典型零件数控加工工艺分析实例
数控车床典型零件加工

前言轴是组成机器的重要零件之一根据轴的承载性质不同可将轴分为转轴、心轴、传动轴三类。
工作时既承受弯矩又承受转矩的轴称为转轴。
转轴是机器中最常见的轴,通常称为轴。
用来支承转动零件,只承受弯矩而不传递转矩的轴称为心轴。
心轴有固定心轴和旋转心轴两种。
根据轴线的形状不同,轴又可以分为直轴、曲轴和挠性钢丝轴。
后两种属于专用零件。
直轴按其外形的不同又可以分为光轴和阶梯轴两种。
光轴形状简单、加工容易,应力集中源少,主要用作传动轴。
阶梯轴个轴段截面的直径不同,这种设计使个轴段的强度接近,而且便于轴上零件的装拆和固定,因此阶梯轴在机器的应用中最为广泛。
直轴一般都制成实心轴,但为了减轻重量或为了满足有些机器结构上的需要,也可以采用空心轴。
轴通常由轴头,轴颈、轴肩、轴环、轴端和不安装任何零件的轴段等部分组成,这次设计我主要是设计减速器当中的传动轴,希望通过这次设计,我能学到更多的东西。
目录摘要ﻩ第一章绪论 ...................................................................................................................1.1数控机床的简介ﻩ1.2数控的发展趋势 ..............................................................................................1.3传动轴的概述ﻩ第二章工艺分析 .............................................................................................................2..1零件图工艺分析 ............................................................................................2.3切削顺序的选择 ............................................................................................2.4切削用量的选择和加工余量的确定ﻩ第三章设备的选择 .......................................................................................................3.1机床选择ﻩ3.2刀具的选择ﻩ3.3刀具卡.............................................................................................................................3.4夹具的选择 ........................................................................................................3.5切削液的选择ﻩ3.6量具的选择 ...................................................................................................... 第四章零件的编程ﻩ4.1手工编程ﻩ4.2工艺卡ﻩ4.3工序卡 ................................................................................................................ 结论…………………………………………………………………参考文献……………………………………………………………附录…………………………………………………………………后记…………………………………………………………………摘要轴是组成机器的重要零件之一,轴的主要功用是支承旋转零件、传递转矩和运动。
数控车床零件的工艺分析及编程典型实例

数控车床零件的工艺分析及编程典型实例更新日期:来源:数控工作室根据下图所示的待车削零件,材料为45号钢,其中Ф85圆柱面不加工。
在数控车床上需要进行的工序为:切削Ф80mm 和Ф62mm 外圆;R70mm 弧面、锥面、退刀槽、螺纹及倒角。
要求分析工艺过程与工艺路线,编写加工程序。
图1 车削零件图1.零件加工工艺分析(1)设定工件坐标系按基准重合原则,将工件坐标系的原点设定在零件右端面与回转轴线的交点上,如图中Op点,并通过G50指令设定换刀点相对工件坐标系原点Op的坐标位置(200,100)(2)选择刀具根据零件图的加工要求,需要加工零件的端面、圆柱面、圆锥面、圆弧面、倒角以及切割螺纹退刀槽和螺纹,共需用三把刀具。
1号刀,外圆左偏刀,刀具型号为:CL-MTGNR-2020/R/1608 ISO30。
安装在1号刀位上。
3号刀,螺纹车刀,刀具型号为:TL-LHTR-2020/R/60/1.5 ISO30。
安装在3号刀位上。
5号刀,割槽刀,刀具型号为:ER-SGTFR-2012/R/3.0-0 IS030。
安装在5号刀位上。
(3)加工方案使用1号外圆左偏刀,先粗加工后精加工零件的端面和零件各段的外表面,粗加工时留0.5mm的精车余量;使用5号割槽刀切割螺纹退刀槽;然后使用3号螺纹车刀加工螺纹。
(4)确定切削用量切削深度:粗加工设定切削深度为3mm,精加工为0.5mm。
主轴转速:根据45号钢的切削性能,加工端面和各段外表面时设定切削速度为90m/min;车螺纹时设定主轴转速为250r/min。
进给速度:粗加工时设定进给速度为200mm/min,精加工时设定进给速度为50mm/min。
车削螺纹时设定进给速度为1.5mm/r。
2.编程与操作(1)编制程序(2)程序输入数控系统将程序在数控车床MDI方式下直接输入数控系统,或通过计算机通信接口将程序输入数控机床的数控系统。
然后在CRT 屏幕上模拟切削加工,检验程序的正确性。
第三讲典型轴类零件数控车削加工工艺及编程

B
准确定位
B
英制O米制OB:基本功能 0:选购功能 数控车设定—— A功能
2. 进给功能(F功能)
F 功能指令用于在程序中控制切削进给量,有两种指令模式: (1)每转进给模式(G99)
编程格式: G99 F ___; F后面的数字表示主轴每转一转刀具的进给量。 单位:mm/r。
说明:模态指令,一经指定直到被G98取代,一直有效。 系统默认状态,车床上一般常用此种进给量指令方式。
A’ 65,2
B’ 10.01,2
C‘ 18.01,-2
D’ 18.01,-20
E‘ 24,-25
F’ 28,-25 G‘ 48.016,-35 H’ 48.016,-51 I‘ 58.023,-51 J‘ 58.023,-58 K’ 62,-58
符号
含义
编程原点
零件外轮廓走刀路线
工序号 程序段号
工步号 加工内容
粗车左端外轮廓,X轴留0.4、 Z轴留0.1精加工余量
精加工左端面外轮廓,各加工 表面符图示要求
审核
产品名称或代号
零件名称
材料 零件图号
XXX
夹具名称
三爪卡盘
刀具号
刀具规格/ (mm)
主轴转速/ (r/min)
T01
25×25
粗600 精1000
螺纹轴
45钢
XXX
使用设备
车间
CK6132
数控车
进给速度/ 背吃刀量/ 备注 (mm/r) (mm)
恒转速控制 编程格式: S ~
S后面的数字表示主轴转速,单位: r/min。
注意:
在具有恒线速功能的机床上, S 功能指令可限制主轴最高转速
(1)主轴最高转速限制(G50)
UGNX8.0数控加工典型实例教程——第2章-平面铣
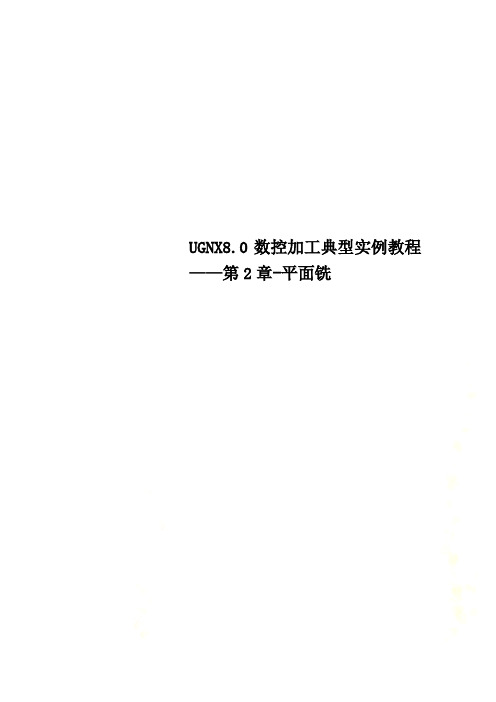
UGNX8.0数控加工典型实例教程——第2章-平面铣第2章平面铣2.1平面铣概述平面铣(Planar Milling)是一种常用的操作类型,用来加工直壁平底的零件,可用作平面轮廓、平面区域或平面岛屿的粗加工和精加工,它可平行于零件底面进行多层铣削,典型零件如图2-1所示。
图2-1 典型平面铣零件平面铣是一种2.5轴加工方式,它在加工过程中首先进行水平方向的XY两轴联动,完成一层加工后再进行Z轴下切进入下一层,逐层完成零件加工,通过设置不同的切削方法,平面铣可以完成挖槽或者轮廓外形的加工。
平面铣的特点包括:刀轴固定,底面是平面,各侧壁垂直于底面。
9 CLEANUP_CORNERS清理拐角使用切削模式为“跟随部件”,清除以前操作在拐角处余留的材料10 FINISH_WALLS精加工壁使用切削模式为“轮廓加工”,精加工侧壁轮廓,默认情况下,自动在底面平面留下余量11 FINISH_FLOOR精加工底面使用切削模式为“跟随部件”,精加工平面,默认情况下,自动在侧壁留下余量12 HOLE_MILLING铣孔用铣刀铣孔13 THREAD_MILLING螺纹铣适用于在预留孔内铣削螺纹14 PLANAR_TEXT 平面文本对文字曲线进行雕刻加工15 MILL_CONTRO铣削控创建机床控制事L 制件,添加后处理命令16 MILL_USER 铣削用户自定义参数建立操作说明:1.第4个是通用操作,可派生出其它各种子类型,其它子类型是在通用操作的基础上派生出来的,主要是针对某一特定的加工情况而定义,即预先指定和限制了一些参数。
2.基本平面铣可实现平面类零件一般的粗加工和精加工,其它子类型可根据实际情况灵活选择。
2.2创建平面铣操作的一般步骤1.在操作导航器中创建程序、刀具、几何、加工方法节点组;说明:大多数情况下只需要创建刀具、几何节点组,程序、加工方法可利用系统提供的节点组或经编辑后使用。
2.在创建操作对话框中指定操作类型为;3.在创建操作对话框中指定操作子类型为;4.在创建操作对话框中指定程序、刀具、几何、加工方法节点组;5.在创建操作对话框中指定操作的名称;6.在创建操作对话框中单击按钮,进入“平面铣”操作对话框;7.如果有未在共享数据(几何节点组)中定义的几何,在平面铣操作对话框中定义;8.定义平面铣操作对话框中的参数;9.单击平面铣操作对话框中的生成按钮,生成刀轨。
数控编程加工工艺实例分析

数控编程加工工艺实例分析文/罗谷清数控机床是一种技术密集度及自动化程度很高的机电一体化加工设备,是综合应用计算机、自动控制、自动检测及精密机械等高新技术的产物,它严格按照加工程序,自动地对被加工工件进行加工。
随着数控机床的发展与普及,现代化企业对于懂得数控加工技术、能进行数控加工编程的技术人才的需求量必将不断增加。
数控车床是目前使用最广泛的数控机床之一。
数控编程是指从零件图样到获得数控加工程序的全部工作过程。
编制数控加工程序是使用数控机床的一项重要技术工作,理想的数控程序不仅应该保证加工出符合零件图样要求的合格零件,还应该使数控机床的功能得到合理的应用与充分的发挥,使数控机床能安全、可靠、高效地工作。
一、数控程序编制的内容及步骤数控编程是指从零件图样到获得数控加工程序的全部工作过程,如图1所示。
二、编程方法数控加工程序的编制方法主要有两种:手工编制程序和自动编制程序。
1.手工编程手工编程指主要由人工来完成数控编程中各个阶段的工作,如图2所示。
一般对几何形状不太复杂的零件,所需的加工程序不长,计算比较简单,用手工编程比较合适。
手工编程的特点:耗费时间较长,容易出现错误,无法胜任复杂形状零件的编程。
据国外资料统计,当采用手工编程时,一段程序的编写时间与其在机床上运行加工的实际时间之比,平均约为30:1,而数控机床不能开动的原因中有20%~30%是由于加工程序编制困难,编程时间较长。
2.计算机自动编程自动编程是指在编程过程中,除了分析零件图样和制定工艺方案由人工进行外,其余工作均由计算机辅助完成。
采用计算机自动编程时,数学处理、编写程序、检验程序等工作是由计算机自动完成的,由于计算机可自动绘制出刀具中心运动轨迹,使编程人员可及时检查程序是否正确,需要时可及时修改,以获得正确的程序。
又由于计算机自动编程代替程序编制人员完成了繁琐的数值计算,可提高编程效率几十倍乃至上百倍,因此解决了手工编程无法解决的许多复杂零件的编程难题。
典型轴类零件数控加工工艺分析
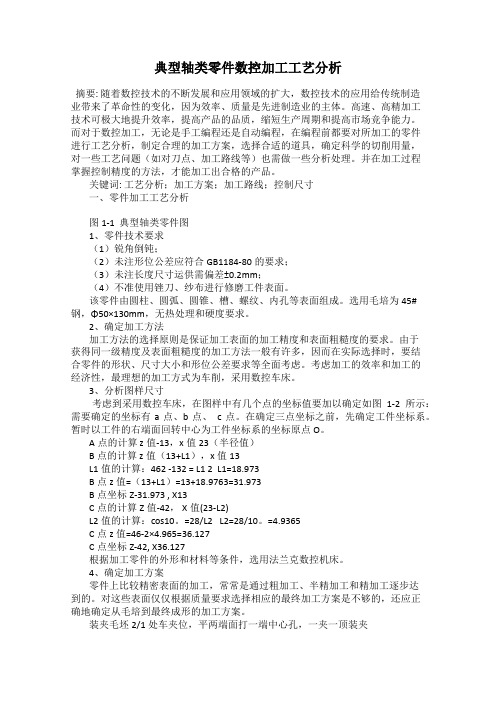
典型轴类零件数控加工工艺分析摘要: 随着数控技术的不断发展和应用领域的扩大,数控技术的应用给传统制造业带来了革命性的变化,因为效率、质量是先进制造业的主体。
高速、高精加工技术可极大地提升效率,提高产品的品质,缩短生产周期和提高市场竞争能力。
而对于数控加工,无论是手工编程还是自动编程,在编程前都要对所加工的零件进行工艺分析,制定合理的加工方案,选择合适的道具,确定科学的切削用量,对一些工艺问题(如对刀点、加工路线等)也需做一些分析处理。
并在加工过程掌握控制精度的方法,才能加工出合格的产品。
关键词: 工艺分析;加工方案;加工路线;控制尺寸一、零件加工工艺分析图1-1 典型轴类零件图1、零件技术要求(1)锐角倒钝;(2)未注形位公差应符合GB1184-80的要求;(3)未注长度尺寸运供需偏差±0.2mm;(4)不准使用锉刀、纱布进行修磨工件表面。
该零件由圆柱、圆弧、圆锥、槽、螺纹、内孔等表面组成。
选用毛培为45#钢,Φ50×130m m,无热处理和硬度要求。
2、确定加工方法加工方法的选择原则是保证加工表面的加工精度和表面粗糙度的要求。
由于获得同一级精度及表面粗糙度的加工方法一般有许多,因而在实际选择时,要结合零件的形状、尺寸大小和形位公差要求等全面考虑。
考虑加工的效率和加工的经济性,最理想的加工方式为车削,采用数控车床。
3、分析图样尺寸考虑到采用数控车床,在图样中有几个点的坐标值要加以确定如图1-2所示:需要确定的坐标有a点、b点、c点。
在确定三点坐标之前,先确定工件坐标系。
暂时以工件的右端面回转中心为工件坐标系的坐标原点O。
A点的计算 z值-13,x值23(半径值)B点的计算 z值(13+L1),x值13L1值的计算:462 -132 = L1 2 L1=18.973B点z值=(13+L1)=13+18.9763=31.973B点坐标Z-31.973 , X13C点的计算Z值-42, X值(23-L2)L2值的计算:cos10。
数控铣床典型零件加工实例图文稿
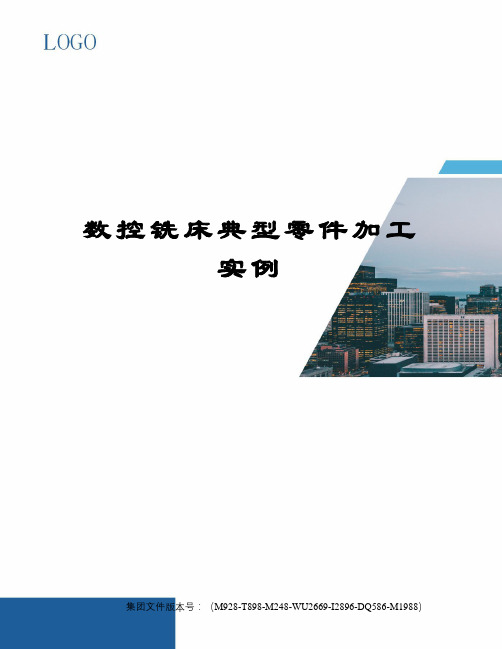
数控铣床典型零件加工实例集团文件版本号:(M928-T898-M248-WU2669-I2896-DQ586-M1988)模块五 数控铣床典型零件加工实例本单元从综合数控技术的实际应用出发,列举了典型数控铣削编程实例,如果希望掌握这门技术,就应该仔细的理解和消化它,相信有着举一反三的效果。
一、数控铣床加工实例1——槽类零件 毛坯为70㎜×70㎜×18㎜板材,六面已粗加工过,要求数控铣出如图2-179所示的槽,工件材料为45钢。
图2-179 凹槽工件1.根据图样要求、毛坯及前道工序加工情况,确定工艺方案及加工路线1)以已加工过的底面为定位基准,用通用机用平口虎钳夹紧工件前后两侧面,虎钳固定于铣床工作台上。
2)工步顺序① 铣刀先走两个圆轨迹,再用左刀具半径补偿加工50㎜×50㎜四角倒圆的正方形。
② 每次切深为2㎜,分二次加工完。
2.选择机床设备根据零件图样要求,选用经济型数控铣床即可达到要求。
3.选择刀具现采用φ10㎜的平底立铣刀,定义为T01,并把该刀具的直径输入刀具参数表中。
4.确定切削用量切削用量的具体数值应根据机床性能、相关的手册并结合实际经验确定,详见加工程序。
5.确定工件坐标系和对刀点在XOY 平面内确定以工件中心为工件原点,Z 方向以工件上表面为工件原点,建立工件坐标系,如图2-118所示。
采用手动对刀方法(操作与前面介绍的数控铣床对刀方法相同)把点O 作为对刀点。
学习目标知识目标: ●学会对工艺知识、编程知识、操作知识的综合运用 能力目标: ●能够对适合铣削的典型零件进行工艺分析、程序编制、实际加工。
6.编写程序考虑到加工图示的槽,深为4㎜,每次切深为2㎜,分二次加工完。
为编程方便,同时减少指令条数,可采用子程序。
该工件的加工程序如下:O0001; 主程序N0010 G90 G00 Z2. S800 T01 M03;N0020 X15.Y0 M08;N0030 G01 Z-2. F80;N0040 M98 P0010; 调一次子程序,槽深为2㎜N0050 G01 Z-4.F80;N0060 M98 P0010; 再调一次子程序,槽深为4mmN0070 G00 Z2.N0080 G00 X0 Y0 Z150. M09;N0090M02 主程序结束O0010 子程序N0010G03 X15. Y0 I-15.J0;N0020 G01 X20.;N0030 G03 X20. YO I-20. J0;N0040 G41 G01 X25. Y15.;左刀补铣四角倒圆的正方形N0050 G03 X15. Y25. I-10. J0;N0060G01 X-15.;N0070 G03 X-25. Y15. I0 J-10.;N0080G01 Y-15.N0090 G03 X-15. Y-25. I10. J0;N0100 G01 X15.;N0110 G03 X25. Y-15. I0 J10.;N0120 G01 Y0;N0130 G40 G01 X15. Y0; 左刀补取消N0140 M99; 子程序结束7.程序的输入(参见模块四具体操作步骤)8.试运行(参见模块四具体操作步骤)9.对刀(参见模块四具体操作步骤)10.加工选择“自动方式”,按“启动”开始加工。
数控车床典型零件加工实例
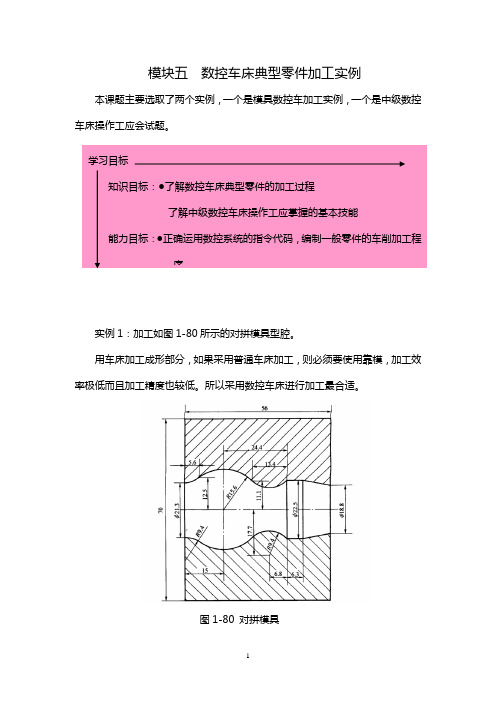
模块五数控车床典型零件加工实例本课题主要选取了两个实例,一个是模具数控车加工实例,一个是中级数控车床操作工应会试题。
学习目标知识目标:●了解数控车床典型零件的加工过程了解中级数控车床操作工应掌握的基本技能能力目标:●正确运用数控系统的指令代码,编制一般零件的车削加工程序。
实例1:加工如图1-80所示的对拼模具型腔。
用车床加工成形部分,如果采用普通车床加工,则必须要使用靠模,加工效率极低而且加工精度也较低。
所以采用数控车床进行加工最合适。
图1-80 对拼模具1.加工准备1)将两拼块分别加工成形。
2)在两拼块上装导钉,一端与下模板过渡配合,另一端与上模板间隙配合。
3)两拼块合装后外形尺寸磨正,对合平面磨平并保证两拼块厚度一致。
4)在花盘上搭角铁,将下模板固定在角铁上,拼合上模板并压紧,用千分表校正后固定角铁,安装示意图如图1-81所示。
图1-81 安装示意图2.所需刀具本工件需要通过钻孔、粗车、精车三个工步加工,钻孔时采用在尾架上装夹φ16mm的钻头手动进给,而粗车和精车则采用自动运行的办法。
粗车时用55°的内孔车刀,刀具号为T01,刀补号为01;精车时用35°的内孔车刀,刀具号为T02,刀补为02。
3.编写加工程序N10 M03 S500N20 T0101N30 G00 X0 Z3.0N40 G01 Z-30.0 F0.5N60 G01 Z-57.0N70 G00 X0N80 G00 Z-31.6N90 G01 X24.4 F0.2N100 G01 Z-50.4N110 G00 X0N120 Z3.0N130 G01 X18.3 Z3.0 F0.3N140 Z0N150 X22.0 Z-10.1N160 W-6.3N170 G02 X21.7 W-13.4 I6.45 J-6.8 N180 G03 X24.5 Z-50.4 I-11.1 J-11.0 N190 GO2 X20.8 Z-56.0 I7.55 J-5.6 N200 G01 X0N210 G00 Z200.0N220 G00 X200.0 T0100N230 T0202N240 G00 Z3.0N250 G01 X18.8 Z3.0 F0.3N260 Z0N280 W-6.3N290 G02 X22.2 W-13.4 I6.45 J-6.8N300 G03 X25.0 Z-50.4 I-11.1 J-11N310 G02 X21.3 Z-56.0 I7.55 J-5.6N320 G01 Z-58.0N330 G00 X0N340 G00 Z100.0N350 G00 X200.0 T0200N360 M05N370 M304.加工过程1)在尾架上装φ16mm的钻头,手动进给钻穿工件。
- 1、下载文档前请自行甄别文档内容的完整性,平台不提供额外的编辑、内容补充、找答案等附加服务。
- 2、"仅部分预览"的文档,不可在线预览部分如存在完整性等问题,可反馈申请退款(可完整预览的文档不适用该条件!)。
- 3、如文档侵犯您的权益,请联系客服反馈,我们会尽快为您处理(人工客服工作时间:9:00-18:30)。
说明:表格中刀尖半径和备注栏可以不要;25×25 指车刀刀柄的截面尺寸。
(5)切削用量选择
一般情况下,粗车:恒转速 n=800r/min 恒线速 v=100m/min
进给量 f=0.2mm/r 以下
vf=120m/min
背吃刀量 ap=2mm 以下
精车:恒转速 n=1100r/min 恒线速 v=150m/min
以零件右端面和中心轴作为 坐标原点建立工件坐标系。
根据零件尺寸精度及技术要 求,零件从右向左加工,将粗、 精加工分开来考虑。
加工工艺顺序为:车削右端面→复合型车削固定循环粗、精加工右端需要加工的所有轮 廓(粗车Φ44、Φ40.5、Φ34.5、Φ28.5、Φ22.5、Φ16.5 外圆柱面→粗车圆弧面 R14.25→ 精车外圆柱面Φ40.5→粗车外圆锥面→粗车外圆弧面 R4.75→精车圆弧面 R14→精车外圆锥 面→精车外圆柱面Φ40→精车外圆弧面 R5)。 (4)选择刀具
所选定刀具参数如表 1-2 所示。 说明:铣削内、外轮廓时,铣刀直径受槽宽限制,可选择φ6 的立铣刀;精铰的量通常 小于 0.2mm;刀刃和长度通常要比切削的深度大。 5.切削用量选择 一般情况下,粗铣:恒转速 n=600r/min
进给量 f=180mm/min 以下 背吃刀量 ap=5mm 以下 精车:恒转速 n=800r/min 进给量 f=120mm/min 以下
零件的底面和外部轮廓已经加工,本工序是在铣床上加工槽与孔。 1.零件图分析
凸轮内外轮廓由直线和圆弧组成。凸轮槽侧面和
20
0.021 0
、
12
0.018 0
两个内孔尺寸精
度要求较高,表面粗糙度要求也较高,Ra1.6;内孔
20
0.021 0
与底面有垂直度要求。
零件材料:HT200(切削性能较好) 毛坯尺寸:无(基本面已经加工) 2. 零件的装夹及夹具的选择
三、典型零件数控加工工艺分析实例
(一)数控车削加工典型零件工艺分析实例
1.编写如图所示零件的加工工艺。
(1)零件图分析 如图所示零件,由圆弧面、外圆锥面、球面构成。其中Φ50 外圆柱面直径处不加工,
而Φ40 外圆柱面直径处加工精度较高。 零件材料:45 钢 毛坯尺寸:Φ50×110
(2)零件的装夹及夹具的选择 采用机床三爪自动定心卡盘,零 件伸出三爪卡盘外 75mm 左右, 以外圆定位并夹紧。 (3)加工方案及加工顺序的确定
零件材料:HT200(切削性 能较好)
毛坯尺寸:170mm×110mm ×45mm (2)零件的装夹及夹具的选 择
用铣床虎钳夹毛坯两侧 面加工下表面;翻面后用下表 面定位铣床虎钳夹毛坯两侧 面,加工上表面、台阶面、钻 孔和镗孔;采用“一面两孔” 方式定位,即以底面和Φ40H7 和Φ13 两个孔为定位基准装夹,加工外轮廓。 (3)加工方案及加工顺序的确定
加工
20
0.021 0
、
12
0.018 0
两个孔时,以底面
A
定位,采用螺旋压板机构夹紧;加工凸
轮槽内外轮廓时,采用“一面两孔”方式定位,即以底面
A
和
20
0.021 0
、
12
0.018 0
两个孔
为定位基准装夹。 3. 加工方案及加工顺序的确定
以零件外轮廓的中心作为 X、Y 轴的坐标原点,以 A 平面为 Z 轴的零点建立工件坐标 系。
选择 1 号刀具为 90°硬质合金机夹偏刀,用于粗、精车削加工。 (5)切削用量选择
粗车主轴转速 n=630r/min,精车主轴转速 V=110m/min,进给速度粗车为 f=0.2mm/r, 精车为 f=0.07mm/r。
2.编写如图 1-26 所示的轴承套的加工工艺
(1)零件图分析 零件表面由内圆锥面,顺圆弧,逆圆弧和外螺纹等组成。有多个直径尺寸与轴向尺寸有
背吃刀量 ap=0.1mm 左右 注:材料为灰铸铁时切削材料要选择较小
粗精镗Φ40 内孔 650/1000
20
30 40 40/30
5
按余量 19
0.8/0.2
5 T05 Φ13 钻头
钻 2×Φ13 孔
500
30
6.5
6 T06 22×14 锪钻 2×Φ22 锪钻
350
25
4.5
Φ25 硬质合金
7 T07
铣削外轮廓
260
40
5
立铣刀
2.编写如图 1-29 所示平面槽形凸轮的加工工艺
根据零件尺寸精度及技术要求,确定基面先行(先孔后轮廓),先切削材料多的后切削 材料较少的面,先粗后精的原则。
加工工艺路线为:钻φ5 中心孔→钻φ19.6 孔→钻φ11.6 孔→铰φ20 孔→铰φ12 孔→ 重新装夹后粗铣槽的内轮廓→粗铣槽的外轮廓→精铣槽的内轮廓→精铣槽的外轮廓→翻面 装夹,铣φ20 孔 A 面侧的倒角。 4.选择刀具
刀具
序号
刀具规格名称
编号
加工表面
主轴转速 进给量 f 背吃刀量 备 S r/min mm/min ap mm 注
Φ125 硬质合金
1 T01铣削Βιβλιοθήκη 、下表面50端面铣刀
Φ63 硬质合金 铣削Φ60 外圆
2 T02
100
立铣刀
及其台阶面
3 T03 Φ38 钻头
钻Φ40 孔
200
4 T04 Φ40 镗孔刀
较高的尺寸精度和表面粗糙度要求(如果加工质量要求较高的表面不多可列出)。 零件材料:45 号钢 毛坯尺寸:φ80×112
(2)零件的装夹及夹具的选择 内孔加工时,以外圆定位,用三爪自动定心卡盘夹紧,需掉头装夹;加工外轮廓时,以
圆锥心轴定位,用三爪卡盘夹持心轴左端,右端利用中心孔顶紧。 (3)加工方案及加工顺序的确定
以零件Φ40 内孔的上端面为坐标原点建立工件坐标系。 加工顺序的确定按基面先行、先粗后精原则确定。 加工工艺顺序为:铣削下表面→翻面平装后铣削上表面→铣削Φ60 外圆及其台阶面→ 钻 3 个φ5 中心孔→钻φ38 内孔→粗、精镗φ40 内孔→钻 2×Φ13 孔→锪钻 2×Φ22 孔→ 铣削外轮廓。(走刀顺序见表所示)。 (4)选择刀具 Φ40H7 内孔采用钻-镗,阶梯孔Φ12 和Φ22 选择钻-锪,零件外轮廓、Φ60mm 外圆 及其台阶面采用立铣刀,上、下表面采用端铣刀加工,详见表格。 (5)切削用量选择 详见表格
以零件右端面中心作为坐标原点建立工件坐标系。 根据零件尺寸精度及技术要求,确定先内后外,先粗后精的原则。 加工工艺顺序为:车端面→钻φ5 中心孔→钻φ26 内孔→粗、精镗一端内孔→掉头装夹 后粗、精镗另一端内孔→粗车外轮廓→精车外轮廓→车螺纹(项目较多可用表格列出)。 (4)选择刀具
所选定刀具参数如表 1-2 所示。
进给量 f=0.07mm/r 以下
vf=150m/min
背吃刀量 ap=0.1mm 左右
(二)数控铣削加工典型零件工艺分析实例
1.编写如图所示零件的加工工艺。
(1)零件图的分析 如图所示,支承部分的外
轮廓由直线和圆弧组成,其它 主要是圆孔。其中内孔Φ40H7 有较高的尺寸加工精度和表 面粗糙度要求。