8D报告格式及写法
实用文档之8D报告(范本)(一)2024

实用文档之8D报告(范本)(一)引言概述:8D报告是一种质量问题解决方法,通过八个步骤系统地分析问题、找到根本原因并制定解决方案,确保问题不再发生。
本文将介绍8D报告的范本,包括每个步骤的具体内容和应注意的事项。
一、定义问题1.明确问题描述:准确描述问题的具体情况;2.收集相关数据:收集与问题相关的数据和已有信息;3.确认问题的严重性:评估问题对业务的影响和损失;4.制定问题解决的目标:明确解决问题的具体目标;二、建立问题解决团队1.选取合适的团队成员:从不同部门选取具有相关知识和经验的成员;2.指定团队负责人:确定一个负责协调和推动整个8D报告进程的人;3.分配任务和责任:明确每个成员的具体任务以及所需完成的时间节点;三、分析问题的根本原因1.使用适当的工具和方法:例如鱼骨图、因果分析等;2.主动排除可能性:排除非原因或不相关的可能性;3.优先性排序:确定可能的根本原因并按重要性排序;4.验证原因的可信度:通过数据和实验验证可能性;5.确定最终根本原因:根据验证结果确定问题的真正根本原因;四、制定问题解决方案1.思考创新的解决方法:发散思维寻找多种解决方案;2.评估和筛选方案:综合考虑时间、成本、可行性等因素选择最优解决方案;3.制定实施计划和时间表:具体规划解决方案的实施步骤和时间要求;4.分配资源和责任:明确每个成员的具体任务和责任;5.监控和评估解决方案:设定评估指标,定期跟踪和监控方案的执行情况;五、预防措施和总结1.制定预防措施:根据根本原因制定相应的预防措施;2.实施预防措施:将预防措施纳入业务流程并推动实施;3.定期检查和评估:设定检查指标,定期检查预防措施的执行情况;4.总结经验教训:总结8D报告的过程,提炼经验教训;5.持续改进:将经验教训应用于持续改进的过程,避免类似问题再次发生。
总结:8D报告是一种解决质量问题的有效方法,通过八个步骤帮助团队深入分析问题和找到根本原因,制定解决方案并加以预防。
8D报告模板 8DReport
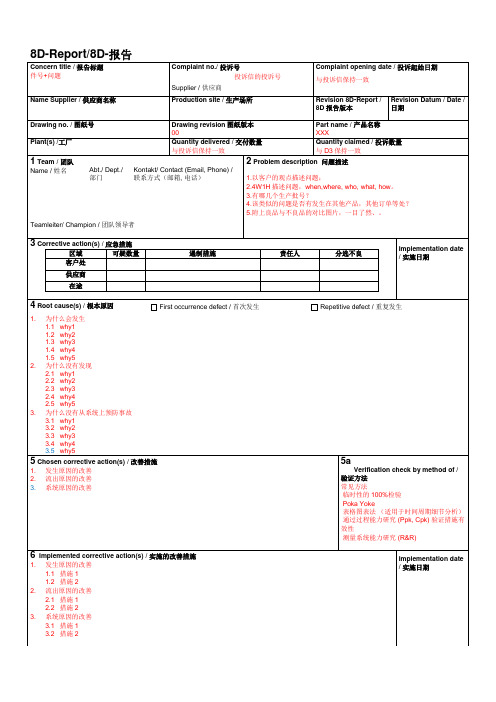
.所有的证据请编号与8D内容对应
例如:
D2.不良照片
D3.挑选指导书/断点标识照片/断点批次信息
D4.原因分析
4.1发生原因的相关作证
4.2流出原因的相关作证
4.3系统原因的相关作证
D6.改善措施
6.1.1措施1的佐证
6.1.2措施2的佐证
6.2.2....
D7预防措施
7.1相关变更文件的截图并圈出变更点
Implementation date/实施日期
Update of Design FMEA no./设计FMEA更新更新的文件需要截图并用红色方框圈出放在附件作为佐证
Update of Process FMEA no./过程FMEA更新
Update of Control plan no./控制计划更新
临时性的100%检验
Poka Yoke
表格图表法(适用于时间周期细节分析)
通过过程能力研究(Ppk, Cpk)验证措施有效性
测量系统能力研究(R&R)
6Implemented corrective action(s)/实施的改善措施
1.发生原因的改善
1.1措施1
1.2措施2
2.流出原因的改善
2.1措施1
Revision 8D-Report/8D报告版本
Revision Datum / Date/日期
Drawing no./图纸号
Drawing revision图纸版本
00
Part name/产品名称
XXX
Plant(s)/工厂
Quantity delivered /交付数量
与投诉信保持一致
Quantity claimed/投诉数量
8d报告完整版范文3篇
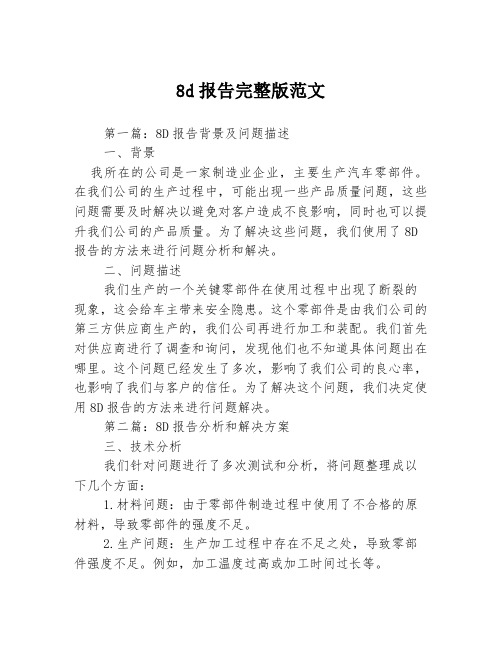
8d报告完整版范文第一篇:8D报告背景及问题描述一、背景我所在的公司是一家制造业企业,主要生产汽车零部件。
在我们公司的生产过程中,可能出现一些产品质量问题,这些问题需要及时解决以避免对客户造成不良影响,同时也可以提升我们公司的产品质量。
为了解决这些问题,我们使用了8D 报告的方法来进行问题分析和解决。
二、问题描述我们生产的一个关键零部件在使用过程中出现了断裂的现象,这会给车主带来安全隐患。
这个零部件是由我们公司的第三方供应商生产的,我们公司再进行加工和装配。
我们首先对供应商进行了调查和询问,发现他们也不知道具体问题出在哪里。
这个问题已经发生了多次,影响了我们公司的良心率,也影响了我们与客户的信任。
为了解决这个问题,我们决定使用8D报告的方法来进行问题解决。
第二篇:8D报告分析和解决方案三、技术分析我们针对问题进行了多次测试和分析,将问题整理成以下几个方面:1.材料问题:由于零部件制造过程中使用了不合格的原材料,导致零部件的强度不足。
2.生产问题:生产加工过程中存在不足之处,导致零部件强度不足。
例如,加工温度过高或加工时间过长等。
3.设计问题:设计过程中没有考虑到应力分布的均匀性,导致零部件在使用过程中容易产生应力过大的现象。
四、解决方案1.材料问题:我们将与供应商重新协商并重新规定原材料标准,以保证原材料的质量。
2.生产问题:我们将对生产过程进行检查和测试,改进加工温度和加工时间,并进一步探究生产中存在的不足之处,以最大程度地提高相关生产能力。
3.设计问题:我们会重新设计零部件,考虑应力分布的均匀性,并对原有零部件进行更加严格的测试和分析以验证新设计的可行性。
第三篇:8D报告措施计划和预防五、措施计划1.与供应商合作并重新规定原材料标准。
2.对生产过程进行检查和测试,并改进加工温度和加工时间。
3.重新设计零部件,考虑应力分布的均匀性,并进行严格的测试和分析。
4.对生产和供应链流程进行跟踪和监控,确保问题不再发生。
纠正措施8D报告格式

纠正措施8D报告格式8D报告是一种针对问题解决的方法,被广泛应用于质量管理和连续改进过程中。
以下是一个正确的8D报告格式,包含1200字以上的内容。
1. 引言(Introduction)在8D报告的开始部分,需要简要介绍报告目的和问题的背景。
描述问题的出现时间、地点和影响范围。
明确问题对组织和客户的影响。
同时,指出报告的目标是解决问题、防止问题再次发生,并改善流程和质量。
2. 问题描述(Problem Description)这一部分详细描述问题的特征和表现。
提供客观的数据和证据支持,例如事故报告、质量记录、测试数据等。
避免使用主观性词语,使用客观事实和数据。
3. 问题分析(Problem Analysis)在这一部分,主要进行问题的根本原因分析。
使用问题分析工具,如5W1H(What,When,Where,Why,Who,How)法、鱼骨图、5P(People, Plant, Process, Product, Policy)法等来帮助分析和查找问题的根本原因。
必须有充足的证据来支持问题源的判断。
4. 紧急控制措施(Immediate Corrective Actions)这一部分主要包括针对问题的紧急控制措施,以阻止问题进一步扩大。
描述已经采取的紧急控制措施,并对其有效性进行评估。
确保采取的措施是可验证的,并提供相关的数据和结果。
5. 根本原因分析(Root Cause Analysis)在这一部分,详细描述和分析问题的根本原因。
使用适当的工具和方法来找到问题根本原因,如流程图、因果关系图、5 Whys等。
分析结果应该是有逻辑性的、合理的,并且经过数据和证据的支持。
6. 校对措施(Corrective Actions)这一部分涉及到解决问题的校对措施。
列出已经制定的和计划中的校对措施。
对每个措施进行详细描述,并给出实施时间表和负责人。
确保每个措施都是可验证的,并提供评估措施有效性的方法。
7. 预防措施(Preventive Actions)在这一部分,列出预防措施,以防止问题再次发生。
范本:8D报告格式及填写说明

D4: Identify Root Cause or Potential Cause:
Date:开会日期
-以4M要素方式检讨分析为什么造成此不良并于报告中填入数据或说明
-从检测方式﹑环境影响等差异分析为什么厂内QC无法发现此不良而流至亚旭﹐
并于报告中填入详细状况
-必要时画出流程图,以便说明
□Acceptance Inspection■Line Reject
□Field Return□Other
Supplier Reference No:
D1: DESCRIBE THE PROBLEM
Date:2006/1/9
此料在SMT ROHS制程过炉后本体保护胶带收缩并卷起.以下不良品图片
注:1.此不良将造成我司维修工时&费用将Charge贵司.
Date:
(QA主官确认审核处)
-Askey QA人员填写是否可结案
Approved by:Checked by:
-可贴上照片,如空冷焊….
Approved by:核准人员签名Checked by:审核人员签名
D5: PERMANENT CORRECTIVE ACTION PLAN
Date:对策日期
-必要时画出改善后的流程图,以便说明
-若有short term & long term solution时,请一并写出
Description:T/F,SMD12,T52079(RoHS),30~60Vdc (input) :10Vdc@1.5A & 18Vdc@20mA (bias) 275KHz 200uH@0.7A(peak),SPEC LIN
TotalQ’TY:44pcs
8D报告格式及写法

8D报告的格式供应商问题分析及整改纠正措施报告8D工作方法的介绍 8D又称团队导向问题解决方法,是福特公司处理问题的一种方法,亦适用于制程能力指数低於其应有值时有关问题的解决,它提供了一套符合逻辑的解决问题的方法,同时对於统计制程管制与实际的产品质量提升架起了一座桥梁。
主要步骤包括: D1:小组成立 D2:问题说明 D3:实施并验证临时措施 D4:确定并验证根本原因 D5:选择和验证永久纠正措施 D6:实施永久纠正措施 D7:预防再发生 D8:小组祝贺 D1:小组成立目的: 成立一个小组,小组成员具备工艺/产品的知识,有配给的时间并授予了权限,同时应具有所要求的能解决问题和实施纠正措施的技术素质。
小组必须有一个指导和小组长。
关键要点: 成员资格,具备工艺、产品的知识目标分工程序小组建设 D2:问题说明目的: 用量化的术语详细说明与该问题有关的内/外部顾客抱怨,如什么、地点、时间、程度、频率等。
“什么东西出了什么问题” 方法:质量风险评定,FMEA分析关键要点: 收集和组织所有有关数据以说明问题问题说明是所描述问题的特别有用的数据的总结审核现有数据,识别问题、确定范围细分问题,将复杂问题细分为单个问题问题定义,找到和顾客所确认问题一致的说明,“什么东西出了什么问题”,而原因又未知风险等级 D3:实施并验证临时措施目的: 保证在永久纠正措施实施前,将问题与内外部顾客隔离。
(原为唯一可选步骤,但发展至今都需采用)方法:FMEA、DOE、PPM 关键要点: 评价紧急响应措施找出和选择最佳“临时抑制措施” 决策实施,并作好记录验证(DOE、PPM分析、控制图等) D4:确定并验证根本原因目的: 用统计工具列出可以用来解释问题起因的所有潜在原因,将问题说明中提到的造成偏差的一系列事件或环境或原因相互隔离测试并确定产生问题的根本原因。
方法:FMEA、PPM、DOE、控制图关键要点: 评估可能原因列表中的每一个原因原因可否使问题排除验证控制计划 D5:选择并验证永久纠正措施目的: 在生产前测试方案,并对方案进行评审以确定所选的校正措施能够解决客户问题,同时对其它过程不会有不良影响。
8D报告模板

报告日期:
报告编号:
年月日
Page 1
D1:Use Team Approach 团队组成
团队 组长:
姓名
部门
职位
成员:
Page 2
D2:Describe the Problem异常问题描述
1) 异常发生/客户投诉时间: 2) 异常发生工序: 3) 异常发现部门(及人员)/客户: 4) 异常缺陷描述: 5) 异常影响范围: 6) 其他描述:
序号 1
针对根本原因的行动措施
负责人 完成期限 完成状态
2 3 4
Page 7
D6:Action(s) 纠正措施效果验证
序号 1 2 3 4 5
行动措施
验证情况(需附相关证据)
验证人
Page 8
D7:Recurrence Prevention 预防再发生
原因调查分析
2
3
4 5
6
注:可附页
Page 5
涉及因素
D4:Root Cause Definition 根本原因分析
D4-2 分析结论: 序号 1
原因分析结果
责任工序 主要原因或 或人员 次要原因
2
3
4
5
备注:主要原因列举在前,次要原因列举在后。
Page 6
D5:Permanent Corrective Action(s) 永久性纠正措施
Page 3
D3:Containment And Short Term Corrective Action(s) 围堵措施及短期行动计划
序号
行动措施
负责人 完成期限 完成状态
行动结果
1
2
8D报告完整版范文

8D报告完整版范文8D是一种问题解决方法,通过8个步骤来进行问题的分析和解决。
下面是一个完整版的8D报告,包含对问题的描述、团队成员、问题的分析、解决方案以及实施结果的评估。
1.问题描述:在公司生产线上,发现了一个质量问题,产品出现了大量次品,导致客户抱怨并要求退货。
问题主要体现在产品的外观质量方面,表面容易出现划痕和凹痕。
2.团队成员:该问题的解决由以下团队成员共同参与:-生产部门:负责产品制造的技术人员和操作工-质量控制部门:负责产品质量的技术人员和检验员-客户服务部门:负责与客户沟通和解决问题3.问题的分析:通过团队成员的讨论和原因分析,我们找到了导致产品质量问题的几个主要原因:-工人操作不规范:工人在产品组装和包装时没有按照操作规程进行操作,导致产品出现划痕和凹痕。
-零部件供应商的质量问题:部分零部件的质量不达标,容易导致产品出现质量问题。
-质量控制不严格:质量控制部门在产品质量检验中存在一定的盲区,没有发现产品质量问题。
4.解决方案:基于问题分析,我们提出了以下解决方案来解决产品质量问题:-进行员工培训:对所有参与生产的员工进行质量意识培训和操作规程培训,确保所有员工按照规范进行生产操作。
-与供应商合作:与零部件供应商建立长期合作关系,并要求供应商提供质量合格证明。
对于质量不达标的零部件,及时通知供应商进行更换或修复。
-加强质量控制:质量控制部门要加强对产品质量的检验,制定更为细致的产品质量检验标准,并对产品检测设备进行定期维护和校准。
5.解决方案的实施:我们按照上述解决方案,分别进行了以下实施步骤:-员工培训:与人力资源部门合作,组织了一次质量培训会议,邀请专业培训师对所有员工进行培训,培训内容包括质量的重要性、操作规程和注意事项等。
-供应商合作:质量控制部门与供应商进行了紧急会议,并要求供应商提供质量合格证明。
部分质量不达标的零部件得到了及时更换和修复。
-质量控制加强:质量控制部门对产品质量检验标准进行了更新,并对产品检测设备进行了定期维护和校准。
- 1、下载文档前请自行甄别文档内容的完整性,平台不提供额外的编辑、内容补充、找答案等附加服务。
- 2、"仅部分预览"的文档,不可在线预览部分如存在完整性等问题,可反馈申请退款(可完整预览的文档不适用该条件!)。
- 3、如文档侵犯您的权益,请联系客服反馈,我们会尽快为您处理(人工客服工作时间:9:00-18:30)。
8D报告的格式
供应商问题分析及整改纠正措施报告
8D工作方法的介绍 8D又称团队导向问题解决方法,是福特公司处理问题的一种方法,亦适用于制程能力指数低於其应有值时有关问题的解决,它提供了一套符合逻辑的解决问题的方法,同时对於统计制程管制与实际的产品质量提升架起了一座桥梁。
主要步骤包括: D1:小组成立 D2:问题说明 D3:实施并验证临时措施 D4:确定并验证根本原因 D5:选择和验证永久纠正措施 D6:实施永久纠正措施 D7:预防再发生 D8:小组祝贺 D1:小组成立目的: 成立一个小组,小组成员具备工艺/产品的知识,有配给的时间并授予了权限,同时应具有所要求的
能解决问题和实施纠正措施的技术素质。
小组必须有一个指导和小组长。
关键要点: 成员资格,具备工艺、产品的知识目标分工程序小组建设 D2:问题说明目的: 用量化的术语详细说明与该问题有关的内/外部顾客抱怨,如什么、地点、时间、程度、频率等。
“什么东西出了什么问题” 方法:质量风险评定,FMEA分析关键要点: 收集和组织所有有关数据以说明问题问题说明是所描述问题的特别有用的数据的总结审核现有数据,识别问题、确定范围细分问题,将复杂问题细分为单个问题问题定义,找到和顾客所确认问题一致的说明,“什么东西出了什么问题”,而原因又未知风险等级 D3:实施并验证临时措施目的: 保证在永久纠正措施实施前,将问题与内外部顾客隔离。
(原为唯一可选步骤,但发展至今都需采用)方法:FMEA、DOE、PPM 关键要点: 评价紧急响应措施找出和选择最佳“临时抑制措施” 决策实施,并作好记录验证(DOE、PPM分析、控制图等) D4:确定并验证根本原因目的: 用统计工具列出可以用来解释问题起因的所有潜在原因,将问题说明中提到的造成偏差的一系列事件或环境或原因相互隔离测试并确定产生问题的根本原因。
方法:FMEA、PPM、DOE、控制图关键要点: 评估可能原因列表中的每一个原因原因可否使问题排除验证控制计划 D5:选择并验证永久纠正措施目的: 在生产前测试方案,并对方案进行评审以确定所选的校正措施能够解决客户问题,同时对其它过程不会有不良影响。
方法:FMEA 关键要点: 重新审视小组成员资格决策,选择最佳措施重新评估临时措施,如必要重新选择验证管理层承诺执行永久纠正措施控制计划 D6:实施永久纠正措施目的: 制定一个实施永久措施的计划,确定过程控制方法并纳入文件,以确保根本原因的消除。
在生产中应用该措施时应监督其长期效果。
方法:防错、统计控制关键要点: 重新审视小组成员执行永久纠正措施,废除临时措施利用故障的可测量性确认故障已经排除控制计划、工艺文件修改 D7:预防再发生目的: 修改现有的管理系统、操作系统、工作惯例、设计与规程以防止这一问题与所有类似问题重复发生。
关键要点: 选择预防措施验证有效性决策组织、人员、设备、环境、材料、文件重新确定 D8:小组祝贺目的: 承认小组的集体努力,对小组工作进行总结并祝贺。
关键要点: 有选择的保留重要文档流览小组工作,将心得形成文件了解小组对解决问题的集体力量,及对解决问题作出的贡献必要的物质、精神奖励。