毕业设计答辩ppt,注塑模具答辩ppt..27页PPT
合集下载
模具毕业答辩ppt

数字化转型
数字化转型为模具设计提供了新的机遇和挑战。如何利用 数字化技术提升模具设计水平,是当前的重要研究课题。
绿色环保
随着环保意识的提高,绿色、环保的模具设计理念逐渐成 为主流。如何实现绿色、环保的模具设计,降低能耗和资 源消耗,是未来的重要发展方向。
05
总结与展望
总结
研究内容概述
简要介绍模具设计的主要研究内容, 包括模具的结构设计、材料选择、工 艺流程等方面的研究。
THANKS
感谢观看
模具设计的基本原则和流程
基本原则
模具设计时应遵循“三化”原则,即标准化、模块化和系列化。标准化是指设计时应采用标准化的零件和标准化 的设计方法;模块化是指将模具分解为多个模块,便于组装和维修;系列化是指将模具设计成系列化产品,便于 扩大使用范围和降低成本。
设计流程
模具设计的基本流程包括产品分析、确定工艺方案、设计模具结构、绘制图纸、审核修改等步骤。在设计过程中, 需要考虑制品的形状、尺寸、精度要求、生产批量等因素,同时还需要进行必要的力学分析和校核。
智能化与自动化技术利用人工智能、机器学 习等技术,实现模具设计的自动化和智能化。 通过智能化技术,设计师可以利用人工智能 算法进行模具优化和智能决策,提高设计效 率和精度。自动化技术则可以减少人工干预, 提高生产效率和质量。
绿色制造理念在模具设计中的应用
总结词
绿色制造理念是现代制造业的重要发展方向,通过环保材料、节能技术和循环经济的运 用,实现模具设计的绿色化。
VS
详细描述
快速原型制造技术利用计算机辅助设计和 数控加工技术,快速制造出模具原型。通 过原型制造,设计师可以在早期阶段发现 和解决设计问题,减少后期修改和优化成 本,提高模具开发成功率。
数字化转型为模具设计提供了新的机遇和挑战。如何利用 数字化技术提升模具设计水平,是当前的重要研究课题。
绿色环保
随着环保意识的提高,绿色、环保的模具设计理念逐渐成 为主流。如何实现绿色、环保的模具设计,降低能耗和资 源消耗,是未来的重要发展方向。
05
总结与展望
总结
研究内容概述
简要介绍模具设计的主要研究内容, 包括模具的结构设计、材料选择、工 艺流程等方面的研究。
THANKS
感谢观看
模具设计的基本原则和流程
基本原则
模具设计时应遵循“三化”原则,即标准化、模块化和系列化。标准化是指设计时应采用标准化的零件和标准化 的设计方法;模块化是指将模具分解为多个模块,便于组装和维修;系列化是指将模具设计成系列化产品,便于 扩大使用范围和降低成本。
设计流程
模具设计的基本流程包括产品分析、确定工艺方案、设计模具结构、绘制图纸、审核修改等步骤。在设计过程中, 需要考虑制品的形状、尺寸、精度要求、生产批量等因素,同时还需要进行必要的力学分析和校核。
智能化与自动化技术利用人工智能、机器学 习等技术,实现模具设计的自动化和智能化。 通过智能化技术,设计师可以利用人工智能 算法进行模具优化和智能决策,提高设计效 率和精度。自动化技术则可以减少人工干预, 提高生产效率和质量。
绿色制造理念在模具设计中的应用
总结词
绿色制造理念是现代制造业的重要发展方向,通过环保材料、节能技术和循环经济的运 用,实现模具设计的绿色化。
VS
详细描述
快速原型制造技术利用计算机辅助设计和 数控加工技术,快速制造出模具原型。通 过原型制造,设计师可以在早期阶段发现 和解决设计问题,减少后期修改和优化成 本,提高模具开发成功率。
模流分析毕业论文答辩PPT
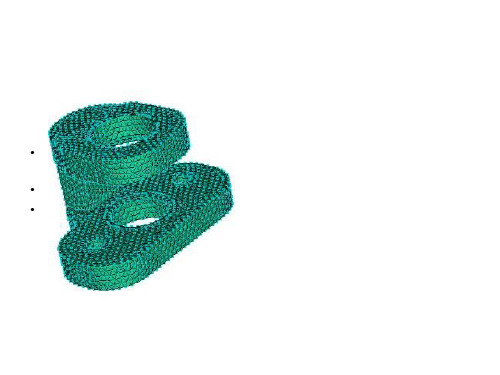
• 从充填结束 时的冻结 层因子 图中可以看出, 在充填结束的时 候, 最大冻结层 因子到达1 〔以下图可以明显看 到〕, 高冻结层部位 将 出现保压困难。
CASE1体积收缩率和缩痕指数〔流动
分析结果〕
• 从图中可以看出, 顶出时的体积收 缩率为15.26% , 从体积收缩率
〔即图中的下面 两幅图〕 图中可 以看到 ,产品的 体积收 缩率分 布 并不均 匀,这 可 能导 致因收缩 不 均匀 因素引 起的 翘曲 变形量较大。
70℃
• 熔体温度:
300.00℃
• 注射时间:
0.4 sec
• 产品体积:
3cm^3
• 总投影面积:
1cm^2
• 冷却条件:
• 冷却介质:
水〔纯〕
• 冷却介质入口温度: 25 ℃
• 保压设置: 保 压 设 置 为两 段保 压 , 第一 段 压力 为 100MPa,持续时 间 ;第二段保压线性递减 ,持续 时间3s; 至 0MPa,持续时间 。总 的成型周期为 ,持续时间3s。总的 成型周期为25s 包括5s开模时间 开 模时间〕 〔包括 开模时间〕。
CASE1结论与建议
• 从分析结果中得知: 1.CASE1方案的进胶方式无法
在注射 机上成型出合格的 产品,出现缩痕,飞边等 缺陷可能性 非常大。 2.考虑到模具设计方面因素, case1方案也不可取。 3.却水路设计效果良好,因 冷却不均引起 的翘曲变形 量非常小。
CASE2
• 方案2是将主流道,分 流道增大一倍,分别 为6mm和3mm。并且 进胶方式也改变,改 为侧面进胶。其他工 艺参数保持与方案1一 致。
• 如图4-6所示,分析结果说明气穴 并不都在分型面附近,根本处于 下端面尾处,因此设计模具时, 应考虑在改位置增加排气措施。
CASE1体积收缩率和缩痕指数〔流动
分析结果〕
• 从图中可以看出, 顶出时的体积收 缩率为15.26% , 从体积收缩率
〔即图中的下面 两幅图〕 图中可 以看到 ,产品的 体积收 缩率分 布 并不均 匀,这 可 能导 致因收缩 不 均匀 因素引 起的 翘曲 变形量较大。
70℃
• 熔体温度:
300.00℃
• 注射时间:
0.4 sec
• 产品体积:
3cm^3
• 总投影面积:
1cm^2
• 冷却条件:
• 冷却介质:
水〔纯〕
• 冷却介质入口温度: 25 ℃
• 保压设置: 保 压 设 置 为两 段保 压 , 第一 段 压力 为 100MPa,持续时 间 ;第二段保压线性递减 ,持续 时间3s; 至 0MPa,持续时间 。总 的成型周期为 ,持续时间3s。总的 成型周期为25s 包括5s开模时间 开 模时间〕 〔包括 开模时间〕。
CASE1结论与建议
• 从分析结果中得知: 1.CASE1方案的进胶方式无法
在注射 机上成型出合格的 产品,出现缩痕,飞边等 缺陷可能性 非常大。 2.考虑到模具设计方面因素, case1方案也不可取。 3.却水路设计效果良好,因 冷却不均引起 的翘曲变形 量非常小。
CASE2
• 方案2是将主流道,分 流道增大一倍,分别 为6mm和3mm。并且 进胶方式也改变,改 为侧面进胶。其他工 艺参数保持与方案1一 致。
• 如图4-6所示,分析结果说明气穴 并不都在分型面附近,根本处于 下端面尾处,因此设计模具时, 应考虑在改位置增加排气措施。
毕业答辩PPT_支架注塑模设计说明书

五、浇注系统设计
1.浇注系统一般由主流道、分流道、浇口和冷料穴组成。 根据moldflow分析结果,浇口选择扇形浇口的形式,同 时不设分流道。 拉料杆:采用球形拉料杆的形式,便于塑件的拉出。 2.设计浇注系统遇到的难点:由于尺寸较小,并且表面 要求比较高,要求不能有太大的表现。为了防止大的变 形,因此采用扇形浇口。 3.扇形浇口扇形浇口对产品成形的应力影响最小,不会对 产品其它的力施加作用力.不干涉其它力的作用.浇口也 不会试塑件产生流纹的现象。
7/29/2019
设计步骤
• 在毕业设计过程中的具体设计步骤:(1)分析塑料产 品图,抄画产品图,进行三维造型;
• (2)根据塑料产品的特点和要求,制定模总体方案, 每一部分的设计都应考虑两种以上的方案;
• (3)绘制详细的模具装配草图,用来和知道老师进行 方案讨论;
• (4)计算模具零件,在说明书中应有详细的计算过程 和结果;
7/29/2019
五、浇注系统设计
主流道尺寸
浇口设计
拉料杆
7/29/2019
六、冷却系统
2、冷却系统方案分析比较 根据塑件的形状特点,水道采用直线式,有2种冷却方案根据计算的结 果,所需的冷却水道数约为一根,因此考虑了两个方案。 方案一,综合考虑到加工的难易和产品的经济性,型腔型芯的冷却回 路分别采用3根,即采用六根冷却管,两个入口。方案二,动模定模分 别采用1根,即2个入口。 为了使效率更高,我们选择方案一对塑件进行冷却。型腔型芯的冷却 回路分别采用3根,即采用六根冷却管。
7/29/2019
方案一
方案二
7/29/2019
七、导向机构和推出方式
1.导向机构:导向定位机构采用导柱导套配合。 导柱与导套的配合采用H7/f7,导套与模具孔的配合 采用H7/m6,导柱与模具的配合采用H7/m6。 2.推出方式:顶出机构采用推杆推出机构。
电位器上盖注塑模具设计-答辩PPT
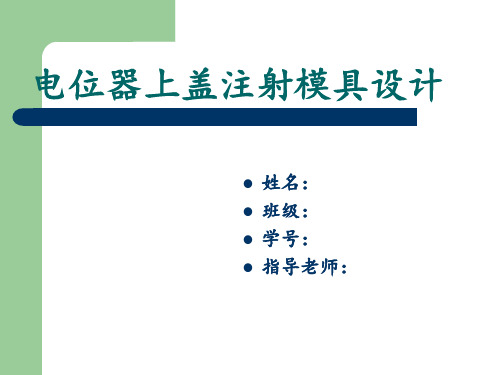
电位器上盖注射模具设计
姓名: 班级: 学号: 指导老师:
摘要
• 产品分析 • 注塑机的选择 • 模具成型零件设计 • 模具整体设计 • 工作过程 • 模具的特点
一、产品分析
1、电位器上盖
2.塑件的材料及性能
1:所设计的塑件的材料为ABS,该材பைடு நூலகம்综合 性能好,冲击强度高,尺寸稳定,易于成 型。 2:成型性能 吸湿大,必须充分干燥, 模温宜取60-80度, 脱模后应进行调湿处理。
六、该模具的特点
1.该模具采用电火花和线切割加工成型 零件,从而能保证精度要求。 2.该模具采用二板式(单分型面)注射 模,一摸一腔的简单设计。 3.无需侧抽芯等较复杂设计,能实现快 速出模,提高效率。
谢谢各位老师
• 根据产品尺寸规格初选标准模架为 300×250mm
2.型腔设计
(1)型腔采用整体式 优点:牢固、不易变形 不会使塑件产生拼接线痕迹 易于保证型腔精度
1.型芯设计 (1) 型芯采用整体式 优点: 加工效率高 减少装配难度 可节约优质钢材 减少加工量
四、模具的整体设计
根据GB/T12556.1—1990并结合塑件的具体情 况选取其它结构零件,最后得到如图所示的模具。
二、选取注塑机
产品的质量为31克,根据以下公式,选择注射 机的最大注射量: K G公≥NG件+G废 式中 K=0.8由于根据设计要求和加工的经济性 取N=1,通过Proe得到G废=4.62g
得到G公=44.525(g) 因此初选注塑量为100 ㎝3 的注塑机 SZ-100/80
三、模具成型零件设计
3.产品要求
1.由于产品内表面有小凸台,所以要有合理 的出模方式,确保产品完整。 2.要保证产品性能、尺寸精度以及互换性。
姓名: 班级: 学号: 指导老师:
摘要
• 产品分析 • 注塑机的选择 • 模具成型零件设计 • 模具整体设计 • 工作过程 • 模具的特点
一、产品分析
1、电位器上盖
2.塑件的材料及性能
1:所设计的塑件的材料为ABS,该材பைடு நூலகம்综合 性能好,冲击强度高,尺寸稳定,易于成 型。 2:成型性能 吸湿大,必须充分干燥, 模温宜取60-80度, 脱模后应进行调湿处理。
六、该模具的特点
1.该模具采用电火花和线切割加工成型 零件,从而能保证精度要求。 2.该模具采用二板式(单分型面)注射 模,一摸一腔的简单设计。 3.无需侧抽芯等较复杂设计,能实现快 速出模,提高效率。
谢谢各位老师
• 根据产品尺寸规格初选标准模架为 300×250mm
2.型腔设计
(1)型腔采用整体式 优点:牢固、不易变形 不会使塑件产生拼接线痕迹 易于保证型腔精度
1.型芯设计 (1) 型芯采用整体式 优点: 加工效率高 减少装配难度 可节约优质钢材 减少加工量
四、模具的整体设计
根据GB/T12556.1—1990并结合塑件的具体情 况选取其它结构零件,最后得到如图所示的模具。
二、选取注塑机
产品的质量为31克,根据以下公式,选择注射 机的最大注射量: K G公≥NG件+G废 式中 K=0.8由于根据设计要求和加工的经济性 取N=1,通过Proe得到G废=4.62g
得到G公=44.525(g) 因此初选注塑量为100 ㎝3 的注塑机 SZ-100/80
三、模具成型零件设计
3.产品要求
1.由于产品内表面有小凸台,所以要有合理 的出模方式,确保产品完整。 2.要保证产品性能、尺寸精度以及互换性。
毕业设计答辩PPT
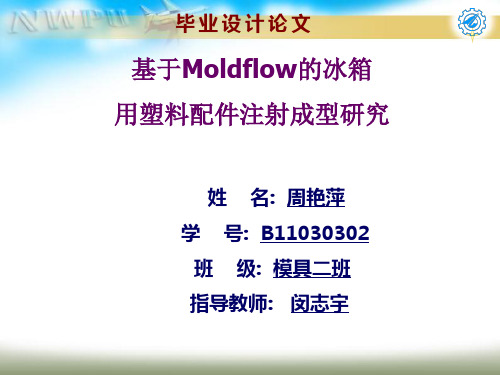
毕业设计论文
第六章 方案优化后的结果
6.1 方案优化后的总结与分析
方案优化前后的分析结果统计如下表所示:
毕业设计论文
毕业设计论文
6.2 模具装配图
模具装配图如图所示:
毕业设计论文
结 论
在完成论文的过程中,遇到了许多问题。首先在用Pro/E 建模和模具设计的过程中遇到了一些想不到的问题,其中遇 到最多的问题还是对Moldflow软件的使用。初始设计方案存 在的问题如下: (1)充填完成后形成了较多的气穴。 (2)浇口位置处以及主流道剪切速率和壁上剪切应力过大。 (3)制件各部分冷却速度不均匀,冷流道冷却时间过长。 (4)制件翘曲变形量较大。
毕业设计论文
2.3 模架结构方案
根据塑件的要求、塑料的成型特点以及型腔的布局。初 选的模架为:A2540型标准模架。
毕业设计论文
第三章 注射成型分析
3.1 模型导入
将模型导入到工程项目中。对模型进行网格划 分结果并进行网格统计结果如图所示:
毕业设计论文
3.2 充填分析
Moldflow 软件的充填分析可以对塑料熔体从开 始进入型腔直至充满型腔的整个过程进行模拟。 (1)建立一模两腔的浇注系统:
毕业设计论文 (2)剪切速率。体积 由充填分析结果可知最高剪切速率约为107100 (1/s),比材料的最大剪切速率高,需要对浇注系 统进行修改。
毕业设计论文 (3)壁上剪切应力 壁上最大剪切应力为0.4504MPa,但材料允许的 最大剪切应力为0.26MPa。出现在浇口位置,因此 需对浇注系统进行修改。
毕业设计论文
谢谢各位老师!
毕业设计论文
第四章 塑件和模具的调整及其优化
4.1 塑件及模具的各项参数作如下调整
本科毕业设计答辩-双组份夹持器注塑模具设计与仿真PPT课件

➢在定模侧,由模板和型 腔组成冷却水回路( ); ➢在定模固定板上组成冷 却水回路。
2020/3/23
11
二、双组份注塑模具结构设计
8、脱模系统设计:
2次分型设计 ➢第一分型面利用橡胶弹 簧完成塑件和型芯的分离
➢第二分型面利用模具镶 件和6根阶梯式推杆完成 成品塑件与模具的分离; 4根圆截面推杆完成流道 凝料与塑件的分离
2020/3/23
14
三、第一组份PP注射模拟分析
➢充填+保压+冷却+翘曲:
(a)总变形量
(b)冷却不均
1.收缩率结果
2020/3/23
(c)收缩不均
(d)取向不均
2.翘曲结果
15
三、第一组份PP注射模拟分析
影响PP塑件收缩率的工艺参数分析
冷却系统
模具温度/注射温度
保压曲线
冷却水道 优化结果
2020/3/23
总结
2020/3/23
2
一、课题背景及主要研究内容
普通注射机 +多色注射模块 普通注射机
同步共注射喷嘴
交叉喷嘴
多色注射机
多色注射机 +发泡/气辅/ 压塑/……
注塑设备
新型喷嘴
多组分 注塑工艺
分离式喷嘴
旋转模板式模具 转位模板式模具
模具结构
型芯收缩式模具 脱件板旋转式模具
转移/滑动式模具
型芯滑动式模具
优化前 制品温度
第2次优化后 制品温度
16
三、第一组份PP注射模拟分析
影响PP塑件收缩率的工艺参数分析
冷却系统
模具温度/注射温度
保压曲线
顶出时收缩率(%)
8
7.8
2020/3/23
11
二、双组份注塑模具结构设计
8、脱模系统设计:
2次分型设计 ➢第一分型面利用橡胶弹 簧完成塑件和型芯的分离
➢第二分型面利用模具镶 件和6根阶梯式推杆完成 成品塑件与模具的分离; 4根圆截面推杆完成流道 凝料与塑件的分离
2020/3/23
14
三、第一组份PP注射模拟分析
➢充填+保压+冷却+翘曲:
(a)总变形量
(b)冷却不均
1.收缩率结果
2020/3/23
(c)收缩不均
(d)取向不均
2.翘曲结果
15
三、第一组份PP注射模拟分析
影响PP塑件收缩率的工艺参数分析
冷却系统
模具温度/注射温度
保压曲线
冷却水道 优化结果
2020/3/23
总结
2020/3/23
2
一、课题背景及主要研究内容
普通注射机 +多色注射模块 普通注射机
同步共注射喷嘴
交叉喷嘴
多色注射机
多色注射机 +发泡/气辅/ 压塑/……
注塑设备
新型喷嘴
多组分 注塑工艺
分离式喷嘴
旋转模板式模具 转位模板式模具
模具结构
型芯收缩式模具 脱件板旋转式模具
转移/滑动式模具
型芯滑动式模具
优化前 制品温度
第2次优化后 制品温度
16
三、第一组份PP注射模拟分析
影响PP塑件收缩率的工艺参数分析
冷却系统
模具温度/注射温度
保压曲线
顶出时收缩率(%)
8
7.8
骨架注塑模具设计毕业答辩ppt课件.ppt

3.2、侧壁厚度与推板厚度的计算
▪ 3.2.1、侧壁厚度
▪ 该型腔为整体式。因此,型腔的强度和刚度按整体式进行计算。由于型 腔壁厚计算比较麻烦,也可以参考经验推荐数据。查《塑料成型工艺与 模具设计》表6.10型腔侧壁厚,取S=20mm。
▪ 3.2.2、推板厚度
H=11.3mm,取16mm。(计算过程略)
93℃。学稳定性, 的抗冲击强度,
不耐酮、醛、有良好的机械强
酯、氯代烃 度和一定的耐磨
等。
性、耐寒性、耐
油性、耐水性、
化学稳定性和电
气性能。
第一部分、原始资料分析
结论 1.升温时粘度增高,所以成型压力较高,在要 求塑件精度高时,模具温度可控制在50~60℃, 而在强调塑件光泽和耐热时,模具温度应控制 在60~80℃,模具应用耐磨钢,并淬火; 2.ABS易吸水,成型加工前应进行干燥处理; 易产生熔接痕,模具设计时应注意尽量减少浇 注系统对料流的阻力; 3.在正常的成型条件下,壁厚、熔料温度对收 缩率影响极小,脱模斜度宜稍大。
斜滑块的导滑长度不能太短,一般应保证滑块在完成 抽拔动作后,留在导滑条中的长度不小于有效长度的 2/3,经计算,该滑块在完成抽拔动作后留在导滑条中 的长度为47.5mm,总的有效长度为65.5mm,所以导滑 条的长度足够。
3.4、冷却与加热系统 。经计算后得知可不需要冷却系统(计算过程略)。
第四部分、选择模架
第一部分、原始资料分析
1.1、塑件的原始材料分析
▪ 1.2.1、结构分析
▪ 从零件图上分析,该零件总体形状为回旋体,在一个直径为 38mm高为17mm的圆柱中间有一个直径为16mm高为11mm和一个 直径为19mm高为6mm的圆柱台阶孔,然后留壁厚为1.5mm。该 塑件有凹槽,因此,模具设计时必须设置侧向分型抽心机构, 该零件属于中等复杂程度。
▪ 3.2.1、侧壁厚度
▪ 该型腔为整体式。因此,型腔的强度和刚度按整体式进行计算。由于型 腔壁厚计算比较麻烦,也可以参考经验推荐数据。查《塑料成型工艺与 模具设计》表6.10型腔侧壁厚,取S=20mm。
▪ 3.2.2、推板厚度
H=11.3mm,取16mm。(计算过程略)
93℃。学稳定性, 的抗冲击强度,
不耐酮、醛、有良好的机械强
酯、氯代烃 度和一定的耐磨
等。
性、耐寒性、耐
油性、耐水性、
化学稳定性和电
气性能。
第一部分、原始资料分析
结论 1.升温时粘度增高,所以成型压力较高,在要 求塑件精度高时,模具温度可控制在50~60℃, 而在强调塑件光泽和耐热时,模具温度应控制 在60~80℃,模具应用耐磨钢,并淬火; 2.ABS易吸水,成型加工前应进行干燥处理; 易产生熔接痕,模具设计时应注意尽量减少浇 注系统对料流的阻力; 3.在正常的成型条件下,壁厚、熔料温度对收 缩率影响极小,脱模斜度宜稍大。
斜滑块的导滑长度不能太短,一般应保证滑块在完成 抽拔动作后,留在导滑条中的长度不小于有效长度的 2/3,经计算,该滑块在完成抽拔动作后留在导滑条中 的长度为47.5mm,总的有效长度为65.5mm,所以导滑 条的长度足够。
3.4、冷却与加热系统 。经计算后得知可不需要冷却系统(计算过程略)。
第四部分、选择模架
第一部分、原始资料分析
1.1、塑件的原始材料分析
▪ 1.2.1、结构分析
▪ 从零件图上分析,该零件总体形状为回旋体,在一个直径为 38mm高为17mm的圆柱中间有一个直径为16mm高为11mm和一个 直径为19mm高为6mm的圆柱台阶孔,然后留壁厚为1.5mm。该 塑件有凹槽,因此,模具设计时必须设置侧向分型抽心机构, 该零件属于中等复杂程度。
诺基亚手机上盖注塑模设计--毕业设计答辩PPT
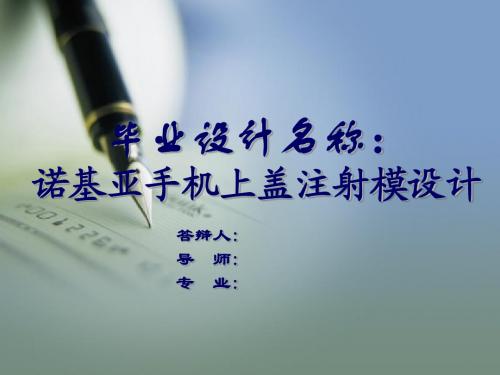
一任务书的分析二制品的proe分析与注射机的选择1利用proe的塑料顾问对产品进行分析2计算制品的体积与重量3注射机的确定三模具设计的工艺过程1分型面的选择2型腔的布局3浇注系统4成型部分尺寸的计算5加热与冷却装置的设计6推出机构7模具的工作过程四总结一任务书的分析手机面壳零件图1该制品尺寸大小为104mmx50mmx5mm属于比较小巧而且是薄板一类的手机
如上图所示,最佳浇注口在制品的中间部分。这个为我接下来设计 侧浇口提供了一个依据。
2)选择填充方式
在这次设计中,填充方法有潜伏式浇口、单侧浇口、双侧浇口,通过比 较之后最终选用如图所示的单侧浇口对制品进行填充。
3)填充时间
如有图所示,填充时 间只需要0.75秒。快速充 满型腔有利于提高生产效 率。
定模
动模
5、加热与冷却装置的设计
加热装置设计: 塑料模具的温度直接影响到塑件的成型质量和生产率。参考《塑料模 具设计》表6-10 常用热塑料的模具温度表可以得知所选塑件材料ABS的模 具温度为:50°C~80°C;模具温度在80°C以下,所以可以不设置加热 装置。 冷却装置设计: 水道的布置如下图所示: 其详细尺寸可见说明书计算 过程及结果
2)分流道的设计
分流道设计:采用平衡式分布。 分流道截面形状选较常用的圆形分流道截面形状。 分流道的尺寸:分流道尺寸由塑料品种、塑件的大小及流道长度确定。 对于重量在200g以下,壁厚在3mm以下的塑件可用以下经验公式计算分 流道的直径。 式中:D——分流道的直径,mm; W——塑件的质量,g; L——分流道的长度,mm; 由于所设计的塑件的质量小于200g,故按以上公式确定其直径。 由于此式计算的分流道直径限于3.2mm~9.5mm,而所算出来的结果小 于此范围,故参考《塑料模具设计》P78表6-1中ABS的分流道推荐值, 定出分流道直径为4mm。
如上图所示,最佳浇注口在制品的中间部分。这个为我接下来设计 侧浇口提供了一个依据。
2)选择填充方式
在这次设计中,填充方法有潜伏式浇口、单侧浇口、双侧浇口,通过比 较之后最终选用如图所示的单侧浇口对制品进行填充。
3)填充时间
如有图所示,填充时 间只需要0.75秒。快速充 满型腔有利于提高生产效 率。
定模
动模
5、加热与冷却装置的设计
加热装置设计: 塑料模具的温度直接影响到塑件的成型质量和生产率。参考《塑料模 具设计》表6-10 常用热塑料的模具温度表可以得知所选塑件材料ABS的模 具温度为:50°C~80°C;模具温度在80°C以下,所以可以不设置加热 装置。 冷却装置设计: 水道的布置如下图所示: 其详细尺寸可见说明书计算 过程及结果
2)分流道的设计
分流道设计:采用平衡式分布。 分流道截面形状选较常用的圆形分流道截面形状。 分流道的尺寸:分流道尺寸由塑料品种、塑件的大小及流道长度确定。 对于重量在200g以下,壁厚在3mm以下的塑件可用以下经验公式计算分 流道的直径。 式中:D——分流道的直径,mm; W——塑件的质量,g; L——分流道的长度,mm; 由于所设计的塑件的质量小于200g,故按以上公式确定其直径。 由于此式计算的分流道直径限于3.2mm~9.5mm,而所算出来的结果小 于此范围,故参考《塑料模具设计》P78表6-1中ABS的分流道推荐值, 定出分流道直径为4mm。