涡流纺
喷气涡流纺纱原理

喷气涡流纺纱原理喷气涡流纺纱原理概述喷气涡流纺纱是一种在高速气流作用下,将聚合物熔体喷射到空气中形成细丝的纺织技术。
该技术可以生产出高强度、高模量、低密度的纤维,广泛应用于航空航天、汽车、建筑等领域。
原理1. 喷嘴喷嘴是喷气涡流纺纱技术中最关键的部件之一。
它由一个圆柱形的进料口和一个锥形的出料口组成。
聚合物熔体经过进料口进入喷嘴,然后通过出料口被喷射到空气中。
2. 气流在喷嘴周围形成高速气流是实现喷气涡流纺纱的必要条件。
这种气流可以通过压缩空气或者惰性气体来产生。
当聚合物熔体被喷射到空气中时,它会受到这种高速气流的牵引和拉伸,形成一个细长而连续的丝状结构。
3. 涡旋区域在喷嘴周围形成的高速气流会形成一个涡旋区域,这个区域是喷气涡流纺纱过程中最重要的部分之一。
在这个区域内,聚合物熔体会被拉伸和剪切,形成一个细长而连续的丝状结构。
同时,在涡旋区域内也会发生聚合物熔体的混合和分散作用,从而使得纤维质量更加均匀。
4. 纤维形成在喷嘴周围形成的高速气流和涡旋区域的作用下,聚合物熔体被拉伸、剪切、混合和分散,最终形成一个连续而均匀的纤维。
这种纤维可以通过不同的控制参数来调节其直径、长度、拉伸率等性能指标。
应用喷气涡流纺纱技术广泛应用于航空航天、汽车、建筑等领域。
在航空航天领域中,该技术可以生产出高强度、高模量、低密度的碳纤维和玻璃纤维等复合材料;在汽车领域中,该技术可以生产出轻量化、高强度的车身结构件;在建筑领域中,该技术可以生产出高强度、高韧性的钢筋混凝土材料。
涡流纺用途
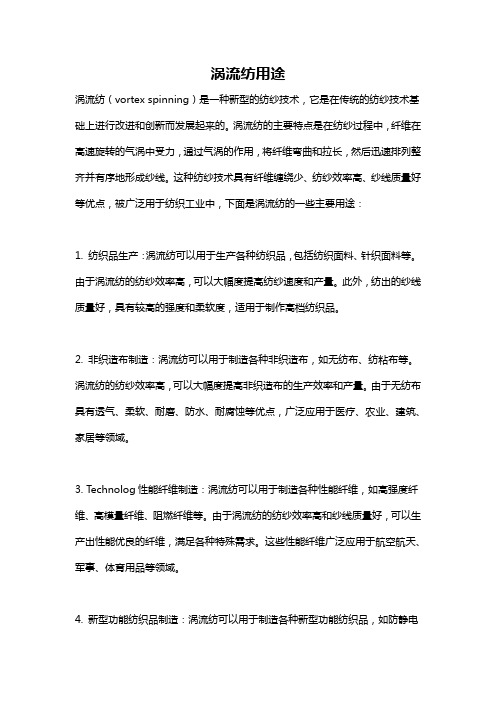
涡流纺用途涡流纺(vortex spinning)是一种新型的纺纱技术,它是在传统的纺纱技术基础上进行改进和创新而发展起来的。
涡流纺的主要特点是在纺纱过程中,纤维在高速旋转的气涡中受力,通过气涡的作用,将纤维弯曲和拉长,然后迅速排列整齐并有序地形成纱线。
这种纺纱技术具有纤维缠绕少、纺纱效率高、纱线质量好等优点,被广泛用于纺织工业中,下面是涡流纺的一些主要用途:1. 纺织品生产:涡流纺可以用于生产各种纺织品,包括纺织面料、针织面料等。
由于涡流纺的纺纱效率高,可以大幅度提高纺纱速度和产量。
此外,纺出的纱线质量好,具有较高的强度和柔软度,适用于制作高档纺织品。
2. 非织造布制造:涡流纺可以用于制造各种非织造布,如无纺布、纺粘布等。
涡流纺的纺纱效率高,可以大幅度提高非织造布的生产效率和产量。
由于无纺布具有透气、柔软、耐磨、防水、耐腐蚀等优点,广泛应用于医疗、农业、建筑、家居等领域。
3. Technolog性能纤维制造:涡流纺可以用于制造各种性能纤维,如高强度纤维、高模量纤维、阻燃纤维等。
由于涡流纺的纺纱效率高和纱线质量好,可以生产出性能优良的纤维,满足各种特殊需求。
这些性能纤维广泛应用于航空航天、军事、体育用品等领域。
4. 新型功能纺织品制造:涡流纺可以用于制造各种新型功能纺织品,如防静电纺织品、医疗纺织品等。
涡流纺可以将特殊纤维与常规纤维混纺,形成一个灵活多样、适应特殊需求的纺织品。
例如,防静电纺织品可以用于电子工业、化工工业等场合,医疗纺织品可以用于医疗防护、康复护理等领域。
5. 纤维增强复合材料制造:涡流纺可以用于制造纤维增强复合材料。
涡流纺可以将纤维弯曲和拉长,使得纤维与复合材料基体之间有更好的结合接触,从而提高复合材料的强度和韧性。
纤维增强复合材料广泛应用于航空航天、汽车、建筑等领域。
总的来说,涡流纺作为一种新型的纺纱技术,具有高效、优质、适应性强等优点,被广泛用于纺织工业和其他相关领域。
随着科技的不断发展和进步,相信涡流纺的应用领域还会进一步拓展和扩大。
环锭纺、气流纺、喷气纺、涡流纺、赛络纺、紧密纺简介

环锭纺、气流纺、喷气纺、涡流纺、赛络纺、严密纺简介环锭纺环锭纺纱是现时市场上用量最多,最通用之纺纱方法,条子或粗纱经牵伸后的纤维条通过环锭钢丝圈旋转引入,筒管卷绕速度比钢丝圈快,棉纱被加捻制成细纱.广泛应用于各种短纤维的纺纱工程.如普梳,精梳及混纺,钢丝圈由筒管通过纱条带动绕钢领回转.进展加捻,同时,钢领的摩擦使其转速略小于筒管而得到卷绕.纺纱速度高,环锭纱的形态,为纤维大多呈外转移的圆锥形螺旋线,使纤维在纱中外缠绕联结,纱的结构严密,强力高,适用于制线以及机织和针织等各种产品。
环锭纺(精梳)流程:清花间--梳棉--预并条--条并卷--精梳--头道并条--二道并条--粗纱--细纱--络筒环锭纺(普梳)流程:清花间--梳棉--头道并条--二道并条--粗纱--细纱--络筒气流纺气流纺不用锭子,主要靠分梳辊、纺杯、假捻装置等多个部件。
分梳辊用来抓取和分梳喂入的棉条纤维,同过他的高速回转所产生的离心力可把抓取的纤维甩出。
纺杯是个小小的金属杯子,他的旋转速度比分梳辊高出10倍以上,由此产生的离心作用,把杯子里的空气向外排;根据流体压强的原理,使棉纤维进入气流杯,并形成纤维流,沿着杯的壁不断运动。
这时,杯子外有一根纱头,把杯子壁的纤维引出来,并连接起来,再加上杯子带着纱尾高速旋转所产生的钻作用,就好似一边“喂〞棉纤维,一边加纱线搓捏,使纱线与杯子壁的纤维连接,在纱筒的旋绕拉力下进展牵伸,连续不断的输出纱线,完成气流纺纱的过程。
气流纺的特征气流纺纱有速度大、纱卷大、适应性广、机构简单和不用锭子、钢领、钢丝圈的优点,可成倍的提高细纱的产量。
气流纺与环锭纺的区别气流纺与环锭纺一个是新型纺织技术,一个是老式纺纱技术。
气流纺是气流纺纱,而环锭纺那么是机械纺,就是由锭子和钢铃、钢丝圈进展加捻,由罗拉进展牵伸。
而气流纺那么是由气流方式输送纤维,由一端握持加捻。
一般来说,环锭纱毛羽较少,强度较高,品质较好。
气流纺工序短,原料短绒较多,纱线毛,支数和拈度不能很高,价格也较低。
涡流纺纱机

纺纱器型式之一 纺纱器型式之二
型式之三
型式之四
型式之五
五圆孔切向进风 型纺纱器
涡流纺纱的原料
• 涡流纺纱机理和生产实践证明:涡流纺对比较细而柔软的纤
维可纺性能好,成纱质量高,对粗硬纤维的适纺性差。
• 使用原料以合成纤维和粘胶纤维为主,以腈纶为最好; • 纤维长度25~65mm, 0.165~0.77tex(1.5~7D),即从棉到中长
圆环形(伞形)纱环
纱尾环在涡流作用下沿管 壁绕中心高速回转而获得 捻度,纤维一边搭接在纱 尾上,一边加捻成纱,并 由纱孔输出,以连续纺纱。
涡流加捻的应用
• 空气涡流加捻具有独特的优越性,条在空气涡流
场中可获得高达每分钟数十万转的回转速度,涡流 加捻的应用:
• 空气变形丝:利用涡流对长丝进行假捻变形; • 包缠纺纱:利用涡流吸引纤维并进行假捻和包缠纤
维,纺制各种花式纱和包芯纱;
• 静电纺中的涡流加捻; • 喷气纺纱:利用涡流对纤维假捻解捻包缠; • 涡流纺纱:利用涡流使纤维凝聚,并加捻成纱
对涡流管的要求
• 能产生高速气流回转对纱条加捻,并使产量达到高于
环锭纺8倍以上;
• 能提高纱线制成率; • 在提高产量的同时,不增加耗电量; • 涡流纱能代替部分环锭纱的使用领域或开发涡流纱特
匀、捻度不匀、断裂伸长比环锭纱好;耐磨性好,染 色性好; 绕在纱芯中,表面成闭环形毛羽,后道飞花少,有利 于做起绒织物;
• 因没有外包和边缘纤维,结构蓬松,纤维两头端多缠
涡流纱的产品
• 针织类:绒类产品,如运动衫裤、起毛毯、仿裘皮大
衣、拉毛围巾、外衣等;
• 机织类:仿毛花呢、交织呢、雪花大衣呢、色织布、
涡流纺纱方法的优势及其未来发展前景

涡流纺纱方法的优势及其未来发展前景涡流纺纱是利用固定不动的涡流纺纱管,来代替高速回转的纺纱杯进行纺纱的一种新型纺纱方法。
从某种意义上说,涡流纺纱才是真正意义上的气流纺纱。
纤维条由给棉罗拉喂入,经过刺辊开松成单纤维,借气流的作用,从输棉管道高速喂入涡流管内。
涡流管由芯管和外管两部分组成。
外管上开有三只切向的进风口,下端与鼓风机相连,风机不断地从管中抽取空气,外面的空气沿进风口进入涡流管内,产生旋涡状的气流。
当旋转向上的气流到达芯管时,与输棉管道进入的纤维汇合,沿涡流管内壁形成一个凝聚纤维环,稳定地围绕涡流管轴线,高速回转,将纤维加捻成纱。
纱从导纱孔中连续不断地由引出罗拉引出卷绕成筒子。
涡流纺纱最主要的特点是省去了高速回转的纺纱部件。
由于采用气流加捻摆脱了高速加捻部件引起的转动惯性问题和轴承负荷问题(如气流纺纱的纺杯),还有因纺纱形成的气圈而增大了纺纱张力的问题(如环锭纺纱)。
涡流纺纱与其他新型纺纱比较具几方面的优势:速度快、产量高涡流纺纱机纺纱速度为100_200m/min,实用速度一般在100_160m/min。
国内用涡流纺纱机纺制6_12英支纱,纺纱速度为100_140m/min,单产600_800(kg/千锭•h),相当于环锭纱的4_5倍;如纺40公支腈纶纱,用10台(192头/台)PF-1型涡流纺纱机,产量达400kg/h。
相当于20台(4000头)BD-200型气流纺纱机的产量,相当于40台环锭纺纱机16320锭的产量。
一个涡流纺纱头的产量,相当于2.08个气流纺纱头或8.5个环锭的产量。
由于涡流纺纱是依靠涡流加捻,如继续研究改进,纺纱速度还可以继续提高。
工艺流程短、制成率高涡流纺纱是用纤维条子直接纺制成筒子纱,所以像其他新型纺纱一样,可省去粗纱和络筒两道工序。
由于涡流纺纱断头率很低,回花损失少,制成率高达99%以上。
适纺性强、宜做起绒产品涡流纺纱可纺制纤维长度在38_60_长的,对棉纤维和化学纤维纯纺与混纺纱。
环锭纺、气流纺、喷气纺、涡流纺、赛络纺、紧密纺简介

环锭纺、气流纺、喷气纺、涡流纺、赛络纺、紧密纺简介环锭纺环锭纺纱是现时市场上用量最多,最通用之纺纱方法,条子或粗纱经牵伸后的纤维条通过环锭钢丝圈旋转引入,筒管卷绕速度比钢丝圈快,棉纱被加捻制成细纱.广泛应用于各种短纤维的纺纱工程.如普梳,精梳及混纺,钢丝圈由筒管通过纱条带动绕钢领回转.进行加捻,同时,钢领的摩擦使其转速略小于筒管而得到卷绕.纺纱速度高,环锭纱的形态,为纤维大多呈内外转移的圆锥形螺旋线,使纤维在纱中内外缠绕联结,纱的结构紧密,强力高,适用于制线以及机织和针织等各种产品。
环锭纺(精梳)流程:清花间--梳棉--预并条--条并卷--精梳--头道并条--二道并条--粗纱--细纱--络筒环锭纺(普梳)流程:清花间--梳棉--头道并条--二道并条--粗纱--细纱--络筒气流纺气流纺不用锭子,主要靠分梳辊、纺杯、假捻装置等多个部件。
分梳辊用来抓取和分梳喂入的棉条纤维,同过他的高速回转所产生的离心力可把抓取的纤维甩出。
纺杯是个小小的金属杯子,他的旋转速度比分梳辊高出10倍以上,由此产生的离心作用,把杯子里的空气向外排;根据流体压强的原理,使棉纤维进入气流杯,并形成纤维流,沿着杯的内壁不断运动。
这时,杯子外有一根纱头,把杯子内壁的纤维引出来,并连接起来,再加上杯子带着纱尾高速旋转所产生的钻作用,就好像一边“喂”棉纤维,一边加纱线搓捏,使纱线与杯子内壁的纤维连接,在纱筒的旋绕拉力下进行牵伸,连续不断的输出纱线,完成气流纺纱的过程。
气流纺的特征气流纺纱有速度大、纱卷大、适应性广、机构简单和不用锭子、钢领、钢丝圈的优点,可成倍的提高细纱的产量。
气流纺与环锭纺的区别气流纺与环锭纺一个是新型纺织技术,一个是老式纺纱技术。
气流纺是气流纺纱,而环锭纺则是机械纺,就是由锭子和钢铃、钢丝圈进行加捻,由罗拉进行牵伸。
而气流纺则是由气流方式输送纤维,由一端握持加捻。
一般来说,环锭纱毛羽较少,强度较高,品质较好。
气流纺工序短,原料短绒较多,纱线毛,支数和拈度不能很高,价格也较低。
新型纺纱技术

(1)自控程度高 (1)自控程度高
涡流纺整个纺纱过程受到电子系统的监控, 电子清纱器发现纱疵时即自动去除疵点,并立 即应用自动接头装置将纱接起来,因此整个纺 纱过程是全自动、连续式的。此外,每个锭子 的纱都受到自动接头器的监控,如有异常,可 实现单锭自动停止纺纱。
(2)工艺流程短 (2)工艺流程短
2、涡流纺的主要特点
涡流纺无高速回转机件采用旋转涡流加捻成纱,比 机械式加捻效率高,高速回转的涡流只作用在纤维 上,与前罗拉引出的纤维的功能一起形成对纤维的 加捻作用,高速涡流除了完成加捻任务外,并不影 响纱线支数的高低,因此可实现高速纺纱,最高纺 速实际可达380m/min,每锭的产量相当于环锭纺单 锭产量的22倍左右。由于纤维受到具有声速的喷气 涡流及卷取罗拉作用而形成真捻,因此这种特殊的 加捻作用是其它纺纱机械不能取代的,纱线高的回 旋速度下的成纱结构比环锭纱线的结构更为紧密和 稳定。
3、紧密纱线的特点
毛羽少,光洁度高。其毛羽一般比普通纱减少 70%-80%; 强度高,捻度减少。同样的纱支捻度减5%-15%, 而强力却提高约15%-25% ; 条干好。由于纤维的利用率得以提高,乌斯特条干能 够达到3%-5%; 能代替股线。由于紧密纱的强度高,其单纱可以替代 传统股线。如 16.2tex的紧密纱与8.1×2tex的传统股 线具有同等强度,在生产工艺上可以减少合股工序;
从以上紧密纱的特点可以看出它是一种与 众不同的高品质纱。由于它的优良特性给纺 纱、准备、织造、印染等一系列后道加工带 来了工艺创新,降低了后加工流程和成本, 尤其是减少了浆纱和烧毛对环境造成的工业 污染。
总之,紧密纺纱技术是目前环锭细纱机关键的重 要技术进步。纱线质量及生产费用等方面的优势,将 使紧密环锭纺纱技术不但本身具有高档产品的特征, 而且将逐步取代传统环锭纺纱技术,使纺织工业及时 装工业具有更开阔的产品开发空间,使服装设计可以 从紧密纱纺纱到最终产品进行一系列的设计,这种独 特的生产优势,一方面提高了产品档次,另一方面也 考虑了产品的经济性、生态环境特性、创新性及独特 性等。现在, 性等。现在,紧密纱在市场上的售价比传统环锭纱每公 斤高1 3.5美元,经济效益十分可观,更重要的是消费 斤高1-3.5美元,经济效益十分可观,更重要的是消费 者非常欢迎。因此,紧密纺纱技术将得到快速发展。
2023年全球及中国涡流纺织机行业全景速览

2023年全球及中国涡流纺织机行业全景速览内容概况:截止2022年底,我国涡流纺纱机存量约在3439台左右,国内厂家年均产量在10台左右,多为试验机或样板厂商展示机型,国内市场对村田、立达涡流纺纱机进口需求较大。
据统计,2022年我国涡流纺纱机市场需求量为709台,同比增长68.8%。
关键词:涡流纺纱机、涡流纺纱、纺织机械一、涡流纺纱机综述自由端纺纱就是纺纱过程中在某处将连续的纤维束断开,使纱尾形成自由状态,以保证纱条加上真捻。
自由端纺纱有多种方式,其基本特点在于喂入端一定形成自由端。
通常是加捻之前把连续的纤维束断开,连续的纤维束大体上是在其轴向被断开,或者在其径向分离出边缘纤维头端自由纤维。
经过断裂分离后的纤维又必须重新凝聚起来成为连续的须条,再经加捻而卷绕成筒子。
涡流纺纱机是在喷气纺的基础上发展起来的一种新型纺纱形式,属于自由端纺纱类别,主要利用涡流状的气流对牵伸后的纤维束进行加捻成纱的一种新型纺纱设备,简称涡流纺。
涡流纺纱机根据不同的操作方式和技术特点可以分为开放式、封闭式和喷射式等。
二、涡流纺纱机产业链从产业链来看,涡流纺纱机产业链上游主要包括设备制造原材料和制造加工设备,原材料主要是金属、合金、塑料和其他构件等,制造加工设备主要包括机械加工设备、焊接设备等。
产业链下游,涡流纺纱机应用于纺纱工业,如内衣、T恤、家纺、牛仔、医疗织物用品等应用领域。
纺织机械是指应用在纺织工艺各个环节中,把天然纤维或者化学纤维加工成为纺织品所需要的各种机械设备。
纺织机械是纺织工业的生产手段和物质基础,其技术水平、质量和制造成本,直接关系到纺织工业的发展。
涡流纺纱机是纺织机械的一种,市场整体发展来看,据中国纺织机械行业协会数据,2022年我国纺织机械行业营收为848亿元,同比增长1.9%,行业市场规模未来有望持续保持正向增长。
三、涡流纺纱机行业现状分析涡流纺纱是一种新型纺纱形式,在喷气纺纱工艺基础上发展而来,全球市场上瑞士立达公司和日本村田公司产品较为成熟,我国市场发展较为缓慢,直到2012年才在上海纺机展展出第一台样机,至今仍未实现大量推广应用。
- 1、下载文档前请自行甄别文档内容的完整性,平台不提供额外的编辑、内容补充、找答案等附加服务。
- 2、"仅部分预览"的文档,不可在线预览部分如存在完整性等问题,可反馈申请退款(可完整预览的文档不适用该条件!)。
- 3、如文档侵犯您的权益,请联系客服反馈,我们会尽快为您处理(人工客服工作时间:9:00-18:30)。
– 动力消耗少 PF一1型涡流纺纱机生产单位重量纱所需 的动力比BD—200型转杯纺纱机少10%一12%,比环锭 纺纱机少15%;而且,机构料损耗少,噪音低。
• 经济效果比较显著 在单位产量相同条件下,采用涡流纺纱所需要的 占地面积为环锭纺纱的60%,所需要的生产工人为环锭纺纱的53%, 劳动生产率为环锭纺纱的1.86倍.单位产品的加工费用为环锭纺纱的 70%。
内,成纱结构最为紧密, 纱线外观光洁、毛羽少,纱 线加捻螺旋结构清晰可见, 纤维几乎没有内外转移。 – 这种纱线结构的改善是通过纺纱加捻三角区的消除而 获得的。
涡流纱的性能
• 喷气涡流纺的成纱结构与环锭纺相似,但还存在 有纱芯,约60 %的纤维在纱中呈螺旋排列。
• 在纺纯棉时喷气涡流纺单纱强力和条干比相应环 锭纱稍差些,其它指标都与环锭纺相当,毛羽比 环锭纱大幅减少。
涡流纺纱
• 要点:
– 1、了解涡流纺的成纱原理 – 2、了解涡流纺纱的特点 – 3、掌握涡流纱的成纱结构特点与纱线性能 – 4、了解涡流纺的适纺原料与适应产品
涡流纺纱概述
• Airvortex spinning,属自由端纺纱 • 1957年德国的哥茨莱德(Gatzfreid)首先设计发明. • 波兰生产的 PF一2型和PF-2RA型涡流纺纱机,纺纱速度达
• 涡流纺纱还具有如下优点:
– 工艺流程短 用二并条子喂入直接纺成筒子纱,甚至可以省去并条 工序,但必须提高生条均匀度,这就需在梳棉机上采用自调匀整 装置。
– 制成率高 它是在负压条件下纺纱,没有飞花外溢现象,由于涡流 纺纱断头少,回花损失也少,制成率高达99%以上。
– 劳动环境好 机台清洁,操作方便,接头方便,断头后涡流管内无 积花,不需要清扫。
– 通过测试起球试验可看出: 涡流纱织物4~ 4.5级, 喷气纱4级, 传统环锭纱2级, 转杯纱2~ 3级, 紧 密纺纱3~4级。
涡流纺纱的适纺性能及产品开发
• 适纺纤维
– 棉型或中长型的化纤混纺或纯纺。 – 纺纯棉产品有困难, – 化纤又以腈纶为主,
• 适纺线密度
– 涡流纺纱适宜纺较粗的纱,一般不低于20tex。 – 对于细特纱,由于断面内纤维根数少,纱条的不匀情况较明显,纺制比
不同纺纱方法成纱结构
传统环锭纺纱线结构
• 传统环锭纱中纤维基本上呈螺旋线排列, 由于存 在纺纱加捻三角区,纤维不能全部被加捻到纱体 中去, 较多边缘纤维一端被捻入纱体,另一端露 在纱条外面形成毛羽, 因而虽然环锭纱结构较为 紧密,但纱条表面相对来说显得杂乱无序, 光洁 度较差。
转杯纺纱线结构
– 转杯纱在加捻过程中,加捻区的纤维缺乏积极握持, 呈松散状态,因而纤维伸直度差,纤维内外转移程度 低。
– 非传统纺纱在耐磨性方面有着明显的优势,转 杯纱、喷气纱和涡流纱均由纱芯和外包纤维两 部分组成, 纱线表面包有不规则的缠绕纤维, 纱线不易解体, 同时纱线表面摩擦系数大, 在织物中纱与纱之间的抱合良好,不易产生相 对滑移,故耐磨性提高。
抗起球
– 涡流纱针织物耐磨性好,抗起球等级高。这是因为涡 流纱中间为平直芯纱,外层包覆缠绕纤维,纤维定向 明显,纱摩擦系数大, 织物内纱与纱之间摩擦性好, 不易产生相对滑移,耐磨性提高,
较困难。
适纺产品
• 涡流纱的特点是蓬松性好,有利于起绒且起绒织物的强 力接近同线密度环锭纱起绒织物。
• 因此,涡流纱最适合做各种机织、针织起绒织物和装饰织 物,也可用涡流包芯纱制成工业用织物
涡流纺纱线结构
– 涡流纱也是一种双重结构的纱,纱条的芯纤维是平行 排列的、无捻度, 依靠旋转气流的作用使末端纤维包 覆缠绕于芯纤维外部加捻成纱。
– 与喷气纱不同的是,涡流纱的外层覆盖纤维比重大(约 60%),以致内部未加捻的纤维几乎被完全覆盖, 表 面纤维排列则更近似于环锭纱。
紧密纺纱线结构
– 紧密纺纱线中的纤维排列最为整齐清晰。 – 由于气流的收缩和聚合作用,纤维的端头均捻入纱线
– 新型纱线结构使纱线表面更加稳定,后加工的毛羽增 加量显著低于传统纱线。特别是作为经纱,在浆纱时 可节约浆料约50%,大大提高织机效率,降低织造成 本。
耐磨性
– 纱线的耐磨性与纱线的结构密切相关。 – 传统环锭纱由于纤维大多呈螺旋线形态, 当
反复摩擦时,螺旋线纤维逐步变成轴向纤维, 纱线易失捻解体而很快磨断, 因而耐磨性较 差。
– 纱的结构分纱芯和外包纤维两部分。 – 纱芯结构与环锭纱相似, 比较紧密; 外包纤维结构
松散,无规则地缠绕在纱芯外面。 – 与传统环锭纱相比, 转杯纱结构比较蓬松,外观较丰
满。
喷气纺纱线结构
– 喷气纱是一种双重结构的纱,一部分是几乎平行、无 捻的芯纤维,另一部分是包缠在芯纱外部的包缠纤维。
– 喷气纱的结构较为蓬松,纤维间的间隙较大,包缠纤 维与芯纤维的比例约为1:9, 包缠纤维将向心的应力 施加于芯纤维条上,给予纱体必要的聚合力以承受外 部应力。
到150m/min • 天津设计制造TW-4型、TW-5型涡流纺纱机,上海研制了
WF-2型涡流纺纱机.
特点
• 纱线毛羽减少3/4,3 mm以上近乎为0;抗起毛起球提高 30%; 吸湿、放湿性能好。
• 人工减少250%,能源节约30%(与现代环锭纺相比)。 • 世界各国涡流纺纱的研究进展不大,主要原因是对涡流纺
纱的研究不够深人,适纺范围较窄有关。
涡流纺纱的工艺流程
涡流纺纱原理
涡流纺纱的特点
• 涡流纺纱届自由端纺纱。 • 纤维条经给棉装置喂入,由小刺辊分硫成单纤维,利
用高速回转的旋涡气流,在涡流管内位纤维凝聚加捻 成纱。 • 利用固定不动的涡流管取代丁其它纺纱方法中高速回 转的加捻器,所以纺纱速度可达100一200m/min(产 量为环锭纺的5—7倍),而且机构十分简单。
• 可以认为用喷气涡流纺纺纯棉纱及其品与环锭纱 是相当的。
强力
– 以环锭纱强力为1,那么其它种类纱线的强 力为:
• 转杯纱0.8~0.9, • 喷气纱0.6~ 0.7, • 涡流纱0.8, • 紧密纺纱强力最高为1.15。。
条干
• 涡流纱的乌斯待条干不匀率与转杯纱和转杯纱的 值相仿。
• 涡流纱的粗细节、棉节比转杯纱和环锭纱都多。 这主要是因为在输送纤维过程中,纤维伸直度差; 涡流场的稳定与否直接影响输送纤维流的均匀。
毛羽
– 相对于传统环锭纱,气流纱、涡流纱、紧密纱 的1~ 2 mm的毛羽均有降低, 而喷气纱由于 缠绕纤维数量低,无捻纱芯覆盖少,因而有较 多的短毛羽。
– 与传统环锭纱相比,非传统纺纱的有害毛羽数(> 3 mm) 显著降低,其中紧密纱约减少80%,喷气纱约减少85 %,涡流纺纱则减幅达90% 以上。
• 适纺范围 涡流纺最适用于纺纤维长度为30一50mm的腈纶、粘纤、 涤纶等各种化学纤维及混纺涤棉纱,还可以用于纺制各种花式纱线, 如包芯纱、螺旋竹节纱等,其产品用途也正在不断开发。
•
涡流纱的结构
• 涡流纱的结构与转杯纱的结构类似,这是 与它们相似的成纱原理决定的。
涡流纺纱线结构
•气流喷射处理过程,它能产生与环 锭纺非常相似的纱线结构,产量首次 达到了转杯纺的2.5 倍。这是个显著 的改进。 •涡流纺在纱线结构上不等同于环锭 纺,但差异很小。