FMEA讲义典型案例运用
FMEA讲义典型案例运用
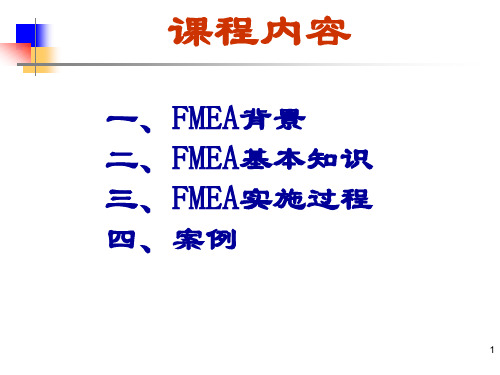
RP N
故 障 等 级
建议事项
负责人
期限
措施内 容
措施结果 S OD
RPN
5
实施FMEA背景
满足顾 客要求
保持竞 争力
减少失 效风险
改进产 品质量
FMEA背景
6
实施FMEA背景
美国用于维修费用的变化趋势
美军50年代,60%~500% 军 用
美军,1959年,25%
2003年,美国企业 美 巨头企业 50家 GM FORD GE
195亿美元 (2.5%) 44亿美元 (2.8%) 35亿美元 (2.5%) 7.4亿美元 (4.5%)
开展可靠性带来了经济利益
FMEA背景 可 靠 性 工 程 产 生 与 发 展
7
实施FMEA背景
FMEA背景
• 所有的制造问题中有80%是由糟糕的设计 引起的。
• 制造停工使英国每年损失470万生产小时。
图(即故障树),确定系统故障原因的各种可能组合方式,计算系统(或过 程 )故障概率,采取相应的纠正措施,以提高系统(或过程)可靠性的一 种设计分析方法。
事件树分析(ETA),是一种逻辑演绎方法,它在给定的一个初因事件的前 提下,分析此初因事件可能导致的各种事件序列的结果,从而可以评价系统 的可靠性与安全性
LOSS COST(大) 评价成本 大
质量成本 大
失败成本 大 预防成本 小
改进方向
采用客户至上的原则,致力于计划中 的事前准备,将问题防止于未然,以图顺畅 生产的高效模型。
假设先行型开发 主动的 QA 防患于未然
● 先期对应管理 - 防患于未然.。 - 真正的原因管理。 - FMEA
- FEED FORWARD(PREACTION)
fmea案例

FMEA案例1. 简介故障模式和效果分析(Failure Mode and Effects Analysis,简称FMEA)是一种通过对系统的故障模式进行分析和评估,以识别和避免潜在故障的方法。
本文将以一个实际案例为例,详细介绍FMEA的过程和应用。
2. 案例背景某公司生产一种新型电子产品,为了确保产品质量和可靠性,决定进行FMEA分析。
在该案例中,我们将关注于产品的电源系统。
3. FMEA分析流程FMEA分析通常包括以下几个步骤:3.1 识别故障模式首先,我们需要识别潜在的故障模式。
在电源系统的例子中,一些可能的故障模式包括过电流、过电压、短路等。
3.2 评估故障后果针对每个故障模式,我们需要评估其对系统的影响。
例如,过电流可能导致电子元件烧毁,过电压可能导致电路板烧毁等。
3.3 评估故障发生的可能性在这一步骤中,我们需要考虑故障发生的可能性。
例如,过电压可能由于不稳定的电源供应而发生。
3.4 计算风险优先级数值通过将故障后果和发生可能性相乘,可以计算出每个故障模式的风险优先级数值。
数值越高,表示该故障模式对系统的影响越大,需要更加重视。
3.5 制定改进计划最后,根据风险优先级数值,我们可以制定改进计划,以减少故障发生的可能性,或者减少故障发生后的影响。
4. 案例应用在电源系统的例子中,我们可以使用FMEA分析来评估不同故障模式的风险并制定相应的改进计划。
4.1 过电流故障模式:发生超过额定电流的情况。
故障后果:可能导致电子元件烧毁,电路板损坏。
故障可能性:由于供电不稳定,过电流的发生可能性较高。
风险优先级数值:故障后果 * 故障可能性 = 高改进计划:加装过电流保护装置,提高电源的稳定性。
4.2 过电压故障模式:发生超过额定电压的情况。
故障后果:可能导致电路板烧毁,系统损坏。
故障可能性:由于电源波动或故障,过电压的发生可能性较高。
风险优先级数值:故障后果 * 故障可能性 = 高改进计划:加装过电压保护装置,提高电源的稳定性。
新版fmea案例

新版fmea案例在一家汽车零部件制造厂中,由于近期发生了多起产品质量问题,导致公司遭受了较大的经济损失和声誉受损,高层管理层意识到必须采取有效的措施来改善产品的质量。
因此,他们决定引入新版FMEA(失效模式与影响分析)方法来提前预防可能的失效模式,并采取相应的措施来减轻损失。
以下是一种新版FMEA方法的案例:首先,公司成立了一个由不同岗位的员工组成的跨部门团队,负责进行新版FMEA分析。
该团队包括设计人员、生产技术人员、品质控制人员以及售后服务人员。
他们共同制定了一个详细的工作计划,包括收集相关数据、分析失效模式和确定相应的控制措施。
团队首先收集了各个部门的历史数据,包括产品质量记录、客户投诉和售后服务的问题反馈。
通过对这些数据的分析,他们确定了几个重要的失效模式,包括产品组装不良、材料使用不当和设备故障等。
接下来,团队进行了详细的失效模式和影响分析。
他们根据每个失效模式的可能性、严重性和检测能力来对它们进行评估。
例如,对于产品组装不良这个失效模式,他们评估了造成客户事故的可能性、产品质量的影响程度以及生产线检测装置的能力。
在评估每个失效模式之后,团队开始制定相应的控制措施。
他们首先关注一些高风险的失效模式,采取主动的控制措施来减轻损失。
例如,对于产品组装不良的失效模式,他们决定增加更为严格的产品组装过程控制和检测步骤,以确保每个产品组装质量的稳定性。
同时,团队还制定了一系列培训计划,以提高员工的技能和意识。
他们认识到单纯的控制措施是不够的,员工的专业技能和操作规范同样重要。
因此,他们组织了一系列培训课程,包括质量控制、产品组装和设备维护等内容,以提高员工的整体素质。
最后,团队设立了一个监控机制,定期对已经实施的控制措施进行检查和评估。
他们收集相关的数据,并根据事故和客户投诉的情况调整控制措施。
这种迭代的过程使得FMEA分析更加灵活和有效。
通过引入新版FMEA方法,该厂成功地改进了产品质量并减少了损失。
FMEA经典案例
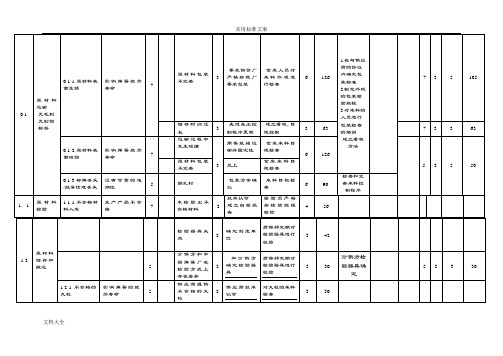
48
5-1抛丸流量不足
弹簧使用寿命降低(早期断裂)
7
丸粒不足
3
-规定丸粒流量并锁定
-丸粒添加程序1次/80min,每次添加25Kg1.2mm丸粒。
-设备报警
1.操作者点检1次/2h
2.QC检查1次/4h
6
126
国产1mm喷丸机加流量报警装置
7
3
3
63
5-2喷丸时间过短
喷丸强度不够
7
1.拨叉速度失控
0.1
原材料运输
-无毛刺
-无划伤
-标签
0.1-1原材料表面生锈
影响弹簧疲劳寿命
7
原材料包装不完善
3
-要求供货厂严格按我厂要求包装
-仓库人员对来料外观进行检查
6
126
1在与供应商的协议内确定包装标准
2制定外观的包装检验规程
3对来料的人员进行包装检查的培训
建立看板方法
7
3
5
105
储存时间过长
3
-先进先出控制程序更新
3
72
6-2压缩次数不符合规范
弹簧长度超差
6
HIC
1.参数调整
2.人员
3
对生产线的调整进行检查
1.操作者自检1次/2h
2.QC检查1次/4h
3
54
6-1几何尺寸超差弹簧流入下道工序
10-1负荷超差,乘客感觉不舒服
6
HIC
长度和圈数不符合规范
3
调整长度
-操作工抽取1/5检查
-检验员4小时检验1次
3
54
-每周重新配置
检查PH值2次/班
5
90
加作业指导书关于表调液的调整方法
质量故障模式与影响分析(FMEA)在质量改进中的应用案例
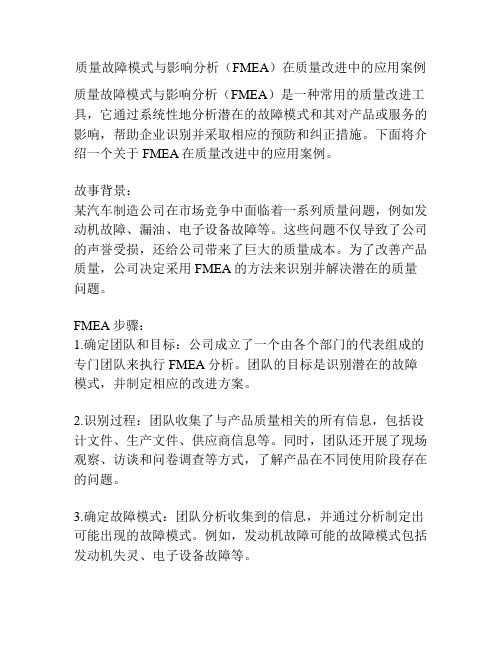
质量故障模式与影响分析(FMEA)在质量改进中的应用案例质量故障模式与影响分析(FMEA)是一种常用的质量改进工具,它通过系统性地分析潜在的故障模式和其对产品或服务的影响,帮助企业识别并采取相应的预防和纠正措施。
下面将介绍一个关于FMEA在质量改进中的应用案例。
故事背景:某汽车制造公司在市场竞争中面临着一系列质量问题,例如发动机故障、漏油、电子设备故障等。
这些问题不仅导致了公司的声誉受损,还给公司带来了巨大的质量成本。
为了改善产品质量,公司决定采用FMEA的方法来识别并解决潜在的质量问题。
FMEA步骤:1.确定团队和目标:公司成立了一个由各个部门的代表组成的专门团队来执行FMEA分析。
团队的目标是识别潜在的故障模式,并制定相应的改进方案。
2.识别过程:团队收集了与产品质量相关的所有信息,包括设计文件、生产文件、供应商信息等。
同时,团队还开展了现场观察、访谈和问卷调查等方式,了解产品在不同使用阶段存在的问题。
3.确定故障模式:团队分析收集到的信息,并通过分析制定出可能出现的故障模式。
例如,发动机故障可能的故障模式包括发动机失灵、电子设备故障等。
4.确定影响:团队评估每个故障模式对产品质量和客户满意度的影响程度。
例如,发动机故障会导致车辆停机,严重影响客户满意度。
5.确定原因:团队分析每个故障模式产生的原因,并列出可能的原因。
例如,发动机故障的原因可能是设计缺陷、生产工艺问题或供应商质量不稳定。
6.确定控制措施:团队制定针对每个故障模式的控制措施,以降低故障发生的可能性或减轻故障对产品的影响。
例如,针对发动机故障,可以加强设计验证、改进生产工艺和加强供应商质量管理等。
7.实施改进:团队将制定的控制措施落实到实际操作中,包括调整设计、改进生产工艺和提高供应商管理等。
同时,团队也要设立有效的跟踪和监控机制,以确保改进方案的有效性。
改进效果:通过FMEA的分析,该汽车制造公司发现了多个潜在的质量问题,并制定了相应的改进措施。
FMEA详解及其案例分析

过程FMEA是一个动态的文件: 1.应在可行性论证阶段或之前开始; 2.在生产用治工具到位之前起动; 3.考虑到从单个部件到总成的所有的制造操作; 包括工厂内所有可能影响制造和装配的操作过程,例如:发
议 措 施
D
责任 及目 标完 成日 期
措施结果
采取 的措 施
S ODR P N
预防: 消除(预防)失效的要因的发生或失效模式的发生,降低发生率。
探测: (DFMEA)在项目放行到生产前,通过解析方法或物理方法识别(探测)要因,失效的 机理或失效模式是否存在。
(PFMEA)识别(探测)失效的要因的发生或失效模式,以导致相关纠正措施或防范措 施的开发。
能做些什么?
-- 设计更改 -- 过程更改 -- 特别控制(SPC,全检) -- 标准、程序或指南的更改 -- 导入防呆措施 -- 加强设备保养 -- 加强参数控制 -- 加强工作技能
如何 探测?
探测 难易度?
再评价, 风险是否 降低?
变化
项目/ 潜在失 潜在 严 级 潜在 发 现行控制
过程
效模式 失效 后果
风险举例说明 钣金冲压工厂 特点:长期、猛烈的冲击振动
频繁的振动
连接处松动
泄漏
油滴到地面上
地面积油 人员摔伤 上告、索赔
根源模式 中间模式 最终模式
风险的描述:
•风险的后果(危害)有多严重?
•风险发生的可能性有多大?
•是否能提前发现风险?
风险的控制:
•风险的后果(危害)有多严重?
降低后果(危害)的影响程度:提高自身“健状度”,增强风 险承受能力。
FMEA讲义典型案例运用2017

用
$1000
$100
$10 $1
概念阶段 计划阶段 设计阶段
验证阶段 生产制 造
市场召回
故障及事 故的赔偿
公司形象 损失
变更处理费用的10倍法则
11
开发阶段的问题点 – 质量问题的发生要因
FMEA背景
在整体质量问题发生的内容中,其根本原因为设计时没有充分考虑顾客与制造环境的质 量问题发生最多。
FMEA,已成为美国航天、国际汽车等行业的强制使用的分析方法。
故障模式分析
4
FMEA背景
何谓 FMEA (Failure Mode & Effects Analysis)
以系统(产品)以及工序、设备等的构成要素为对象. 利用所谓的“故障模式(Failure Mode)”思考方式. 事先排除可能出现的问题. 通过故障的原因和影响说明问题的重要性. 连接设计(工艺)的手法.
• 对于许多制造过程,缺陷产品仍然以百分 数来测量,而不是以百万件中缺陷产品数 来测量。
8
开发阶段的 问题点 – 开发日程和设计变更件数
FMEA背景
统计表明,设计变更集中在开发后半段,批量生产以后还有大量变更.
设计 变更件数
过去
目标
开发日程和设计变更件数
时间
9
FMEA 的起源与发展
FMEA背景
195亿美元 (2.5%) 44亿美元 (2.8%) 35亿美元 (2.5%) 7.4亿美元 (4.5%)
开展可靠性带来了经济利益
FMEA背景 可 靠 性 工 程 产 生 与 发 展
7
实施FMEA背景
FMEA背景
• 所有的制造问题中有80%是由糟糕的设计 引起的。
FMEA案例范文

FMEA案例范文FMEA即故障模式与影响分析(Failure Mode and Effects Analysis)是一种系统的方法,用于识别和评估系统或过程中可能存在的潜在故障和其可能的影响。
它将系统的故障模式进行分类,以评估它们对系统的安全性、可靠性和性能的影响程度,并提出针对这些故障模式的改善措施。
以下是一个FMEA案例分析,旨在说明FMEA的方法和应用。
案例分析:电子产品生产厂家正在设计一款新的电子产品。
该电子产品是一种智能家居控制系统,用于远程控制家庭设备。
该控制系统具有触摸屏界面,可以通过无线网络连接到用户的手机或平板电脑上进行远程操作。
工程团队开展FMEA分析,以评估该系统可能存在的潜在故障和影响,并制定相应的改善措施。
1.选择团队成员并确定范围:工程团队成员包括设计工程师、软件工程师、生产工程师和测试工程师。
确定分析的范围是该控制系统的硬件及软件部分。
2.识别故障模式:团队成员在会议中一起讨论并记录可能发生的故障模式。
例如,电源故障、触摸屏失灵、网络连接问题、界面操作误解等。
3.评估故障模式的严重性:每个故障模式都被团队成员分别评估其对系统的严重性。
使用1-10的评分标准,10表示最严重。
例如,电源故障的严重性得分为9,因为它可能导致整个系统无法正常工作。
4.识别潜在故障原因:团队成员根据经验和专业知识,识别导致每个故障模式发生的潜在原因。
例如,电源故障可能由于电源适配器质量不良、电源电路设计缺陷等原因导致。
5.评估故障影响:判断每个故障模式的潜在影响,并使用1-10的评分标准进行评估。
例如,触摸屏失灵的影响为8,因为它会使用户无法操作控制系统。
6.识别控制措施:团队成员讨论并提出相应的控制措施,以减少故障的发生和影响。
例如,为电源设计备用电源或采用更可靠的电源适配器,以降低电源故障发生的概率。
7.评估控制措施的效果:评估每个控制措施的实施效果,并分配评分。
例如,备用电源对电源故障的影响较小,评分为78.重新评估故障严重性:在实施控制措施后,对故障严重性进行重新评估。
- 1、下载文档前请自行甄别文档内容的完整性,平台不提供额外的编辑、内容补充、找答案等附加服务。
- 2、"仅部分预览"的文档,不可在线预览部分如存在完整性等问题,可反馈申请退款(可完整预览的文档不适用该条件!)。
- 3、如文档侵犯您的权益,请联系客服反馈,我们会尽快为您处理(人工客服工作时间:9:00-18:30)。
$1000
$100
$10 $1
概念阶段 计划阶段 设计阶段
验证阶段 生的赔偿
公司形象 损失
变更处理费用的10倍法则
11
开发阶段的问题点 – 质量问题的发生要因
FMEA背景
在整体质量问题发生的内容中,其根本原因为设计时没有充分考虑顾客与制造环境的质 量问题发生最多。
质量问题发生分类
故障模式预测 故障的原因和影响解析 评价问题的重要程度
设计(工艺)改进
对象型号 解析水平/ 整体水平 影响解析范围
设计 FMEA
作成日期: 实施负责人 : 参与者 :
Page FM EA No.
No. 构成部件
机能
故障模式
深 故障的影响 刻
度
故障的原因
发 生 频 度
现 设计管理 预防 检出
探 测 度
FMEA,已成为美国航天、国际汽车等行业的强制使用的分析方法。
故障模式分析
4
FMEA背景
何谓 FMEA (Failure Mode & Effects Analysis)
以系统(产品)以及工序、设备等的构成要素为对象. 利用所谓的“故障模式(Failure Mode)”思考方式. 事先排除可能出现的问题. 通过故障的原因和影响说明问题的重要性. 连接设计(工艺)的手法.
12
从 被动(后发管理)到主动(先期管理)的转变
FMEA背景
现有方式
按照被称作高度成长期遗留物的落后 对应型,树立计划并实施,事后处理已发 生的问题,是高损失成本的模型。
事后解决问题型开发 被动的 QA 防止再发生
● 落后对应管理 - 事后管理 - 现象管理 - QC 7种工具 - FEED BACK
故障(或失效)模式
2
失效分析
FMEA背景
失效分析就是分析、寻找系及其组成部分的失效原因(失 效机理、故障机理、诱发失效的因素等),从而提出补救 和预防、纠正措施
3
常用失效分析方法
FMEA背景
仪器设备测试法(因果图法、直方图法、主次图法)
FMEA FTA:通过对可能造成系统(或过程)故障的各种因素进行分析,画出逻辑
195亿美元 (2.5%) 44亿美元 (2.8%) 35亿美元 (2.5%) 7.4亿美元 (4.5%)
开展可靠性带来了经济利益
FMEA背景 可 靠 性 工 程 产 生 与 发 展
7
实施FMEA背景
FMEA背景
• 所有的制造问题中有80%是由糟糕的设计 引起的。
• 制造停工使英国每年损失470万生产小时。
• 对于许多制造过程,缺陷产品仍然以百分 数来测量,而不是以百万件中缺陷产品数 来测量。
8
开发阶段的 问题点 – 开发日程和设计变更件数
FMEA背景
统计表明,设计变更集中在开发后半段,批量生产以后还有大量变更.
设计 变更件数
过去
目标
开发日程和设计变更件数
时间
9
FMEA 的起源与发展
FMEA背景
FMEA 的起源与发展(美国)
LOSS COST(大) 评价成本 大
质量成本 大
失败成本 大 预防成本 小
改进方向
采用客户至上的原则,致力于计划中 的事前准备,将问题防止于未然,以图顺畅 生产的高效模型。
假设先行型开发 主动的 QA 防患于未然
● 先期对应管理 - 防患于未然.。 - 真正的原因管理。 - FMEA
- FEED FORWARD(PREACTION)
RP N
故 障 等 级
建议事项
负责人
期限
措施内 容
措施结果 S OD
RPN
5
实施FMEA背景
满足顾 客要求
保持竞 争力
减少失 效风险
改进产 品质量
FMEA背景
6
实施FMEA背景
美国用于维修费用的变化趋势
美军50年代,60%~500% 军 用
美军,1959年,25%
2003年,美国企业 美 巨头企业 50家 GM FORD GE
FMEA的起源与发展 (日本)
1970年代初 日本科學技術聯盟 NASDA (日本宇宙開發事業團) 引进 在民用产业迅速普及
- 宇宙航空、汽车、电气·电子、机械、软件等所有产业领域 10
事后处理的费用法则
FMEA背景
()
$10000000
变
$1000000
更
修
$100000
定
$10000
费
用
课程内容
一、FMEA背景 二、FMEA基本知识 三、FMEA实施过程 四、案例
1
故障(失效)的概念
FMEA背景
产品在规定条件下, (环境、操作、时间)不能完成既定功 能。(事例)
在规定条件下, 产品参数值不能维持在规定的上下限之 间(事例)
产品在工作范围内, 导致零组件的破裂、断裂、卡死、 损坏现象(短路、开路、过度损耗等)(事例)
50年代:格鲁曼公司开发了FMEA,用于飞机发动机故障防范; 70年代:海军制定了FMEA标准, 1976年,美国国防部采纳了FMEA标准; 80年代:汽车工业和微电子工业应用FMEA 90年代:ISO9000推荐采用FMEA; 1994,FMEA成为QS-9000认证要求。21世纪:??????????? 军工产业,宇宙开发领域 可靠性、安全性评价工具
经济性(大) 评价成本 小
质量成本 小
失败成本 小 预防成本 大
13
FMEA 的引进背景与实施目的
FMEA 的引进背景
『防止再发生』 ⇒ 『防患于未然』事故的转变 随系统的高度化、负责华而产生的事前解析的重要性增大 随开发时间的短缩而发生的问题最小化 PL(Product Liability)法的 有效地对应
问题发生要因
对应方案
设计要因
48%
制造要因
31%
外包质量
21%
• 设计上没有充分把握顾客的 要求事项
• 设计上没有考虑制造能力
• 开发质量保证的技能不足 与 执行能力微弱
开发阶段中的源流性 质量确保 (源流管理)
顾客要求的明确化 规格/设计的 优化 开发业务的效率化
资料 : 1996年 日本的 某 汽车企业分析资料
图(即故障树),确定系统故障原因的各种可能组合方式,计算系统(或过 程 )故障概率,采取相应的纠正措施,以提高系统(或过程)可靠性的一 种设计分析方法。 事件树分析(ETA),是一种逻辑演绎方法,它在给定的一个初因事件的前 提下,分析此初因事件可能导致的各种事件序列的结果,从而可以评价系统 的可靠性与安全性 FMEA、FTA是常被用到的重要的失效分析方法,应用也相当广泛。特别是
FMEA 的实施目的
提前防止故障发生. ▷ 防止丧失解决故障的机会. ▷ 防止发生问题的巨额解决费用.