炼钢-精炼工艺介绍共46页
合集下载
炼钢工艺流程介绍(PPT47页)

炼钢转炉--氧枪设备
❖ 氧枪系统主要设备 ❖ 氧枪横移装置。 ❖ 氧枪升降装置 ❖ 氧枪滑道装置 ❖ 氧枪本体 ❖ 氧枪(氧、氮、水)
阀门站
炼钢转炉-(-次)除尘设备
❖ 蒸发冷却塔系统装置 ❖ 静电除尘器系统装置 ❖ 切换站系统装置 ❖ 轴流风机系统装置 ❖ 煤气冷却器系统装置 输灰系统 ❖ 输灰系统装置 ❖ 放散点火装置 ❖ CO气体检测报警
❖电弧炉炼钢法 ❖平炉炼钢法
Байду номын сангаас
炼钢流程图
钢产线流程图
炼钢工艺与设备
根据炼钢工艺流程, 可以把炼钢作业分为4部分:
1、冶炼前的铁水预处理工序 2、铁水冶炼 3、钢水精炼 4、钢水浇铸
炼钢 预处理
在铁水进入炼钢炉冶 炼前,除去其中的某 些有害成分或提取其 中某些有益成分的工 艺过程。 可分为普通铁水预处 理和特殊铁水预处理。前者有铁水预脱硫,铁水 预脱硅,铁水预脱磷;后者有铁水提钒,铁水提 铌,铁水脱铬等。
炼钢 预处理
重要的工艺节点: 兑铁(如果不是专用的预处理罐则没有) 前扒渣 预处理(脱硫、脱磷等) 后扒渣 出铁
炼钢 预处理
炼钢 混铁炉
高炉和转炉之间的 炼钢辅助设备。 主要用于调节和均 衡高炉和转炉之间 铁水供求的设备, 保证不间断地供给 转炉需要的铁水, 铁水在混铁炉中储 存和混匀铁水成份 及均匀温度,对转 炉炼钢非常有利。
炼钢工艺与设备
炼钢工程概述
❖ 本项目为山东焦化北海新区节能新工艺示范工程配套建设 项目,
❖ 拟建炼钢车间生产规模为年产合格钢水500万吨。项目分 两期完成,
❖ 一期配置1座600t混铁炉(预留)、2套复合喷吹脱硫装 置、2座120t顶底复吹转炉、2套150tLF、2套R9m8 机8流方坯连铸机,年产合格钢水250万吨。
炼钢工艺简介

一、 转炉炼钢厂冶炼工艺特点
转炉的顶吹工艺:转炉炼钢厂采用顶吹冶炼工艺,加速了 炉内脱碳反应接近平衡状态,缩短了冶炼周期,同时在节 约氧气、降低消耗、节约合金方面取得良好的效果。
音频化渣技术:2000年转炉与上海工业大学合作开发的音 频化渣技术,该项技术能根据炉内反应的声音,分析炉渣 的性质,及时指导氧枪枪位控制,促进化渣
连铸快换中间包:在不中断生产的前提下,迅速更换中间 包,保证连铸生产的连续性,使连铸作业率及连浇炉数大 幅提高,平均连浇炉数大幅度提高。
连铸快换水口:快速更换中包上水口,提高中包寿命,降 低耐材成本,现中包寿命最高达25小时(1500吨钢/包)
连铸坯热送:转炉于1998年开始连铸坯热送,目前转炉炼 钢厂的平均热送率已达60%以上,吨钢综合成本降低15元左 右。
转炉工艺:装入制度(铁水、废钢装入量)、供氧制度 (控制氧气流量、供氧强度、氧枪枪位)、造渣制度(炼钢 就是炼渣)、终点控制(控制碳含量、氧含量)、温度制度 (控制出钢温度)、脱氧合金化(采用脱氧方式、合金化操 作)。 精炼工艺:精炼工序主要是去气去夹杂、脱硫、微合金化
调整温度的作用。
连铸工艺:温度制度(控制中包温度)、拉速制度(根据 温度制定拉速表)、配水制度(根据不同的钢种、断面、拉 速制定出合理的冷却方案)。
• 吹炼速度快、生产率高 氧气顶吹转炉由于采用含量在99%以上的氧气进行吹
炼,反应激烈,脱碳、升温速度很快,冶炼周期很短,一 般转炉生产周期在30~40分钟,如宝钢300吨转炉平均冶炼 周期为36分钟/炉,。我们目前在20~30分钟,而平炉则 要5~6小时(吹氧)才能炼一炉钢。氧气顶吹转炉炼钢的 生产率为平炉的6~8倍,是一种效率极高的炼钢炉。
氧气顶吹转炉炼钢法的发展
炼钢-精炼-连铸工艺简介(PPT 40页)
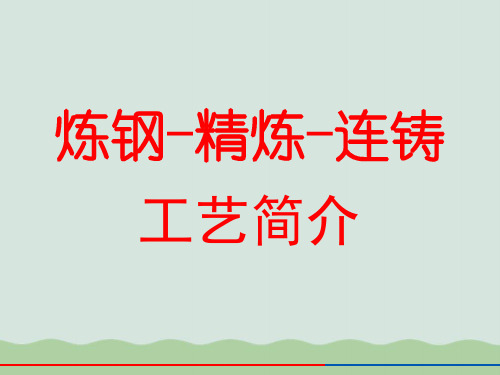
LF的基本功能
1、脱硫:利用造碱性还原渣和电弧的高温区进行脱硫 2、加热:采用电极放电加热钢水 3、合金化:成份微调 4、均匀钢液和去除夹杂:采用底吹Ar气搅拌钢液 5、生产组织中的缓冲:平衡转炉和铸机之间的供钢节奏。
喂线工艺
在RH-KTB工位和LF工位都设有 喂线装置,线的种类为Ca-Si 线和Ca-Al线。
•
1、有事业的峰峦上,有汗水的溪流飞 淌;在 智慧的 珍珠里 ,有勤 奋的心 血闪光 。
•
2、人们走过的每一个足迹,都是自己 生命的 留言; 留给今 天翻过 的日历 ,留给 未来永 久的历 史。
•
3、人生是一座可以采掘开拓的金矿, 但总是 因为人 们的勤 奋程度 不同, 给予人 们的回 报也不 相同。
出钢温度可由下式计算:
T出=T凝+△t1+△t2+△t3+△t4+△t5+α 式中:△t1—出钢过程温降,℃
△t2—出钢完毕至精炼开始的温降,℃ △t3—钢水精炼过程温降,℃ △t4—钢水精炼完毕至开浇前的温降,℃ △t5—钢水从钢包至中间包的温降,℃
α—连铸要求的钢水过热度,℃
终点控制
钢水达到钢种成分和温度要求的时刻,称之为“终点”。 1)钢中碳含量达到所炼钢种控制要求; 2)钢中P、S含量低于规格以下的一定范围; 3)出钢温度能保证进行精炼和浇铸; 4)对于沸腾钢,钢水应具有一定的氧化性。
连铸工艺示意图
连铸工艺的优点
• 简化工艺流程,提高生产效率
连铸省掉了脱模、整模、钢锭均热和开坯等工序。
• 提高金属收得率
连铸的切头、切尾损失为1%-2%,可提高金属收得率10%-14%。
• 降低能耗
由于提高了成坯率,省掉均热、开坯等能耗。
金属冶炼中的精炼工艺

精炼效果
经过精炼处理,金属的纯度可以得到 显著提高,同时其物理和化学性能也 可以得到改善。
02
精炼工艺的种类
电解精炼
总结词
通过电解过程去除杂质,实现金属的纯化。
详细描述
电解精炼是一种常用的金属精炼方法,通过电解过程将金属从其化合物中还原出来,同时去除其他杂质元素。该 方法适用于铜、镍、锌等金属的精炼。在电解精炼过程中,将粗金属或其化合物作为阳极,纯金属作为阴极,通 过电解作用使杂质元素留在阳极或进入电解液中,从而实现金属的纯化。
金属冶炼的流程
矿石准备
将矿石破碎、磨细,以便进行 后续的冶炼过程。
氧化焙烧
通过添加氧化剂(如空气或纯 氧)将矿石中的有价金属氧化 ,生成可溶性的盐类。
还原熔炼
将氧化焙烧后的矿渣与还原剂 (如焦炭、煤粉等)混合,在 高温下进行还原熔炼,生成金 属和炉渣。
精炼
通过化学或物理方法将金属中 的杂质去除,提高金属的纯度
详细描述
化学精炼是通过化学反应选择性地将杂质转化为可分离的形态,从而实现金属的纯化。该方法适用于 多种金属的精炼,如铝、镁等轻金属和铁、钴等重金属。在化学精炼过程中,利用不同金属元素与特 定试剂的反应特性,将杂质转化为易于分离的化合物或金属,从而实现金属的纯化。
其他精炼工艺
• 总结词:其他非主流的精炼工艺。
精炼工艺的成本与效率问题
成本高昂
金属冶炼中的精炼工艺需要大量原材料和能源, 导致生产成本较高。
效率低下
传统精炼工艺流程长、能耗高,导致生产效率较 低。
技术更新
通过不断的技术更新和改造,提高精炼工艺的效 率和降低成本。
新型精炼技术的研发与推广
富氧底吹熔炼技术
01
炼钢工艺资料

炼钢工艺的检测方法
• 化学分析法:通过化学实验,测定钢的成分。 • 金相分析法:通过金相显微镜,观察钢的组织结构。 • 力学性能测试法:通过拉伸试验机、硬度计等仪器,测试钢的力学性能。 • 工艺性能测试法:通过加工、焊接等实验,测试钢的工艺性能。
炼钢工艺的产品质量影响因素及控制措施
炼钢工艺的产品质量影响因素
炼钢原料的预处理及储存
炼钢原料的预处理
• 生铁:破碎、除杂,提高炼钢效率。 • 废钢:切割、除杂,提高废钢的利用率。 • 合金元素:破碎、筛选,提高合金元素的纯度。 • 脱氧剂、脱硫剂、脱磷剂:破碎、筛选,提高有效成分的含量。
炼钢原料的储存
• 储存环境:保持干燥、通风,防止原料受潮、氧化。 • 储存方式:分类存放,避免原料混杂,影响炼钢质量。 • 储存期限:合理安排原料的采购和储存,避免长期积压,影响原料质量。
CREATE TOGETHER
DOCS SMART CREATE
炼钢工艺详解 DOCS
01
炼钢工艺的基本原理与方法
炼钢工艺的发展历程及重要性
炼钢工艺的发展历程
• 古代炼钢:使用炭火将生铁加热熔化,加入矿石等原料进行冶炼,得到低碳钢。 • 19世纪中期:发明了转炉炼钢法,使用氧气或空气吹炼生铁,提高了炼钢效率。 • 20世纪初:出现了电炉炼钢法,利用电能为炼钢提供热能,进一步提高了炼钢速度和质量。 • 现代炼钢:发展出多种炼钢方法,如连铸、连轧、真空脱气等,实现了钢的连续生产和高 质量化。
• 原材料质量:原料质量直接影响钢的质量。 • 工艺参数:炼钢过程中的温度、时间、压力等参数影响钢的质量。 • 设备性能:设备性能的稳定性和可靠性影响钢的质量。 • 操作水平:操作人员的技能和经验影响钢的质量。
• 化学分析法:通过化学实验,测定钢的成分。 • 金相分析法:通过金相显微镜,观察钢的组织结构。 • 力学性能测试法:通过拉伸试验机、硬度计等仪器,测试钢的力学性能。 • 工艺性能测试法:通过加工、焊接等实验,测试钢的工艺性能。
炼钢工艺的产品质量影响因素及控制措施
炼钢工艺的产品质量影响因素
炼钢原料的预处理及储存
炼钢原料的预处理
• 生铁:破碎、除杂,提高炼钢效率。 • 废钢:切割、除杂,提高废钢的利用率。 • 合金元素:破碎、筛选,提高合金元素的纯度。 • 脱氧剂、脱硫剂、脱磷剂:破碎、筛选,提高有效成分的含量。
炼钢原料的储存
• 储存环境:保持干燥、通风,防止原料受潮、氧化。 • 储存方式:分类存放,避免原料混杂,影响炼钢质量。 • 储存期限:合理安排原料的采购和储存,避免长期积压,影响原料质量。
CREATE TOGETHER
DOCS SMART CREATE
炼钢工艺详解 DOCS
01
炼钢工艺的基本原理与方法
炼钢工艺的发展历程及重要性
炼钢工艺的发展历程
• 古代炼钢:使用炭火将生铁加热熔化,加入矿石等原料进行冶炼,得到低碳钢。 • 19世纪中期:发明了转炉炼钢法,使用氧气或空气吹炼生铁,提高了炼钢效率。 • 20世纪初:出现了电炉炼钢法,利用电能为炼钢提供热能,进一步提高了炼钢速度和质量。 • 现代炼钢:发展出多种炼钢方法,如连铸、连轧、真空脱气等,实现了钢的连续生产和高 质量化。
• 原材料质量:原料质量直接影响钢的质量。 • 工艺参数:炼钢过程中的温度、时间、压力等参数影响钢的质量。 • 设备性能:设备性能的稳定性和可靠性影响钢的质量。 • 操作水平:操作人员的技能和经验影响钢的质量。
炼钢工艺流程及典型案例介绍PPT课件

氧装置都带两只氧枪,一只工作,一只
备用。
枪身由三层同心圆钢管组成,枪尾 与
进水管、出水管和进氧管相连。
喷头 :是将压力能转换成动能的能量
器,
氧枪:氧气转炉炼钢中的主要工艺设备之一
14
第14页/共63页
2.4氧气转炉的辅助设备
•
炉料喷补设备:喷补方法分为湿法
和干法两种。喷补机的驱动电机经减
速器带动搅拌器旋转,将料斗内的补
2.7氧气转炉的主要原料
• 转炉对铁水进行冶炼操作
•
转炉炼钢主要是以液态生铁为原料的炼钢方法。其主要特
点是:靠转炉内液态生铁的物理热和生铁内各组分(如碳、锰、
硅、磷等)与送入炉内的氧进行化学反应所产生的热量,使金
属达到出钢要求的成分和温度。
转炉冶炼的炉料主要为铁水、造渣料(如石灰、石英、 萤石等)、铁合金(如硅铁、锰铁等)、脱氧剂(如硅化铁等) 以及增碳剂(如碳粉等),为调整温度,可加入废钢及少量的 冷生铁块和矿石等。
15
第15页/共63页
2.4氧气转炉的辅助设备
•铁(钢)包车的作用是承载钢包、接受钢水并运送钢包过跨 铁水包 鱼 雷 铁 包 车
炉渣盆
16
第16页/共63页
2.5氧气转炉的气体
• 一、氧气 • 氧气是氧气转炉炼钢的主要氧化剂,要求含氧量达到99.5%
以上,并脱除水分与皂液。 • 工业用氧是通过制氧机把空气中的氧气分离、提纯来实现的。
3
第3页/共63页
第一章 炼钢的主要任务:
脱碳
措施
炼钢过程使用氧化剂,如吹入氧 气,加入铁矿石等
主 要
脱磷、脱硫
措施 使用造渣剂造好渣
任 务
脱氧合金化
炼钢精炼工艺介绍PPT学习教案
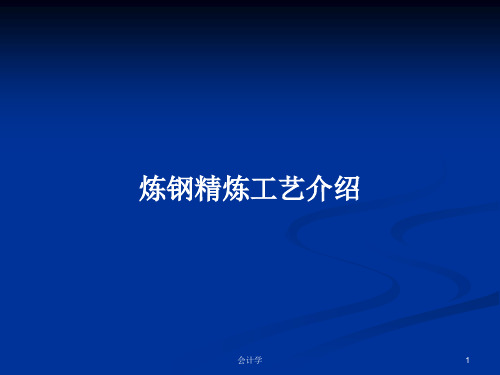
氩搅拌强度越大越有利于脱硫。
知识点: 1、喂线机的组成、结构及工艺参数要求。
2、喂线的主要冶金效果有哪些。 技能点: 1、正确操作喂线机,掌握喂线工艺参数值的设定、计数。 2、掌握喂线脱氧、酸溶铝控制的计算。
第19页/共46页
3、喂线工艺
例: XGL生产,到站O:160pPM,要求出站O:35ppm,试计算喂入的铝线量?
FeSi75-C
72.0~80.0
化学成份,%
Mn
Cr
P
不大于
0.4
0.3
0.035
0.5
0.5
0.04
SiS%i-Ca包Ca%芯线B:a% P%
≥50
≥14
≥14
≤0.02
SiA%l线: Ca%
P%
≥50
≥28
≤0.02
S% ≤0.03
线径 Φ13mm
S% ≤0.03
线径 Φ13mm
S
C
0.02
允许电流负荷
抗折强度/Mpa
电阻率/μΩ·m
密度/g·cm3
电极
接头
电极接头电极 Nhomakorabea接头
知识点: 21000~31000A 1、精炼用主要耐火材料≮9.和8 辅助≮1材4.0 料的≮规7.5格、名≮6.称5 、性≮1能.60 及主≮要1.70
化学成份。
2、精炼用能源介质的要求、功能特点。
第8页/共46页
吹氩压力大,搅拌动力大,气泡上升快,气泡在钢水中停留时间短,同时与 钢水接触面积小。因而,为提高吹氩效果,应保持较低压力下,加大氩气流 量。
2.1.3氩气流量和吹氩时间 采用透气砖吹氩,吹氩时间不宜太长,一方面受钢水温度下降的限制,另一
知识点: 1、喂线机的组成、结构及工艺参数要求。
2、喂线的主要冶金效果有哪些。 技能点: 1、正确操作喂线机,掌握喂线工艺参数值的设定、计数。 2、掌握喂线脱氧、酸溶铝控制的计算。
第19页/共46页
3、喂线工艺
例: XGL生产,到站O:160pPM,要求出站O:35ppm,试计算喂入的铝线量?
FeSi75-C
72.0~80.0
化学成份,%
Mn
Cr
P
不大于
0.4
0.3
0.035
0.5
0.5
0.04
SiS%i-Ca包Ca%芯线B:a% P%
≥50
≥14
≥14
≤0.02
SiA%l线: Ca%
P%
≥50
≥28
≤0.02
S% ≤0.03
线径 Φ13mm
S% ≤0.03
线径 Φ13mm
S
C
0.02
允许电流负荷
抗折强度/Mpa
电阻率/μΩ·m
密度/g·cm3
电极
接头
电极接头电极 Nhomakorabea接头
知识点: 21000~31000A 1、精炼用主要耐火材料≮9.和8 辅助≮1材4.0 料的≮规7.5格、名≮6.称5 、性≮1能.60 及主≮要1.70
化学成份。
2、精炼用能源介质的要求、功能特点。
第8页/共46页
吹氩压力大,搅拌动力大,气泡上升快,气泡在钢水中停留时间短,同时与 钢水接触面积小。因而,为提高吹氩效果,应保持较低压力下,加大氩气流 量。
2.1.3氩气流量和吹氩时间 采用透气砖吹氩,吹氩时间不宜太长,一方面受钢水温度下降的限制,另一
炼钢工艺简介
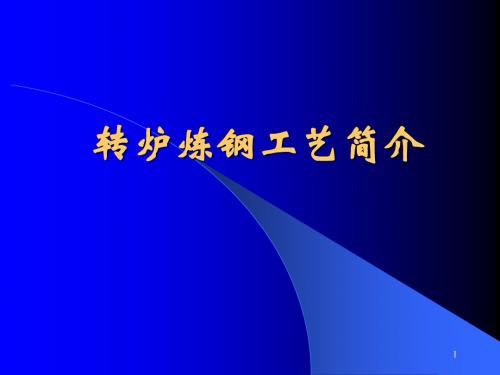
4
5
2. 转炉冶炼工艺
目的:
去碳、 升温、 成分控制、 脱磷硫
6
2. 转炉冶炼工艺
铁水和钢水的区别
化学成分(%) 温度 C Si 0.3~ 0.6 Mn P S 性能
铁水
4.5
0.11
0.08
0.02
1300
脆、不能轧制
钢水
<0.7
~3.0
>0.10 <0.25 <0.015 1650
强度、塑性高, 可轧制
2
转炉炼钢的工艺流程(现状)
铁水预处理
转炉冶炼
钢水炉外精炼
连铸
3
1. 铁水预处理(脱硫扒渣)
目的 去除铁水中的硫磺[S],并扒去脱硫渣。
脱硫的原理 将脱硫剂(石灰或金属镁),以N2作为载气, 通过喷枪吹入铁水中,来降低铁水中的硫黄. CaO+[S](CaS)+[O] Mg+[S] (MgS)
28
3. 连铸
目的:
将炉外精炼后 的钢水浇注成 一定形状的合 格的连铸坯。
29
24
3. 连铸
目的:
将炉外精炼后 的钢水浇注成 一定形状的合 格的连铸坯。
25
3. 连铸
目的:
将炉外精炼后的钢水 浇注成一定形状的合 格的连铸坯。
26
3. 连铸
连铸机种类:
板坯:中薄板坯、厚板坯、超低头板坯 方坯:小方坯、大方坯
27
3. 连铸
目的:
将炉外精炼后的钢水 浇注成一定形状的合 格的连铸坯。
3. 钢水炉外精炼-RH
目的:
脱碳、 去气
19
3. 钢水炉外精炼-RH
5
2. 转炉冶炼工艺
目的:
去碳、 升温、 成分控制、 脱磷硫
6
2. 转炉冶炼工艺
铁水和钢水的区别
化学成分(%) 温度 C Si 0.3~ 0.6 Mn P S 性能
铁水
4.5
0.11
0.08
0.02
1300
脆、不能轧制
钢水
<0.7
~3.0
>0.10 <0.25 <0.015 1650
强度、塑性高, 可轧制
2
转炉炼钢的工艺流程(现状)
铁水预处理
转炉冶炼
钢水炉外精炼
连铸
3
1. 铁水预处理(脱硫扒渣)
目的 去除铁水中的硫磺[S],并扒去脱硫渣。
脱硫的原理 将脱硫剂(石灰或金属镁),以N2作为载气, 通过喷枪吹入铁水中,来降低铁水中的硫黄. CaO+[S](CaS)+[O] Mg+[S] (MgS)
28
3. 连铸
目的:
将炉外精炼后 的钢水浇注成 一定形状的合 格的连铸坯。
29
24
3. 连铸
目的:
将炉外精炼后 的钢水浇注成 一定形状的合 格的连铸坯。
25
3. 连铸
目的:
将炉外精炼后的钢水 浇注成一定形状的合 格的连铸坯。
26
3. 连铸
连铸机种类:
板坯:中薄板坯、厚板坯、超低头板坯 方坯:小方坯、大方坯
27
3. 连铸
目的:
将炉外精炼后的钢水 浇注成一定形状的合 格的连铸坯。
3. 钢水炉外精炼-RH
目的:
脱碳、 去气
19
3. 钢水炉外精炼-RH