低变催化剂结盐的原因及处理
制氢题库
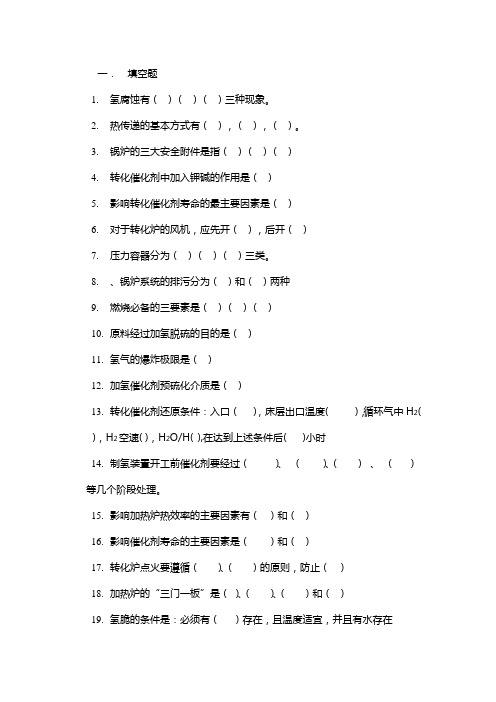
一.填空题1.氢腐蚀有()()()三种现象。
2.热传递的基本方式有(),(),()。
3.锅炉的三大安全附件是指()()()4.转化催化剂中加入钾碱的作用是()5.影响转化催化剂寿命的最主要因素是()6.对于转化炉的风机,应先开(),后开()7.压力容器分为()()()三类。
8.、锅炉系统的排污分为()和()两种9.燃烧必备的三要素是()()()10.原料经过加氢脱硫的目的是()11.氢气的爆炸极限是()12.加氢催化剂预硫化介质是()13.转化催化剂还原条件:入口(),床层出口温度( ),循环气中H2( ),H2空速( ),H2O/H( ),在达到上述条件后( )小时14.制氢装置开工前催化剂要经过()、()、()、()等几个阶段处理。
15.影响加热炉热效率的主要因素有()和()16.影响催化剂寿命的主要因素是()和()17.转化炉点火要遵循()、()的原则,防止()18.加热炉的“三门一板”是()、()、()和()19.氢脆的条件是:必须有()存在,且温度适宜,并且有水存在20.转化引蒸汽时,转化入口温度应大于()℃21.、汽包液位应保持在()22.汽水循环方式主要有()()两种23.转化降量的原则先降()再降()后降()24.润滑油的作用有()()()()()()()25.转化催化剂结盐主要是()26.离心泵的工作点不恰当的话很容易产生()现象27.计量泵属于()28.转化和PSA系统置换合格的标准是()29.灭火的四种基本方法()()()()答案1氢蚀、氢鼓泡、氢脆2传导、对流、辐射3安全阀、压力表、水位计4抗积炭5结炭6引风机、鼓风机7一级、二级、三级8连续排污、间断排污9可燃物、助燃物、着火源10避免转化催化剂中毒11.4-74%12氮气13. 入口480-500℃、床层出口温度≤750℃、循环气中H2≥60%),H2空速(≥300/时),H2O/H (≤7), 在达到上述条件后8-12小时14. 装填、干燥、预硫化、还原15烟气出炉温度、过剩空气系数16中毒和结碳 1 7均匀、对称,转化炉管受热不匀18风门、油门、汽门和烟道挡板19硫化物20. 320℃21. 40%——70% 22. 自然循环强制循环23燃料原料蒸汽24润滑冷却冲洗保护减震卸荷密封25蒸汽质量不合格26气蚀27往复式泵28氧气O2<0.5%,烃类含量<1%29隔离、窒息、冷却、抑制30,我装置转化催化剂型号为(),活性组分为()。
SCR催化剂失活机理及寿命管理

SCR催化剂失活机理及寿命管理李磊【摘要】From the several aspects of SCR catalyst poisoning, blocking, sintering and wear to analysis the mechanism of SCR catalyst deactivation, and from the aspects of operation maintenance to put forward the measures of catalyst life management which should be taken, as much as possible to maintain or extend the SCR catalyst activity, prolong its service life, thereby reach the objective of reducing the denitrification unit operation cost.%从SCR催化剂中毒、堵塞、烧结和磨损几个方面分析SCR催化剂失活的机理,并有针对性的提出从运行、维护等方面应采取的催化剂寿命管理措施,尽可能保持或延长SCR催化剂的活性,延长其寿命,从而达到降低机组脱销运行成本的目的。
【期刊名称】《全面腐蚀控制》【年(卷),期】2014(000)011【总页数】7页(P82-88)【关键词】SCR催化剂;失活机理;寿命管理;措施【作者】李磊【作者单位】北京京能电力股份有限公司石景山热电厂,北京100041【正文语种】中文【中图分类】TG174.42根据火电厂大气污染物排放标准(GB 13223-2011),自2014年7月1日起现有火力发电锅炉NOx排放浓度限值为100mg/Nm3[1]。
大量火力发电厂需要安装选择性催化还原法(SCR)脱硝装置。
其中催化剂的寿命直接决定着SCR系统的运行成本。
催化剂的还原方法与失活原因分析

催化剂的还原方法与失活原因分析催化剂在化学反应中起着至关重要的作用,它们能够加速反应速率,降低活化能,提高反应的选择性和效率。
然而,随着反应的进行,催化剂也会逐渐失去活性,需要进行还原处理,以恢复其催化性能。
本文将探讨催化剂的还原方法以及失活原因的分析。
一、催化剂的还原方法催化剂的还原主要是指将其氧化态还原为还原态。
常见的还原方法有物理还原和化学还原两种。
物理还原是指通过高温退火或氢气等物质的作用,将催化剂的氧化态转化为还原态。
高温退火能够促使氧化物表面的晶格缺陷重新排列,从而恢复催化剂的活性。
氢气可以与催化剂氧化物表面的氧原子发生反应,生成水蒸气,使催化剂还原。
物理还原方法操作简单,成本较低,是常用的催化剂还原方法之一。
化学还原是指通过添加化学试剂,将催化剂的氧化物还原为还原态。
常用的化学还原试剂有硫氢化物、异硫氰酸盐和亚磷酸钠等。
这些还原试剂可以与氧化物表面的氧原子发生反应,将其还原为相应的还原物。
化学还原方法能够在较低温度下实现催化剂的还原,但需要考虑试剂对环境的影响和处理废物的问题。
二、催化剂失活的原因分析催化剂失活是指在反应过程中,催化剂的活性逐渐降低或完全丧失的现象。
催化剂失活的原因多种多样,主要包括物理失活、化学失活和中毒失活等。
物理失活是指在反应过程中,催化剂的物理性质发生变化导致活性降低。
例如,催化剂的晶格结构受热膨胀、热收缩或晶格氧化等因素的影响,产生裂纹、微孔等缺陷,导致活性降低。
此外,催化剂的活性组分也可能随着时间的推移而释放,导致活性降低。
化学失活是指在反应过程中,催化剂与反应物或产物发生化学反应,使催化剂的活性降低。
这种失活多发生在高温、高压和高浓度等条件下。
例如,某些金属催化剂在高温条件下容易与氧化物反应,生成难溶的金属氧化物,导致活性降低。
此外,催化剂的活性组分也可能被氧化、硫化或硝化等反应所改变,导致活性降低。
中毒失活是指在反应过程中,催化剂与反应物或产物中的杂质发生反应,形成难溶的杂质物或中间体,使催化剂的活性降低。
分馏塔结盐原因分析及优化处理
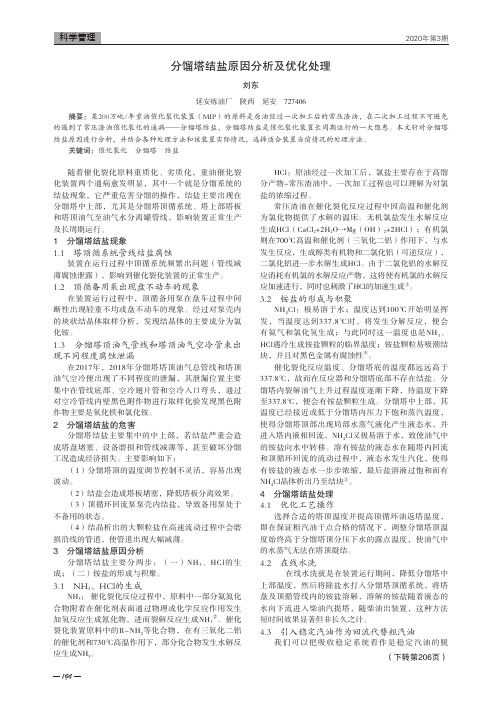
194随着催化裂化原料重质化、劣质化,重油催化裂化装置两个通病愈发明显,其中一个就是分馏系统的结盐现象,它严重危害分馏的操作,结盐主要出现在分馏塔中上部,尤其是分馏塔顶循系统、塔上部塔板和塔顶油气至油气水分离罐管线,影响装置正常生产及长周期运行。
1 分馏塔结盐现象1.1 塔顶循系统管线结盐腐蚀装置在运行过程中顶循系统频繁出问题(管线减薄腐蚀泄露),影响到催化裂化装置的正常生产。
1.2 顶循备用泵出现盘不动车的现象在装置运行过程中,顶循备用泵在盘车过程中间断性出现轻重不均或盘不动车的现象。
经过对泵壳内的块状结晶体取样分析,发现结晶体的主要成分为氯化铵。
1.3 分馏塔顶油气管线和塔顶油气空冷管束出现不同程度腐蚀泄漏在2017年,2018年分馏塔塔顶油气总管线和塔顶油气空冷便出现了不同程度的泄漏,其泄漏位置主要集中在管线底部、空冷翅片管和空冷入口弯头,通过对空冷管线内壁黑色附作物进行取样化验发现黑色附作物主要是氧化铁和氯化铵。
2 分馏塔结盐的危害分馏塔结盐主要集中的中上部,若结盐严重会造成塔盘堵塞、设备磨损和管线减薄等,甚至破坏分馏工况造成经济损失。
主要影响如下:(1)分馏塔顶的温度调节控制不灵活,容易出现波动。
(2)结盐会造成塔板堵塞,降低塔板分离效果。
(3)顶循环回流泵泵壳内结盐,导致备用泵处于不备用的状态。
(4)结晶析出的大颗粒盐在高速流动过程中会磨损沿线的管道,使管道出现大幅减薄。
3 分馏塔结盐原因分析分馏塔结盐主要分两步:(一)NH 3、HCl的生成;(二)铵盐的形成与积聚。
3.1 NH 3、HCl的生成NH 3: 催化裂化反应过程中,原料中一部分氨氮化合物附着在催化剂表面通过物理或化学反应作用发生加氢反应生成氰化物,进而裂解反应生成NH 3②。
催化裂化装置原料中的R-NH 2等化合物,在有三氧化二铝的催化剂和730℃高温作用下,部分化合物发生水解反应生成NH 3。
HCl:原油经过一次加工后,氯盐主要存在于高馏分产物-常压渣油中,一次加工过程也可以理解为对氯盐的浓缩过程。
一氧化碳低温变换工艺及应用
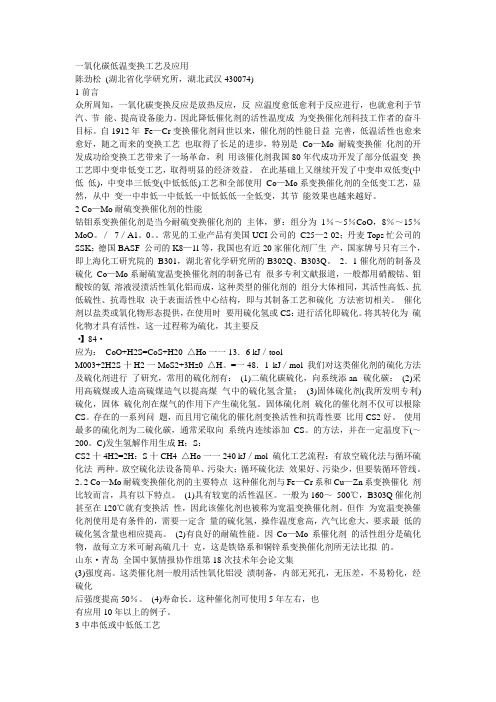
一氧化碳低温变换工艺及应用陈劲松(湖北省化学研究所,湖北武汉430074)1前言众所周知,一氧化碳变换反应是放热反应,反应温度愈低愈利于反应进行,也就愈利于节汽、节能、提高设备能力。
因此降低催化剂的活性温度成为变换催化剂科技工作者的奋斗目标。
自1912年Fe—Cr变换催化剂问世以来,催化剂的性能日益完善,低温活性也愈来愈好,随之而来的变换工艺也取得了长足的进步,特别是Co—Mo耐硫变换催化剂的开发成功给变换工艺带来了一场革命,利用该催化剂我国80年代成功开发了部分低温变换工艺即中变串低变工艺,取得明显的经济效益。
在此基础上又继续开发了中变串双低变(中低低),中变串三低变(中低低低)工艺和全部使用Co—Mo系变换催化剂的全低变工艺,显然,从中变一中串低一中低低一中低低低一全低变,其节能效果也越来越好。
2 Co—Mo耐硫变换催化剂的性能钴钼系变换催化剂是当今耐硫变换催化剂的主体,萝:组分为1%~5%CoO,8%~15%MoO。
/7/A1。
0。
常见的工业产品有美国UCI公司的C25—2-02;丹麦Tops忙公司的SSK;德国BASF 公司的K8—1l等,我国也有近20家催化剂厂生产,国家牌号只有三个,即上海化工研究院的B301,湖北省化学研究所的B302Q、B303Q。
2.1催化剂的制备及硫化Co—Mo系耐硫宽温变换催化剂的制备已有很多专利文献报道,一般都用硝酸钴、钼酸铵的氨溶液浸渍活性氧化铝而成,这种类型的催化剂的组分大体相同,其活性高低、抗低硫性、抗毒性取决于表面活性中心结构,即与其制备工艺和硫化方法密切相关。
催化剂以盐类或氧化物形态提供,在使用时要用硫化氢或CS:进行活化即硫化。
将其转化为硫化物才具有活性,这一过程称为硫化,其主要反·】84·应为:CoO+H2S=CoS+H20 △Ho一一13.6 kJ/toolM003+2H2S十H2一MoS2+3Hz0 △H。
=一48.1 kJ/mol 我们对这类催化剂的硫化方法及硫化剂进行了研究,常用的硫化剂有:(1)二硫化碳硫化,向系统添an--硫化碳;(2)采用高硫煤或人造高硫煤造气以提高煤气中的硫化氢含量;(3)固体硫化剂(我所发明专利)硫化,固体硫化剂在煤气的作用下产生硫化氢。
催化裂解装置反应系统结焦原因分析及应对措施
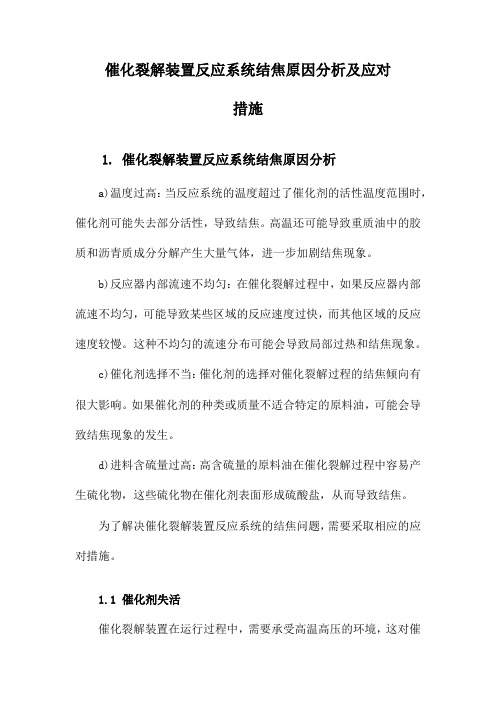
催化裂解装置反应系统结焦原因分析及应对措施1. 催化裂解装置反应系统结焦原因分析a)温度过高:当反应系统的温度超过了催化剂的活性温度范围时,催化剂可能失去部分活性,导致结焦。
高温还可能导致重质油中的胶质和沥青质成分分解产生大量气体,进一步加剧结焦现象。
b)反应器内部流速不均匀:在催化裂解过程中,如果反应器内部流速不均匀,可能导致某些区域的反应速度过快,而其他区域的反应速度较慢。
这种不均匀的流速分布可能会导致局部过热和结焦现象。
c)催化剂选择不当:催化剂的选择对催化裂解过程的结焦倾向有很大影响。
如果催化剂的种类或质量不适合特定的原料油,可能会导致结焦现象的发生。
d)进料含硫量过高:高含硫量的原料油在催化裂解过程中容易产生硫化物,这些硫化物在催化剂表面形成硫酸盐,从而导致结焦。
为了解决催化裂解装置反应系统的结焦问题,需要采取相应的应对措施。
1.1 催化剂失活催化裂解装置在运行过程中,需要承受高温高压的环境,这对催化剂的活性和稳定性提出了很高的要求。
在长时间的高温高压作用下,催化剂会发生热老化、碱腐蚀等现象,导致其活性降低甚至失活。
催化裂解装置的空速是影响催化剂活性的重要参数,如果空速过快,会导致催化剂表面的气体流速过大,从而使催化剂表面积炭速度加快,进而导致结焦现象的发生。
催化裂解装置所处理的原料油品质直接影响催化剂的使用寿命和活性。
如果原料油中杂质含量过高,如硫、磷等元素含量过高,会加速催化剂的失活过程,从而导致结焦现象的发生。
催化裂解装置的操作条件对催化剂的活性有很大影响,如温度、压力、进料量等参数设置不当,都可能导致催化剂失活,进而引发结焦现象。
选择适合催化裂解工艺条件的催化剂,并对其进行优化设计,以提高其抗高温、抗高压、抗污染等性能,从而降低催化剂失活的风险。
通过调整空速参数,使催化剂表面的气体流速保持在合适的范围内,减缓催化剂表面积炭的速度,降低结焦风险。
加强对原料油的质量监控和管理,严格控制原料油中硫、磷等有害元素的含量,降低催化剂失活的可能性。
甲醇原料气中氢碳比的调控
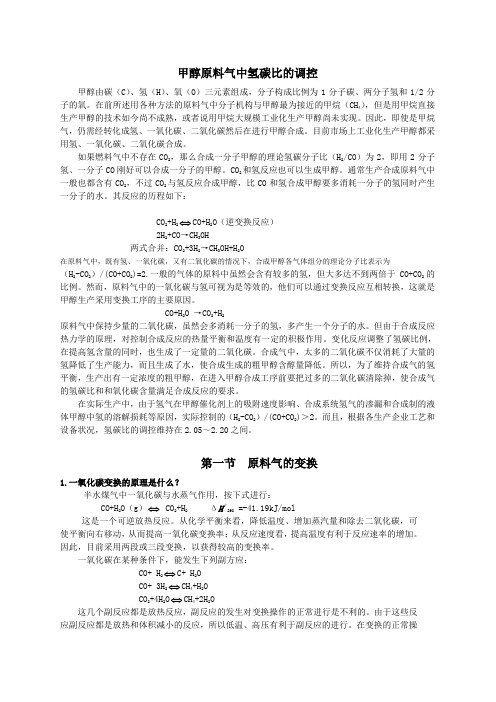
甲醇原料气中氢碳比的调控甲醇由碳(C)、氢(H)、氧(O)三元素组成,分子构成比例为1分子碳、两分子氢和1/2分子的氧。
在前所述用各种方法的原料气中分子机构与甲醇最为接近的甲烷(CH4),但是用甲烷直接生产甲醇的技术如今尚不成熟,或者说用甲烷大规模工业化生产甲醇尚未实现。
因此,即使是甲烷气,仍需经转化成氢、一氧化碳、二氧化碳然后在进行甲醇合成。
目前市场上工业化生产甲醇都采用氢、一氧化碳、二氧化碳合成。
如果燃料气中不存在CO2,那么合成一分子甲醇的理论氢碳分子比(H2/CO)为2,即用2分子氢、一分子CO刚好可以合成一分子的甲醇。
CO2和氢反应也可以生成甲醇。
通常生产合成原料气中一般也都含有CO2,不过CO2与氢反应合成甲醇,比CO和氢合成甲醇要多消耗一分子的氢同时产生一分子的水。
其反应的历程如下:CO2+H2⇔CO+H2O(逆变换反应)2H2+CO→CH3OH两式合并:CO2+3H2→CH3OH+H2O在原料气中,既有氢、一氧化碳,又有二氧化碳的情况下,合成甲醇各气体组分的理论分子比表示为(H2-CO2)/(CO+CO2)=2.一般的气体的原料中虽然会含有较多的氢,但大多达不到两倍于CO+CO2的比例。
然而,原料气中的一氧化碳与氢可视为是等效的,他们可以通过变换反应互相转换,这就是甲醇生产采用变换工序的主要原因。
CO+H2O →CO2+H2原料气中保持少量的二氧化碳,虽然会多消耗一分子的氢,多产生一个分子的水。
但由于合成反应热力学的原理,对控制合成反应的热量平衡和温度有一定的积极作用。
变化反应调整了氢碳比例,在提高氢含量的同时,也生成了一定量的二氧化碳。
合成气中,太多的二氧化碳不仅消耗了大量的氢降低了生产能力,而且生成了水,使合成生成的粗甲醇含醇量降低。
所以,为了维持合成气的氢平衡,生产出有一定浓度的粗甲醇,在进入甲醇合成工序前要把过多的二氧化碳清除掉,使合成气的氢碳比和和氧化碳含量满足合成反应的要求。
水煤气变换新工艺
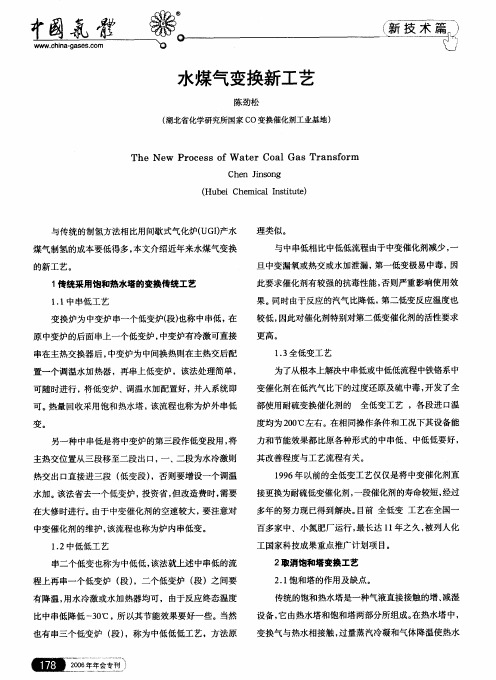
串二个低变也称为中低低, 该法就上述中串低的流
程上再串一个低变炉 ( , 段) 二个低变炉 ( 段)之间要
有降温, 用水冷激或水加热器均可,由于反应终态温度
21 .饱和塔的作用及缺点。
传统的饱和热水塔是一种气液直接接触的增、 减湿 设备, 它由热水塔和饱和塔两部分所组成。 在热水塔中, 变换气与热水相接触, 过量蒸汽冷凝和气体降温使热水
一由于水煤气中的氧和硫化物在饱和热水塔循环水中生成酸性的硫酸盐水煤气的脱硫大多数使用氨水又为了降低饱和热水塔的腐蚀也往循环水中加入氨水这样使饱和塔的总固体硫酸盐居高不下通过带水或水雾进入变换炉一段总固体大都为铵盐在中串低或中低低流程中由于进口温度为300c铵盐挥发后都沉淀在后面的低变催化剂上这就是中串低的低变和中低低的第一低变使用寿命短的万吨合成氨, 02 1 0 20
扣 月
卜术 卑」 、、 ℃J /
脱水 年 1 盐 月应用。 点 琳 附川 淤
汁 林 }针 、
( 湖南湘潭, 万吨合成氨, 04 月 20年6 4 ) 1 6
ki 应用。 4 *
a 寸 1 6 f
w wci -ae . m w . n g ss o ha c
降低催化剂利用率。 而且循环热水腐蚀介质随着变换气 带出热水塔, 是造成二水加热器、 软水加热器腐蚀的重
要原因。
三、 循环热水中 的氧和硫化物在金属填料的 催化作 用下还有部分生成元素硫, 而元素硫熔点是1 .0, 15 沉 4 C
变换炉为中变炉串一个低变炉( 也称中串低, 段) 在 原中变炉的后面串上一个低变炉, 中变炉有冷激可直接 串在主热交换器后, 中变炉为中间换热则在主热交后配 置一个调温水加热器,再串上低变炉,该法处理简单, 可随时进行, 将低变炉、 调温水加配置好, 并人系统即 可。 热量回收采用饱和热水塔, 该流程也称为炉外串低
- 1、下载文档前请自行甄别文档内容的完整性,平台不提供额外的编辑、内容补充、找答案等附加服务。
- 2、"仅部分预览"的文档,不可在线预览部分如存在完整性等问题,可反馈申请退款(可完整预览的文档不适用该条件!)。
- 3、如文档侵犯您的权益,请联系客服反馈,我们会尽快为您处理(人工客服工作时间:9:00-18:30)。
催 化 剂 结盐 后 , 在 催 化 剂上 层形 成 盐 层 硬 会 解 决 了生产 系统 的氨 水 平衡 难 题 , 轻 了环 保压 减 力 。 目前开 机模 式下 , 每年 生 产 3 0 d 装 置 日 按 0 、 平 均 回收液 氨 1 右 , 氨 22 0 t , 5i 左 n 液 0 计 则
1 2 生产 负荷 大 .
系统 改造后 生 产 负 荷增 大 , 低 变 炉 催 化 剂 但 装填量 没 有增加 , 因而低 变炉 处理量 已达 到极 限 。
1 低 变 催 化 剂 结盐 的原 因
1 1 脱 盐水质 量 不好 .
2 结 盐 的 危 害
2 1 增加 系统 阻力 和能 耗 .
1膨 胀 机 转 速 / r n ) (・ mi 2膨 胀 机 转 速 / r n ) (・ mi
年 产生 经济 效益 654 4 .8万元 。
回收 的气 氨转 化成 液 氨需要 增开 1台额 定 功
膨胀 后 温度 /C  ̄ 三级 分 氨后 气 温 /C o
解 析 气 压 力/ a MP
小氮肥
第3 8卷
第 3期
21 0 0年 3月
1 3
低 变 催 化 剂 结 盐 的 原 因及 处 理
李晓 波
( 化集 团有 限公 司 齐 齐哈 尔 114 ) 黑 60 1 C O 。在人 低 变炉前 气 体 经过 饱 和 热水 塔 将脱 盐
0 前 言
黑龙 江黑 化集 团有 限公 司硝 酸铵 厂 C O变 换 系统采用加压 中低温变换 串联工艺 流程 , 变炉采 低 用 L 2 4型铜锌 铝 型低 变催 化 剂 , 填 量 为 4 , B0 装 8t 分 2层装填 , 操作 压力在 1 2 .5~17 M a 0 3年 . P 。2 0 以来 , 司对净 化 系统 的部 分 装置 进 行 了改 造 , 公 改
造后原料气量 大幅度提 高 , 由于低变 炉催化 剂结 但
盐造成 阻力 升高 , 使生 产 能力 降低 , 重影 响 装置 严 正常运行 。为此 , 对低 变炉催化 剂结盐 的原 因进 行 了分析 , 采取相 应措 施 , 并 取得 了满 意的效 果 。
而造 成一 次脱盐 水 的质量 下 降 。
弛放 气 流 量 / i ・ , 态 ) ( h一 标 n 气氨 压 力 / a MP 废 气 压 力/ a MP 废 气 流 量/( h , 态 ) m・ 标 废气 中 妒 N 3/ ( H ) % 分 氨 尾 气 中 ( H3 / N )%
回收 氨 ( d ) m ・
人员 工资 为 1 . 0 0万元 。
4 效 益 分 析
该装 置采 用深 冷 法 回收 弛 放气 中 的 氨 , 效 有
总计 , 该装 置 年产生 经济 效益 297 2 .9万元 。
( 收稿 日期 2 0 -53 ) 0 90 . ห้องสมุดไป่ตู้ 0
1 4
小氮肥
第3 8卷
第 3期
2 1 3月 0 0年
低 变炉 内 的 主 要 反 应 为 : O +H O =H C +
表 1 改 造后 运 行 工 艺 参 数
项 目 0 -5 1 —0 1 -7 1 - 80 0 1 0 2 1 1 5
5 0 5 ) 5 o 5 0 29 0 31( 0 45 o 4lo 5 0O 4 l 0 5 0 5 0 3 2 H 5 0 5 0 0 550
6 9 4 3
—7 0 —3 9
—7 2 —4 8
—7 0 —41
—
率 20k 的冰机 , 2 W 电价 按 0 3 .5
则 年增 加成本 5 . 4万元 。 54
(W ・ ) , k h计
18 2 1 83 .5 .6 18 2 18 2 . 3 .3 1 O1 8 l0 6 5 l0 2 6 l08 3
水 直接 喷入 , 已达 到水 气 比大于 2 0的要 求 。 由于
设 备改 造后 系统 中工 艺气 量 加 大 , 致 脱 盐水 的 导
用 量增 加 。生 产 中使用 的脱盐 水 为水处 理系 统 的
一
次脱 盐水 , 的电导率 小 于 1 S e 由于近 它 0 t / m。 x
几 年生产 规模 不 断 扩 大 , 得 水 处 理 量增 加 了几 使 倍, 原有 水处理 装 置虽经 改造 也满 足不 了要求 , 因
解析 气 流量 / m’h~ , 态 ) ( ・ 标
弛放 气 压 力 / a MP
19 5 1 80 .4 .8 19 5 19 3 . 6 .2 l5 3 0 16 6 5 15 11 l5 8 5
装 置总投 资 约 为 2 0万 元 , 备 折 旧 年 限 为 5 设
装 置开 车后 , 现有 开机模 式下 , 两气 塔 氨水质
量分 数 由约 2 % 降 到 约 1 % , 外 销 7 / , 5 5 按 0td 每 下降 1 %按 1 计算 , 年减 少 氨 水外 销 收 益 为 4元 则
2 4 0万 元 。 9.
人员 工资 年薪 2 5万 人 , 4人 计 , 年 . 按 则
8a按资 金使 用 成本 为 1% 计 算 , 每 年 增 加成 , 0 则
本 5 .5万元 。 62
0. 2 O. 4 0 1 O O. 3 1 5 15 . 3 18
0. 8 0. 8 0 2 5 0. 8 2 3 2 6 . 8 2 5 1 81 7 0 5 . 3 1 5 . 1 1 6 4. 1 7 l8 9 8 2 8 18 9 5 0. 9 5 16 .0 1 8 4. 04 .5 1 3 .3 1 4 5. 0. 5 5 15 . 6 1 8 4.