(完整版)不同纺纱方法的成纱结构和特性
纱线的分类与结构特征

纱线捻度
表示纱线紧密程度的指标,合适的捻度使纱线更加牢 固。
纱线毛羽
反映纱线表面毛糙程度的指标,毛羽越少品质越好。
提高纱线品质的途径与方法
选用高品质原料
使用高品质的纤维原料能够从 根本上提高纱线的品质。
优化纺纱工艺
通过改进纺纱工艺和设备,可 以降低纱线的不匀率和毛羽数 。
捻度与捻向对纱线的强度、弹性、 耐磨性等性能有重要影响。不同 捻度和捻向的纱线适用于不同的 织物品种和生产工艺,如牛仔布 需要使用高捻度纱,而针织品则 需使用低捻度纱。
纱线的结构形态与外观特征
定义
纱线的结构形态是指纱线内部纤维的排列方式和结构特点,而外观特征是指纱线的颜色、光泽、条干等表面特征。
分类
随着技术的进步,高性能纤维纱线的 生产成本逐渐降低,其应用领域也在 不断扩大,为纺织行业的发展提供了 新的机遇。
智能化纺纱技术的应用
智能化纺纱技术是指通过自动化、数字化和智能化的技术手 段,提高纱线生产的效率和质量,降低能耗和减少人工干预 。
智能化纺纱技术的应用,可以实现纱线生产的自动化、连续 化和智能化,提高生产效率和产品质量,降低生产成本。
可分为天然纤维纱线和化学纤维纱线两大类。天然纤维纱线包括棉纱、毛纱、麻纱等,化 学纤维纱线则根据原料和制作工艺的不同,可以分为人造纤维纱线和合成纤维纱线。
按纺纱工艺分类
可分为环锭纺纱、气流纺纱、静电纺纱、涡流纺纱等。不同的纺纱工艺会对纱线的结构和 性能产生影响。
按用途分类
可分为机织用纱、针织用纱、起绒用纱、特种用纱等。不同用途的纱线在品质、性能和结 构上都有一定的要求和特点。
应用
线密度是纱线的重要参数之一, 它直接影响着织物的风格、质地、 手感以及生产成本等。不同线密 度的纱线适用于不同的织物品种 和生产工艺。
(完整版)主要新型纺纱的比较

主要新型纺纱的比较1、成纱原理:转杯纺依靠调整回转的纺杯,将纱尾贴紧在纺杯内壁聚槽内,而头端为引纱罗拉握持并连续输出加捻成纱。
喷气纺靠两只喷嘴喷射相反方向的回旋气流,对由牵伸装置输出的须条先加捻后解捻,表面纤维形成包缠成纱。
摩擦纺一般用两只同向回转的摩擦元件,对其楔形区的纤维施加摩擦力偶,使纤维束滚动而加捻成纱。
2、成纱截面中纤维根数不同:喷气纱中最少纤维根数略高于环锭纱,可纺中低线密度纱;摩擦纺和转杯纺中的最少纤维根数较多。
3、对纤维性能要求不同:影响转杯纱强力的主要因素是纤维的强力和线密度,摩擦纱则是纤维的摩擦因数和强力。
4、纺纱速度和成纱线密度:环锭纺的可纺线密度覆盖面最广,但产量太低,各种新型纺纱的纺纱速度都比环锭纺高,但可纺线密度有局限性5、新型特点:新型纺纱取消了锭子、筒管、钢领、钢丝圈等加捻卷绕元件,并将加捻和卷绕作用分开完成,具有产量高,细纱机的产量取决于锭子的速度,而锭速的提高,一方面受钢丝圈速度的限制,另一方面受气圈张力的限制;卷装大,环锭细纱机上增大卷装的途径是增加筒管长度和加大钢领直径,但筒管加长则气圈高度加长,钢领加大则钢丝圈线速度增大,这些都会导致断头增多,而新型纺纱方法将加捻和卷绕分开进行,可直接纺成筒子纱;工艺流程短,新型纺纱采用条子喂入,直接纺成筒子纱,省去粗纱、络筒两道工序。
转杯纺1、原理:纺杯高速旋转,纺杯内便产生离心力,离心力可使从分流腔转移到纺杯内的棉纤维产生凝聚而成为须条,须条被加捻后便成为纱条。
2、工艺过程:条子从条筒中引出送入喂给罗拉,喂给罗拉与喂给板将条子向前输送,经分梳辊分梳成单纤维,被补风口和引纱管的气流吸入纺纱杯,沿纺纱杯壁滑入凝聚槽形成凝聚须条,由于纺纱杯高速回转产生的离心力使引纱纱尾贴附于凝聚槽面而与须条连接,并被纺纱杯摩擦握持而加捻成纱。
3、转杯纱结构与性能:转杯纱由纱芯与外包缠纤维两部分组成,内层的纱芯比较紧密,外层的包缠纤维结构松散;环锭纱没有纱芯,纤维在纱中大多呈螺旋线排列。
棉纺手册 第三篇 成纱 第二章 转杯纺纱

第二章转杯纺纱(棉纺手册P687-775)第一节转杯纺纱的技术特点与机械结构一、技术特点转杯纺纱是通过高速回转的转杯及杯内负压完成纤维输送、凝聚、并合、加捻成纱的一种新型纺纱方法(属于自由端纺纱范畴)。
现代转杯纺纱机都是通过分梳辊将喂入条子分梳成连续不断的纤维并随气流均匀地输入转杯,由引纱卷绕机构将转杯纺的纱引出并卷绕成纱筒。
转杯纺纱使加捻与卷绕分开,解决了高速和大卷装间的矛盾。
转杯纺纱的原料以棉为主,还包括化纤、毛、麻、丝等。
废棉和再生纤维在转杯纺纱厂里也可使用。
转杯纺纱与传统的环锭纺纱相比,具有高速高产、大卷装、缩短工序、改善劳动条件、使用原料广泛、成纱均匀、结杂少、耐磨和染色性能好等特点。
因此,转杯纺纱是目前技术上最成熟、应用面最广、经济效益十分显著的一种新型纺纱方法。
二、机械结构和纺纱流程转杯纺纱的截面示意图如图3-2-1所示,转杯纺纱机的机械结构主要由喂给分梳机构、排杂回收机构、纤维输送机构、凝聚加捻机构、引纱卷绕机构和负压排风系统组成。
转杯纺纱机的电器、仪表和自动控制部分完成了机电一体化与自动化。
图3-2-1 转杯纺纱机截面示意图纺纱器是一个由喂给分梳机构、成纱机构及引纱管组成的独立部件,其示意图如图3-2-2所示。
转杯纺纱的纺纱流程与纤维流的运动规律见图3-2-3。
图3-2-2 纺纱器示意图1—转杯2—分梳辊3—排杂区4—假捻盘5—阻捻器6—输纤通道7—喂给罗拉8—喂给板9—引纱管10—可调补气阀图3-2-3 转杯纺纱的纺纱流程与纤维流的运动规律V1—条子喂给线速度V2—分梳辊线速度V3—输纤通道入口速度V4—输纤通道出口线速度V5—转杯滑移面线速度V6—转杯凝聚槽线速度V7—纱剥离点线速度V7—V6—纱剥离点相对转杯的线速度V8—引纱线速度V9—卷绕线速度三、转杯纺纱机的分类1.按转杯内负压的形式分类转杯可分为两类,排气式转杯(如图3-2-4)和抽气式转杯(如图3-2-5)。
排气式是在转杯上自身打有排气孔(一般是8个),回转时类似离心风扇的作用,在转杯内产生负压;抽气式是转杯自身无排气孔,依靠外界抽气在转杯上口与罩盖之间抽吸,产生转杯内负压。
纱线的结构知识
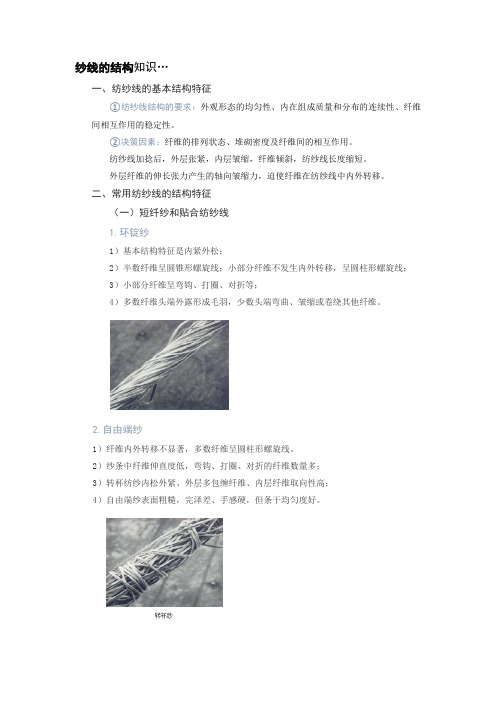
纱线的结构知识…一、纺纱线的基本结构特征①纺纱线结构的要求:外观形态的均匀性、内在组成质量和分布的连续性、纤维间相互作用的稳定性。
②决策因素:纤维的排列状态、堆砌密度及纤维间的相互作用。
纺纱线加捻后,外层张紧,内层皱缩,纤维倾斜,纺纱线长度缩短。
外层纤维的伸长张力产生的轴向皱缩力,迫使纤维在纺纱线中内外转移。
二、常用纺纱线的结构特征(一)短纤纱和贴合纺纱线1.环锭纱1)基本结构特征是内紧外松;2)半数纤维呈圆锥形螺旋线;小部分纤维不发生内外转移,呈圆柱形螺旋线;3)小部分纤维呈弯钩、打圈、对折等;4)多数纤维头端外露形成毛羽,少数头端弯曲、皱缩或卷绕其他纤维。
2.自由端纱1)纤维内外转移不显著,多数纤维呈圆柱形螺旋线。
2)纱条中纤维伸直度低,弯钩、打圈、对折的纤维数量多;3)转杯纺纱内松外紧、外层多包缠纤维、内层纤维取向性高;4)自由端纱表面粗糙,完泽差、手感硬,但条干均匀度好。
3、层压纱和结构纱的结构特征层压纱的结构特征,由其长/短、短/短、长/长贴合比例和张力所决策。
这种结构可有效提高纱强,增加纱的连续性和平稳性。
结构纱的结构特征,由其纤维分布方式和聚集密度决策。
(二)长丝纱结构特征1、无捻长丝纱结构特征:横向结构极不稳定,柔软。
2、有捻长丝纱结构特征:纵横向都很稳定,硬挺。
3、变形纱结构特征:整理方法不同,卷曲形态不同,如螺旋形、波浪形、锯齿形、环圈形等。
堆砌密度和排列及其分布也不同。
(三)股线的结构特征一次并捻单纱的根数在3根以内股线结构稳定;4~5根有不稳定因素,6根及以上,必定回到3根的稳定态。
单纱和股线的捻向相反时,捻回稳定,股线结构均匀稳定。
功能性纱线———抗紫外线纱、防辐射纱、抗菌纱功能性纤维对人体具有特种保健功能的纤维称功能性纤维。
常见的品种有远红外纤维、抗紫外线纤维、电磁屏蔽纤维、负离子纤维、抗菌纤维、阻燃纤维、麦饭石纤维、远红外纤维、抗紫外线纤维、电磁屏蔽纤维、负离子纤维、抗菌纤维、阻燃纤维、麦饭石纤维。
(完整版)不同纺纱方法的成纱结构和特性

不同纺纱方法的成纱结构和特性当前棉纺领域有5种实用的、倍受关注的纺纱方法,即传统环锭纺、转杯纺、喷气纺、涡流纺和改进环锭纺——紧密纺。
环锭纺纱方法已有逾一个半世纪的历史,而后四者是在近几十年甚至是近几年发展起来的,统称为新型纺纱方法。
不同的纺纱方法无论在产量、质量方面,还是在成纱结构和特性方面,都有各自非常独特之处。
1 成纱机理1.1 传统环锭纺环锭纺纱是将牵伸、加捻和卷绕同时进行的一种纺纱方法,粗纱在牵伸系统中被牵伸至所要求纱支的须条,再经钢领、钢丝圈的加捻和卷绕形成一根纱线。
由于牵伸作用,主牵伸区中的须条宽度是所纺纱线直径的数倍,此时各根纤维抵达前钳口线时呈自由状态。
当这些纤维离开前钳口线后即被捻合在一起,这样就形成了一个纺纱加捻三角区。
此纺纱加捻三角区阻止了边缘纤维完全进入纱体,部分边缘纤维脱离主体形成飞花,较多的边缘纤维则是一端被捻入纱体,而另一端形成毛羽。
这些纤维不但对纱线的均匀度、弹性等性能起消极作用,且对纱线的强力极其不利。
另外,在加捻时处于三角区外侧的纤维受到的张力最大,而在中心的纤维受到的张力最小,故成纱时这些纤维的初始张力不等,从而影响成纱的强力。
这些都是传统环锭纺纺纱三角区造成的缺陷。
1.2 转杯纺转杯纺又称气流纺,属于自由端纺纱方法。
直接喂入纺纱器的棉条经分梳辊分梳成了单纤维状,纤维靠分梳辊的离心力和纺杯内负压气流的作用脱离分梳辊表面经输棉管道而进入纺杯,并在凝聚槽中形成一个完整的纤维环,纤维环随着纺杯高速旋转,在接头纱的作用下,随着捻度不断的传递和连续剥离纤维束而成纱。
1.3 喷气纺喷气纺纱以日本村田公司制造的MJS(Murata Jet Spinner)机型为代表。
棉条直接喂入牵伸装置,经牵伸后的须条进入喷嘴,两个方向相反的高速旋转气流对纱条进行假捻并包缠成纱,纱条引出后经电子清纱器去除疵点后被卷绕在筒子上。
1.4 涡流纺涡流纺纱是继MJS之后,村田公司推出的新一代的喷气纺纱技术MVS(Murata Vortex Spinning)。
不同纺纱方法的成纱结构和特性

各种纺纱方法简介(1)环锭纺纱<RING SPINNING>(2)无捻纺纱<TWISTLESS YARN PROCESSING>(3)自捻纺纱<SELF-TWIST SPINNING>(4)离心纺纱<CENTR FUGAL SPINNING>(5(帽锭纺纱<CAP SPINNING>(6)走绽纺纱<MULE SPINNING>(7)自由端纺纱<OPEN-END SPINNING>(8)气流纺纱(转杯纺纱)<ROTOR SPINNING>(9)静电纺纱<ELECTRO STATIC SPINNING>(10)涡流纺纱<VORTEX SPINNING>(11)喷气纺纱 <JET SPINNING.>(12)摩擦纺纱<FRICTION SPINNING>(13)尘笼纺纱(德雷夫纺纱)<DREF SPINNING>(1)环锭纺纱(ring spinning),是现时市场上用量最多,最通用之纺纱方法,条子或粗纱经牵伸后的纤维条通过环锭钢丝圈旋转引入,筒管卷绕速度比钢丝圈快,棉纱被加拈制成细纱.广泛应用于各种短纤维的纺纱工程.如普梳,精梳及混纺,钢丝圈由筒管通过纱条带动绕钢领回转.进行加拈同时,钢领的摩擦使其转速略小于筒管而得到卷绕.纺纱速度高,环锭纱的形态,为纤维大多呈内外转移的圆锥形螺旋线,使纤维在纱中内外缠绕联结,纱的结构紧密,强力高,适用于制线以及机织和针织等各种产品.环锭纺(精梳)流程:清花间--梳棉--预并条--条并卷--精梳--头道并条--二道并条--粗纱--细纱--络筒环锭纺(普梳)流程:清花间--梳棉--头道并条--二道并条--粗纱--细纱--络筒(2)无拈纺纱(twistless processing)使用粘合剂使纤维条中的纤维互相粘合成纱的一种纺纱方法.粗纱经牵伸装置牵伸后,须条被送到加捻滚筒上,回滚筒上来自槽箱中的薄层粘合剂接触.纤维条由数根回转的小压辊与滚筒一起向前输送,其中一根小压辊还同时作轴向往复运动,将纤维条搓成圆形截面,并使每根纤维都能均匀地接触到粘合剂.圆形纤维条通过加热器烘燥,纤维互相粘牢成纱.纺纱速度可比常规纺纱方法大2~4倍,制成的纱可供织造用.(3)自拈纺纱(self-twist spinning)一种非传统纺纱方法.(siro yarn类同)将两根纤维条经牵伸装置拉细,由前罗拉、搓捻辊输出,在导纱钩处合.搓捻辊除回转外,并快速轴向往复运动,搓转纱条,使搓捻辊前后的纱条获得方向相反的捻回.在导纱钩处 合后的两根纱条,依靠它们本身的抗扭力矩自行拈合成双股自拈纱(ST纱),卷绕成筒子.自拈纱的形态特点是相邻纱段交替地呈正反方向的捻回,交替处为无捻回.在捻线机上加一个方向的捻度,制成加捻自捻线(STT纱).两组自捻纱以无捻区相位差90°配置并合而成的四股纱,简称“2ST纱”,再在捻线机上低捻并制成(2ST)T纱.两次自并称为“(ST)2”纱.用一根长丝代替自捻中一根单纱条时,可以相应地制成STM和(STM)T纱.此纺法专用于多股纱线上,如毛纺或仿毛化纤产品.高质量的自捻纱可直接用于纬编针织,但机织用经纱,须使用加捻自捻线,改善强力性能.(4)离心纺纱(centrifugal spinning)以高速离心罐(杯)和升降导纱管实施加捻卷绕的连续纺纱方法.粗纱经牵伸装置后由前罗拉连续输出纤维条,经导纱钩、导纱管进入高速回转的圆柱形离心罐中,纱条在离心力作用下紧贴于罐内壁而与罐子同转,使导纱管下端与前罗拉间的纱条受到加捻作用,并用导纱管下水平方向纱条转动速度落后于离心罐而产生卷绕.导纱管按一定规律升降,形成交叉卷绕的纱饼,卷绕达到一定长度要求时,前罗拉停止输出纤维条,导纱管上升退出离心罐,将空筒管急速下降到离心罐内,纱头钩住筒管下部的钩纱器,使纱饼上的纱退绕到筒管上,退绕完毕,取下满管.同环锭纺纱比较,功率消耗大,回丝多,断头难处理,纱重绕到纱管上,前罗拉需停转,影响生产率.现时很少人使用。
4.纺纱形式和纱线性能

环锭纺纱的性能特点
技术成熟,应用广泛 原料及品种的适应性较大 原料、纺纱工艺、品种规格决定纱线的基本性能 作为不同纺纱方法纱线性能的比较依据
紧密纺的成纱机理和纱线结构及性能
紧密纺的工艺过程
喂入:具有一定捻度的粗纱
工艺过程:
作用特点:在普通环锭纺的基础上减小加捻三角区
紧密纺的成纱机理和纱线结构及性能
涡流纺的成纱机理和纱线结构及性能
涡流纺的工艺过程
喂入:纤维条
工艺过程:
作用特点:
涡流纺纱的结构特征
包缠结构,存在真捻 表面有大量的螺旋加捻纤维,占60%左右 无捻或弱捻芯纤维,占30%左右 毛羽少,且有方向性
涡流纺纱的性能特点
强力高于一般喷气纺纱线 毛羽少 适合做包芯纱产品
赛络纺的成纱机理和纱线结构及性能
赛络纺的工艺过程
喂入:两根具有一定捻度的粗纱,间隔一定的距离
工艺过程:
作用特点:
赛络纺纱的结构特征
有类似于股线的结构 双组份结构 双色(多色)结构 不均匀结构
赛络纺纱性能特点
纱线机械物理性能的综合提升 双(多)组分产品 双(多)色产品
紧密赛络纺的成纱机理和纱线结构及性能
主要内容
短纤维纺纱的一般作用
环锭纺的成纱机理和纱线结构及性能 紧密纺的成纱机理和纱线结构及性能
赛络纺的成纱机理和纱线结构及性能
紧密赛络纺的成纱机理和纱线结构及性能 转杯纺的成纱机理和纱线结构及性能 涡流纺的成纱机理和纱线结构及性能
短纤维纺纱的一般作用
原料的初步加工
紧密纺纱的结构特征
结构紧密、表面光洁 纤维内外转移程度低于普通环锭纺纱 纤维取向度高于普通环锭纱
紧密纺纱的性能特点
纱线结构特点及概述应用详述

六、不同纺纱型式纱线的应用
(一)环锭纱
历史悠久, 无可争辩的优势 ,占有主导地位 1. 产品应用广泛:适应所纺的品种繁多 2. 中高档纱线体现其价值 。 3. 缺点:流程长、毛羽多。卷装小、纺短、差纤维差,用工多 4. 低支纱6---32市场气流纺取代 ,中支纱20---60市场喷气涡流纺取
3. 随着技术的进步和高档转杯纺设备的引进,转杯纱在针织领 域的应用将会大大增强,其比例可望达到6∶4。
• 改善毛羽、强力,满足高档次面料和织造的要求 • 应用范围拓宽、应用理念在改变
色织——应用最多,紧密纱首先得到了讲究生活质量、钟爱 高档纯棉服饰的欧洲人追捧,据介绍欧洲80 %男衬衫用紧 密纱面料;
白织——高支高密织物(防羽布、斜纹、直贡、缎条) 针织——也有很强优势:经编、纬编等,如常常可以省去烧
图4 不同纺纱方法成纱的捻势对比
3. 涡流纱中由于有高比例的平 行纤维,捻回力小,同样具有 良好的后加工特性。
曲水流觞 生态 校 园 !
五、不同纺纱型式纱线特性比较
(四)抗起球性:弹力棉布氨纶汗布 粘胶 100% Ne30+ 氨纶 40d
线圈横列 线圈纵行
起球等级 3.5
起球等级 1.0
曲水流觞
生态 校 园 !
曲水流觞 生态 校 园 !
五、不同纺纱型式纱线特性比较
(六)耐磨性
1. 纱线的耐磨性与纱线的结构密切相关 2. 环锭纱由于纤维大多呈螺旋线形态,当反复摩擦时
,螺旋线纤维逐步变成轴向纤维,纱线易失捻解体 而很快磨断,因而耐磨性较差。 3. 转杯纱、喷气纱和涡流纱均由纱芯和外包纤维两部 分组成,纱线表面包有不规则的缠绕纤维,纱线不 易解体,同时纱线表面摩擦系数大,在织物中纱与 纱之间的抱合良好,不易产生相对滑移,故耐磨性 提高。 4. 相对于环锭纱,紧密纺纱的纤维排列整齐顺直,纱 线结构紧密,纤维不易脱散,因而纱线的耐磨性佳
- 1、下载文档前请自行甄别文档内容的完整性,平台不提供额外的编辑、内容补充、找答案等附加服务。
- 2、"仅部分预览"的文档,不可在线预览部分如存在完整性等问题,可反馈申请退款(可完整预览的文档不适用该条件!)。
- 3、如文档侵犯您的权益,请联系客服反馈,我们会尽快为您处理(人工客服工作时间:9:00-18:30)。
不同纺纱方法的成纱结构和特性当前棉纺领域有5种实用的、倍受关注的纺纱方法,即传统环锭纺、转杯纺、喷气纺、涡流纺和改进环锭纺——紧密纺。
环锭纺纱方法已有逾一个半世纪的历史,而后四者是在近几十年甚至是近几年发展起来的,统称为新型纺纱方法。
不同的纺纱方法无论在产量、质量方面,还是在成纱结构和特性方面,都有各自非常独特之处。
1 成纱机理1.1 传统环锭纺环锭纺纱是将牵伸、加捻和卷绕同时进行的一种纺纱方法,粗纱在牵伸系统中被牵伸至所要求纱支的须条,再经钢领、钢丝圈的加捻和卷绕形成一根纱线。
由于牵伸作用,主牵伸区中的须条宽度是所纺纱线直径的数倍,此时各根纤维抵达前钳口线时呈自由状态。
当这些纤维离开前钳口线后即被捻合在一起,这样就形成了一个纺纱加捻三角区。
此纺纱加捻三角区阻止了边缘纤维完全进入纱体,部分边缘纤维脱离主体形成飞花,较多的边缘纤维则是一端被捻入纱体,而另一端形成毛羽。
这些纤维不但对纱线的均匀度、弹性等性能起消极作用,且对纱线的强力极其不利。
另外,在加捻时处于三角区外侧的纤维受到的张力最大,而在中心的纤维受到的张力最小,故成纱时这些纤维的初始张力不等,从而影响成纱的强力。
这些都是传统环锭纺纺纱三角区造成的缺陷。
1.2 转杯纺转杯纺又称气流纺,属于自由端纺纱方法。
直接喂入纺纱器的棉条经分梳辊分梳成了单纤维状,纤维靠分梳辊的离心力和纺杯内负压气流的作用脱离分梳辊表面经输棉管道而进入纺杯,并在凝聚槽中形成一个完整的纤维环,纤维环随着纺杯高速旋转,在接头纱的作用下,随着捻度不断的传递和连续剥离纤维束而成纱。
1.3 喷气纺喷气纺纱以日本村田公司制造的MJS(Murata Jet Spinner)机型为代表。
棉条直接喂入牵伸装置,经牵伸后的须条进入喷嘴,两个方向相反的高速旋转气流对纱条进行假捻并包缠成纱,纱条引出后经电子清纱器去除疵点后被卷绕在筒子上。
1.4 涡流纺涡流纺纱是继MJS之后,村田公司推出的新一代的喷气纺纱技术MVS(Murata Vortex Spinning)。
涡流纺的成纱原理是棉条直接喂入牵伸装置,经牵伸后的须条从前罗拉钳口输出,立即被纺纱器的直喷嘴中涡流所产生的负压吸入,形成芯纤维,当纤维的末端脱离前罗拉时,因涡流作用而扩张,覆盖在空心锭子表面,并沿着固定的空心内壁回转,随着纱条的向前运动,纤维末端缠绕于纱芯上使纱线获得捻度而成纱。
1.5 改进环锭纺——紧密纺紧密纺(Compact Spinning)亦称集聚纺。
它主要是在环锭细纱机牵伸装置前增加了一个纤维凝聚区,从牵伸装置前罗拉钳口线迁移出来的纤维束集聚在一条线上,基本消除了前罗拉至加捻点之间的纺纱加捻三角区,很好地解决了传统环锭纺纱存在的成纱强力、毛羽和飞花等关键问题,并给后续加工和产品质量带来一系列益处。
不同的机器制造商提供了多种用于凝聚这些纤维的专利,但其原理基本相同,都是旨在通过集聚作用,使须条中的纤维特别是边缘纤维和浮游纤维得到有效的控制,大大降低牵伸须条带的宽度,从而基本消除纺纱加捻三角区,生产出新型高质量的紧密环锭纱。
2 纱线结构形态不同纺纱方法有不同的成纱机理,纤维在纱线中的排列形态以及纱线的紧密度亦不相同。
图1为不同纺纱方法的成纱电子显微照片,从中可以看出明显的差异。
2.1 传统环锭纺纱线结构传统环锭纱中纤维基本上呈螺旋线排列,由于存在纺纱加捻三角区,纤维不能全部被加捻到纱体中去,较多边缘纤维一端被捻入纱体,另一端露在纱条外面形成毛羽,因而虽然环锭纱结构较为紧密,但纱条表面相对来说显得杂乱无序,光洁度较差。
2.2 转杯纺纱线结构转杯纱在加捻过程中,加捻区的纤维缺乏积极握持,呈松散状态,因而纤维伸直度差,纤维内外转移程度低。
纱的结构分纱芯和外包纤维两部分。
纱芯结构与环锭纱相似,比较紧密;外包纤维结构松散,无规则地缠绕在纱芯外面。
因此与传统环锭纱相比,转杯纱结构比较蓬松,外观较丰满。
2.3 喷气纺纱线结构喷气纱是一种双重结构的纱,一部分是几乎平行、无捻的芯纤维,另一部分是包缠在芯纱外部的包缠纤维。
喷气纱的结构较为蓬松,纤维间的间隙较大,包缠纤维与芯纤维的比例约为1∶9,包缠纤维将向心的应力施加于芯纤维条上,给予纱体必要的聚合力以承受外部应力。
2.4 涡流纺纱线结构涡流纱也是一种双重结构的纱,纱条的芯纤维是平行排列的、无捻度,依靠旋转气流的作用使末端纤维包覆缠绕于芯纤维外部加捻成纱。
但与喷气纱不同的是,涡流纱的外层覆盖纤维比重大(约60 %),以致内部未加捻的纤维几乎被完全覆盖,表面纤维排列则更近似于环锭纱。
2.5 紧密纺纱线结构紧密纺纱线中的纤维排列最为整齐清晰,从一定意义上讲,可能是纱线中理想化的纤维排列方式。
由于气流的收缩和聚合作用,纤维的端头均捻入纱线内,成纱结构最为紧密,纱线外观光洁、毛羽少,纱线加捻螺旋结构清晰可见,纤维几乎没有内外转移。
这是集聚纺纱最显著的特性。
这种纱线结构的改善是通过纺纱加捻三角区的消除而获得的。
3 纱条特性不同的成纱加捻过程,产生不同的纱线结构,也产生不同的产品特性。
3.1 强力纱线强力取决于纤维间的抱合力和摩擦力。
如果纤维的形态及其排列状态不良,即有弯曲、打圈、对折、缠绕等纤维存在,就相当于减短了纤维长度,削弱了纤维的接触程度,因而易产生纤维间的滑移,降低纱线强力。
经试验得知,如以环锭纱强力为1,那么其它种类纱线的强力为:转杯纱0.8 ~0.9,喷气纱0.6 ~0.7,涡流纱0.8,紧密纺纱强力最高为1.15。
图2直观地反映了不同纱线的强力对比情况。
3.2 毛羽纺织产品的手感和特性主要由毛羽多少决定。
从生产试验可清楚地看到:长度小于2 mm 的毛羽对生产过程和织物的外观质量影响不大,相反会使织物具有一种天然的柔软手感。
但是,长度超过3 mm以上的毛羽却是影响纱线质量的潜在因素。
相对于传统环锭纱,气流纱、涡流纱、紧密纱的1 ~2 mm的毛羽均有降低,而喷气纱由于缠绕纤维数量低,无捻纱芯覆盖少,因而有较多的短毛羽,当然,具体在纺纱过程中可以通过调整工艺参数来控制毛羽的数量。
图3为不同纺纱方法的成纱毛羽数的比较。
与传统环锭纱相比,非传统纺纱的有害毛羽数(>3 mm)显著降低,其中紧密纱约减少80 %,喷气纱约减少85 %,涡流纺纱则减幅达90 %以上,因而新型纱线均具有良好的后加工特性。
由于新型纱线结构使纱线表面更加稳定,后加工的毛羽增加量显著低于传统纱线。
特别是作为经纱,在浆纱时可节约浆料约50 %,大大提高织机效率,降低织造成本。
有资料介绍,在美国使用新型纱线每100 m布织造成本可降低2.4美元,飞花减少72 %。
3.3 耐磨性纱线的耐磨性与纱线的结构密切相关。
传统环锭纱由于纤维大多呈螺旋线形态,当反复摩擦时,螺旋线纤维逐步变成轴向纤维,纱线易失捻解体而很快磨断,因而耐磨性较差。
非传统纺纱在耐磨性方面有着明显的优势,转杯纱、喷气纱和涡流纱均由纱芯和外包纤维两部分组成,纱线表面包有不规则的缠绕纤维,纱线不易解体,同时纱线表面摩擦系数大,在织物中纱与纱之间的抱合良好,不易产生相对滑移,故耐磨性提高。
相对于环锭纱,紧密纺纱的纤维排列整齐顺直,纱线结构紧密,纤维不易脱散,因而纱线的耐磨性佳。
3.4 捻势捻势也是纱线的重要特性,并决定了织物的一些特性,如针织布的斜路。
图4 为不同纺纱方法的成纱捻势对比。
传统环锭纱和紧密纱为真捻纺纱,捻势大,易产生针织物的斜路和卷边,有时需用并线来给予弥补。
转杯纱、喷气纱、涡流纱的成纱结构,决定了其捻势小。
转杯纱Z捻和S捻同时存在,因而捻势最低,喷气纱中由于有高比例的平行纤维,捻回力小,同样具有良好的后加工特性。
3.5 抗起球涡流纱针织物耐磨性好,抗起球等级高。
这是因为涡流纱中间为平直芯纱,外层包覆缠绕纤维,纤维定向明显,纱摩擦系数大,织物内纱与纱之间摩擦性好,不易产生相对滑移,耐磨性提高,此外,起球还与成纱毛羽情况关系密切。
通过测试起球试验可看出:涡流纱织物4 ~4.5级,喷气纱4级,传统环锭纱2级,转杯纱2 ~3级,紧密纺纱3 ~4级。
4 纱线的应用4.1 环锭纱尽管出现了许多新型纺纱方法,但直到今天环锭纺仍存在无可争辩的优势,在所有纱线中占有主导地位,产品应用广泛。
这是由于环锭纺机构简单、适纺范围广、成纱质量好。
但环锭纺加工过程长,质量进一步提高受到限制,特别是纱线毛羽多,影响了在一些产品上的应用,如高档衬衫面料。
4.2 转杯纱转杯纺纱产品应用领域比较宽,尤其在牛仔布、针织布两大系列面料应用上有得天独厚的优势。
因为转杯纺大多以生产粗支纱为主,外松内紧的纱线结构能获得较好的染色牢度和较深的色泽,从而形成牛仔面料蓝中透白的独特风格。
目前我国转杯纱在机织、针织的应用比例约为9∶1,随着技术的进步和高档转杯纺设备的引进,转杯纱在针织领域的应用将会大大增强,其比例可望达到6∶4。
4.3 喷气纱喷气纱、涡流纱能彻底消除针织物的扭矩和斜度,因而一出现即成为针织市场的主流应用产品,喷气纱针织物抗起球等级高,无歪斜,条影少,缩水率低,布面匀整丰满。
其产品主要有运动装、双面休闲装、儿童服装、针织T恤衫和内衣等,原料主要以涤棉混纺品种为主。
由于喷气纱具有毛羽少、条干疵点少等优点,虽然强力较环锭纱低,但强力CV值小,恰好最能满足无梭织机用纱标准,故适宜于无梭织机使用,一般采用喷气纱可以提高织机效率2 % ~ 3 %。
喷气纱机织产品主要有两大类:一是服饰面料产品,另一类是家纺产品。
据介绍,美国市场50 %以上的家纺产品和制服面料是以喷气纱为原料制成的。
此外,喷气纱较适合万米无结头缝纫线的加工。
虽然传统喷气纺技术不大适应生产纯棉纱,但对化学纤维,尤其是细旦化纤等差别化纤维具有独特的优势。
随着世界人口的增加,对化学纤维的依赖性将更加明显,化学纤维在服装用布、装饰用布及产业用布中所占的比例将会快速增加,因此喷气纺技术及其产品也会得到相应的发展。
4.4 涡流纱涡流纺可以加工纯棉纱线,而且具有纺纱速度高的优点,因此在21世纪初得到了快速的发展。
涡流纱具有环锭纱的结构,具备更多的功能及流行的特点,纱线毛羽很少,织物起球现象亦减少,染色性能及耐磨性好,织物外观光滑,吸湿性好、快干。
因而涡流纱织物多用作针织运动衫、休闲服饰、家纺产品等,产品应用领域比较广泛。
4.5 紧密纱紧密纱的出现首先得到了讲究生活质量、钟爱高档纯棉服饰的欧洲人的追捧,据有关资料介绍在欧洲有80 %的紧密纱用于男式衬衫面料。
欧洲用户现在将紧密纱作为高品质纱线的标准。
这是由于紧密纺成纱毛羽少、强力高等特点,特别适合纺制高支精梳纱,用于机织高档纯棉衬衫、防羽布等,并具有上浆成本低、织造飞花少、织造效率高、织物光泽度佳、外观纹路清晰、色彩对比度增强等优点,紧密纱的应用将使纺织产品的质量达到一个新的水平。