FMEA讲义(mqe)
FMEA讲义
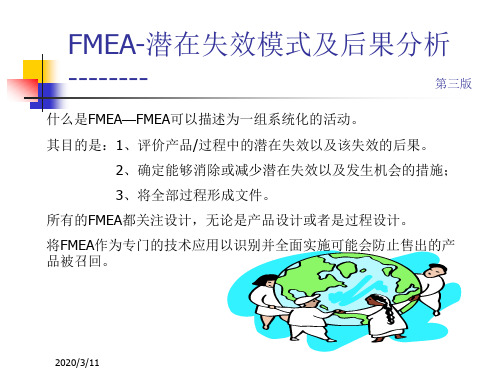
DFMEA中标明的特殊性也必须在PFMEA中作为重 点分析的内容。
2020/3/11
FMEA线路图
准备功能框图或过程流程图
确认现行控制
输入信息到FMEA表格
确认任务成功
用头脑风暴考虑所有 可能的问题和忧虑
2020/3/11
严 级 潜在
重 别 失效
度
起因/Leabharlann S机理有多糟 糕?
起因 是什 么?
频 现行控 度制 O
预探 防测
发生 的频 率如 何?
探R 测P 度N D
建议措 施
责任及 目标完 成日期
能做些什么? 设计更改 过程设计 特殊控制 标准、程序
或指南的更改
措施结果
采取 S O D R
的措
P
施
N
怎样能 得到预 防和探 测?
2020/3/11
思维方式的转变
采用像FMEA这样的工具,对于我们每一个人来说,有 利于提升我们工作质量,有利于全面发展,因为,对 于工程师来说,从单纯的技术的角度去分析问题,问 题的范围可能会局限于一个很窄的范围,而且很容易 犯经验主义,根据前期大量的实验和多年的经验,很容 易得出与事实真相完全背离的结果。如果我们的工程 师从质量的角度出发分析问题,借助诸如FMEA这样 的工具,将每一个潜在的失效因素细化,文件化。尤 其对于微电子这样的生产,细化每一项操作是非常重 要的。
确定失效模式和原因
是评定 FMEA
建立频度
完成FMEA分析
确认探测方法并 建立探测度
确认后果并 建立严重度
使用排列图;根据 需求选择需改进之处
FMEA工程应用培训讲义

FMEA工程应用培训讲义FMEA (Failure Mode and Effects Analysis)是一种常用的风险管理工具,广泛应用于工程设计和制造过程中,旨在提前识别和消除潜在的故障和缺陷。
FMEA可以帮助工程师在设计和制造过程中确定风险,并制定相应的措施来降低潜在故障和缺陷的发生概率。
一、FMEA的基本原理1.1 FMEA的概念FMEA是一种通过系统化的方法,对产品、设计或工作过程中的潜在故障模式进行分析和评估的方法。
通过找出故障模式的潜在原因和效应,可以采取相应的预防措施来减少故障的发生。
1.2 FMEA的目的FMEA的主要目的是通过提前识别和消除潜在的故障和缺陷,提高产品和流程的可靠性和质量。
它能够帮助工程师在设计和制造的过程中识别可能导致产品故障的因素,并制定相应的改进措施。
二、FMEA的应用步骤2.1 选择要分析的过程或产品首先确定要进行FMEA分析的具体产品或过程。
这可以是一个正在开发的新产品,也可以是一个现有产品的改进过程。
2.2 组织FMEA团队确定一个专门的团队来进行FMEA分析。
该团队应由各个领域的专家组成,包括设计工程师、制造工程师和质量控制专家。
2.3 确定潜在故障模式分析可能导致产品故障的各个环节,包括设计、制造、运输、安装和使用过程。
对每个环节,确定可能发生的故障模式。
2.4 评估故障模式的严重性对每个故障模式,评估其可能对产品或过程的影响程度,包括安全性、可靠性和成本等方面。
2.5 确定故障模式的原因对每个故障模式,找出可能导致其发生的潜在原因。
这些原因可以是设计缺陷、制造误差、操作错误等。
2.6 评估故障模式的概率对每个故障模式,评估其发生的概率。
这可以通过历史数据、专家访谈等方式进行评估。
2.7 评估故障模式的可探测性对每个故障模式,评估其是否可以通过检测手段及时发现。
如果不能及时发现,应考虑改进措施。
2.8 制定改进措施根据故障模式的严重性、原因、概率和可探测性,制定相应的改进措施。
FMEA我的讲义

FMEA的实施 FMA:Failure Mode Analysis
FMA(失效模式分析) FMEA(潜在失效模式及后果分析)
失效已经产生
失效还未产生,可能发生,但不是一 定要发生
核心:纠正
核心:预防
诊断已知的失效
评估风险和潜在失效模式的影响
开始于产品设计和工艺开发活动之前
指引开发和生产
指引贯穿整个产品周期
• 4、1985年由国际电工委员会(IEC)出版的FMECA 国际标准(IEC812),即参考MIL-STD-1629A加以部分 修改而成。
13
FMEA 之適用範圍
• 1、ISO9004 8.5節FMEA作為設計審核的要項,另 FTA(失效樹分析)風險分析亦是。
• 2、CE標志,以FMEA作為安全分析方法。
E: Effect 後果
Effect談三種: 1.對本身的立即影響
2.對同一水平的影響, 也可能對下一工序的影響 3.對產品使用者的影響
6
FMEA定義
後果的通常表現形式:
人身安全 不舒服的氣味 不穩定 作業中斷 無法繫緊 無法安裝 損壞裝備
手感不良
作業過多
無法操作
操作不良
車控不良
顧客不滿意
滲漏
外觀不良
12
FMEA 之沿革
• 1、FMEA的前身為FMECA,是在1950由格魯曼飛機 提出,用在飛機主控系統的失效分析
• 2、波音與馬丁公司在1957年正式編訂FMECA的作业 程序,列在其工程手冊中
• 3、60年代初期,美太空总署将FMECA成功的应用于 太空计划。美军同时也开始应用FMECA技术,并于 1974年出版MIL-STD-1629 FMECA作业程序。
FMEA讲义(mqe)

• FMEA从局部失效入手,分析其对上一级系统、 相关部分、下游程序以及总体系统的后果。分析 路径“由下至上”。
• FTA一般由系统的失效模式入手、分析造成该失 效产生的原因。分析路径“由上至下”。
FMEA讲义(mqe)
和装配性问题的补充,应该反馈到DFMEA中去。
FMEA讲义(mqe)
第3章 PFMEA
3.1 PFMEA的准备工作
❖ PFMEA的准备工作包括:
① 建立小组 ② 准备必要的资料,如:
➢ 过程流程图 ➢ 过程特性矩阵表 ➢ 现有的类似的PFMEA资料模板 ➢ 现有的类似的PFMA资料 ➢ 特殊过程特性明细表 ➢ SOP工程规范
FMEA讲义(mqe)
第 1 章 概论
1. 3 FMEA主要用途
设计用
设计分析及改 善
设计品质/可靠 度
FME A
分析 用途
制程用
制程分析及改 善
提升制程能力
设备用
设备分析及评 估
提升设备能力
1设计改进; 2保养、维修、稽 核 制度及清单 3 sop
sop制程管制 重点
系统及方法
Checklist 设备管制、调整、
FMEA讲义(mqe)
第 1 章 概论
1. 1 什么是FMEA?
❖ FMEA是一种系统分析、强调事实、数据化; ❖ FMEA及早地指出根据经验判断出的弱点和可能产
生的缺陷,及其造成的后果和风险,并在运作过程 中采取措施加以消除; ❖ FMEA是目前全世界工程界最行之有效的预防手段 ,其准则是 “避免缺陷产生较之以后发现缺陷,而 不得不加以排除,显得更合理,更经济”; ❖ FMEA是用于评定风险的一种按优先次序排列的矩 阵工具。
六、FMEA讲义
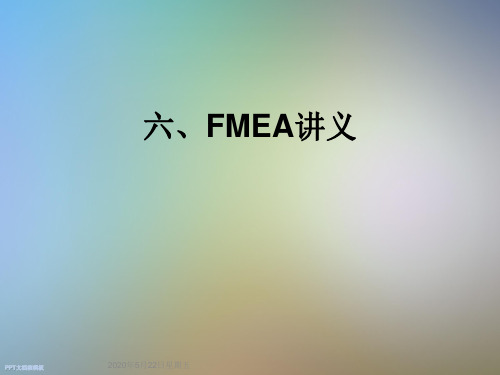
严重度评价表
• 失效模式的潜在要因(f):失效的潜在要因按照失效 怎么发生的迹象来定义,按照可纠正或可控制的情 形来描述.失效的潜在要因是设计或过程弱点的显 示,后果就是失效模式。失效模式可能是由一种或 一种以上的要因导致的。
• 发生率(O)(g): 发生率是失效特定要因发生的可能 性,发生可能性的排序值相对绝对值而言更有意义, 在1至10等级范围内评估失效潜在要因的发生可 能性。
• 严重度(s)(d): 严重度是与给定的失效模式最严重 后果相符的值。严重度是在单独FMEA范围内的 相关排序。
• 对等级9或10的不建议修改标准,等级为1的失效模 式不应再进一步分析。
• 分类(e):这栏可用于强调高优先权失效模式或可能 要求额外工程评估的要因,(为标识特殊特性)。
• FMEA中严重度等级识别为9或10的特殊特性,由 于这可能影响工程文件,应该通知负有设计责任的 工程师。
• 探测率(D) (i): 探测度是与探测控制栏列出 的最佳探测控制相符的级别.探测率是单独 FMEA范围内的相对排序,为了获得一个较 低的级别,一般来讲须改善计划的探测控制.
• 风险优先系数(RPN) (j): 帮助措施最优排序 的一种方法是使用风险优化系数。
• RPN=严重度(S) X 发生率(O) X 探测率 (D)
• FMEA帮助我们了解
• 哪里可能出错? • 造成的影响是什么? • 影响多严重? • 造成的原因是什么? • 发生概率多高? • 管制的方式是什么? • 管制多有效? • 整体风险多高? • 如何降低风险?
• 使用FEMA的好处
• 提高产品的质量、产品的可靠性和安全性。 • 帮助增加客户满意度。 • 减少产品开发时间和成本。 • 减少返工、维修和报废的数量。 • 记录并跟踪为减少风险而采取的行动。 • 优先考虑各缺点,关注改进努力。
FMEA(讲义)

11
——零部件 零部件FMEA 零部件
子系统FMEA是子系统 是子系统FMEA的子集.示例 的子集. 子系统 是子系统 的子集 包括:刹车片是刹车总成的零部件之一, 包括:刹车片是刹车总成的零部件之一, 刹车总成又是底盘系统的一个子系统. 刹车总成又是底盘系统的一个子系统. 范围不同,小组的成员也不同. 注:范围不同,小组的成员也不同.
26
ቤተ መጻሕፍቲ ባይዱ
过程流程图和PFMEA的关系 的关系 过程流程图和
过程流程图描述的是整个过程中: 过程流程图描述的是整个过程中:从来料 到出货的流程. 到出货的流程. 包括了制造装配过程中每个步骤, 包括了制造装配过程中每个步骤,输入和 输出的要求. 输出的要求. 初始过程流程图是一种粗略描述的流程图. 初始过程流程图是一种粗略描述的流程图.
16
设计FMEA—步骤和完成时间 步骤和完成时间 设计
在生产设计发布之前, 在生产设计发布之前,完成DFMEA. .
——定义顾客 定义顾客 ——成立小组 成立小组 ——可制造性,可装配性和可服务性的考虑 可制造性, 可制造性
表
17
设计FMEA—功能要求 功能要求 设计
表
用尽可能简明的文字来说明被分析项目满足设计 意图的功能. 意图的功能. ——产品的目的和产品整体的设计目标 产品的目的和产品整体的设计目标 ——安全性 安全性 ——政府法规 政府法规 ——可靠性(功能寿命) 可靠性( 可靠性 功能寿命) ——外观 外观 设计严重度.doc表1 ——可装配性设计和制造性设计等 可装配性设计和制造性设计等
表
7
FMEA方法 成立小组 方法— 方法
FMEA开发主题 开发主题
范围 职能, 职能,要求和期望 潜在失效模式-过程和产品可能导致失效的模式 潜在失效模式 过程和产品可能导致失效的模式 失效影响和结果失效影响和结果-对内部过程或对下游顾客的影响和后果 潜在失效的原因 潜在失效发生的频率 现行预防控制的应用 现行探测控制的应用 要求的推荐措施
公开课-FMEA培训讲义

• 分析方法:从局部入手,分析对总成的影响
4
第四页,共69页。
FMEA实施的十大步骤
按照?GB7826-1987S失效模式和后果分析程序?规定:
1、定义系统及其功能和要求
2、拟定功能和工艺流程图
3、确定分析的根本原那么 4、找出失效模式、原因及后果 5、找出失效的监测、纠正措施
19
第十九页,共69页。
设计 FMEA的标准表
系统 子系统
零部件
车型年/车辆类型
核心小组
(8)
潜在失效模式及后果分析
(2) 设计责任 (5) 关键日期
〔设计FMEA〕
(3年) 年 (6)
FMEA编号:
(1)
共 页,第 页
编日制期人 〔编:制〕(4)〔修订〕
(7)
FMEA
等
项目 潜在
失效
模式
功能要
求
突出对高优先度的失效模式进行工程评定。 要注意符号的一致性:DFMEA、PFMEA和控制方案, 工艺文件,作业指导书,检验文件都要标注。
30
第三十页,共69页。
(14〕失效的潜在起因/机理
• 所谓失效的潜在起因是指设计薄弱局部的迹象,其结果就 是失效模式。
• 尽可能地列出每一失效模式的每一个潜在起因和/或失效 机理。起因/机理应尽可能简明而全面的列出,以便有针 对性地采取补救的努力。
公开课-FMEA培训讲义
1
第一页,共69页。
根本概念
• 失效:产品/过程失去本身功能。
• 失效模式:产品/过程失效时所表现的形式。 • 失效模式分析:对已出现的失效模式进行分析,是一种事后
行为。 • 潜在失效模式分析:对可能要发生的失效模式进行分析,是
FMEA培训讲义(PPT 103页)

适时性:在“时间之窗”关闭之
前+
小组的努力:集体的智慧
9
9
天津华诚认证中心
CAQC Certification Inc.
适时性
成功实施FMEA项目的 最重要因素之一
FMEA是预防性的 不是反应性的
应当尽量避免失效 而不是等着顾客提出申诉
10
10
天津华诚认证中心
CAQC Certification Inc.
1
天津华诚认证中心
CAQC Certification Inc.
课程内容
一、FMEA概 述
二、设计 FMEA
三、过程 FMEA
FMEA的定义、起源 FMEA的实施、跟踪 FMEA的分类
设计FMEA简介 设计FMEA的实施
过程FMEA简介 过程FMEA的实施
2
2
天津华诚认证中心
CAQC Certification Inc.
及 回
2、制造开发(1:10)
报
比
3、装配(1:1)
4、服务(1:0.5)
5、顾客抱怨,投诉后处理(1:0.05)
4
4
天津华诚认证中心
CAQC Certification Inc.
FMEA的作用
质
量
意
质量是规划出来的
识
三
质量是生产出来的
层
次
质量是检验出来的
预防作用 经验库
设计\规划部门 生产\制造部门 检验部门
不合格品、顾 客抱怨等
17
17
天津华诚认证中心
CAQC Certification Inc.
3.什么情况下 进 行 F M E A ?
新设计、新技术或新过程。 对现有设计或过程的修改。 将现有的设计或过程用于新的环境、新的场所。
- 1、下载文档前请自行甄别文档内容的完整性,平台不提供额外的编辑、内容补充、找答案等附加服务。
- 2、"仅部分预览"的文档,不可在线预览部分如存在完整性等问题,可反馈申请退款(可完整预览的文档不适用该条件!)。
- 3、如文档侵犯您的权益,请联系客服反馈,我们会尽快为您处理(人工客服工作时间:9:00-18:30)。
产品设计部门的下一道工序是过程设计,产品设计 应充分考虑可制造性和可装配性问题,由于产品设 计中没有适当考虑制造中技术与操作者体力的限制, 可能造成过程失效模式的发生。如:
• 必要的拔模斜度 • 表面处理的限制 • 装配空间/工具可使用性 • 钢材硬度的限制 :装配“基地面”还是“装入件 ” • 过程能力/性能:“点胶水”连接
31
第3章 PFMEA
3.3 潜在的失效模式
对于试验、检验过程,可能的失效模式有两种:接 受不合格的零件和拒收合格的零件。 零件被拒收,既要考虑最终顾客不接受,也要考虑 下一道工序及下游工序不接受的问题。如壳件的变 形使缝隙过大,螺装错位等。 运用失效链原理:上游工序的失效模式可能是下游 工序的失效原因,下游工序的失效模式可能是上游 工序失效模.3DFMEA运作
DFMEA是一个动态文件,在整个产品寿命周期
内,根据反馈信息,在进行设计修改时对 DFMEA进行重新评审和修改; 关闭管理:产品DPL
13
第 2 章 DFMEA
2.4 失效链
一个潜在的失效事件的发生,如果没有采取 或来不及采取或事实上不可能采取措施,而 使之引起下游系统或相关系统产生连锁失效 事件,我们称之为“失效链”。
• FMEA从局部失效入手,分析其对上一级系统、
相关部分、下游程序以及总体系统的后果。分析 路径“由下至上”。 • FTA一般由系统的失效模式入手、分析造成该失 效产生的原因。分析路径“由上至下”。
7
第 1 章 概论
新的 更改的 设计 评价 方框图
设计 FMEA
DFMEA
产品 过程 特性 过程流 程图 过程 FMEA
PFMEA,由“负责制造的各专业、职能工程师/小 组”采用的一种分析技术 着眼工艺过程(经验和问题、可能) 系统化、规范化,有完整的PDCAS过程
• 确定与产品相关的过程潜在失效模式; • 评价失效对顾客?的潜在影响; • 确定潜在制造或装配过程失效的起因,确定减少失效发
生或找出失效条件的过程控制变量; • 编制潜在失效模式分级表,然后建立考虑纠正措施的优 选体系; • 将制造或装配过程的结果编制行动文件。
19
第3章 PFMEA
PFMEA可以用于新工装或设备的开发。 其方法是一样的,只是应将所设计的机器或设 备当作一种产品来考虑,确定了潜在失效模式, 采取纠正措施,消除潜在失效模式或不断减小 其发生的可能性。
20
第3章 PFMEA
流程图应确定与每个工序有关的产品/过程特性参数。同时 接应相应的设计DFMEA已某些产品特性及后果。
17
第 2 章 DFMEA
2.7 DFMEA与PFMEA的联系
产品设计DFMEA不能依靠过程检测作为 控制措施 PFMEA应将DFMEA作为重要的对接、输 入。对DFMEA中标明的特殊特性也必须 在FMEA中作为重点分析的内容;
细部应用方法集中到下章节讲解
18
第3章 PFMEA
过程
PFMEA
1.2 FMEA种别
• •
8
SFMEA– 系统FMEA; DFMEA– 设计FMEA;PFMEA– 过程FMEA AFMEA—应用FMEA;SFMEA—服务FMEA;PFMEA—采购FMEA
第 1 章 概论
1. 3 FMEA主要用途
设计用 设计分析及改 善 设计品质/可靠 度 制程分析及改 善 提升制程能力 1设计改进; 2保养、维修、稽 核 制度及清单 3 sop sop制程管制 重点 系统及方法
10
第 2 章 DFMEA
2.1 由谁来做DFMEA?
团队构成:公司组织的产品开发、制造、装配、售后服 务、质量及可靠性方面的专家
a 与设计有关的上游(如供方、材料、上一个相关系统工程师); b下游(如下一个相关系统工程师)的部门也将被吸收参加小组的工 作;
c专长和责任领域:装配、制造、设计、分 析/试验、可靠性、材料、
第3章 PFMEA
3.3 潜在的失效模式
• •
失效模式有两种类型: 不能完成规定的功能,如零件超差, 错装。又称Ⅰ 型 产生了非期望功能:如加工过程使操作者或机器受 到伤害、损坏,产生有害气体、过大的噪声、振动, 过高的温度、粉尘、刺眼的光线,等等。又称Ⅱ型
30
第3章 PFMEA
3.3 潜在的失效模式
第 1 章 概论
1. 1 什么是FMEA?
FMEA是一种系统分析、强调事实、数据化; FMEA及早地指出根据经验判断出的弱点和可能产 生的缺陷,及其造成的后果和风险,并在运作过程 中采取措施加以消除; FMEA是目前全世界工程界最行之有效的预防手段 ,其准则是 “避免缺陷产生较之以后发现缺陷,而 不得不加以排除,显得更合理,更经济”; FMEA是用于评定风险的一种按优先次序排列的矩 阵工具。
评价PFMEA必须覆盖全过程的流程图/风险开始。
PFMEA是一份动态文件,应在生产开始前、工 装准备前进行。
在产品生产过程可行性分析阶段或之前开始,覆盖自制 件到总装的所有生产工序。对新产品生产过程或修改时进 行早期评审和分析有利于促进预测、解决或监控潜在过程 问题。
PFMEA假定所设计的产品会满足设计要求。
( 过程 FMEA)
项目名称: FMEA 编号: 核心小组
项目
第 页,共 页 ⑶ 编 制 者: ⑺ ⑷
⑴ ⑸
车型年/车辆类型: 关键日期: ⑼
潜在 失效后果 严 重 度 (S) 级 别
⑵
过程责任部门: FMEA 日期(编制):
现行 现行 过程 控制 探测
⑹
修订: ⑻
措施结果(23)
⑽
功能
潜在 失效模式
3.1 PFMEA的准备工作
第3章 PFMEA
PFMEA原则上是产品设计能够满足顾客需要 的。
仅对工艺过程中的潜在失效模式进行分析,不要把 DFMEA的工作拿进来
因此,PFMEA有可能成为设计FMEA中对可制造性 和装配性问题的补充,应该反馈到DFMEA中去。
23
产品设计中DFM、DFA的缺陷可能造成过程 潜在失效模式的发生。
32
第3章 PFMEA
3.3 潜在的失效模式
在产品设计DFMEA中已经分析的失效模式原则上不 需在PFMEA中重复,却需要进行后续的工艺设计, 注意对接DFMEA。
不需包含设计缺陷产生的失效模式。
PFMEA不依靠改变产品设计来克服过程缺陷的。
但它要考虑与计划的制造或装配过程有关的产品设计特 性参数,以便最大限度地保证产品能满足顾客的QCDS 要求。
21
第3章 PFMEA
典型PFMEA目标方向:
加工方法的合理性(选用的加工工艺与产品的质量要求
应相一致) 加工方法的安全性(对人和设备应有保护作用) 安全可靠且稳定的生产工序(工序能力足够,例如重要 工序其工序能力指数CPK≥1.33) 交货保障能力(质量体系和生产工艺) 最广泛的自检(尽可能全面的自检方案和工具) 所有工序控制项目及质量状态是透明的、明确的 维修及排除故障的能力保障 生产工艺变更时的有效管理 22
广义的“顾客”包括:
最终顾客:产品/服务的使用者 直接顾客:下一道工序或用户 中间顾客:下游工序或用户 其他凡是产品/服务受益或受损害者均在广义顾客概念之
中 TMT具体:aoe、qe、模具、供应商、电源、声学、DQA、 售后、系统工作组
16
第 2 章 DFMEA
2.6DFMEA与PFMEA的联系
潜在失效 起因/机理
频度 过程 (O) 控制
⑾
⑿
⒁
⒀
⒂
⒃ 预防 ⒄
探测 度 (D) (18)
风险 顺序数 RPN
建议的措施
责任和目 标完成日期
(19)
(20)
(21)
采取的措施 严重度 频度 探测度 RPN (S) (O) (D) (22)
⒄
第3章 PFMEA
3.1 PFMEA的准备工作
④
(1)项目名称:填入所分析的零件、组件、子系统的过程 名称、编号。 (2)车型年/车辆类型:填入将使用/或正被分析过程影响 的预期的产品及产品类型。 (3)过程责任:填入部件厂组、部门和小组名单。按照生 产部门组织图 还应包括供应商的名称。
在进行PFMEA之前,应先填写好该表格表头的各 项内容,它们是:
(4)编制者:填入负责准备PFMEA工作的工程师 的姓名、电话和所在公司名称。
26
3.1 TCL之PFMEA
第3章 PFMEA
27
第3章 PFMEA
填写流程步骤:工艺工序名称,是指该过程或 工序目的。
按sop统一描述。如果过程涉及到数个操作位(如总装工艺卡 合工序的),应分别把这些工序作为独立的位则列出
5
第 1 章 概论
1. 1 什么是FMEA?
FMEA 与8D(Failure Mode Analysis) 分析 的区别:
• FMEA是一种事前行为; • 8D是一种事后行为;
• 8D报告是进行FMEA的重要的资料。
6
第 1 章 概论
1. 1 什么是FMEA?
FMEA与失效树状图FTA(Failure Tree Analysis)分析的区别:
质量、服务、 供方配套……
11
第 2 章 DFMEA
2.2 什么时候做DFMEA?
DFMEA旨在及早识别出潜在的失效,因此愈
早开始愈好。一般说来,在一个设计概念形成, 设计方案初步确定时应该开始DFMEA初稿的 编制。 随着设计活动的展开,在设计的各个重要阶段, 对DFMEA的初稿进行评审,不断进行修改。 DFMEA作为设计活动的一部分,应该在设计 任务完成(如设计图样完成、过程设计文件完 成)之时完成DFMEA工作。 12