新型汽车轻量化设计要点
汽车轻量化设计与材料选择

汽车轻量化设计与材料选择随着环境保护和能源危机的日益严重,汽车轻量化已经成为了全球汽车工业发展的趋势。
轻量化设计可以减少汽车的整体质量,降低燃料消耗和排放,提高车辆的性能和安全性。
本文将探讨汽车轻量化的设计原则和常用的材料选择方法,旨在为汽车工程师和制造商提供一些有用的参考。
一、汽车轻量化设计原则1. 结构优化:通过优化汽车的结构设计,可以实现对重要部位和关键连接的强化,减少车身重量并提高整体刚性。
结构优化的方法包括有限元分析、疲劳试验、原型制造和模拟仿真等。
2. 部件集成:将不同功能的部件进行集成,可以减少重复的结构和材料,提高汽车的空间利用率和运动效率。
部件集成可以通过设计共享平台、模块化设计和系统集成等方法来实现。
3. 材料优化:选择合适的材料可以在保证安全性和性能的前提下减轻汽车的重量。
常见的轻量化材料包括高强度钢、铝合金、镁合金、碳纤维复合材料等。
不同材料的优缺点需要结合实际需求进行综合评估。
4. 智能设计:引入智能化技术可以提高车辆的轻量化设计效果,如使用先进的CAD/CAM软件进行设计和优化、运用虚拟现实技术进行仿真和验证等。
二、汽车轻量化材料选择1. 高强度钢:高强度钢具有较高的强度和刚度,可以减少车身和车架的重量。
它能够有效吸收能量,在碰撞事故中提供良好的安全保护。
高强度钢的选择需要综合考虑强度、塑性、焊接性等因素。
2. 铝合金:铝合金具有较低的密度和良好的加工性能,适用于制造车身和发动机等部件。
铝合金的使用可以有效降低汽车的燃料消耗和排放。
3. 镁合金:镁合金是一种轻质高强度材料,具有良好的耐腐蚀性和可回收性。
它可以用于制造车身结构、发动机零部件和底盘等,有助于降低车辆的整体重量。
4. 碳纤维复合材料:碳纤维复合材料具有高强度、高模量和低密度的特点,广泛应用于汽车领域。
它可以用于制造车身、车架和零部件等,具有良好的刚性和抗冲击性能。
5. 塑料材料:塑料材料具有较低的密度和良好的成型性能,可以替代传统的金属材料。
新能源汽车底盘轻量化设计方向

新能源汽车底盘轻量化设计方向近年来,随着环保意识的提高和能源紧缺问题的加剧,新能源汽车逐渐成为汽车行业的发展趋势。
新能源汽车以其环保、高效、低碳的特点,受到了广大消费者的追捧,也得到政府的大力支持和鼓励。
在新能源汽车的发展过程中,底盘轻量化设计是一个非常重要的方向。
底盘作为汽车的重要部件,对汽车的性能和安全起着至关重要的作用。
传统燃油汽车的底盘由钢铁材料构成,虽然结实耐用,但是重量较重,不利于提高能源利用效率和行驶里程。
而新能源汽车采用的电池和电动机等部件相对较轻,为了进一步降低整车的重量,必须对底盘进行轻量化设计。
底盘轻量化设计的方向主要有以下几个方面:1. 材料选用:传统燃油汽车多采用钢铁材料作为底盘的主要结构材料,而新能源汽车可以采用更轻的材料,如铝合金、镁合金、碳纤维等。
这些材料具有较高的强度和刚度,在保证底盘强度的前提下减少了材料的重量。
2. 结构优化:通过优化底盘的结构设计,可以减少底盘材料的使用量,从而达到减轻底盘重量的目的。
采用空心结构设计、网状结构设计等,可以在保证底盘强度的同时减少材料的用量。
3. 制造工艺:底盘的制造工艺也是轻量化设计的重要方面。
传统燃油汽车的底盘多采用焊接的方式进行组装,这在一定程度上增加了底盘的重量。
而新能源汽车可以采用先进的制造工艺,如铸造、锻造、粘接等,可以使得底盘结构更加紧凑,降低底盘的重量。
4. 部件集成:底盘的轻量化设计还包括对各个部件的集成设计。
新能源汽车采用了电池、电动机等多个部件,这些部件的位置和布局会直接影响底盘的重量。
通过合理规划各个部件的位置,可以减少底盘结构的复杂性,降低底盘的重量。
底盘轻量化设计不仅能够降低整车的重量,提高能源利用效率和行驶里程,还能够提升车辆的操控性和安全性能。
在底盘轻量化设计过程中也面临一定的挑战。
新材料的应用需要进一步研究和验证,以确保其强度和可靠性满足车辆的使用要求。
轻量化设计也需要与车辆的其他性能指标相匹配,不能只追求轻量化而忽视了其他方面的要求。
新能源汽车底盘轻量化设计方向
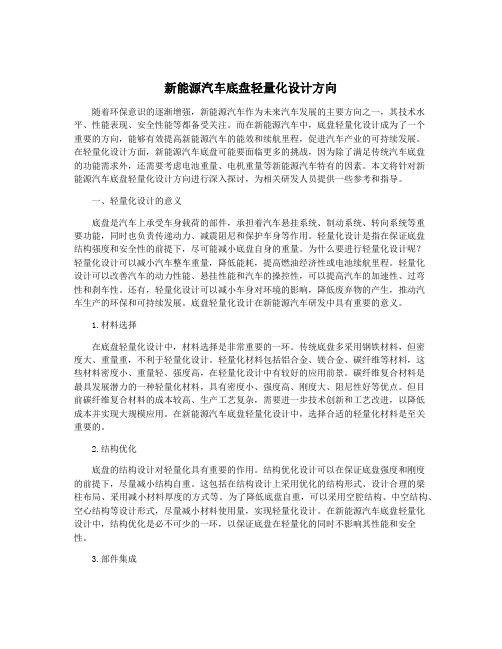
新能源汽车底盘轻量化设计方向随着环保意识的逐渐增强,新能源汽车作为未来汽车发展的主要方向之一,其技术水平、性能表现、安全性能等都备受关注。
而在新能源汽车中,底盘轻量化设计成为了一个重要的方向,能够有效提高新能源汽车的能效和续航里程,促进汽车产业的可持续发展。
在轻量化设计方面,新能源汽车底盘可能要面临更多的挑战,因为除了满足传统汽车底盘的功能需求外,还需要考虑电池重量、电机重量等新能源汽车特有的因素。
本文将针对新能源汽车底盘轻量化设计方向进行深入探讨,为相关研发人员提供一些参考和指导。
一、轻量化设计的意义底盘是汽车上承受车身载荷的部件,承担着汽车悬挂系统、制动系统、转向系统等重要功能,同时也负责传递动力、减震阻尼和保护车身等作用。
轻量化设计是指在保证底盘结构强度和安全性的前提下,尽可能减小底盘自身的重量。
为什么要进行轻量化设计呢?轻量化设计可以减小汽车整车重量,降低能耗,提高燃油经济性或电池续航里程。
轻量化设计可以改善汽车的动力性能、悬挂性能和汽车的操控性,可以提高汽车的加速性、过弯性和刹车性。
还有,轻量化设计可以减小车身对环境的影响,降低废弃物的产生,推动汽车生产的环保和可持续发展。
底盘轻量化设计在新能源汽车研发中具有重要的意义。
1.材料选择在底盘轻量化设计中,材料选择是非常重要的一环。
传统底盘多采用钢铁材料,但密度大、重量重,不利于轻量化设计。
轻量化材料包括铝合金、镁合金、碳纤维等材料,这些材料密度小、重量轻、强度高,在轻量化设计中有较好的应用前景。
碳纤维复合材料是最具发展潜力的一种轻量化材料,具有密度小、强度高、刚度大、阻尼性好等优点。
但目前碳纤维复合材料的成本较高、生产工艺复杂,需要进一步技术创新和工艺改进,以降低成本并实现大规模应用。
在新能源汽车底盘轻量化设计中,选择合适的轻量化材料是至关重要的。
2.结构优化底盘的结构设计对轻量化具有重要的作用。
结构优化设计可以在保证底盘强度和刚度的前提下,尽量减小结构自重。
新能源汽车轻量化设计优化

新能源汽车轻量化设计优化引言近年来,随着环境污染和能源危机的日益严重,新能源汽车作为解决之道备受关注。
然而,新能源汽车的轻量化设计也成为了研究的热点之一。
本文将从材料选择、结构优化和创新技术方面探讨新能源汽车轻量化设计的优化。
第一章材料选择新能源汽车轻量化设计的第一步是选择适合的材料。
传统的钢铁材料虽然强度高,但其密度也较大。
在轻量化设计中,选择轻质材料如铝合金、镁合金和复合材料可以降低整车重量。
与此同时,这些材料还具有较高的强度和刚度,能够满足车辆在使用过程中的应力要求。
第二章结构优化在材料选择完成后,接下来需要对车辆的结构进行优化。
通过采用优化设计方法,可以在保证车辆结构稳定性的前提下,进一步减轻车身重量。
其中一种常用的优化方法是拓扑优化,它可以通过数学模型和计算算法,自动确定最佳的材料分布,以达到最小重量的设计目标。
此外,使用有限元分析工具可以对结构进行强度和刚度的评估,有助于精确优化设计。
第三章创新技术除了材料选择和结构优化外,创新技术也是新能源汽车轻量化设计的重要方向之一。
例如,3D打印技术可以实现复杂结构的生产,并且可以根据实际需要控制材料的分布,以实现轻量化设计。
另外,纳米材料也具有很大的潜力,它们在车身材料中的应用可以显著提高强度和刚度,从而减轻车辆重量。
第四章挑战与展望在新能源汽车轻量化设计的过程中,仍然存在一些挑战。
首先,新材料的应用面临成本和可靠度的问题,这需要在技术发展和经济实用性之间寻找平衡。
其次,轻量化设计需要与车辆的安全性能相兼顾,确保在碰撞等意外情况下仍能提供足够的保护。
此外,新材料的使用也需要考虑资源和环境可持续性。
展望未来,随着科技的进步和工艺的改进,新能源汽车轻量化设计优化将迎来更多机遇。
新材料的发展将为轻量化设计提供更多选择和解决方案,同时结构优化和创新技术的不断发展也将为轻量化设计提供更高效和精确的工具。
在不久的将来,我们有理由相信,新能源汽车轻量化设计优化将成为汽车行业的重要发展方向。
新能源汽车轻量化的关键技术

新能源汽车轻量化的关键技术随着全球环境污染问题的日益严重以及对传统石油资源的依赖性不断降低,新能源汽车的发展日益受到社会的关注。
而新能源汽车轻量化是提高其运行效能和续航能力的关键技术之一。
下面将分析新能源汽车轻量化的关键技术。
(一)车身结构轻量化技术车身结构是新能源汽车最重要的部分,其轻量化设计是带来轻量化的最关键技术之一。
轻量化的设计需要寻找的一个平衡点,既满足强度和刚度的要求,又能够通过新材料的使用来减轻车身总重量。
目前,研究重点主要集中在铝合金和碳纤维复合材料应用于车身结构上。
铝材质轻,可以在车身结构上减轻重量,而碳纤维复合材料的轻量化效果更为显著,但其成本较高,需要更多的技术改善才能实现日常使用。
(二)电池系统轻量化技术电池是新能源汽车最重要的部分,也是最为昂贵的零部件之一。
现代电池系统的重量通常超过车身重量的20%。
因此,电池系统的轻量化是提高新能源汽车性能的关键所在。
目前,研究人员在电池结构中广泛采用钛合金和高强度钢材来代替重量较大且容易腐蚀的铅酸和镍氢电池。
另外,针对电池组件的设计也得到了发展,包括探索开发更高效,更坚固且更轻的电池系统。
驱动系统是新能源汽车能源转化的核心,包括电机、电控系统、变速器等。
驱动系统轻量化主要是实现电机的轻量化,以提高驱动效率。
从材料角度,新型高性能磁性材料以及碳纤维等轻质高强材料的应用将为电机重量的降低提供保持所需强度和刚度的可行方案。
同时,减少电机尺寸也能够降低新能源汽车的总重量,提高续航里程。
底盘和悬架系统是新能源汽车的支撑系统,其轻量化设计是提高整车性能的重要手段。
底盘和悬架系统通常采用高强度铝合金和钛合金等轻质高强度材料,以减轻车身重量,降低燃油消耗量。
同时,通过结构优化,减少车轮和刹车系统的重量也能够显著降低新能源汽车的总重量。
综上所述,新能源汽车轻量化是提高其运行效能和续航能力的关键技术之一。
目前,应用于新能源汽车轻量化设计的铝合金和碳纤维复合材料,以及钛合金、高强度钢材和新型高性能磁性材料等轻质高强材料。
新能源汽车底盘轻量化设计方向

新能源汽车底盘轻量化设计方向随着全球汽车行业的发展和环境问题的日益突出,新能源汽车已经成为了未来汽车发展的主要方向。
而在新能源汽车的设计中,底盘轻量化是提高车辆性能和续航里程的重要手段之一。
本文将从材料选择、结构设计和制造工艺三个方面探讨新能源汽车底盘轻量化的设计方向。
一、材料选择材料选择是新能源汽车底盘轻量化的第一步。
目前常用的新能源汽车底盘材料主要有铝合金、镁合金和碳纤维复合材料。
铝合金是目前底盘轻量化的主要材料之一。
它具有密度低、刚度高、耐腐蚀、可塑性好等优点,而且现有的铝合金工艺成熟,生产成本相对较低。
将铝合金应用于新能源汽车底盘可以有效降低整车重量,提高能源利用效率。
镁合金是另一种常用的新能源汽车底盘材料。
镁合金具有密度低、刚度高、比强度大等特点,是目前轻量化设计中最有潜力的材料之一。
由于镁合金可塑性差,容易发生脆性断裂,加工难度大,所以在底盘设计中还需要进一步改进工艺和制造技术。
碳纤维复合材料是轻质、高强度的材料,具有优异的机械性能和耐腐蚀性能。
碳纤维复合材料的生产成本相对较高,而且在强度和韧性之间的权衡也是一个挑战。
在新能源汽车底盘设计中,碳纤维复合材料可以用于关键部件的制造,以提高整车的重量和性能。
二、结构设计新能源汽车底盘的结构设计是底盘轻量化的关键环节之一。
合理的结构设计可以在保证底盘强度的最大限度地降低底盘重量。
底盘的刚性要满足安全和稳定性的要求。
在底盘横梁和纵梁的设计中,应将材料和结构进行优化匹配,以保证车辆在运行中的变形和应力分布均匀。
新能源汽车底盘的设计中应注重空间利用率。
由于电池组的体积较大,因此在设计底盘结构时要合理利用底盘空间,以提高电池组的装载率和整车的续航里程。
底盘的设计中应注重降低风阻。
减小底盘部件的截面积和向上突出的部位,以减小底盘对空气的阻力,提高整车的空气动力性能。
三、制造工艺制造工艺是新能源汽车底盘轻量化设计的重要环节。
合理的制造工艺可以提高底盘的制造效率,降低成本,提高质量。
汽车轻量化的主要技术

汽车轻量化的主要技术
汽车轻量化是汽车行业开发、提高汽车性能和减少燃油消耗的重要技术。
通过汽车轻量化,不仅有效的减轻汽车重量,提高汽车的加速性能,减少能耗,而且有助于减少材料和能源的消耗。
汽车轻量化的主要技术有:
1.车身材料改进:通过使用合理的车身材料,达到车身更轻、更坚固,
更好、更有效的结构,从而减少车身重量。
通常使用的材料包括:钢材、铝
合金、高强度塑料等。
2.底盘优化设计:车身下部部分是重车身重量最大的部分,通过优化设计,减少底盘的重量和面积,减少结构梁的数量,加强车身的刚性,改善汽
车行驶的舒适性,实现底盘结构的轻量化。
3.焊接工艺优化:焊接技术是车身部件轻量化的重要技术,有助于将大
型车身部件拆分,缩小模型尺寸,从而实现更轻量化的结构。
4.金属发泡:金属发泡是一种可以大大减少汽车重量的复合材料技术。
金属发泡材料特殊的复合结构,能极大的降低车身重量,同时又能满足强度
和刚性的要求。
汽车轻量化已经成为当前汽车行业的主流发展,通过应用上述多种技术,可以大大减小汽车重量,提高能源利用效率,减少燃料消耗,是提高汽车效
率和节省能源的有效措施。
新型轻量化汽车结构设计与优化

新型轻量化汽车结构设计与优化随着科技和工业的不断发展,汽车作为日常生活中必需品也受到了人们越来越多的关注。
尤其是在环保问题和节能减排的形势下,新型轻量化汽车逐渐成为了主流发展方向。
本文将就新型轻量化汽车的结构设计和优化进行探讨。
一、新型轻量化汽车结构设计的重要性对于汽车制造商来说,减轻车辆的重量是提高其燃油效率的一种重要方法。
轻量化设计就是指将汽车的重量越来越轻,以此来达到提高燃油效率的目的。
因此,汽车结构设计方案和制造材料应以“越轻越好”的原则为基础。
以此来推动轻量化汽车的发展。
二、新型轻量化汽车结构设计方案在新型轻量化汽车结构设计方案中,材料的选择是至关重要的。
我们通常使用的钢板材料本身就是一种相对较重的材料,而且使用寿命不够长。
因此,汽车制造商不得不使用其他材料来代替钢板材料。
这些材料包括铝合金、碳纤维等。
铝合金由于具有出色的耐腐蚀性和高阻尼特性,可以有效地减少振动和噪音的传播,因此逐渐成为了轻量化汽车的首选材料之一。
同时,铝合金比钢板材料更轻,可以显著地降低汽车的重量,从而提高了汽车的燃油效率,减少了尾气排放。
碳纤维是一种具有轻重比非常优异的材料。
其重量仅为钢钢材料的1/5,同时其强度却要比钢板材料高10倍以上。
因此,汽车制造商开始将碳纤维应用于汽车的制造中来,以此来打造更具轻量化的汽车。
除了材料的选择,汽车结构设计方案还应该充分考虑到现代科技和计算机辅助设计技术的应用。
比如,设计师可以使用虚拟仿真技术来模拟汽车在不同路况下的行驶情况。
这将有助于他们找到最佳结构方案和优化材料布局。
虚拟仿真也可以创建和测试新型零部件和系统,以验证其在实体车辆中的重要性。
三、结构优化设计结构优化是在保证汽车机械性能、安全性、舒适性等基础上,通过减轻汽车整车重量来提高汽车燃油效率的一种技术。
优化设计的核心思想是在设计阶段就考虑到减重问题,从而实现最佳轻量化设计效果。
下面将提到两个方面的优化设计。
(1)车身设计的优化在轻量化设计中,车身设计是一个重要的环节。
- 1、下载文档前请自行甄别文档内容的完整性,平台不提供额外的编辑、内容补充、找答案等附加服务。
- 2、"仅部分预览"的文档,不可在线预览部分如存在完整性等问题,可反馈申请退款(可完整预览的文档不适用该条件!)。
- 3、如文档侵犯您的权益,请联系客服反馈,我们会尽快为您处理(人工客服工作时间:9:00-18:30)。
TPV吹塑管与EPDM胶管硫化粘接 为一体
具体结构合理设计主要有以下3个方面: 通过结构优化设计,减小车身骨架及车身钢板的质量,对车身强度和 刚度进行校核,确保汽车在满足性能的前提下减轻自重。 通过结构的小型化,促进汽车轻量化,主要通过其主要功能部件在同 等使用性能不变的情况下,缩小尺寸。 采取运动结构方式的变化来达到目的。比如采用轿车发动机前置、前 轮驱动和超轻悬架结构等,使结构更紧凑,或采取发动机后置、后轮
1325g
657g
项目 — 6.9MPa 10.3MPa 制动液相容性试验 143±℃×5h 拉伸强度试验 臭氧试验 100mPa±10mPa /40℃±3℃/48h±10h 爆破压力
主要性能 — ≤0.6 cm3/m ≤1.0cm3/m ≥60MPa ≥1446N 外覆层无龟裂或裂纹 外覆层无龟裂或裂纹
汽车轻量化研究
内容
• • • • •
汽车轻量化的趋势 汽车轻量化途径 结构设计优化 制造工艺创新 材料轻量化
研究表明,轿车减重减重100kg与节油效果关系如下所示:
全寿命 减重 重量 平均油耗 减重节油 周期里程 全寿命节油 车辆类型使用条件
t 小型轿车 长途为主 1 L/100km L/100km 1000km 6 0.36 200 L 720
结构优化
原方案
前罩锁区域Z方 向刚度分析 变形 刚度
新方案
原始方案 1.53mm 100% 优化方案 1.39mm 110%
从模流分析结果看,原方案的玻纤取向 略差,经浇口调整后玻纤取向有所改善。 CAE计算显示优化后刚度提升了10%。
结合产品的结构设计,减重方案的开发与应用
高流动材料PP , 降低产品壁厚,提高产品刚性,产品减重
最新材料 23 46 1.08 17 2400 28±3
结合产品的 结构设计,可 减轻更多的重量!
mm
3.0
2.5
• 通过开发汽车车身、底盘、动力传动系统等大型 零部件整体加工技术和相关的模块化设计和制造 技术,使节能型汽车从制造到使用各个环节都真 正实现节能、环保。 • 通过结合参数反演技术、多目标全局优化等现代 车身设计方法,研究汽车轻量化结构优化设计技 术,包括多种轻量化材料的匹配、零部件的优化 分块等。从结构上减少零部件数量,确保在汽车 整车性能不变的前提下达到减轻自重的目的。
小型轿车 市区为主
1
8.5
9 11
0.55
0.28 0.52
150
300 500
829
844 2578
中型轿车 长途为主 1.6 中型轿车 出租 1.6
豪华轿车 长途为主
2
12
0.30
100
300
汽车轻量化趋势
=
绿色、环境友好型趋势
在保证汽车的强度和安全性能的前提下,尽可能地降低汽车的整备质量,从而提高汽车 的动力性能,减少燃料消耗,降低排气污染。
同时,还有零部件数量集成及功能集成,实现整车轻量化
结构优化
对汽车总体结构进行分析和优化,实现对汽车零部件的精简、整体化和轻质化。
在现代汽车工业中,利用CAD/CAE/CAM等软件辅助汽车设计已经成为不可或缺的环 节,涵盖了汽车设计和制造的各个环节。通过这类软件能够建立数字化模型,准确实
现车身的实体结构设计和局部设计,同时可以通过仿真计算来检验汽车结构的刚度,
驱动的方式,达到使整车局部变小,实现轻量化的目标。
在汽车结构优化设计方面,我国已经完全从依靠经验设计发展到 应用有限元等现代设计方法进行静强度计算和分析阶段。
新工艺的开发与应用
微发泡注塑工艺 优势: 1.轻量化:微发泡工艺可节省产品原材料20%左右及有利于内外饰件轻量化; 2.成本优势:微发泡工艺注塑可缩短产品成型周期及节省20%左右原材料有利 于降低塑料零部件成本; 3.高精度:微发泡工艺注塑可减小或消除了常规模塑在合模和保压过程中产生 的模内应力,提升了产品成型尺寸精度。
材料轻量化应用的现状
汽车材料在汽车上的应用比例
随着汽车材料技术的飞速发展, 现代汽车制造材料的构成也在不断发 生变化。以现代轿车用材为例,按照 重量换算,钢材占汽车自重的 55 %~ 60 % ,铸铁占 5 %~ 12 %,有色金属
占 6%~ 10%,塑料占 8%~12%,橡
整车重量减少100kg
油耗:-0.4L/100km
CO2 : -10g/100km 环保和节能的需要… 轻量化已经成为世界汽车发展的潮流和趋势!
汽车轻量化的途径 结构设计优化
材料轻量化
高强钢、镁合金、铝合金、 工程塑料及其复合材料和陶瓷材料等
制造工艺创新
热压成型、液压成型、 内高压成型、激光拼焊等
TPU外覆层+钢丝增强+PTFE内管
低温弯曲试验(弯曲半径R60) ﹣45℃~﹣48℃×72h
以少代多典型应用案例二
EPDM胶管+不锈钢管+卡箍
项目
原管路系统 集成管路 7件 1.2kg 3件 0.75kg 减重率 37%
中 冷 器 出 气 管
零件数 重量
测试项目 爆破压力 剥离强度
集成管主要性能 常温 80℃ 1.4(MPa) ≥0.6 (MPa) ≥3KN/m
模态等参数,并且能够便捷地对汽车结构进行改造。 利用CAD/CAE/CAM一体化技术,可以准确实现各构件的开头配置、板材厚度的变化 进行分析,并可从数据库中提取由系统直接生成的有关该车的相关数据进行工程分析 和刚度、强度计算。对于采用轻质材料的零部件,还可以进行布局分析和运动干涉分 析等,使轻量化材料能够满足车身设计的各项要求。
• 通过开发汽车车身、底盘、动力传动系统等大型 零部件整体加工技术和相关的模块化设计和制造 技术,使节能型汽车从制造到使用各个环节应用案例一
金属管+橡胶管+卡箍+接头
项目 零件数 原管路系统 集成管路 36件 6件 减重率 50%
重量
离 合 器 软 管
容积膨胀量
1.高刚度保证零件的薄壁化
单位 填充物比例 熔融指数(230 ℃ ) 密度(比重) 拉伸强度 弯曲模量 冲击强度(23℃) 实例 (前保险杠壁厚变化) % g/10min g/cm3 MPa MPa KJ/m2 普通材料 15 18 1.035 21.1 1950 34±3
2.高流动性保证薄壁零件的成形性