复杂曲面五轴侧铣加工的运动学优化方法
机械制造中的五轴联动加工工艺优化研究
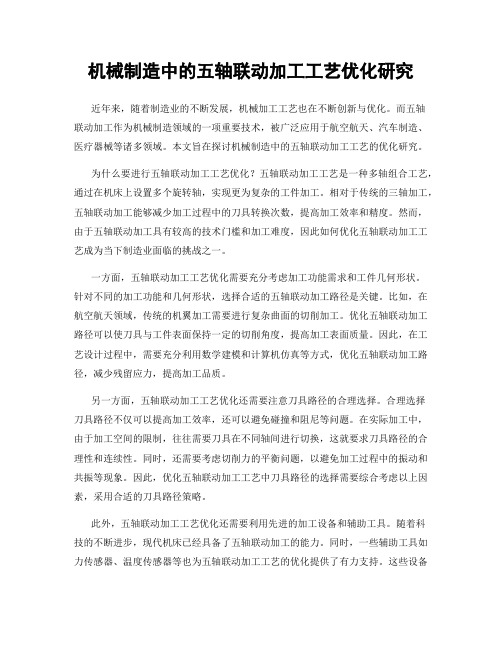
机械制造中的五轴联动加工工艺优化研究近年来,随着制造业的不断发展,机械加工工艺也在不断创新与优化。
而五轴联动加工作为机械制造领域的一项重要技术,被广泛应用于航空航天、汽车制造、医疗器械等诸多领域。
本文旨在探讨机械制造中的五轴联动加工工艺的优化研究。
为什么要进行五轴联动加工工艺优化?五轴联动加工工艺是一种多轴组合工艺,通过在机床上设置多个旋转轴,实现更为复杂的工件加工。
相对于传统的三轴加工,五轴联动加工能够减少加工过程中的刀具转换次数,提高加工效率和精度。
然而,由于五轴联动加工具有较高的技术门槛和加工难度,因此如何优化五轴联动加工工艺成为当下制造业面临的挑战之一。
一方面,五轴联动加工工艺优化需要充分考虑加工功能需求和工件几何形状。
针对不同的加工功能和几何形状,选择合适的五轴联动加工路径是关键。
比如,在航空航天领域,传统的机翼加工需要进行复杂曲面的切削加工。
优化五轴联动加工路径可以使刀具与工件表面保持一定的切削角度,提高加工表面质量。
因此,在工艺设计过程中,需要充分利用数学建模和计算机仿真等方式,优化五轴联动加工路径,减少残留应力,提高加工品质。
另一方面,五轴联动加工工艺优化还需要注意刀具路径的合理选择。
合理选择刀具路径不仅可以提高加工效率,还可以避免碰撞和阻尼等问题。
在实际加工中,由于加工空间的限制,往往需要刀具在不同轴间进行切换,这就要求刀具路径的合理性和连续性。
同时,还需要考虑切削力的平衡问题,以避免加工过程中的振动和共振等现象。
因此,优化五轴联动加工工艺中刀具路径的选择需要综合考虑以上因素,采用合适的刀具路径策略。
此外,五轴联动加工工艺优化还需要利用先进的加工设备和辅助工具。
随着科技的不断进步,现代机床已经具备了五轴联动加工的能力。
同时,一些辅助工具如力传感器、温度传感器等也为五轴联动加工工艺的优化提供了有力支持。
这些设备和工具的合理使用,可以实时监测和控制加工过程中的力、温度等关键参数,提高加工的精度和一致性。
采用不同的刀具和方法优化五轴加工

采用不同的刀具和方法优化五轴加工使用五轴加工可以从几个方面提供诸多益处。
通过分析设备、工艺和装夹,尤其是切削刀具和切削作用,就能从中而受益。
除了通过全五轴加工才能完成某些特征外,也可选择性地简化利用五轴的加工工艺。
其中包括使用三加二轴,或有时仅使用三轴,尤其是对于各种粗加工、半精加工和修铣工序。
尽管有些零件特征具有双曲线轮廓,并且会同时沿着五轴运动,但使用正确的刀具再保持适当的恒定吃刀量,就能高效地加工出几乎任何曲度。
使用五轴加工的主要好处显而易见是能够高效地获得复杂的三维(双面)零件特征,不仅精度高,而且表面质量极佳。
一般仅需一次装夹和最少的切削工序,切削时间大为缩短,刀具悬伸始终保持尽可能地短。
此外,往往也会进步金属往除率,并且刀具碰撞风险可控。
对五轴加工、联动加工以及三加二轴加工而言,切削刀具和工艺选择是获得成功结果的关键因素。
与三加二轴加工相比,联动加工时的工艺选择更为重要,由于前者挑战性较低,可以当作三轴工序看待。
图1 (图片编号101108)五轴CNC加工基于机床在五个轴上运动而天生3D零件外形的能力。
而且,真正的五轴联动加工指的是除了能够沿着旋转轴定位刀具外,切削时刀具还能顺着这些轴进给。
其必然结果是使得机床一次装夹就能形成复杂的零件外形。
除三个基本轴(x、y和z)之外,还包括两个附加轴(b和c,或者有时为a和c,具体取决于机床配置),切削时绕着z轴和绕着y轴(或x 和y)旋转。
当机床主轴或工作台以某一角度固定,并且在三轴模式下进行加工时,即为三加二轴加工。
从机床的角度来看,有多种方法可以获得五轴加工:五轴加工中心、倾斜工作台布置或通过主轴头附件。
图2 (图片编号081744)采用CoroMill Plura(金刚铣)整体硬质合金立铣刀五轴联动加工叶轮旋转刀具产生在零件表面上的纹路是主要的考虑因素。
为此,切进角和刀具倾斜角度通过CAD-CAM程序实现,并且应在设计装夹方式时予以考虑。
数控加工中心五轴复杂曲面零件加工技术研究及加工精度控制

数控加工中心五轴复杂曲面零件加工技术研究及加工精度控制摘要:随着社会经济的不断发展,各行各业对产品制造精度的要求越来越高。
而数控加工中心是一种高效率、高精度、多功能的加工设备,已成为现代制造业必不可少的工具。
为了满足现代制造业对于高精度、高效率及多样化的加工需求,数控加工中心五轴复杂曲面零件加工技术得到广泛关注。
本文研究该领域中的加工过程和加工精度控制,并提出一种基于机器学习的方法用于优化加工参数,显著地提高了加工效率和精度。
关键词:数控加工中心;五轴复杂曲面;加工技术;精度控制;机器学习一、数控加工中心和五轴复杂曲面零件的特点和加工难点数控加工中心和五轴复杂曲面零件是现代制造业中的重要设备和关键部件。
数控加工中心以其高效、高精度和多功能等特点,成为现代制造业不可或缺的加工工具,而五轴复杂曲面零件则由于其异常复杂的形状和表面几何变化,难以通过常规方式进行加工,因此充满挑战性,也因此引起了广泛的关注。
在加工过程中,数控加工中心一般采用立式刀库,能够根据需要调整角度和位置,实现多种加工操作。
五轴复杂曲面零件的特点则在于它们所具有的极端复杂的几何形状和表面设计,包括向外突出的棱和边、开口孔和内部各种壁面,而这些都需要经过精密的加工才能达到标准。
然而,在面对加工复杂曲面零件时,存在着以下几大加工难点:几何参数测量:针对五轴复杂曲面零件,必须完全了解这样一个元件形状中的复杂性质并产生命令来摆放该物体进行加工;工具路径规划:为了处理复杂曲面上的不同加工区域,需要寻找合适的、高效率的轨迹以用来掌控工件在加工期间机器终端上的运动;剪力和热源问题:五轴复杂曲面零件的特殊形态给剪力和热源性能带来了挑战。
较大的压力会导致断屑、撕裂,并影响表面质量;同时温度过高也会导致损坏。
加工精度控制:由于其表面几何变化比较大,需要高精度的控制方案才能够确保正常完成任务。
二、数控加工中心和五轴复杂曲面零件在现代制造业中的重要性数控加工中心和五轴复杂曲面零件在现代制造业中具有极为重要的地位。
五轴数控车床加工技术及优化

五轴数控车床加工技术及优化五轴数控车床加工技术是一种高精度、高效率的加工技术。
它采用数字化控制寻找加工点的方法,利用机床上旋转的工具和工件移动,通过各种角度的定位,达到实现工件的复杂加工。
近年来,五轴数控车床加工技术的应用范围越来越广泛,尤其在航空、汽车、模具制造等领域得到了广泛应用。
五轴数控车床加工技术的优势与传统的三轴车床相比,五轴数控车床加工技术具有以下优势:①高精度:五轴数控车床加工技术可以实现高精度的加工,可以满足复杂形状和高精度的加工要求。
②高效率:五轴数控车床加工技术可以一次性完成多个加工步骤,避免了不必要的操作和工序,提高了加工效率。
③工件形状自由:五轴数控车床加工技术可以实现三维加工,可以加工出各种复杂形状的工件。
④生产灵活性高:五轴数控车床加工技术可以适应各种不同的工件加工需求,具有高度的生产灵活性。
五轴数控车床加工技术的应用①航空领域在航空领域中,五轴数控车床加工技术的应用非常广泛。
航空发动机的叶轮、涡轮等部件的制造都离不开五轴数控车床的加工技术。
这些零部件的制造需要高精度的加工,以保证安全和性能的稳定。
同时,五轴数控车床加工技术可以减少加工时间和提高加工效率,降低生产成本和提高生产效率,这在航空制造行业中非常重要。
②汽车领域五轴数控车床加工技术在汽车制造业中也有广泛应用。
尤其是在汽车模具制造中,五轴数控车床加工技术可以实现高效率、高精度的加工,可以满足复杂形状的零部件制造的需求。
另外,在汽车零部件的加工中,五轴数控车床加工技术也可以实现高精度加工,提高零部件的精度和质量。
③模具制造领域模具制造是五轴数控车床加工技术的另一重要应用领域。
在模具制造中,五轴数控车床加工技术可以实现复杂形状的模具加工,例如塑料模具、压铸模具等。
在制造过程中,五轴数控车床加工技术可以实现精度高、速度快的加工,大大提高了模具的制造效率和质量。
五轴数控车床加工技术的优化虽然五轴数控车床加工技术具有非常大的优势,但是在实际应用中还存在一些问题,主要包括以下几个方面:①机械加工精度低:五轴数控车床加工中机械加工精度通常较低,这会限制其应用领域。
复杂曲面机械零件的数控加工优化研究

复杂曲面机械零件的数控加工优化研究1. 引言复杂曲面机械零件的数控加工是现代制造技术领域的关键问题之一。
在机械零件的加工过程中,通过合理的数控加工优化研究,可以提高加工效率、降低成本、提高零件质量。
本文将探讨复杂曲面机械零件的数控加工优化问题,并提出相应的解决策略。
2. 数控加工的挑战与需求复杂曲面机械零件具有形状复杂、加工难度大、加工工艺复杂等特点,使得数控加工面临一系列挑战。
首先,复杂曲面的数学描述与数控机床的坐标系描述存在差异,需要进行坐标系变换和数学模型转换。
其次,复杂曲面的加工路径不规则,需要合理设计加工路径,减少加工时间和误差。
此外,由于复杂的曲面结构,加工过程中容易出现切削震动、刀具磨损等问题,也需要进行相应的优化处理。
3. 数控加工优化的策略为了解决复杂曲面机械零件加工过程中的问题,需要采取针对性的数控加工优化策略。
以下是几个常用的策略:3.1 五轴加工技术五轴加工技术是一种常用的复杂曲面机械零件数控加工优化策略。
通过增加刀具在不同方向上的旋转能力,可以减少加工路径,提高加工效率,减少误差。
这种技术能够处理复杂曲面的多个曲率变化,提高加工精度和表面质量。
3.2 加工路径优化加工路径优化是为了减少加工时间和误差,提高加工效率的一项重要技术。
通过合理规划加工路径,减少刀具在曲面上的移动距离,可以大大提高加工效率。
同时,还可以通过优化刀具进给速度、切削深度等参数,减少切削震动等问题。
3.3 刀具轨迹优化复杂曲面加工过程中,刀具的接触点会发生变化,而曲面的局部特性也会影响刀具的入射角度。
因此,刀具轨迹的优化是提高加工精度和表面质量的关键。
通过合理设计刀具轨迹,保证刀具与曲面的最佳接触,可以实现高质量的加工效果。
3.4 切削参数优化切削参数的优化对于复杂曲面机械零件数控加工至关重要。
通过合理选择切削速度、进给速度、切削深度等参数,可以最大程度地减少切削震动、刀具磨损等问题,提高加工质量。
4. 数控加工优化实例分析以某复杂曲面机械零件的数控加工为例进行分析。
五轴数控铣削机床的运动控制系统设计与优化
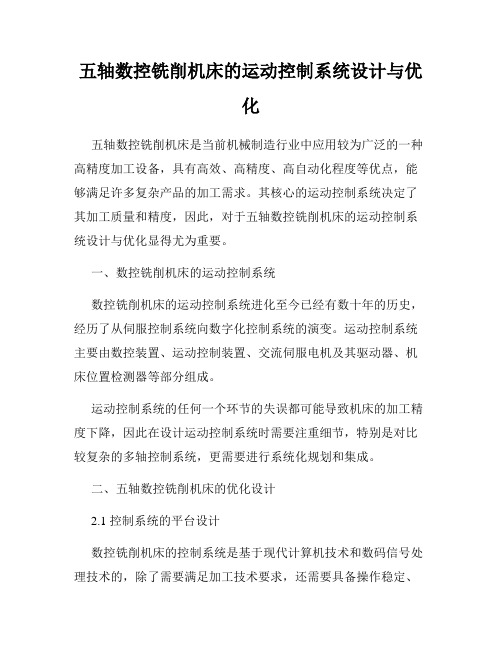
五轴数控铣削机床的运动控制系统设计与优化五轴数控铣削机床是当前机械制造行业中应用较为广泛的一种高精度加工设备,具有高效、高精度、高自动化程度等优点,能够满足许多复杂产品的加工需求。
其核心的运动控制系统决定了其加工质量和精度,因此,对于五轴数控铣削机床的运动控制系统设计与优化显得尤为重要。
一、数控铣削机床的运动控制系统数控铣削机床的运动控制系统进化至今已经有数十年的历史,经历了从伺服控制系统向数字化控制系统的演变。
运动控制系统主要由数控装置、运动控制装置、交流伺服电机及其驱动器、机床位置检测器等部分组成。
运动控制系统的任何一个环节的失误都可能导致机床的加工精度下降,因此在设计运动控制系统时需要注重细节,特别是对比较复杂的多轴控制系统,更需要进行系统化规划和集成。
二、五轴数控铣削机床的优化设计2.1 控制系统的平台设计数控铣削机床的控制系统是基于现代计算机技术和数码信号处理技术的,除了需要满足加工技术要求,还需要具备操作稳定、图形显示清晰、数据处理速度快等特点。
现代控制系统多采用集成处理器为核心,外加一些控制芯片组成,使得控制系统能够同时执行多种运动命令。
在五轴数控铣削机床中,控制系统的硬件和软件的设计都要与加工对象的特性相适应,对于不同的加工要求,需要设计不同的加工程序,以实现更加精准的加工。
2.2 型号识别及误差补偿在五轴数控铣削机床的加工过程中,由于机床误差、刀具误差和工件误差等因素的影响,会导致加工的产品存在一定的误差。
为避免这些误差,需要对型号进行识别,并对其误差进行补偿。
首先,需要在加工之前对工件进行扫描,获取其三维形状和位置信息。
然后,运用支持向量机(SVM)等算法识别工件型号,进而进行误差补偿,使得加工零件能够保证高精度要求。
2.3 控制系统的动态响应优化动态响应指机床的加工效率和加工精度,提高动态响应意味着加工零件拥有更高的精度和更快的加工速度。
为优化控制系统的动态响应,需要进行系统建模,并通过动态调整控制参数的方式,实现加工效率和加工精度的平衡。
复杂曲面五轴数控加工刀矢的运动学控制方法[发明专利]
![复杂曲面五轴数控加工刀矢的运动学控制方法[发明专利]](https://img.taocdn.com/s3/m/7558c0e952ea551811a6872b.png)
专利名称:复杂曲面五轴数控加工刀矢的运动学控制方法专利类型:发明专利
发明人:贾振元,秦纪云,马建伟,王福吉,曲云松
申请号:CN201310451610.9
申请日:20130928
公开号:CN103558808A
公开日:
20140205
专利内容由知识产权出版社提供
摘要:本发明复杂曲面五轴数控加工刀矢的运动学控制方法属于复杂曲面五轴数控机床精密高效加工领域,特别涉及复杂曲面五轴数控加工过程中刀轴矢量的运动学控制方法。
刀矢的运动学控制方法在确定复杂曲面参数化方程的基础上,建立刀轴矢量与加工轨迹曲线参数的函数关系;然后,建立五轴数控机床旋转进给轴运动参数计算方法,获得旋转进给轴角速度、角加速度计算结果;最后,对刀轴矢量进行光顺,保证机床旋转进给轴运动平滑,实现对刀轴矢量的运动学控制。
本发明提供了一种复杂曲面五轴数控加工刀轴矢量的运动学控制方法,应用范围广,有效提高复杂曲面加工质量、更好地发挥机床性能。
申请人:大连理工大学
地址:116024 辽宁省大连市凌工路2号
国籍:CN
代理机构:大连理工大学专利中心
代理人:关慧贞
更多信息请下载全文后查看。
五轴联动加工中的刀具姿态优化

五轴联动加工中的刀具姿态优化随着制造业的技术不断发展,五轴联动加工成为现代工业领域中不可或缺的加工方法之一。
五轴联动机床的优点在于,它可以完成复杂曲面零件的加工,并且可以提高加工效率和质量。
然而,在加工中,如何优化刀具姿态以提高加工效率和质量,成为制约五轴联动加工发展的瓶颈。
本文将探讨在五轴联动加工中的刀具姿态优化的方法以及实现的途径。
一、五轴联动加工过程的刀具姿态五轴联动加工的刀具姿态有着不同的表达方式,如欧拉角、四元数、转动矩阵等,本文采用的是欧拉角。
五轴联动加工机床通过调节刀具姿态实现工件的加工。
图1为五轴联动加工机床的刀具姿态图。
图1 五轴联动加工机床的刀具姿态图在五轴联动加工过程中,刀具姿态对加工精度和效率有着重要的影响。
因此,如何根据工件的加工需求和机床的性能特点选择最合适的刀具姿态是五轴联动加工的重要问题。
二、刀具姿态优化的方法在五轴联动加工过程中,刀具姿态的优化既要考虑到工件的加工精度和表面质量,也要考虑到加工效率和机床的使用寿命。
刀具姿态优化的方法有以下三种:1、基于经验的刀具姿态基于经验的刀具姿态是根据加工工艺经验,结合加工工件的形状和尺寸,选取合适的刀具姿态。
这种方法简单易实现,但其缺点在于每个工件的形状和尺寸不同,需要针对不同的工件重新开发加工工艺。
2、基于计算的刀具姿态基于计算的刀具姿态是通过数值分析方法获得的最优刀具姿态。
该方法需要建立工件和机床的数学模型,利用数学优化算法求解。
这种方法具有广泛的适用性,可以在较短的时间内得出最优的刀具姿态,但需要花费大量的时间和资源。
3、基于试验的刀具姿态基于试验的刀具姿态是在实际加工中通过试验方法确定合适的刀具姿态。
该方法需要具有专业的试验设备,成本较高,但是可以获得更准确的刀具姿态,提高加工效率和质量。
三、刀具姿态优化的实现途径在实际五轴联动加工中,刀具姿态的优化由以下几个方面实现:1、机床性能优化机床的精度、刚性和稳定性对刀具姿态的优化有着重要的影响。
- 1、下载文档前请自行甄别文档内容的完整性,平台不提供额外的编辑、内容补充、找答案等附加服务。
- 2、"仅部分预览"的文档,不可在线预览部分如存在完整性等问题,可反馈申请退款(可完整预览的文档不适用该条件!)。
- 3、如文档侵犯您的权益,请联系客服反馈,我们会尽快为您处理(人工客服工作时间:9:00-18:30)。
轴运动对刀刃微元去除材料的影响,确定刀轴运动优化的约束条件。在 虚 拟 环 境 中 仿 真 复 杂 曲 面 五 轴
侧 铣 加 工 过 程 ,通 过 自 适 应 控 制 器 调 整 刀 轴 运 动 速 度 ,使 机 床 在 多 约 束 加 工 条 件 下 最 大 限 度 地 发 挥 其 工
Δdi = ‖Pi+1 -Pi‖烌
fLi
=
Δdi Δti
烍
(1)
vLi
=
Pi+1 -Pi ‖Pi+1 -Pi‖
烎
式中,Δti 为刀具经过刀路段i 所需的时间。
在每一个刀路段上,刀轴均会绕轴ki 从Ti 旋
转到Ti+1,固 定 轴ki 为 刀 具 进 给 方 向 轴。 刀 轴 以
恒 定的角速度ωi 转过 Δθi。ki 轴与 Δθi 角及角速
作潜能。整个刀轴运动规划过程随刀具与工件接触区域的变化而不断 优 化 ,最 后 将 优 化 结 果 存 储 在 每
个 刀 位 点 上 。 仿 真 与 实 验 结 果 表 明 ,刀 轴 自 适 应 控 制 的 运 动 学 优 化 方 法 有 效 可 行 ,为 五 轴 侧 铣 加 工 过 程
提供了有力的分析工具。
刀 尖 经 过 刀 路 段i 的 时 间 为
Δti
=
Δdi fLi
(3)
式中,Δdi 为刀尖在刀路段i 上 的 移 动 距 离 ;fLi 为 刀 尖 点
的速度。
在 Δti 时间内,刀具同时以角速度ωi 旋转 Δθi 的 角 度 ,则
Δti
=
Δθi ωi
(4)
由于刀具运动是其线性平动与旋转运动的复
合运 动,因 此 刀 具 总 进 给 速 度 沿 刀 轴 方 向 不 断
收 稿 日 期 :2010—12—10 基 金 项 目 :国 家 自 然 科 学 基 金 资 助 项 目 (50875171);上 海 高 校 选 拔 培 养 优 秀 青 年 教 师 科 研 专 项 基 金 资 助 项 目 (gjd09003)
· 2588 ·
切 削 力 增 大 、刀 具 变 形 及 磨 损 等 ,而 单 一 恒 定 的 速 度值会降低 加 工 效 率 。 [3-4] 目 前 对 复 杂 曲 面 侧 铣 加工的研究较少,且 一 般 情 况 下 曲 面 加 工 不 能 一 刀 成 形 ,刀 路 规 划 需 要 过 多 人 为 干 预 ,致 使 加 工 效 率 较 低 。 [5-6]
图2 五轴侧铣过程中刀具运动示意图
如果已 知 每 一 个 微 元 的 切 屑 厚 度、刀 刃 几 何 参 数 及 切 削 力 系 数 ,则 即 可 求 得 微 元 上 的 切 削 力 ,
图3 球头刀水平进给方向上产生的切屑厚度
切屑厚度的计算公式为
hXj(j,z)=cXjsinj(z)sinκ(z)
Key words:five-axis;flank milling;kinematical model;adaptive control
0 引 言
五轴数控加工已成为高性能复杂零件高效加 工的重要手 段。 与 三 轴 加 工 相 比,五 轴 数 控 加 工 的优势主要通过 改 变 刀 轴 方 向 来 实 现,从 而 达 到 提高刀具的可达 性,避 免 刀 具 和 工 件 之 间 干 涉 的 目的。五轴侧铣加工是利用回转刀具的侧刃切削 零件表面,主要用 于 具 有 狭 窄 型 腔 的 零 件 或 者 存 在平坦参数方向的自由曲面的加工 。 [1] 在目前 加 工规划中,选 择 加 工 参 数 时 CAM 程 序 的 生 成 仅 基于几何与体积 的 分 析,没 有 考 虑 加 工 过 程 中 的 切削力等物理因 素,因 而 无 法 避 免 如 刀 具 破 损 或 刀具变形而产生过切等状况 。 [2] 由于曲面加工 中 零件几何表面的 复 杂 性,很 难 选 取 适 合 切 削 的 参 数来获得高的生产效率。过高的切削速度会引起
所 以 式 (7)中 的 负 号 表 示 向 上 进 给 。
3 多约束自适应速度优化策略
图5 虚拟加工过程流程方块图
图5中 ,H (z)为 切 削 过 程 的 传 递 函 数 ;fL(z) 为输入 量 (刀 尖 速 度 );yTS(z)、yTD(z)、yTQ(z)和 yCL(z)分别为一个主轴 周 期 内 的 刀 具 应 力、刀 具 变 形 、切 削 扭 矩 以 及 最 大 切 屑 厚 度 的 输 出 峰 值 。
1 五 轴 侧 铣 过 程 中 刀 轴 运 动 学 模 型
复杂曲面加工的五轴刀具路径是由大量的小
复 杂 曲 面 五 轴 侧 铣 加 工 的 运 动 学 优 化 方 法 ——— 张 立 强 王 克 用 王 宇 晗
段 连 接 而 成 ,在 每 一 条 刀 具 路 段 上 ,刀 具 平 移 与 旋 转的速度被认为 是 恒 定 的,仅 在 刀 具 路 段 的 连 接 点或每一个 数 控 程 序 块 的 最 后 发 生 变 化,如 图 1 所示。
{ ε(j)=
1 st ≤j(z)≤ex 0 j(z)<st,j(z)>ex
其中,st 和ex 分别为刀具对工件的切入切出角,
ε为基于切入 切 出 沉 浸 角 的 开 关 函 数,即 如 果 切
削 刃与工件接触,则ε为1,否则为0。因为向下进
给 会 增 大 切 屑 厚 度 ,而 向 上 进 给 会 减 小 切 屑 厚 度 ,
关 键 词 :五 轴 ;侧 铣 ;运 动 学 模 型 ;自 适 应 控 制
中 图 分 类 号 :TG506 文 章 编 号 :1004—132X(2011)21—2588—06
Kinematical Optimum Method for Five-axis Flank Milling Complex Surfaces Zhang Liqiang1 Wang Keyong1 Wang Yuhan2
中 国 机 械 工 程 第 22 卷 第 21 期 2011 年 11 月 上 半 月
复杂曲面五轴侧铣加工的运动学优化方法
张 立 强1 王 克 用1 王 宇 晗2
1.上 海 工 程 技 术 大 学 ,上 海 ,201620 2.上 海 交 通 大 学 ,上 海 ,200240
摘要:针对五轴侧铣加工中刀轴的运动可能导致加工材料过切与效率低下的问题 ,提出采用多约束
本文提出一种基于多约束自适应控制的刀轴 运动优化方法,对 五 轴 侧 铣 加 工 过 程 进 行 分 析 优 化 ,在 曲 面 侧 铣 过 程 中 对 球 头 刀 进 行 运 动 学 建 模 , 分析刀轴在运动过程中对材料去除的影响。在运 动学 模 型 基 础 上,综 合 考 虑 刀 具 应 力、刀 具 变 形、 切削扭矩与切屑 厚 度 的 约 束 条 件,采 用 虚 拟 自 适 应速度控制策略 对 刀 轴 速 度 进 行 优 化,最 大 限 度 发挥五轴机床工 作 潜 能,提 高 零 件 的 加 工 效 率 与 加工质量。
(5)
式中,cXj 为刀刃j 上 沿 进 给 方 向 的 每 齿 进 给 量 ;j(z)为
刀刃j的沉浸角;κ(z)为轴向沉 浸 角,即 刀 轴 与 刀 具 表 面
· 2589 ·
外法向之间的夹角。
进给速度在垂直方向上对切屑厚度的影响如 图4所示,该图描 述 了 两 个 离 散 的 刀 位 点 从 一 点 到另一点运动中切掉的材料厚度。
hZj(z)=cZjcosκ(z)
(6)
式中,cZj 为刀刃j 上沿垂直方向的每齿进给量。
在仿真 中 为 避 免 奇 异 性,将 切 削 刃 单 元 的 中
间位置作为切削力计算位置。
考虑水平 与 垂 直 进 给 对 切 屑 厚 度 的 综 合 影
响 ,此 时 计 算 公 式 为
hcj(j,z)=ε(cXjsinj(z)sinκ(z)-cZjcosκ(z)) (7)
度计算公式为
熿kxi燄
烌
ki = kyi
=
Ti ×Ti+1 ‖Ti ×Ti+1‖
燀kzi燅
Δθi
=
arctan
‖Ti ×Ti+1 Ti·Ti+1
‖
烍
(2)
ωi
=
Δθi ti
烎
沿着刀轴方向将切削深度细分为一系列的微
元 ,如 图 2 所 示 。
通过将刀具工件接触区内的所有微元上切削力进 行相加,即可得到作用在刀具上的总切削力 。 [7]
运动对刀刃微元去 除 材 料 的 影 响,确 定 刀 轴 运 动
优化时切屑厚度的约束条件。
2 刀轴运动速度对材料去除的影响分析
在某一 给 定 高 度 上,总 的 进 给 量 可 分 解 为 两 个主要方 向 (水 平 进 给 与 垂 直 进 给 )上 的 分 量。 这两个进给方向都会对总的切屑厚度产生影响。 刀具在水平进给分量上产生的切屑厚度沿切削刃 分布如图3所示。
图 1 五 轴 侧 铣 加 工 刀 路 段 示 意 图
刀位点i上的坐标用Pi 表示,刀位点i上刀轴 的 单位矢量用Ti 表示,如果刀路段i非常短,刀尖 可以假定为以恒 定 线 速 度 fLi 沿vLi 从 刀 尖 点Pi 移动到Pi+1,与此同时,刀轴以恒定的角速度ωi 由 Ti 旋转到Ti+1。刀尖点经过的距离与刀尖点的速 度 大 小 、方 向 由 下 式 给 出 :
变化。
为使刀 路 轨 迹 保 持 不 变,角 速 度 与 刀 尖 速 度
的比率必须保持不变。当刀尖进给速度增大或减
小时,刀 具 旋 转 角 速 度 必 须 同 时 相 应 地 进 行 缩 放 。 [8] 假定每个刀路段上刀尖的线速度及刀具 角
速度保持不变。
接下来 在 运 动 学 模 型 基 础 上,通 过 分 析 刀 轴
1.Shanghai University of Engineering Science,Shanghai,201620 2.Shanghai Jiaotong University,Shanghai,200240