院
60
浙江工业大学化学工程与材料学院
61
改进的Anelli氧化-TEMPO/PhI(OAc)2体系
浙江工业大学化学工程与材料学院
66
Oppenauer氧化在氧化甾醇时特别成功体化合物。但是, 最早的方法几乎只局限于这个领域,在醇氧化成醛的反应 方面,热力学和副反应都限制了这个反应更多的应用。进 一步研究用环己酮作氧化剂,Oppenauer氧化在合成酮的 领域中有广泛的应用。
浙江工业大学化学工程与材料学院
Corey-Kim氧化体系 是唯一不用DMSO的活化二甲基亚砜氧化体系
浙江工业大学化学工程与材料学院
42
醇选择性氧化合成醛酮
3. 高价碘氧化物
2020/8/13
浙江工业大学化学工程与材料学院
43
浙江工业大学化学工程与材料学院
44
Dess-Martin Periodinane氧化 NMP
NMP是一个爆炸性的化合物。 其实是由于其中的杂质引起。使用时一定要小心。
第七章_催化氧化 (第二节)(共40张PPT)

催化剂活性较高、选择性较好 反应条件不太苛刻,反应比较平稳 设备简单,容积较小,生产能力较高 反应温度通常不太高,反应热利用率较低 在腐蚀性较强的体系时要采用特殊材质 催化剂多为贵金属,必须分离回收
一、催化自氧化
具有自由基链式反响特征,能自动加速 的氧化反响。使用催化剂加速链的引发 ,称为催化自氧化。 工业上生产有机酸、过氧化物
主反响:以乙烯和氧气〔或空气〕为原料,在由氯化钯、氯化铜、盐酸组成的催化剂水溶液中,进行液相氧化生产乙醛。
氯化钯是催化剂,氯化铜氧化剂,没有氯化铜的存在,是不能完成催化过程的。
具有自由基链式反响特征,能自动加速的氧化反响。
3其、结工构艺简条单件,影检响修及工很选方择业便 生产中对催化剂溶液的控制指标主要有:钯含量、铜含量、
副反响:
络合催化氧化
① 平行副反响:主要生成氯乙烷、氯乙醇 等 副产物;
② 连串副反响:主要生成氯代乙醛、醋酸、氯代醋酸、 丁烯醛、草酸及深度氧化产物等。
副产品虽然种类繁多,但它们的量甚少, 一般除一氯乙醛外,均无别离回收价值。通常将气体副产 物通入火炬燃烧,液体副产物作生化处理后排放。
络合催化氧化
优点
原料廉价,本钱低及乙醛收率高,副反响少等
目前被认为是生产乙醛最经济的方法,世界上约有70 %的乙醛是采用此法来进行生产的
缺点
氯化钯、氯化铜的盐酸溶液作催化剂,对设备的腐蚀极为 严重。贵金属钛等特殊材料。
2、反响原理
1〕根本反响过程:
主反响:以乙烯和氧气〔或空气〕为原料, 在由氯化钯、氯化铜、盐酸组成的催化剂水溶液中, 进行液相氧化生产乙醛。
④ 氧化度:氧化度——指在总铜中Cu2+所占比
例,即[Cu2+]/{[Cu2+]+[Cu+]}。氧化度过
选择性催化氧化反应的研究及应用

选择性催化氧化反应的研究及应用近年来,选择性催化氧化反应已成为化学界研究的热点之一。
这种反应在有机合成、能源领域等方面均有广泛应用。
本文将从选择性催化氧化反应的基本原理、各类催化剂的研究及应用方面进行阐述。
一、选择性催化氧化反应的基本原理选择性催化氧化反应是指在化学反应过程中,通过选择适当的催化剂,使反应分子只发生局部氧化,而不引起分子整体氧化的化学反应。
在这一过程中,催化剂发挥着至关重要的作用。
它不仅影响着反应转化率,更重要的是决定着反应产物的选择性。
具体来说,选择性催化氧化反应需要满足以下几个条件。
首先,催化剂必须具有良好的选择性。
其次,反应条件必须精确控制,以保证局部氧化反应的发生。
再次,反应物的选择也很关键。
最后,反应后的催化剂的再生过程也要注意。
二、各类催化剂的研究及应用在选择性催化氧化反应研究中,各类催化剂的研究是至关重要的。
下面我们分别介绍金属催化剂、酶催化剂、分子筛催化剂和氧化剂等四个方面。
1. 金属催化剂金属催化剂是目前应用最广泛的选择性催化剂之一。
这类催化剂的特点是催化活性高,反应速率快,反应条件较为温和。
此外,不同金属类别的催化剂也表现出不同的催化活性和选择性。
目前,铑、钯、铁、镍和银等金属催化剂在选择性催化氧化反应中表现出了卓越的性能。
例如,在烯烃氧化反应中,银催化剂能够将二烯烃氧化成为相应的酮。
在醛类氧化反应中,铁催化剂能够将醛转化为相应的酸。
金属催化剂的研究在有机合成和能源领域等方面有广泛应用。
2. 酶催化剂酶催化剂是生物催化剂的代表。
与金属催化剂相比,酶催化剂的催化反应具有高度选择性和专一性。
而且,酶催化剂在反应条件温和,不需要高温高压,非常环保。
此外,酶催化剂还可以在体内或体外进行。
目前,酶催化剂主要应用在医学领域和食品工业中。
例如,葡萄糖氧化酶被用于葡萄糖探测器的制造中。
α-淀粉酶和胆固醇酶被用于致命家族高胆固醇的治疗中。
3. 分子筛催化剂分子筛催化剂是一种针孔结构的催化剂。
化工工艺学课件催化氧化

06 案例分析
某石化企业催化氧化工艺改造
改造背景
某石化企业原有催化氧化 工艺存在能效低、污染物 排放量大等问题,需要进 行技术升级和改造。
改造内容
采用新型高效催化剂,优 化反应条件,提高反应速 度和选择性,降低能耗和 污染物排放。
改造效果
改造后,催化氧化工艺的 能效提高了30%,污染物 排放量减少了50%,同时 提高了产品收率和质量。
产品后处理与分离
产物分离
催化氧化反应结束后,产物需要经过分离和提纯才能得到最 终产品。分离和提纯的方法包括蒸馏、萃取、重结晶等,应 根据产物的性质和要求选择合适的分离方法。
废水处理
催化氧化过程中会产生一定量的废水,需要进行处理以避免 对环境造成污染。废水处理的方法包括物理法、化学法和生 物法等,应根据废水的性质和排放标准选择合适的方法进行 处理。
THANKS
鼓泡塔反应器的优点是结构简单、操作方便、催化剂装填量较大,但传质效率相对 较低。
催化氧化设备的选择与设计
选择催化氧化设备时,应根据具 体的工艺要求、物料性质和处理
规模等因素进行综合考虑。
设计催化氧化设备时,应注重设 备的结构、材料、热工条件、安 全环保等方面的要求,以确保设
备的可靠性和经济性。
在实际应用中,可以根据具体的 情况选择合适的催化氧化设备, 以达到最佳的处理效果和经济效
原料的提纯
对于某些含有杂质的原料,需要进行提纯以提高其纯度。提纯的方法包括萃取、重结晶、 蒸馏等,应根据原料的性质和目标产物选择合适的提纯方法。
催化剂的选择与装填
催化剂的选择
催化剂在催化氧化过程中起着至关重要的作用,选择合适的催化剂可以提高反应 速率、产物纯度和选择性。在选择催化剂时,应考虑其活性、稳定性、选择性以 及经济性等因素。
化工工艺学烃类选择性氧化过程
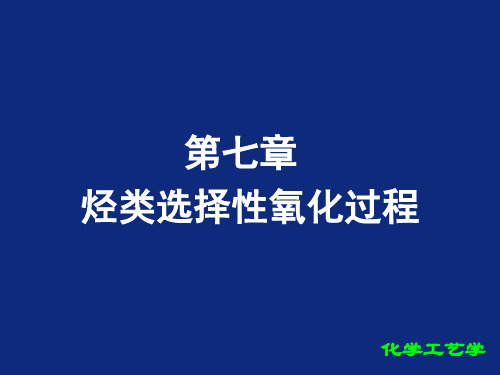
非均相催化氧化
工业上使用的有机原料:
➢ 具有π电子的化合物 烯烃 芳烃
➢ 不具有π电子的化合物 醇类 烷烃
低碳烷烃的选择性氧化: 丁烷代替苯氧化制顺酐 丙烷代替丙烯氨氧化制丙烯腈
化学工艺学
重要的非均相氧化反应
化学工艺学
催化自氧化
具有自由基链式反应特征,能自 动加速的氧化反应。使用催化剂 加速链的引发,称为催化自氧化
工业上生产有机酸、过氧化物
化学工艺学
催化自氧化催化剂
催化剂多为Co、Mn等过渡金属离子 的盐类,溶解在液态介质中形成均相
助催化剂,又称氧化促进剂
缩短反应诱导期,加速反应的中间过程
化学工艺学
第七章 烃类选择性氧化过程
化学工艺学
主要内容
氧化反应的特点 氧化剂的种类
氧化反应类型(均相、非均相) 氧化反应的典型产品和工艺
化学工艺学
氧化反应
化学工业中氧化反应是一大类重 要化学反应,它是生产大宗化工 原料和中间体的重要反应过程
有机物氧化反应当数烃类的氧化 最有代表性
烃类氧化反应可分为完全氧化和 部分氧化两大类型
过程易燃易爆
安全性Байду номын сангаас
化学工艺学
氧化剂的选择
空气 纯氧 过氧化氢 其它过氧化物 反应生成的烃类过氧化物
或过氧酸
化学工艺学
烃类选择性氧化过程的分类
反应类型: 碳链不发生断裂的氧化反应 碳链发生断裂的氧化反应 氧化缩合反应
化学工艺学
烃类选择性氧化过程的分类
反应相态
催化自氧化
均相催化氧化 络合催化氧化
化学工艺学
均相催化氧化
自氧化反应机理
化学工艺学
有机工艺学第七章

◆氧空速 空速↑,有利气液接触,氧吸收↑,有利反应进行; 过高空速,氧停留时间短,氧利用率↓,尾气氧含量↑
应用举例一 对二甲苯氧化制对苯二甲酸
●对苯二甲酸性质
两个羧基分别与苯环中相对的两个碳原子相连接 而成的二元芳香羧酸。白色晶体或粉末,低毒,可 燃。若与空气混合,在一定的限度内遇火即燃烧甚 至发生爆炸。
◆溶剂的影响 不仅改变反应条件,对反应历程和产物产生影响 (对二甲苯氧化对苯二甲酸,醋酸溶剂选择性95%,无溶
剂20%,主要产物醇、醛、酮) ◆杂质的影响 杂质存在会导致体系自由基失活,破坏链引发和传递
阻化作用,阻化剂 ◆温度的影响 动力学控制;温度↑,有利反应,副产物↑,选择性↓
◆氧气分压的影响 氧分压不足,反应速率降低,氧分压影响选择性
工业上用于生产有机酸、过氧化物p224
●烃类自氧化反应机理—自由机链式反应机理
烃分子均裂生成自由基 决定性步骤
ROOH的生成是链传递反应的控制步骤
烃分子发生均裂的活化能 叔C-H<仲C-H<伯C-H
链传递受(7-3)控制,ROOH不稳定,可生成新自由基 产物组成中有:醇、醛、酮、酸,组成复杂
●催化自氧化催化剂p224
分子氧
PdCl2+烯烃 PdCl42-
烯烃氧化 Pd0 +CuCl2
PdCl2 CuCl
反应速率最慢,控制步骤
O2
催化剂:Pd2+、Pt2+、Rh3+、Ir4+、Ru3+和Ti3+
氧化剂:CuCl2、FeCl3、H2O2、MnO2、苯醌等 溶 剂:水、乙醇、环丁砜等
●烯烃配位催化氧化
烟气中NO选择性催化氧化催化剂

烟气中NO的来源030201NO对环境和人体的危害NO可以与O3发生反应,导致臭氧层破裂,影响人类健康。
臭氧层破坏光化学烟雾酸雨温室效应在阳光照射下,NO与烃类化合物反应,形成光化学烟雾,对环境和人类健康造成危害。
NO与雨水反应,形成硝酸或硝酸盐,导致土壤和水体酸化,对生态环境和人类健康产生影响。
NO可以与大气中的CO2反应,形成温室气体,加剧全球气候变暖。
催化剂的定义催化剂的分类催化剂的定义与分类选择性催化氧化原理选择性催化氧化是指在一定条件下,仅对某些特定底物进行氧化反应,而不是对所有底物都进行氧化反应。
温度和压力对选择性催化氧化的影响温度和压力是影响选择性催化氧化反应的重要因素。
一般来说,随着温度的升高,反应速率会加快,但同时也会导致副反应增多。
压力对选择性催化氧化的影响则相对较小。
选择性催化氧化的原理催化剂在选择性催化氧化中的作用催化剂在选择性催化氧化中的重要性催化剂在选择性催化氧化中起着至关重要的作用。
通过使用催化剂,可以大大降低反应活化能,提高反应速率,并降低副反应发生的可能性。
催化剂的活性与稳定性催化剂的活性是指其在一定条件下对特定反应的催化能力。
稳定性则是指催化剂在使用过程中保持其活性的能力。
一个好的催化剂应具有较高的活性和稳定性。
贵金属催化剂03Fe2O3催化剂金属氧化物催化剂01V2O5催化剂02MnO2催化剂HZSM-5催化剂MCM-41催化剂分子筛催化剂复合催化剂Pt/Al2O3催化剂Pd/ZnO/Al2O3催化剂1浸渍法23将载体浸入含有所需活性组分的溶液中,通过液相吸附使活性组分均匀地附着在载体表面。
原理将载体浸泡在含有活性组分的溶液中,浸泡时间一般为数小时至数十小时,浸泡后进行干燥、焙烧等处理。
步骤浸渍法适用于制备成分较简单的催化剂,制得的催化剂活性较高,但制备过程中易造成载体表面堵塞或活性组分团聚。
应用原理步骤应用共沉淀法熔融法原理01步骤02应用03其他制备方法性能评价方法与指标活性评价通过测量反应速率、转化率等参数,评估催化剂的活性。
- 1、下载文档前请自行甄别文档内容的完整性,平台不提供额外的编辑、内容补充、找答案等附加服务。
- 2、"仅部分预览"的文档,不可在线预览部分如存在完整性等问题,可反馈申请退款(可完整预览的文档不适用该条件!)。
- 3、如文档侵犯您的权益,请联系客服反馈,我们会尽快为您处理(人工客服工作时间:9:00-18:30)。
第七节选择性催化氧化一、烃类晶格氧选择性催化氧化概念烃类的选择性催化氧化,在工业上一般以氧气或空气为氧化剂,催化剂多为可变价过渡金属复合氧化物。
就反应机理而言,大多符合Redox机理,它包括两个主要的过程:①气相的烃分子与高价态金属氧化物催化剂表面上的晶格氧(或吸附氧)作用,烃分子被氧化为目的产物,晶格氧参与反应后,催化剂的金属氧化物被还原为较低价态;②气相氧将低价金属氧化物氧化到初始高价态,补充晶格氧,完成Redox循环。
按Mars和Van Krevenlen提出的Redox模型,选择氧化反应:C n H m+O2→C n H m-2+H2O (1)可写成两个基元反应:C n H m+2OM→C n H m -2O+H2O+2M (2)2M+O2→2OM (3)式中,M——低价态的活性位;OM——有晶格氧的活性位。
但是总反应(1)的速率,实际上是受两个基元反应(2)和(3)中速率较慢的反应所控制。
在通常情况下,催化剂被烃分子还原的反应(2)是慢步骤。
烃类催化氧化反应动力学的研究结果表明,副反应对氧气的反应级数比主反应对氧气的反应级数高,所以提高氧分压通常不能有效增加反应(1)的速率,反而会导致选择性下降。
这是因为提高气相氧分压,一方面会增加与气相氧出于平衡的可逆吸附氧物种(如O2-、O22-、或O-)的表面浓度,这种高活性的可逆吸附氧物种,一般认为主要参与非选择性氧化反应;另一方面对于高温(>900K)的烃类氧化过程表面催化反应外,还伴随有气相自由基反应发生,气相氧的存在也会加快气相深度氧化反应,导致选择性下降。
为了避免气相氧对烃类分子的深度氧化,提高目的产物的选择性,人们在不断改进催化剂性能的同时,尝试了采用催化剂晶格氧作为氧源的反应新工艺。
该工艺按Redox 模型将烃分子与氧气或空气分开进行反应,以便从根本上排除气相深度氧化反应。
目前有两种反应工艺可用于烃类晶格氧选择氧化,一种是膜反应器,另一种是循环流化床。
(1)膜反应器对烃类选择氧化而言,所用的催化膜通常由具有氧离子/电子导体性能和催化活性的金属氧化物材料制得。
其反应机制如下图所示,烃分子与催化膜左侧的晶格氧反应生成氧化产物,氧分子在催化膜的右侧离解吸附,获得电子转化为氧离子,催化膜作为氧离子/电子导体,可把氧离子从膜的右侧输送到左侧,同时把电子从左侧输送到右侧,实现还原-氧化循环。
这种膜反应器虽然可显著提高氧化反应的选择性,但由于氧离子的传输速率较慢,限制了膜反应器的反应速率,其反应速率通常比共进料反应器慢1~2个数量级。
此外,这种膜反应器的放大,目前在制造技术上还存在很多难题有待解决催化膜反应示意图(2)循环流化床提升管反应器循环流化床提升管反应器(见下图)是一种很有前景的方法。
该工艺在无气相氧存在下用催化剂晶格氧作为供氧体,按Redox模式,使还原-再氧化循环分别在反应器和再生器中完成;也就是说,在提升管反应器中烃分子与催化剂的晶格氧反应生成氧化产物,失去晶格氧的催化剂被输送到再生器中用空气氧化到初始高价态,然后送到反应器与烃原料反应。
循环流化床反应器烃类晶格氧选择氧化工艺不仅可以避免原料和产物与气相氧的直接接触,还可消除沸腾床中容易发生的返混现象,使目的产物的收率和选择性得以显著提高。
烃类氧化的循环流化床提升管反应器示意图上述新工艺的优点是:①可使催化剂的还原和再氧化分开进行,以便于选择各自的最佳操作条件;②因无气相氧分子存在,而且在提升反应器中排除了返混现象,可大幅度提高选择氧化反应单程收率、选择性和时空产率;③烃类的进料浓度不受爆炸极限的限制,可提高反应产物的浓度,使反应产物容易分离回收;④可用空气代替纯氧作氧化剂,省去制氧的投资和操作费用。
以上优点是属于比较理想的情况,实际上烃类晶格选择氧化工艺还存在许多问题有待克服。
二、选择性氧化实例—丁烷氧化制顺酐工艺过程烃类晶格氧选择氧化的开创性研究始于1940年代末期,DuPont公司于近年才开发成功晶格氧丁烷选择氧化制顺酐新工艺,该工艺用催化剂的晶格氧代替气相氧作为氧源,按还原-氧化(Redox)模式将丁烷和空气分别进入循环流化床提升管反应器和再生器,可使顺酐选择性摩尔分数从45%~50%提高到了70%~75%,未反应的丁烷可循环利用,被赞誉为对环境友好的催化过程。
这表明烃类晶格氧选择氧化新工艺是控制深度氧化、提高选择性、节约资源和保护环境的有效催化新技术。
1 、传统工艺过程—正丁烷氧化法制顺酐自从1974年美国孟山都化学公司等实现工业化生产以来,此法发展很快。
由于正丁烷价廉、化工利用不广以及尾气排放污染程度较小,所以此法成为有竞争力的生产方法。
目前国外新建的顺丁烯二酸酐装置中,正丁烷所占比例已超过苯法,据预测美国的顺丁烯二酸酐生产今后将绝大部分为正丁烷法。
我国对此法也正加紧研究开发。
(1)生产基本原理。
正丁烷和空气(或氧气)混合后通过V2O5-P2O5系等催化剂气相氧化生成顺丁烯二酸酐,其反应如下:•主反应:•C4O10+7/2O2→C4H2O3+4H2O △H=-1261kJ/mol•副反应:•C4O10 +11/2O2→2CO+2CO2+5H2O △H=-2091kJ∕mol还有生成醛、酮、酸等副反应。
正丁烷存在于炼厂气、油田伴生气和石油裂解气中,工业上主要以油田伴生气回收的正丁烷为原料。
•催化剂为V2O5-P2O5、V-Mo-O或Co-Mo并含少量CeCl2,以SiO2为载体。
原料中含正丁烷1.6%~1.8%(摩尔分数),其余为空气。
用纯氧代替空气好处不大,因反应选择性低,大量纯氧消耗在无用的副反应上,且需加入惰性气体稀释,以免落入爆炸范围。
其反应温度为370~430℃,转化率约为85%,选择性大于70%,总收率为理论的60%左右。
(2)工艺流程及主要工艺参数。
•Halcon/SD公司正丁烷制顺丁酸酐的工艺流程图如图所示。
•为了取得正丁烷法更高的经济效益,众多公司正在开发正丁烷法流化床反应器新工艺,比利时UCB公司和日本三菱化成公司将其应用于工业生产。
(3)“三废”处理无论是苯、丁烯或正丁烷氧化法生产顺丁烯二酸酐,反应尾气中均含有未转化的苯、丁烯或丁烷及CO、微量醛、酮、酸等有害气体,可在800℃左右通过焚烧炉或助燃剂焚烧回收热量后再排入大气,或经过催化剂(如贵金属等)进行催化燃烧处理。
2 、晶格氧氧化工艺针对丁烷/空气共进料工艺存在丁烷浓度低和顺酐选择性低等缺点,1980年代初期,DuPont公司开始致力于研究开发丁烷晶格氧选择氧化循环流化床新工艺。
经过近10余年的努力,该公司解决了两个关键技术问题:其一是研制成功抗磨硅胶壳层VPO 晶格盐催化剂;其二是开发成功循环流化床提升管反应器。
•在丁烷氧化的循环流化床提升管反应器中,VPO催化剂在流化床再生器中被氧化,氧化态的催化剂粒子通过立管移动至提升管反应器底部入口处,用含丁烷的高速原料气流提升至反应器顶部,丁烷在提升管中被催化剂的晶格氧氧化为顺酐,然后从顶部进入旋风分离器把被还原的催化剂粒子和反应产物分开,回收的催化剂粒子经惰气体吹脱除去吸附的碳物种后,被送入再生器用空气再氧化,完成Redox循环。
因为反应物和催化剂在提升管中基本上为活塞流,而且无气相氧分子存在,催化剂表面态可通过优化再生操作和在进入提升管反应器前吹脱除去表面吸附的非选择性氧物种,所以可显著提高顺酐的选择性。
为了取得工业放大的设计数据,DuPont公司于1990年在Oklahoma的Ponca市动工兴建丁烷氧化制顺酐的CFB提升管示范装置,于1992年初建成开车。
该示范装置的提升管反应器直径为0.15m,高30m,配备了适当大小的催化剂再生器、气提段和立管,以保证足够的催化剂循环速率。
为了进行比较,该装置也可按共进料模式进行操作。
除配备了过程的控制和数据收集系统外,还配备了在线的质谱、红外、紫外和其他分析仪器,并包括产品回收、净化、污水处理和未反应丁烷的循环装置。
示范装置的CFB提升管反应器的操作条件汇总于下表。
表DuPont丁烷制顺酐CFB提升管示范装置的操作条件原料气中丁烷浓度对选择性的影响很小,但转化率对选择性有较大影响。
当丁烷转化率为80%(摩尔分数)时,顺酐选择性为60%(摩尔分数)。
在丁烷转化率为20%~50%(摩尔分数)范围内,顺酐的选择性为70%~80%(摩尔分数),顺酐选择性在丁烷转化率为20%(摩尔分数)时达到最大值,丁烷转化率低于20%(摩尔分数),顺酐选择性反而下降。
这一现象与空气再生后的催化剂表面存在O2-或O-等非选择性氧物种有关,采用在催化剂进入提升管反应器之前,通过一个吹扫段,可吹除去弱吸附的非选择性氧物种,使顺酐选择性提高85%(摩尔分数)•下表为在提升管中补充氧气的反应结果。
可以看出,补充氧气可增加丁烷转化率,但会导致顺酐选择性下降,当原料中氧含量为6%(摩尔分数)时,丁烷转化率增加4.1%(摩尔分数),而顺酐选择性仅下降0.4%(摩尔分数)。
但当氧含量增至16%(摩尔分数)时,丁烷转化率仅增加5.8(摩尔分数),相应的顺酐选择性则降低5.7%(摩尔分数)。
所以补充少量气相氧可明显提高丁烷转化率,同时对选择性的影响也不大,在有的情况下也可作为一种选择。
表在提升管中补充氧气的反应结果•如上所述,丁烷晶格氧选择氧化工艺可显著提高顺酐选择性,但是每千克催化剂在一次Redox循环中只能转化2kg丁烷。
这是因为每转化一个丁烷分子需要7个氧原子。
•CFB提升管丁烷氧化顺酐工艺比同等规模的流化床工艺降低投资20%,减少反应器的催化剂藏量50%。
CFB提升管丁烷氧化制顺酐工艺的经济性不仅取决于选择性和时空产率,而且也取决于催化剂的可逆储氧能力。
该参数决定催化剂的循环量和循环所需的能量消耗。
例如,以每千克催化剂可提供的储氧量能生产1g顺酐计算,一个产量为2万t/a顺酐装置的催化剂循环量为650kg/s,循环所需的能量消耗很大。
VPO催化剂的再氧化过程较慢,如果要使再生器的大小比较合理,催化剂的循环量就要增加到1500~3000kg/s,循环所需能量约占生产能耗的20%~30%。
在这种情况下顺酐的时空产率以提升管和再生器中的催化剂计为0.04~0.08(顺酐/催化剂)h-1, 只以提升管中的催化剂计为0.16~0.24(顺酐/催化剂)h-1。
提高催化剂的可逆性储氧能力,可使CFB 提升管丁烷氧化制顺酐工艺在经济上更加有利。