EN 12680-2-2003 中文版 锻造超声波检验.第2部分高应力零部件用钢铸件
BS_EN_12668-1-2000中文版_无损检验[1].超声波检验设备的表征和验证.仪器
![BS_EN_12668-1-2000中文版_无损检验[1].超声波检验设备的表征和验证.仪器](https://img.taocdn.com/s3/m/9da8ee1c14791711cc7917c1.png)
2.参考标准 说明略
EN 1330-4:2000 无损检测-术语 第四部分 超声检测术语 EN 12668-3:2000 无损检测-超声检验设备的表征及验证-第三部分 组合设备 EN ISO 9001 质量体系 设计/开发 生产 安装与服务的质量保证模式 ISO 9001:1994 EN ISO 9002 质量体系 生产 安装与服务的质量保证模式 ISO 9002:1994
欧洲标准 EN 12668-1 2000 年 9 月 无损检测-超声检查设备的表征及验证-仪器
本文件规范了脉冲式 模拟式和数字式的 A 显示手动无损检测用超声波检验装置电气性能 的评定方法和验收标准 关键词 无损检测 超声检测 试验装置 规范 性能评定 试验 一致性试验 可接受 性
适合于某些超声仪器的 可用于校正反射振幅随距离减少的时间相关或扫描增益功能 3.31 窄脉冲 short pulse 脉冲幅度超过最大峰值振幅一半 时间间隔小于 1.5 周期的未整流脉冲 3.32 抑制 suppression 优先抑制接近屏幕基线的信号 有意除去草状回波和噪声或者使大回波的后沿变陡峭 3.33 开关滞后 switching hysteresis 接通和关断监视器闸门情况下 信号之间的振幅差异
EN_12681:2003(E)铸造-射线检验

英国标准BS EN12681:2003 铸造-射线检验欧洲标准EN 12681:2003和英国标准具有同等效力ICS 77.040.20未得到BSI许可不允许复制,除非版权法允许这么做BSI英国标准版权归欧洲标准化委员会所有星期三12月31日10:58:58 2003国家前言本英国标准是EN 12681:2003的官方英文版本。
英国政府委托铸造工艺技术委员会ISE/NFE/9参与本标准的制订工作,其职责如下:—帮助有疑问的人员理解标准文本;—向国际/欧洲有关委员会提交关于解释、或修改建议的询问,并向英国有关方面照会/反馈信息;—追踪国际及欧洲在相关方面的发展并在英国发布这些信息。
可向委员会秘书索取代表该委员会的组织机构名单。
交叉参考可以在名为“国际标准通信索引”部分下的BSI目录或使用BSI电子目录“搜索”工具或使用英国标准在线“搜索”工具找到本文件中参考的执行国际或欧洲出版标准的英国标准。
本标准不打算涵盖一份合同的所有必要条款。
使用者对标准的正确应用负责。
与英国标准相符并不意味其具有法律责任豁免权。
2003年2月4日本英国标准经标准政策和战略委员会授权发布页码概要本文件包括封面、封面内页、EN扉页、2~22页、封底内页和封底。
发布新标准时要在标准中简要说明BSI版权日期。
© BSI 4 Feb 2003 ISBN 0 580 41201 6欧洲标准EN 126812003年1月ICS 77.040.20英文版铸造-射线检验本欧洲标准于2002年11月21日由CEN批准。
CEN成员必须遵守CEN/CENELEC内部规程,在此法规下规定了一些条件,对于本欧洲标准应无任何改变地给出国家标准的地位。
在中央秘书处或任何CEN成员处可获得应用这些国家标准的最新状态列表及参考目录。
本欧洲标准有三种官方正式版本(英文,法文,德文)。
由某个CEN成员在其职责范围内将某一版本通过翻译转换成本地语言,并通知中央秘书处后,则该译本与官方正式版本具有同等效力。
EN 12680-3-2003 锻造.超声波检验.第3部分球墨铸铁铸件(中文版)

Feature
Unit
1
2
Severity level
3
4
5
Wall thickness, in the examined area
mm
—
<50 50 to 200
Percentage of wall thickness
%
—
20
Largest discontinuity in the rim zonea,b
5
> 100 to 250
8
> 250 to 500
10
铸件探伤区域的壁厚(mm) > 10 to 20 > 20 to 100
> 100 to 250 > 250 to 500
表3 —超探适用性要求
可探最小平底孔直径(见5.2) 3 5 8 10
Table 4 — Ultrasonic indications to be evaluated
Evaluation limits
Wall thickness of the casting in the examined area
(mm)
reduction of backwall echo
min (dB)
smallest flat-bottom hole diameter detectable
mm2
C
600
1000
Largest discontinuity in the core zone
mm2
C
10000 15000
Total area of
discontinuities as percentage of
%
EN 12680-3

○在未得到德国标准委员会许可之前,不得对本标准的任何部分进行复制。
德国柏林10772 Beuth Verlag股份有限公司拥有对德国标准销售的独家代理权。
参照号:DIN EN 12680-3 : 2003-06销售编号:111110.03欧洲标准EN 12680-32003年1月ICS 77.040.22英文版铸造—超声检测第3部分:球墨铸铁件该欧洲标准由CEN于2002年11月21日批准。
CEN完全遵守CEN/CENELEC内部条例,没有做任何修改和调整,这些条例规定了使该欧洲标准成为国家标准的所需条件。
通过向管理中心或者任何CEN成员进行申请,可以获得与此类欧洲标准相关的最新清单和文献资料。
欧洲标准有英语、法语和德语三种官方版本。
如果CEN成员负责将其翻译成其本国语言,并通知管理中心,该译本与官方版本拥有同样地位。
CEN成员为各国标准团体,包括澳大利亚,比利时,捷克共和国,丹麦,芬兰,法国,德国,希腊,匈牙利,冰岛,爱尔兰,意大利,卢森堡,马耳他,荷兰,挪威,葡萄牙,斯洛伐克,西班牙,瑞典,瑞士和英国。
CEN欧洲标准委员会参照号:EN 12680-3 : 2003 E ○c2003. CEN –CEN各成员国保留在世界范围内以任何形式和任何方法对本标准进行宣传和开发的权利。
目录前言 (2)1. 适用范围 (3)2. 规范性引用文件 (3)3. 术语和定义 (3)4. 要求 (4)4.1 订购信息 (4)4.2 检测范围 (4)4.3 容许的最大瑕疵 (4)4.4 人员资质 (4)4.5 铸件壁剖面分区 (4)5. 检验方法 (5)5.1 原则 (5)5.2 材料 (5)5.3 设备,耦合媒质,校准及灵敏度 (5)5.4 铸件表面检测准备 (8)5.5 检测步骤 (8)5.6 检测报告 (10)参考资料 (17)前言本文件(EN 12680-3 : 2003)由CEN/TC 190欧洲铸造技术标准化委员会编写,该委员会的秘书处由DIN控制并管理。
BS-EN-12680-3-2003中文版--铸件-超声检测-第3部分-球墨铸铁件
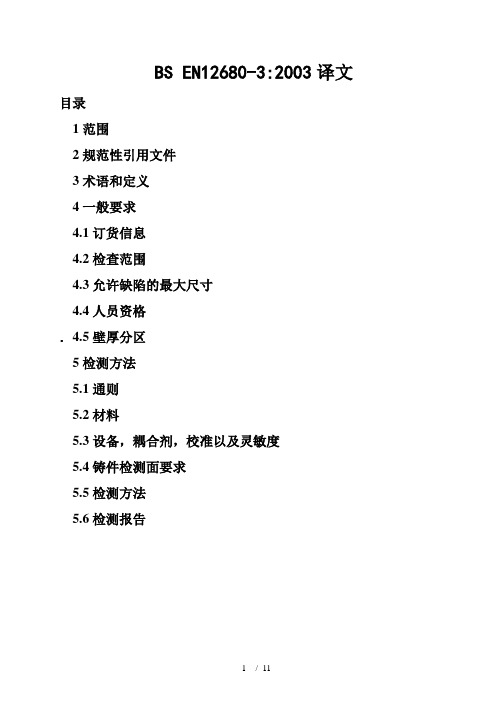
BS EN12680-3:2003译文目录1范围2规范性引用文件3术语和定义4一般要求4.1订货信息4.2检查范围4.3允许缺陷的最大尺寸4.4人员资格.4.5壁厚分区5检测方法5.1通则5.2材料5.3设备,耦合剂,校准以及灵敏度5.4铸件检测面要求5.5检测方法5.6检测报告铸件超声检测第3部分:球墨铸铁件1 范围本标准适用于应用脉冲反射法检测球墨铸铁件内部缺陷的方法。
本标准不涉及球墨铸铁球化率的超声检测。
本标准不包含穿透法。
注穿透法对球墨铸铁中缺陷的检测不敏感,仅在特殊的情况下使用。
(译者注:穿透法主要用于形状适合的如板,片材,高衰减材料,薄壁件等。
)2规范性引用文件本标准在正文中引用了标注或未标注日期的下列相关标准。
凡标注日期的引用标准,其随后所有的修订或改版均不适用于本标准,除非在新版本也包括相应的内容(译者注:应不包括勘误的内容)。
凡是不注日期的引用文件,其最新版本适用于本标准(包括修订)。
EN 583 -1.无损检测—超声检测—第一部分:一般要求EN 583 -2,无损检测—超声检测—第二部分:灵敏度和范围设定EN 583 -3.无损检测—超声检测—第三部分:穿透法EN 583 -5.无损检测一超声检测一第五部分;不连续的特征和尺寸EN 1330 -4.无损检测—术语—第四部分:超声检测术语EN 12223.无损检测—超声检测—NO.1标准试块的规格EN 12668 -1.无损检测—超声检测设备的特性和验证—第1部分:仪器EN 12668 -2,无损检测—超声检测设备的特性和验证—第2部分:探头EN 12668 -3.无损检测—超声检测设备的特性和验证—第3部分:组合设备EN 27963,钢焊缝—超声焊缝检测用NO.2标准试块(IS0 7963: 1985)。
注参考书目中列举了在编制本标准时使用了参考文件,这些参考文件引用在本标准适当位置。
3术语和定义本标准中的术语和定义符合EN1330-4的规定.4一般要求4.1 订货信息使用本标准时,供需双方必须规定下面内容(也可参见EN 583 -1):---铸件的检测区域、数量或比例。
BSEN12680-3-2003中文版铸件-超声检测-第3部分-球墨铸铁件

BSEN12680-3-2003中文版铸件-超声检测-第3部分-球墨铸铁件BS EN12680-3:2003译文目录1范围2规范性引用文件3术语和定义4一般要求4.1订货信息4.2检查范围4.3允许缺陷的最大尺寸4.4人员资格.4.5壁厚分区5检测方法5.1通则5.2材料5.3设备,耦合剂,校准以及灵敏度5.4铸件检测面要求5.5检测方法5.6检测报告铸件超声检测第3部分:球墨铸铁件1 范围本标准适用于应用脉冲反射法检测球墨铸铁件内部缺陷的方法。
本标准不涉及球墨铸铁球化率的超声检测。
本标准不包含穿透法。
注穿透法对球墨铸铁中缺陷的检测不敏感,仅在特殊的情况下使用。
(译者注:穿透法主要用于形状适合的如板,片材,高衰减材料,薄壁件等。
)2规范性引用文件本标准在正文中引用了标注或未标注日期的下列相关标准。
凡标注日期的引用标准,其随后所有的修订或改版均不适用于本标准,除非在新版本也包括相应的内容(译者注:应不包括勘误的内容)。
凡是不注日期的引用文件,其最新版本适用于本标准(包括修订)。
EN 583 -1.无损检测—超声检测—第一部分:一般要求EN 583 -2,无损检测—超声检测—第二部分:灵敏度和范围设定EN 583 -3.无损检测—超声检测—第三部分:穿透法EN 583 -5.无损检测一超声检测一第五部分;不连续的特征和尺寸EN 1330 -4.无损检测—术语—第四部分:超声检测术语EN 12223.无损检测—超声检测—NO.1标准试块的规格EN 12668 -1.无损检测—超声检测设备的特性和验证—第1部分:仪器EN 12668 -2,无损检测—超声检测设备的特性和验证—第2部分:探头EN 12668 -3.无损检测—超声检测设备的特性和验证—第3部分:组合设备EN 27963,钢焊缝—超声焊缝检测用NO.2标准试块(IS0 7963: 1985)。
注参考书目中列举了在编制本标准时使用了参考文件,这些参考文件引用在本标准适当位置。
en10028-2-2003

0.012 1.15
0.30 0.60
_
_
13CrMoSi5-5
1.7336 ≤ 017
0.50- 0.400.80 0.65
≤
≤
e
0.015 0.005
≤
1.00- ≤
0.45-
_
≤
_
0.012 1.50
0.30 0.65
0.30
10CrMo9-10
1.7380 0.08- ≤
0.40- ≤
≤
e
≤
403
前言
本文件是由 ECISS/TC22“承压用钢—品种”技术委员会制订的,其秘书长由 DIN 担任。
本欧洲标准应最迟在 2003 年 12 月以相同文本出版物或认可的形式赋予国家标准的 地位,与之相冲突的国家标准最迟应于 2003 年 12 月取消。
本文件代替 EN10028-2:1992(1993) 本文件是根据欧洲委员会和欧洲自由贸易联合会的授权而制订的,它支持相应的欧 共体(EU)指令的基本要求。 与 EU 指令的关系,见资料性附录 ZA,这是本文件的组成部分。 本欧洲标准包括下列部分,总题目是“承压用扁平钢产品”: 第一部分:一般要求 第二部分:具有规定高温性能的非合金钢和合金钢 第三部分:正火的可焊接细晶粒钢 第四部分:具有规定低温性能的镍合金钢 第五部分:温度形变轧制(TMCP)的可焊接细晶粒钢 第六部分:淬火和回火的可焊接细晶粒钢 第七部分:不锈钢 注意:用两个点(●●)标记的条款包含有在询问和订货时可以协商的信息。 附录 A,A,C 仅供参考。附录 D 和 E 为标准性附录。 本文件包括一份参考文献目录。 根据 CEN/CENELEC 的内部规定,以下国家的国家标准组织有义务执行本欧洲标 准:奥地利,比利时,捷克,丹麦,芬兰,法国,德国,希腊,匈牙利,冰岛,爱尔兰, 意大利,卢森堡,马耳他,荷兰,挪威,葡萄牙,斯洛伐克,西班牙,瑞典,瑞士以及 英国。
大型铸件超声波检测工艺控制
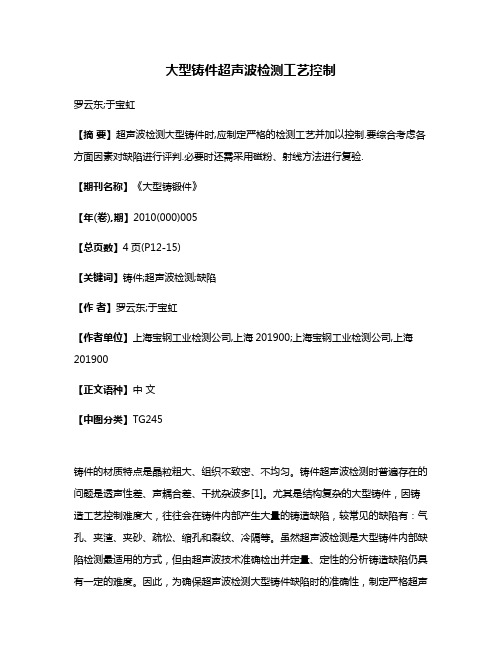
大型铸件超声波检测工艺控制罗云东;于宝虹【摘要】超声波检测大型铸件时,应制定严格的检测工艺并加以控制.要综合考虑各方面因素对缺陷进行评判.必要时还需采用磁粉、射线方法进行复验.【期刊名称】《大型铸锻件》【年(卷),期】2010(000)005【总页数】4页(P12-15)【关键词】铸件;超声波检测;缺陷【作者】罗云东;于宝虹【作者单位】上海宝钢工业检测公司,上海201900;上海宝钢工业检测公司,上海201900【正文语种】中文【中图分类】TG245铸件的材质特点是晶粒粗大、组织不致密、不均匀。
铸件超声波检测时普遍存在的问题是透声性差、声耦合差、干扰杂波多[1]。
尤其是结构复杂的大型铸件,因铸造工艺控制难度大,往往会在铸件内部产生大量的铸造缺陷,较常见的缺陷有:气孔、夹渣、夹砂、疏松、缩孔和裂纹、冷隔等。
虽然超声波检测是大型铸件内部缺陷检测最适用的方式,但由超声波技术准确检出并定量、定性的分析铸造缺陷仍具有一定的难度。
因此,为确保超声波检测大型铸件缺陷时的准确性,制定严格超声波检测工艺并进行控制是至关重要的。
1 铸件超声波检测的技术准备1.1 了解被检测对象进行超声波检测前,首先要全面了解被检测的铸件情况。
通过查看图纸、现场检查及委托方对项目的介绍等方式明确检测铸件的材质、结构特征、浇铸方式、冒口位置分布、工件摆放的形式、可接触到的检测面、工件各部位的厚度尺寸、表面状况以热处理状况、修复情况及工件的加工余量等。
这些情况对于超声波检测工艺参数的选取、检测工艺的制定及检测波型的分析、缺陷的定性等具有非常重要的意义。
此外还需要了解超声波检测铸件的制造进度,以便在合适的检测节点和环境进行检测,以免错过最合适的检测环境。
1.2 明确超声波检测技术要求超声波检测技术要求是编制超声波检测方案及实施超声波检测的依据。
铸件的设计图纸一般会明确规定超声波检测扫查面、依据的标准及验收规范或技术条件。
在超声波检测实施前,检测人员应充分地了解相关标准及规范内容,明确超声波检测关键参数的选择原则,尤其明确超声波检测频率、探头、灵敏度调节、缺陷定量方式、判定依据等主要规定。
- 1、下载文档前请自行甄别文档内容的完整性,平台不提供额外的编辑、内容补充、找答案等附加服务。
- 2、"仅部分预览"的文档,不可在线预览部分如存在完整性等问题,可反馈申请退款(可完整预览的文档不适用该条件!)。
- 3、如文档侵犯您的权益,请联系客服反馈,我们会尽快为您处理(人工客服工作时间:9:00-18:30)。
EN 12680-2-2003(E)-CN铸件---超声检测---第二部分:受高压铸钢件前言:本欧洲标准由德国工业标准秘书处的CEN/TC 190“铸件”技术委员会制定,本欧洲标准可以作为国家标准,最迟于2003年6月以等效版本或签署文件发行,与之冲突的相关国家标准最迟在2003年6月作废。
根据工作程序,CEN/TC 190技术委员会组织CEN/TC 190/WG4.10“内部缺陷”具体编制了如下标准:EN 12680-2铸件---超声检测---第二部分:受高压铸钢件本标准为欧洲铸件检测标准之一,其余见下:EN 12680-1铸件---超声检测---第一部分:通用铸钢件EN 12680-1铸件---超声检测---第三部分:球墨铸铁件附件A和B根据CEN/CENELEC内部规定如下国家的国家标准组织应采用此欧洲标准:澳大利亚,比利时,捷克共和国,丹麦,芬兰,法国,德国,希腊,冰岛,爱尔兰,意大利,卢森堡,新西兰,挪威,葡萄牙,西班牙,瑞典,瑞士和英国。
1.总则本欧洲标准规定了受高压的(铁素体)铸钢件超声检测的目的和要求以及用脉冲回波技术测定内部不连续的方法。
其适用于晶粒细化后的壁厚小于等于600mm的铸钢件超声检测,当壁厚超过此时,对于检测工艺和记录级别应特殊协商。
本欧洲标准不适用奥氏体刚和焊接件。
2 参考文件本部分在其中适当的位置引用了下列的有发布日期和无发布日期的标准,对于无发布日期的标准采用的为最新版本,对于有发布日期的标准根据随后对标准的修订和更新来相应修改本标准。
EN 583—1超声检测—第一部分:通用原理EN 583—2超声检测-第二部分:灵敏度和范围调整EN 583—5超声检测—第五部分:不连续的测长和特征EN 12223 超声检测—1号校准试块规范EN 12668-1 无损检测—超声设备的特征和验证—第一部分:仪器EN 12668-2 无损检测—超声设备的特征和验证—第二部分:探头EN 12668-3 无损检测—超声设备的特征和验证—第三部分组合设备EN 27963 钢焊缝—焊缝超声检测用2号校准试块3.术语和定义本欧洲标准规定如下术语和定义注:本标准中的其它术语和定义见EN 583—1,EN 583—2,EN 583—5和EN1330—43.1参考不连续回波尺寸在超声检测评价时期需要记录的最小显示,通常用平底孔当量直径来表示3.2点状不连续尺寸小于或等于声束宽度的不连续3.3复杂不连续尺寸大于声束宽度的不连续注: 本标准中的尺寸指长度,宽度和沿壁厚方向的尺寸3.4 平面不连续在两个方向可以测量的不连续3.5体积不连续有三个方向可以测量的不连续3.6特殊边缘区域有特殊要求的外部边缘区域(如:机加工面,高应力区,和密封面)3.7工艺焊接在最终供货前加工时期的焊接3.7.1焊接用于将部件装配为一个整体的工艺焊接3.7.2焊接加工为保证铸件的质量等级而实施的工艺焊接4.要求4.1订货信息在订货和询价时应包括如下的信息-超声检测的铸件的区域和百分比(检测体积和范围)-铸件不同区域或面积处采用的严重等级(验收标准)-书面检查工艺的要求-是否需要对检测工艺增加要求,同样见5.5.14.2检测范围应采用最合适的检测技术对铸件协商的所有区域进行检测(从铸件的形状考虑尽量满足),对于壁厚超过600mm的铸件,应对检测工艺和记录和验收级别协商一致。
4.3不连续允许的最大尺寸4.3.1总则购货方应该根据规定的铸件检测范围内每个区域要求的平面和体积不连续的严重等级来确定验收等级。
壁厚按照图2根据铸件待装配时(精加工)的尺寸进行分类。
4.3.2无可测量尺寸的指示在特殊边缘区域和需焊接的部位,无可测量尺寸的指示的极限用可允许的指示的最大数量来衡量,该极限见于表1不能超过表中所示的值。
4.3.3有可测量尺寸的指示4.3.3.1平面型指示平面型不连续不能超过表1中的极限,对于长度可测量而沿壁厚尺寸无法测量的指示的面积的计算按照图2给出的公式进行计算。
小平面不连续的测长见图2,且随着声程和声束直径的增加,测长变得困难。
作为指导对边缘区域30mm厚度内进行测长,需要采用双晶聚焦探头。
4.3.3.2体积不连续体积不连续边缘区域不能超过图3给出的尺寸,心部区域不能超过图4给出的尺寸。
严重等级1级不允许有可测量尺寸的指示。
长度可测而宽度不可测的指示的面积计算按照图3图3给出的公式进行计算。
4.4人员资格推荐符合EN 473要求的有资质和水平的人员进行超声检测4.5壁厚的划分壁厚按照图2根据铸件待装配时(精加工)的尺寸进行分类4.6严重等级如果购方在同一铸件的不同区域规定了不同的严重等级,所有区域应在购方图纸清楚的注明并应包括:---所有关于本区域位置的必须尺寸---所有焊接区域范围及特殊区域的厚度严重等级1只适用于需要焊接区域和特殊边缘区域,除非在确认订货时,对焊接加工应使木材满足要求。
5.检测5.1原理超声检测的原理见EN 583-1 EN 583-2 EN 583-5。
5.2材料材料的超声可探性通过将参考反射体波高(通常为一次底波)和噪声信号相比来评定,评定应在整个厚度范围内且能代表工件表面状态的区域进行,评定区域应有较平的平面。
参考回波应至少比噪声信号高6dB。
当工件底面处最小平底孔或当量的长横孔直径比噪声信号低dB时超声可探性较差。
这时应在报告中记录信噪比大于等于6 dB的平底孔或长横孔直径,而且增加的检测工艺应有工序上方协商一致。
注:为很好的评定平底孔尺寸大小,可以采用DGS法或与工件同厚度同热处理同材料带有按照表2规定直径的平底孔的试块或同等的长横孔试块,下式可用于长横孔和平底孔之间的转换:DQ=4935×D FBH4/λ2×s此处:DQ:长横孔直径mm D FBH:平底孔直径mm λ:波长mm s:声程mm本公式适用于DQ≥2λ和s≥5倍近场长度且仅适用于单晶探头。
5.3设备,耦合剂,灵敏度和分辨率的检测5.3.1超声仪器超声仪器应满足EN 12668-1的要求且应具有如下的特征:-范围设定对纵波和横波传输时应至少能探10mm到2m范围内-增益,应至少有80dB增益器,误差小于1dB,步进最大为2dB。
-时基线性和扫描线性要低于屏高的5%-适用于主频为1MHZ至6MHZ的采用脉冲技术的单晶和双晶探头。
5.3.2探头和探头频率探头和探头频率除了应满足EN12668-2和EN 12668-3的要求还应满足如下:-主频范围为1MHZ至6MHZ-对于斜入射时应采用35°和70°之间的斜探头注:铸钢件检测可用直探头或斜探头,探头的类型选择根据铸件的形状和检测的不连续的类型。
检测近表面区域时优先选用双晶探头(直探头或斜探头)5.3.3超声仪器的检测超声仪器应按照EN 12668-3由检查者定期检查。
5.3.4耦合剂按照EN 583-1采用合适的耦合剂,其性能应能很好的浸润检测表面保证很好的声传输,对于校准和随后的检测应采用同一种耦合剂注:声传输性可用平行的面一次或多次底波来衡量。
5.3.5灵敏度和分辨率的检测设备灵敏度检测至少应满足5.5.2要求的灵敏度调整,设备和探头组合分辨率应满足附录A的要求。
5.4检测铸件表面状况被检铸件的表面状况要求见EN 583-1。
铸件的被检面应保证与探头很好的耦合,对于单晶探头如果表面质量按照EN 1370要求达到4S1或4S2即可达到很好的耦合效果。
任何机加工后表面的粗糙度应满足R a≤12.5μm。
对于特殊技术需要更高的表面质量如2S1、2S2R a≤6.3。
5.5检测工艺5.5.1总则探头和入射方向的选择大部分决定于铸件的形状或铸件中可能出现的不连续或焊接加工出现的不连续。
合适的检测工艺应由铸件的生产方制定,在特殊的情况下应协商一致。
如有可能检测区域要从两个面进行检测,当从一个面检测时为检测出近表面的不连续应增加采用近程分辨率好的探头,对于壁厚小于50mm的可采用双晶探头。
另外除非供需双方协商,对于所有铸件其厚度小于50mm的如下区域应采用双晶探头或斜探头:-关键区域如:圆角,过渡区域和外冷铁区域-焊接加工-订货时规定的焊接区-特殊边缘区域,按照订货时的规定铸件的关键部位深度大于50mm的焊接加工的部位应采用合适的斜探头增加检测。
角度超过60°的斜探头,其声程不能超过150mm,对于所有检测区域要重叠覆盖保证完全检测到。
扫查速度不能超过150mm/s。
5.5.2范围设定范围设定根据EN 583-2在显示屏上用直探头或斜探头采用如下三种方法之一来调整: -用EN 12223中1号试块或EN 27963中2号试块来校准。
-用与待检工件同种材料同样声束特性的校准试块-直探头检测时在铸件上直接进行,此时铸件的表面被检测区域应平行,其距离可知。
5.5.3灵敏度调整5.5.3.1总则范围设定调整后按照EN 583-2进行灵敏度调整,可采用如下两种技术:-距离波幅修正曲线技术(DAC):它是利用一系列相等尺寸而声程不同的反射体的波高建立的(平底孔FBH或长横孔SDH)。
注:2MH频率探头和6mm的平底孔经常用到-距离增益尺寸技术(DGS):它是利用一系列理论曲线,该曲线和声程,仪器增益和 垂直于声轴的平底孔直径有关。
5.5.3.2传输补偿传输补偿按照EN 583-2,当采用校准试块时,必须考虑传输补偿,其中不仅要考虑耦合表面质量状况而且要考虑对面的表面状况,因为对面的表面质量对底波也有影响,当此面的光洁度达到EN 1370规定的4S1或4S2时可以用于传输修正的测量。
5.5.3.3不连续的检测检测时将增益提高至噪声信号可见(扫查灵敏度)。
表2给出定的平底孔或同等的长横孔在被测工件厚度范围内的波高达到至少40%屏高。
如果检测时出现底波的降低量超过需要记录的值(见表3)应在局部降低灵敏度进行复探,并记下底波的降低的dB值,斜探头的灵敏度调整应保证反射体的动态回波类型在显示屏清晰可见。
(见图3)注:推荐斜探头的灵敏度调整在真正的(非人工型)平面型不连续上进行(沿壁厚方向的裂纹)或垂直于表面的大平底,有些情况下,探头的斜楔和铸件外形匹配。
5.5.4不同类型的指示的区别在铸件的检测过程中上述类型中的指示可能单独或同时出现,此时应注意和评价如下内容:-非铸件形状或耦合造成的底波降低量-不连续回波指示底波降低量用底波高度下降的分贝数来表示,指示的波高用平底孔或长横孔直径来表示。
5.5.5记录和记录极限5.5.5.1底波降低量所有底波降低量大于12 dB都应记录,底波降低的区域应在工件上标明并测量出面积。
5.5.5.2缺陷波缺陷波的纪录极限为相对应于参考不连续尺寸大小的回波高度。
当波高超过表3给出级别和图3和图4给出的验收准则的所有可测量尺寸的缺陷波都应记录。