喷气纺纱和涡流纺纱的产品特点及其发展
喷气涡流纺纱原理

喷气涡流纺纱原理喷气涡流纺纱原理概述喷气涡流纺纱是一种在高速气流作用下,将聚合物熔体喷射到空气中形成细丝的纺织技术。
该技术可以生产出高强度、高模量、低密度的纤维,广泛应用于航空航天、汽车、建筑等领域。
原理1. 喷嘴喷嘴是喷气涡流纺纱技术中最关键的部件之一。
它由一个圆柱形的进料口和一个锥形的出料口组成。
聚合物熔体经过进料口进入喷嘴,然后通过出料口被喷射到空气中。
2. 气流在喷嘴周围形成高速气流是实现喷气涡流纺纱的必要条件。
这种气流可以通过压缩空气或者惰性气体来产生。
当聚合物熔体被喷射到空气中时,它会受到这种高速气流的牵引和拉伸,形成一个细长而连续的丝状结构。
3. 涡旋区域在喷嘴周围形成的高速气流会形成一个涡旋区域,这个区域是喷气涡流纺纱过程中最重要的部分之一。
在这个区域内,聚合物熔体会被拉伸和剪切,形成一个细长而连续的丝状结构。
同时,在涡旋区域内也会发生聚合物熔体的混合和分散作用,从而使得纤维质量更加均匀。
4. 纤维形成在喷嘴周围形成的高速气流和涡旋区域的作用下,聚合物熔体被拉伸、剪切、混合和分散,最终形成一个连续而均匀的纤维。
这种纤维可以通过不同的控制参数来调节其直径、长度、拉伸率等性能指标。
应用喷气涡流纺纱技术广泛应用于航空航天、汽车、建筑等领域。
在航空航天领域中,该技术可以生产出高强度、高模量、低密度的碳纤维和玻璃纤维等复合材料;在汽车领域中,该技术可以生产出轻量化、高强度的车身结构件;在建筑领域中,该技术可以生产出高强度、高韧性的钢筋混凝土材料。
国内外气流纺纱的发展及产品开发状况
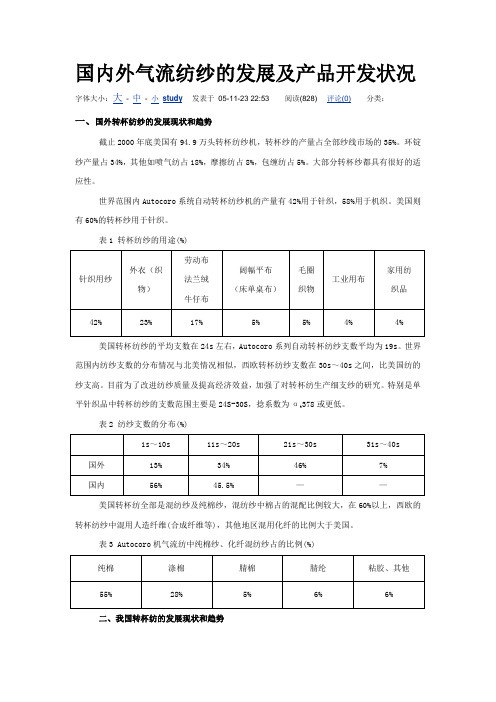
截止2001年底,我国转杯纺已超过85万头,占环锭纺的2.43%,国际上为占环锭纺的4.78%(其中进口占20%,自排风式占70%,抽气式占30%)。
企业估计在600-700家以上。
尚有一定的发展空间。
开发的原料和领域还很多,1.对棉而言,应用于针织品领域生产中细支转杯纺纱国内尚处于起步阶段(据对上海三枪、宁波申洲、江苏AB等企业调查现均为国外订单,与涤混纺的订单比例还及少)。
由于受国产设备水平所限及价格因素和习惯的影响,因此国内应用需要有一过程,需要大力的宣传和推广,这是转杯纺可以进一步发展和应用的重点方向。
2.开发非棉纤维原料产品。
3.开发花色纱线产品。
4.应用到装饰和其他产业领域。
三、转杯纺纱的最终用途恰当地选配及改进棉纤维、人造纤维的性质,将有助于改进转杯纺的纺纱性能,在许多方面比环锭优异得多,从而使转杯纺纱逐步在一些领域里代替环锭纺纱成为可能,另外对原料加工处理的新技术亦大大提高了适应调整转杯纺的性能。
转杯纺纱最近一些新的最终用途发展如下:1、用转杯纱生产的各式牛仔布织物重量从340g/m2~410g/m2到475g/m2~540g/m2。
2、26s~30s纯棉或50/50涤/棉纱织成优质平纹织物。
3、用30s~40s纯棉或50/50涤/棉纱制成双面针织布。
4、穆斯林布:用50/50涤/棉混纺26s纱织成。
5、高级印花布:用35s~40s纯棉或50/50涤/棉混纺纱织成。
6、高密薄纱布:用35s~40s50/50涤/棉纱及纯棉纱织成。
7、100%纯棉单纱或绒纱织制起圈毛巾。
8、用100%纯棉绒作纬纱织制窄幅或宽幅灯芯绒。
9、工业用布:由于转杯纺纱具有很好的覆盖性,在后工序整经、浆纱、机织或会织等工序,断头停台少、生产效率高。
在2000年后,世界上转杯纺纱产量占市场上的比重将由28%上升到约50%,而美国转杯纺纱产量的比重由35%将增加到55%~60%,可想而知,21世纪转杯纺纱的发展前景是很好的。
新型纺纱技术的现状及其发展趋势

“德昌杯”2006年全国紧密纺纱技术研讨会要用于床上用品,50%的床上用品用的是喷气纱;三是用于针织纱、台布用纱、花色布用纱等。
村田最新喷气纺机有No.810涡流纺纱机(MVS)、No.81T涡流纺纱机(双股线)、No.8R2喷气纺纱机(MJS)、No.881HR喷气纺纱机(双股线)。
TPF228喷气纺纱机在国内浙江泰坦纺机开发成功。
图lMvS成纱过程村田公司于1995年推出了村田涡流纺纱机(MurataVortexSpinning,简称MVS,也有涡流纺)。
可以纺纯棉及其它短纤维。
本文认为MVS是在喷气包缠纺的基础上发展起来的一种纺纱方法,利用气流喷射在喷嘴内产生高速旋转气流,使须条的边纤维(一端自由纤维)的自由端对内层纤维产生相对角位移,使须条获得真捻而成纱。
尽管MVS被称为涡流纺,但其与传统意义上的涡流纺相差较大,MVS实际上仍然属于喷气纺的范畴,可以称为喷气涡流纺。
当然,在纺纱机理上,MVS有着自由端纺纱的特征,但又不完全自由端,本文认为属于部分自由端、一定程度的自由端或亚自由端纺纱。
喷气涡流纱的结构不同于传统喷气包缠纱的结构,其成纱结构与环锭纺相似,但还存在有纱芯;喷气涡流纺纱(MvS)可以做到无接头,毛羽飞花少,单纱强力高,基本上与同支环锭纱接近。
MVS纱虽然在单纱强力上不如环锭纱,但在喷气织机上用Mrs纱织布的停台率却比环锭纱织布的停台率低,纱线毛羽非常少,比环锭细纱的毛羽大大减少,具有非常好的抗起球性能,纱体蓬松,具有很好的吸湿及快速去湿性能。
国内喷气纺设备的引进和使用较早,但发展缓慢。
1985年江苏丹阳棉纺厂首次引进了日本村田MJS一801喷气纺设备。
其后,在湖北嘉鱼、湖北蒲析、山东五莲、河南焦作、广东肇庆、天津、西北等地也陆续引进喷气纺。
我国是一个棉纺大国’,但喷气纺少之又少,仅占纺纱能力的0.03%左右,剔除外资设备供直接出口,国内市场的覆盖率更小。
.9R.有重要影响。
此外,环锭纱的结构主要是在三角区中形成的,其形成过程或机理决定了具有纱中纤维预张力不均匀一致的特点,因而,使后续工序及最终产品受到拉伸时预张力大的纤维会首先断裂,可见纱线的强力并不能发挥纱中所有纤维的作用,纱线的强力达不到应有的水平。
喷气纺的原理

喷气纺的原理喷气纺是一种用于制造合成纤维的纺织设备,它采用高压气流将熔融的聚合物喷射到环境中,形成纤维。
它与传统纺纱方式相比,具有高产量、快速生产、低成本和灵活性高等优点。
下面我将详细介绍喷气纺的原理。
喷气纺的原理主要分为三个关键步骤:熔融纤维聚合物的形成、纤维形成的喷射过程以及纤维固化的步骤。
首先,纺丝原料(聚合物颗粒)经过加热和挤出处理后,形成粘稠的熔融物。
这个过程通常在熔融纺丝机中进行,其中聚合物颗粒通过高压螺杆从进料口输送到螺杆筒中。
在螺杆筒中,聚合物颗粒被螺杆带动并加热,从而在高温和高压下熔化。
接下来,熔融的聚合物通过纺丝口进入喷嘴,喷嘴通常位于纺丝器上部。
纺丝器通过提供高速气流,将熔融的聚合物喷射到环境中。
这个高速气流(称为喷射气流)具有两个主要效果:一是将熔融的聚合物细化为纤维,并带走纤维形成过程中所产生的倍体剂;二是保持纺织过程中所需的纤维形成条件,例如温度和湿度。
聚合物的喷射过程中,纺织丝被拉伸并形成细长的纤维,这是通过喷射气流的冷却效应实现的。
高速气流使得聚合物熔融后的纺丝丝变得非常细小,同时也使得纺丝丝变得更长。
此外,喷射气流还将纺织纤维拉伸,并稳定纺织纤维的直径和形状,以获得一致性的纤维质量。
最后,从喷嘴中喷射出的纺织纤维在接触到空气后迅速固化。
此时,纤维内部的温度较高,但由于喷射气流的冷却作用,纤维会在短时间内冷却并固化。
这个过程中,纤维的形态和质量由多种因素决定,包括聚合物的性质、纺丝参数(如温度、压力和流量)以及环境条件(如温度和湿度)等。
总的来说,喷气纺的原理是利用高压气流将熔融的聚合物喷射到环境中,通过高速气流的冷却效应形成细长的纺织纤维,并在喷射过程中对纤维进行拉伸和固化。
这种纺织方法具有高效、低成本以及灵活性高等优点,广泛应用于合成纤维的生产中。
喷气涡流纺与环锭纺转杯纺三种纺纱方法综合对比分析

差(%) CVb% +0.5 +1.6 +1.7 2.01 1.46 1.38
环锭纺 转杯纺 喷气涡 流纺
从以上对比数据中可以看出: 条干CV%和细节-50%:环锭纺最好,其次喷气涡流纺,转杯 纺最差。 粗节+50%:环锭纺最好,其次喷气涡流纺,转杯纺最差。 棉结+200%:喷气涡流纺最好,其次环锭纺,转杯纺最差。 单纱断裂强度:环锭纺最高,其次涡流纺,转杯纺最低。 条干CVb%:喷气涡流纺最好,其次转杯纺,环锭纺最差。
涡流
切向 开口 进风孔
涡流管
负压装置
2 原料使用
三种纺纱方法由于成纱结构不一样,相同规格 的原料所纺出的纱在强力、条干方面差异较大 针对不同的纺纱方法和纺纱支数,需要选择不同 规格的原料来弥补各自成纱中的不足
环锭纺选用 原料规格为 1.67dtex×3 8mm 100%, 成纱纤维根 数为118根 转杯纺配置 ¢33mm纺杯, 所选原料 1.33dtex×32m m 100%,成纱 纤维根数为148 根 喷气涡流纺 选用原料为 1.33dtex×3 8mm 100%, 成纱纤维根 数为148根
生产效率(%) 97.4 96.0 95.2 94.4 93.1 91.7 90.0 87.8 85.9 每台每小时断头率(根) 204.1 280.2 320.4 370.7 416.1 440.4 455.4 469.8 513.1 折千锭时断头率(根) 2551 3503 4005 4634 5201 5505 5693 5873 6414
3 工艺流程
3 喷气涡流 纺
FA002抓棉机→SFA035混开棉机→FA106A梳针开棉机→FA161振 动棉箱给棉机→A076F成卷机→FA204C梳棉机→FA306A并条机 (二道)→RSB D401自调匀整并条机→种纺纱方法生产的19.7tex粘胶纱成纱质量指标对比 原料 纺纱方 法 ( 条干 细节50% 3 13 6 dtex·mm) CV% 规格 1.67×38 1.33×32 1.33d×38 12.67 13.80 13.39 粗节 +50 % 17 38 29 棉节 +200 % 28 59 23 单纱强 力CV% 9.3 8.9 10.0 单纱断裂 强度 (cN/tex) 15.1 11.5 12.8 百米重 量 CV% 1.8 1.1 0.9 重量偏 条干
喷气涡流纺纱技术发展现状与理论研究进展

喷气涡流纺纱技术发展现状与理论研究进展
王泳智;奚传智;金凯;裴泽光
【期刊名称】《纺织器材》
【年(卷),期】2024(51)3
【摘要】为提高喷气涡流纺纱成纱质量,阐述喷气涡流纺纱设备的革新历程,及导引体、涡流管、纺锭等喷嘴关键元器件设计优化进展;以麻纤维纱线、包芯纱、功能性纱线为例,介绍喷气涡流纺纱线产品开发要点及成果;详细分析喷气涡流纺喷嘴内气流流动特性,模拟纤维在气流场中的运动。
指出:喷气涡流纺纱技术向速度更快、自动化程度更高、纱线品种更加多样的方向发展,但不同纤维原料成纱质量差距较大,应借助仿真模拟技术研究喷嘴内流场分布和纤维运动规律,掌握纤维加捻成纱的根本原理,同时加强喷嘴结构设计和工艺参数优选方面的研究。
【总页数】6页(P11-16)
【作者】王泳智;奚传智;金凯;裴泽光
【作者单位】东华大学机械工程学院
【正文语种】中文
【中图分类】TS104.7
【相关文献】
1.转杯纺与喷气涡流纺新型纺纱技术发展与进步的新亮点——参观2014中国国际纺织机械展览会暨ITMA亚州展览会的启示
2.喷气涡流纺纱与转杯纺纱的对比分
析3.喷气涡流纺纱捻回数的理论研究4.喷气纺纱与涡流纺纱的成纱机理及产品开发5.喷气涡流纺纱机及其关键技术的应用与研究进展
因版权原因,仅展示原文概要,查看原文内容请购买。
喷气涡流纺纱产品开发实践
喷气涡流纺纱产品开发实践
喷气涡流纺纱产品开发的第一步是需求分析。
在这个阶段,我们需要了解市场需求和竞争态势,确定产品的定位和目标用户群体。
通过市场调研和用户需求调查,我们可以了解到目标用户的喜好、购买能力和竞争产品的特点,为产品开发提供方向。
接下来是技术研发。
喷气涡流纺纱产品的核心技术是涡流喷射和纺纱技术。
在技术研发过程中,我们需要建立实验室和测试设施,进行工艺参数的确定和设备优化。
同时,我们还需开展纺纱工艺的研究和技术改进,以提高产品的质量和生产效率。
产品设计是喷气涡流纺纱产品开发的重要环节。
在产品设计过程中,我们需要考虑产品的结构、功能和外观设计。
首先,我们需要设计合理的结构,使得产品能够正常运行和维护。
其次,我们还需确定产品的功能,以满足用户的需求。
最后,我们需要进行外观设计,使产品具有美观的外观和符合人体工学的设计。
在产品开发的过程中,需要进行验证和调试。
通过样机制造和实际生产的验证,我们可以检验产品的稳定性和可靠性。
同时,还可以根据不同用户的反馈和意见,进行产品的调整和改进。
市场推广是喷气涡流纺纱产品开发的最后一步。
在市场推广阶段,我们需要建立销售渠道和推广计划,进行产品宣传和推广活动。
同时,还需要提供良好的售后服务,以增强用户对产品的信心和忠诚度。
综上所述,喷气涡流纺纱产品开发是一个复杂而庞大的工作,需要从需求分析、技术研发、产品设计、验证和调试以及市场推广等多个方面进
行。
只有经过科学的实践和持续的努力,才能开发出具有竞争力和市场价值的喷气涡流纺纱产品。
涡流纺
– 动力消耗少 PF一1型涡流纺纱机生产单位重量纱所需 的动力比BD—200型转杯纺纱机少10%一12%,比环锭 纺纱机少15%;而且,机构料损耗少,噪音低。
• 经济效果比较显著 在单位产量相同条件下,采用涡流纺纱所需要的 占地面积为环锭纺纱的60%,所需要的生产工人为环锭纺纱的53%, 劳动生产率为环锭纺纱的1.86倍.单位产品的加工费用为环锭纺纱的 70%。
内,成纱结构最为紧密, 纱线外观光洁、毛羽少,纱 线加捻螺旋结构清晰可见, 纤维几乎没有内外转移。 – 这种纱线结构的改善是通过纺纱加捻三角区的消除而 获得的。
涡流纱的性能
• 喷气涡流纺的成纱结构与环锭纺相似,但还存在 有纱芯,约60 %的纤维在纱中呈螺旋排列。
• 在纺纯棉时喷气涡流纺单纱强力和条干比相应环 锭纱稍差些,其它指标都与环锭纺相当,毛羽比 环锭纱大幅减少。
涡流纺纱
• 要点:
– 1、了解涡流纺的成纱原理 – 2、了解涡流纺纱的特点 – 3、掌握涡流纱的成纱结构特点与纱线性能 – 4、了解涡流纺的适纺原料与适应产品
涡流纺纱概述
• Airvortex spinning,属自由端纺纱 • 1957年德国的哥茨莱德(Gatzfreid)首先设计发明. • 波兰生产的 PF一2型和PF-2RA型涡流纺纱机,纺纱速度达
• 涡流纺纱还具有如下优点:
– 工艺流程短 用二并条子喂入直接纺成筒子纱,甚至可以省去并条 工序,但必须提高生条均匀度,这就需在梳棉机上采用自调匀整 装置。
– 制成率高 它是在负压条件下纺纱,没有飞花外溢现象,由于涡流 纺纱断头少,回花损失也少,制成率高达99%以上。
– 劳动环境好 机台清洁,操作方便,接头方便,断头后涡流管内无 积花,不需要清扫。
喷气涡流纺纱与转杯纺纱的对比分析
同的工艺参数在 两种 纺纱设备上进行生产 , 对生产效率 、 品质 量 、 产 生产成本作对 比分析 。指出了喷气涡流纺
纱 的优 越 性 与有 待解 决 的 问 题 。 关键词 : 气涡流纺纱 ; 纱机理 ; 构 ; 量分析 喷 成 结 质 中 图分 类 号 : S O . 文 献 标 识 码 : 文 章 编 号 :0 9 2 5 2 1 ) 5 0 1 -0 T L47 B 1 O ~ 6 X(0 0 0 - 0 3 3
的 比率 增加 , 成 柔 软 的 实捻 的纱 ; 是 距 离 过 大 , 形 但 则 落棉 率也 增 加 。于 是 通 常将 距 离 L设 定 为 比供
给 棉条 的平 均纤 维 长度稍 微 短些 。 喷气 涡流纺一直 以其输 出速度高 、 纺较小 线密 可
度纱支 的特 性 而被 业 内人 士 所 看好 。因其 取消 了高 速 回转的加 捻部件 而利用 高速 回转的压缩空气对 纱条 进行 加捻 , 而使 出纱 速度 可 高达 30 0m, n其 从 5 ̄40 / , mi
的作 用 紧贴 在 凝 聚槽 的表 面 , 后 纱 头 压 着纤 维 条 然
・
作者简介 : 洪新强 (93 , , 北黄 冈人 , 16 一)男 湖 工程 师, 主要从
1 纺纱原 理
这个 反转 纤维 群 , 对应 不 同线 密 度 的有孔 中 空锭 被
子拉人 时 , 已经 形 成 芯 的纤 维 的 四周 朝 一 定方 向 在 ( 旋转 气 流方 向) 绕 , 成 涡流纱 。所 以 , 前 罗拉 缠 形 从 的钳 口点 到锭 子 前 端 为 止 的距 离 ( 中 L) 是 决 定 图 , 涡流纱 物性 的重 大 因 素 。加 大 该 距 离 , 则缠 绕 纤 维
技术|几种主流纺纱方法的发展方向和技术优势
纺纱方式种类繁多不同的新型纺纱方法有其不同的纺技术丨几种主流纺纱方法的发展方向和技术优势随着科技的发展和社会的进步,人类对纺织品的要求不断提高,对纱线品质的要求也提出了更高的标准。
因此,发现新的纺纱原理,研究新的纺纱方法,以提高纺纱产量、质量和开发新的纱线品种已成为努力的方向之一。
人类纺纱技术的发展经历了一个漫长的过程,环锭纺纺纱方法的出现,把纺纱技术推进到了一个新的阶段,但是,由于环锭纺纱受成纱机理的限制,纺纱速度和产量难以再进一步大幅度提高,而且,环锭纺系统在加工过程中,还存在许多不合理的方面。
因此,开辟新的纺纱原理,研究新的纺纱方法,以提高纺纱产量、质量和开发新的纱线品种已成为人们努力的方向之一。
新型纺纱技术的发展一直未曾停止,从20世纪的50 年代起,就先后涌现出了成纱机理与环锭纺截然不同的转杯纺、喷气纺、静电纺、摩擦纺、平行纺、涡流纺、自捻纺等新型纺纱技术。
近年来,又出现了喷气涡流纺(MVS) ,这些新型纺纱方法和技术的出现,突破了传统纺纱的成纱机理,使得纺纱速度的提高、卷装的增大成为了可能,使劳动生产率大幅度提高,花色品种大大增多,从而有力地推动了纺纱技术的发展。
纱器机构和成纱机理(主要是加捻特点),其成纱结构、成纱性能以及进一步的应用也有较大的不同。
可以分为非环锭加捻新型纺纱技术(自由端纺纱方法、非自由端纺纱方法)和基于环锭加捻(锭子加捻)的新型纺纱方法两大类。
对于非自由端纺纱,如喷气纺、自捻纺等,其纤维须条在纺纱过程中是完全连续的。
所以,其纤维的喂入通常是由与环锭纺相类似的罗拉牵伸装置来完成,罗拉牵伸过程中对纤维有较强的控制,从而使纤维的排列更加伸直、平行,为成纱质量提供了保证。
此外,非自由端纺纱中,纤维在加捻时,两端均受到机械控制,使成纱紧密度高,纤维在成纱的过程中伸直平行度好。
对于自由端纺纱,如转杯纺、摩擦纺、静电纺等,由于纤维成纱是通过真捻的方式完成的,因此,必须在纤维的输送过程中确保产生一个断裂点(自由端),以满足加真捻的要求。
- 1、下载文档前请自行甄别文档内容的完整性,平台不提供额外的编辑、内容补充、找答案等附加服务。
- 2、"仅部分预览"的文档,不可在线预览部分如存在完整性等问题,可反馈申请退款(可完整预览的文档不适用该条件!)。
- 3、如文档侵犯您的权益,请联系客服反馈,我们会尽快为您处理(人工客服工作时间:9:00-18:30)。
喷气纺纱和涡流纺纱的产品特点及其发展
于修业
(中国纺织大学)
1 引言
喷气纺和涡流纺的原理起源讴早,但作为新型纺纱方法还是七十年代以后分别由日本村田公司(Murata)和波兰罗兹公司(Lods)研制成功的。
日本村田公司1980年推出MJS-801喷气纺纱机,以后分别在历届国际纺织机械展览会上展出。
波兰罗兹公司1975年在米兰国际纺织机械展览会上展出过PF一1型涡流纺纱机。
这两种新型纺纱有它们的共同点:即都是利用气流旋转形成涡流场对纱条进行加捻。
加捻机构都很简单,投有高速回转机件,适应高速生产,纺纱速度一般在l50~200米/分,但它们又有截然不相同的成纱机理;喷气纺属于非自由端纺纱,纱的结构是假捻一退捻一包缠纱,而涡流纺则是自由端纺纱。
由于两种纺纱适纺的范围和产品有局限性,对它的成纱结构及特点人们的认识还不充分,使之研制和发展受到了不同程度的影响。
但从纺纱原理和纱的结构来看都有独到之处,它们的产生和进一步发展.对纺织工业技术和产品结构的影响将会起着不能忽视的作用.
2 纱的结构特点及其产品
喷气纺纱是把罗拉牵伸输出的须条,经两个气流旋转方向相反的双喷嘴所形成的涡流场推动纱条回转,对纱条进行加捻成纱。
第二喷嘴的气压和旋转能量大于第一喷嘴,第一喷嘴产生的回转气流只能使第二喷嘴对纱条施加的捻度解捻,使这段纱条呈弱捻状态,同时使前罗拉输出须条的边纤维形成半自由状态的开端纤维,然后再以反向包覆在纱的表面。
当纱条通过第二喷嘴后,由于假捻而反方向迅速退捻,在退捻力矩作用下,外表包覆的开端纤维更紧密地包缠在纱芯上,成为纱芯纤维基本平行,表面有捻的包缠喷气纱,如图1所示。
图1 喷气纱的形成
喷气纺最适合纺涤棉混纺纱,纺纱号数(tex)可在29~9tex(20~60Nc英支),纱的强力为同等环锭纱的90~95%;条干均匀、强力不匀低、纱疵、长毛羽少[6、7]。
但纤维一端缠在纱芯上,头端留在纱的表面,呈0.5毫米以下短羽毛较多;适宜制机织和针织物,织物手感硬、挺、膨松、丰满、厚实、透气性好、耐磨、染色性能好。
目前国内喷气纺的大宗产品如表1所示。
表l 喷气纺纱的产品
T/C 中长
T/C 65/35,9tex 仿毛织物
股线,强力高、挺括、万米无接头
注:T/C 65/35代表涤(T)与棉(C)混纺,比例为65%与35%。
喷气纱做色织纬磨绒织物类产品.就会扬长避短,发挥了喷气纱的膨松短毛羽多、纤维一端缠在纱芯上的特点;比同类环锭纱织物显得绒平整、坚牢、厚实、外观纹路立体感强、耐磨、染色性能好等优点。
涡流纺纱则是采用刺辊分梳成单纤维,再输送进涡流管内,在涡流场的作用下形成回转的自由端纱尾环,绕涡流管中心回转而加捻成纱[8]。
如图2所示。
图2 涡流纺纱器
这种纺纱方法,实验证明,它对纤维的整齐度和纤维表面性状要求较高,最适宜于纺制腈纶纤维。
由于离心力的作用,使涡流管内的纱尾从引纱孔开始形成伞状锥形回转体。
如图3所示。
图3 锥形纱尾环
伞状锥形纱尾环,在涡流场内受气流推动,产生的回转速度为:
ωy=ω-C dy3 r3
式中:ωy--纱条回转角速度;ω--涡流回转角速度;dy --纱条直径;r--纱条偏离涡流管中心距离;C--常数(与阻力系数、纱条刚度有关)。
从式中可以看出,纱条回转速度ωy,即是纱条所获得的捻度,是随纱条偏离涡流管中心距离r和纱条直径dy(号数)的变化而改变。
这一性质使涡流纱的捻度可随纺纱号数的不同而自行调节,通过实验发现这种加捻的特点是捻度与强力的关系不象环锭和气流纱那样,曲线斜率小。
如图4所示,捻度在较大范围变化对纱的强力影响不大。
图4 捻度与强力的关系
从图2可以看出,喂入涡流管内的单纤维从喂入口进入,碰到纺纱头而弯曲,再沿纺纱头下滑与纱尾环接触而被抓取,随机地添加在纱尾环上,由于纤维的转移、伸直、凝聚和加捻成纱全部利用气流的吸力和旋转来完成的,所以纱内的纤维平行度和定向性较差,打圈纤维多,表面层纤维则是包卷状态,成闭环形毛羽,纤维在纱中的分布状态如表2所示。
表2 纤维在涡流纱内的形态
由于上述纱的结构状态,涡流纱强力是同等环锭纱的60%~70%,但涡流纱做起绒织物,其强力却接近环锭纱起绒织物的强力,实验对比资料如表3表4所示。
表3 纱的试验
表4 起绒坯布试验
试验表明,涡流纱织物起绒后的强力只降低5%左右,环锭纱织物起绒后的强力降低了40%之多。
其原因是涡流纱中打圈纤维多,呈闭环形毛羽,纤维两头端均缠绕在纱芯上,起绒后,表面纤维破拉断,不影响承担强力的纱芯;而环锭纱织物起绒时,拉断了纱纤维,纱的强力就会大幅度下降。
又因为涡流纱织物起绒后,被拉断的纤维另一端紧紧钩住纱芯,绒面没有僵斑,绒毛平整细密,起绒厚度厚、耐磨、保暖、坚牢、落毛率少,这是涡流纱独特的性质,是其他纺纱不能与之相比的极大优点。
目前用涡流纱纺制的产品如表5所示。
3 技术经济对比
喷气纺纱在国内经过较长时间的生产实践,作了较系统的技术经济分析,并与环锭和气流纺进行了对比,见表6、表7表8所示。
表5 涡流纱产品
表6 成纱质量对比
对比分析表明:喷气纱强力约低于环锭l0%;重不匀率、强不匀率、条干、结杂都优于环锭纱,也优于气流纱,乌氏试验的棉结有时珞高于环锭,喷气纺产量是环锭纺的7.35~8.53倍;占地面积比环链减少25%左右,比气流纺减少15%左右;用人工约减少60%;设备投资比国产环锭纺设备高近2倍.与环锭纺引进设备的投资相近;用电比国产环锭高40~50%,与引进设备相当,低于气流纺;机物料消耗费比环锭低30%;综合成本因国内电价高、工资低而高出环锭6~7%。
表7 喷气纺技术经济分析一
表8 喷气纺技术经济分析二
涡流纺在世界范围内纱锭不多,难作系统的分析,波兰早期曾对涡流纺、气流纺、环锭纺三者作过对比分析,见表9所示。
国内对国产涡流纺纱机与环锭细纱机也做过比较,见表10、表l1所示从初步分析看出,涡流
纺产量是环锭纺的8倍,单位面积产量是环锭的2.4倍;耗电略高于环锭,低于气流纺;投资费用也低于环锭和气流纺。
表9 涡流纺技术经济分析
表10 涡流纺技术经济分析
表l1 涡流纺纱技术经济分析
4 前景展望
根据国内外喷气纺生产实践,证明该机技术先进,涤棉混纺中细支纱的产品有一定特色,特别在磨绒织物更有优越性,可以代替部分环锭纺的产品。
由于喷气纺在纺纯棉纱时的强力较低,使之应用范围和发展受到一定限制。
1988年日本村田公司对MJS-881改进了牵伸装置和喷嘴结构,推出了MJS-802、MJS-881新型的喷气纺纱机,可纺涤棉,也可纺纯棉中细支纱和双纱合股及花式线。
该机纺纱质量如表12所示。
表12 MJS-802,MJS-881纺纯棉纱的质量指标
这种新机型虽然纺纱质量(单强)还不高,但它的出现使喷气纺纱技术的发展前景极为可观;如果能在牵伸装置和喷嘴设计进一步研究,使纺纱质量进一步提高,并使应用范围更广泛,在其他类纤维纺纱(毛、麻)领域中也能应用,将对整个纺纱工艺技术和产品结构起着巨大的影响。
而涡流纺,目前存在着对纤维的整齐度、纤维表面性状要求较高,纺纱支数偏低,强力电不高、条干较羞,适纺产品范围狭窄等问题,有待进一步研究但是。
它能生存至今的原因是:可以纺腈纶纱做起绒织物优于各种纺纱的起绒织物。
从纺纱原理看也是有生命力的。
一旦技术关键得到突破,就尝有所前进。