8D实例-后桥漏油8D整改报告
全顺动力转向器漏油8D整改

全顺动力转向器漏油8D整改一、问题背景全顺汽车作为一款广受欢迎的商用车型,其动力转向器的性能和可靠性至关重要。
然而,近期我们在生产和售后环节中发现,部分全顺动力转向器存在漏油的问题,这不仅影响了车辆的正常使用,也对用户的驾驶体验和安全造成了潜在威胁。
为了彻底解决这一问题,提高产品质量,我们启动了 8D 整改流程。
二、8D 整改小组成立为了确保整改工作的顺利进行,我们成立了专门的 8D 整改小组,成员涵盖了设计、工艺、质量、生产等多个部门的专业人员。
小组成员分工明确,各自负责相关领域的问题调查和整改措施的制定与实施。
三、问题描述经过对漏油的全顺动力转向器进行详细的检查和分析,我们发现漏油问题主要集中在以下几个部位:1、油封处:油封老化、磨损或安装不当,导致密封失效,油液从油封处渗漏。
2、油管连接处:油管接头松动、密封垫圈损坏或安装不到位,造成油液泄漏。
3、转向器壳体:壳体存在铸造缺陷或加工精度不足,导致油液从壳体缝隙中渗出。
四、临时措施在制定根本解决措施之前,我们首先采取了一系列临时措施,以减少问题的影响和损失:1、对库存的全顺动力转向器进行全面检查,将存在漏油风险的产品进行隔离和标识,防止其流入市场。
2、对于已经销售出去的车辆,通知用户及时回店进行检查和维修,为用户免费更换有问题的零部件。
3、加强生产过程中的检验环节,增加抽检频率,及时发现和处理潜在的漏油问题。
五、原因分析通过对漏油问题的深入调查和分析,我们总结出以下几个可能的原因:1、设计方面油封的选型不合理,其材质和结构不能满足长期使用的要求。
油管接头的设计存在缺陷,连接方式不够可靠,容易松动。
2、原材料和零部件质量油封和密封垫圈的供应商提供的产品质量不稳定,部分产品存在尺寸偏差和材质缺陷。
转向器壳体的铸造材料和工艺不符合要求,导致壳体强度和密封性不足。
3、生产工艺油封和油管的安装工艺不规范,操作人员未能按照标准作业流程进行操作,导致安装不到位。
8D整改报告

Verifier
日期
Date
a.已与委外供应商建立订单系统,并有编制和批准;
b.已开始制订交付计划给供应商,而且有供应商的签字保证,月底进行绩效考核评估。
7.Systematicpreventive actions/系统预防措施
责任人
Person in charge
完成日期
Finish date
责任人
Person in charge
完成日期
Finish date
a.在接收到工程变更通知时,首先由项目负责人按工程变更控制文件流程组织相应人员进行评审分析,填写工程更改通知单和评审文件,保留记录。
8.Appendices/附件清单
附件一:工程更改控制工作指导书
附件二:工程变更管理培训记录
8D Report /8D报告
3.Correctiveactions/遏止措施
责任人
Person in charge
完成日期
Finish date
由项目负责人立即组织小组,对该变更完成后的事项(工艺文件,控制文件)进行检查,并对变更过程中沟通的邮件打印存档。
Verification of the effectiveness of corrective actions/遏止措施效果验证
8D Report /8D报告
问题来源
Question Source
发现日期
FoundDate
编 号
No.
01
1.Problem Description/问题描述:
xx年9月21日来自上海通用变更EWO 1736886,组织缺少证据表明工程变更实施了评审和评价了库存品的影响。
2.Member of group/组成小组:
8d改善报告范文

8d改善报告范文以下是为您生成的一篇关于“8D 改善报告范文”的作文,尽量满足您的需求,内容可能不够专业和准确,仅供参考。
---#在我们的生产线上,最近出现了一个让人头疼的问题——产品质量出现了波动。
这可把我们整个团队都给急坏了,要知道,质量可是我们的生命线啊!于是,一场轰轰烈烈的 8D 改善行动就此展开。
**一、问题描述**这批产品在质检环节中被发现存在外观瑕疵、尺寸偏差以及性能不稳定等多种问题。
客户那边已经开始抱怨了,说我们的产品影响了他们的生产进度,这压力可真是山大呀!就拿外观瑕疵来说吧,有的产品表面有明显的划痕,就像是被小猫小狗抓过一样;还有的产品颜色不均匀,一块深一块浅的,看起来特别别扭。
尺寸偏差也很让人头疼,本该是标准的长度和宽度,结果有的大了一圈,有的小了一截,这怎么能行呢?性能方面就更不用说了,部分产品在测试的时候,一会儿正常,一会儿又出故障,简直就像个任性的小孩子,让人捉摸不透。
**二、小组成立**为了解决这个问题,我们迅速成立了 8D 改善小组。
小组里有生产线上的工人师傅老张、老李,有负责质量检测的小王,有技术部门的专家刘工,还有我这个负责统筹协调的小组长。
大家虽然来自不同的岗位,但都怀着一颗要把问题解决的心,聚到了一起。
老张是个经验丰富的老师傅,平时话不多,但一说起生产的事儿,那可是头头是道。
老李呢,干活儿特别麻利,而且点子多。
小王虽然年轻,但工作认真负责,眼睛里容不得一点沙子。
刘工就更不用说了,技术方面的权威,大家都对他充满了期待。
**三、临时措施**在找到根本原因之前,我们先采取了一些临时措施,尽量减少问题的影响。
首先,对已经生产出来的有问题的产品进行隔离,防止它们混入合格品中。
然后,加强了质检的频率和力度,确保每一个出厂的产品都经过严格的检验。
同时,通知客户我们正在积极解决问题,并承诺会尽快给出一个满意的解决方案。
这期间可真是忙得脚不沾地啊!小王每天都在质检室里加班加点,眼睛都快看花了。
8D报告范例范文

8D报告范例范文本报告是针对公司产品出现质量问题的8D报告,旨在通过8D方法分析问题、找出原因、并提出解决方案以改善产品质量。
下面是详细的报告内容。
1.问题描述产品在正常使用过程中出现漏油现象,导致产品性能下降,严重影响用户体验。
经过初步调查,问题可能来自产品密封件的设计或制造方面。
2.8D步骤2.1班组成立在得知问题后,为了高效解决问题,我们成立了一支专门的班组,负责分析问题、实施改进措施以及跟踪改进效果。
班组成员包括:质量工程师、产品设计师、制造工程师、供应链专员等。
2.2执行D1:构建团队、定义问题、描述过程团队成员召开会议,明确问题:产品漏油,影响性能。
详细描述漏油过程,以便后续的问题分析。
2.3执行D2:搜集数据通过实地走访、访谈用户以及产品测试,我们收集了大量数据。
数据显示,产品漏油现象主要发生在高温环境下,并且漏油量与使用时间呈正相关。
2.4执行D3:定义原因基于收集到的数据,我们确定可能的原因有:密封件材料质量不良、制造过程中的误差以及设计缺陷等。
通过进一步分析,我们确定其中一个可能的原因是密封件材料质量不良。
2.5执行D4:制定临时对策2.6执行D5:根本原因分析为了找到根本原因,我们对生产过程和所有可能影响密封件质量的环节进行了深入的分析和调查。
最终,我们发现密封件工艺中存在的一道环节,操作规范不够严谨,导致部分产品的密封件未能完全发挥效果。
2.7执行D6:制定永久对策基于根本原因分析,我们制定了一套完善的永久对策。
首先,我们修订了密封件工艺的操作手册,明确每个环节的操作标准。
其次,我们进行员工培训,提高操作人员的技能和质量意识。
最后,我们与供应商合作,共同制定更严格的材料质量标准。
2.8执行D7:验证效果在实施永久对策后,我们对受影响的产品进行了再次测试。
测试结果显示,产品漏油现象明显减少,产品性能得到有效改善。
2.9执行D8:预防措施为了防止类似问题再次出现,我们总结了经验教训,并制定了一系列的预防措施。
8d报告案例范文

8D报告案例:汽车制造业中的质量问题解决1. 案例背景汽车制造业是一个竞争激烈的行业,汽车制造商需要不断提高产品质量以满足市场需求。
然而,由于生产过程中的各种原因,质量问题时常出现。
这就需要制造商采取措施解决问题,以降低不良率,提高产品质量。
本案例以某汽车制造商的一个具体质量问题为背景,展示了如何使用8D报告方法解决质量问题。
2. 案例过程2.1 问题发现在该汽车制造商的生产线上,某一型号的汽车在组装过程中出现了一定比例的漏油问题。
漏油问题不仅影响了汽车的外观和品质,还可能导致机械故障,给消费者带来不便和安全隐患。
因此,该问题被认为是一个严重的质量问题,需要尽快解决。
2.2 问题分析制造商成立了一个专门的团队来分析漏油问题。
团队首先进行了现场调查,观察了漏油现象发生的具体情况,并收集了相关数据和样本。
通过对数据和样本的分析,团队发现漏油问题主要发生在某一特定的组装工序中。
进一步的分析表明,问题可能是由于该工序使用的密封胶出现了质量问题,导致密封不完全,从而引起漏油。
2.3 制定解决方案基于问题分析的结果,团队制定了以下解决方案:1.更换密封胶供应商:通过与多家供应商的沟通和评估,选择一家质量可靠的密封胶供应商,以确保密封胶的质量稳定。
2.优化工艺参数:对组装工序的工艺参数进行优化,确保密封胶的使用量和施工方式合理,从而提高密封效果。
3.强化质量控制:加强对组装工序的质量控制,建立更严格的检查和测试流程,确保每辆汽车的密封质量符合标准。
2.4 实施解决方案制造商在生产线上实施了以上的解决方案。
他们与新的密封胶供应商建立了合作关系,并对工艺参数进行了调整。
此外,他们还培训了员工,提高了他们对质量控制的意识和能力。
2.5 结果评估在实施解决方案后,制造商对漏油问题进行了跟踪和评估。
经过一段时间的观察和测试,他们发现漏油问题得到了显著改善。
对于经过改进的生产线,漏油问题的发生率大大降低,质量得到了有效控制。
突出8D解决方案的报告案例

突出8D解决方案的报告案例1. 引言在当今竞争激烈的商业环境中,为了提供高质量的产品和服务,企业必须能够快速响应和解决各种问题。
其中,8D(8 Disciplines)解决方案是一种经典的问题解决方法,它提供了一套系统性的步骤和工具,帮助企业有效地解决各种问题,并确保问题不再重复发生。
本报告案例将以某家汽车制造公司的质量问题为例,详细介绍了如何运用8D解决方案,从而推动问题解决并提高产品质量。
2. 问题描述某汽车制造公司最近发现了一批汽车发动机出现了质量问题,导致了多起车辆故障甚至安全事故。
经初步调查发现,这一问题主要源于发动机的燃烧室密封性不足,致使燃气泄漏,进而影响了发动机的性能和耐久性。
3. 8D解决方案的步骤步骤1:组建小组首先,我们组建了一个由涉及到这一问题的相关部门和专业人员组成的小组,他们包括工程师、技术员、生产人员和质量控制员,以确保具有全面的技术和业务知识。
步骤2:问题描述小组成员共同收集了相关数据和信息,对问题进行了详细描述和分析。
我们确定了发动机燃烧室密封性不足是这一问题的根本原因。
步骤3:制定临时措施为了尽快解决问题和减少可能的损失,我们制定了一系列的临时措施。
这些措施包括对受影响的发动机进行检查和修复,以及对生产线进行调整和优化,以确保新生产的发动机质量符合要求。
步骤4:根本原因分析小组成员对发动机燃烧室密封性不足的根本原因进行了深入分析。
经过多次测试和试验,我们发现了设计上的问题,导致了密封件材料的选择错误,无法满足密封要求。
步骤5:制定长期措施基于根本原因分析的结果,我们制定了一系列的长期措施。
这些措施包括重新设计发动机的密封部件,更换合适的材料,并对生产工艺进行调整和优化,以确保密封性能的稳定和可靠。
步骤6:验证措施的有效性我们对重新设计的发动机密封部件进行了测试和验证。
测试结果表明,新的设计和材料显著提高了发动机的密封性能和耐久性。
步骤7:预防措施为了避免类似的问题再次发生,我们制定了一项预防措施计划。
8D改善报告范文

8D改善报告范文一、引言8D改善法是一种全面系统的质量改进方法,通过八个步骤的循环反馈和持续改进,帮助企业解决问题和提高效率。
本报告将介绍我在执行8D改善过程中所遇到的问题和改进措施。
二、背景在上个季度的质量分析中,我所负责的产品出现了较高的不合格率。
经过深入调查和分析,我确定了问题的性质和原因,并采取了8D改善法来解决这些问题。
三、8D改善步骤1.成立团队:我组建了一个由各部门的专家组成的改善小组,包括生产、质量、工程等部门的成员。
2.描述问题:我们仔细分析了问题的性质、出现的频率和影响范围,并制定了一个详细的问题描述。
3.立即行动:我们采取了紧急措施,包括停机检查,对原材料和生产设备进行全面检测和整理等,以防止问题进一步扩大。
4.确定根本原因:通过对问题的原因进行深入调查和分析,我们确认了生产设备的故障和操作员的技术技能不足是导致问题的根本原因。
5.提出纠正措施:我们采取了多个纠正措施,包括修复设备,提高操作员的培训和技能水平,实施严格的工艺控制等。
6.核实效果:我们对纠正措施进行了实施和监控,并定期进行效果核实,确保问题得到解决和改进。
7.预防措施:为了预防类似问题的再次发生,我们对相关流程和设备进行了改进和优化,并增加了更严格的质量控制措施。
8.应用经验:我们总结了改善过程中的经验教训,并将其应用到其他产品和工艺中,以促进整个企业的质量改进。
四、改善效果通过以上的改善措施,我们有效地降低了不合格率,并提高了产品的质量和交付能力。
原本每天都有几批次不合格产品,现在已经几乎没有不合格产品的产生了。
此外,员工的工作效率也有了明显的提升,避免了因处理不合格产品而浪费的时间和资源。
五、改善经验在执行8D改善过程中,我们总结了以下几点经验,希望能对其他企业的改善工作有所帮助:1.团队合作:组建一个多部门的改善小组,充分利用每个成员的专业知识和经验,共同解决问题。
2.快速行动:问题一旦发现,应立即采取紧急措施,避免问题进一步扩大或恶化。
实例-8D改善措施报告
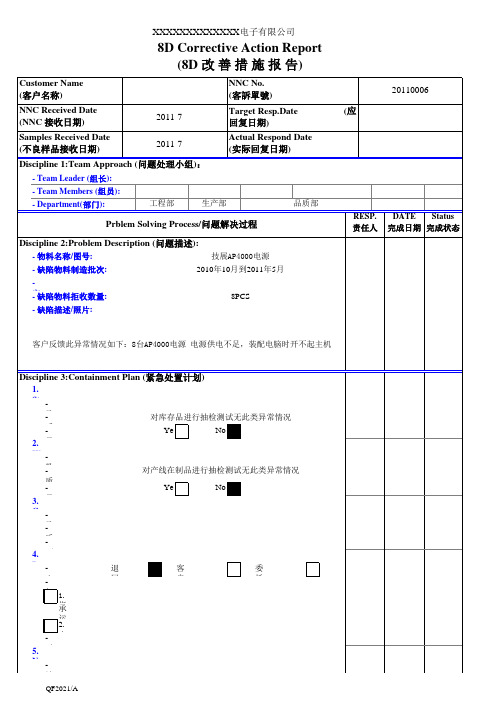
XXXXXXXXXXXXX电子有限公司
8D Corrective Action Report
(8D 改善措施报告)
- 送货数量:
- 原定的交期是否能按时完成?Yes No
Discipline 4:Describe The Root Cause (根本原因描述):
1. Root Cause (根本原因):
客户投诉的8PCS电源封条编码分别为:① 8429566(2011年1月)②7340100(2011年3月的)③6991373(2010年10月)④ 7240224(2011年4月)⑤7371092(2011年3月)⑥7061714(2010年10月)⑦
6876661(2010年7月)⑧509809(2011年5月)
对以上8台电源进行全面测试,结果如下:①-⑥的6台电源均为好机高压、负载测试、线材测试均正常,⑦⑧(封条编码:6876661和
509809)2台电源测试时有敲保护现象
进一步分析结果如下:⑦6876661电源R05与IC的10脚相碰
⑧509809电源R05与R22脚相碰造成电源敲机测试时出现敲保护现象
测试、异常原因截图见附件1,对6台良品电源进行装机老化测试,老化时间为4小时,老化后电源均为良品,老化情况见附件2/sheet1
⑧509809电源R05与
R22脚相碰
⑦6876661电源R05
与IC的10脚相碰。
- 1、下载文档前请自行甄别文档内容的完整性,平台不提供额外的编辑、内容补充、找答案等附加服务。
- 2、"仅部分预览"的文档,不可在线预览部分如存在完整性等问题,可反馈申请退款(可完整预览的文档不适用该条件!)。
- 3、如文档侵犯您的权益,请联系客服反馈,我们会尽快为您处理(人工客服工作时间:9:00-18:30)。
PPM < LSL PPM > USL PPM Total
主动齿轮凸缘、桥壳轴头表面粗糙度工序稳定
4、装配油封时,油封装歪
设计专用油封压装套筒,用油压机压 装,避免人为因素造成油封装歪,专 用压油封压装套筒增加了导向装置, 确保油封压装正确。 装配主减全部在专用装配线上装配, 减少人为因素装配的装配失误。 完成时间:2003/5/25
USL
Within Overall
Potential (Within) Capability Cp CPU CPL Cpk Cpm Overall Capability Pp PPU PPL Ppk 1.89 2.32 1.45 1.45 2.34 2.89 1.80 1.80 *
0.0
0.1
0.2
后桥漏油8D整改报告
VRT1小组成员
组长: XXX——江铃底盘公司质保部主管 组员: XXX——江铃底盘公司质保部长 XXX——江铃底盘油封采购员 XXX——江铃底盘主动齿轮凸缘工艺员 XXX——江铃底盘装配车间主任 XXX——江铃底盘涂装质管员 XXX——江铃底盘涂装工艺员
组内分工
USL
Within Overall
Potential (Within) Capability Cp CPU CPL Cpk Cpm Overall Capability Pp PPU PPL Ppk 2.24 1.49 2.99 1.49 2.42 1.61 3.23 1.61 *
0.0
0.1
Observed Performance
油封 漏油
料
法
环
确定并验证根本原因
影响后桥油封漏油的原因有: 油封质量达不到要求; 油封主副唇口之间锂基润滑脂过多,工作时锂 基润滑脂变稀,易产生漏油假相; 油封装配表面粗糙度低或端部有毛刺; 压装油封时油封压歪; 油封轴颈加工方法不对。
选择和验证永久性措施
1、油封质量达不到要求
向供应商提出明确的油封质量性能指标, 并提供检验报告,采用进口油封; 定期提供台架试验报告,并监督供应商进 行试验。 完成时间:2003/6/25
2003年6月30日对桥壳轴头检查表面粗糙度
Process Capability Analysis for BJ1046
LSL
Process Data USL Target LSL Mean Sample N StDev (Within) StDev (Overall) 0.800 * 0.000 0.307 30 0.0568599 0.0706879
结合面漏油 20%
主动齿轮油 封漏油 60%
原因分析
寻找根本原因
人
操作者责任心
油封装配时 同心度不好
机
油封压具不当
压装时油 清洁度差 油封质量达 封压歪 主动齿轮凸缘 不到要求 油封唇口润 油封外圆密 表面粗糙度低 滑脂过多 封胶不均匀 主动齿轮凸缘 桥壳轴端 油封轴颈表面 端面有毛刺 部有毛刺 加工方法不对 桥壳轴头油封 表面粗糙度低
0.2
Exp. "Within" Performance 0.00 0.00 0.00 PPM < LSL PPM > USL PPM Total 0.00 0.67 0.67
0.3
0.4
Exp. "Overall" Performance PPM < LSL PPM > USL PPM Total 0.00 3.90 3.90
许建荣——负责小组工作安排与协调 胡义华——负责改进效果的跟踪、考核 罗晓宇——负责外配件油封质量的采购、质量改进 陈田兵——负责主动齿轮凸缘工艺的修订与更改,负 责金工车间质量控制 黄 浩——负责装配质量的控制 周晓晶——负责装配质量的跟踪、 陈 伟——负责装配工艺的修订、更换
问题说明
0.3
0.4
0.5
0.6
0.7
0.8
Observed Performance PPM < LSL PPM > USL PPM Total 0.00 0.00 0.00
Exp. "Within" Performance PPM < LSL PPM > USL PPM Total 0.03 0.00 0.03
故障描述:主动齿轮油封漏油故障12起, 占总故障的19.4%,其它漏油故障8起, 占总故障的12.9%。后桥漏油的故障率占 总故障的32.3%,仅次于后桥异响的故障 率.
改进目标:杜绝焊缝漏油、平面漏油;油封漏 油故障率降至4‰以下。
后桥漏油故障分析
轮毂油封漏油 10% 焊缝漏油 10%
后格漏油故障分布
实施永久性措施
将上述措施全部纳入控制计划,实施永 久控制措施。 完成时间:2003/07/15
Exp. "Overall" Performance PPM < LSL PPM > USL PPM Total 7.0
Process Capability Analysis for 凸缘
LSL
Process Data USL Target LSL Mean Sample N StDev (Within) StDev (Overall) 0.400 * 0.000 0.267 30 0.0275128 0.0297511
2、油封主副唇口锂基润滑脂过多,工 作初始状态润滑脂变稀溢出,造成后桥 油封漏油的假相;
装配时严格控制主动齿轮油封主副辱唇口的润 滑脂用量,要求油封供应商加注油封唇口润滑 脂时,采用定量加脂枪实施加注润滑脂,以免 润滑脂过多,造成后桥假相漏油,造成不必要 的维修。(已在2002/1/31完成)。
3、油封工作表面粗糙度低或端面有毛刺 油封轴颈加工方法不对 增加油封装配表面外圆表面及端面抛 光工序,提高油封工作表面粗糙度, 去除轴颈端面毛刺。 油封装配表面抛光时砂带不能左右移 动,确保表面纹路与轴线垂直。 完成时间:2002/12/25