液态硅橡胶模具设计要点
液体硅橡胶模具胶编制说明(征求意见稿)
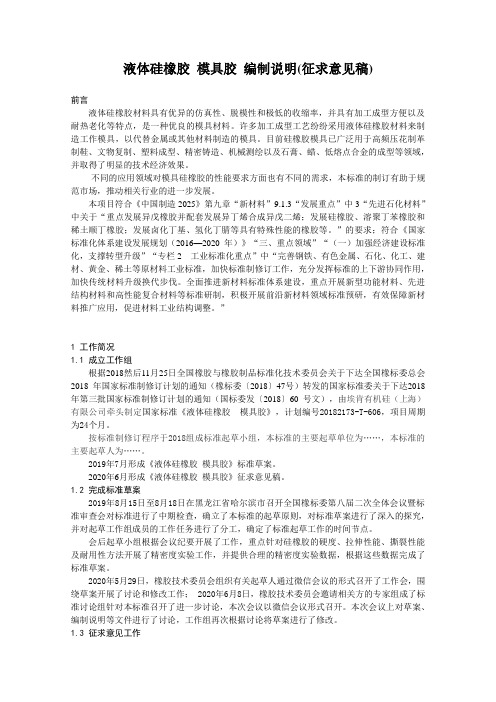
液体硅橡胶模具胶编制说明(征求意见稿)前言液体硅橡胶材料具有优异的仿真性、脱模性和极低的收缩率,并具有加工成型方便以及耐热老化等特点,是一种优良的模具材料。
许多加工成型工艺纷纷采用液体硅橡胶材料来制造工作模具,以代替金属或其他材料制造的模具。
目前硅橡胶模具已广泛用于高频压花制革制鞋、文物复制、塑料成型、精密铸造、机械测绘以及石膏、蜡、低熔点合金的成型等领域,并取得了明显的技术经济效果。
不同的应用领域对模具硅橡胶的性能要求方面也有不同的需求,本标准的制订有助于规范市场,推动相关行业的进一步发展。
本项目符合《中国制造2025》第九章“新材料”9.1.3“发展重点”中3“先进石化材料”中关于“重点发展异戊橡胶并配套发展异丁烯合成异戊二烯;发展硅橡胶、溶聚丁苯橡胶和稀土顺丁橡胶;发展卤化丁基、氢化丁腈等具有特殊性能的橡胶等。
”的要求;符合《国家标准化体系建设发展规划(2016—2020年)》“三、重点领域”“(一)加强经济建设标准化,支撑转型升级”“专栏2工业标准化重点”中“完善钢铁、有色金属、石化、化工、建材、黄金、稀土等原材料工业标准,加快标准制修订工作,充分发挥标准的上下游协同作用,加快传统材料升级换代步伐。
全面推进新材料标准体系建设,重点开展新型功能材料、先进结构材料和高性能复合材料等标准研制,积极开展前沿新材料领域标准预研,有效保障新材料推广应用,促进材料工业结构调整。
”1 工作简况1.1 成立工作组根据2018然后11月25日全国橡胶与橡胶制品标准化技术委员会关于下达全国橡标委总会2018 年国家标准制修订计划的通知(橡标委〔2018〕47号)转发的国家标准委关于下达2018年第三批国家标准制修订计划的通知(国标委发〔2018〕60 号文),由埃肯有机硅(上海)有限公司牵头制定国家标准《液体硅橡胶模具胶》,计划编号20182173-T-606,项目周期为24个月。
按标准制修订程序于2018组成标准起草小组,本标准的主要起草单位为……,本标准的主要起草人为……。
光学液态硅胶模具设计方案解析

善和优化。
年推出的 84 像素矩阵式 ADB 模组,代表着光学液态
2.1
个性化设计和多样化发展。图 1 所示为矩阵式 ADB
据实际经验发现,硅胶件受流动方向和累积公差影
硅胶正式进入汽车照明领域,打开的汽车照明系统的
多针齿模组示意图。
液态硅胶材料的收缩率
目前 LSR 材料的收缩率在 2%~2.5%左右,但是根
热传导率低的材料,如钛合金或者是传导率低的树脂
性和一致性。如图 4 所示,加热丝 A、加热丝 B 与加热
阀针与定模仁接触面必须使用隔热帽,其隔热帽选择
材料。
不同区域所需要的加热丝功率,有效控制模温的稳定
丝 C 属于一根加热丝,但是根据科学热量模拟分析,
加热丝 A-1 和 A-4 的加热功率是加热丝 A-2 和 A-3
针对硅胶阀针,也有着特殊要求,也必须使用含
2.4
1
2.5
模具抽真空气设计
光学硅胶在注塑过程中容易裹挟气泡,所以,模
300MPa 以上的承压的材料,为保证隔热板强度,隔热
具必须增加抽真空工序,配置抽真空泵站,其模具密
0.05~0.1mm,如图 3 所示。
圈槽的边缘需要倒圆角处理,放置模具尖钢割坏密封
板 中 间 需 要 增 加 承 压 块 ,承 压 块 比 耐 磨 板 厚 度 高
silicone mold design stage. The field of automotive lighting has special requirements for silicone
products, such as high-gloss mirror, small warpage deformation and no cape flyedge design
液体硅胶产品设计方案模板
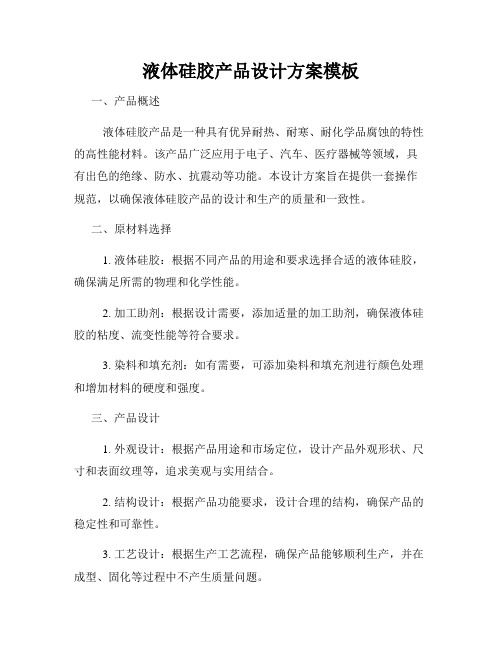
液体硅胶产品设计方案模板一、产品概述液体硅胶产品是一种具有优异耐热、耐寒、耐化学品腐蚀的特性的高性能材料。
该产品广泛应用于电子、汽车、医疗器械等领域,具有出色的绝缘、防水、抗震动等功能。
本设计方案旨在提供一套操作规范,以确保液体硅胶产品的设计和生产的质量和一致性。
二、原材料选择1. 液体硅胶:根据不同产品的用途和要求选择合适的液体硅胶,确保满足所需的物理和化学性能。
2. 加工助剂:根据设计需要,添加适量的加工助剂,确保液体硅胶的粘度、流变性能等符合要求。
3. 染料和填充剂:如有需要,可添加染料和填充剂进行颜色处理和增加材料的硬度和强度。
三、产品设计1. 外观设计:根据产品用途和市场定位,设计产品外观形状、尺寸和表面纹理等,追求美观与实用结合。
2. 结构设计:根据产品功能要求,设计合理的结构,确保产品的稳定性和可靠性。
3. 工艺设计:根据生产工艺流程,确保产品能够顺利生产,并在成型、固化等过程中不产生质量问题。
四、产品制造过程1. 材料配比:按设计要求进行液体硅胶和其他材料的配比,确保各种原材料在适宜的比例下进行混合。
2. 混合:使用搅拌设备对原材料进行充分混合,确保混合均匀,消除气泡等不良现象。
3. 充模:将混合好的液体硅胶倒入模具中,确保模具内部表面涂布均匀。
4. 固化:按设计要求和工艺条件,对液体硅胶进行固化处理,使其在一定时间内达到预期性能。
5. 后处理:将固化后的产品进行去除模具、修整、清洁等后处理工序,确保产品质量。
五、产品质量控制1. 原材料检验:对所采购的液体硅胶和其他原材料进行检测,确保其符合产品质量要求。
2. 生产过程控制:对每个生产环节进行严格的控制和记录,确保产品的一致性和稳定性。
3. 产品检测:对成品产品进行抽样检测,测试其物理性能、化学性能等指标,确保产品质量达标。
4. 不良品处理:对不合格或不良品进行分类、记录和处理,以提高产品质量和生产效率。
六、环境保护1. 废弃物处理:对生产过程中产生的废弃物进行分类、储存和处理,确保环境的卫生和安全。
液态硅胶模具设计要点1.2379

液态硅胶模具设计要点1.2379液态硅胶模具设计要点1.2379液态硅胶模具是一种常用于制作工艺品、玩具、电子产品外壳等产品的模具,它具有耐热、耐磨、精度高等特点,因此在工业生产中得到了广泛的应用。
设计液态硅胶模具时,要考虑到产品的形状、材质、工艺要求等多个方面,以确保最终的模具能够满足生产需要。
在本文中,我将介绍液态硅胶模具设计的要点,并逐步解释每个要点的重要性。
首先,设计液态硅胶模具需要考虑到1.2379材质的选择。
1.2379是一种优质的工具钢,具有较高的硬度、耐磨性和耐热性,非常适合用于制作液态硅胶模具。
这种材质的选择可以确保模具具有足够的耐用性和稳定性,能够承受长时间的使用而不失去精度。
此外,1.2379材质还具有良好的加工性能,可以轻松实现模具的精密加工,从而确保产品的精度和表面质量。
其次,设计液态硅胶模具需要考虑到模具的结构。
模具的结构设计直接影响着产品的成型效果和生产效率。
一般来说,液态硅胶模具的结构应该尽可能简单,以便于脱模和组装。
同时,还需要考虑到产品的具体形状和尺寸,合理确定模具的分型面和开模方式,以确保产品能够完整成型并且易于脱模。
此外,还需要考虑到模具的冷却系统和排气系统的设计,以确保产品的表面质量和减少生产周期。
另外,设计液态硅胶模具还需要考虑到产品的工艺要求。
不同的产品在成型过程中可能需要不同的工艺要求,比如表面光洁度、尺寸精度、壁厚均匀性等。
因此,在设计模具时需要充分了解产品的工艺要求,并根据这些要求合理确定模具的设计参数,比如模腔的尺寸、结构和表面处理方式等。
只有充分考虑产品的工艺要求,才能确保模具能够满足产品的生产需求。
总之,设计液态硅胶模具是一个复杂的工程,需要综合考虑产品的形状、材质、工艺要求等多个方面。
只有在充分了解产品的需求和合理选择材质、设计结构、考虑工艺要求的基础上,才能设计出满足生产需要的液态硅胶模具。
希望本文能够对液态硅胶模具的设计有所帮助。
液体硅橡胶LSR注射成型工艺的设计

液体硅橡胶L S R注射成型工艺的设计seek; pursue; go/search/hanker after; crave; court; woo; go/run after液体硅橡胶LSR注射成型工艺的设计在过去的三到五年里,热固性液体硅橡胶LSR的注塑技术得到了快速的发展.LSR的注塑设计与刚性工程热塑料有着重要的差别,这主要是因为这两种橡胶的物理性质,如低粘度,流变学性质快速固化,剪切变稀性质,以及较高的热膨胀系数等区别较大.由于LSR的粘度较低,因此它在注射成型过程中,即使在注射压力较低的情况下,填充流速也可以较快,但是为了避免空气滞留,对模具通风的要求更加严格.总的来说,现代LSR的快速硫化的循环时间更短某些情况下循环时间不到20秒,为了充分利用这一特性,加工机械、注射成型机以及部件转移系统等必须相互配合,作为一个高度集成的整体运作.冷流道成型现代冷流道体系充分利用了LSR剪切变稀的性质,真正达到了无浪费,无毛边成型.在过去的三到五年里,冷流道模塑在制造业中的优势地位急速上升,并导致橡胶产品的产量增加、废品减少、劳动成本降低等良好的势头.LSR不会在模具中收缩,这一点和热塑性塑料类似.但是由于膨胀系数较高,加热时会发生膨胀,冷却时却仅有微小的收缩.因此,部件通常不能在模具中保持准确的侧边距,只有在表面积较大的空腔中才可以保持.与热流道模塑相似,在冷流道加工中,热固LSR应保持较低温度和可流动性,以确保没有物料的损失.这种加工方法最适用于在清洁的室内环境中生产大小、结构相似的大体积部件.理想模型是在人为因素影响最小的设备中昼夜不停的运转,并逐步增大运转周期日或周.目前所用的冷流道设备有两种基本类型,即闭合系统和开放系统,它们各有优缺点.注射循环中,闭合系统在每一个管道中都采用“开动销”或“针形阀”来控制LSR橡胶的流量.而开口系统则根据注射压力的大小,利用“收缩嘴”和阀门来控制物料的流量.与开口系统相比较,闭合系统最典型的特点是在较低的注射压力下进行注塑.设备中可调控的“节流口”可以对不平衡的分流道以及物料的不同剪切变稀性能进行微调.缺点是对某些给定大小的部件和模具,设备需作额外的调整.开放系统利用通过喷嘴或者阀门的高剪切速率,在注射压力降低时,进行截流.一般情况下,开放系统的空腔填充时间要比闭合系统稍微短一些.开放系统由于分流道和喷嘴较小,空腔密度较高.分流道则要求自然平衡,并与物料本身的流变性能严格匹配.因为开放系统的流道尺寸较小,所以通常不用可调“节流口”,只需普通阀门就可以很好的控制流量,并获得最佳的压力点.分模线设计液体硅橡胶注射成型模具时,首先要考虑分模线的位置,因为分模线内部需设置一些通道,利用这些通道完成通风任务,通风孔必须设置在注射物料最后到达的模具末端.预先考虑以上因素,有助于避免空气的夹带和焊接线边缝强度的损失.由于LSR的粘度低,所以必须确保分模型线的精确度,避免出现毛边.虽然如此,最终产品上的分模线清晰可见.部件的几何形状和分模线的位置还会影响脱膜过程.在部件设计中,轻微的根切有助于确保被塑部件与模具空腔之间坚固的结合在一起.收缩虽然液体硅橡胶在注射成型过程中没有收缩,但是由于硅橡胶具有较高的热膨胀系数,因而在脱膜、冷却后通常会有2%-3%的收缩.确切的收缩数据主要取决于物料配方,但是从加工的观点来看,设计者如果在构思的时候,预先对影响收缩的一些因素有所考虑的话,最后的收缩情况会有所变化,这些因素主要包括加工的温度,物料脱膜的温度,空腔压力等.另外要考虑的是注入口的位置,因为通常物料在流动方向上的收缩要比其垂直方向的收缩来得明显些.另外,部件的尺寸也是一个影响因素,一般来说,部件越厚,收缩越小如果在实际应用中要求二次硫化,则还要考虑额外增加0.5%-0.7%的收缩.通风当模具空腔关闭时,空气滞留在内,随着LSR的注射,空气首先被挤压,接着逐渐被填料赶出空腔,由于LSR的粘度较低,空腔很快被填充.在快速填料过程中,如果空气不能完全被赶出空腔,将会夹带在硫化后的物料中通常表现为沿部件周边一圈白边或是内部光滑的小气泡.典型的通气管道宽1-3mm,深0.004-0.005mm,现已成功应用于生产中.排除空腔滞留空气的最佳方法,是在每一个注射成型循环中,采用抽真空的办法将空腔中滞留空气赶走.就是说,在设计分模线时确保模具密闭,真空泵通过模具开关下面的夹具将所有空腔抽真空.一旦真空度达到预想标准要求,立刻关闭模具,开始注射.还有一种成功应用的方法是,利用调节夹具力度达到赶走空气的目的.制造者在夹具力较低时LSR 填充至空腔的90%-95%,之后再将夹具力度调高,同时避免积压液体硅橡胶溢出,产生毛边.注入口一个合适的加工设计,既希望阀门的痕迹小而坚固,又希望阀门的位置不易察觉,这是非常困难的.但是如果将阀门设置在非临界区域或内表面上,就可以避免很多麻烦,例如前面提到的,利用冷流道系统进行LSR材料的注射成型就可以省去注入口痕迹的消除,从而避免了劳动集约型的生产过程和大量物料的浪费.很多情况下,无注入口设计也将缩短循环时间.如果采用冷流道系统,在热空腔与冷流道之间设置有效的隔离温度是十分重要的.如果分流道太热,物料在注射前就开始固化,而如果冷却太快的话,它会从模具阀门区域吸收过多热量,防碍固化的完成.闭合系统的阀门或是开动销,一般设计为0.5-0.8mm之间,以保证销和它周围流动的物料的活动空间.而开口系统中,喷嘴和阀门通常要小一些0.2-0.5mm,这样可以较好的控制流量.对于低粘度的LSR来讲,若是通过传统注入口注入物料,例如潜伏式阀门或是锥形阀门,那么喂料直径要略小些.注入口直径通常在0.2-0.5mm之间.脱模除非是较特殊的配方,一般固化LSR容易粘在金属表面上,这给脱模带来了一定的困难.虽然如此,目前LSR橡胶的热撕裂强度还是能够满足脱模要求的,在脱模后基本没有损失.应用最为普遍的脱模技术设备,包括分馏柱塔板,推顶销和空气推顶.其他应用较多的方法包括滚筒扫除机,排除塔,和机器人操作.使用推顶系统时,必须使推顶系统保持在相近的公差范围内.如果推顶销和套管之间清除过度,或是元件磨损时间过长,都会引起部件毛边的出现.反锥形或蘑菇形推顶器的接触压比较大,可增进系统的密闭性,因而功效很强.模具材料一般情况下,护圈板都是采用非合金加工钢no.1.1730,DINcodeC45W来制造的.由于模板要暴露在170℃-210℃的高温下,所以应该采用预回火的钢材no.1.2312,DINcode40CrMnMoS86制造,以提高抗冲压性能.具有空腔的模板最好采用耐温性好的弹性热钢为材料.针对像抗油品级这类高填充LSR材料,推荐使用更强硬的材料,例如镀铬钢和粉末金属都在这一应用上有了较大的发展钢.在为研磨性物料制作模具时,要注意使用特别的插件或者其他可替换加工工具,这样元件磨损后可以单独替换,而不必更换整个模具.模具空腔表面的优劣对部件的品质有重要的影响,简单讲,铸好的部件会将模具空腔的原貌准确的复制下来.抛光钢对于透明部件显得十分重要.表面经过处理的钛/镍钢具有很高的抗磨损能力,而PTFE/镍更加容易脱膜.LSR材料在某种程度上具有研磨特性,因而最好不要选择铝质材料.在经济条件允许的情况下,选用最好的金属材料,以便得到更好的相容性,同时便于由粗产品加工为最终产品.温度控制LSR成型工艺中,典型的加热方式是电加热,通常采用电热丝加热器、加热管或者加热盘.LSR的一次型固化过程中,模具内温度的均匀分配是非常重要的.在大型模具中,最经济的加热方法是“油温控制法”.用绝缘板包裹模具,也有助于减少热损失.如果表面温度下降过快,会使物料的固化速度降低,不断抑制部件的释放,影响部件的品质.加热器与分模线之间保留一段距离,可以大大避免模板的弯曲与变形,但是会使铸好的部件出现毛边.如果模具是为冷流道系统设计的,那么在冷热界面上必须有适合的隔离,这是必不可少的.像3.7165TiAl6V4这样的钛合金,相比其他钢材料来说,其热导性能差,因此是冷热隔离的良好材料.对于整体模具加热体系,应该在模具与模板之间放置绝缘层,把热损失降低到最小.模拟设计LSR分流道系统中,LSR将均匀填充所有的模具空腔,在这样的一个体系中,LSR分流道规划的平衡显得十分重要.采用电脑物流动力学模拟软件来设计分流道阀门和通风口,可以帮助模具的改进,避免反复试错法的高消耗.其实验结果可以用填充研究来论证,但是,正确的模拟要求工程师对所注塑的LSR配方的机械反应性能了如指掌.利用有限元分析法进行部件设计的实验,可忽略高应力区.小结予以恰当的设计和规划,LSR材料的注射成型是一项经济收益好,操作相对简洁的生产工艺.充分理解注射成型与流程设计的原则,制造者即可在避免出现问题的同时,进行高效生产,相信LSR出色的空腔填充性能和快速硫化特性,必将带来高品质、高产出的工业效应.来源:机电之家·机电行业电子商务平台。
液体硅橡胶模具设计原则
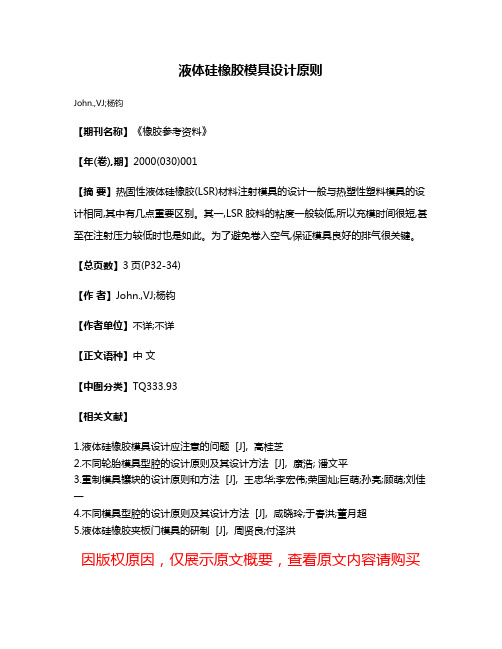
液体硅橡胶模具设计原则
John.,VJ;杨钧
【期刊名称】《橡胶参考资料》
【年(卷),期】2000(030)001
【摘要】热固性液体硅橡胶(LSR)材料注射模具的设计一般与热塑性塑料模具的设计相同,其中有几点重要区别。
其一,LSR胶料的粘度一般较低,所以充模时间很短,甚至在注射压力较低时也是如此。
为了避免卷入空气,保证模具良好的排气很关键。
【总页数】3页(P32-34)
【作者】John.,VJ;杨钧
【作者单位】不详;不详
【正文语种】中文
【中图分类】TQ333.93
【相关文献】
1.液体硅橡胶模具设计应注意的问题 [J], 高桂芝
2.不同轮胎模具型腔的设计原则及其设计方法 [J], 康浩; 潘文平
3.重制模具镶块的设计原则和方法 [J], 王忠华;李宏伟;荣国灿;巨萌;孙亮;顾萌;刘佳一
4.不同模具型腔的设计原则及其设计方法 [J], 咸晓玲;于春洪;董月超
5.液体硅橡胶夹板门模具的研制 [J], 周贤良;付泽洪
因版权原因,仅展示原文概要,查看原文内容请购买。
液态硅橡胶模具设计的七大要点

液态硅橡胶模具设计的七大要点热固性液态硅橡胶(LSR)注压模具的结构,总的来说跟热塑性胶料所用的模具结构相似,但也有不少显著差别。
例如,LSR胶料一般粘度较低,因而充模时间很短,即使在很低的注射压力下也是如此。
为了避免空气滞留,在模具中设置良好的排气装置是至关重要的。
另外,LSR胶料在模具内不会像热塑性胶料那样收缩,它们往往遇热膨胀,遇冷轻微收缩。
因而,其制品并不总是如所期望的那样留在模具的凸面上,而是滞留在表面积较大的模腔内。
1 收缩率虽然LSR并不会在模内收缩,但它们在脱模和冷却后,常常会收缩2.5%-3%。
至于究竟收缩多少,在一定程度上取决于该胶料的配方。
不过,从模具角度考虑,收缩率可能受到几种因素的影响,其中包括模具的温度、胶料脱模时的温度,以及模腔内的压力和胶料随后的压缩情况。
注射点的位置也值得斟酌,因为胶料流动方向的收缩率通常比与胶料垂直流动方向的收缩率大一些。
制品的外形尺寸对其收缩率也有影响,较厚的制品的收缩率一般要比较薄者小。
如果需进行二次硫化,则可能再额外地收缩 2 分型线确定分型线的位置是设计硅橡胶注压模具的前几个步骤之一。
排气主要是通过位于分型线上的槽沟来实现的,这样的槽沟必经处在注压胶料最后到达的区域内。
这样有助于避免内部产生气泡和降低胶接处的强度损失。
由于LSR粘度较低,分型线必须精确,以免造成溢胶。
即便如此在定型的制品上还常能看见分型线。
脱模受制品的几何尺寸和分型面位置的影响。
将制品设计成稍有倒角,有助于保证制品对所需的另一半模腔有一致的亲合力。
3 排气随着LSR的注入,滞留在模腔内的空气在模具闭合时被压缩,然后随着充模过程而通过通气槽沟被排出。
空气如果不能完全排出,就会滞留在胶料内(这样往往会造成制品部分露出白边)。
通气槽沟一般宽度为lmm-3mm,深度为0.004mm-0.005mm。
在模具内抽真空可创造最佳的排气效果。
这是通过在分型线上设计一个垫圈,并用真空泵迅速将所有的模腔抽成真空来实现的。
液态模具基础知识
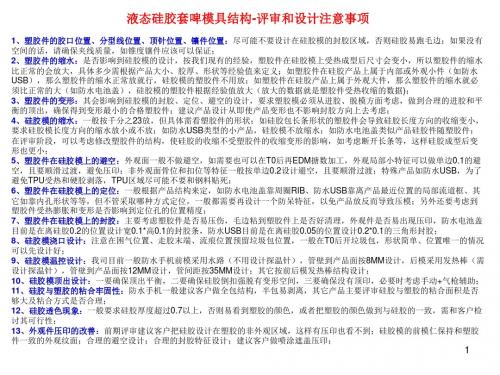
2
液态硅胶设计要点
液态硅胶模与塑胶模的区别
1、成型原理对比: 与塑胶模最大的不同是冷却入水(即入水系统需冷却),模仁加热固化成型(即成型 部分需加热), 刚好与塑胶模成型原理相反; 2、模具结构对比: 流道板和唧嘴走冷水,A板和B板放加热棒(也可以用油温),建议直接模仁设计发热 管,避免 温度损失过快,其它同塑胶模结构一致; 一、唧嘴走冷水,与热嘴原理相反; 二、前后模仁加热,与塑胶模走冷水相反; 三、A板和B板底部加隔热板,防止热传递; 四、进胶口为针点状和翼状,流道板分流道全部密封; 五、顶出多为推块、推板顶出或气枪辅助手动取产品,下不了顶针,因为顶针位易跑批锋,加不了 自拆,但模具温度较高,手动取产品不易;顶出行程注意不能太少,一般高于分型面20MM, 利于清理垃圾。 六、产品有披锋可采用CNC锣自拆或EDM(同固态相同,个人不建议使用); 七、一般不设计镶件结构,镶件处易跑批锋,如果非要镶,可以设计斜度紧配避免或设计顶块加 自拆解决(个人建议); 八、分型面尽可能设计平面,磨床加工,否则CNC加工弧面封胶,易导致批锋,需设计自拆(个人 认为液态硅胶一般不设计自拆); 九、设计完成后检查出模角度,有些虽然考虑到加工没有问题,但模仿顶出后会发现有干涉,所以 倒扣位需加工和出模方式都要考量; 十、排气槽深度不要超过0.005MM.否则会有毛边产生; 十一、了解客户对产品要求,一般选用液态注射对毛边和气纹等都是有很高要求,高光高透和胶料 小于40度瑕疵最易显现; 十二、产品直身可以脱模,即可以不用脱模角度; 3
液态硅胶设计要点
收缩率的定义
1、收缩一般为2.3%左右,与原材料性能及硬度、 成型温度、产品大小有关;一般 硬度越硬,缩水越小;如固态硅胶缩水一般为3.2 %或2.8 %,手机护套放
- 1、下载文档前请自行甄别文档内容的完整性,平台不提供额外的编辑、内容补充、找答案等附加服务。
- 2、"仅部分预览"的文档,不可在线预览部分如存在完整性等问题,可反馈申请退款(可完整预览的文档不适用该条件!)。
- 3、如文档侵犯您的权益,请联系客服反馈,我们会尽快为您处理(人工客服工作时间:9:00-18:30)。
液态硅橡胶模具设计要点
热固性液态(LSR)注压模具的结构,总的来说跟热塑性胶料所用的模具结构相似,但也有不少显著差别。
例如,LSR胶料一般粘度较低,因而充模时间很短,即使在很低的注射压力下也是如此。
为了避免空气滞留,在模具中设置良好的排气装置是至关重要的。
另外,LSR胶料在模具内不会像热塑性胶料那样收缩,它们往往遇热膨胀,遇冷轻微收缩。
因而,其制品并不总是如所期望的那样留在模具的凸面上,而是滞留在表面积较大的模腔内。
1 收缩率
虽然LSR并不会在模内收缩,但它们在脱模和冷却后,常常会收缩2.5%-3%。
至于究竟收缩多少,在一定程度上取决于该胶料的配方。
不过,从模具角度考虑,收缩率可能受到几种因素的影响,其中包括模具的温度、胶料脱模时的温度,以及模腔内的压力和胶料随后的压缩情况。
注射点的位置也值得斟酌,因为胶料流动方向的收缩率通常比与胶料垂直流动方向的收缩率大一些。
制品的外形尺寸对其收缩率也有影响,较厚的制品的收缩率一般要比较薄者小。
如果需进行二次硫化,则可能再额外地收缩0.5%-0.7%。
2 分型线
确定分型线的位置是设计注压模具的前几个步骤之一。
排气主要是通过位于分型线上的槽沟来实现的,这样的槽沟必经处在注压胶
料最后到达的区域内。
这样有助于避免内部产生气泡和降低胶接处的强度损失。
由于LSR粘度较低,分型线必须精确,以免造成溢胶。
即便如此在定型的制品上还常能看见分型线。
脱模受制品的几何尺寸和分型面位置的影响。
将制品设计成稍有倒角,有助于保证制品对所需的另一半模腔有一致的亲合力。
3 排气
随着LSR的注入,滞留在模腔内的空气在模具闭合时被压缩,然后随着充模过程而通过通气槽沟被排出。
空气如果不能完全排出,就会滞留在胶料内(这样往往会造成制品部分露出白边)。
通气槽沟一般宽度为lmm-3mm,深度为0.004mm-0.005mm。
在模具内抽真空可创造最佳的排气效果。
这是通过在分型线上设计一个垫圈,并用真空泵迅速将所有的模腔抽成真空来实现的。
一旦真空达到额定的程度,模具即完全闭合,开始注压。
有些注射模压设备容许在可变化的闭合力下操作,这使加工者可以在低压下闭合模具,直到模腔的90%-95%被LSR充满(使空气更容易排出),然后切换成较高的闭合力,以免硅橡胶膨胀而发生溢胶。
4 注射点
模压LSR时采用冷流道系统。
可最大限度地发挥这种胶料的优点,并可将生产效率提升至最高限度。
以这么一种方式来加工制品,就不必去掉注胶道,从而避免增加作业的劳动强度,有时还可避免材料的大量浪费。
在许多情况下,无注胶道结构还可缩短操作时间。
胶料注射嘴由针形阀来作正向流控制,目前许多制造厂商可将带气控开关的注射嘴作为标准设备提供,并能将其设置在模具内的各个部位。
有些模具制造商专门研制出了一种开放式冷流道系统,其体积非常之小,以致要在极其有限的模具空间内设置多个注射点(进而充满了整个模腔)。
这项技术在无需使胶注口分离的情况下,使大量生产优质硅橡胶制品成为可能。
如果采用冷流道系统,那么重要的是在热的模腔和冷的流道之间形成有效的温度间隔。
若流道太热,胶料可能在注射前便开始硫化。
但是若冷却得太急,它就会从模具的浇口区吸收太多的热,导致不能完全硫化。
对于用常规的注浇道(如潜入式浇道和锥形浇道)注射的制品,适宜采用小直径注胶口加料(加料口直径通常为0.2mm-0.5mm)来浇注。
低粘度的LSR胶料如同热塑性胶料一样,平衡流道系统显得十分重要,只有这样,所有的模腔才会被胶料均匀地注满。
利用设计流道系统的模拟软件,可以大大简化模具的研制过程,并通过充模试验证明其有效性。
5 脱模
通过硫化的液体硅橡胶容易粘附在金属的表面,制品的柔韧性会使其脱模困难。
而LSR拥有的高温撕裂强度能使之在一般条件下脱模,即使较大的制品也不会被损伤。
最常见的脱模技术包括脱模板脱模、脱模销脱模和气力脱模。
其它常见的技术有辊筒刮模、导出板脱模和自动御模。
使用脱模系统时,必须使其保持在高精度范围内。
若顶推销与导销套之间的间隙太大,或者部件因长时间磨损而间隙变大,就可能造成溢胶。
倒锥形或蘑菇形顶推销的效果甚佳因为它允许采用较大的接触压力,便于改善密封性育旨。
6 模具材料
模具托板常用非合金工具钢(no.1.1730,DIN code C45W)制成,对干需承受170℃-210℃高温的模具托板,考虑到抗冲击性,应当用预回火钢(no.1.2312,DIN code 40 CrMn-M oS 8 6)制造。
对于设置模腔的模具托板,应采用经氮化或回火热处理的乙具钢制造,以确保其耐高温性能。
对填充量高的LSR,如耐油级LSR,推荐采用硬度更高的材料来制造模具,例如光亮的镀铬钢或为此用途专门研制的粉末金属
(no.1.2379,DIN code X 155 CrVMo121)。
设计高磨损材料模具时,应该将那些承受高磨擦的部件设计成可更换的形成,这样就不用更换整个模具了。
模腔内表面对制品的光洁度影响甚大。
最明显的是定型制品将同模腔表面完全吻合。
透明制品用模具应采用抛光的钢材制造。
经过表面处理的钦/镍钢耐磨性极高,而聚四氟乙烯(PTFE)/镍则能使脱模更加容易。
7 温度控制
一般来说,LSR的模压以采用电加热方式为宜,通常是采用带形电热器、筒形加热器或加热板加热。
关键的是要使整个模具的温度场均匀
分布,以促进LSR均匀固化。
在大型模具上,是经济有效的加热法当推油温控制加热。
用绝热板包覆模具有利于减少热损失。
热模任何部位的不适宜都可能使之在各操作工序之间遭受大的温度波动,或造成跑气。
如果表面温度降得过低,胶料固化速度就会减慢,这往往会使制品无法脱模,引起质量问题。
加热器和分型线之间应保持一定的距离,以防止模板弯翘变形,在成品上形成溢胶毛边。
若设计冷流道系统的模具,热端和冷端之间必须确保完全隔开。
可以采用特制的钦合金(如3.7165[TiA16V4])制造,这是因为与别的钢材相比,其导热性低得多。
对于一个整体的模具加热系统而言,隔热板应设置在模具与模具托板之间,以使热损失最小。
恰当的设计和构思可确保LSR注压成型,在此模具十分重要。
上述模具设计原则旨在使胶料充满模腔,缩短固化时间,成品质量上乘,产量高,从而使硅橡胶加工者获得良好的经济效益。