硅溶胶型壳常见缺陷及防止措施
低温蜡-硅溶胶型壳的应用实践

1.2 低温 蜡与 中温 蜡 的比较
笔者认 为采 用低 温蜡 (指 常用 的石 蜡一硬 脂 酸蜡 料 ) 代 替 中温蜡 生产 硅溶 胶 型 壳 是符 合 我 国 国情 也 是 值得 推荐 的合理 工 艺 ,更是 我 国大部 分采 用水 玻璃 及 复合 型 壳的 精铸 厂技 术改进 的合 理选 择 。笔者 认 为 ,生产 一 般 质量 要求 (Ra一6.3~ 25 m,CT5~ CT7)的 民用 、商用 精铸 件 ,特别 是 5 kg以上 的 中 、大件 ,低 温 蜡 比中 温蜡 更 为经济 实用 。
(2)低温蜡 的强度 、软 化 点及 硬 度 (针 人度 )均 比 中 温蜡 低 ,虽便 于修饰 、焊 装 ,但 锐边 、尖 角处 易碰 损 ,字模 也 因压力 低 而不够 清晰 ,生产 簿壁 ( 2 mm)或 细长 杆 等精 铸 件 比较 困难 ,蜡 模表 面粗糙 度也 比中温蜡 低 1个 等级 。又 由于低 温蜡 固液相 温度 区 间甚 小 ,故蜡 模 尺寸 稳定 性较 差 ,不利 于生 产高尺 寸 精度 的铸件 。
服 了其对 蜡 模 润 湿 性 差 的 困难 后 ,将 会 在 我 国 推 广 应 用 。
(3)采 用 硅溶胶 型 壳 的铸 件 ,尤其 是不 锈钢 、耐 热钢 等高 合金 钢铸 件 ,表 面质 量 大 为 提 高 ,返 修 率 、焊 补 、清 铲 、打磨 工序 工作 量 明显 减 轻 ,故 其 后 道 工 序 的 工 时 和 材料 消耗 比水 玻璃 有所 降低 。另外 ,由于型壳 厚度 大 为 减薄 ,焙烧 温 度提 高 (水 玻 璃 型壳 焙 烧 温度 为 800 950 ℃),焙烧 时 间缩 短 ,也 使 能耗下 降 。又 由于铸 件 尺寸精 度高 ,表 面缺 陷少 ,铸 件 加 工 余 量 也 可 减 小 。按 以 上 因 素综 合 计算 ,每 kg铸 件 实 际 成本 又 可 下 降 1元 。综 上 所述 ,硅 溶胶 型 壳与水 玻璃 型壳 的铸件 综合 成本 差价 可 缩 小 到每 kg 1~2元 ,其平 均销 售 差价 可缩 小为 每 kg 2 元 以 内 。在 提高 铸件 质量 前提 下 ,适 当提高 铸件 销售 价 完 全可 以得 到 客户 的理解 和认 同。
硅溶胶的胶团结构和干燥胶凝过程-对硅溶胶型壳的几点认识之一

硅溶胶的胶团结构和干燥胶凝过程)))对硅溶胶型壳的几点认识之一中国科学技术大学 许云祥X蓬莱金创精铸阀业有限公司 鲁 蕊 李 磊摘 要 介绍了硅溶胶的胶团结构,胶团由胶核、吸附层和扩散层组成。
硅溶胶中的水分由自由水、吸附水和结构水3部分组成。
计算了硅溶胶开始胶凝的失水率和胶凝区范围。
关键词:硅溶胶 胶凝 失水 胶团结构中图分类号:TG249.5 文献标识码:A 文章编号:1001-2249(2004)02-0052-031 硅溶胶的胶团结构硅溶胶是一种乳白色的透明胶体溶液,胶体颗粒近似于球状。
目前国内熔模铸造使用的是碱性硅溶胶,其SiO 2的质量分数为30%左右,胶粒直径为7~20nm 。
图1所示为硅溶胶的胶团结构。
胶核的基本成分为SiO 2,其内部结构为Si-O-Si 键相联结的立体网状结构,在胶核和水接触的界面上形成了Si-OH 硅醇键,由于此硅醇键为极性分子键,因此使得胶核表面呈现了负热力学电位<。
图1 硅溶胶的胶团结构硅溶胶中的水能按式(1)进行解离,形成H 3O +和OH -的离子,氢离子在水中永远是以水化形态H 3O +存在的[1],但是H 2O 的电离度极小。
H 2O +H 2O =H 3O ++OH -(1)另外未解离的水分子中的O -H 键不是直线对称分布,而是有角度的,其键角为105b ,因此水分子是极性分子,有偶极存在。
在胶核的负电位作用下,胶核将吸附水化氢离子H 3O +,同时也将吸附极性水分子并使其取向,形成吸附层。
而取向的极性水分子正是水化氢离子H 3O +的载体,其量远远大于水化氢离子数,在正常熔模铸造使用的硅溶胶中,是水化氢离子数的几亿倍到几十亿倍。
吸附层与胶核结合紧密,当胶核运动时,吸附层能相随一起运动,因此将带有吸附层的胶核统称为胶粒,此时的胶粒带有负的动电电位F 。
由于胶粒动电电位的存在,水中的H 3O +也将受其电场的静电作用,但由于热运动而使H 3O +离子扩散分布,形成扩散层。
硅溶胶水玻璃复合工艺易出现的问题

一、对硅溶胶水玻璃复合工艺的介绍硅溶胶水玻璃复合工艺是一种常见的玻璃加工工艺,通过将硅溶胶涂覆在玻璃表面后再进行固化处理,形成一层具有耐磨、防水、耐腐蚀等特性的材料。
这种工艺广泛应用于建筑、玻璃工艺制品、家居用品等领域。
二、硅溶胶水玻璃复合工艺易出现的问题1. 硅溶胶选择不当:硅溶胶的选择直接影响着复合后的玻璃表面性能,如果选择不当,可能导致复合膜的附着力不足、耐磨性差等问题。
2. 复合厚度不均匀:在复合过程中,如果涂覆的硅溶胶层厚度不均匀,可能导致玻璃表面出现凹凸不平的情况,降低美观度和使用寿命。
3. 固化温度不足:硅溶胶水玻璃复合后需要进行固化处理,如果固化温度不足,可能导致复合膜的硬度不足,影响其耐磨、耐腐蚀性能。
4. 固化时间不足:固化时间不足会导致硅溶胶水玻璃复合层未完全固化,使得其性能不稳定,容易出现开裂、剥离等问题。
5. 操作流程不规范:在硅溶胶水玻璃复合工艺中,如果操作人员在操作过程中存在疏忽大意、操作流程不规范等问题,可能导致复合效果不理想。
三、解决硅溶胶水玻璃复合工艺易出现的问题的建议1. 选择合适的硅溶胶:在进行硅溶胶水玻璃复合工艺时,应根据玻璃的具体用途和要求选择合适的硅溶胶,保证复合后的性能满足需求。
2. 控制涂覆厚度:在复合过程中,要严格控制涂覆厚度,确保复合膜的厚度均匀,避免出现凹凸不平的情况。
3. 严格控制固化条件:在固化过程中,要严格控制固化温度和固化时间,确保复合膜能够充分固化,保证其性能稳定。
4. 规范操作流程:在进行硅溶胶水玻璃复合工艺时,要制定规范的操作流程,严格按照操作规程进行操作,避免出现疏忽大意导致的问题。
四、结语硅溶胶水玻璃复合工艺是一种常见的玻璃加工工艺,在实际应用中容易出现一些问题。
通过选择合适的硅溶胶、严格控制涂覆厚度、固化条件和规范操作流程,可以有效解决这些问题,保证复合后的玻璃具有良好的性能和稳定的质量。
在进行硅溶胶水玻璃复合工艺时,除了上述提到的问题和解决建议外,还有一些其他容易出现的问题需要引起注意。
硅溶胶型壳常见缺陷及防止措施
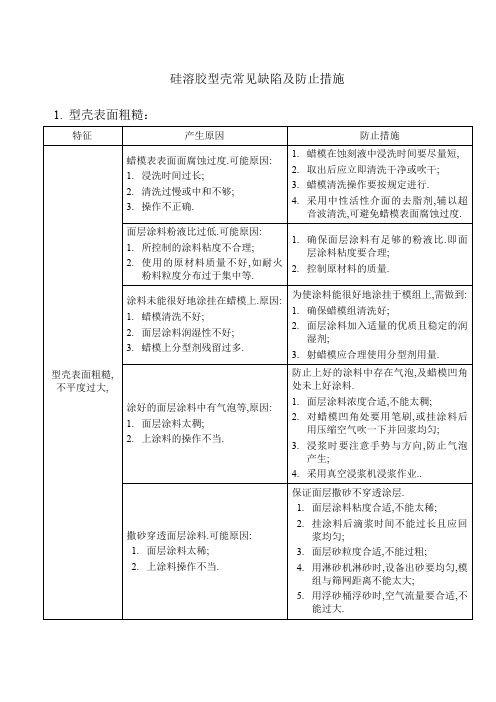
当浸浆时,预湿液已经干燥或流失,则死角地区仍被空气占据,失去预浸功能,因此,应训练作业人员的回浆作业手法,在浸浆之前,应用回浆手法使预湿液能均匀的占据蜡型(或壳型)的每一个角落.挤除空气并预湿表面.
浆内气泡太多
配制浆料后,必须要经过4h以上的浸润浆料及排除气泡,湿润剂在过度的搅拌下也会产生气泡,故需对搅拌速度进行适当设定.虽然一切均无问题,浆液中仍会因混入空气而有小气泡,故在浆液中要加入少量的消泡剂辅助去除气泡.
面浆内的湿润剂不够
不同厂牌的湿润剂,效果不同,其用量亦不相同,应各自试用恰当的用量,不可过多,否则会产生过多的气泡.另外醇基湿润剂会挥发,故隔一段时间后应继续追加.
10.壳模破裂:
特征
形成原因
防止措施
壳模局部位置表面出现一定深度的裂痕,严重者则为自内而外穿透性裂缝.
脱蜡前陶壳破裂
浸浆室及干燥区的温度不稳定,造成蜡型热胀,使陶壳胀裂。需改善空调温控系统与除湿间的保温绝热性能。
面层耐火砂堆积太厚
面层耐火砂一般均用100目左右的细砂,在面层沾浆作业时,常会产生堆集层,在浸第二层浆前,预浸时未将堆集的耐火砂支队,则经二层浆所接触的是面层的浮砂而非面层壳,形成脆弱的浆—砂—砂—浆结构,而不是正常的浆—砂—浆—砂结构。解决办法为在制作下层型壳前抖落或吹除浮砂。
背层浆料料浓度太高
背层浆的浓度太高时,浆的流动性本就不够好,再加上前层干陶壳的吸水作用,使浆的流动性更差无法渗入砂层建立坚强的陶壳,仅能沾在前层陶壳砂的外端,自然很容易形成浆—砂—砂—浆的不良陶壳。在脱蜡泄压太快或陶壳在脱蜡后放置干燥时间不够,在烧结陶壳时的快速升温,都会因蒸汽压而使陶壳分层剥裂。
9.未润湿:
特征
产生原因
熔模铸造型壳六大缺陷分析 入木三分
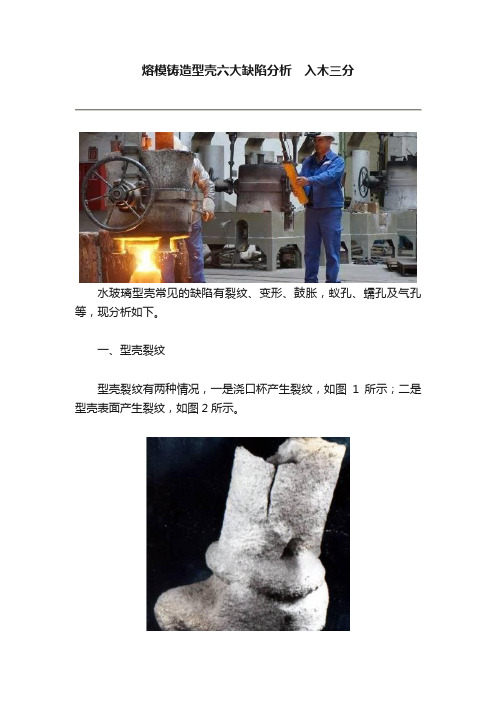
熔模铸造型壳六大缺陷分析入木三分水玻璃型壳常见的缺陷有裂纹、变形、鼓胀,蚁孔、蠕孔及气孔等,现分析如下。
一、型壳裂纹型壳裂纹有两种情况,一是浇口杯产生裂纹,如图1所示;二是型壳表面产生裂纹,如图2所示。
图1 浇口杯裂纹图2 型壳表面裂纹浇口杯裂纹特征:型壳的浇口杯有裂纹,严重时浇口杯开裂。
型壳表面裂纹:在型壳的表面上有弯曲的、深浅不等的裂纹。
1.产生原因(1)涂料中水玻璃的模数、密度过高或过低;涂料中的粉液比过低;或硬化剂的浓度、温度和硬化时间不当,硬化不充分;或型壳在硬化前的自然风干时间不够,不利于硬化剂的继续渗透硬化,影响了硅凝胶的连续性和致密性;或型壳的层数不够等原因,导致型壳的强度低,出现了裂纹。
(2)涂料层涂挂的不均匀,或撒砂层厚薄不均;尤其是浸涂料后没有撒上砂的部位,硅凝胶在收缩时受力不均匀,导致型壳产生裂纹。
(3)脱蜡液的温度低,脱蜡时间太长。
由于蜡料的热膨胀系数大于型壳的热膨胀系数,脱蜡缓慢将导致型壳在脱蜡的过程中受到各种应力的作用;如果超过此时型壳的强度极限,就会产生裂纹,甚至开裂。
(4)焙烧时,型壳入炉温度高,升温过快,或高温出炉急冷;或型壳多次焙烧,产生微裂纹,甚至裂纹,降低了强度;或型壳的高温强度低,使型壳在焙烧时产生裂纹。
(5)清理浇口杯时,机械损伤浇口杯。
2.防止措施(1)采用下列措施,型壳的高温强度就高。
①水玻璃的模数M=3.0~3.4,密度ρ=1.30~1.33 g/cm3配制的加固层涂料。
②采用合理的涂料配制工艺,并执行涂料的“配比-温度-粘度”曲线。
③采用合理的硬化工艺,控制硬化剂的“浓度-温度-硬化时间”;或选用氯化铝代替氯化铵硬化型壳。
④合理的制壳工艺,如涂料粘度与撒砂粒度的合理配合,硬化工艺参数要确保型壳充分硬化。
⑤采取措施增加型壳强度,如常用的增加型壳层数,或采用复合型壳等;必要时大件型壳可用铁丝加固等。
(2)蜡模浸入检验合格的涂料中,上下移动和不断地转动,提起后滴去多余的涂料,使涂料均匀地覆盖在模组的表面上;不能出现涂料的局部堆积或缺少涂料(漏涂);并及时、均匀撒砂。
精铸硅溶胶型壳工艺的改进电子教案

5.由表十一,十二及十三实验结果得出以下结论:
⑴.在表面层涂料中加入少量“分散剂”能改变硅溶胶涂料的流变特性,增
加涂料的屈服值从而可提高涂挂性和覆盖性(涂层平均厚度)3可提高15-25%。同时由于
“分散剂”作用能使粉料“分散”不易“结团”。使平均粒径减小因而3增加。虽然粉液比
n略有下降,但致密性k%仍在要求范围之内(表七)。涂料的均匀性,悬浮性,涂挂性和流 平性均有提高。“板结”“老化”时间延长(稳定性提高)。
1.美国在2006年前面层涂料的典型工艺是在锆英粉中掺加5-10%(质量)的熔融石英粉。
其主要目的是:降低成本,提高铸件尺寸精度和改善脱壳性、透气性。国外重点工艺改进方 向是:充分利用熔融石英纯度高,杂质少,密度和热膨胀系数小,加上高温“析晶”,低温
“相变”的特点,使型壳在高温时保持高强度而在低温时因相变产生剧烈收缩(-3.7%)致
精铸硅溶胶型壳工艺的改进
前言:
众所周知,全球精铸界通用的硅溶胶型壳工艺存在三大缺点:
1.成本高。2.制壳周期长。3.铸件脱壳性差(型壳残留强度高)。
据统计,表面层型壳通用的耐火料锆英石砂、粉占型壳原辅材料成本的48%占总生产成本
的10%(平均值)[1]。优质锆英石资源稀缺,因而寻找它的代用品或减少其消耗量是当今 国内外精铸界共同关心,重点研究的课题之一。
2.混合涂料用粉料粒度要求应符合表五规定。
注:1•采用GSL-101BI型“激光颗粒度测定仪” 测定(丹东市辽宁仪器仪表研究所生产)
2.粒度判定以DV90, DV50及Wo三项指标为主要依据。DV98 DV84为参考指标。
3.无粒度检测条件时,可将待测粉料与“标准”硅溶胶配制成“标准”涂料来判定
对熔模铸造硅溶胶型壳清理问题的探讨申鹏帅

对熔模铸造硅溶胶型壳清理问题的探讨申鹏帅发布时间:2023-06-15T01:59:17.468Z 来源:《中国电业与能源》2023年7期作者:申鹏帅[导读] 本文就熔模铸造硅溶胶型壳清理进行探究,最先阐述了熔模铸造硅溶胶型壳的常见清理方法,之后对影响熔模铸造硅溶胶型壳的清理因素进行分析,对制备过程与焙烧过程中的工艺进行分析,进一步降低清理难度,提高清理效率,实现良好的型壳清理。
上海万泽精密铸造有限公司 201400摘要:本文就熔模铸造硅溶胶型壳清理进行探究,最先阐述了熔模铸造硅溶胶型壳的常见清理方法,之后对影响熔模铸造硅溶胶型壳的清理因素进行分析,对制备过程与焙烧过程中的工艺进行分析,进一步降低清理难度,提高清理效率,实现良好的型壳清理。
关键词:熔模铸造;硅溶胶型壳;型壳焙烧引言铸造型壳是熔模铸造的关键部件,其性能好坏直接影响到铸件质量。
由于硅溶胶型壳的高强度、低密度、耐热性、耐腐蚀性和高耐磨性等优点,在熔模铸造中得到广泛应用。
但是,硅溶胶型壳在使用过程中,会产生一些缺陷,如型壳表面的积粉、粘砂、气孔等。
如果处理不当,会导致铸件质量下降。
因此,如何有效地清除型壳上的积粉和粘砂是非常重要的。
1.型壳清理的方法为了解决硅溶胶型壳清理的问题,人们进行了大量的研究,但目前还没有比较有效的方法。
目前,最常用的型壳清理方法有湿法、干法、化学法和机械法四种。
(1)湿法是用水、化学试剂或机械力去除型壳上的积粉和粘砂。
湿法清理型壳的主要特点是:(1)用水或化学试剂清除型壳上的积粉和粘砂很方便,一般用水就能达到目的。
(2)可以不留型壳上的残余涂料,因为在清理后型壳表面基本没有残留涂料。
(3)对于大直径的型壳,湿法清理成本很低。
干法清理型壳的主要特点是:(1)型壳上残留有大量的粉尘颗粒,有时会产生积粉和粘砂。
(2)清理后型壳表面很干净,不会留下残余涂料。
(3)由于型壳表面无残留涂料,因此型壳在使用过程中不易产生裂纹或裂纹倾向。
涂料制壳工序存在的几个常见的不足

涂料制壳工序存在的几个常见的不足硅溶胶模壳的缺点就是干燥时间长,而且越到后面越难干燥。
因此,干燥是硅溶胶涂料制壳的一道重要工序。
硅溶胶模壳通过干燥获取湿强度。
但是,在实际生产中,制壳现场经常存在一下一些不当之处,影响制壳干燥。
1.模壳摆放稠密,导致模壳干燥时间变长或者干燥不良。
在模壳干燥中,湿度是影响模壳干燥的第一大要素。
正是因为模壳内部涂料的湿度与外部环境有湿度差,才能保证模壳中水分蒸发。
模壳稠密堆积,局部湿度大,影响模壳内部水分蒸发速度。
对有些深腔,窄槽,不通孔类产品,可能还会造成同样干燥时间但干燥不良的情况。
2.有干燥线,但形同摆设。
顾名思义,模壳干燥线是用来干燥模壳的。
但是在有些企业中,由于工作习惯以及产品结构方面的原因,存在干燥线上悬挂的产品很少,而且结构相对简单,易干燥。
而真正需要上干燥线难干燥的产品,却放在架子上。
这是非常不合理的。
3.风扇数量不足或者有风扇不充分利用。
在涂料制壳背层模壳干燥时,风速是一个干燥的重要因素,而且要求立体风。
何谓立体风,就是四面八方都有风,促进模壳中的水分蒸发。
在生产现场经常存在风扇不开或者只开部分,这些都是造成模壳干燥不良的隐患。
另外,风扇分布也是制壳工序需注意的一个重要内容。
4.模组吊钩盖板不能正确使用。
模组使用吊钩盖板有两个作用。
一是便于悬挂,二是减少蜡污染。
但在现场经常存在两种情况:一是盖板是变形的,不能彻底盖住模组浇口杯的顶部;而是在沾浆时浆料进入模头的内部,既难清理而且污染蜡,给后面的蜡处理带来很大的麻烦。
5.涂料制壳现场是个环绕立体风的地方。
水分蒸发比较快。
但是好多单位设计时将浆桶(操作现场)与干燥室放在一起,而且经常不盖浆桶,很容易导致硅溶胶水分失去产生胶凝,进而变质,而且存在不补加水分(蒸发)。
6.涂料制壳现场经常是粉尘比较大,对干燥线以及浆桶、空调等设备性能发挥产生很大的副作用,必须及时对现场设备除尘,加油等。
如果做不到这点,可能会对设备的正常使用产生影响。
- 1、下载文档前请自行甄别文档内容的完整性,平台不提供额外的编辑、内容补充、找答案等附加服务。
- 2、"仅部分预览"的文档,不可在线预览部分如存在完整性等问题,可反馈申请退款(可完整预览的文档不适用该条件!)。
- 3、如文档侵犯您的权益,请联系客服反馈,我们会尽快为您处理(人工客服工作时间:9:00-18:30)。
硅溶胶型壳常见缺陷及防止措施1.型壳表面粗糙:
2.型壳面层裂纹:
特征产生原因防止措施
型壳表面层出现不规则的裂纹,或出现极细小的龟状裂纹这些裂纹是型壳干燥时产生的,主
要是由于面层干燥过快,或涂料干
燥收缩过大引起的,或由于蜡模热
膨胀使面层型壳被胀裂.及型模焙
烧不当引起.具体产生原因:
1.环境相对湿度太低
2.面层干燥时间过长
3.空气流动不均匀而且过大
4.环境温度变化过大
5.壳模焙烧不当.
1.面层干燥区相对湿度宜在RH60~
70%之间.
2.面层干燥时间以4~6h为宜,特殊
产品不要超过10h.
3.风不要正对模组吹,应降低直接吹
到模组上的气流量.
4.制壳间温度应严格控制,保持在
22~25℃之间.
5.脱蜡后壳模应在至少4h后装炉焙
烧.尽量避免高温-低温-高温焙烧
及二次焙烧.
3.型壳面层鼓裂:
特征产生原因防止措施
型壳面层局部与蜡模分开向外鼓起(图a),或鼓起后破裂导致背层涂料流到蜡模和面层之间,但未将空
隙填满(图b、图c)., 1.面层型壳与蜡模间附着力太
差
1.确保蜡模清洗好.
2.面层涂料润湿剂加入量合适.
2.面层型壳外表面干燥过度、内
表面干燥不足.
1.控制好环境相对湿度、面层干燥时
间和风速,确保面层型壳外、内表面
干燥合适.
2.应使面层涂料厚合适,不要过厚.
3.面层型壳湿强度不足,特别是
在蜡模锐角处其强度低
1.保证面层型壳湿强度.为此,要保证
硅溶胶和耐火材料的质量,按工艺规
范保持涂料正确配方,配制方法及确
保涂料性能合格.
2.要保证蜡模锐角处有一定厚度的
涂料,且涂料不要滴得过干.
4.制壳间温度不均匀保持制壳间温湿度均匀.
4.型壳内孔搭桥:
特征产生原因防止措施内孔、凹槽处的型壳不致
密,局部有未上好涂料,未撒上砂使该处型壳存在孔隙搭桥. 1.第一层或背层涂料太稠.
2.孔洞或狭缝处浸浆不足.
3.撒砂过粗,以致孔洞或狭缝
处很快就被塞住.
4.孔洞或狭缝处松散砂粒在
浸下层浆时未被清除掉.
5.内孔或凹槽处型壳干燥不
足.
1.控制好第二层和背层涂料粘度.
2.细致地上孔洞或狭缝处的涂料.
3.撒砂使用较细的砂,防止孔洞或
狭缝处过早被塞住.
4.注意将孔洞或狭缝处松散的浮
砂吹除,再上下层涂料.
5.注意内孔或凹槽处型壳干燥情
况,不干时不能制作下层模壳.
5.型壳面层剥落:
特征产生原因防止措施
型壳型腔尺寸变大,表面不光洁. 面浆与蜡型的附着力太差
1.改善蜡模蚀刻清洗,利用溶剂轻微腐
蚀蜡模表面以增强其与浆层的吸附
力.
2.破坏宽大之平面,在宽广平面上加上
若干凸出物或筋,减少平面宽广程度,
以利浆附着.
3.在型蜡中添加一些亲水性物质,改善
蜡的亲水性,也可有效增强面浆与蜡
型的吸附力.
面层在制下层型壳过程中剥落,这是
由于面层还没有干燥就制第二层型
壳,硅溶胶发生回溶现象,使面层型壳
剥落.
控制好环境相对湿度、温度、风速和干燥
时间,确保面层干燥后再做第二层.
面层干燥过快或过度
增加面层干燥区的的湿度,一般为
RH60~70%,但在特殊有深穴如盒状铸件
内部不易干燥的状况,甚至相对湿度设定
为70~80%.减少空气的流速,避免内外
速率相差太大,外部本就较易干燥,若再
加风吹,则外部已干燥过度,而内部尚未
干燥,因此减少空气流动,对拉动内外干
燥一致有较大助益.
相对湿度愈高,风速愈小,则室内的干湿
球温差愈小,如此,可避免壳型在干燥初
6.型壳强度低:
7.型壳裂纹:
8.气泡、毛刺:
9.未润湿:
10.壳模破裂:
11.壳模层间剥落:
12.壳模鼓胀变形、强度不足:。