(仅供参考)扭杆悬架设计
悬架设计指南
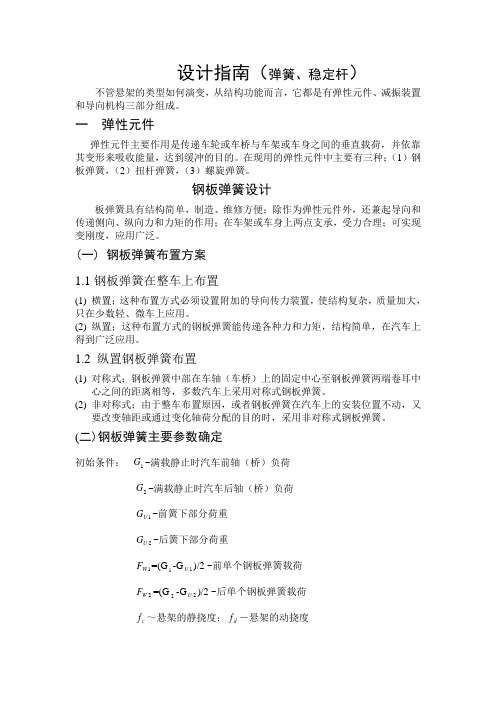
设计指南(弹簧、稳定杆)不管悬架的类型如何演变,从结构功能而言,它都是有弹性元件、减振装置和导向机构三部分组成。
一 弹性元件弹性元件主要作用是传递车轮或车桥与车架或车身之间的垂直载荷,并依靠其变形来吸收能量,达到缓冲的目的。
在现用的弹性元件中主要有三种;(1)钢板弹簧,(2)扭杆弹簧,(3)螺旋弹簧。
钢板弹簧设计板弹簧具有结构简单,制造、维修方便;除作为弹性元件外,还兼起导向和传递侧向、纵向力和力矩的作用;在车架或车身上两点支承,受力合理;可实现变刚度,应用广泛。
(一) 钢板弹簧布置方案1.1钢板弹簧在整车上布置(1) 横置;这种布置方式必须设置附加的导向传力装置,使结构复杂,质量加大,只在少数轻、微车上应用。
(2) 纵置;这种布置方式的钢板弹簧能传递各种力和力矩,结构简单,在汽车上得到广泛应用。
1.2 纵置钢板弹簧布置(1) 对称式;钢板弹簧中部在车轴(车桥)上的固定中心至钢板弹簧两端卷耳中心之间的距离相等,多数汽车上采用对称式钢板弹簧。
(2) 非对称式;由于整车布置原因,或者钢板弹簧在汽车上的安装位置不动,又要改变轴距或通过变化轴荷分配的目的时,采用非对称式钢板弹簧。
(二)钢板弹簧主要参数确定初始条件:1G ~满载静止时汽车前轴(桥)负荷2G ~满载静止时汽车后轴(桥)负荷1U G ~前簧下部分荷重2U G ~后簧下部分荷重1W F =(G 1-G 1U )/2 ~前单个钢板弹簧载荷2W F =(G 2-G 2U )/2 ~后单个钢板弹簧载荷c f ~悬架的静挠度;d f -悬架的动挠度1L ~汽车轴距;1、 满载弧高a f满载弧高指钢板弹簧装在车轴(车桥)上,汽车满载时钢板弹簧主片上表面与两端(不包括卷耳孔半径)连线间的最大高度差。
a f 用来保证汽车具有给定的高度。
当a f =0时,钢板弹簧在对称位置上工作。
为在车架高度已确定时得到足够的动挠度,常取a f = 10~20mm 。
2、 钢板弹簧长度L 的确定L —指弹簧伸直后两卷耳中心间的距离(1)钢板弹簧长度对整车影响当L 增加时:能显著降低弹簧应力,提高使用寿命;降低弹簧刚度,改善汽车平顺性;在垂直刚度C 给定的条件下,明显增加钢板弹簧纵向角刚度;减少车轮扭转力矩所引起的弹簧变形;原则上在总布置可能的条件下,尽可能将钢板弹簧取长些。
扭杆弹簧及扭杆弹簧悬架设计的新方法
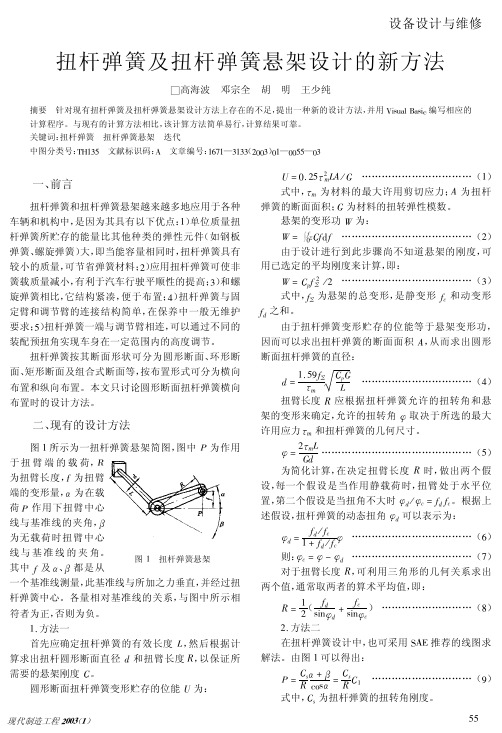
一、 前言
扭杆弹簧和扭杆弹簧悬架越来越多地应用于各种 车辆和机构中, 是因为其具有以下优点: 单位质量扭 +) 杆弹簧所贮存的能量比其他种类的弹性元件 (如钢板 弹簧、 螺旋弹簧) 大, 即当能容量相同时, 扭杆弹簧具有 较小的质量, 可节省弹簧材料; 应用扭杆弹簧可使非 1) 簧载质量减小, 有利于汽车行驶平顺性的提高; 和螺 ,) 扭杆弹簧与固 旋弹簧相比, 它结构紧凑, 便于布置; 3) 定臂和调节臂的连接结构简单, 在保养中一般无维护 要求; 扭杆弹簧一端与调节臂相连, 可以通过不同的 -) 装配预扭角实现车身在一定范围内的高度调节。 扭杆弹簧按其断面形状可分为圆形断面、 环形断 面、 矩形断面及组合式断面等, 按布置形式可分为横向 布置和纵向布置。本文只讨论圆形断面扭杆弹簧横向 布置时的设计方法。
$ !! $" ……………………………………(#") ( $ ) ()* ………………………(#,) !, ! ! " ! ( #$ %&’ ! $") ! 此处的 !, 与设计方法二中 !, 的物理意义相同。 根据设计方法二, 扭杆弹簧悬架在静载荷 $ 的作 用下, 任意一点的折算静变形 % 为: ( $ ) ()* ………………(#-) % ! #!, ! # ! " ! ( #$ %&’ ! $") ! 所以扭 又因为任意一点的折算静变形 % ! $ & ! , 杆弹簧悬架的扭转刚度 ! 为: ( $ $#$ %&’ ! $") ! …………………(#0) !! ! % # ( ()* ! $") ! 对于计算得出的扭杆弹簧悬架的扭转刚度 ! , 可
汽车双横臂扭杆弹簧独立悬架设计

汽车双横臂扭杆弹簧独立悬架设计悬挂系统在汽车中起到了关键的作用,它直接影响着汽车的操控性、行驶稳定性、乘坐舒适性等方面。
对于高性能车辆而言,悬挂系统的设计尤为重要。
双横臂扭杆弹簧独立悬架是一种高性能的悬挂系统,本文将对其进行详细的设计。
双横臂扭杆弹簧独立悬架是一种常见的汽车悬挂系统,其结构简单紧凑、重量轻、刚性优越、行驶稳定性好等特点使其成为高性能车辆中的首选。
该悬挂系统主要由两根横臂、一根扭杆和弹簧组成。
其中,横臂分别安装在车体和车轮悬架之间,扭杆则固定在两个横臂之间。
而弹簧则连接在横臂和车体之间,起到支撑和缓冲的作用。
在设计双横臂扭杆弹簧独立悬架时,需要考虑的因素包括悬挂系统的刚度、悬挂高度和行驶稳定性等。
首先,我们需要确定悬挂系统的刚度。
刚度对于悬挂系统来说非常重要,它直接影响着汽车的操控性和行驶稳定性。
刚度过高会降低乘坐舒适性,而刚度过低则会影响操控性能。
因此,我们需要根据车辆的使用环境、车型和车重等因素来确定悬挂系统的刚度。
其次,需要确定悬挂高度。
悬挂高度是指汽车底盘与地面的距离,它会影响到汽车的通过性、行驶平稳性和乘坐舒适性等方面。
在确定悬挂高度时,需要综合考虑不同因素的影响,如车身重心、悬挂系统刚度和弹簧等。
最后,需要考虑悬挂系统的行驶稳定性。
悬挂系统的行驶稳定性决定着汽车在高速行驶和急转弯等情况下的控制性能。
为了提高行驶稳定性,可以采用多种方式,如增加悬挂系统的刚度、调整悬挂系统的几何结构和采用电子控制悬挂系统等。
在进行双横臂扭杆弹簧独立悬架设计时,还需要对各组件的材料和结构进行选择。
材料的选择应考虑强度、刚度、重量等因素。
而结构的设计需要考虑各组件之间的连接方式、布局和受力情况等。
总之,汽车的悬挂系统是其性能表现和乘坐舒适性的重要因素之一、双横臂扭杆弹簧独立悬架作为一种高性能的悬挂系统,其设计需要综合考虑悬挂系统的刚度、悬挂高度和行驶稳定性等因素。
通过合理的选择和设计,可以使汽车的悬挂系统达到最佳的运行状态,提供出色的操控性、行驶稳定性和乘坐舒适性。
悬架构造实验报告(3篇)

第1篇一、实验目的1. 了解汽车悬架系统的基本组成和结构。
2. 掌握不同类型悬架系统的构造特点。
3. 分析悬架系统在汽车行驶中的作用。
二、实验原理汽车悬架系统是连接车架与车轮的部件,其主要功能是将路面传递给车轮的载荷和反作用力传递到车架上,以保证汽车的平稳行驶。
悬架系统由弹性元件、减振器和导向机构三部分组成。
三、实验内容1. 扭杆梁式悬架系统2. 麦弗逊式独立悬架系统3. 电子控制主动式油气弹簧悬架系统四、实验步骤1. 观察扭杆梁式悬架系统(1)观察悬架系统的整体结构,了解其组成。
(2)观察扭杆梁的形状和材料,了解其作用。
(3)观察减振器和弹簧的安装位置和结构,了解其作用。
2. 观察麦弗逊式独立悬架系统(1)观察悬架系统的整体结构,了解其组成。
(2)观察滑动立柱和横摆臂的形状和材料,了解其作用。
(3)观察减振器和弹簧的安装位置和结构,了解其作用。
3. 观察电子控制主动式油气弹簧悬架系统(1)观察悬架系统的整体结构,了解其组成。
(2)观察油气弹簧的结构和材料,了解其作用。
(3)观察传感器、电控单元和电磁阀的安装位置和作用。
五、实验结果与分析1. 扭杆梁式悬架系统扭杆梁式悬架系统通过扭杆梁来平衡左右车轮的上下跳动,以减小车辆的摇晃,保持车辆的平稳。
在实验中,我们观察到扭杆梁的形状和材料,以及减振器和弹簧的安装位置和结构,从而了解了扭杆梁式悬架系统的构造特点。
2. 麦弗逊式独立悬架系统麦弗逊式独立悬架系统由滑动立柱和横摆臂组成,具有较好的操控性和稳定性。
在实验中,我们观察到滑动立柱和横摆臂的形状和材料,以及减振器和弹簧的安装位置和结构,从而了解了麦弗逊式独立悬架系统的构造特点。
3. 电子控制主动式油气弹簧悬架系统电子控制主动式油气弹簧悬架系统由油气弹簧、传感器、电控单元和电磁阀等组成,可以实现悬架刚度和阻尼的调节。
在实验中,我们观察到油气弹簧的结构和材料,以及传感器、电控单元和电磁阀的安装位置和作用,从而了解了电子控制主动式油气弹簧悬架系统的构造特点。
(精选文档)汽车扭转梁悬架毕业设计[管理资料]
![(精选文档)汽车扭转梁悬架毕业设计[管理资料]](https://img.taocdn.com/s3/m/e683764fc77da26924c5b031.png)
第1章绪论悬架的重要性现代汽车除了保证其基本性能,即行驶性、转向性和制动性等之外,目前正致力于提高安全性与舒适性,向高附加价值、高性能和高质量的方向发展。
对此,尤其作为提高操纵稳定性、乘坐舒适性的轿车悬架必须进行相应的改进。
舒适性是汽车最重要的使用性能之一。
舒适性与车身的固有振动特性有关,而车身的固有振动特性又与悬架的特性相关。
图1-1为扭转梁后悬架示意图图1-1 扭转梁后悬架悬架的功能悬架的主要作用是传递作用在车轮和车身之间的一切力和力矩,比如支撑力、制动力和驱动力等,并且缓和由不平路面传给车身的冲击载荷、衰减由此引起的振动、保证乘员的舒适性、减小货物和车辆本身的动载荷。
其主要任务是传递作用在车轮和车架(或车身)之间的一切力和力矩;缓和路面传给车架(或车身)的冲击载荷,衰减由此引起的承载系统的振动,保证汽车的行驶平顺性;保证车轮在路面不平和载荷变化时有理想的运动特性,保证汽车的操纵稳定性,使汽车获得高速行驶能力。
汽车在不平路面上行驶时,由于悬架的弹性作用,使汽车产生垂直振动。
为了迅速衰减这种振动和抑制车身、车轮的共振,减小车轮的振幅,悬架应装有减振器,并使之具有合理的阻尼。
利用减振器的阻尼作用,使汽车振动的振幅连续减小,直至振动停止。
悬架的设计要求为了满足汽车具有良好的行驶平顺性,要求由簧上质量与弹性元件组成的振动系统的固有频率应在合适的频段,并尽可能低。
前、后悬架固有频率的匹配应合理,对乘用车,要求前悬架固有频率略低于后悬架的固有频率,还要尽量避免悬架撞击车架(或车身)。
在簧上质量变化的情况下,车身高度变化要小,因此,应采用非线性弹性特性悬架。
要正确地选择悬架方案和参数,在车轮上、下跳动时,使主销定位角变化不大、车轮运动与导向机构运动要协调,避免前轮摆振;汽车转向时,应使之稍有不足转向特性。
悬架与汽车的多种使用性能有关,为满足这些性能,对悬架提出的设计要求有:(1)保证汽车有良好的行驶平顺性。
扭杆设计(案例)

扭杆设计扭杆的设计是整个翻转机构中最重要的一项,设计时所需要的信息相对较多,还要涉及到一些计算。
下面举例说明其设计过程。
①确定扭杆的刚度:这是设计扭杆的第一步。
在这之前,必须知道以下两个方面的因素:A.车身的重量。
B.车身的重心相对于翻转点的位置。
现有一车身,重量m=420千克,车身未翻起时重心相对翻转点的坐标G(700,500),单位:毫米,拉手距离翻转点1.5m.根据以上信息可以确定车身重力相对翻转点所产生的力矩M随翻转角度的变化(0~36°)的特性表,如下表:m=420kg, G(700,500),为了直观表现翻转角与重力力矩的关系,可以绘制其关系曲线图,见图1,图1随着翻转角度的增加,重力矩反而减小,几乎是直线下降。
根据设计要求,线下降。
根据设计要求,扭杆刚度必须满足以下几个条件:A.扭杆力矩直线必须与重力矩变化曲线接近;B.两线必须相交,且在翻转角为16°~20°之间;C.当翻转角为0°时,≤25kg.f。
根据以上要求,可以直接在图1的基础上做出扭杆的力矩变人力作用F手化图,见图2:两条刚度参考线分别在翻转角为16°和20°时相交,起点在52°处,说明扭杆的工作角为52°。
为什么扭转角要选择52°?从图中很明显的看出,当选择其他角度时,直线斜率明显增大,当翻转角为0°时,扭杆产生力矩明显高出重力矩许多,不符合条件C。
参考线1的斜率为63.9,图2当翻转角度为0°,扭杆产生力矩为3323牛.米,根据要求C 得:3323-2940≤250×1.5,该不等式不成立。
参考线2斜率为62.4,满足要求C 。
根据上述计算,取中间值,扭杆刚度K=63牛.米/度,扭转角52°。
验算:当翻转角为0°时:F 手=(52×63-2940)÷1.5=22.4kg.f<25kg.f 满足要求A 、B 、C 。
汽车双横臂扭杆弹簧独立悬架设计

汽车双横臂扭杆弹簧独立悬架设计崔敏【摘要】This paper is mainly to analysis a light truck’s computing method of the front independent suspension design and testing of design experiment. Firstly, it goes with the stress analysis and the trajectory calculation of the double wishbone independent suspension, and then continues with the suspension design calculation such as the design of torsion bar spring , front suspension’s stiffness, offset frequency calculation, stabilizer bar’s design, roll stiffness calculation, shockabs orber’s design, and finally the suspension offset frequency and riding comfort can be verified through the test.%文章主要研究某轻型载货汽车前独立悬架的设计计算方法以及独立悬架的设计试验验证,首先对双横臂式独立悬架进行受力分析、运动轨迹计算,然后对悬架进行设计计算如扭杆弹簧的设计、前悬架的刚度、偏频计算、稳定杆的设计、侧倾刚度计算、减震器的设计,最后通过试验验证悬架的偏频、平顺性。
【期刊名称】《汽车实用技术》【年(卷),期】2016(000)006【总页数】4页(P11-14)【关键词】轻型载货汽车;双横臂式独立悬架;平顺性【作者】崔敏【作者单位】安徽江淮汽车股份有限公司技术中心,安徽合肥 230601【正文语种】中文【中图分类】U463.33+210.16638 /ki.1671-7988.2016.06.005CLC NO.: U463.33+2 Document Code: A Article ID: 1671-7988 (2016)06-11-04悬架是现代汽车上的一个重要总成,他把车架与车轴弹性地连接起来。
悬架设计

悬架设计手册二.扭杆悬架扭杆式双横臂独立悬架,用扭杆作为弹性元件,简称为扭杆悬架。
2.1 扭杆悬架的典型结构2.1.1悬架的导向机构悬架的导向机构是一种四连杆机构,四连杆机构由上摆臂、下摆臂及主销构成。
图2-1为悬架系统结构简图,三角型DEF为悬架上摆臂,DE为上摆臂轴;三角型ABC为悬架下摆臂,AB为下摆臂轴;F为上球头销、C为下球头销FC构成转向桥的主销车轮跳动过程中,上摆臂、下摆臂各自绕它们的摆臂轴进行摆动。
M、N分别为转向梯型上的两点,M为转向梯型断开点,N为转向节臂与转向拉杆的连接点。
图2-1摆臂结构有两种:A形臂和一字臂,呈A字形或三角形的摆臂为A形臂;呈一字形的摆臂为一字臂。
上摆臂一般都是A形臂。
上下摆臂均为A形臂的称为双A形臂结构,四驱的车辆或四驱平台上的两驱车辆一般采用双A形臂,如:长丰猎豹、BJ2027皮卡;一般SUV车因考虑越野性能,其前悬架大多采用双A形臂,如:长城赛弗、五十铃竞技者、海拉克斯、华泰特拉卡等。
采用双A形臂的车辆不带推力杆。
另一种布置结构为:上摆臂是A形臂,下摆臂为一字臂。
两驱车辆一般采用该种结构。
如BJ1027皮卡、长城皮卡、田野皮卡等。
该种结构因下摆臂为一字臂必须设置推力杆。
2.1.2 上置扭杆与下置扭杆扭杆的安装型式主要有两种,一种为上置扭杆,一种为下置扭杆,见图2-2。
扭杆的上置与下置主要与整车及发动机布置有关,主要看它的布置空间。
采用上置扭杆的有:BJ6486轻客、长城赛弗、金杯海狮等;采用下置扭杆的有:BJ1027皮卡、长城皮卡、江铃皮卡、庆铃皮卡等。
图2-22.。
1。
3 双横臂轴的布置为了获得优良的性能,双横臂轴线在纵平面内和水平面内都有可能布置夹角,双横臂轴线在纵平面内形成的夹角为刹车点头角,在水平面内形成的夹角为斜置角。
图2-3列出了BJ1032、BJ0127、BJ6486的双横臂轴线的布置及其特点:图2-3图中M-M为上摆臂轴线,N-N为下摆臂轴线。
- 1、下载文档前请自行甄别文档内容的完整性,平台不提供额外的编辑、内容补充、找答案等附加服务。
- 2、"仅部分预览"的文档,不可在线预览部分如存在完整性等问题,可反馈申请退款(可完整预览的文档不适用该条件!)。
- 3、如文档侵犯您的权益,请联系客服反馈,我们会尽快为您处理(人工客服工作时间:9:00-18:30)。
4.3扭杆悬架设计作为悬架弹性元件的一种——扭杆弹簧的两端分别与车架(车身)和导向臂连接。
工作时扭杆弹簧受扭转力矩作用。
扭杆弹簧在汽车上可以纵置、横置或介于上述两者之间。
因扭杆弹簧单位质量储能量比钢板弹簧大许多,所以扭杆弹簧悬架质量小(簧下质量得以减少),目前在轻型客车、货车上得到比较广泛的应用。
除此之外,扭杆弹簧还有工作可靠、保养维修容易等优点。
扭杆弹簧可以按照断面形状或弹性元件数量的不同来分类。
按照断面形状不同,扭杆弹簧分为圆形、管形、片形等几种。
按照弹性元件数量不同,扭杆可分为单杆式(图4—12a、b)或组合式两种。
组合式扭杆又有并联(图4—12c、d)和串联(图4—12e)两种。
端部做成花键的圆形断面扭杆,因工艺性良好和装配容易而得到广泛应用,与管形扭杆比较材料利用不够合理是它的缺点。
管形断面扭杆有制造工艺比较复杂的缺点,但它也有材料利用合理和能够用来制作组合式扭杆的优点。
片形断面扭杆在一片断了以后仍能工作,所以工作可靠性好,除此之外还有工艺性良好、弹性好、扭角大等优点。
片形断面扭杆的材料利用不够合理。
组合式扭杆能缩短弹性元件的长度,有利于在汽车上布置。
采用圆断面组合式扭杆时,可以用2、4或6根组合形成的组合式扭杆。
图4—12 扭杆断面形状及端部结构a)圆形断面扭杆,端部为花键 b)圆形断面扭杆,端部为六角形c)片形组合式扭杆d)圆形组合式扭杆e)串联组合式扭杆下面以汽车上常用的圆形断面扭杆为例,介绍扭杆弹簧的设计要点。
设计前应当根据对汽车平顺性的要求,先行选定悬架的刚度c。
设计扭杆弹簧需要确定的主要尺寸有扭杆直径d和扭杆长度L(图4—13)。
图4-13扭杆弹簧与臂设计时应当根据最大扭矩计算扭杆直径d 3max16πτM d = (4—21)式中,为扭杆承受的最大扭矩;max M τ为扭转切应力,可取允许扭转切应力代人计算。
扭杆的有效长度L 用下式计算 nc Gd L 324π=(4—22)式中,G 为切变模量,设计时取G=MPa ;为扭杆的扭转刚度。
4107.7×n c 分析式(6—22)可知:扭杆直径d 和有效长度L 对扭杆的扭转刚度有影响。
增加扭杆直径d 会使扭杆的扭转刚度增大,因悬架刚度与扭杆扭转刚度成正比,所以汽车平顺性变坏;而扭杆直径d 又必须满足式(6—21)的强度要求,不能随意减小。
增加扭杆有效长度L 能减小扭杆的扭转刚度,使汽车平顺性获得改善,但过长的扭杆在汽车上布置有困难,此时宜采用组合式扭杆。
n c n c n c 常采用45CrNiMoV A 、40Ct 、42CrMo 、50CRV 等弹簧钢制造扭杆。
为了提高疲劳强度,扭杆需要经过预扭和喷丸处理。
经过预扭和喷丸处理的扭杆许用切应力[]τ可在800~900MPa 范围内选取,轿车可取上限,货车宜取下限。
扭杆弹簧可分为端部、杆部和过渡段三部分。
圆形扭杆使用有花键的端部占多数,这种结构在端部直径较小时也能保证足够的强度。
为使端部和杆部寿命一样,推荐端部直径D=(1.2~1.3)d ,其中d 为扭杆直径;花键长度D l 4.0=,端部花键一般采用渐开线花键。
从端部直径到杆部直径之间的一段称为过渡段。
为了使这段应力集中降到最小,过渡段的尺寸应该是逐渐变化的。
比较常用的方法是采用一个30°夹角的锥体,把端部和杆部连接起来(图4—14a),过渡段长,过渡圆角ο15tan 2/)(d D L g −=d r 5.1=。
过渡段可以分为靠近直径为D 的花键端部的非有效部分和靠近直径为d 的杆部的有效部分,即这一部分可以看作是扭杆工作长度的一部分,称为有效长度。
对于如图4—14a 所示结构,有效长度,可用下式计算e L e L ⎥⎥⎦⎤⎢⎢⎣⎡⎟⎠⎞⎜⎝⎛+⎟⎠⎞⎜⎝⎛+=323D d D d D d L L g e (4—23)图4—14 扭杆端部、杆部与过渡段a)锥度过渡段 b)圆弧过渡段对于如图4—14b 所示结构,有效长度可用下式计算e L ⎥⎥⎦⎤⎢⎢⎣⎡⎟⎠⎞⎜⎝⎛−⎟⎠⎞⎜⎝⎛−++⎟⎠⎞⎜⎝⎛+⎟⎠⎞⎜⎝⎛=5.05.0231arctan 151510848d D d D d D d D d D d L L g e (4—24) 过渡段圆弧半径R 为42dD dD L R g −+−=(4—25) 扭杆的工作长度L 等于杆身长再加上有效长度的两倍,即0L e Le L L L 20+= 与扭杆花键连接的支座上的内花键长度要求比扭杆上的外花键长度长些,并且设计时还应保证内花键的两端长度都要超出扭杆花键长度。
有的扭杆端部采用直接锻造出六角形的结构。
为了提高侧边的平直度,锻后再进行精压加工。
六角对边的宽度B 与扭杆直径d 之间要求保持B =(1.2~1.4)d 的关系,以保证六角形的端部有足够的强度。
4.4螺旋弹簧悬架设计螺旋弹簧作为弹性元件,由于其结构简单、制造方便及有高的比能容量,因此在现代轻型以下汽车的悬架中应用相当普遍,特别是在轿车中,由于要求良好的乘坐舒适性和悬架导向机构在大摆动量下仍具有保持车轮定位角的能力,因此螺旋弹簧悬架早就取代了钢板弹簧。
螺旋弹簧在悬架布置中可在弹簧内部安装减振器、行程限位器或导向柱使结构紧凑。
通过采用变节距的或用变直径弹簧钢丝绕制的或两者同时采用的弹簧结构,可以实现变刚度特性。
1.螺旋弹簧的刚度及应力计算螺旋弹簧在其轴向载荷作用下的变形为P f 428GdiPD f m ⋅= (4-26) 式中——弹簧中径,mm ; m D d ——弹簧钢丝直径,mm ; i ——弹簧工作圈数;G ——弹簧材料的剪切弹性模量,取MPa 。
4103.8×因此弹簧刚度iD Gd f P C m s ⋅==348 (4-27) 弹簧在压缩时其工作方式与扭杆类似,都是靠材料的剪切变形吸收能量,弹簧钢丝表面的剪应力为2'3'88dPCK d K PD m ππτ== Mpa (4-28) 式中C ——弹簧指数(旋绕比),d D C m /=;'K ——曲度系数,为考虑簧圈曲率对强度影响的系数,C C C K 615.04414'+−−=。
(4-29)对于前面讨论的直的扭杆,其表面的剪应力呈均匀分布,而螺旋弹簧钢丝表面的剪应力则相对复杂。
在静载状态下,这种截面内的应力分布不均匀可以忽略不计,但在承受动载时,由于弹簧内侧应力水平较高并且应力变化幅值也更大,导致螺旋弹簧的失效总是发生在内侧。
为了在设计时考虑内侧应力的增大,引入修正系数'K 。
一般情况下,弹簧钢的许用剪应力[]τ与许用拉应力[]σ成比例关系,通常情况下,可以取[]τ=0.63[]σ。
2.弹簧端部形状螺旋弹簧端部可以碾细、并紧,直角切断或向内弯曲,典型结构如图4—15所示。
其中(a)为两端碾细,亦即在绕制弹簧之前先将钢丝两端碾细,碾细部分长度在绕后约占240°,末端厚度为钢丝直径的1/3左右,绕成后末端几乎贴紧相邻一圈弹簧。
必要时,两端都要磨平。
这种结构的优点是节约材料,占用垂向空间小,特别是由于两端都平整,安装时可以任意转动,因而设计时弹簧的圈数可以取任意值,不必限于整数。
其缺点是碾细需要专门工序和设备,增加了制造成本。
(b)为直角切断型,其中一端并紧形成与弹簧轴线垂直的平面。
这种结构的优点在于绕制简单,成本低,其缺点是增大了垂向尺寸和材料消耗,安装时需要一定方向并且需与之相配套的弹簧座,若两端都未整平,则修改设计时,弹簧圈数必须按整数增减。
(c)为端部向内弯曲并形成与弹簧轴线垂直的平面,这种结构常用于和弹簧座配合起定位作用,若两端都内弯,则需要专用设备。
图4-15螺旋弹簧的端部结构表4—1列出了不同端部结构时弹簧总圈数与有效圈数i 以及弹簧完全并紧时的高度间的关系,其中公式中的系数1.01为考虑螺旋角的补偿系数,t 为端部碾细时的末端厚度。
n s H s H 表4-1螺旋弹簧不同端部结构时的总圈数及并紧高度n s H 总圈数n 完全并紧时的高度s H 两端碾细 i +2 t n d 2)1(01.1+− 两端切断 i +1.33)1(01.1+n d 两端内弯 i +1.50 )25.1(01.1−n d一端碾细一端切断i +1.67t dn +01.1一端碾细一端内弯 i +1.75 t n d +−)1(01.1一端切断一端内弯i +1.42dn 01.3.螺旋弹簧的设计计算螺旋弹簧的设计计算分以下几步:(1)根据总布置要求及悬架的具体结构型式求出需要的弹簧刚度,设计载荷时弹的受力,及弹簧高度,悬架在压缩行程极限位置时弹簧高度。
s C i P i H m H (2)初步选择弹簧中径D 。
,端部结构型式及所用的材料。
(3)参考相关标准确定台架试验时伸张及压缩极限位置相对于设计载荷位置的弹簧变形量,,并确定要想达到的寿命 (循环次数)。
1f 2f c n (4)初选钢丝直径d ,并由相关材料标准查出许用拉应力[]σ。
(5)由式(4-27)解出i ,用表4—1中的相应公式求出。
s H (6)由,,及可求出弹簧在完全压紧时的载荷,台架试验伸张、压缩极限位置对应的载荷,,以及工作压缩极限位置的载荷分别为s H i P i H s C s P 1P 2P m P )(s i s i s H H C P P ++= (4-30) 11f C P P s i −= (4-31) 22f C P P s i += (4-32) )(m i s i m H H C p P −+= (4-33)(7)按弹簧指数及d D C m /='K 的表达式(见式(4-29)下的说明)求得'K ,运用式(4—28)求出载荷,,以及所对应的剪切应力1P 2P s P m P 1τ,2τ,s τ以及max τ (计算出的s τ>max τ,但max τ是悬架工作时弹簧实际对应的最大剪应力,对应悬架的极限压缩状态)。
(8)校核max τ是否小于[]τ=0.63[]σ,若不成立,则返回第(4)步重新选择钢丝直径d ;若余量很大,则视第(9)步寿命校核结果决定是否重新选取较小些的直径d 。
(9)校核台架试验条件下的寿命。
给定试验条件下的循环次数n ,可按下式估算:13.01808.1⎟⎟⎠⎞⎜⎜⎝⎛=e c K n (4-35)式中[])(48.1)(74.01212ττσττ+−−=e K若算出的小于预期的台架寿命,则返回第(4)步重新选择d ;若有较大余量,则与第(8)步的结果综合考虑是否选择更小的钢丝直径以节约材料,减小质量。
c n (10)得到合适的d 以后,可以进一步确定弹簧的自由高度和最小工作高度:0H n H s i i C P H H /0+= (4-36) di H H s n δ+= (4-37)式中δ——与弹簧指数有关的系数。