注射模设计大作业1
注射成型模具设计——习题答案

第四章注射成型模具设计——习题答案一、填空题1.根据模具总体结构特征,塑料注射模可分为:(1)_单分型面注射模_;(2)_双分型面注射模_;(3)_斜销侧向分型抽芯机构_;(4)_带有活动镶件的注射模_;(5)_自动卸螺纹的注射模_;(6)_定模设置推出机构的注射模_;(7)_哈夫模_等类型。
2.注射成型机合模部分的基本参数有_锁模力__、_模具最大尺寸_、_顶出行程_和_顶出力__等。
3.通常注射机的实际注射量最好在注射机的最大注射量的___80%___以内。
4.注射机的锁模力必须大于型腔内熔体压力与塑料及浇注系统在_分型面上的投影面积之和_的乘积。
5.设计的注射模闭合厚度应满足下列关系:_Hmin≦Hm≦Hmax_。
若模具厚度小于注射机允许的模具最小厚度时,则可采用_增加垫块高度或另外加垫板的方法来调整,使模具闭合。
6.注射机顶出装置大致有_中心顶杆机械顶出_、_两侧双顶杆机械顶出_、_中心顶杆液压顶出与两侧双顶杆机械顶出联合作用_、_中心顶杆液压顶出与其他开模辅助油缸联合作用_等类型。
7.注射模的浇注系统由__浇口__、__主流道_、__分流道__、__冷料穴_等组成。
8.主流道—般位于模具_中心位置_,它与注射机的_喷嘴轴心线_重合。
9.注射模分流道设计时,从传热面积考虑,热固性塑料宜用_梯形截面和半圆形截面_分流道;热塑性塑料宜用_圆形_分流道。
从压力损失考虑,_圆形截面_分流道最好,从加工方便考虑用__梯形__、_U型或矩形_分流道。
10.在多型腔模具中,型腔和分流道的排列有_平衡式_和_非平衡式_两种。
11.当型腔数较多,受模具尺寸限制时,通常采用非平衡式布置,由于各分流道长度不同,可采用_将浇口设计成不同的截面尺寸_来实现均衡进料,这种方法需经_多次试模和整修_才能实现。
12.注射模型腔与分流道布置时,最好使塑件和分流道在分型面上总投影面积的几何中心和_锁模力_的中心相重合。
13.浇口的类型可分_点浇口_、_侧浇口_、_直接浇口_、_中心浇口_、_潜伏式浇口_、_护耳浇口_等几类。
注射模设计步骤与实例
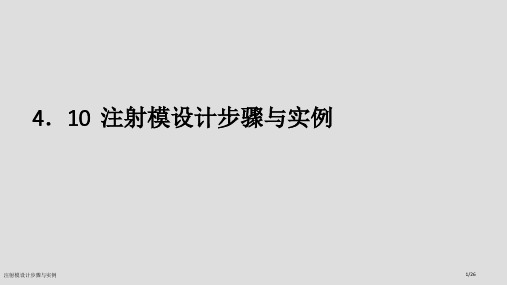
❖ 因为上模板座和上凸模固定板尺寸尚不确定,初定δ=
25mm,D=20mm,计算后,取L=55mm。假如以后δ,有
注射模设计步改骤与变实例,则再修正L长度。
12/26
❖ ④滑块与导槽设计 ❖ 滑块与侧型芯(孔)连接方式设计 本例中侧向抽芯机
构主要是用于成型零件侧向孔和侧向凸台,因为侧 向孔和侧向凸台尺寸较小,考虑到型芯强度和装配 问题,采取组合式结构。型芯与滑块连接采取镶嵌 方式,其结构如图4-149所表示。 ❖ 滑块导滑方式 本例中为使模具结构紧凑,降低模 具装配复杂程度,拟采取整体式滑块和整体导向槽 形式,其结构如图4-149所表示。为提升滑块导向 精度,装配时可对导向槽或滑块采取配磨、配研装 配方法。 ❖ 滑块导滑长度和定位装置设计 本例中因为侧芯距 较短,故导滑长度只要符合滑块在开模时定位要求 即可。滑块定位装置采取弹簧与台阶组合形式,如 图4-149所表示。
4.10 注射模设计步骤与实例
注射模设计步骤与实例
1/26
4.10.1 注射模设计基本程序
❖ 1.了解塑件技术要求 ❖ 2.依据塑件形状尺寸,估算塑件体积和重量 ❖ 3.分析塑件,确定成形方案 ❖ 4.绘制方案草图 ❖ 5.设计计算 ❖ 6.绘制模具设计总装图 ❖ 7.绘制零件工作图 ❖ 8,经过全方面审核后投产加工
❖ 另加3~5mm抽芯安全系数,可取抽芯距S轴=4.9mm。
❖ ②确定斜导柱倾角 斜导柱倾角是斜抽芯机构主要技术参数 之一,它与抽拔力以及抽芯距有直接关系,—般取α=15°~ 20°,本例中选取α=20°。
❖ ③确定斜导柱尺寸 斜导柱直径取决于抽拨力及其倾斜角度, 可按设计资料相关公式进行计算,本例采取经验估值,取斜 导柱直径d=14mm。斜导柱长度依据抽芯距、固定端模板厚 度、斜销直径及斜角大小确定(参见本章第六节斜导柱长度 计算公式)。
注射模具设计实验
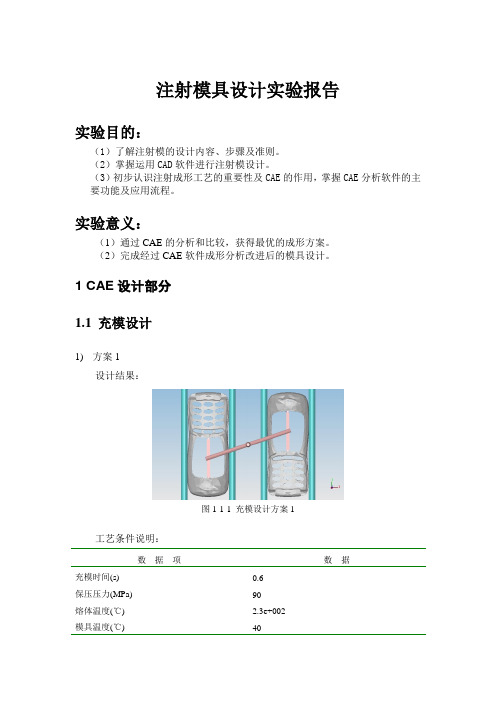
注射模具设计实验报告实验目的:(1)了解注射模的设计内容、步骤及准则。
(2)掌握运用CAD软件进行注射模设计。
(3)初步认识注射成形工艺的重要性及CAE的作用,掌握CAE分析软件的主要功能及应用流程。
实验意义:(1)通过CAE的分析和比较,获得最优的成形方案。
(2)完成经过CAE软件成形分析改进后的模具设计。
1 CAE设计部分1.1 充模设计1)方案1设计结果:图1-1-1 充模设计方案1工艺条件说明:数据项数据充模时间(s) 0.6保压压力(MPa) 90熔体温度(℃) 2.3e+002模具温度(℃) 40空气温度(℃) 20该方案的优点:1.优点1:该方案中每个行腔都有两个内浇道,塑料熔体流程较短,压力损失较少,注射压力小,不容易出现填充不足缺陷。
2.优点2:有两个内浇道,不易出现浇不足。
该方案的缺点:1.缺点1:由于采用多浇道,所以浇道设计比较复杂,浪费材料。
2.缺点2:该方案采用多浇道,所以产生熔纹倾向更大。
分析结果:图1-1-2 充模设计方案1分析结果(熔合纹)分析结果说明:从图中可以看出,产品两侧和按键部位产生熔合纹的倾向很大,产生这种结果的原因是,在按键部位和产品两侧,塑料熔体分流比较严重,所以很容易产生熔合纹。
这种现象可以通过改变工艺参数来改善。
2)方案2设计结果:图1-1-3 充模设计方案2工艺条件说明:数据项数据充模时间(s) 0.35保压压力(MPa) 90熔体温度(℃) 2.3e+002模具温度(℃) 40空气温度(℃) 20该方案的优点:1.优点1:内浇道设计比较简单,材料利用率比较高,模具设计比较简单。
2.优点2:只有一个内浇道,产生熔合纹的倾向较小。
该方案的缺点:1.缺点1:注射压力较大,最终产品的收缩倾向较大。
2.缺点2:冲型时间较长,压力损失较大。
分析结果:(10分)图1-1-4 充模设计方案2分析结果(熔合纹)分析结果说明:从上图可以看出,由于每一个型腔内都只有一个内浇口,因此产品的左右两侧的中间部分基本上不会产生分流的熔体相遇的情况,也就不太可能形成熔合纹。
注射模具设计实例

7. 导向机构的确定: 采用有肩导柱导向;导柱设在动模侧,以防损 坏型芯;不对称布置以保证正确的合模位置; 8.排气机构:利用分型面和推杆间缝隙排气; 9.温度控制方式: 冷却水管直径8mm;采用单一矩形冷却回路 10.模具材料: 型腔、型芯、镶块等成形部分零件采用强度、 耐磨性较好的专用模具合金钢如T8A,Cr12, Cr12MoV,P20等;模板、垫板、固定板、支撑块 等可采用普通45钢或Q235,Q275钢等
4)浇口:宽度b=2mm,厚 度h1=0.8mm; 5)定位环及浇口套:根据 注射机定模板中心孔尺 寸,选取定位环直径为 φ55mm,浇口套公称直 径为φ22mm。
4. 确定成形零件的结构
1)型腔、型芯的结构设计: 为便于热处理和节约优质模具钢,型腔 采用整体镶块式结构;为便于制造,型芯 采用局部镶拼结构; 2)固定方式: 型腔和型芯均通过套板以台阶方式固定, 型芯中的小镶件用台阶或铆接固定。
(一)产品工艺性分析
3. 结构工艺性: 零件壁厚基本均匀,塑件的最小壁厚0.8mm,注 射成型时应不会发生充填不足现象;塑件有侧孔, 注射模具应有侧抽芯机构。 4. 零件体积及质量估算 1)单个塑件 体积V=1649.46mm3,质量 m=V×ρ=1.73g; 2)两个塑件和浇注系统凝料:总体积V总≈4.95cm3, 总质量m总=5.2g;
模具与注射机的相关尺寸校核最大注射模具与注射机的相关尺寸校核最大注射量注射压力安装尺寸开模及顶出行量注射压力安装尺寸开模及顶出行锁模力的校核七根据校核计算结果修改完善模具装配图七根据校核计算结果修改完善模具装配图
注射模具设计实例
大连理工大学材料学院 陈国清
2.1.2 注射模具设计实例
塑料旋钮
塑料旋钮相关参数及技术要求
注射模设计大作业1.

注射模设计本设计为一塑料杯盖,如图4—327所示。
塑件比较简单,塑件的质量要求是不允许有裂纹和变形缺陷,脱模斜度30'~1º;塑件材料ABS,生产批量为大批量,塑件公差按模具设计要求进行转换。
图4—327一、塑件成型工艺性分析1、塑件的分析(1)外形尺寸该塑件壁厚为1和2.5mm ,塑件外形尺寸不大,塑件熔体流程不长,适合于注射成型,如图4—327所示(2)精度等级每个每个尺寸的公差不一样,有的属于一般精度,有的属于高精度,就按实际公差进行计算。
(3)脱模斜度ABS属无定型塑料,成型收缩率较小参考表2—10选择该塑件上型芯和凹模的统一脱模斜度为1º。
2、ABS的性能分析(1)使用性能综合性能好,冲击强度、力学强度较高,尺寸稳定,耐化学性,电气性能良好;易于成型及机械加工,其表面可镀铬,适合制作一般机械零件、减摩零件、传动零件和结构零件。
(2)成型性能1)无定型塑料。
其品种很多,各品种的机电性能及成型特性也各有差异,应按品种来确定成型方法及成型条件。
2)吸湿性强含水量应小于0.3%(质量),必须充分干燥,要求表面光泽的塑件应要求长时间预热干燥。
3)流动性中等。
溢边料0.04mm左右。
4)模具设计时要注意浇注系统,选择好进料口位置、形式。
推出力过大或机械加工时塑件表面呈现白色痕迹。
(3)ABS主要性能指标其性能指标见表4—44表4—44 ABS的性能指标密度g/cm3 1.02~1.08 屈服强度/MPa 50比体积cm3/g 0.86~0.98 拉伸强度/MPa 38吸水率(%)0.2~0.4 拉伸弹性模量/MPa 1.4×1000熔点/℃130~160 抗弯强度/MPa 80计算收缩率(%)0.4~0.7 抗压强度/MPa 53比热容J /(kg·℃)1470 弯曲弹性模量/MPa 1.41×0003、ABS 的注射成型过程及工艺参数 (1)注射成型过程1)成型前的准备。
注射模具设计实验报告 完整
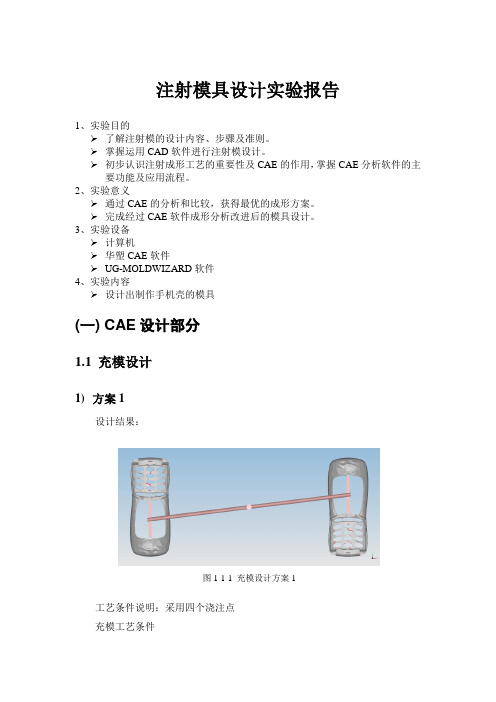
开模停留时间(s)
4.00
冷却时间计算方式
用户指定:冷却时间(s)
0
系统优化:可顶出面积比(%)
95.00%
该方案的优点:
13.优点1:冷却速度快,制品温度低
14.优点2:冷却时间较短,成型率高,生产效率高
该方案的缺点:
15.缺点1:管道多而结构复杂,工艺参数难以控制
16.缺点2:成本高,设计复杂
型芯型腔平均温差(℃)
9.56
制品中心面温度区间(℃)
[39.8, 156.9]
制品截面平均温度区间(℃)
[39.1, 122.4]
制品单元冷却时间区间(s)
[0.7, 14.6]
图6-1稳态温度场
图6-2热流密度场
图6-3型芯型腔温差场
图6-4截面平均温度场
图6-5中心面温度场
图6-6冷却时间场
图6-7冷却介质温度场
数据
评价
说明/建议
冷却时间(s)
10.00
制品温度区间(℃)
[26.7, 70.6]
制品平均温度(℃)
45.26
稳态温度场均方差(℃)
6.49
可顶出面积百分比(%)
96.67
制品热流密度区间(W/m2)
[-23874.5, 37682.5]
型芯型腔温差区间(℃)
[-32.1, 31.6]
型芯型腔平均温差(℃)
冷却分析结果
数据项
数据
评价
说明/建议
冷却时间(s)
9.00
制品温度区间(℃)
[35.3, 69.8]
制品平均温度(℃)
47.40
稳态温度场均方差(℃)
8.09
单分型面注射模具设计大作业题目(1-15).
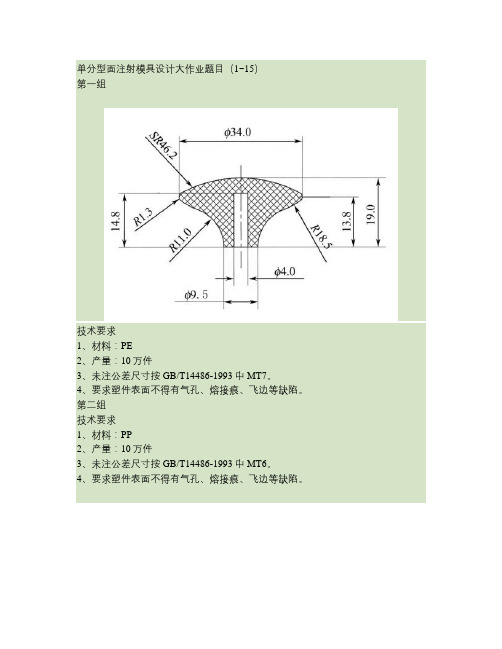
单分型面注射模具设计大作业题目(1~15)第一组技术要求1、材料:PE2、产量:10万件3、未注公差尺寸按GB/T14486-1993中MT7。
4、要求塑件表面不得有气孔、熔接痕、飞边等缺陷。
第二组技术要求1、材料:PP2、产量:10万件3、未注公差尺寸按GB/T14486-1993中MT6。
4、要求塑件表面不得有气孔、熔接痕、飞边等缺陷。
第七组技术要求1、材料:RPVC2、产量:10万件3、未注公差尺寸按GB/T14486-1993中MT5。
4、要求塑件表面不得有气孔、熔接痕、飞边等缺陷。
第十四组技术要求1、材料:PS2、产量:10万件3、未注公差尺寸按GB/T14486-1993中MT5。
4、要求塑件表面不得有气孔、熔接痕、飞边等缺陷。
第十二组技术要求1、材料:PMMA2、产量:10万件3、未注公差尺寸按GB/T14486-1993中MT5。
4、要求塑件表面不得有气孔、熔接痕、飞边等缺陷。
第五组技术要求1、材料:PA2、产量:10万件3、未注公差尺寸按GB/T14486-1993中MT6。
4、要求塑件表面不得有气孔、熔接痕、飞边等缺陷。
第三组技术要求1、材料:PP2、产量:10万件3、未注公差尺寸按GB/T14486-1993中MT6。
4、要求塑件表面不得有气孔、熔接痕、飞边等缺陷。
第六组D=40-0.34 B=10-0.20 R1=5 H1=24-0.28 d1=34+0.34 d2=3.5 d3=6.5 h1=19+0.28h2=3.5 C1=16±0.2 C2=4 C3=3 R2=2 α=45° 技术要求 1、材料:RPVC 2、产量:10万件 3、未注公差尺寸按GB/T14486-1993中MT5。
4、要求塑件表面不得有气孔、熔接痕、飞边等缺陷。
第十组技术要求1、材料:ABS2、产量:10万件3、未注公差尺寸按GB/T14486-1993中MT7。
4、要求塑件表面不得有气孔、熔接痕、飞边等缺陷。
注射模具设计实例样稿
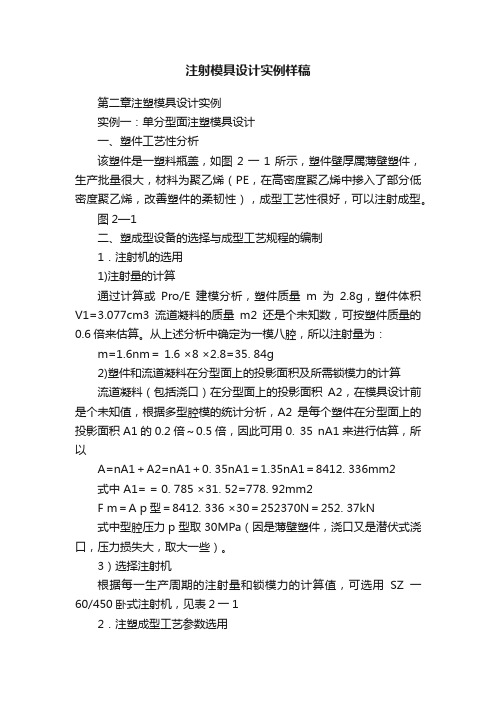
注射模具设计实例样稿第二章注塑模具设计实例实例一:单分型面注塑模具设计一、塑件工艺性分析该塑件是一塑料瓶盖,如图2一1所示,塑件壁厚属薄壁塑件,生产批量很大,材料为聚乙烯(PE,在高密度聚乙烯中掺入了部分低密度聚乙烯,改善塑件的柔韧性),成型工艺性很好,可以注射成型。
图2—1二、塑成型设备的选择与成型工艺规程的编制1.注射机的选用1)注射量的计算通过计算或Pro/E建模分析,塑件质量m为2.8g,塑件体积V1=3.077cm3流道凝料的质量m2还是个未知数,可按塑件质量的0.6倍来估算。
从上述分析中确定为一模八腔,所以注射量为:m=1.6nm=1.6 ×8 ×2.8=35. 84g2)塑件和流道凝料在分型面上的投影面积及所需锁模力的计算流道凝料(包括浇口)在分型面上的投影面积A2,在模具设计前是个未知值,根据多型腔模的统计分析,A2是每个塑件在分型面上的投影面积A1的0.2倍~0.5倍,因此可用0. 35 nA1来进行估算,所以A=nA1+A2=nA1+0. 35nA1=1.35nA1=8412. 336mm2式中A1= = 0. 785 ×31. 52=778. 92mm2F m=A p型=8412. 336 ×30=252370N=252. 37kN式中型腔压力p型取30MPa(因是薄壁塑件,浇口又是潜伏式浇口,压力损失大,取大一些)。
3)选择注射机根据每一生产周期的注射量和锁模力的计算值,可选用SZ一60/450卧式注射机,见表2一12.注塑成型工艺参数选用三、塑模具结构方案设计1.型腔数量的确定及型腔的排列1)型腔数量的确定该塑件精度要求不高,又是大批大量生产,可以采用一模多腔的形式。
考虑到模具制造费用、设备运转费用低一些,初定为一模八腔的模具形式。
2)型腔排列形式的确定该塑件有两圈内螺纹,要使螺纹型芯从塑件上脱出,必须设计一套自动脱螺纹的齿轮传动结构,并且型腔的分布圆直径和齿轮分布圆直径相吻合,若采用一模八腔,型腔分布圆直径就相当大了,这样模具结构尺寸就比较大,加上齿轮传动系统,模具结构复杂,制造费用也很高。
- 1、下载文档前请自行甄别文档内容的完整性,平台不提供额外的编辑、内容补充、找答案等附加服务。
- 2、"仅部分预览"的文档,不可在线预览部分如存在完整性等问题,可反馈申请退款(可完整预览的文档不适用该条件!)。
- 3、如文档侵犯您的权益,请联系客服反馈,我们会尽快为您处理(人工客服工作时间:9:00-18:30)。
注射模设计本设计为一塑料杯盖,如图4—327所示。
塑件比较简单,塑件的质量要求是不允许有裂纹和变形缺陷,脱模斜度30'~1º;塑件材料ABS,生产批量为大批量,塑件公差按模具设计要求进行转换。
图4—327一、塑件成型工艺性分析1、塑件的分析(1)外形尺寸该塑件壁厚为1和2.5mm ,塑件外形尺寸不大,塑件熔体流程不长,适合于注射成型,如图4—327所示(2)精度等级每个每个尺寸的公差不一样,有的属于一般精度,有的属于高精度,就按实际公差进行计算。
(3)脱模斜度ABS属无定型塑料,成型收缩率较小参考表2—10选择该塑件上型芯和凹模的统一脱模斜度为1º。
2、ABS的性能分析(1)使用性能综合性能好,冲击强度、力学强度较高,尺寸稳定,耐化学性,电气性能良好;易于成型及机械加工,其表面可镀铬,适合制作一般机械零件、减摩零件、传动零件和结构零件。
(2)成型性能1)无定型塑料。
其品种很多,各品种的机电性能及成型特性也各有差异,应按品种来确定成型方法及成型条件。
2)吸湿性强含水量应小于0.3%(质量),必须充分干燥,要求表面光泽的塑件应要求长时间预热干燥。
3)流动性中等。
溢边料0.04mm左右。
4)模具设计时要注意浇注系统,选择好进料口位置、形式。
推出力过大或机械加工时塑件表面呈现白色痕迹。
(3)ABS主要性能指标其性能指标见表4—44表4—44 ABS的性能指标密度g/cm3 1.02~1.08 屈服强度/MPa 50比体积cm3/g 0.86~0.98 拉伸强度/MPa 38吸水率(%)0.2~0.4 拉伸弹性模量/MPa 1.4×1000熔点/℃130~160 抗弯强度/MPa 80计算收缩率(%)0.4~0.7 抗压强度/MPa 53比热容J /(kg·℃)1470 弯曲弹性模量/MPa 1.41×0003、ABS 的注射成型过程及工艺参数 (1)注射成型过程1)成型前的准备。
对ABS 的色泽、粒度与均匀度等进行检验,由于ABS 吸水性较大,成型前应进行充分的干燥。
2)注射过程。
塑件在注射机料筒内经过加热、塑化达到流动状态后,由模具的浇注系统进行模具型腔成型,其过程可分为充模、压实、保压、倒流和冷却五个阶段。
3)塑件的后处理。
处理的介质为空气和水,处理温度为60~75℃,处理时间为16~20s 。
(2)注射工艺参数1)注射机:螺杆式,螺杆转数为30r/min2)料筒温度(℃):后段150~170;中段165~180;前段180~200。
3)喷嘴温度(℃):170~180。
4)模具温度(℃):50~80。
5)注射压力(MPa ):60~100。
6)成型时间(S ):17(注射时间取1.6,冷却时间7.4,辅助时间8)二、拟定模具的结构形式1.分型面位置的确定通过对塑件结构形式的分析,分型面应选在端盖截面积最大且利于开模取出塑件的底平面上,其位置如图1所示。
2.型腔数量和排列方式的确定(1)型腔数量的确定 该塑件采用的精度一般在2~3级之间,且为大批量生产,可采取一模多腔的结构形式。
同时,考虑到塑件尺寸、模具结构尺寸的大小关系,以及制造费用和各种成本费等因素,初步定为一模两腔结构形式。
(2)型腔排列形式的确定 多型腔模具尽可能采用平衡式排列布置,且要力求紧凑,并与浇口开设的部位对称。
由于该设计选择的是一模两腔,故采用直线对称排列,如图2所示。
(3)模具结构形式的确定 从上面的分析可知,本模具设计为一模两腔,对称直线排列,根据塑件结构形状,推出机构采用脱模板推出形式。
浇注系统设计时,流道采用对称平衡式,浇口采用侧浇口,且开设在分型面上。
因此,定模部分不需要单独开设分型面取出凝料,动模部分需要添加型芯固定板、支撑板和脱模板。
由上综合分析可确定选用带脱模板的单分型面注射模。
三、注射机型号的确定(1)注射量的计算 通过三维软件建模设计分析计算得塑件体积:3139.17cmv =塑塑件质量:g m 5.17139.1702.1V =⨯==塑塑ρ式中,ρ参考表4-44可取3/02.1cm g(2)浇注系统凝料体积的初步估算 根据经验浇注系统凝料体积按塑件体积的0.2倍估算,即浇筑系统凝料和两个塑件体积之和为314.4122.01139.1722.01V cm V =⨯+⨯=⨯+=)()(塑总(3)选择注射机 根据第二步计算得出一次注入模具型腔塑料总体积为314.41cm V =总,并结合式(4-18),则有:342.510.8/cm V=总。
根据以上计算初步选定公称注射量为125cm 3,注射机型号为XS-ZY-125卧式注射机,主要技术参数如下 理论注射容量/cm 3125 移模行程/mm300 螺杆柱塞直径/mm 42 最大模具厚度/mm 300 注射压力/MPa 150 最小模具厚度/mm200 注射速率/g ·s -1 锁模形式 塑化能力/g ·s -1 模具定位孔直径/mm 100 螺杆转速/r ·min-1 10~40 喷嘴球半径/mm 12 锁模力/kN 900 喷嘴口孔径/mm4 拉杆内间距/mm260×360注射机的相关参数的校核1) 注射压力的校核 查表可知ABS 所需注射压力为80~110MPa ,取p 0=100MPa 。
注射机公称注射压力p 公=150MPa ,注射机安全系数k 1=1.25~1.4,取k 1=1.3,则k 1p 0=1.3×100=130MPa <p 公,所以注射机注射压力合格。
2) 锁模力校核① 塑件在分型面上的投影面积A 塑,则22247763914.3r mm A =⨯==π塑② 浇注系统在分型面上的投影面积A 浇,则A 浇=0.2A 塑。
③ 塑件和浇注系统在分型面上总的投影面积A 总,则24.1146247762.047762A 2.0(A (mm A n A n A =⨯+⨯=+=+=)())塑塑浇塑总④ 模具型腔内的胀型力F 胀,则KN 184.401N 354.11462P =⨯==模总胀A FABS 属中等粘度塑件及有精度要求的塑件,p 模取35MPa 。
已知注射机的公称锁模力F 锁=1000kN ,锁模力安全系数为k 2=1.1~1.2,取k 2=1.2,则 锁胀F KN F k <=⨯=42.481184.4012.12 所以注射机锁模力合格。
四、浇注系统的设计 1.主流道的设计主流道通常位于模具中心塑料熔体的入口处,它将注射机喷嘴注射出的熔体导入分流道或型腔中。
主流道的形状为圆锥形,以便熔体的流动和开模时主流道凝料的顺利拔出。
主流道的尺寸直接影响到熔体的流动速度和充模时间。
另外,由于其与高温塑料熔体及注射机喷嘴反复接触,因此设计中常设计成可拆卸更换的浇口套。
(1)主流道尺寸1)主流道的长度:小型模具应尽量小于60mm ,本次设计中初取35mm 进行设计。
2)主流道小端直径:d=注射机喷嘴尺寸+(0.5~1)mm = (4+0.5) mm =4.5mm 。
3)主流道大端直径:'d =d+主L 2tan =4.5+2⨯35。
45tan ⨯=9.4mm ,式中= 。
4)主流道球面半径: S=注射机喷嘴球头半径+(1~2)mm=(12+2)mm=14mm5) 球面配合高度:h=3mm 。
(2)主流道凝料体积 =++=)(主主主主主主r R r L V 22R 3π314.3x35x(27.4+225.2+4.7x2.25)=1.383cm(3)主流道当量半径:mm R n5.3225.27.4=+= (4)主流道浇口套的形式 主流道衬套为标准件可选购。
主流道小端入口处与注射机喷嘴反复接触,易磨损。
对材料的要求比较严格,因而尽管小型注射模可以将主流道浇口套与定位圈设计成一个整体,但考虑上述因素通常仍然将其分开来设计,以便于拆卸更换。
同时也便于选用优质钢材进行单独加工和热处理。
设计中常用碳素工具钢(T8A 或T10A ),热处理淬火表面硬度为20~55HRC 。
2.分流道的设计(1)分流道的布置形式 在设计时应考虑尽量减少在流道内的压力损失和尽可能避免熔体温度降低,同时还要考虑减小分流道的容积和压力平衡,因此采用平衡时分流道。
(2)分流道的长度 由于流道设计简单,根据两个型腔的结构设计,分流道较短,故设计时可适当小一些。
单分流道长度取35mm ,如下图所示。
(3)分流道的当量径因为该塑件的质量g m 5.17139.1702.1V =⨯==塑塑ρ ,根据式 (4-16) ,分流道的当量直径为 mm L m D 7.2355.172654.0265.044=⨯⨯==分塑分(4)分流道截面形状 常用的分流道截面形状有圆形、梯形、U 形、六角形等,为了便于加工和凝料的脱模,分流道的大多设计在分形面上。
本设计采用梯形截面,其加工工艺性好,且塑料熔体的热流量损失、流动阻力均不大。
(5)分流道截面尺寸 设梯形的下底宽度为x ,底面圆角的半径为R=1mm ,并根据表4-6设置梯形的高度h=2.054mm ,则该梯形的截面积为052.28tan 052.22052.28tan 052.22(⨯+=⨯⨯⨯++=)()。
分x x x A再根据该面积与当量直径为 2.7mm 的圆面积相等,可得72.547.214.34052.28tan 054.2(22=⨯==⨯+分。
)D x π ,即可得:mm 6.2≈⨯,则梯形的上底约为3.2mm ,如图所示 (6)凝料体积 1)分流道的长度2)分流道截面积 228.5052.226.22.3mm mm A =⨯+=分 3)凝料体积 3324.04068.570A L cm mm mm V ≈≈⨯==分分分 (7)校核剪切速率1)确定注射时间:查表4-8,可取t=1.6s 2)计算分流道体积流量:s cm t q /116.1139.174.0V V 3=+=+=塑分分 3)由式 可得剪切速率 13333.106.4)27.2(10113.3R 3.3-⨯=⨯⨯⨯==s q ππγ分分分该分流道的剪切速率处于浇口主流道与分流道的最佳剪切速率之间,所以,分流道内熔体的剪切速率合格。
(8)分流道的表面粗糙度和脱模斜度 分流道的表面粗糙度要求不是很低,一般取即可,此处取。
另外,其脱模斜度一般在之间,这里取脱模斜度五.浇口的设计该塑件要求不允许有裂纹和变形缺陷,表面质量要求较高,采用一模两腔注射,为便于调整充模时的剪切速率和封闭时间,因此采用侧浇口。
其截面形状简单,易于加工,便于试模后修正,并且设在分型面上,从型腔的边缘进料。
塑件轮毂和外周有4条肋板相连,而浇口正对其中一块肋板,有利于向轮毂和顶部填充。