扭振的测量
实船轴系扭振测量
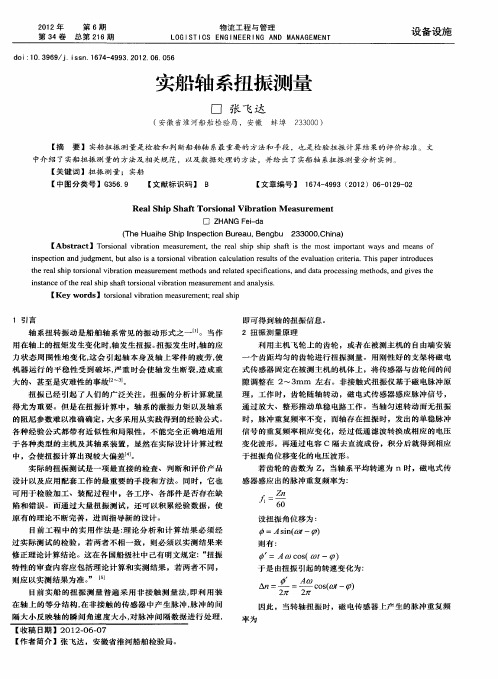
1 引 言
即可得到轴的扭振信息 。
2 扭 振 测 量 原 理
轴 系 扭 转 振 动 是 船 舶 轴 系 常 见 的 振 动 形 式 之 一 [。 当作 1 】 用 在 轴 上 的扭 矩 发 生 变 化 时 , 发 生 扭 振 。 振 发 生 时 , 的应 轴 扭 轴
利 用 主 机 飞 轮 上 的齿 轮 ,或 者在 被 测 主 机 的 自由端 安 装
is e t n a d u g n , u l rin l irt n c l l inrs l f h v lainci r . h s a e t d c s n p c o n d me tb t s i at s a vb ai a ua o ut o ee a t r ei T i p p r nr u e i j a os o o o c t e s t u o t a i o
于 扭振角位移变化的电压波形。
于 各 种 类 型 的 主 机 及 其 轴 系 装 置 ,显 然 在 实 际 设 计 计 算 过 程 中 ,会 使 扭 振 计 算 出 现 较 大 偏 差 H。 】 实 际 的扭 振 测 试 是 一 项 最直 接 的 检 查 、判 断 和 评 价 产 品 设 计 以及 应 用 配 套 工 作 的最 重 要 的手 段 和 方法 。 同 时 ,它 也 可 用 于 检 验 加 工 、 装 配 过 程 中 ,各 工 序 、 各 部 件 是 否 存 在 缺
21 0 2年 第 6期 第3 4卷 总 第 2 6期 1
物 流 工 程 与 管理
LOG J STI ENGl CS NEERl AND NG MANAGEMENT
设 备设 施
d : 0 3 6 /j s11 7 — 9 3 2 2 0 . 5 oi 1 . 9 9 .i r 6 4 4 9 . 01 . 6 0 6 s .
船用柴油机轴系扭转振动测量方法

中华人民共和国国家标准UDC 621.431.713.6船用柴油机轴系扭转振动测量方法GB 6299-86The measuring method for torsional vibrationin shaft system of marine diesel engine标准适用于船用柴油机轴系的扭振测量。
其他动力的船舶轴系的扭振测量亦可参照使用。
注:轴系包括与扭振计算有关的动力机、传动元件和受功构件。
1 量标以柴油机曲轴回转中心线为参考,第一曲拐(从自由端数起)上死点为基准,取被测点在定转速各谐次的角位移振幅为量标,以(°)或rad为计量单位。
2 测量仪器2.1 总的要求2.1.1 测量仪器系统必须经过校验,能够获得被测轴系扭振响应正确信息的记录,同时还要获取测点的转速信息。
2.1.2 测量频率范围一般为1~600Hz。
如所选测量仪器的频率范围不足,则必须满足测量信号中主谐次(即柴油机各单位曲柄相对振幅矢量同向时的谐次)或副谐次的频率要求,其频率响应平直部分的允许误差为上10%。
如果测量仪器低频响应不足,其特性确定,则可以使用,但必须对扭振测量值进行修正。
2.1.3 测量仪器应按规定在国家主管机关认可的单位进行校验,并具有校验证书。
2.2 机械式扭振仪2.2.1 正确选择仪器的安装位置,并保批安装精度。
2.2.2 合理选择或调整有关的仪器工作参数如:传动比、弹簧常数、皮带长度和松紧(如用皮带传动时)、划笔放大比和阻尼等。
2.3 电测扭振仪2.3.1 仪器组成测量仪器系统一般由传感器、放大器、记录器及监测指示装置等组成。
在能满足2.1.1款要求的条件下,允许改变其组成。
2.3.2 传感器传感器与被测点之间的联系装置应尽量减小尺寸,并保证其制造和安装精度,以减少非扭振信号对测量精度的影响。
选用的传感器,在规定的工作环境(如温度、湿度、磁场、油污等)下,应能可靠地工作。
传感器经受非正常状况(如冲击、过热、浸油、浸水等)后,应及时校验。
船舶轴系扭振计算与测量分析简介

船舶轴系扭振计算与测量分析简介高莹莹(青岛齐耀瓦锡兰菱重麟山船用柴油机有限公司技术部)摘要:随着现代船舶计算的发展,船舶轴系扭转振动成为船舶动力装置安全运行的重要因素之一,各船级社规范也对船舶轴系扭振提出了计算和实测的要求,本文结合实例对船轴系用霍尔茨法进行自由振动计算和采用能量法进行共振计算进行了简单介绍,结合实船的扭振测量的结果和理论计算结果进行对比分析.结果表明,采用精确的原始轴系数据和柴油机参数,使得扭振计算的理论结果和实测结果非常吻合,本船的理论计算值符合实船状况,转速禁区设定正确.关键词:当量系统霍尔茨法能量法测量修正随着船舶工业的发展,造船数量和吨位不断增大,造船行业对造船技术的工艺和质量要求越来越高。
高质量、高效率的生产设计离不开现代化的技术支持。
然而船舶柴油机轴系的扭转振动是影响船舶动力装置安全运行的重要动力特性之一。
轴系振动计算不但对深入研究船舶推进轴系的可靠性、安全性、用于动力装置故障诊断等具有重要意义,而且是船舶推进轴系设计、制造、安装和检验比不可少的环节之一,为推进装置可靠安全运行提供了有力保障。
基于此,本文结合一30万吨VLCC船舶的轴系实例对船舶柴油机扭振计算和测量分析做了简要的概述。
1,当量系统的转化根据有关轴系振动理论,船舶柴油机及推进轴系实际就是一个多质量有阻尼强迫振动系统。
实际计算分析中,可以将其转化成为若干用无惯量的轴连接起来的集中质量系统,称之为当量扭振系统。
为了使转化后的当量扭振系统能代表实际的轴系的扭振特性,一般要求:当量扭振系统的固有频率应与实际系统的固有频率基本相等;其振型与实际的振型相似。
如下图Fig.1为一30万吨VLCC油轮轴系的当量扭振系统模型。
该船安装的是瓦锡兰7RT-flex82T电喷柴油机,主机的额定功率31640Kw,额定转速80rpm。
中间轴长9927mm,直径700mm,抗拉强度为590N/mm2;螺旋桨轴长10233mm,艉轴承处直径850mm,抗拉强度为590N/mm2。
扭振检测:柴油发电机组扭振特性的验证-最新年文档

扭振检测:柴油发电机组扭振特性的验证1 扭振现象产生机理与检测原理本次测试的试验对象为CAT3516型柴油机,属于往复式柴油机。
往复式柴油机在工作时,旋转的曲轴在燃气压力的不断作用下,产生了平均力矩和交变力矩分量,两者同时作用下会引起扭振现象。
当曲轴不同部位的转速增量有幅值和相位的相对变化时,轴上某一位置的平均转速会产生上下波动,此时即可证明扭振现象已经发生。
当激励频率接近于扭振谐振频率时,旋转件内应力迅速增加,易诱发严重的车辆结构耐久性问题,同时引起振动、噪声的大幅上升。
本次检测的采集信号来自自制辅助工装配合非接触式传感器检测到的曲轴角速度相位差。
该信号经传感器内的前置放大――单稳电路――低通滤波――积分放大处理后,向傅里叶分析记录仪输出信号,通过FFT快速傅里叶频谱分析后,输出分析数据。
通过对数据分析与比对,完成对柴油发电机组的扭振测试。
2 扭振检测标准的确定2.1 试验依据JB/T 9759-2011 内燃发电机组轴系扭转振动的限值及测量方法GB/T 6072.5-2003 往复式内燃机-- 性能第5 部分:扭转振动GB/T 15371-2008 曲轴轴系扭转振动的测量与评定方法2.2 试验标准通过对CAT3516B型柴油发电机组自身的数据要求,结合现存标准,确定了试验标准,测量的曲轴自由端扭振最大分谐波振幅不超过以下极限值:0.5 〜1.0 order 土 Idegree1.5 order ±0.25degree>1.5 order 土0.15degree3 扭振检测应用环境、检测系统、检测工装3.1 应用环境柴油机基本参数:①柴油机型号:3516B HD型;②柴油机参数:标定功率2240kW标定转速1800r/min ;怠速:600r/min ;③结构特征:16缸、V型、四冲程、增压、直喷式、涡轮增压、电喷;3.2 试验条件①所有试验设备,试验前经试运行一切正常并都在有效期内。
扭振测量方法

扭振测量方法
1.使用专业的扭振仪器进行测量。
扭振仪器通常包括传感器、放大器和数据记录器,可以测量物体的扭转变形和震动。
2.进行适当的预处理和滤波。
在进行扭振测量之前,需要对数据进行适当的预处理和滤波,以消除噪声和干扰,确保数据的准确性和可靠性。
3.选择合适的测量位置和方法。
在进行扭振测量时,需要选择合适的测量位置和方法,以确保所得到的数据能够真实反映物体的扭转变形和震动。
4.分析和评估测量数据。
在完成扭振测量之后,需要对所得到的数据进行分析和评估,以确定物体的稳定性和可靠性,并采取相应的措施进行改进和优化。
总之,扭振测量方法是一种非常重要的技术,对于评估和改进机械、电子设备和结构具有重要的意义。
- 1 -。
扭矩的测量方法
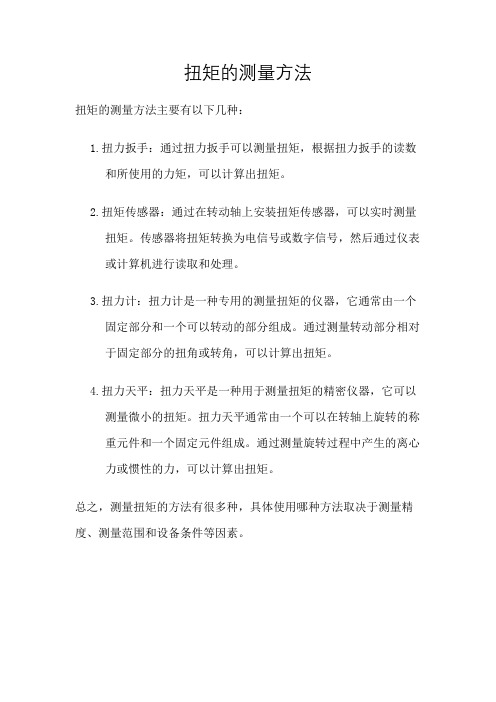
扭矩的测量方法
扭矩的测量方法主要有以下几种:
1.扭力扳手:通过扭力扳手可以测量扭矩,根据扭力扳手的读数
和所使用的力矩,可以计算出扭矩。
2.扭矩传感器:通过在转动轴上安装扭矩传感器,可以实时测量
扭矩。
传感器将扭矩转换为电信号或数字信号,然后通过仪表或计算机进行读取和处理。
3.扭力计:扭力计是一种专用的测量扭矩的仪器,它通常由一个
固定部分和一个可以转动的部分组成。
通过测量转动部分相对于固定部分的扭角或转角,可以计算出扭矩。
4.扭力天平:扭力天平是一种用于测量扭矩的精密仪器,它可以
测量微小的扭矩。
扭力天平通常由一个可以在转轴上旋转的称重元件和一个固定元件组成。
通过测量旋转过程中产生的离心力或惯性的力,可以计算出扭矩。
总之,测量扭矩的方法有很多种,具体使用哪种方法取决于测量精度、测量范围和设备条件等因素。
转轴扭振测量基本原理.
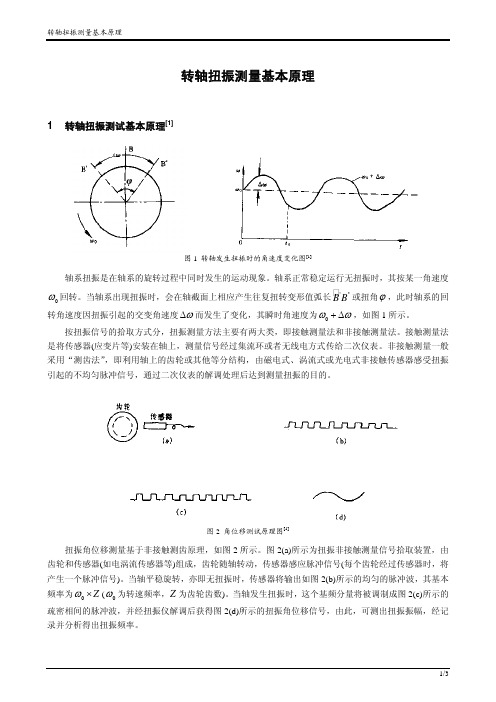
转轴扭振测量基本原理1 转轴扭振测试基本原理[1]图1 转轴发生扭振时的角速度变化图[1]轴系扭振是在轴系的旋转过程中同时发生的运动现象。
轴系正常稳定运行无扭振时,其按某一角速度0ω回转。
当轴系出现扭振时,会在轴截面上相应产生往复扭转变形值弧长 '''BB 或扭角ϕ,此时轴系的回转角速度因扭振引起的交变角速度ωΔ而发生了变化,其瞬时角速度为0ωω+Δ,如图1所示。
按扭振信号的拾取方式分,扭振测量方法主要有两大类,即接触测量法和非接触测量法。
接触测量法是将传感器(应变片等)安装在轴上,测量信号经过集流环或者无线电方式传给二次仪表。
非接触测量一般采用“测齿法”,即利用轴上的齿轮或其他等分结构,由磁电式、涡流式或光电式非接触传感器感受扭振引起的不均匀脉冲信号,通过二次仪表的解调处理后达到测量扭振的目的。
图2 角位移测试原理图[1]扭振角位移测量基于非接触测齿原理,如图2所示。
图2(a)所示为扭振非接触测量信号拾取装置,由齿轮和传感器(如电涡流传感器等)组成,齿轮随轴转动,传感器感应脉冲信号(每个齿轮经过传感器时,将产生一个脉冲信号)。
当轴平稳旋转,亦即无扭振时,传感器将输出如图2(b)所示的均匀的脉冲波,其基本频率为0Z ω×(0ω为转速频率,Z 为齿轮齿数)。
当轴发生扭振时,这个基频分量将被调制成图2(c)所示的疏密相间的脉冲波,并经扭振仪解调后获得图2(d)所示的扭振角位移信号,由此,可测出扭振振幅,经记录并分析得出扭振频率。
2 消除转轴弯曲振动影响的措施[1]图3 消除弯曲振动双接头180度布置图[1]对于小扭幅的扭振信号,为消除转轴弯曲振动的影响,每个测点应装设二只相对180度的传感器如图3所示,由质量不平衡等引起弯曲振动可分解成垂直和水平两方向。
水平方向的弯曲振动对传感器的调制信号无影响,而垂直方向的弯曲振动则会使靠近传感器的齿轮瞬时线速度叠加上一个由该振动形成的附加分量,影响传感器的调频信号。
曲轴扭振测试方法

曲轴扭振测试方法
曲轴扭振测试方法通常选用频响函数法。
频响函数法是利用频响函数测试扭振的方法,主要通过测量曲轴扭转减振器的频响函数来获取扭振频率。
在测试过程中,通常会沿X方向对系统进行锤击,给系统切向激励,以模拟实际工作状态。
同时,测试之前需要先将曲轴扭转减振器加热到指定温度,然后利用保温装置进行保温,并利用非接触式温度测量装置测量系统温度,以保证测试结果的准确性。
另外,由于橡胶在100℃时会有高温失效的倾向,而实际工作温度通常低于100℃,因此通常仅对20、40、60、80℃这四个温度下的曲轴扭转减振器扭振频率进行测试。
以上信息仅供参考,具体操作可能需要根据具体情况进行调整。
如需更多信息,建议咨询专业技术人员或查阅相关技术手册。
- 1、下载文档前请自行甄别文档内容的完整性,平台不提供额外的编辑、内容补充、找答案等附加服务。
- 2、"仅部分预览"的文档,不可在线预览部分如存在完整性等问题,可反馈申请退款(可完整预览的文档不适用该条件!)。
- 3、如文档侵犯您的权益,请联系客服反馈,我们会尽快为您处理(人工客服工作时间:9:00-18:30)。
扭振的测量
概括而言,因为所有的动设备在运行中都存在一定程度的扭振,但与横向振动不同,扭振难于用简单、直接的方法测量,经常被忽视。
如果因此视而不见,扭振就会成为设备损坏的隐形杀手,给企业带来巨大的直接和间接的损失。
无论ISO标准还是API标准,都要求正常运行时,设备的临界转速(其实也包括周边可能受影响的结构固有频率。
只是要求更高,要求其固有频率高于可能的稳态运行的频率的10倍)应该在稳态运行时,可能的激振频率的±10%之外(也有更严的要求:在15%~20%之外)。
扭振固有频率同样可能被激起,所以和横向振动一样,也必须知道你的转子系统的扭振固有频率。
转子的裂纹大多由扭振破坏引起,键、键槽等的损坏通常也与扭振密切相关,还有齿轮损坏、联轴器损坏、热涨(冷缩)配合的失效等也可能是扭振的失效引起。
扭矩的测量,必须要两个探头,在转子的两个截面测量,单个截面、单个探头只能测量扭振动态信号。
扭矩的大小正比于转子角转速的变化(欧拉定义)。
扭矩的变化通常发生于运行转速的变化,并因此产生扭振。
我们从力学理论中知道,扭矩测量的方法通常是应变片法,但在高速旋转的转子上贴应变片,信号还要传递出来,测量的频率范围还有一定的要求等,哪个方面都是难点。
应力-应变-单位轴向长度变化的角度等有确定的关系,可以用角度的测量来表达扭矩及扭振。
而角度的关系实质是一种时间的关系。
市场上缺乏测量扭振的通用、成熟产品。
英国有一家公司生产一种短节式的测量系统,但必须串进原机组的轴系中,所以是一种需要在设计阶段就考虑好,比较贵的系统。
本特利的3500/42M(MOD 183484, 162572)和System1的Classic支持这种装置。
这个方法其实也是一种测量时间间隔的方法(TIM):计算相邻两个
脉冲的时间间隔,而时间间隔的变化与特定转速下的扭振有关。
但近年来发展了一类简便方法,不改变原转子系统,使用已有的固定安装的键相(每转一个脉冲)信号,或者使用斑马带或多齿齿轮(MEW)产生的每转多个脉冲信号,高速采样,分析其中的扭振信号。
特点是:成本低,快捷,仅需要单个探
头。
当然,单个探头只能测量扭振,是无法测量扭矩的。
好在一般也不需要检验扭矩,机器的破坏大多是扭振,而不是扭矩造成的。
1.利用已有的键相信号。
高速采集键相脉冲信号,不用停机,使用键相信号的限制是最大的分析频率是转子转速频率的一半,如果转速低,而扭振固有频率较高就不够用了。
2.使用斑马反光带/激光探头法。
需要停机贴斑马带,最大分析频率范围扩大了。
主要是用于临时故障诊断,不能用于监测,带要注意结合部的不连续性。
要确认分析软件考虑到了这个因素。
3.使用多齿齿轮/激光探头法。
需要有齿轮盘或者额外安装齿轮盘,可用激光探头或其它能高速采集脉冲信号的探头,优点是安装牢靠、信号可靠。
但要注意齿形几何的不一致性,也要确认相应的软件考虑了这个误差可能带来的影响。
可以用于监测。
对于基于TIM的方法,同时要求较高的幅值精度和时域分辨率。
本特
利用ADRE408来采集连续原始波形,其128KHz的采样率能保证波形分辨率,而其24位的数模转换能满足幅值精度。
实践表明,不是随便的斑马反光带和普通的激光传感器都能胜任的。
反光带对反光条的间距和黑白对比度要求高,激光传感器要求有较高的采样频率。
对于持有ADRE 408的工程师,建议在日常启机采集信号时,应该总是激活键相信号的原始数据功能,以评估机组是否存在扭振问题,额定转速后解除原始波形的录波功能。
目前最常用的斑马反光带测量法,安装中有诸多技巧和注意事项,比如轴表面及条纹表面清洁要求,垂直、对齐要求,头尾结合点应是黑色非反光超长条要求,探头和斑马带的距离、角度要求等等,这里就不详述了。