第二章 伺服系统误差分析
数控机床进给伺服系统类故障诊断与处理(3篇)

数控机床进给伺服系统类故障诊断与处理数控机床进给伺服系统是数控机床中非常关键的一个组成部分,它直接影响机床加工的精度和效率。
然而,在使用过程中,由于各种原因,进给伺服系统可能会出现故障。
本文将介绍数控机床进给伺服系统的常见故障及其诊断与处理方法。
一、数控机床进给伺服系统常见故障1. 运动不平稳:机床在加工工件时,出现运动不平稳的情况,可能是由于进给伺服系统的故障引起的。
这种情况表现为运动过程中有明显的抖动或者不稳定的现象。
2. 运动失效:机床无法正常运动,不响应操作指令。
这种情况可能是由于进给伺服系统的电源故障、控制器故障或者连接线路故障引起的。
3. 位置误差过大:机床在加工过程中,位置误差超过了允许范围,导致加工工件的尺寸不准确。
这种情况可能是由于进给伺服系统的位置反馈元件(如编码器)故障引起的。
4. 加工速度过慢:机床在加工时,进给速度远低于预设值,导致加工效率低下。
这种情况可能是由于进给伺服系统的电机故障或者速度控制回路故障引起的。
二、故障诊断与处理方法1. 运动不平稳的诊断与处理:首先,检查机床的润滑系统,确保润滑油是否充足,并且清洁。
其次,检查机床的传动系统,确保螺杆和导轨的润滑良好。
如果问题还未解决,可以通过检查进给伺服系统的控制器参数是否正确、电机驱动器是否正常工作等方式进一步诊断。
2. 运动失效的诊断与处理:首先,检查进给伺服系统的电源供应情况,确保电源正常。
其次,检查进给伺服系统的连接线路,包括电源线、编码器连接线等,确保线路没有松动或者断裂。
如果问题还未解决,可以通过检查进给伺服系统的控制器和电机驱动器是否正常工作等方式进一步诊断。
3. 位置误差过大的诊断与处理:首先,检查进给伺服系统的位置反馈元件,如编码器是否损坏或者松动。
如果问题还未解决,可以通过检查进给伺服系统的控制器参数是否正确、电机驱动器是否正常工作等方式进一步诊断。
4. 加工速度过慢的诊断与处理:首先,检查进给伺服系统的电机是否正常工作,包括电机是否有异常声音或者发热等。
伺服编码器误差 -回复

伺服编码器误差-回复什么是伺服编码器误差?伺服编码器是一种用于测量和反馈电机转动位置和速度的设备。
它由一个光栅盘和一个读取头组成,通过光栅盘上的光学线条来生成电信号,并将其转换为数字脉冲。
这些脉冲信号由控制系统使用,以确保电机按照预定位置和速度运动。
然而,由于制造和安装过程中的各种因素,伺服编码器可能会产生误差。
这些误差可能会导致电机的位置和速度控制不准确,从而影响设备的性能和精度。
伺服编码器误差主要分为几种类型:1. 累积误差:这是指伺服编码器在长时间使用后逐渐累积的误差。
它可以由于光栅盘上的线条损坏或读取头的漂移等原因而产生。
2. 移动误差:这是指在电机加速或减速时由于编码器反应速度不够快而产生的误差。
当电机在瞬间改变速度时,编码器可能需要一定的时间来重新生成脉冲信号,这样就会导致位置和速度的偏差。
3. 安装误差:这是指伺服编码器在安装过程中由于位置、方向或角度不准确而导致的误差。
如果伺服编码器没有正确地安装在电机上,或者安装位置和方向与电机轴线不一致,都会导致误差的出现。
如何解决伺服编码器误差?1. 定期校准:为了减小累积误差,伺服编码器应定期进行校准。
校准过程涉及到对伺服编码器进行复位,重新校正光栅盘和读取头的位置,以确保其准确测量位置和速度。
2. 优化安装:正确的安装是减少误差的关键。
确保伺服编码器正确安装在电机上,并与电机轴线对齐,可以减少安装误差的发生。
使用精确的安装工具和技术,如光栅盘对准装置,可以帮助确保安装的准确性。
3. 提高读取头的分辨率:为了减小移动误差,可以使用更高分辨率的读取头。
高分辨率的读取头可以更准确地获取光栅盘上的线条信息,并快速反馈给控制系统,以便更精确地控制电机的位置和速度。
4. 使用编码器反馈补偿技术:编码器反馈误差可以通过使用编码器反馈补偿技术进行补偿。
这些技术可以根据测量误差的模式和特征,在控制系统中进行数学补偿,从而减小误差对电机运动的影响。
5. 检测和修复故障:定期检查伺服编码器的工作状态和性能,并及时修复任何故障。
开环控制的伺服系统误差分析

开环控制的伺服系统误差分析在开环控制的伺服系统中,由于没有位置检测及反应装置,为了保证工作精度的要求,必须使其机械系统在任何时刻、任何情况下都能严格跟随步进电动机的运动而运动。
但实际上,在机械系统的输入与输出之间总会有误差存在,其中除了零部件的制造及安装所引起的误差外,还有由于机械系统的动力参数(如刚度、惯量、摩擦、间隙等)所引起的误差。
在系统设计时,必须将这些误差控制在允许范围内。
一、死区误差所谓死区误差(又叫失动量),是指启动或反向时,系统的输入运动与输出运动之间的差值。
产生死区误差的主要原因:a.传动机构中的间隙b.导轨运动副间的摩擦力c.电气系统和执行元件的启动死区(又称不灵敏区)。
由传动间隙所引起的工作台等效死区误差δc(mm)可按下式计算式中,p是丝杠导程(mm);δi是第i个传动副的间隙量(rad);ii是第i个传动副至丝杠的传动比。
由摩擦力引起的死区误差实质上是在驱动力的作用下,传动机构为克服静摩擦力而产生的弹性变形,包括拉压弹性变形和扭转弹性变形。
由于扭转弹性变形<<拉压弹性变形,常被忽略,于是由拉压弹性变形所引起的摩擦死区误差δμ(mm)为:式中:Fμ—导轨静摩擦力(N);K0—丝杠螺母机构的综合拉压刚度(N/m)。
由电气系统和执行元件的启动死区所引起的工作台死区误差与上述两项相比很小,常被忽略。
如果已采取消除间隙措施,则系统死区误差主要取决于摩擦死区误差。
假设静摩擦力主要由工作台重力引起,则工作台反向时的最大反向死区误差Δ(mm)可按下式求得式中,m—工作台质量(kg);g—重力加速度,g=9.8m/s2;μ0—导轨静摩擦系数;ωn—丝杠—工作台系统的纵振固有频率(rad/s)。
减小系统死区误差的措施:1.消除传动间隙;2.采取措施减小摩擦,提高刚度和固有频率。
对于开环伺服系统为保证单脉冲进给要求,应将死区误差控制在一个脉冲当量以内。
二、由系统刚度变化引起的定位误差仅讨论由丝杠螺母机构综合拉压刚度的变化所引起的定位误差。
CNC机床伺服系统跟随误差与轮廓误差分析_孙建仁.
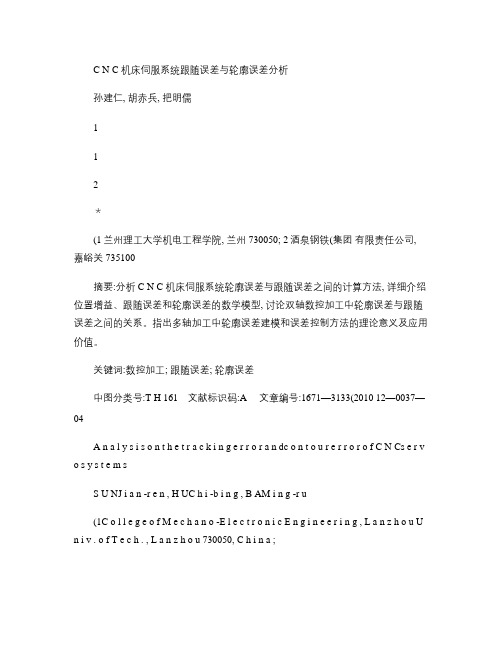
C N C 机床伺服系统跟随误差与轮廓误差分析孙建仁, 胡赤兵, 把明儒112*(1兰州理工大学机电工程学院, 兰州730050; 2酒泉钢铁(集团有限责任公司, 嘉峪关735100摘要:分析C N C 机床伺服系统轮廓误差与跟随误差之间的计算方法, 详细介绍位置增益、跟随误差和轮廓误差的数学模型, 讨论双轴数控加工中轮廓误差与跟随误差之间的关系。
指出多轴加工中轮廓误差建模和误差控制方法的理论意义及应用价值。
关键词:数控加工; 跟随误差; 轮廓误差中图分类号:T H 161文献标识码:A 文章编号:1671—3133(2010 12—0037—04A n a l y s i s o n t h e t r a c k i n g e r r o r a n dc o n t o u r e r r o r o f C N Cs e r v o s y s t e m sS U NJ i a n -r e n , H UC h i -b i n g , B AM i n g -r u(1C o l l e g e o f M e c h a n o -E l e c t r o n i c E n g i n e e r i n g , L a n z h o u U n i v . o f T e c h . , L a n z h o u 730050, C h i n a ;2J i u q u a n I r o n &S t e e l (G r o u p C o . L t d . , J i a y u g u a n 735100, G a n s u , C h i n aA b s t r a c t :H o wt o c a l c u l a t e t h e t r a c k i n ge r r o r a n dc o n t o u r e r r o r o f s e r v os y s t e m s w a s a n a l y z e d . T h e p o s i t i o ng a i n 、tr a c k i n g e r r o r a n d c o n t o u r e r r o r w e r e d i s c u s s e d , t h e m a t h e m a t i c m o d e l s w e r e g i v e n i n d e t a i l . T h e r e l a t i o no f t r a c k i n g e r r o r a n dc o n t o u r e r r o r i n b i a x i a l s e r v o s y s t e m s w a s d i s c u s s e d . T h e t h e o r e t i c a l a n d p r a c t i c a l s i g n i f i c a n c e o f m o d e l i n g e r r o r a n d c o n t r o l l i n g e r r o r i n C N Cs e r -v o s y s t e m s w a s p o i n t e do u t .K e yw o r d s :C N Cm a c h i n i n g ; t r a c k i n g e r r o r ; c o n t o u r e r r o r1120引言在数控机床轮廓加工过程中, 各坐标轴常要求随加工形状的不同瞬时启停或改变速度, 控制系统应同时精确地控制各坐标轴运动的位置与速度, 由于系统的稳态和动态特性, 影响了各坐标轴的协调运动和位[1-3]置精度, 从而产生了轮廓的形状误差。
伺服系统误差分析

伺服系统误差分析(1)机械误差:机械误差是由机械部件制造和装配等因素引起的误差。
例如,机械传动系统中齿轮、螺杆的间隙、磨损等都会导致系统误差。
(2)电气误差:电气误差是由电气部件的特性和性能引起的误差。
例如,伺服电机转子的不平衡、定子线圈的电阻误差等都会引起误差。
(3)控制误差:控制误差是由控制系统的设计和参数设置等因素引起的误差。
例如,控制系统的采样周期、控制增益等都会影响系统误差。
2.误差分析方法(1)开环测试:开环测试是在不进行控制的情况下,直接给伺服系统输入参考信号,然后测量输出信号和参考信号之间的差异。
通过开环测试可以得到系统的静态误差(即参考输入和输出之间的偏差)。
(2)封闭环测试:封闭环测试是在进行反馈控制的情况下,给伺服系统输入参考信号,然后测量输出信号和参考信号之间的差异。
通过封闭环测试可以得到系统的动态误差(即参考输入和输出之间的响应时间和过渡过程中的误差)。
(3)频率特性分析:频率特性分析是通过对伺服系统进行频率响应测试,得到系统的幅频特性和相频特性等信息。
通过频率特性分析可以找出系统的频率响应范围、稳定性特性等。
(4)数学模型分析:数学模型分析是通过建立伺服系统的数学模型,对系统进行解析求解。
通过数学模型分析可以计算出系统的稳态误差、过渡过程中的误差等。
3.误差补偿方法(1)调节控制增益:根据伺服系统的误差特性,适当调节控制增益,可以减小系统的稳态误差。
(2)设计前馈控制器:将参考输入信号通过数学模型进行预测,然后加入到控制器输出信号中,可以减小系统的动态误差。
(3)使用反馈补偿器:通过测量系统输出信号和参考信号之间的误差,根据误差大小调节控制器输出信号,可以减小系统的误差。
(4)提高系统的机械和电气性能:优化机械部件的加工和装配精度,提高电气元件的质量和性能,可以减小系统的误差。
伺服系统定位误差形成原因与克服办法

伺服系统定位误差形成原因与克服办法1.机械结构方面的原因机械结构方面的原因是导致伺服系统定位误差的一个主要因素。
机械件的加工精度、刚性以及装配质量都会对定位误差产生影响。
例如,机床滚珠丝杠的传动精度不高、松动现象严重,会导致定位误差增大。
为了克服这一问题,可以采取以下方法:-提高机械制造工艺,增加机械加工的精度和装配的精度,以减小机械结构方面的误差;-选择高精度的机械件,例如精密滚珠丝杠、高精度的导轨等,可以提高定位的精度;-采用刚性好的机械结构,减小机械变形,从而减小定位误差。
2.传感器方面的原因传感器方面的原因也是导致伺服系统定位误差的一个重要因素。
传感器的精度、分辨率以及非线性特性都会影响定位的准确性。
为了克服这一问题,可以采取以下方法:-选择高精度、高分辨率的传感器,例如光电编码器、磁性编码器等,以提高测量的精度;-对传感器进行校准和补偿,消除传感器的非线性特性,实现更准确的测量;-采用多传感器测量的方法,提高定位系统的容错能力和鲁棒性。
3.控制系统方面的原因控制系统方面的原因也会导致伺服系统定位误差的增大。
控制系统的采样周期、控制算法以及采样信号的噪声都会对定位系统的性能产生影响。
为了克服这一问题,可以采取以下方法:-缩短控制系统的采样周期,提高对系统状态的采样频率,以实时调整控制量,减小定位误差;-采用更高级的控制算法,例如模糊控制、自适应控制等,提高系统的鲁棒性和适应性;-提高采样信号的质量,例如增加滤波器、降低噪声等,提高采样信号的可靠性,减小错误干扰。
4.环境因素的原因环境因素也会对伺服系统的定位误差产生影响。
例如,温度变化会导致机械结构的膨胀和传感器的漂移,进而影响定位的准确性。
为了克服这一问题,可以采取以下方法:-在机械结构设计中考虑温度膨胀的影响,采用温度补偿措施,减小温度变化对定位系统的影响;-选用温度稳定性好的材料,降低机械结构的热膨胀系数,减小温度变化对定位精度的影响;-对传感器进行温度补偿,校正传感器的漂移,提高测量的准确性。
伺服系统定位误差形成原因与克服办法概要
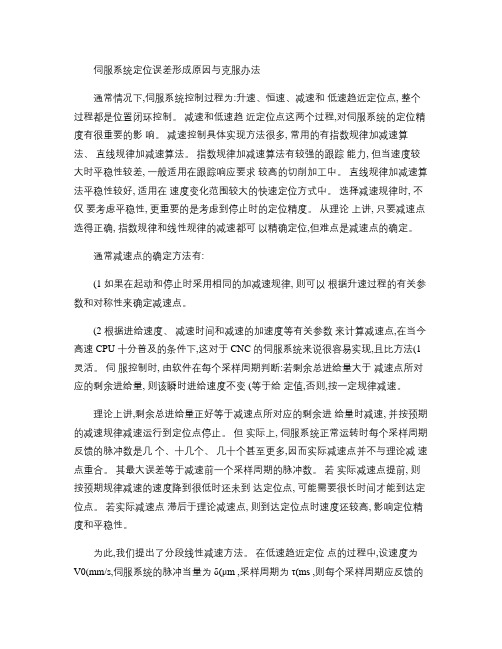
伺服系统定位误差形成原因与克服办法通常情况下,伺服系统控制过程为:升速、恒速、减速和低速趋近定位点, 整个过程都是位置闭环控制。
减速和低速趋近定位点这两个过程,对伺服系统的定位精度有很重要的影响。
减速控制具体实现方法很多, 常用的有指数规律加减速算法、直线规律加减速算法。
指数规律加减速算法有较强的跟踪能力, 但当速度较大时平稳性较差, 一般适用在跟踪响应要求较高的切削加工中。
直线规律加减速算法平稳性较好, 适用在速度变化范围较大的快速定位方式中。
选择减速规律时, 不仅要考虑平稳性, 更重要的是考虑到停止时的定位精度。
从理论上讲, 只要减速点选得正确, 指数规律和线性规律的减速都可以精确定位,但难点是减速点的确定。
通常减速点的确定方法有:(1 如果在起动和停止时采用相同的加减速规律, 则可以根据升速过程的有关参数和对称性来确定减速点。
(2 根据进给速度、减速时间和减速的加速度等有关参数来计算减速点,在当今高速 CPU 十分普及的条件下,这对于 CNC 的伺服系统来说很容易实现,且比方法(1灵活。
伺服控制时, 由软件在每个采样周期判断:若剩余总进给量大于减速点所对应的剩余进给量, 则该瞬时进给速度不变 (等于给定值,否则,按一定规律减速。
理论上讲,剩余总进给量正好等于减速点所对应的剩余进给量时减速, 并按预期的减速规律减速运行到定位点停止。
但实际上, 伺服系统正常运转时每个采样周期反馈的脉冲数是几个、十几个、几十个甚至更多,因而实际减速点并不与理论减速点重合。
其最大误差等于减速前一个采样周期的脉冲数。
若实际减速点提前, 则按预期规律减速的速度降到很低时还未到达定位点, 可能需要很长时间才能到达定位点。
若实际减速点滞后于理论减速点, 则到达定位点时速度还较高, 影响定位精度和平稳性。
为此,我们提出了分段线性减速方法。
在低速趋近定位点的过程中,设速度为V0(mm/s,伺服系统的脉冲当量为δ(μm ,采样周期为τ(ms ,则每个采样周期应反馈的脉冲数为:N0=V0τ/δ。
小型光电伺服转台的设计及误差分析
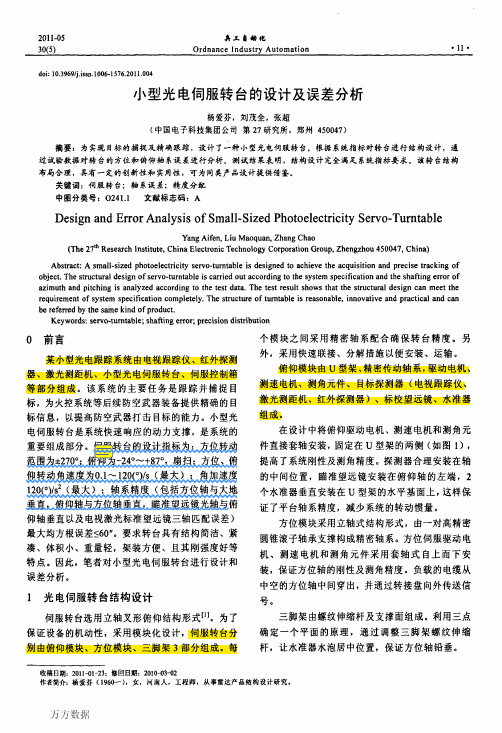
个模块之间采用精密轴系配合确保转台精度。另 外,采用快速联接、分解措施以便安装、运输。
俯仰模块由U型架、精密传动轴系,驱动电机、 测速电机、测角元件、目标探测器(电视跟踪仪、 激光测距机、红外探测器)、标校望远镜、水准器 组成。
在设计中将俯仰驱动电机、测速电机和测角元 件直接套轴安装,固定在U型架的两侧(如图1),
误差值/ (”)
-24 一14
-6
翟一
图2误差变化曲线
以水平仪读数为纵坐标,方位角为横坐标,做 出误差变化曲线(a),对测得的误差曲线作一最佳吻 合的正弦曲线Y=18.2sinx一8.9(使两者的均方根误 差最小)(b)。2条曲线的偏差就是方位轴的实际晃
第5期
杨爱芬,等:小型光电伺服转台的设计及误差分析
关键词:伺服转台;轴系误差;精度分配 中图分类号:0241.1 文献标志码:A
Design and Error Analysis of Small..Sized Photoelectricity Servo..Turntable
Yang Aifen,Liu Maoquan,Zhang Chao (The 27”Research Institute,China Electronic Technology Corporation Group,Zhengzhou 450047,China)
201l-05 30(5)
兵工自动化 Ordnance Industry Automation
doi:10.3969/j.issn.1006·1576.2011.004
小型光电伺服转台的设计及误差分析
杨爱芬,刘茂全,张超 (中国电子科技集团公司第27研究所,郑州450047)
摘要:为实现目标的捕捉及精确跟踪,设计了一种小型光电伺服转台。根据系统指标对转台进行结构设计,通 过试验数据对转台的方位和俯仰轴系误差进行分析。测试结果表明,结构设计完全满足系统指标要求。该转台结构 布局合理,具有一定的创新性和实用性,可为同类产品设计提供借鉴。
- 1、下载文档前请自行甄别文档内容的完整性,平台不提供额外的编辑、内容补充、找答案等附加服务。
- 2、"仅部分预览"的文档,不可在线预览部分如存在完整性等问题,可反馈申请退款(可完整预览的文档不适用该条件!)。
- 3、如文档侵犯您的权益,请联系客服反馈,我们会尽快为您处理(人工客服工作时间:9:00-18:30)。
传感器输出变化的最小输入变化值。指传感器能够检测到的被测
量对象的最小值。(分辨力反映了最小示值误差的辨别能力)
传感器的分辨力和其量程之比的百分数称为分辨率。
(4)重复性ex:指传感器输入量按同一方向变化,并连续多次
测量所测得的输出不一致的程度。它反映了传感器的随机误差。
ex=±[3σ/UFS]×100%
自整角机的静态精度分三个等级
精度等级
0级
1级
2级
静误差不大于 ±5(角分) ±10(角分) ±20(角分)
放大器
控制 线圈
r
U
刻度盘 E2
伺 服 电机 减 速 器 ZKB
雷达天线 俯仰角
ZKF
计算自整角机的测量误差时,分
a
Ui
1.
雷达俯仰角自动显示系统
自整机都有明确的精度等级,实际就是一个综合的精度指标。
1、如果各量均为确定函数,用拉氏变换归化:
3
E(s) e (s)R(s) eNi (s)Ni (s) i0
e (s)
E(s) R(s)
1 (s)
1 1 G1(s)G2 (s)G3 (s)G4 (s)
eN0
(s)
C ( s) N0 (s)
G1(s)G2 (s)G3 (s)G4 (s) 1 G1(s)G2 (s)G3 (s)G4 (s)
线性度表示图
当传感器输入量缓慢地从零点开始,逐渐增加到传感器输出值
刚刚开始微小变化时的输入值Δrs。
死区为输入量变化的一个有限区间内,输出为零。
对于双量测量元件,如果拟合直线通过死区中点,那么灵敏限
和死区是一致的。单向测量元件,二者本来一致。
(3)
分辨力指传感器输入从任意某个非零值开始变化时,所引起
(2)精密度(简称精度) 它表示传感器示值间的不一致程度。也就是说,测量结果不致性; 精度等级反映传感器综合精度的基本指标; 在工程测量中,为简单表示传感器测量结果的可靠程度,常用 精度等级A%来表示精度等级的概念。
附: 准确度:被测量的测量值与真值之间的一致程度;其不是一个量,不给出有 数字的量值。
2、分指标精度(七个分指标) U
(1) 线性度ef(非线性误差)
UFs
表示实测输出特性曲线与理想拟合
实际情况
U max
直线之间的吻合程度。其最大偏差为
ΔUmax,满量程输出为UFS,
拟合直线
ef=±[ΔUmax/UFS]×100%
把ef折算为输入量,还需除以该传感
r
器的灵敏度。 (2) 灵敏限(死区)Δrs
精度等级A%定义为
A% max 100% Δmax:在规定工xm作ax条件x下mi,n 测得的最大绝对误差允许值
Xmax
Xmin:测量范围下限值
L = Xmax - Xmin 量程
精度等级的意义:
A%=0.1%时,该传感器为0.1级;Δmax 在出厂时,一般取
3σ值。这意味着把随机误差看成高斯分 布,有99.73%的把握,
几点说明:
·关于误差E(s)与偏差ε(s)的区别
定义: E(s)=Cr(s) -C(s); ε(S)=R(s) -C(s)H(s) 对单位反馈,期望输出cr等于实际输入r,有E(s)= ε(s); 对非单位反馈,期望输出cr不等于实际输入r,其关系为:
Cr (s)=R (s)/H (s)=R′(S); E(s)= ε(s)/ H(s)
r
ε
_
G
c
r
r' 1/H
e
G
_
H
c
H
·关于干扰对误差E(s)的影响
C ( s)
·eN0 (s)
, N0 (s)
关于负号问题
而不是eN0 (s)
E(s) N0 (s)
ef (t) crf (t) c f (t)
Q crf (t) 0,ef (t) c f (t)
2、若输入r及干扰ni为随机量,且相互间独立,各自
使随机误差不大于Δmax。也有用2σ 值,即有95.45%的把握保
证随机误差不大于Δmax
如果给出了传感器的精度等级和量程L,传感器的最大误差
Δmax=A%·L
我国工业仪表等级分为0.1,0.2,0.5,1.0,1.5,2.5,5.0七个等级 ;
过程检测控制仪表的精度等级有0.005、0.02、0.1、0.35、0.5、 1.0、1.5、2.5、4等
(6)电源波动引起的误差 Δ6 = 10mV/V×0.01V = 0.1mV
总均方差
2
1 6
6 i 1
2 i
0.926(mv)2 ;
0.9811mv
3σ=±2.9434 mV 可以将输出最大误差折算到输入端(信号端),求出传感器的最
二、自整角机对的误差
自整角机广泛应用于冶金、航海等位置、 方位同步指示系统和火炮、雷达等伺服系统。 随动系统中常用自整角机作为测角元件, 并且成对使用。自整角机有力矩式和控制式 (变压器式)两种。力矩式用于同步指示系统; 控制式用作测角元件。
线性关系
对于动态情况,c与r的各阶导数有关,理想情况是各 阶导数为零。
输出与理想输出的偏差可看成随机分布,不管其原因
传感器给出的精度指标一般有两种(综合与分指标)
综合精度——精确度
这种指标把输出对于理想输出的偏差都看成是随机分布,不管 它是由什么原因造成的。综合精度有正确度和精密度两种。
(1)正确度(trueness) 它表明传感器示值有规律地偏离真值大小的程度,反映了元件 系统误差的大小;(大量测定的均值与真值的接近程度,与随机误差无关。) 其特点是被测量对象受少数几个元件影响显著作用而出现的误差; 一般来说,这些误差是有规律地出现的,它可通过适当地修
的静态误差为
2F 2J 102 202 22.4
三、提高测量精度的方法
对要求很高的控制系统,现有测量元件满足不了测量精度的 要求,需要从方法上提高测量精度。
提高测量精度的方法是针对元件主要测量误差来源不同而采 取不同的措施。有的方法能提高综合精度,有的能提高单项精 度。常用的方法
1.采用双读数的方法
一对精粗测自整角机测量装置。减速器的速比为i
如果发送机为1级精度,接收变压器为2级精度,仅用粗测对时
§2 伺服系统元件误差
了解元件误差,可以计算各 种元件误差对系统性能的影 响,利于正确选择元件,提 高系统精度。
次要输入
冲击振动 电磁场 供电 温度
测量元件的误差占系统误差 主 要 输 入 传 感 器
的比例重
(基准加使用)
主要输出
伺服系统中的测量元件对系 统精度的影响是直接的
反馈所包围回路中的各种放 大、执行等元件的误差或因 环境条件变化而引起的误差, 一般都会得到有效的抑制
第二章 伺服系统误差分析
主要内容
概述 伺服系统元件误差 伺服系统原理动态误差 伺服系统原理稳态误差 随机系统误差分析 伺服系统设计中的误差分配
§1 概 述
伺服系统要求被控对象(角度、位移、速度)按指 定的规律变化
系统稳定的前提下,总是存在一定的误差(也称控 制精度,精度是重要指标之一)
要,测量区域常常不包含零点。因此,线性度、迟滞回差、重复
性、温度误差和电源误差是主要的误差来源)
计算总误差时可以认为它们是独立的、且对总误差影响很小的
随机变量服从高斯分布。设每个单项误差为Δi,则总的误差为
emax 3 ,
1
n
n
i2
i 1
有的元件在使用时还要考虑输入阻抗、输出阻抗的匹配问题。
例 计算CYG
ed = [Δd/UFS ]×100% 其中:
Δd为相邻时间间隔对应于满量程UFS输入的同一100%输入所 测得的输出最大差值;UFS
em = [ Δc/UFS ]×100%
Δc为相邻时间间隔对应于满量程UFS输入的同一90%输入所
CJSYS-A01角速度传感器
实际的测量元件,有的只给出上面多项指标中的几项;
eN1 (s)
C ( s) N1 ( s)
G2 (s)G3 (s)G4 (s) 1 G1(s)G2 (s)G3 (s)G4 (s)
eN 2
(s)
C ( s) N2 (s)
1
G3 (s)G4 (s) G1(s)G2 (s)G3 (s)G4 (s)
eN3
(s)
C ( s) N3 (s)
G4 (s) 1 G1(s)G2 (s)G3 (s)G4 (s)
规格:0.5MPa, 1MPa, 2.5MPa, 10MPa, 20MPa 输出灵敏度:10mV/V; 非线性、迟滞、重复性:≤0.5%
输出阻抗:1KΩ; 零位温漂:4 104/C·FS
灵敏度温漂:4 104 /C·FS
求激励电源为15V±1%,50℃时的非零点测量精度。 解:满量程输出 UFS = 10mV/V×15V = 150mV
讨论系统各环节对输入信号、干扰信号引起的误差传 递和归化
结构已知的系统如下:
n0
n1
r
E(s)
_ G1(s)
G2(s)
n2
G3(s)
n3
G4(s) c
输入R(s),输入干扰噪声N0(s),输出C(s),误差E(s),各级的 等效扰动信号分别为N1(s)、N2(s)、N3(s)。对单位反馈系统而 言,总的误差就是R(s)、N0(s)、N1(s)、N2(s)、N3(s)所引起的误 差归化到E(s)点上的总和。
/ KT0 ]100%
式中KT1表示变温后的灵敏度;KT0表示常温下的灵敏度;T1表示
变温后的温度;T0
b)温度零点飘移
eT
U0T1 U0T0 T1 T0
式中U0T1表示变温后的零位输出;U0T0表示变温前的零位输出。